摘要
研究了超声喷丸对7075铝合金棒材微观组织结构、显微硬度、电化学腐蚀以及晶间腐蚀行为的影响。金相、XRD以及TEM等结果表明,采用超声喷丸制备了表层晶粒尺寸约为78.2 nm的梯度纳米结构7075铝合金,且合金表层时效析出强化相 (η和η′相) 回溶基体。显微硬度结果表明,超声喷丸处理后合金表层硬度提升了约20%。在0.1 mol/L Na2SO4+20 mmol/L NaCl溶液中的极化曲线结果表明,合金在超声喷丸处理后点蚀电位正移,说明合金耐点蚀萌生能力增强。在3.5%NaCl溶液中的极化曲线与电化学阻抗谱结果表明,7075铝合金棒材在超声喷丸处理后腐蚀速率加快,且腐蚀速率在深度方向上呈递减趋势。晶间腐蚀浸泡实验表明7075铝合金在超声喷丸处理后耐晶间腐蚀能力降低。最后,讨论了超声喷丸7075铝合金棒材的表层强化机制与腐蚀机理。
关键词: 7075铝合金棒材 ; 表面纳米化 ; 显微硬度 ; 腐蚀行为
7000系铝合金 (Al-Zn-Mg-Cu系) 具有低密度、高强度、高韧性等特点[1],在航空航天领域应用广泛。然而,由于其元素组成以及特定的微观组织结构特征,7000系合金容易发生点蚀、晶间腐蚀 (IGC) 和应力腐蚀开裂 (SCC) 等局部腐蚀[2]。通过合金化与调整热处理和时效制度,可以改善7000系铝合金的耐局部腐蚀性能。譬如,峰时效处理后,铝合金晶内存在大量弥散分布的η′相,这使得材料具有较高的强度,但是晶界上连续分布的η相会使材料的耐局部腐蚀性能变差,导致腐蚀沿晶间扩展。双级过时效工艺可以改变晶间η相的分布状态,使η相在晶间粗大断续分布,显著增强了铝合金的耐腐蚀能力,但以强度损失10%~15%为代价[3~5]。提高Zn和Mg含量可进一步提升7000系铝合金强度,但同样以牺牲耐蚀性能为代价。由此可见,强度与耐蚀性能之间的倒置关系在7000系合金中普遍存在。
解决铝合金强度与耐蚀性能倒置关系的一个思路是创新材料设计方法。合金化和热处理等传统方法制备的材料是一个均匀的块体,然而自然界中广泛存在的材料往往不是均匀的,而是具有梯度结构。经过几百万年甚至上亿年的进化,生物材料往往表现出多方面的优异性能,如强度和韧性的“完美”结合等。仅从材料科学的角度讲,生物材料实现人造材料无法达到的优异性能的原因之一是其多维结构的梯度化。螳螂虾的锤节以及蜘蛛的爪牙等是生物材料利用梯度结构获取优异性能的典型例子[6~8]。受自然界生物材料梯度化的启发,研究人员在结构材料的梯度化领域已经做了不少有益的尝试,如气相沉积[9]、自蔓延[10]、高温注入[11]、离子束掺杂[12]、表面渗氮[13]、增材制造[14]等技术已经被用以制备梯度结构材料。一些表面剧烈塑性变形技术如喷丸处理[15, 16]、超声喷丸处理[17]、滑动摩擦处理[18, 19]等表面处理技术可以将合金表层晶粒纳米化,而合金芯部组织结构不发生变化,从而获得从芯部到表层组织不断变化的纳米梯度结构材料[20]。人们已经利用多种表面机械处理技术提高铝合金的性能。通过表面机械处理技术在铝合金表面形成的表层纳米组织跟铝合金基体没有明显的界面分层,与传统的表面沉积技术相比更加稳定。表面机械处理技术在提升合金强度的同时,基体粗晶组织的存在还使其仍保留了良好的塑性,且合金的使用寿命可得到大幅度提升。Pandey等[21]研究了超声喷丸处理对7075铝合金腐蚀行为的影响。研究发现超声喷丸处理过的样品具有比未处理样更高的腐蚀电位和更低的电流密度,耐腐蚀性能的提升得益于超声喷丸处理后粗大析出相的细化、表层区域残余应力的引入以及表面更加致密均匀的钝化膜形成。遗憾的是,Pandey等[21]的研究中没有涉及7075铝合金的晶间腐蚀行为。相比于电化学腐蚀信息,晶间腐蚀性能对7000系铝合金更为关键,这是因为航空铝合金的应力腐蚀开裂行为往往与晶间腐蚀密切相关。Huo等[18]研究了经滑动摩擦处理 (SFT) 的7075铝合金,发现其机械强度和耐晶间腐蚀能力都有所提升,机械强度增加的原因主要是晶粒细化,耐晶间腐蚀能力的提升得益于SFT造成的晶粒细化以及晶界析出相和无沉淀析出带的消失。本课题组[22]研究了超声喷丸冲击能量对7150铝合金腐蚀行为的影响,结果表明超声喷丸对7150铝合金的局部腐蚀行为具有双重作用:当冲击能量足够高时,7150的局部腐蚀被完全抑制;而当冲击能量较低时,7150铝合金的耐局部腐蚀的能力并没有增强,晶间腐蚀扩展反而被梯度纳米结构加速。Bao等[23]研究了二次喷丸处理对7075铝合金腐蚀行为的影响,二次喷丸处理后7075铝合金的局部腐蚀坑数量和深度都有所减少,耐局部腐蚀能力增强,裂纹扩展被有效抑制,耐应力腐蚀性能增强。这是因为经二次喷丸处理的7075铝合金表面粗糙度有所下降,且具有更高的残余应力。
本文以国产7075铝合金棒材为研究对象,探究了超声喷丸处理对7075铝合金显微组织和硬度的影响,同时结合其晶间腐蚀行为以及不同深度的电化学腐蚀信息,讨论了超声喷丸处理对7075铝合金棒材的强化机制与腐蚀机理。
1 实验方法
实验材料为7075-T6铝合金棒材 (恒瑞铝业),其成分 (质量分数,%) 为:Zn 5.5,Mg 2.3,Cu 1.9,Si 0.4,Fe 0.5,Mn 0.3,Cr 0.2,Zr 0.2,其他0.15,Al余量。采用线切割机加工成直径30 mm、厚度5 mm的圆形样品,之后依次用400#、600#、1000#、1500#的砂纸进行打磨,最后超声清洗。超声喷丸装置示意图如图1所示,对所得样品在不锈钢制圆柱形腔室进行超声喷丸处理。所用喷丸材质为304不锈钢,振子以20 kHz的频率振动,带动喷丸高速撞击样品,使样品表面产生剧烈的塑性变形。超声喷丸处理的能量会影响样品塑性变形层的厚度,而冲击的能量又主要受喷丸直径、冲击距离、超声振幅和冲击时间的影响。本研究中选用喷丸直径为3 mm,超声振幅为60 μm,冲击时间是8 min。选取不同的冲击距离 (15、25、40和60 mm) 探究了冲击能量对7075铝合金硬化层厚度的影响,并将冲击距离为15 mm的高能喷丸样用于后续电化学腐蚀和晶间腐蚀测试。
图 1 超声喷丸处理装置示意图
将喷丸处理后的样品进行切割,使用环氧树脂封装,并露出样品截面,依次用400#、600#、1000#、1500#、2000#的砂纸进行打磨,0.5 μm Al2O3抛光,超声清洗备用。采用凯勒试剂 (0.5% HF+l.5% HCl+2.5% HNO3+95.5% H2O) 侵蚀以在Axiolab5型光学显微镜下观察其金相组织。利用CuKα 辐射的TD-3500型X射线衍射仪 (XRD) 以2.4°/min的2θ扫描速率获得样品的XRD结果,对比喷丸前后样品表层相组成的变化。采用聚焦离子束-电子束双束系统 (FEI Scios) 制备厚度小于200 nm的薄膜,采用透射电子显微镜 (TEM, JEM-3200FS) 和选区电子衍射 (SAED) 技术分别获取表层纳米晶的形貌与衍射信息。
选用HM101显微硬度仪测试距喷丸面不同深度的硬度值。每个深度处选取5个位置测量硬度并求平均值,为避免应变强化的影响,不同点位间的距离超过压痕对角线距离的5倍,所用载荷为20 g,加载时间为10 s。
选用CHI 660电化学工作站测试样品在室温下的开路电位-时间曲线 (OCP)、电化学阻抗谱 (EIS) 和极化曲线。将电化学工作站连接到三电极体系,工作电极为7075铝合金试样,对电极为Pt片,参比电极是Ag/AgCl电极,工作电极接触到电解质溶液的面积是1 cm2。根据需要,采用千分尺辅助打磨7075铝合金喷丸样品至一定厚度,最终以Al2O3镜面抛光收尾,研究喷丸样不同深度区域的电化学腐蚀行为。分别采用0.1 mol/L Na2SO4+20 mmol/L NaCl溶液 (为了得到明显的点蚀电位) 以及3.5% NaCl溶液为电化学腐蚀测试溶液。静置20 min等待体系稳定,然后进行开路电位-时间曲线测试,测试时间为1200 s。待OCP稳定后,进行EIS测试,选用频率范围为105~1 Hz,施加的电位扰动为±5 mV。使用ZView软件对EIS结果进行拟合。随后,进行极化曲线测试,扫描速率为0.3 mV/s。所有的电化学测试均在Faraday电笼中进行。
根据ASTM G110-92标准,在57 g/L NaCl+10 mL/L HCl (37%) 溶液中进行晶间腐蚀测试。室温下,将样品浸入溶液中分别浸泡6 h,之后用凯勒试剂侵蚀样品截面,以观察喷丸面和未处理面的晶间腐蚀形貌差异。
2 实验结果
2.1 金相组织
图2为不同冲击距离超声喷丸处理后的7075铝合金截面金相,其基体部分为拉长的纤维状晶粒,晶粒的平均宽度约为33.1 μm,其统计结果如图3所示。当冲击距离为40 mm (图2a和图d) 时,表层变形层厚度较小,晶粒的尺寸和排布方向未有明显的变化。随着冲击距离的减少,喷丸冲击能量增强,从图中可以看到,当冲击距离为25 mm (图2b和图e) 和15 mm (图2c和f) 时,合金表层形成了梯度结构,晶粒细化层厚度约为500 μm。当接近喷丸表面时,晶粒尺寸逐渐减小,且排布方向发生改变,由基体部分的纤维状逐渐向近表层的等轴晶随机排列转变。
图2 不同冲击距离的超声喷丸7075铝合金截面金相图片
图3 7075铝合金棒材的平均晶粒尺寸
2.2 XRD
图4给出了7075铝合金在超声喷丸处理前后的XRD结果。为了研究喷丸样在不同深度处的相组成变化,对冲击距离为15 mm的7075铝合金喷丸样分别打磨0、50、100、200、300和400 μm深度,然后进行XRD测试。可以看出,7075铝合金未处理样XRD结果显示出明显的棒材择优取向面(111),且未有(220)面和(311)面的峰出现。喷丸处理后的样品表面XRD结果与铝的计算结果接近,原因是超声喷丸处理后表层的粗大纤维状晶粒破碎并细化为纳米等轴晶。另外,若未处理样中的粗大析出相细化至尺寸过小,或是其回溶进基体,距喷丸表面越近时,代表η相和η′相(MgZn2)的衍射峰强度会逐渐降低,直至消失,如图4b。结合图5 TEM结果,未在表层观察到破碎后弥散分布的细小析出相,这表明在超声喷丸处理后,7075铝合金表层的时效析出强化相出现了回溶。
图4 7075铝合金棒材在超声喷丸处理前后的XRD
图5 超声喷丸处理后7075铝合金棒材表层约5 μm处的TEM结果
2.3 TEM
利用透射电子显微镜对喷丸处理后7075铝合金的表层纳米晶进行了表征。图5是冲击距离15 mm喷丸样在距表面约5 μm处的TEM明场像以及对应的选区电子衍射结果。从图5a中TEM明场像可以看到,经超声喷丸处理后,合金表面形成了纳米级别的等轴晶,未有尺寸较小的破碎析出相出现。统计得平均晶粒尺寸约为78.2 nm,如图5c所示。图5b中所示的明锐环状选区衍射花样也说明了纳米多晶体的形成,选区衍射的区域是图5a范围内的最大圆形部分。
2.4 硬度测试
图6显示了超声喷丸处理后7075铝合金的显微硬度在深度方向上的变化趋势。该试样的冲击距离为15 mm,最表层的显微硬度值约为203 HV,且随着深度的增加硬度逐渐降低。在深度约为1200 μm处,硬度降至168 HV左右,即7075铝合金基体的硬度。因此,该喷丸试样的表层硬化深度约为1200 μm。7075铝合金表层的喷丸强化机制将在讨论部分进行探讨。
图6 超声喷丸处理后7075铝合金棒材的硬度-深度曲线
2.5 电化学腐蚀测试
对7075铝合金棒材未处理样、冲击距离40与15 mm的喷丸样进行开路电位与极化曲线测试,结果如图7所示。为了获得明显的点蚀电位,采用0.1 mol/L Na2SO4+20 mmol/L NaCl溶液为腐蚀电介质[24, 25]。随着冲击距离的减少,冲击能量增加,7075铝合金的开路电位先正移后负移,同时自腐蚀电位变化趋势跟开路电位也相符合,这主要与超声喷丸处理引起的表层元素偏析有关[26]。相比于未处理样,喷丸样的点蚀电位都变得更正,说明7075铝合金耐点蚀诱发的能力得到了增强。然而,7075铝合金棒材在超声喷丸处理后的自腐蚀电流密度增大至未处理样的4倍以上,这是由于超声喷丸过程中不可避免地引入了外来杂质的缘故[27]。作者所在课题组在前期研究中确定外来杂质主要是非晶态的富含铁氧的混合物[28],且随着喷丸能量的提升,在样品表层引入的杂质含量越多。由表1可见,冲击距离为40 mm的7075铝合金喷丸样能量较小,引入的杂质较少,故相比于冲击距离为15 mm的喷丸样 (-0.42 VAg/AgCl),其点蚀电位更正 (-0.35 VAg/AgCl)。
图7 未处理样和不同冲击距离7075铝合金喷丸样在0.1 mol/L Na2SO4+20 mmol/L NaCl溶液中的开路电位-时间曲线与极化曲线
表1 未处理样和不同冲击距离7075铝合金喷丸样的极化曲线参数
为进一步研究外来污染以及表层组织改变对7075铝合金电化学腐蚀性能的影响,将超声喷丸处理样品从表面打磨至不同的深度 (0、50、100 μm),再分别进行开路电位、极化曲线以及EIS测试,腐蚀测试溶液为室温下的3.5% NaCl溶液。测得的开路电位-时间曲线和极化曲线如图8所示。与未处理区域相比,喷丸样表面具有更负的开路电位,随着更接近基体部分,开路电位逐渐正移。此外,从极化曲线中得到的自腐蚀电位的趋势与开路电位的趋势较为吻合。因此,若在喷丸处理后的表面出现了局部腐蚀,表层与次表层/基体之间会产生电偶作用,喷丸样的表面充当阳极,对合金基体提供阳极保护。从表2结果可知,相比于喷丸样表面 (1.6×10-7 A·cm-2),抛光去除50 和100 μm表层的样品的腐蚀速率均出现大幅度下降,这充分说明了外来杂质污染对喷丸样腐蚀行为的影响。相比于抛光去除50和100 μm表层的喷丸样品,7075未处理样的自腐蚀电流密度最小,这证明喷丸引起的组织变化加速了7075铝合金棒材在3.5% NaCl溶液中的腐蚀。
图8 7075铝合金未处理样和喷丸样在3.5%NaCl溶液中的开路电位-时间曲线和极化曲线
表2 7075铝合金棒材未处理样和喷丸样在3.5%NaCl溶液中极化曲线的参数
图9给出了EIS测试结果,其中图9a为Nyquist图,图9b和c为Bode图。图9d为EIS拟合所用的等效电路,其中,Rs为溶液电阻,CPE1为钝化膜对应的常相位角元件,Rpit为点蚀坑电阻,CPEpit为点蚀坑对应的常相位角元件,Rct为电荷转移电阻。采用上述等效电路拟合的EIS结果由表3给出。结果表明,喷丸处理后Rct数值减少,说明合金腐蚀速率升高,与极化曲线测得的自腐蚀电流密度变化趋势对应。此外,相比于喷丸样表面,打磨掉50 或100 μm后的样品的Rct数值增加,且随着深度的增加,Rct逐渐接近未处理样的对应数值。
图9 7075铝合金未处理样和喷丸样在3.5%NaCl溶液中的EIS结果
表3 图9中EIS的拟合结果
2.6 晶间腐蚀测试
晶间腐蚀测试后7075铝合金的截面腐蚀形貌如图10所示。在浸泡6 h后的未处理样 (图10a) 和喷丸样 (图10b) 中都观察到了剧烈的晶间腐蚀,且喷丸样的晶间腐蚀深度更深,从264 μm增加到292 μm。需要说明的是,6 h浸泡后合金的晶间腐蚀过于严重,表层已经形成了轻微的剥落腐蚀。为了更清楚地揭示喷丸处理对7075耐晶间腐蚀能力的影响,增加了浸泡2 h的实验组,此时样品表面都已有晶间腐蚀出现,但未形成剥落腐蚀,如图10b和d所示。可见,浸泡2 h后,喷丸样的平均晶间腐蚀深度为256 μm,而未处理样的平均晶间腐蚀深度为191 μm,且出现晶间腐蚀的区域面积更少。图10所示的结果充分说明,经超声喷丸处理之后,7075铝合金棒材的耐晶间腐蚀能力降低。
图10 7075铝合金在晶间腐蚀测试后的截面光镜形貌
3 讨论
3.1 表层强化机制
经超声喷丸处理后,7075铝合金棒材引入了多重强化机制,如细晶强化、加工硬化等,并在几种机制的协同影响下才最终决定了材料的强度。晶粒细化后的合金强度遵从Hall-Petch关系:
(1)
式中,σ为材料的强度,d为晶粒的尺寸,σ0为与材料相关的强度常数,k为常数,在超声喷丸处理后,表层区域的微米级晶粒破碎、细化,变为纳米等轴晶,即d减小,从而提高材料的强度。同时,喷丸处理在表层区域引入了高密度的位错缺陷,起到了加工硬化的作用。
众所周知,常规7075铝合金的高强度主要来源于时效析出强化效应。然而,XRD结果显示,喷丸处理过程中7075铝合金的强化析出相出现了回溶。超声喷丸处理后析出相的溶解可归因于Gibbs-Thomson效应[29]:
(2)
如 公式2所示,在一个溶质微粒A溶解到基体B中的过程中,γ是两者间的界面能,Vm是溶质B的摩尔体积,r是溶质微粒B的半径。当溶质微粒附近的基体具有高密度的各种缺陷时,如晶界、空位和位错,γ增加,从而ΔGγ 升高,根据摩尔自由能-组分关系图,B在A中的溶解度会增加。超声喷丸处理后,由于表层变为纳米晶,晶界增多,且位错密度增加,故析出相更倾向于回溶到铝基体中。原本存在的时效析出强化相的回溶对7075铝合金棒材来讲是一个软化因素,因此超声喷丸7075铝合金的表层硬度是细晶强化、加工硬化与析出相回溶软化效应互相竞争的结果。为了进一步提升超声喷丸处理对7075铝合金棒材的表层强化作用,可以考虑采用后续热处理的办法让时效析出相重新析出,且在重新析出的同时不会引起纳米晶的长大以及位错的回复。
3.2 腐蚀机理
超声喷丸处理后,7075铝合金抵抗点蚀萌生的能力增强,但极化曲线和EIS结果却显示出了腐蚀速率的增加。这可能是由于表面污染层的存在提升了喷丸样的腐蚀速率[28, 29]。已有研究表明,在超声喷丸处理过程会在材料表面引入其他杂质元素。我们课题组[27]发现,经超声喷丸处理之后的7150铝合金表面出现一层富含Fe和O的污染层,这些污染主要来自喷丸以及喷丸室内壁。由于污染层与铝基体之间的电偶作用,相对于未处理样,喷丸样的腐蚀速率增加。此外,对喷丸进行后续打磨抛光去除污染层,其电化学测试结果表明,当剔除污染层的干扰后,喷丸引起的组织改变并未降低7075铝合金棒材的电化学腐蚀速率。
IGC实验表明,超声喷丸处理后7075铝合金耐晶间腐蚀能力下降。这一结果与文献中超声喷丸7150[30]和7075铝合金[31]的结果不一致。本课题组[22]研究表明,超声喷丸处理造成的表层晶粒细化对于晶间腐蚀有双重作用:对于未处理样,其晶粒呈纤维状,被腐蚀后会出现较大直径的点蚀坑,喷丸处理后,由于表层纳米等轴晶的存在,其点蚀发生时间会比未处理样更慢,但是由于其点蚀坑直径更小,因此腐蚀产物容易堆积在腐蚀坑处,使得点蚀坑更加闭塞,一旦形成局部腐蚀,其扩展速率反而会被梯度纳米结构加速。超声喷丸处理时的能量会影响晶间腐蚀能力[22],高能喷丸处理可以全面抑制合金晶间腐蚀,而低能喷丸样的晶间腐蚀反而进一步加剧,会发展成为更深的针状点蚀坑。因此,超声喷丸处理后的7075铝合金耐晶间腐蚀能力下降可能是由于: (1) 超声喷丸处理所用能量不够。由于“双刃剑”作用的存在,喷丸能量较低时7075铝合金晶间腐蚀能力较弱,所以在使用超声喷丸处理调控7075铝合金的耐晶间腐蚀能力时,要注意选取合适的喷丸处理参数。(2) 超声喷丸处理过程中7075铝合金微观组织结构的改变不同于其他铝合金,未起到改善耐晶间腐蚀能力的作用。由于成分的不同,喷丸处理后晶内或晶界析出相以及晶界无沉淀析出带的行为也会有差异[32],若表层细晶层的晶界析出相以及晶界无沉淀析出带未有明显减少,喷丸处理将无法起到改善耐晶间腐蚀能力的作用。
4 结论
(1) 通过超声喷丸处理技术,在7075铝合金棒材粗晶样品上成功制备了表层晶粒尺寸约为78.2 nm的梯度纳米结构,且超声喷丸处理后,原本存在的时效析出强化相 (η和η′相) 回溶到铝基体中。
(2) 超声喷丸处理后,7075铝合金棒材的表层硬度由168 HV增加至203 HV,提升了约20%。表层硬度改变是细晶强化、加工硬化与析出相回溶软化效应互相竞争的结果。
(3) 超声喷丸处理后7075铝合金棒材的耐点蚀萌生能力增强,但其腐蚀速率增加,耐晶间腐蚀能力减弱。
参考文献
1 Yuan J, Pan S H, Zheng T Q, et al. Nanoparticle promoted solution treatment by reducing segregation in AA7034 [J]. Mater. Sci. Eng., 2021, 822A: 141691
2 Sun Q Q, Han Q Y, Wang S, et al. Microstructure, corrosion behaviour and thermal stability of AA 7150 after ultrasonic shot peening [J]. Surf. Coat. Technol., 2020, 398: 126127
doi: 10.1016/j.surfcoat.2020.126127
3 Yang W C, Ji S X, Zhang Q, et al. Investigation of mechanical and corrosion properties of an Al-Zn-Mg-Cu alloy under various ageing conditions and interface analysis of η′ precipitate [J]. Mater. Des., 2015, 85: 752
doi: 10.1016/j.matdes.2015.06.183
4 Knight S P, Birbilis N, Muddle B C, et al. Correlations between intergranular stress corrosion cracking, grain-boundary microchemistry, and grain-boundary electrochemistry for Al-Zn-Mg-Cu alloys [J]. Corros. Sci., 2010, 52: 4073
doi: 10.1016/j.corsci.2010.08.024
5 Chen S Y, Chen K H, Peng G S, et al. Effect of heat treatment on strength, exfoliation corrosion and electrochemical behavior of 7085 aluminum alloy [J]. Mater. Des., 2012, 35: 93
doi: 10.1016/j.matdes.2011.09.033
6 Amini S, Masic A, Bertinetti L, et al. Textured fluorapatite bonded to calcium sulphate strengthen stomatopod raptorial appendages [J]. Nat. Commun., 2014, 5: 3187
doi: 10.1038/ncomms4187 pmid: 24476684
7 Weaver J C, Milliron G W, Miserez A, et al. The stomatopod dactyl club: a formidable damage-tolerant biological hammer [J]. Science, 2012, 336: 1275
doi: 10.1126/science.1218764 pmid: 22679090
8 Liu Z Q, Meyers M A, Zhang Z F, et al. Functional gradients and heterogeneities in biological materials: Design principles, functions, and bioinspired applications [J]. Prog. Mater Sci., 2017, 88: 467
doi: 10.1016/j.pmatsci.2017.04.013
9 Dobrzański L A, Lukaszkowicz K, Paku?a D, et al. Corrosion resistance of multilayer and gradient coatings deposited by PVD and CVD techniques [J]. Arch. Mater. Sci. Eng., 2007, 28: 12
10 Sun D C, Ke L M, Xing L, et al. Self-propagating high-temperature synthesis of gradient transitional layer between ceramics and metal [J]. Trans. China Weld. Inst., 2000, 21(3): 44
10 孙德超, 柯黎明, 邢 丽 等. 陶瓷与多种梯度过渡层的自蔓延高温合成 [J]. 焊接学报, 2000, 21(3): 44
11 Pender D C, Padture N P, Giannakopoulos A E, et al. Gradients in elastic modulus for improved contact-damage resistance. Part I: The silicon nitride-oxynitride glass system [J]. Acta Mater., 2001, 49: 3255
doi: 10.1016/S1359-6454(01)00200-2
12 Colli A, Fasoli A, Ronning C, et al. Ion beam doping of silicon nanowires [J]. Nano Lett., 2008, 8: 2188
doi: 10.1021/nl080610d pmid: 18576693
13 Tong W P, Tao N R, Wang Z B, et al. Nitriding iron at lower temperatures [J]. Science, 2003, 299: 686
pmid: 12560546
14 Studart A R. Additive manufacturing of biologically-inspired materials [J]. Chem. Soc. Rev., 2016, 45: 359
doi: 10.1039/c5cs00836k pmid: 26750617
15 Ye Z Y, Liu D X, Li C Y, et al. Effect of shot peening and plasma electrolytic oxidation on the intergranular corrosion behavior of 7A85 aluminum alloy [J]. Acta Metall. Sin. (Engl. Lett.), 2014, 27: 705
doi: 10.1007/s40195-014-0104-9
16 Bagheri S, Guagliano M. Review of shot peening processes to obtain nanocrystalline surfaces in metal alloys [J]. Surf. Eng., 2009, 25: 3
doi: 10.1179/026708408X334087
17 Rakita M, Wang M, Han Q Y, et al. Ultrasonic shot peening [J]. Int. J. Comput. Mater. Sci. Surf. Eng., 2013, 5: 189
18 Huo W T, Hu J J, Cao H H, et al. Simultaneously enhanced mechanical strength and inter-granular corrosion resistance in high strength 7075 Al alloy [J]. J. Alloy. Compd., 2019, 781: 680
doi: 10.1016/j.jallcom.2018.12.024
19 Greiner C, Liu Z L, Schneider R, et al. The origin of surface microstructure evolution in sliding friction [J]. Scr. Mater., 2018, 153: 63
doi: 10.1016/j.scriptamat.2018.04.048
20 Lu K. Gradient nanostructured materials [J]. Acta Metall. Sin., 2015, 51: 1
doi: 10.11900/0412.1961.2014.00395
20 卢 柯. 梯度纳米结构材料 [J]. 金属学报, 2015, 51: 1
21 Pandey V, Singh J K, Chattopadhyay K, et al. Influence of ultrasonic shot peening on corrosion behavior of 7075 aluminum alloy [J]. J. Alloy. Compd., 2017, 723: 826
doi: 10.1016/j.jallcom.2017.06.310
22 Sun Q Q, Han Q Y, Xu R, et al. Localized corrosion behaviour of AA7150 after ultrasonic shot peening: Corrosion depth vs. impact energy [J]. Corros. Sci., 2018, 130: 218
doi: 10.1016/j.corsci.2017.11.008
23 Bao L, Li K, Zheng J Y, et al. Surface characteristics and stress corrosion behavior of AA 7075-T6 aluminum alloys after different shot peening processes [J]. Surf. Coat. Technol., 2022, 440: 128481
doi: 10.1016/j.surfcoat.2022.128481
24 Sun Q Q, Zhou W H, Xie Y H, et al. Effect of trace chloride and temperature on electrochemical corrosion behavior of 7150-T76 Al alloy [J]. J. Chin. Soc. Corros. Prot., 2016, 36: 121
24 孙擎擎, 周文辉, 谢跃煌 等. 微量Cl-和温度对7150-T76铝合金电化学腐蚀性能的影响 [J]. 中国腐蚀与防护学报, 2016, 36: 121
doi: 10.11902/1005.4537.2015.051
25 Sun Q Q, Chen Q Y, Chen K H. Link between pitting potentials and stress cracking corrosion susceptibility of 7150 Al Alloy with Different Ageing Processes [J]. Chin. J. Nonferrous Met., 2016, 26: 1400
25 孙擎擎, 陈启元, 陈康华. 不同热处理7150铝合金的点蚀电位与应力腐蚀敏感性 [J]. 中国有色金属学报, 2016, 26: 1400
26 Sun Q Q, Xu R, Han Q Y, et al. Long distance chemical gradient induced by surface nanocrystallization [J]. Appl. Mater. Today, 2019, 14: 137
doi: 10.1016/j.apmt.2018.12.002
27 Sun Q Q, Han Q Y, Liu X T, et al. The effect of surface contamination on corrosion performance of ultrasonic shot peened 7150 Al alloy [J]. Surf. Coat. Technol., 2017, 328: 469
doi: 10.1016/j.surfcoat.2017.08.028
28 Lin B, Zhang J Y, Sun Q Q, et al. Microstructure, corrosion behavior and hydrogen evolution of USSP processed AZ31 magnesium alloy with a surface layer containing amorphous Fe-rich composite [J]. Int. J. Hydrogen Energy, 2021, 46: 10172
doi: 10.1016/j.ijhydene.2020.12.132
29 Perez M. Gibbs-Thomson effects in phase transformations [J]. Scr. Mater., 2005, 52: 709
doi: 10.1016/j.scriptamat.2004.12.026
30 Sun Q Q, Cao F H, Wang S. Nanoscale corrosion investigation of surface nanocrystallized 7150 Al alloy in 3.5 wt% NaCl solution by using FIB-TEM techniques [J]. Corros. Sci., 2022, 195: 110021
doi: 10.1016/j.corsci.2021.110021
31 Beura V K, Karanth Y, Darling K, et al. Role of gradient nano-grained surface layer on corrosion behavior of aluminum 7075 alloy [J]. npj Mater. Degrad., 2022, 6: 62
doi: 10.1038/s41529-022-00271-z
32 Chao D Y, Sun Y Z, Liu X T, et. al . Effect of Zn/Mg ratio and aging temperature on precipitation behavior of Al-Zn-Mg-Cu aluminum alloy [J]. Mater. Rep., 2019, 33(suppl.2) : 398
32 晁代义, 孙有政, 刘晓滕 等. Zn/Mg比及时效温度对Al-Zn-Mg-Cu系合金析出行为的影响 [J]. 材料导报, 2019, 33(): 398
免责声明:本网站所转载的文字、图片与视频资料版权归原创作者所有,如果涉及侵权,请第一时间联系本网删除。
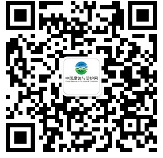
官方微信
《腐蚀与防护网电子期刊》征订启事
- 投稿联系:编辑部
- 电话:010-62316606
- 邮箱:fsfhzy666@163.com
- 腐蚀与防护网官方QQ群:140808414