CO2地质利用与封存环境下钢材腐蚀行为与腐蚀控制措施研究进展
2024-03-05 16:48:08
作者:腐蚀与防护 来源:腐蚀与防护
分享至:
随着全球工业的不断发展,大量以CO2为代表的温室气体被排入大气中,地球正经历日益严重的气候变暖过程。联合国政府间气候变化专门委员会(IPCC)在2021年度报告中指出:截至2019年,CO2的年平均质量浓度已达到410 mg/L,大气CO2浓度已达到200万年以来最大值;若不加以控制,将对自然生态系统和人类生活环境造成巨大威胁。CO2地质利用与封存(CGUS)技术是目前较为有效的CO2减排方式,其主要是通过工程技术手段将捕集的CO2注入地下,利用地质条件生产或强化能源、资源开采,同时实现注入CO2与大气长期隔绝的过程。在CGUS过程中,钢材腐蚀可能发生在CO2输送、驱油利用、咸水层封存等多个过程中,主要的腐蚀方式有金属管道腐蚀、井筒油管和套管腐蚀、设备阀门与井筒阀门腐蚀等,如图1所示。
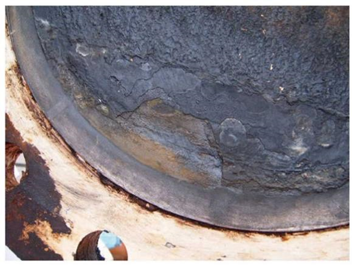
我国已有部分试验性和驱油用管道投入运行,在胜利油田、鄂尔多斯盆地、准噶尔盆地等地开展了规模化CGUS项目建设。为最大限度地减少CO2腐蚀导致的安全风险,开展CO2地质利用与封存环境下钢材腐蚀行为研究十分必要。
干燥的CO2本身并没有腐蚀性,但在储存、输送和利用过程中,不可避免地会接触水和其他杂质。当CO2溶于水后,其酸度往往比相同pH的盐酸更高,对钢材的腐蚀更严重。
相比于一般井下CO2腐蚀环境,为了提高CO2封存效率,CGUS过程一般向地下注入大量超临界态CO2,会在含水层中形成独立的超临界CO2相,并具有很高的分压(超临界CO2相分压一般在10 MPa以上)。在此条件下,CO2在水中的溶解度显著增加,形成具有强腐蚀性的碳酸溶液,极端条件下碳酸溶液的pH值可降至3以下,极大地增加了井下管柱发生腐蚀的风险,从而更容易导致泄漏等安全事故的发生。
考虑到CGUS技术的应用现状和发展前景,探明CGUS环境下的钢材腐蚀行为及机理,明确CO2腐蚀的影响因素,探究相应的防腐措施,对揭示钢材CO2腐蚀规律、规避CO2腐蚀风险、实现CO2减排,具有十分重要的现实意义。
CO2腐蚀钢材总的反应并不复杂,生成的腐蚀产物主要为FeCO3,其在一定条件下对钢材表面能够起到保护作用。溶解于水中的CO2会改变水溶液的化学性质,形成的H+、HCO3–、CO32–等离子会影响钢材腐蚀的电化学反应(包括阴极和阳极反应)。与单纯的强酸腐蚀和氧化腐蚀相比,CO2作用下钢材腐蚀的阴极和阳极反应过程更为复杂。
在CO2水环境下,阴极反应机制会受到溶液条件的影响。针对碳酸盐离子对阴极反应的影响,有直接还原和“缓冲效应”两种不同的反应机制。这两种机制并不相互排斥,但理清更适用于解释CO2对腐蚀影响的机制至关重要。
“缓冲效应”机制仅考虑H+的还原,H2CO3和HCO3–只是作为贮存H+的“容器”,随着H+的还原而减少,反应式如下:
而在直接还原机制中,H2CO3和HCO3–中的H+可能直接被还原,反应式如下:
Remita等使用电化学技术研究了与HCO3–离子相关的“缓冲效应”机制。他们开发了一个仅考虑H+还原和“缓冲效应”的模型,并利用该模型拟合了在不同转速、饱和与非饱和CO2溶液条件下的极化曲线,用于解释在饱和CO2溶液中测得较高极限电流的原因,从而证明了“缓冲效应”机制的合理性。
Kahyarian等使用了类似的方法来证实“缓冲效应”机制,他们的模型认为H+还原是唯一可能发生的阴极反应,其通量方程综合了腐蚀溶液中所有酸和碱的均相反应速率,能够预测CO2饱和溶液的动电位阴极极化(图2),从而得到钢材电化学腐蚀过程的动力学特征,包括腐蚀速率的确定、腐蚀控制因素的分析、腐蚀机理等。
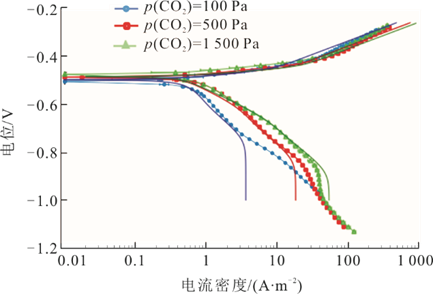
图2 API 5L X65低碳钢在10 ℃、0.1 mol/L NaCl溶液、 4.6 m/s流速、pH=6以及p(CO2)=100、500、1500 Pa条件下的极化曲线(实线为模型预测曲线)
直接还原机制通常用于解释在水溶液中CO2溶解量较大、浓度较高时具有较高腐蚀速率的现象。Nesic等人在另一项研究中指出,在含有CO2的水溶液中,腐蚀极限电流高于在相同pH值的HCl溶液中的腐蚀极限电流。他们将这种现象归因于金属表面上H2CO3的直接还原。
Gulbransen和Bilkova通过线性极化电阻(LPR)和失重法测量也发现,随着溶液中乙酸浓度的增加,即使阳极反应(Fe发生溶解)受到抑制,腐蚀速率依然会增加。他们也将这种现象归因于碳酸和乙酸的直接还原。
与阴极反应类似,阳极反应同样受到溶液条件的影响。在CO2存在的情况下,Fe溶解的阳极反应途径依然存在争议,特别是CO2在金属表面或其他中间产物表面上的吸附机制尚未完全阐明。确定阳极反应机制是预测腐蚀过程动力学的关键。Heusler和Bockris使用电化学技术研究了阳极反应过程,提出了催化机制(Heusler机制)和连续机制(Bockris机制)两种不同的机制。在催化机制中,生成的中间产物FeOHads与催化剂类似,能够加快Fe溶解的进程且自身没有发生变化,反应式如下:
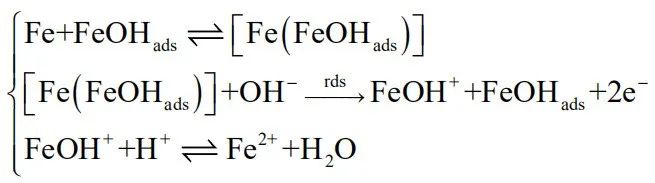
而在连续机制中,Fe的溶解被认为是一种连续的“序列”,中间产物FeOHads随着反应的进行会发生不可逆的变化,反应式如下:
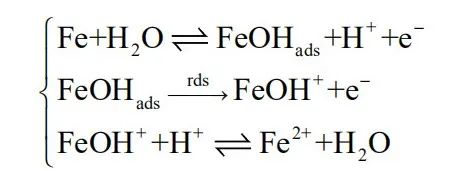
Kahyrian等同样研究了在不同CO2分压下CO2对阳极反应的作用,发现在不同CO2分压下测得的塔菲尔斜率系数略有不同。这证明了CO2参与了阳极反应。
溶解在水中的“碳”对电化学反应有重大影响。在pH值相同的情况下,由于直接还原或“缓冲效应”机制,CO2的存在会增加腐蚀速率。CO2分压越高,腐蚀电流越大。由于中间产物的复杂性和多样性,CO2在阳极反应中的作用尚未完全了解。目前来说,仍然需要利用电化学技术对CO2腐蚀钢材的阴极和阳极反应机制加以深入研究。
CGUS过程所面临的地层条件十分复杂,特别是在CO2注入后,会将环境改变为高CO2浓度、低pH的腐蚀性环境。与此同时,地层下的高温高压条件、杂质离子及气体、液体的流动冲刷等各项因素相互作用,将会影响甚至改变钢材的腐蚀过程。
CO2分压对钢材的腐蚀具有显著的影响,随着井下压力不断发生变化,CO2的相态也将发生相应的改变。在不同的相态下,钢材的腐蚀情况也有所不同。吴保玉等研究了在非临界、亚临界、超临界(6、7、8、10 MPa)3种工况下CO2/H2O体系中N80钢和J55钢的腐蚀行为。结果表明在超临界环境下,N80钢和J55钢的腐蚀速率均高于非临界环境,并且在超临界CO2/H2O体系CO2相和H2O相中,钢材的腐蚀类型不同。H2O相中,钢材以相对均匀的全面腐蚀为主;而CO2相中,钢材则表现为显著的局部坑蚀(图3)。压力不仅影响相态的改变,还会影响腐蚀产物的形成过程,并通过影响CO2的溶解度导致体系中H2CO3等物质的含量以及pH值发生变化,进而影响整个腐蚀过程。CO2在水中的溶解度随CO2分压的增加而显著增加。在大气压条件下,CO2在纯水中的溶解度仅为0.029 mol/kg(0.1 MPa,30 ℃);而在CGUS条件下,CO2分压可达10 MPa以上,对应的溶解度达到了1.361 mol/kg(10 MPa,30 ℃)。
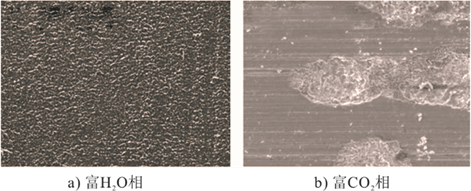
图3 超临界CO2/H2O体系在富H2O相和富CO2相环境下N80钢微观腐蚀形貌
CO2分压的变化会影响水与CO2的互溶度,从而改变腐蚀性物质的浓度,进而影响腐蚀过程。在相同的温度下,钢材在超临界CO2环境中的腐蚀速率要远远大于低压气态环境。这是因为在超临界状态下,CO2在水中的溶解度会迅速增大,造成超临界状态下水溶液中H2CO3、HCO3–、CO32–等腐蚀性介质的浓度增大,相应的阴极反应速率加快,最终加快腐蚀速率。与CO2在水中溶解度增大类似,在低压气态环境中,水在CO2中的溶解度远大于超临界环境。
Wei等计算出1 MPa时水在CO2中的溶解度约为10 MPa时的4倍,这说明低压时有较多的水分溶解于CO2中,只有少量水分凝结析出;而超临界环境下恰恰相反,大量的水凝结在钢材表面,其中的腐蚀性物质浓度远高于低压环境,因此腐蚀程度更严重。
相关研究表明,温度会改变钢材表面腐蚀产物膜的结构,进而影响腐蚀速率。在CGUS过程中,井下管柱的埋藏深度通常超过800 m,温度随着埋藏深度的增大可从常温升高至100 ℃左右,因此对该温度范围内钢材CO2腐蚀行为开展研究是发展CGUS技术的重要内容。李大朋等通过试验发现:在CO2分压4 MPa的条件下,温度较低时,N80钢的腐蚀产物晶粒粗大,堆垛较疏松,保护性较差;温度升高后,腐蚀产物膜更致密,腐蚀速率降低。张均生等也研究了不同温度对平均腐蚀速率和点蚀速率的影响。结果表明在30 ℃时,平均腐蚀速率与点蚀速率均处于较低水平;而随着温度的升高,平均腐蚀速率于60 ℃达到最大值,点蚀速率于90 ℃达到最大值;温度继续升高至120 ℃,腐蚀产物膜与基体间结合更加紧密,保护作用增强,腐蚀速率下降。李党国等利用交流阻抗技术研究了在模拟地层水中温度对钢材CO2腐蚀的影响。他们观察到:低温下出现了与双电层电容和传递电阻有关的高频容抗弧,对应于腐蚀产物膜活性溶解的中低频感抗弧和与腐蚀产物膜生成有关的低频容抗弧3个时间常数;随着温度的升高,感抗弧逐渐缩小直至消失,而低频容抗弧则逐渐扩大,有利于腐蚀产物膜的生成;传递电阻也逐渐增大,说明腐蚀产物膜的致密性增强,从而更好地保护基体,减小腐蚀速率。
就目前而言,针对CGUS环境中温度变化对CO2状态的改变、CO2与水的互溶度、钢材表面腐蚀机理等方面的研究并不多见,依然需要开展针对性的试验进行探究。
流速的变化会改变钢材表面腐蚀产物膜的结构性能,如致密程度、对钢材的保护作用等。高纯良等研究了流速对N80钢CO2腐蚀行为的影响,结果表明随着流速的增大,腐蚀产物膜的破坏加剧,保护性降低,腐蚀速率几乎呈指数形式增长。
李岩岩等发现,在超临界CO2环境中,流体流动加速了腐蚀性物质向钢材表面传质过程,同时对钢材表面施加了剪切应力,破坏了FeCO3膜的完整性和致密性(图4),从而加快了腐蚀速率。除此之外,流速变化还可能造成钢材的局部腐蚀。
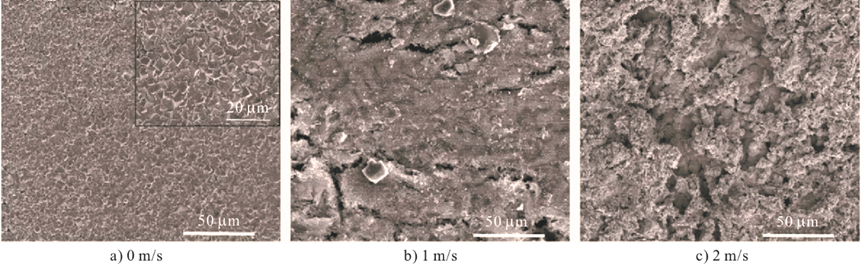
图4 N80钢在60 ℃、不同流速超临界CO2地层水中腐蚀24 h后的表面形貌
Schmitt等研究发现,当流体的流动速度或强度达到一定程度时,就能够抑制具有保护作用的腐蚀产物膜的再生,而局部腐蚀就会在腐蚀产物膜剥落的部位发生。
虽然目前已经明确了流速对钢材腐蚀会产生一定的影响,但针对高浓度CO2环境,特别是在环境条件十分复杂的地层作用下多相流对钢材腐蚀造成影响的研究并不多见,因此仍然需要进行大量的实验研究以探明在CGUS环境中流体流动条件下钢材的腐蚀行为及腐蚀机理。
随着石油和天然气需求量的不断增大,越来越多的非常规油气田被勘探和开采,由于这类油气田的矿化度较高,腐蚀性较强,CGUS应用风险也随之增大。目前的研究主要关注高矿化度采出水对钢材CO2腐蚀的影响。Dong等研究发现,随着矿化度的增加,X60钢腐蚀产物的形态和密度发生了改变,钢的表面腐蚀产物由松散变为致密,保护性增强。薛玉娜等采用电化学方法研究了CT80钢在高矿化度油井水中的腐蚀行为以及矿化度对腐蚀过程的影响。结果表明,随着矿化度的增大,CT80钢的开路电位正移,电荷传递电阻先减小后增大,在电阻最小时出现腐蚀速率最大值。出现这种结果,可能与溶液中的溶解氧有关。溶液的pH值是影响钢制管材腐蚀的重要因素。Wang等发现,随着pH值从6降至2,碳钢的腐蚀速率增加了近10倍。Pessu等研究了pH值对X65钢在CO2饱和盐水中点蚀行为的影响。结果表明,随着pH值的增大,X65钢表面的腐蚀产物由无保护性的Fe3C逐渐演变为具有保护作用的FeCO3,总的腐蚀速率也随之降低。
Deng等采用电化学方法研究了不同pH值对X80钢冲蚀行为的影响,发现随着pH值的增加,X80钢的自腐蚀电位负移,腐蚀电流密度呈逐渐减小的趋势,阻抗谱图的电容和电阻弧半径逐渐增大,总极化电阻增大,腐蚀速率降低,耐蚀性提高(图5)。
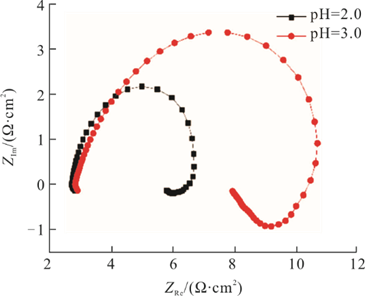
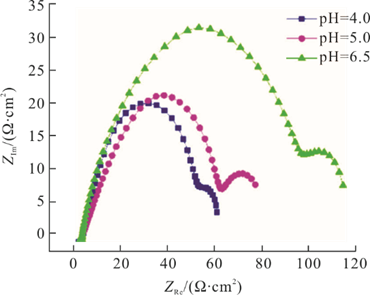
图5 X80钢在不同pH值下阻抗谱图
以上研究结果表明:在单一条件下,随着矿化度的增大,钢材的腐蚀速率随之加快;随着pH的增大,钢材的腐蚀速率随之减慢。但在多相条件下,两者对钢材CO2腐蚀的影响程度和影响规律依然没有达成统一的认识,还需要进一步的探究。
在CGUS过程中,想要得到单一的CO2环境是几乎不可能做到的。地层中往往含有一定量的水和腐蚀性杂质(如O2、SO2、H2S、NO2),这些杂质与H2O、CO2共同作用,对钢材造成更为严重的腐蚀。O2作为一种强氧化剂,它的存在(特别是当O2与CO2在水中共存时)会对钢材受CO2腐蚀产生影响。黄天杰等发现:当CO2/O2体系中CO2分压大于O2分压时,N80钢的腐蚀以CO2腐蚀为主,腐蚀产物膜的成分主要为FeCO3,产物膜呈晶态结构,具有较好的保护作用;而当O2分压较大时,则是以O2腐蚀为主,腐蚀产物膜的成分以Fe的氧化物为主,FeCO3只占少部分,产物膜疏松,几乎没有保护作用。孙永涛等的研究也得到了类似的结果:当CO2/O2体系中O2为微量时,起主导作用的是CO2腐蚀过程,CO2参与反应形成的FeCO3具有保护作用;而体系中存在O2时,生成的FeOOH或Fe2O3不具有保护作用。H2S通常来源于天然气生产及燃烧过程,是CGUS中常见的杂质成分。与CO2/O2相比,CO2/H2S体系中的腐蚀行为更为复杂。学者们认为在CO2/H2S体系中,CO2对腐蚀具有促进作用,随着其相对含量的增加,腐蚀过程将逐步转化为由CO2主导。而H2S既可以直接参与阴极反应,加剧CO2腐蚀;也可与Fe反应生成FeS膜,减缓腐蚀。因此在CO2和H2S共存的环境中,两者具有竞争或协同效应。目前针对CO2/H2S的研究,主要是从分压比这一因素切入,但现有的研究对两者主导腐蚀的分压比界限划分还没有统一的标准。Sridhar等认为:CO2/H2S的分压比大于200时(CO2主导腐蚀),CO2是主要的腐蚀介质,腐蚀速率与钢材表面生成的FeCO3膜的结构性能密切相关;CO2/H2S的分压比小于或等于200时(H2S主导腐蚀),H2S的存在会使钢材表面优先生成一层致密的FeS膜,从而阻碍FeCO3膜的生成,而这层FeS膜是否起保护作用则与温度和酸碱度有关。对于分压比界限的划分,Pots等持有不同的观点。他们认为当CO2/H2S的分压比小于20时,H2S控制腐蚀过程,腐蚀产物主要为FeS;当分压比处于20~500时,CO2与H2S混合交替控制腐蚀过程,腐蚀产物包含FeS和FeCO3;当分压比大于500时,CO2控制腐蚀过程,腐蚀产物主要为FeCO3。SO2同样会对钢材的腐蚀造成影响。其原因在于SO2与水反应后生成H2SO3,从而降低了体系的pH值。当上述体系中同时存在O2时,H2SO3进一步转化为H2SO4,从而造成更严重的腐蚀问题。相关研究表明,当O2、H2S、SO2、NO2这些腐蚀性杂质共存时,可能会相互反应,形成新的腐蚀性物质(如H2SO4、HNO3、S等),这些物质的存在会影响钢材的腐蚀进程。Barker等系统总结了各种杂质之间可能发生的作用及钢材在相应环境中的腐蚀机制,指出除了在溶液-钢材界面发生电化学腐蚀之外,O2、H2S、SO2、NO2之间还可以发生许多反应,但这些反应对腐蚀产生的影响仍不明确,还有待于进一步研究。除了气体之外,地层溶液中的一些离子同样影响钢材的腐蚀行为。当溶液中存在Cl-时,钢材的腐蚀速率会受到很大的影响。在通常情况下,Cl-会对钝化膜造成破坏,容易导致点蚀的发生。Zhang等人通过电化学技术研究了J55钢在NaCl/NaHCO3溶液中的点蚀行为,发现随着Cl-的加入,腐蚀速率增加。Liu等研究发现随着Cl-含量的增加,N80钢的腐蚀速率先增大后减小。在达到最大值之前,Cl-含量的增加加快了阳极反应速率,促进了腐蚀;而达到最大值后,Cl-含量的增加降低了CO2的溶解度,并对溶液中其他物质参与腐蚀反应产生影响,导致腐蚀速率降低。而当溶液中存在Ca2+和Mg2+时,两者可以降低CO2的溶解度,并产生CaCO3和MgCO3沉淀。由于CaCO3和MgCO3的晶体结构与FeCO3相似,Ca2+和Mg2+能够替代FeCO3结构中的Fe2+,这可能导致腐蚀产物层结构形态和保护性能的改变,从而影响CO2腐蚀钢材的机制。缓蚀剂是一种以适当的浓度和形式存在于环境中时,可以防止或减缓材料腐蚀的化合物或混合物。添加缓蚀剂是钢材腐蚀防护中较为有效和廉价的方法,特别是在石油天然气开采和运输过程中得到了广泛的应用。针对CO2腐蚀环境,研发的缓蚀剂主要有咪唑啉类缓蚀剂、有机胺类缓蚀剂、季铵盐类缓蚀剂3类。
目前,在能够抑制CO2腐蚀的缓蚀剂中,咪唑啉及其衍生物的用量是最大的。其分子结构主要包括含N的五元杂环(咪唑啉环)、R1基团和R2基团(图6)。赵景茂等研究了咪唑啉类缓蚀剂在CO2/H2S环境中的缓蚀效果,结果表明缓蚀效率可达86.8%。有机胺可以吸附在金属表面,抑制Fe氧化菌的生长,抵抗CO2和微生物双重腐蚀。
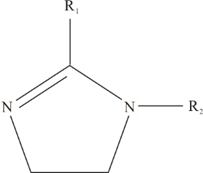
图6 咪唑啉类缓蚀剂基本结构
刘宏伟等研究了十二胺缓蚀剂对Q235钢的缓蚀效果,发现在静态条件下十二胺缓蚀剂的缓蚀效率可达93.44%;而在动态条件下,最低缓蚀效率也达到了87.93%,缓蚀效果较好。事实上,单组分缓蚀剂已经难以满足越来越苛刻的CO2腐蚀环境。因此,研究人员尝试将缓蚀效果显著的咪唑啉类缓蚀剂与其他缓蚀剂复配,从而得到缓蚀效果更好的缓蚀剂。咪唑啉季铵盐具有比单组份咪唑啉更好的缓蚀性能,特别是在高温高压CO2/H2S环境下,可形成性能稳定且不易分解的有机膜,具有较好的抗硫性能。Harris等研究了氯化二甲基苄基烃铵缓蚀剂对碳钢CO2腐蚀的影响,结果表明缓蚀剂的缓蚀效果受温度影响,在高温条件下,缓蚀剂的加入会破坏碳钢表面形成的FeCO3保护膜,造成缓蚀效率降低。因此,选择应用于高温条件的缓蚀剂时,应考虑其对腐蚀产物膜的影响,而关于这部分内容的研究还较为少见。
尽管缓蚀剂的研究已经取得了较多成果,但大多是在实验室较为理想的CO2腐蚀环境得到的结果,实际CO2腐蚀环境十分复杂,缓蚀机理需进一步加强。能够适应大多数CO2腐蚀环境的缓蚀剂尚未面世,想要开发出绿色高效且适用范围广的缓蚀剂仍然需要不断的探索。
涂层也是一种应用广泛的防腐措施。对于钢材而言,有机涂层和金属涂层具有优异的屏障性能与阴极保护性能,可以保护其免受腐蚀的危害。贾营坤等将高温热还原氧化石墨烯(TRGO)作为二维纳米填料添加到聚酰亚胺(PI)聚合物基质中,制备出了TRGO/PI纳米复合耐蚀涂层,其在海水中具有良好的腐蚀防护效果。蒋穹等制备出了热烧结铝锌硅合金涂层,其具有阴极保护作用,并且Al-Zn-Si合金延缓了涂层金属粉末的消耗,使牺牲阳极的腐蚀速率减慢。管铁鑫通过电化学技术测试了Fe基非晶涂层抗CO2腐蚀的能力,并与其他几种金属进行了比较,结果表明Fe基非晶涂层的抗CO2腐蚀能力显著高于316L和Cr13等耐蚀金属,具有优异的耐蚀性能。王珂等测试了两种涂层油管在油田CO2环境中耐蚀性能,结果表明与普通无涂层油管相比,内涂层油管的腐蚀速率远小于普通油管。
目前已经研制出的涂层种类繁多,且均具有良好的防腐性能,然而涂层的现场应用实例并不多见,原因可能在于涂层的制备成本较高,需要通过进一步的研究以降低其应用成本。此外,针对CGUS环境中用于保护钢材的防腐涂层研究还较为罕见,仍然需要通过大量实验对防腐涂层的成分、防腐机理等进行探究。
在含有CO2的腐蚀环境下,选用耐蚀性好的钢材往往能够有效地延缓或阻碍腐蚀。相关研究表明,在钢材中加入Cr元素能够显著提高其耐蚀性,且成本要低于同等级的传统碳钢。谢涛等对N80、L80、1Cr、3Cr、13Cr等5种不同材质油套管钢进行了CO2腐蚀试验发现,随着Cr含量的增加,油套管钢的腐蚀速率明显降低。Muraki等观察到Cr钢在形成腐蚀产物膜之前,其瞬时腐蚀速率高于碳钢,但随后便显著降低。他们认为发生这一现象的原因在于Cr钢表面形成了具有保护作用的腐蚀产物膜,提高了Cr钢的抗CO2腐蚀性能。Cr钢表面腐蚀产物膜的主要成分为Cr(OH)3和Cr2O3,其中Cr(OH)3能够阻碍FeCO3的形成,降低腐蚀产物膜中FeCO3的含量,使腐蚀产物膜变得致密,从而起到保护作用。大多数耐蚀合金,如钛合金、316合金、镍基合金等都含有Cr元素,并且每种耐蚀合金Cr元素含量及与其他合金元素含量的比例有所差异。这些合金在受到CO2腐蚀时,表面也会形成含有Cr元素的腐蚀产物层,并具有优良的抗CO2腐蚀性能。吕祥鸿等研究发现,TC4钛合金在含CO2地层水中处于钝化状态,随着温度的升高,其最大腐蚀速率仅为0.0012 mm/a。Firouzdor等研究了3种镍基合金在超临界CO2中的腐蚀行为,发现3种镍基合金均表现出优异的耐蚀性,并且三者的表面都有一层富Cr氧化物。综上所述,耐蚀合金抗CO2腐蚀性能已经得到证明,但对于Cr元素的添加量及其与其他合金元素含量的比例对钢材耐蚀性能的影响程度还不够明确,依然需要大量的实验进行深入研究。此外,在面对高浓度CO2的苛刻腐蚀环境时,可以将耐蚀合金与缓蚀剂或涂层结合使用,从而得到更好的抗CO2腐蚀效果。然而,目前关于这方面的研究鲜有报道,还有待于深入研究。
总体而言,目前针对CGUS环境中的CO2腐蚀钢材问题的研究仍然较少,在高浓度CO2腐蚀钢材机理、各项环境因素影响CO2腐蚀机制、CO2腐蚀防护技术等方面的研究仍然存在一定的局限性。基于上述局限性,总结了CGUS环境中钢材腐蚀方向的研究展望,具体包括:
(1) 当前对CO2腐蚀钢材的反应机制依然存在争议,特别是中间产物对阴极和阳极反应过程的影响尚未厘清,需要通过大量的实验进一步探究。(2) CO2腐蚀环境,特别是针对高浓度CO2多相流环境中的各项因素对CO2腐蚀的影响机制,以及它们共存时的协同作用和交互影响规律尚未完全阐明,需要大量的、系统的实验加以研究。(3) CO2腐蚀防护技术仍存在应用范围窄、成本偏高的局限,缓蚀剂及涂层的应用范围具有一定的局限性。如想实现大规模的应用,开发适用范围广、使用成本低、绿色高效的缓蚀剂将是今后研究的重点。此外,还需要对高压高浓度CO2等更为苛刻条件下的缓蚀剂与涂层的研发开展更加深入的研究。耐蚀合金的研发还不够充分,特别是对耐蚀合金中的耐蚀元素的含量及其对腐蚀程度的影响还需要继续研究。
免责声明:本网站所转载的文字、图片与视频资料版权归原创作者所有,如果涉及侵权,请第一时间联系本网删除。