摘要:为解决传统环氧富锌涂料锌粉含量过高导致的涂层起泡、缩孔、机械性能差等问题,对涂料配方进行优化筛选,并添加超高导电性的石墨烯,制备了一种高性能低锌粉含量环氧防腐涂料。并对涂层的附着力、耐冲击性、耐水性、耐中性盐雾性及耐湿热性等性能进行测试。结果表明:用19.35%环氧树脂E-20、2.15%聚酰胺加成物固化剂、45%锌粉、10%滑石粉、2%触变剂881B、1%流平剂AFCONA-3777、0.5%石墨烯、20%稀释剂2033,制备的环氧石墨烯低锌防腐涂料,涂层具有较高的耐冲击性(50 cm)、附着力(16 MPa)和优异的耐盐雾性(2000 h)、耐水性(2000 h)和耐湿热性(2000 h),可应用于苛刻腐蚀环境。
关键词:环氧富锌涂料; 石墨烯; 低锌; 防腐涂料; 高导电性;
环氧富锌涂料是重防腐涂料体系中常用的底漆之一,在国内外钢结构防腐中得到广泛的使用[1]。传统的环氧富锌涂料必须含有足够多的锌粉(≥78%),才能使涂层内形成良好的导电网络,对金属基材实现阴极保护作用[2]。然而锌粉含量过高,会使涂层多孔,引起横向共聚破坏(分层),导致机械性能降低。锌粉分散较为困难,也容易发生沉淀和结饼,这就需要增加溶剂的用量,造成环境污染[2,3]。另外,若为了增强涂层的防腐蚀能力而加厚涂层,便会使涂层在干燥过程中产生收缩,增加产生裂纹的倾向,反而使防腐蚀效果明显降低[4]。
石墨烯的电子迁移率高达15000 cm2/(V·s),比表面积高达2630 m2/g[5,6]。环氧富锌涂料中的石墨烯具有以下双重功能:其超高比表面积的片状结构在聚合物基质中发挥不可渗透的屏障作用[7];具有超高导电性,导通更多锌粉,增强富锌涂层的阴极保护作用。因此,石墨烯是减少锌粉用量、提高富锌涂层耐腐蚀性的理想材料[8,9]。
基于此,本研究对环氧富锌涂料的配方进行设计,通过添加微量的石墨烯粉体来提高涂层导电性,从而提高传统环氧富锌涂料的性能并降低锌粉的用量。
1 实验部分
1.1 主要原料及仪器
环氧树脂E-51(SM618)、环氧树脂E-06(NPES901):工业级,三木集团;环氧树脂E-20(SM607):工业级,南亚集团;3种环氧树脂基本技术参数如表1所示。
脂环胺、聚酰胺:工业级,科宁化工(中国)有限公司;腰果油改性固化剂、二乙烯三胺加成物、间苯二甲胺加成物、聚酰胺加成物:工业级,瀚森;石墨烯:3~10层,苏州格瑞丰;锌粉:球状,1 000目,长沙新威凌锌业发展有限公司;滑石粉:1250目,市售;流平剂(BYK-300):BYK;触变剂(有机膨润土881B):浙江青虹;流平剂(氟碳改性聚酯AFCONA-3777)、稀释剂2033:工业级,市售。
表1 不同环氧树脂的基本技术参数
QHQ型涂膜铅笔划痕硬度仪、QFZ型涂膜附着力试验仪、QTX型漆膜柔韧性测定仪、QCJ型漆膜冲击器:天津精科材料试验机厂;SH系列中性盐雾箱、SH-P-120T型湿热箱:东莞市升鸿检测仪器有限公司;CM-8855型电涡流式膜厚仪:武汉科瑞仪器设备有限公司。
1.2 实验方法
选用3种不同Mn的环氧树脂作为底漆的基料,以聚酰胺为固化剂。筛选出综合性能较优的树脂作为成膜物,再对几种环氧用胺类固化剂进行对比研究。确定树脂与固化剂的最优复配方案,在此基础上分批次加入不同的填料和助剂,逐步筛选出最优的填料、助剂的种类和比例。最终得到环氧石墨烯低锌涂料的最优配方。
1.3 涂料制备
环氧石墨烯低锌涂料的基础配方如表2所示。按照所述配比,首先加入环氧树脂,1200 r/min搅拌速度下,按配方分不同批次加入A组分中的石墨烯、锌粉、滑石粉和助剂,搅拌20~30 min后,倒入小型卧式砂磨机中,加入适量锆珠,研磨分散至细度<70μm,静置消泡。B组分为固化剂,接着按m(环氧树脂)∶m(固化剂)=9∶1加入固化剂,手动搅拌均匀后出料,得到所需涂料。
1.4 样板制备
采用空气喷涂法,在处理过的马口铁片和Q235钢板上喷涂制备好的涂料,表干后,先80℃烘烤15 min,然后升至120℃烘烤25 min,最后180℃烘烤30 min,即得到样板。
表2 高性能环氧石墨烯低锌涂料基础配方
涂层干燥时间、柔韧性和耐冲击性测试的样板采用打磨过的马口铁片(120 mm×50 mm×1 mm),干膜厚度为(20±3)μm;耐盐雾性、耐水性、附着力和耐湿热性测试用样板采用除油喷砂处理的Q235钢板(150 mm×70 mm×3 mm),干膜厚度为(150±30)μm。
1.5 性能测试
按照GB/T 1728—2020测试涂层干燥时间;按照GB/T 13452.2—2008测试涂层厚度;按照GB/T6753.3—1986测试涂料贮存稳定性;按照GB/T 5210—2006和GB/T 9286—2021测试涂层附着力;参考GB/T 1731—2020测试涂层柔韧性,采用曲率半径为1 mm的轴棒6测试,未观察到网纹、裂纹及剥落现象则为通过,否则为不通过,并记录涂层表面状态;参考GB/T 1732—2020测试涂层耐冲击性,采用1 kg重锤,测试高度50 cm,涂层不破损则为通过,否则为不通过,并记录涂层表面状态;参考GB/T 1733—1993中的浸水实验法测试涂层耐水性,测试时间为1 500 h,涂层无起泡、起皱、脱落现象则为通过,否则为不通过,并记录涂层表面状态;按照GB/T 1740—2007测试涂层耐湿热性;按照GB/T 1771—2007测试涂层耐中性盐雾性。
2 结果与讨论
2.1 树脂种类对涂层性能的影响
选用3种不同Mn的双酚A型环氧树脂作为底漆的基料,选用聚酰胺为固化剂。涂层的附着力、耐冲击性以及耐水性测试结果如表3所示。
表3 不同环氧树脂对涂层性能的影响
由表3可知,只有E-51树脂涂层出现裂纹,耐冲击性未通过。这是因为E-51树脂的Mn低,分子链最短,环氧基含量多,与胺类固化剂反应后,涂料交联密度大[10],导致涂层柔韧性下降,影响耐冲击性能[11]。其中E-06树脂涂层的耐水性测试未通过,这是因为具有较长主链的高Mn环氧树脂中含有更多羟基等亲水基团,交联密度低,耐介质性下降。因此,实验选择双酚A型中等Mn环氧树脂(E-20)作为成膜物质。
2.2 固化剂种类对涂层性能的影响
以E-20树脂作为成膜物,对几种环氧用胺类固化剂进行了对比研究,结果如表4所示。为快速筛选合适的固化剂,选用了较为快速的划格法测试涂层附着力。
从表4可以看出,只有使用聚酰胺和聚酰胺加成物作为固化剂的涂层通过了性能测试。并且聚酰胺与环氧树脂反应制成聚酰胺加成物固化剂后,涂层附着力显著提高,这是因为加入了环氧化合物进行扩链,并对聚酰胺进行加成封端,调节了固化剂的活性,进而控制成膜时的反应速度[12],使涂层对底材的附着力得到了改善。
表4 固化剂对涂层性能的影响
因此,确定E-20树脂与聚酰胺加成物固化剂的复配方案作为成膜物体系。
2.3 填料对涂层性能的影响
2.3.1 石墨烯
以上述得到的最优成膜物体系为基础,调整石墨烯质量分数为0、0.2%、0.4%、0.6%、0.8%,测试所得涂层耐盐雾性,结果如图1所示。
从图1可见,经过2000 h的中性盐雾试验,石墨烯质量分数为0.2%和0.8%的涂层已经出现了少量气泡,划叉区域扩蚀严重。而石墨烯质量分数为0.4%和0.6%的涂层划叉区域几乎无扩蚀,板面无起泡。当石墨烯质量分数较低时,涂层的耐腐蚀性随着质量分数增加有逐渐提高的趋势,这是因为石墨烯的二维片层结构和小尺寸使其在防腐涂料中形成致密的物理隔绝层,起到很好的物理隔绝作用。石墨烯的快速导电能力,也能使阳极反应产生的电子传递到涂层表面,阳极反应受到抑制,进而对金属表面进行保护[13,14]。
图1 不同石墨烯质量分数时涂层的耐中性盐雾性能
但是当石墨烯质量分数超过0.6%时,涂层的防腐性能出现下降的趋势,可能是体系中石墨烯过量,在涂层当中分布不均,出现团聚导致内部缺陷增多,反而加速腐蚀,影响了涂层的防护性能[16,17]。
石墨烯质量分数对涂层性能的影响如表5所示。
表5 石墨烯质量分数对涂层性能的影响
从表5可以看出,石墨烯质量分数的增加对耐冲击性并无明显的影响;加入石墨烯后涂层的拉开附着力出现了明显的提升,是因为石墨烯片层的共轭结构能够与基材产生范德华作用力[18],而石墨烯的质量分数对涂层耐水性能影响不大。结合图1和表5结果,石墨烯质量分数确定为0.4%~0.6%。
2.3.2 锌粉
在0.5%石墨烯质量分数条件下,考察涂料中的锌粉质量分数对涂层性能影响,结果如表6所示。
从表6中可以看出,锌粉质量分数为30%~55%的涂层,其耐冲击性和耐水性均通过,而附着力随着锌粉含量的增加出现下降的趋势,耐中性盐雾性随着锌粉含量的增加出现升高的趋势。附着力下降是因为当颜基比过高时,颜填料无法完全被树脂包裹,导致涂层和基材的结合力受到影响[19]。综合比较,45%~50%锌粉质量分数的环氧石墨烯锌粉涂料具有很好的综合性能,并且锌粉质量分数远低于传统环氧富锌涂料中的。后续实验中锌粉质量分数为45%。
表6 锌粉质量分数对涂层性能的影响
2.3.3 滑石粉
采用前段实验筛选出的最优条件,选用1250目超细滑石粉,研究其质量分数对涂层性能的影响,结果如表7所示。
表7 滑石粉质量分数对涂层性能的影响
由表7可知,随着滑石粉质量分数增加,涂层表面状态从逐渐平滑到出现橘皮,耐冲击性逐渐降低,但贮存稳定性得到提高。由于滑石粉具有特殊的层状结构和较大的径厚比,随含量增加,粒子在基体中分散性差而产生团聚现象,使涂层的耐冲击性降低[20]。贮存稳定性的提高是因为当质量分数增加时,滑石粉的体积占比和颗粒浓度增加,颗粒之间的相互作用力增强,从而降低了沉降的倾向性[21]。根据表7结果综合分析,可以确定滑石粉质量分数为7.5%~10%。后续实验中滑石粉质量分数为10%。
2.4 助剂对涂层性能的影响
2.4.1 触变剂
为解决填料导致的涂料沉底问题,加入触变剂有机膨润土881B。对触变剂质量分数进行研究,结果见表8。
表8 触变剂质量分数对涂料性能的影响
从表8中可以看出,在触变剂质量分数≤2%时,有机膨润土颗粒在涂料中分散较好,产生了良好的增稠、触变效应,当质量分数继续增加,部分颗粒可能产生聚集,反而影响体系黏度和流变性[22]。因此,触变剂最佳的质量分数为2%。
2.4.2 流平剂
研究了2种流平剂对涂层性能的影响,结果见表9。
表9 流平剂质量分数对涂层性能的影响
从表9可以看出,加入BYK-300(有机硅类型)对涂层的流平性和外观有很大的改善,但是当质量分数超过0.5%,涂层容易出现缩孔。使用AFCONA-3777(氟碳改性聚酯)对涂层流平性的改善稍弱于BYK-300,质量分数达到1%时流平效果良好,进一步增加对涂层外观无明显影响。
这是因为有机硅类流平剂能较好地改善前期流平,提高短波流平效果,但随着质量分数的增加,其与涂料相容性出现问题,且热稳定性不好,温度高于150℃时可能会发生分解而失去应有的特性,涂层外观效果反而下降[23]。氟碳改性类流平剂具有较好的表面状态控制能力,基材润湿性良好,防缩孔能力强,长波流平性好[24],所以随着AFCONA-3777用量的增加,涂层外观效果提高。考虑实际生产情况以及可能出现的层间结合力问题,选用质量分数1%的AFCONA-3777。
2.5 涂层综合性能
按上述最优配方制备涂料,其中固化剂采用聚酰胺加成物(H-0627锌黄固化剂),按m(环氧树脂)∶m(固化剂)=9∶1添加,按稀释剂用量20%计算,得到环氧树脂用量为19.35%,固化剂用量为2.15%。优化后的配方制备涂料后的性能测试结果如表10所示。
表10 环氧石墨烯低锌涂层主要性能
表10中的技术指标以HG/T 5573—2019为基础,按合作单位要求,耐水性、耐中性盐雾性和耐湿热性等指标更为严格。由表10可知,涂层性能均通过测试,可应用于苛刻腐蚀环境。
3 结语
(1)以双酚A型中等Mn的E-20环氧树脂为基料,以聚酰胺加成物为固化剂,控制环氧树脂和固化剂的质量比为9∶1,石墨烯、锌粉、滑石粉、触变剂、流平剂AFCONA-3777的质量分数分别为0.5%、45%、10%、2%和1%,研制出了高性能环氧石墨烯低锌防腐涂料。添加石墨烯不仅有效降低了锌粉用量,提高了涂层的耐中性盐雾性,增加了涂层与底材之间的附着力,还能延长保护期限,节约了重涂维修费用。
(2)所研制的环氧石墨烯低锌防腐涂料,具有较高的附着力(16 MPa)以及优异的耐中性盐雾性(2000 h)、耐水性(2000 h)以及耐湿热性(2000 h),可以在苛刻腐蚀环境下服役。
参考文献:
[1] SHI H W,LIU F C,HAN E H. The corrosion behavior of zinc-rich paints on steel:influence of simulated salts deposition in an offshore atmosphere at the steel/paint interface[J]. Surface and Coatings Technology,2011,205(19):4532-4539.
[2] 孙保库,姚家昌,陆阿定,等.水性环氧石墨烯锌粉涂料的研制[J].涂料工业,2021,51(5):43-50.
[3] 于晓辉,朱晓云,郭忠诚,等.鳞片状锌基环氧富锌重防腐涂料的研制[J].表面技术,2005,34(1):53-55.
[4] 金晓鸿,郑添水.鳞片状锌基环氧富锌底漆的研究[J].材料保护,1999,32(4):25-26.
[5] GERGELY A,P?SZTI Z,MIH?LY J,et al. Galvanic function of zinc-rich coatings facilitated by percolating structure of the carbon nanotubes. Part II:protection properties and mechanism of the hybrid coatings[J].Progress in Organic Coatings,2014,77(2):412-424.
[6] SHREEPATHI S,BAJAJ P,MALLIK B P,et al.Electrochemical impedance spectroscopy investigations of epoxy zinc rich coatings:role of Zn content on corrosion protection mechanism[J]. Electrochimica Acta,2010,55(18):5129-5134.
[7] ZHOU S G,WU Y M,ZHAO W J,et al. Designing reduced graphene oxide/zinc rich epoxy composite coatings for improving the anticorrosion performance of carbon steel substrate[J]. Materials&Design,2019,169:107694.
[8] 陈中华,李青,何畅.石墨烯的氧化程度和含量对水性锌粉涂料防腐性能的影响[J].涂料工业,2019,49(6):35-41.
[9] 刘佳明,洪研,吴雨晟,等.石墨烯对水性环氧富锌涂料中锌粉的取代能力研究[J].涂料工业,2020,50(1):14-19.
[10] 张显友,陈平.环氧树脂预聚物分子量对其固化物性能的影响[J].复合材料学报,1996,13(1):9-13.
[11] LIANG G Z,REN P G,ZHANG Z P,et al. Effect of the epoxy molecular weight on the properties of a cyanate ester/epoxy resin system[J]. Journal of Applied Polymer Science,2006,101(3):1744-1750.
[12] ZHOU T,ZHANG J,ZHAO J G,et al. In-situ grafted graphene oxide-based waterborne epoxy curing agent for reinforcement corrosion protection of waterborne epoxy coating[J]. Surface and Coatings Technology,2021,412:127043.
[13] DING J H,ZHAO H R,ZHOU M,et al. Super-anticorrosive inverse nacre-like graphene-epoxy composite coating[J].Carbon,2021,181:204-211.
[14] ZHANG R Y,YU X,YANG Q W,et al. The role of graphene in anti-corrosion coatings:a review[J].Construction and Building Materials,2021,294:123613.
[15] CUI G,BI Z X,ZHANG R Y,et al. A comprehensive review on graphene-based anti-corrosive coatings[J]. Chemical Engineering Journal,2019,373:104-121.
[16] 雒新亮,谭伟民,狄志刚,等.石墨烯水性环氧低锌防腐涂料的制备及电化学研究[J].涂料工业,2020,50(10):33-38.
[17] 梁宇,陈凯锋,张心悦,等.石墨烯改性环氧锌基防腐涂料的制备与性能研究[J].涂料工业,2019,49(9):30-34.
[18] 薛鹏,李文凯,胡秀东,等.石墨烯浆料在环氧锌粉复合防腐涂料中的应用[J].涂料工业,2017,47(11):59-62,76.
[19] SUN J Z,WEI X F,HUANG P Q,et al. Preparation of the plastic water-based gravure primary ink with high pigment[J].Advanced Materials Research,2012,380:15-19.
[20] 殷代武,谭卉文.滑石粉的应用特性及表面改性[J].广东化工,2013,40(18):75-77.
[21] 张婧,钱建刚,田佩秋.超细滑石粉的分散及其在水性涂料中的应用[J].涂料工业,2008,38(4):52-54.
[22] TAN Y F,HAO S Q,LI H W,et al. Effects of thixotropic agent and storage time on the rheological properties of epoxy resin[J]. Applied Mechanics and Materials,2012,217:582-585.
[23] 彭洪安.涂膜表面状态调节助剂的应用[J].涂料技术与文摘,2015,36(4):30-34.
[24] 向洪平,葛建芳,崔少伟,等.丙烯酸丁酯改性有机硅型流平剂的制备与性能研究[J].化工新型材料,2011,39(7):126-129.
免责声明:本网站所转载的文字、图片与视频资料版权归原创作者所有,如果涉及侵权,请第一时间联系本网删除。
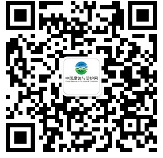
官方微信
《腐蚀与防护网电子期刊》征订启事
- 投稿联系:编辑部
- 电话:010-62316606
- 邮箱:fsfhzy666@163.com
- 腐蚀与防护网官方QQ群:140808414