摘要
Cr 涂层能够有效提高核电反应堆锆包壳管的事故容错能力,但在高温下其内部可能会萌生裂纹导致涂层开裂失效,现有 Cr 涂层开裂行为研究多针对常温,因此研究不同温度下 Cr 涂层的开裂行为对于其应用具有重要的理论和工程价值。采用多弧离子镀技术在 N36 锆合金包壳管外表面制备厚度为 14 μm 左右的 Cr 涂层,采用 WDW-100C 万能试验机对涂层管分别进行室温(25 ℃)与高温(100、200、300、400 ℃)拉伸试验,并通过超景深显微镜和扫描电镜(SEM)观察涂层的裂纹表面与截面形貌,对 Cr 涂层在不同温度下的开裂行为与开裂机理进行研究。结果表明,随着温度升高,涂层管的屈服强度从(400±5)MPa 下降到(150±5)MPa,涂层管的总体塑性变化不大;室温下裂纹萌生于涂层内部,其开裂方式为脆性沿晶断裂;100 ℃时涂层开裂方式不变,但表面裂纹数量减少,裂纹尖端出现钝化,由 V 字形转变为 U 字形; 随着温度进一步升高,涂层的塑性变形能力提高,其表面呈流线形塑性变形;200 ℃及以上温度下,涂层表面无明显开裂,仅出现少量微裂纹,塑性的升高导致拉伸过程中涂层的变形量与基体存在差异,裂纹开始萌生于界面处,其断裂方式也由脆性断裂转变为韧性断裂。采用单轴拉伸法研究温度对锆包壳 Cr 涂层开裂行为的影响,可为 Cr 涂层在核电领域的应用提供一定数据与理论支撑。
关键词: 变形温度 ; 锆合金 ; 铬涂层 ; 开裂行为
0 前言
包壳管是核反应堆中燃料元件的重要组成部分,也是核电站的第二道安全屏障,其作用是防止裂变产物逸散、保证燃料元件的整体性、避免燃料受冷却剂腐蚀及有效导出热能。锆合金由于具有良好的力学性能、耐腐蚀性能及低的中子截面吸收系数等,是目前核电反应堆中应用最广的核燃料包壳材料[1]。自福岛核事故之后,国际上对核燃料的研发重点由提高其可靠性和经济性转向增强其事故容错能力。同时,在锆包壳表面制备涂层也成为事故容错燃料(Accident tolerant fuel,ATF)的重点研发方向之一[2,3]。
Cr 具有不与水反应、高熔点、耐高温氧化、中子吸收截面适中、热膨胀系数与锆合金接近等特点,在锆包壳表面制备 Cr 涂层目前已成为国际公认的提升包壳管耐事故能力、简便易行且经济的方法[4-6]。近年来国内外针对锆包壳 Cr 涂层的研究主要集中在以下两个方面:一是 Cr 涂层的制备方法与工艺研究,二是 Cr 涂层在包壳管服役工况下的抗高温氧化性能研究。KIM 等[7-8]采用激光熔覆技术在 Zr-4 合金表面制备了大于 50 μm 厚的 Cr 基涂层,涂层组织致密,结合性能好,但其均匀性较差,涂层表面粗糙且热影响区较宽(100~200 μm)。PARK等[9]采用冷喷涂在锆合金表面制备了约 45 μm 厚的 Cr 涂层,通过优化工艺参数降低了涂层表面粗糙度,且涂层在 1 200℃的水蒸汽氧化试验中表现出良好的抗高温氧化性能,但用于喷涂的 Cr 粉制备成本相对较高,且涂层与基体的结合性能有待提高。 ZHONG 等[10]采用磁控溅射技术在 Zr-2 合金表面制备了 1 μm 左右的 Cr 涂层,结果表明,Cr 涂层可以有效减少基体的氧化,但涂层太薄,提供的保护能力有限。黄鹤等[11]将磁控溅射和多弧离子镀制备的 Cr 涂层进行对比,结果表明,多弧离子镀 Cr 涂层表面孔隙少,抗高温氧化性能明显优于磁控溅射 Cr 涂层。WEI 等[12]采用多弧离子镀在锆包壳表面制备 Cr 涂层,结果表明,锆包壳管的耐水热腐蚀性能及抗高温氧化性能得到显著提高。因此,根据现有研究可知,Cr 涂层可以有效提高锆包壳的抗高温氧化能力,且多弧离子镀技术是目前在锆包壳表面制备高质量 Cr 涂层理想的工艺方法。
然而,包壳管的工作温度在 300~350℃,Cr 涂层在服役过程中处于高温环境,在热应力的作用下可能在其内部会萌生微裂纹,从而导致涂层开裂失效,加速基体氧化。因此,针对锆包壳管 Cr 涂层的开裂行为研究也尤为重要。NGUYEN 等[13]通过原位拉伸试验对镀 Cr 锆合金的开裂行为进行研究,发现涂层中的第一道裂纹在 0.3%~0.4%的宏观应变下开始出现,且穿晶和沿晶裂纹都不会明显扩展到基体中。JIANG 等[14-15]对磁控溅射镀 Cr 涂层的锆合金试样进行拉伸试验和三点弯曲试验,研究 Cr 涂层中裂纹的初始位置和扩展行为及涂层的断裂韧性。结果表明,大多数裂纹最初形成在涂层和基体的界面处,随后随着拉伸应变的增加,裂纹垂直扩展到涂层表面,此外少量裂纹萌生于涂层表面的微缺陷处。Cr 涂层的断裂韧性为 65 J / m2,界面断裂强度和韧性为 150 MPa 和 200 J / m2。XU 等[16]建立了含有初始斜裂纹的锆合金 Cr 涂层整体模型,研究了裂纹长度、涂层厚度、初始裂纹倾角对裂纹扩展行为的影响。结果表明,与裂纹长度相比,涂层厚度对裂纹扩展的影响较小,裂纹扩展引起的涂层失效类型随初始裂纹倾角和初始裂纹长度的变化而变化。综上所述,针对 Cr 涂层开裂行为的现有研究大多针对常温,因此,Cr 涂层在高温环境下的开裂行为还仍有待研究[3,17]。
本文采用单轴拉伸法研究温度对锆包壳 Cr 涂层开裂行为的影响,以期为 Cr 涂层在 ATF 上的应用提供一定数据支撑。
1 材料与方法
1.1 涂层制备
采用多弧离子镀技术在锆合金管外表面制备 Cr 涂层,制备过程如图1 所示。
图1 多弧离子镀过程示意图
基体为长度 400 mm、外径 9.5 mm、壁厚 0.6 mm 的 N36 锆合金管(名义成分为 Zr-1Sn-1Nb-0.3Fe),靶材为纯度 99.99%的 Cr 靶,保护气为纯度 99.999% 的氩气。Cr 涂层的沉积参数见表1,沉积前用酒精和丙酮对基体进行清洗,完成后放入炉腔进行等离子体清洗,再进行离子轰击镀膜(制备打底层),最后沉积 Cr 涂层。制备打底层的偏置电压提高至 500 V,其余参数与 Cr 涂层沉积参数相同,其目的在于提高功率使晶粒细化,增强涂层与基体之间的结合力。
表1 Cr 涂层沉积参数
1.2 拉伸试验
拉伸试验在 WDW-100C 万能试验机上进行,试验温度分别为 25、100、200、300、400℃,每种温度重复 3 次,拉伸应变速率为 0.002 / s。拉伸试样设计如图2 所示,考虑到管状样品夹持问题,在锆包壳 Cr 涂层管(简称涂层管)两端各加总长度为 30 mm 的塞头,以防止夹持端变形对拉伸过程产生影响。
图2 拉伸试样与塞头尺寸示意图
1.3 表征与分析
采用 LY-WN-YH600 超景深显微镜观察涂层拉伸试验后裂纹宏观形貌,采用 FEI Nova Nano SEM 400 型场发射电子显微镜观察拉伸试验后涂层的表面、截面微观形貌,并对涂层拉伸断口形貌进行分析。
2 结果与分析
2.1 原始涂层形貌
Cr 涂层的原始形貌(未拉伸)如图3 所示。由图3a 可知,涂层表面均匀、连续,同时在表面可以明显观察到部分大颗粒存在,这是多弧离子镀沉积样品的典型特征,其产生原因是在高能粒子轰击下,熔融的金属液滴飞溅并沉积在基体上凝固成大颗粒。由图3b 可知,涂层内部成形良好,致密且无明显气孔和裂纹等缺陷。涂层与基体之间结合较好,结合区平整无明显缺陷,证明多弧离子镀技术及工艺参数选择合适,涂层平均厚度为 14 μm 左右。
图3 Cr 涂层原始形貌
2.2 拉伸试验结果
涂层管在 5 种温度下的拉伸应力应变曲线与拉伸结果对比(包括断后延伸率、屈服强度及抗拉强度,屈服强度及抗拉强度的误差较小,因此误差棒在图中不明显)如图4 所示,其中室温与高温拉伸的屈服强度以规定塑性延伸强度 Rp0.2 计算。
由图4b 可知,室温下涂层管具有最高的屈服强度(376 MPa)与抗拉强度(506 MPa)。随着温度升高,涂层管的屈服强度与抗拉强度几乎呈线性下降,在 400℃时达到最低,分别降至 146 MPa 与 250 MPa。在各个温度下,涂层管的延伸率稳定在 40%左右,整体波动不大。不同温度下的拉伸结果表明温度主要影响涂层管的强度,对整体的塑性影响不大,说明高温下涂层管的塑性主要受基体材料的影响,即使 Cr 涂层的塑性提高,但因为涂层较薄,对样品整体塑性的影响较小。根据以往工作经验可知,随着涂层厚度的增加,涂层管的屈服强度和抗拉强度都增加,但是涂层厚度超过 20 μm 时,其断后延伸率有所下降。然而涂层厚度低于 10 μm 时,它对包壳管的保护作用不足,因此合适的涂层厚度范围在 10~20 μm。
图4 不同温度下的拉伸试验结果
2.3 涂层表面裂纹形貌
2.3.1 裂纹宏观形貌
涂层管在不同温度下拉伸断口位置处的表面裂纹宏观形貌如图5 所示。室温与高温拉伸后断口附近涂层与基体结合良好,且均未出现大面积剥落,表现出优异的膜基结合力。由图5a 可知,室温下涂层管表面观察到大量垂直于拉应力方向的环形裂纹,且裂纹密度最大。相邻两条裂纹之间的宽度(简称裂纹宽度)较小,平均裂纹宽度约 230 μm,单条裂纹开口平均约 16 μm。除完整的环形裂纹外,在两个相邻裂纹间有新的裂纹,由于 Cr 涂层晶界的阻碍作用,并未沿周向扩展形成完整的环形[18]。由图5b 可知,当温度升高至 100℃时,涂层表面裂纹数量大幅度减少,同时裂纹宽度增大到约 500 μm,单条裂纹开口增大到约 65 μm,这表明 100℃下 Cr 涂层的塑性变形能力与抗裂性能较其在室温下有一定提升。如图5c~5e 所示,在 100℃以上温度下,涂层表面无法观察到具有明显方向性的裂纹,只在靠近断口位置附近出现少量微裂纹,裂纹相对较小且分离,不是细长而平行。
图5 涂层管断口处表面裂纹宏观形貌
2.3.2 裂纹微观形貌
涂层管在不同温度下拉伸断口位置表面裂纹微观形貌如图6 所示。SEM 拍摄时,将样品倾斜 30~45°可同时观察到涂层表面、涂层晶粒形貌、表面裂纹,以及裂纹间隙较大时暴露的基体。
图6 不同温度拉伸后涂层表面微观形貌
如图6a 所示,室温下锆合金基体存在大量韧窝,呈现典型的韧性断裂特征,表明基体的塑性较好,与 2.2 节的拉伸试验结果吻合。涂层的组织为垂直于基体表面的柱状晶,且与基体结合良好,在室温下呈脆性沿晶断裂。在图6b 中,100℃下涂层表面的裂纹数量减少,且开裂方式保持不变。当温度升高到 200℃时,如图6c 所示,涂层表面的裂纹形貌与室温下不同,断口附近裂纹(箭头处)呈扁平状且长度减小,由于裂纹尺寸较小且开口处边缘较为圆润,未观察到明显的涂层边缘晶粒形貌。由于严重的塑性变形,涂层表面呈现出流线形,与 KUMAWAT等[19]研究的Si-Fe-Cr涂层高温拉伸后的表面形貌类似,这也说明随着温度升高,涂层的塑性提高,其开裂方式逐渐由脆性断裂转变为韧性断裂。如图6d 所示,300℃下涂层有更好的塑性变形能力,随着持续施加拉伸载荷,其表面出现微裂纹,裂纹开口在 3~10 μm,同时还观察到两个相邻的微裂纹之间通过相互扩展发生聚集。如图6e 所示,裂纹开口随着温度升高逐渐减小,400℃时,裂纹开口减小至 1 μm 左右。
2.4 涂层截面裂纹形貌
为了进一步研究涂层在拉伸作用下的开裂行为,对涂层距断口 10 mm 处平行于拉伸方向的截面进行观察分析,图7 为室温与高温拉伸后涂层截面的微观形貌。如图7a 所示,室温下由于涂层的断裂韧性较低,裂纹贯穿了整个涂层且扩展至基体,在拉伸试验后期基体表面裂纹作为裂纹源最终导致试样断裂。由于良好的界面结合力,裂纹未在界面处横向扩展。此外,在涂层内部还存在部分微小孔洞,这些孔洞对涂层的保护性能不利,这可能是表面宏观裂纹的起裂位置。如图7b 所示,100℃下拉伸后涂层裂纹截面呈 U 字形,其裂纹尖端形状与常温下的 V 字形相比出现了钝化,且向基体扩展的深度减小。
图7 不同温度拉伸后涂层截面微观形貌
如图7c~7e 所示,高温下涂层截面均未形成纵向贯穿裂纹,而是只在涂层内部出现与常温下相同的微小孔洞。值得注意的是,200℃时,孔洞开始出现在涂层与基体的界面位置(圆圈处),随着温度升高,涂层内部孔洞的数量减少,而界面处孔洞的尺寸逐渐增大。温度升高至 400℃时,涂层内部孔洞最少且在界面处形成了微裂纹,这些微裂纹可能沿纵向扩展至基体内部与涂层表面,最终导致样品断裂。
2.5 涂层开裂机理分析
基于上述试验结果进行分析,如图8 所示,在不同温度下,Cr 涂层的裂纹的萌生位置与扩展行为存在显著差异。室温下锆包壳表面多弧离子镀 14 μm Cr 涂层的膜基体系是一种典型的脆性涂层韧性基体体系,在拉伸载荷作用下,涂层发生脆性断裂。涂层在制备过程中可能存在部分细微缺陷,拉伸过程中缺陷位置容易造成局部应力集中,使得涂层柱状晶粒变形破碎[20],而其他晶粒在室温下的塑性变形能力不足,最终表现为在涂层内部形成平行于拉伸方向的微小孔洞。当应力增大到超过涂层的抗拉强度时,微裂纹便从孔洞或其他薄弱晶界处产生,同时涂层横向存在较多不同方向的晶界会阻碍裂纹的扩展,而涂层单个柱状晶在纵向上提供了一个几乎贯穿整个厚度方向上的晶界,因此微裂纹沿着涂层柱状晶界扩展至表面形成宏观裂纹。裂纹到达涂层表面后,相邻位置裂纹聚集生长,逐渐形成环形裂纹。而裂纹扩展至膜基界面后,会因为涂层结合性能的不同出现不同扩展方向,一是涂层结合性能很差时,裂纹沿着膜基界面扩展,使膜基界面分层,甚至导致涂层剥落;二是涂层结合性能一般时,涂层裂纹既向基体扩展也沿界面扩展;三是涂层结合性能较好时,涂层裂纹扩展至基体,室温下 Cr 涂层则为第三种情形。
图8 涂层裂纹萌生与扩展示意图
温度升高至 100℃时,由于涂层塑性提升,涂层在拉伸过程中通过增加变形来释放涂层中的应力,从而阻碍了涂层中新裂纹的形成,如图5b 所示,因此涂层表面裂纹密度大幅下降,同时随着拉伸载荷的持续和非弹性变形的积累,单条裂纹开口增大。由于涂层裂纹向基体的扩展深度会受到裂纹扩展速率的影响,裂纹扩展速率越高,其裂纹初始驱动力越大,向基体扩展的深度就越大。因此,在 100℃ 下,涂层塑性提高,裂纹在涂层内的扩展速率降低,裂纹向基体扩展的驱动力减小,最终导致向基体扩展的深度减小。此外裂纹在基体中扩展时,其尖端产生大量塑性变形,消耗驱动能量,直至裂纹不再扩展,而 100℃下涂层裂纹提供的驱动力小,基体裂纹止裂后随着应变增大,裂纹深度不再改变,而是裂纹间隙变大,裂纹尖端基体发生塑性变形,导致裂纹尖端钝化[21-22]。然而,此时涂层塑性提升有限,涂层还是表现出脆性断裂。
温度达到 200℃及以上时,Cr 涂层的塑性变形能力得以进一步提高,表面宏观裂纹消失,此时涂层则会在拉应力和颈缩产生的环向应力的作用下发生塑性变形,一方面表现为涂层厚度随着温度升高不断减小,另一方面表现为涂层表面变得粗糙,呈现出显著的塑性流动行为,这也表明 Cr 涂层的韧脆转变温度在 100~200℃。此时,涂层晶粒拥有更大的塑性变形能力,在外力作用下能够及时填补空缺,因此随着温度升高涂层内部的孔洞数量减少。同时根据拉伸试验结论,基体的塑性在不同温度下的变化不大,而 200℃下涂层更好的塑性以及抗裂能力使得涂层与基体变形量出现差异,在剪切应力的作用下孔洞开始在界面处形成。随着温度升高,界面处的孔洞尺寸逐渐增大,最终在 400℃下,界面处形成微裂纹且向基体扩展,此时,Cr 涂层的塑性与抗裂性能已经高于基体,界面裂纹的产生释放了涂层与界面间的剪切力与涂层内部应力,有效阻碍了涂层中新裂纹的形成,因此 400℃时涂层内部孔洞数量最少,同时表明高温下 Cr 涂层对锆合金基体的裂纹萌生具有抑制作用,能够有效延长锆合金包壳管的使用寿命。
本文探究了不同温度对于 Cr 涂层开裂行为的影响,此外,涂层的厚度也是影响涂层开裂行为的因素之一。根据前文的分析,室温下 Cr 涂层主要表现出脆性断裂特征,随着涂层厚度增加,涂层脆性增大,晶粒的塑性变形能力不足以抵抗外部拉应力。因此,室温下涂层管断裂后其表面裂纹数量以及裂纹向基体扩展的深度,应随着涂层厚度增加而不断增加。高温下涂层的塑性提高,不同厚度涂层的塑性提升不尽相同,因此其开裂行为有待进一步研究。
3 结论
(1)通过对镀 Cr 涂层的锆合金包壳管进行单轴拉伸试验研究 Cr 涂层在不同温度下的开裂行为,弥补了 Cr 涂层在不同温度下力学性能方面研究的空缺。
(2)研究不同温度下 Cr 涂层表面和截面的裂纹形貌,并从裂纹的微观特征来解释 Cr 涂层的开裂机理,为 Cr 涂层在 ATF 的实际工程应用提供了一定的理论支撑。
(3)只对固定厚度的 Cr 涂层断裂后的表面和截面的开裂情况进行观察与分析,拉伸过程中以及不同厚度涂层在不同温度下的开裂行为仍有待进一步研究。
参考文献(共22条):
[1] YANG J,STEINBRÜCK M,TANG C,et al.Review onchromium coated zirconium alloy accident tolerant fuelcladding[J].Journal of Alloys and Compounds,2022,895:162450.
[2] ZINKLE S J,TERRANI K A,GEHIN J C,et al.Accidenttolerant fuels for LWRs:A perspective[J].Journal ofNuclear Materials,2014,448(1-3):374-379.
[3] CHEN H,WANG X,ZHANG R.Application anddevelopment progress of Cr-based surface coatings innuclear fuel element:I.selection,preparation,andcharacteristics of coating materials[J].Coatings,2020,10(9):808.
[4] KAM D H,LEE J H,LEE T,et al.Critical heat flux forSiC-and Cr-coated plates under atmospheric condition[J].Annals of Nuclear Energy,2015,76:335-342.
[5] PARK J,KIM H,PARK J,et al.High temperaturesteam-oxidation behavior of arc ion plated Cr coatings foraccident tolerant fuel claddings[J].Surface and CoatingsTechnology,2015,280:256-259.
[6] 王永利,刘实,熊良银.磁控溅射法制备锆合金包壳Cr涂层[C]//中国核学会2019年学术年会,包头,2019-08-20.北京:中国原子能出版社,2019.
WANG Yongli,LIU Shi,XIONG Liangyin.Zirconiumalloy cladding tube Cr coating prepared by magnetronsputtering method[C]//2019 Annual Conference of theChinese Nuclear Society,Baotou,Inner Mongolia,China,2019-08-20.
Beijing:China Atomic Energy Press,2019.(in Chinese)
[7] KIM H,KIM I,JUNG Y,et al.Adhesion property andhigh-temperature oxidation behavior of Cr-coatedZircaloy-4 cladding tube prepared by 3D laser coating[J].Journal of Nuclear Materials,2015,465:531-539.
[8] KIM H,YANG J,KIM W,et al.Development status ofaccident-tolerant fuel for light water reactors in Korea[J].Nuclear Engineering and Technology,2016,48(1):1-15.
[9] PARK D J,KIM H G,IL JUNG Y,et al.Behavior of animproved Zr fuel cladding with oxidation resistant coatingunder loss-of-coolant accident conditions[J].Journal ofNuclear Materials,2016,482:75-82.
[10] ZHONG W,MOUCHE P A,HEUSER B J.Response ofCr and Cr-Al coatings on Zircaloy-2 to high temperaturesteam[J].Journal of Nuclear Materials,2018,498:137-148.
[11] 黄鹤,邱长军,陈勇,等.锆合金表面磁控溅射与多弧离子镀Cr涂层的高温抗氧化性能[J].中国表面工程,2018,31(2):51-58.
HUANG He,QIU Changjun,CHEN Yong,et al.Hightemperature oxidation resistance of magnetron sputteringand multi-arc ion plating Cr films on zirconium alloy[J].China Surface Engineering,2018,31(2):51-58.(inChinese)
[12] WEI T,ZHANG R,YANG H,et al.Microstructure,corrosion resistance and oxidation behavior of Cr-coatingson Zircaloy-4 prepared by vacuum arc plasmadeposition[J].Corrosion Science,2019,158:108077.
[13] NGUYEN D V,Le SAUX M,GÉLÉBART L,et al.Mechanical behavior of a chromium coating on a zirconium alloy substrate at room temperature[J].Journalof Nuclear Materials,2022,558:153332.
[14] JIANG J,ZHAI H,GONG P,et al.In-situ study on thetensile behavior of Cr-coated Zircaloy for accidenttolerant fuel claddings[J].Surface & Coatings Technology,2020,394:125747.
[15] JIANG J,YUAN M,DU M,et al.On the crackpropagation and fracture properties of Cr-coated Zr-4alloys for accident-tolerant fuel cladding:In situthree-point bending test and cohesive zone modeling[J].Surface & Coatings Technology,2021,427:127810.
[16] XU Z,WEI J,LIU Y,et al.The effect of oblique crack onstability and fracture properties of Cr-coated Zircaloycladding[J].Annals of Nuclear Energy,2021,163:108560.
[17] CHEN H,WANG X,ZHANG R.Application anddevelopment progress of Cr-based surface coating innuclear fuel elements:II.Current status and shortcomingsof performance studies[J].Coatings,2020,10(9):835.
[18] JIANG J,ZHAN D,LV J,et al.Comparative study on thetensile cracking behavior of CrN and Cr coatings foraccident-tolerant fuel claddings[J].Surface & CoatingsTechnology,2021,409:126812.
[19] KUMAWAT M K,ALAM M Z,KUMAR A,et al.Tensile behavior of a slurry Fe-Cr-Si coated Nb-alloyevaluated by gleeble testing[J].Surface & CoatingsTechnology,2018,349:695-706.
[20] 吴艳青,施惠基,牛莉莎.超塑性变形晶界效应研究综述[J].力学进展,2005,35(4):525-540.
WU Yanqing,SHI Huiji,NIU Shali.A review on grainboundary effects in superplasticity[J].Advances inMechanics,2005,35(4):525-540.(in Chinese)
[21] 热障涂层裂纹扩展的数值模拟研究进展. 胡忠超;王亮;庄铭翔;张桓瑜;李广书;王铀;杨勇.中国材料进展,2020
[22] High temperature steam-oxidation behavior of arc ion plated Cr coatings for accident tolerant fuel claddings. Jung-Hwan Park;;Hyun-Gil Kim;;Jeong-yong Park;;Yang-Il Jung;;Dong-Joon Park;;Yang-Hyun Koo.Surface & Coatings Technology,2015
免责声明:本网站所转载的文字、图片与视频资料版权归原创作者所有,如果涉及侵权,请第一时间联系本网删除。
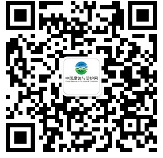
官方微信
《腐蚀与防护网电子期刊》征订启事
- 投稿联系:编辑部
- 电话:010-62316606
- 邮箱:fsfhzy666@163.com
- 腐蚀与防护网官方QQ群:140808414