引 言 镁合金具有密度低、力学性能良好、比强度高、比刚度高、尺寸稳定性好、导热导电性能优良等优点。镁合金(ZM5)作为结构材料在航空航天、汽车工业领域中被广泛应用,尤其是发动机附件机匣、减速机匣均由镁合金制成。但是镁合金制件耐腐蚀性差,尤其是在盐水、清洗液环境下出现严重电化学腐蚀,有的深度达到3mm,带来很大的安全隐患。 目前镁合金制件发生腐蚀后采取冷喷涂金属复合涂层修复或直接报废处理。冷喷涂金属复合涂层修复后整体寿命较短,抗腐蚀效果不明显,而且涂层与镁合金会发生严重的电偶腐蚀;直接报废处理会造成很大的经济损失。本研究针对上述存在问题和不足,提出了用防腐底漆和修补腻子修复镁合金(ZM5)制件腐蚀坑的方法。
针对镁合金制件存在较大、较多腐蚀坑的现象,本研究提出如下修复工艺:
腐蚀坑打磨处理→化学氧化处理→喷涂防腐底漆(20~30 µm)→凹坑处刮涂腻子→表面打磨→喷涂防腐底漆(20~30 µm)→成品(修复涂层厚度40~60 µm)。
其中化学氧化处理方法为:
(1)手工溶剂除油
使用棉纱、软布或刷子沾二甲苯溶剂,将试板表面的油污清理干净,待试板表面的溶剂挥发干净后备用。
(2)酸溶液清洗
酸液配方:氢氟酸质量分数为80 g/L;
工艺:将氢氟酸兑稀至要求后,用加热装置将碱液加热至25~35 ℃后,把经过溶剂除油的试板放入溶液中浸泡5~6 min,然后用流动的冷水冲洗2 min以上,再用去离子水冲洗2 min以上。
(3)重铬酸钾洗
重铬酸钾配方:重铬酸钾质量分数为105g/L,氟化镁质量分数为 2.5g/L;
工艺:将重铬酸钾液按配方配制后,用加热装置将碱液加热至(96±3)℃后,把经过氢氟酸清洗的试板放入重铬酸钾液中浸泡30 min,然后用流动的冷水冲洗2 min以上,再用去离子水冲洗2 min以上,晾干备用。
根据技术方案设计,本技术研究需要用到防腐底漆和腻子两种产品。
2.1防腐底漆选型
防腐底漆对镁合金附件的保护起主要作用,市面上有众多的环氧防腐底漆,但其防腐性能评价时间较长。因此本研究选用本单位生产的高性能环氧底漆(含铬系颜填料)、无铬高固体份防腐底漆和高固体份防腐底漆(含铬系颜填料)3种性能优异的防腐底漆进行对比。
其中,高性能环氧底漆采用环氧与聚酰胺固化体系以及铬系颜填料,具有铬系颜填料的防腐优势;无铬高固体份防腐底漆采用酚醛环氧与脂环胺固化体系以及环保型颜填料,具有耐高低温、耐介质优势;含铬高固体份防腐底漆采用酚醛环氧与脂环胺固化体系以及铬系颜填料,具有高附着力、柔韧性、抗冲击、耐各种介质性能、耐高低温循环、长效防腐等性能优势。本研究对3种防腐底漆开展性能对比,对比结果见表1。
表1 防腐底漆性能对比
从表1可以看出,高性能环氧底漆耐盐雾性能和耐液压油性能较差,含铬系颜填料的高固体份防腐底漆耐盐雾性能可达1000 h以上,耐LD-4液压油30 d基本无变化。这是因为酚醛环氧具有较好的耐酸性,而铬系颜填料的存在也提升了防腐涂料的耐盐雾性能。因此本研究最终选用性能最好的高固体份防腐底漆(含铬系颜填料)作为修补用防腐底漆。
2.2 腻子选型
目前应用比较成熟的腻子有原子灰(不饱和聚酯腻子)、环氧腻子和聚氨酯腻子等。原子灰具有干燥快、易打磨、附着力强等优点,但也存在柔韧性差且收缩性大、内聚力不足的缺点。柔性环氧腻子具有附着力强、易打磨、适用期长、储存稳定性好等优点,但其在低温下(5℃以下)的反应活性较低。聚氨酯腻子具有更好的弹性, 防裂抗振, 抗老化等性能。多数镁合金制件应用环境为高温、震动,因此要求腻子需具有较好的耐温性和弹性。目前汽车行业、航空业等使用的不饱和聚酯腻子柔韧性差,不能满足技术指标要求。因此本研究选用本单位生产的柔性环氧腻子和聚氨酯腻子开展技术研究。
本项目针对这两种不同的腻子进行了性能比较,结果见表2。
表2 腻子性能比较
通过表2可以看出,柔性环氧腻子附着力12.5 MPa,适用期120 min,远优于聚氨酯腻子的附着力6.7 MPa和适用期25 min。聚氨酯腻子表干时间和实干时间较柔韧环氧腻子有优势,因此本研究分别用两种不同类型的腻子与防腐底漆配套,开展性能比较。
本研究选用高固体份防腐底漆(含铬系颜填料)分别与柔性环氧腻子和聚氨酯腻子配套制板,并对其进行性能评价,具体配套方案为:
方案1:含铬高固体份防腐底漆+柔性环氧腻子+含铬高固体份防腐底漆。
(1)对镁合金结构材料进行打磨至无可见腐蚀;
(2)用铬酸盐对镁合金结构材料整体进行化学前处理,材料表面形成转化膜;
(3)喷涂含铬高固体份防腐底漆,常温干燥;
(4)刮涂柔性环氧腻子,常温干燥;
(5)机械打磨至表面平整;
(6)喷涂含铬高固体份防腐底漆,常温干燥,完成修复。
方案2:含铬高固体份防腐底漆+聚氨酯腻子+含铬高固体份防腐底漆。
(1)对镁合金结构材料进行打磨至无可见腐蚀;
(2)用铬酸盐对镁合金结构材料整体进行化学前处理,材料表面形成转化膜;
(3)喷涂含铬高固体份防腐底漆,常温干燥;
(4)刮涂聚氨酯腻子,常温干燥;
(5)机械打磨至表面平整;
(6)喷涂含铬高固体份防腐底漆,常温干燥,完成修复。
所有样板制备完成后在(23±2)℃环境下养护7d,进行性能测试,两种修复方案效果对比如下:
(1)外观和附着力
依照GB/T 5210—2006标准进行样板的外观、附着力测试,结果如图1所示。
图1 外观、附着力测试
两种配套方案外观均匀且平整光滑,配套方案1附着力达到12.5 MPa、13.6 Mpa,配套方案2附着力6.5 Mpa,7.0 Mpa,环氧腻子配套后附着力优于聚氨酯腻子配套的附着力。这是因为环氧树脂的结构中有许多羟基、醚键和活泼的环氧基,使环氧树脂有很强的粘结力。羟基、醚键有很强的极性,使得环氧树脂分子与相邻的金属界面产生吸引力。
(2)耐润滑油性能
依照GB/T9274—1988标准测试样板的耐飞马Ⅱ号合成润滑油性能和耐8号(75%)+20号(25%)混合航空润滑油性能,结果如图2、图3所示。
图2 (121±5)℃×8 h耐飞马Ⅱ号合成润滑油
图3 121±5℃×8 h耐 8号(75%)+20号(25%)混合航空润滑油
配套涂层最外层均为含铬高固体份防腐底漆,配套涂层耐完润滑油后有明显变色,继续做500 g划痕试验,基本无划痕耐,两个方案无差别。
(3)耐燃油性能
依照GB/T9274—1988标准测试样板的耐常温燃油(RP-3、RP-5、50% RP-3+50%RP-5 )性能、耐45℃5号航空煤油性能,结果如图4所示。
图4 耐常温燃油
配套涂层最外层均为含铬高固体份防腐底漆,配套涂层耐常温燃油(RP-3、RP-5、50% RP-3+50%RP-5 )、耐45℃5号航空煤油基本无变化,继续做500 g划痕试验,基本无划痕耐,两个方案无差别。
(4)耐热性
依照GB/T 1735—2009标准测试样板的耐热性,结果如图5、图6所示。
图5 200 ℃处理24 h 图6 200℃处理48h
两个配套方案试验结果均为200 ℃,24 h处理涂层变色,试板有弯曲;200 ℃,48 h处理涂层变色,试板弯曲严重,继续做500 g划痕试验,板面无痕迹。
因为现场修复存在较深的腐蚀坑,深度可达5 mm以上,为更贴近实际工况环境,本研究在宽15 mm,深0.6 mm的凹槽中分别刮涂两种不同腻子,待腻子实干后放入200 ℃烘箱中。结果表明,环氧腻子烘8 h后,开裂严重;聚氨酯腻子仅有轻微变色,无开裂现象。这是因为环氧树脂一般在180~200 ℃下就会发生热氧化分解,而氨基甲酸酯基的热分解温度为240 ℃,具有较好的热稳定性。
(5)耐温度冲击性能
依照GJB/T 150.5A—2009标准进行样板的耐温度冲击性能测试。配套样板在(120℃±3)℃放置25 min后,在1 min内将试片移入(-54℃±3)℃放置5 min,做5次循环。两个方案无差别,配套涂层耐温度冲击试验后无任何变化。
(6)耐霉菌性能
依照GJB/T 150.10A—2009标准进行样板的测试,结果表明,两种配套方案无差别, 霉菌等级均为0级。
(7)耐湿热性能
依照GJB/T 150.9A—2009标准进行样板的耐湿热测试。本研究两种配套方案耐湿热250d后试样表面均无锈蚀、起泡;耐湿热280 d后配套方案1漆膜颜色变淡,无锈蚀、起泡等现象,配套方案2漆膜颜色变淡,表面有起泡现象,如图7所示。说明环氧腻子与含铬高固体份防腐底漆配套耐湿热性更好。
图7 耐湿热测试
(8)耐中性盐雾
依照GB/T 1771—2007标准进行中性盐雾试验评价,结果表明,中性盐雾1000 h后,两种配套方案试样表面均无锈蚀、起泡。
(9)耐盐水
依照GB/T 9274—1988标准进行耐盐水评价,常温(23±3)℃,耐5%盐水,30d后,两种配套方案试样表面均无锈蚀、起泡,如图8所示。
图8 耐盐水测试
通过两种配套方案性能评价比较,环氧腻子配套方案具有附着力高、耐湿热性好,聚氨酯腻子配套方案具有更好的耐热性,而且其附着力和耐湿热性也满足正常工况使用,因此本研究最终选用配套方案2作为最终修复方案,即含铬高固体份防腐底漆与聚氨酯腻子配套方案。
本研究对防腐底漆在不同温度下干燥时间,可打磨时间,最长复涂时间进行了探讨,确定了其配套参数,具体见表3。在底漆可打磨时间和最长复涂间隔之间可直接刮涂腻子,在最长复涂间隔时间之后需对漆膜进行表面打磨之后再刮涂腻子。
表3 含铬高固体份防腐底漆配套参数
含铬高固体份防腐底漆可采用刷涂、普通喷枪喷涂、静电喷涂的方式进行施工。将底漆与固化剂按质量比10:4配制好,搅拌均匀后,加入稀释剂稀释至施工粘度,静置熟化20~30 min后再施工。
其中刷涂根据个人习惯按比例配漆后进行刷涂。
空气喷涂最佳施工参数为:枪嘴与涂面的距离20~30 cm;气压0.3~0.4 Mpa;喷枪运行 20~30 cm/s;
静电喷涂最佳施工参数为:静电喷枪进气压力0.4 Mpa;物料泵压力0.2 MPa;枪嘴与涂面的距离 20~30 cm;喷枪运行20~30 cm/s。
本研究对腻子在不同温度下干燥时间,可打磨时间进行了探讨,确定了其配套参数,具体见表4。其中腻子打磨后即可喷涂底漆。
表4 弹性聚氨酯腻子配套参数
弹性聚氨酯腻子采用刮涂的方式进行施工。将腻子与腻子固化剂按质量比100:12搅拌均匀后,用刮刀或调刀将混合后的腻子刮涂在需要修复的表面,表面刮涂平整,待完全干燥后用1000目砂纸打磨平整,继续喷涂含铬高固体份防腐底漆,完成腐蚀坑修复。
结 语 本研究采用含铬高固体份防腐底漆和聚氨酯腻子形成一种修复镁合金制件腐蚀坑的方法,并探究了两种产品在不同温度下的配套工艺,实现镁合金(ZM5)附件机匣腐蚀坑的快速修复,成本低,修复后的镁合金(ZM5)制件具有较强的耐高低温、耐介质、耐湿热及防腐蚀能力。
免责声明:本网站所转载的文字、图片与视频资料版权归原创作者所有,如果涉及侵权,请第一时间联系本网删除。
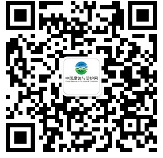
官方微信
《腐蚀与防护网电子期刊》征订启事
- 投稿联系:编辑部
- 电话:010-62316606
- 邮箱:fsfhzy666@163.com
- 腐蚀与防护网官方QQ群:140808414