摘要
采用回归再时效处理2024铝合金并对其进行透射电镜和扫描电镜观察、硬度、晶间腐蚀和电化学腐蚀测量,研究了回归时间对2024铝合金的微观组织和耐蚀性能的影响。结果表明:经回归再时效处理的2024铝合金其主要析出强化相为S相。回归处理时间为0.2 h的合金,S相细小且呈弥散均匀分布,性能有显著的提高,硬度为147.2 HV0.5、晶间腐蚀深度为98.5 μm、自腐蚀电位为-0.64 V、自腐蚀电流密度为0.24 μA·cm-2、电阻值为31397 Ω·cm2。这表明,适当时间的回归处理有利于提高2024铝合金的硬度和耐蚀性。
关键词: 金属材料; 2024铝合金; 回归再时效; 耐蚀性; 析出相
2024铝合金(Al-Cu-Mg合金)属于2xxx系铝合金(Al-Cu系合金),是一类可通过热处理弥散强化的变形铝合金。2024铝合金具有高比强度、质轻和良好的机械性能,广泛用于航空航天以及汽车制造等领域[1~4]。但是,2024铝合金的耐蚀性较低,进行不同的热处理可将其提高[5~7]。单级峰值时效(T6)处理能有效改善2024铝合金的硬度和强度,但是其耐蚀性的提高不明显[8,9]。李海等[10]发现,过时效状态的Al-4.5Cu合金晶界处的析出相由线状变为链状,降低了其晶间腐蚀(Intergranular corrosion, IGC)敏感性。詹鑫等[11]发现,非等温峰时效处理状态的2A14铝合金,在晶界和晶内均出现二次析出第二相,其自腐蚀电流密度、电位和极化阻抗均高于T6态。
回归再时效(Retrogression and re-aging, RRA)处理,是针对7xxx系铝合金(Al-Zn系合金)的一种热处理工艺。RRA处理,分为预时效、短时高温回归和再时效三个部分。RRA处理可使7xxx铝合金具有高强度和硬度,和良好的耐蚀性[12~17]。赵刚等[18]提出,将欠时效作为预时效处理和适当的回归处理配合RRA处理,有利于提高2014铝合金的强度和延展性。YUAN等[19]提出,与单级时效处理相比,2A97铝合金预时效后,回归处理的抗拉强度降低且延展性提高,再经RRA处理其抗拉强度提高且延展性降低。WARD等[20]提出,随着回归温度的提高和时间的延长,2195铝合金的强度值逐渐降低。本文研究回归时间对2024铝合金的组织和耐蚀性能的影响。
1 实验方法
表1列出实验用2024铝合金的成分。
表1 实验用2024铝合金的成分(质量分数,%)
先将从锻件上切下的不同尺寸的试样在500℃箱式电阻炉中进行40 min固溶处理,然后将其快速水淬至室温。将试样在190℃预时效处理2 h,空冷至室温后再将其在320℃分别回归处理0.1 h、0.2 h、0.3 h、0.4 h和0.5 h,水淬冷却至室温。最后将回归处理后的试样均在190℃电热鼓风干燥箱中再时效处理8 h。表2列出了不同编号试样的热处理工艺。
表2 不同编号试样的热处理工艺
将试样表面打磨抛光,用UH250型数显维氏硬度计测试抛光面的硬度,载荷为5 N,加载时间为10 s。每个试样测5个点取结果的平均值,误差值为±2.1 HV0.5。根据国家标准GB/T 7998-2005标准进行IGC实验,测试三个热处理工艺不同的平行样品以减小误差。将试样打磨和抛光后进行预处理,然后将其垂直悬浮在腐蚀溶液中(用500 mL蒸馏水溶解28.5 g NaCl和5 mL H2O2),浸泡时间为6 h,腐蚀溶液温度为35±2℃,浸泡时的面体积比小于2 dm2·L-1。实验结束后,用TM3030扫描电镜观察IGC深度。使用CS310电化学工作站进行电化学腐蚀实验,采用三电极体系测试极化曲线和交流阻抗谱(Electrochemical impedance spectroscopies, EIS),试样为工作电极,辅助电极为Pt电极,参比电极为饱和甘汞电极,实验温度为25℃。3.5% NaCl溶液为腐蚀介质,扫描电位范围为±1 V,扫描速率为2 mV·s-1。EIS的频率范围为0.01~100000 Hz,正弦交流信号幅值为10 mV,用Zview软件拟合EIS的数据。
用JEM-2100透射电镜(Transmission electron microscope, TEM)观察不同热处理试样的微观结构。先将片状试样打磨至50 μm,然后冲成直径为3 mm的小圆片。将圆片放在装有腐蚀液(30% HNO3和70% CH3OH)的TJ100-SE电解双喷仪中,用液氮降温后进行双喷减薄,实验温度为-25℃。
2 实验结果
2.1 不同热处理后合金的硬度
图1给出了不同热处理合金的维氏硬度。由图1可见,经RRA处理的合金其硬度的变化趋势是先提高后降低,回归处理0.2 h后再时效处理其硬度值达到最高,为147.2 HV0.5。回归处理时间超过0.4 h后进行再时效处理,合金的硬度值降至仅预时效处理的合金硬度值以下。这表明,只有回归处理时间适当才能提高RRA处理的2024铝合金的硬度。
图1 不同热处理后合金的硬度
2.2 晶间腐蚀
图2给出了不同热处理后合金的IGC形貌。如图2a可见,仅进行预时效处理的合金其截面的腐蚀面积较大,腐蚀沿着合金的晶界和相界进行且腐蚀的深度较大(表3),最长的IGC深度为228.2 μm。由图2b、c、d、e和f可见,随着回归时间的增加RRA处理后合金的IGC深度先减小再增大,回归处理时间为0.2 h的合金经RRA处理后的腐蚀面积最小,IGC深度最浅,最长的腐蚀深度为98.5 μm。这表明,适当的回归时间使RRA处理后的合金耐晶间腐蚀性能更高。
图2 不同热处理后合金的IGC照片
表3 不同热处理后合金的IGC深度
2.3 电化学腐蚀
进行电化学腐蚀实验能从根本上研究合金的腐蚀性能[21]。图3给出了不同热处理后合金的极化曲线。可以看出,极化曲线的形状基本相同,先发生氧还原的阴极极化,到达自腐蚀电位后发生阳极极化,此时腐蚀电流密度迅速增大,阳极溶解顺利。与仅经预时效处理的合金相比,RRA处理的合金其自腐蚀电位提高,电流密度也明显降低。式
图3 不同热处理后合金的极化曲线
表明,腐蚀电流密度与腐蚀速率成正相关[22],因此RRA处理后的合金腐蚀速率也降低了。 式(1)中M为相对原子量,n为合金失去的电子数,S为工作电极的面积 (cm2),ρ是合金的密度 (g·cm-3)。回归时间为0.2 h、经RRA处理的合金其自腐蚀电位最高为-0.64 V,自腐蚀电流密度和腐蚀速率最低,其耐蚀性最好。其它试样的极化曲线参数如表4所示。
表4 不同热处理后合金的极化曲线参数
可根据EIS研究不同热处理后合金的腐蚀特性,图4中只有一个容抗弧,其直径表征合金的耐蚀性能。图5给出了对应的等效电路,当电极的双电层阻抗行为偏离等效电容的阻抗行为时用恒相位角原件CPE在数学上模拟双电层电容Cd,可得到更好的拟合效果,根据式
图4 不同热处理后合金的Nyquist图
图5 等效电路
可知电容的受制因素[23]。 式(2)中n为双电层的弥散指数(为0.6~1),n越接近于1则CPE的拟合效果越接近等效电容,Z0为常数。等效电路中的Rs为溶液的电阻,Rt为合金与溶液之间的电荷转移电阻。结合EIS与等效电路,EIS中的容抗弧代表合金与溶液之间的双电层行为[24]。表5列出了不同热处理合金的EIS参数。合金在仅经预时效处理时容抗弧直径较小,电阻值较小为6515 Ω·cm2,合金的耐蚀性能较差。经RRA处理后合金的耐蚀性能明显提高。随着回归时间的增加容抗弧直径先增大后减小,回归处理0.2 h的合金经RRA处理后的容抗弧直径最大,电阻值最大为31397 Ω·cm2,合金的耐蚀性能最佳。
表5 不同热处理后合金的EIS参数
2.4 组织形貌
图6给出了不同热处理后合金的明场TEM照片。可以看出,单级时效处理和RRA处理的2024铝合金其主要基体析出相(Matrix precipitates, MPts)为针棒状的S相(Al2CuMg)。从图6a可见,经190℃预时效处理2 h的合金其内的MPts为S'相和S相,以S'相居多且分布较为弥散。从图6b、c、d、e和f可以看出,经RRA处理后合金内的主要MPts为S相。图6b中的S相总体分布不均;图6c中S相的数量比图6b中的多,且更加均匀弥散,尺寸约为100 nm,左下角给出了选中区域的S相在[001]Al上的电子衍射花样;从图6d、e和f可见,随着回归时间的增加合金经RRA处理后MPts分布均匀,但是粗化越来越严重。
图6 不同热处理后合金的明场TEM照片
3 分析讨论
合金的组织决定其性能。2024铝合金的主要析出相强化相为S相和θ相,MPts主要为S相。2024铝合金中S相的析出序列为[25~29]
其中SSS为过饱和固溶体,GPB区为原子偏聚区,S''相和S'相为与基体半共格的亚稳过渡相,S相为稳定的与基体非共格的平衡相。2024铝合金在固溶处理后迅速水淬冷却形成SSS,冷却迅速SSS内定格了大量空位。Mg原子的扩散率和空位结合能均大于Cu原子[30],虽然Cu原子的含量比Mg原子高,在初步的时效处理过程中2024铝合金内产生大量Cu-Mg团簇,其体积小但是密度大。在随后的时效处理过程中Cu-Mg团簇因得到更多的能量而转为过渡相,随着时效过程的进行最终转变为平衡相。
S相中的Mg元素电位低,较为活泼,因此在腐蚀的最初阶段S相作为阳极而发生点蚀,Al基体则发生氧还原的阴极反应。在Mg元素迅速消耗后,出现富Cu的剩余物。Cu元素的电位比Al基体高,富Cu剩余物为阴极。Al基体与溶液中的H2O和侵蚀性离子Cl-同时发生反应而使Al基体发生阳极溶解,O2的传输在阴极生成OH-,在合金表面生成钝化膜,而腐蚀液中的Cl-很快破坏合金表面的钝化膜。如图3所示,在阳极极化过程中没有产生钝化区,阳极溶解顺利进行。Cl-在已经发生点蚀处(例如S相)优先击穿其表面钝化膜,在金属表面形成小蚀坑,使点蚀更加严重,甚至在晶界处发展为IGC。而回归时间为0.2 h的合金经RRA处理后,MPts的弥散均匀分布使Cl-分散,在析出相上发生不剧烈的点蚀,点蚀坑很小,如图4所示,腐蚀反应不明显。
如图6a所示,2024铝合金在190℃预时效处理2 h后MPts多为S'相,还有少量S相。其原因是,因时效处理时间较短合金内的能量有限,大部分MPts以过渡相的形式存在,且预时效后的欠时效状态更有利于细小MPts在回归处理时回溶。预时效后的2024铝合金经较高温度的回归处理,MPts开始回溶进基体。但是随着回归时间的增加部分较为粗大的MPts未能回溶,并逐渐长大。如图6b、c、d、e和f所示,合金经RRA处理后回溶的MPts重新析出,以S相为主分散于基体中。回归处理时间越长合金经RRA处理后的粗化相越多,粗大的MPts不仅使合金的硬度降低,还使MPts与基体之间的电位差提高,使合金更易发生点蚀,降低了合金的耐腐蚀性能。因此,回归时间为0.2 h后经RRA处理后合金,其内的S相细小且分布均匀弥散,使合金的硬度和耐蚀性最好。
4 结论
(1) 回归处理时间为0.2 h、经RRA处理的2024铝合金其硬度最高、晶间腐蚀深度最浅、自腐蚀电位最高、自腐蚀电流密度最小,分别为147.2 HV0.5、98.5 μm、-0.64 V和0.24 μA·cm-2。
(2) 在RRA处理的2024铝合金内的主要析出强化相为S相,随着回归时间的延长合金经RRA处理后的MPts分布均匀弥散,但是越来越粗化,使其硬度和耐蚀性的降低。因此,选择适当的回归时间是RRA处理的关键。
(3) 2024铝合金中的MPts优先腐蚀,而细小弥散的MPts可降低与基体之间的电位差,减小点蚀和晶间腐蚀等局部腐蚀,提高合金的耐蚀性。
参考文献
1 Fan C H, Ou L, Hu Z Y, et al. Re-dissolution and re-precipitation behavior of nano-precipitated phase in Al-Cu-Mg alloy subjected to rapid cold stamping[J]. T. Nonferr. Metal. Soc., 2019, 29(12):2455
doi: 10.1016/S1003-6326(19)65153-8
2 Wang H C, Yang H B, Liu G L, et al. Influence of Al-5Ti-0.25C refiner on microstructure and mechanical properties of 2024 alloy[J]. Mater. Rev., 2016, 30(20): 81
2 王海超, 杨化冰, 刘桂亮 等. Al-5Ti-0.25C细化剂对2024铝合金组织及力学性能的影响[J]. 材料导报, 2016, 30(20): 81
3 Zhang X M, Liu S D. Aerocraft aluminum alloys and their materials processing[J]. Materials China, 2013, 32(01): 39
3 张新明, 刘胜胆. 航空铝合金及其材料加工[J]. 中国材料进展, 2013, 32(01): 39
4 Li T, Tao J L, Wang Q Y. The mechanism of fatigue crack initiation of 2024-T3 and 2524-T34 aluminum alloys[J]. Chin. J. Mater. Res., 2011, 25(01): 67
4 李 棠, 陶俊林, 王清远. 2024-T3和2524-T34铝合金疲劳裂纹的萌生机制[J]. 材料研究学报, 2011, 25(01): 67
5 Shi W N, Zhou H F, Zhang X F. High-strength and anti-corrosion of Al-Cu-Mg alloy by controlled ageing process[J]. Phil. Mag. Lett., 2019, 99(07): 235
doi: 10.1080/09500839.2019.1662960
6 Qu F J, Xiao B L, Cao Y, et al. Effect of aging on corrosion resistance of 2024 aluminum alloy[J]. Nonferrous Metals Processing, 2020, 49(05): 53
6 曲凤娇, 肖宝靓, 曹阳 等. 时效处理对2024铝合金腐蚀性能的影响[J]. 有色金属加工, 2020, 49(05): 53
7 Sun L, Niu F J, Wu C L, et al. Influence of precipitation microstructure change on the stress corrosion behavior of AA2024 aluminum alloy[J]. Rare Metal Mat. Eng., 2019, 48(09): 2944
7 孙 丽, 牛凤姣, 伍翠兰 等. 时效析出行为的改变对AA2024铝合金应力腐蚀行为的影响[J]. 稀有金属材料与工程, 2019, 48(09): 2944
8 Barros A, Cruz C, Silva A P, et al. Length scale of solidification microstructure tailoring corrosion resistance and microhardness in T6 heat treatment of an Al-Cu-Mg alloy[J]. Corros. Eng. Sci. Techn., 2020, 55(06): 471
doi: 10.1080/1478422X.2020.1742410
9 Zuiko I, Kaibyshev R. Aging behavior of an Al-Cu-Mg alloy[J]. J. Alloy. Compd., 2018, 759: 108
doi: 10.1016/j.jallcom.2018.05.053
10 Li H, Zhou Y, Wang Z X. Effect of aging state and Cu content on intergranular corrosion sensitivity of Al-Cu alloy[J]. Hot Working Technology, 2020: 1
10 李 海, 周 洋, 王芝秀. 时效状态及Cu含量对Al-Cu合金晶间腐蚀敏感性的影响[J]. 热加工工艺, 2020: 1
11 Zhan X, Li H Z, Liang X P, et al. Effect of non-isothermal aging on intergranular corrosion and mechanical properties of 2A14 aluminum alloy[J]. Min. Metall. Eng., 2018, 38(06): 139
11 詹 鑫, 李慧中, 粱霄鹏 等. 非等温时效对2A14铝合金晶间腐蚀和力学性能的影响[J]. 矿冶工程, 2018, 38(06): 139
12 Reda Y, Abdel-Karim R, Elmahallawi I. Improvements in mechanical and stress corrosion cracking properties in Al-alloy 7075 via retrogression and reaging[J]. Mat. Sci. Eng. A-Struct., 2008, 485(01-02): 468
doi: 10.1016/j.msea.2007.08.025
13 Wu Y P, He Z Y, Zhou Z G, et al. Effect of non-isothermal retrogression and re-aging treatments on the microstructure and mechanical properties of 7050 alloy[J]. Mater. Rev., 2019, 33(S2): 394
13 吴懿萍, 何臻毅, 周志纲 等. 非等温回归再时效对7050铝合金组织与力学性能的影响[J]. 材料导报, 2019, 33(S2): 394
14 Su R M, Qu Y D, Li X, et al. Low-temperature retrogression of spray formed 7075 alloy[J]. Chin. J. Nonferrous. Met., 2016, 26(12):2523
doi: 10.1016/S1003-6326(16)64378-9
14 苏睿明, 曲迎东, 李想 等. 喷射态7075合金欠时效低温回归处理[J]. 中国有色金属学报, 2016, 26(12): 2523
15 Peng G S, Chen K H, Chen S Y, et al. Influence of dual retrogression and re-aging temper on microstructure, strength and exfoliation corrosion behavior of Al-Zn-Mg-Cu alloy[J]. T. Nonferr. Metal. Soc., 2012, 22(04): 803
doi: 10.1016/S1003-6326(11)61248-X
16 Gong J, Wang M P, Zhang Q, et al. Influence of retrogression and re-aging treatment on intergranular and exfoliation corrosion of 1973 aluminum alloy[J]. Journal of Central South University (Science and Technology), 2012, 43(07): 2520
16 龚 静, 汪明朴, 张 茜 等. RRA处理对1973铝合金晶间腐蚀与剥蚀的影响[J]. 中南大学学报(自然科学版), 2012, 43(07): 2520
17 Wang X, Liu C P, Lv H B, et al. Effect of retrogression reaging on microstructure and electrochemical corrosion resistance of 6082 aluminum alloy[J]. Special Casting & Nonferrous Alloys, 2019, 39(01): 84
17 王 鑫, 刘春鹏, 吕海波 等. 回归再时效对6082合金组织及电化学腐蚀性的影响[J]. 特种铸造及有色合金, 2019, 39(01): 84
18 Zhao G, Liu C M, Zhu L Y, et al. Retrogression and reaging treatments of 2014 alloy[J]. Journal of Materials and Metallurgy, 2003, (03): 210
18 赵 刚, 刘春明, 朱丽颖 等. 2014合金的回归再时效[J]. 材料与冶金学报, 2003, (03): 210
19 Yuan Z S, Lu Z, Xie Y H, et al. Effects of RRA treatments on microstructures and properties of a new high-strength aluminum-lithium alloy-2A97[J]. Chinese J. Aeronaut., 2007, 20(02): 187
doi: 10.1016/S1000-9361(07)60031-4
20 Ward N, Tran A, Abad A, et al. The effects of retrogression and reaging on aluminum alloy 2195[J]. J. Mater. Eng. Perform., 2011, 20(06): 1003
doi: 10.1007/s11665-010-9739-5
21 Ghosh K S, Tripati K. Microstructural characterization and electrochemical behavior of AA2014 Al-Cu-Mg-Si alloy of various tempers[J]. J. Mater. Eng. Perform., 2018, 27(11): 5926
doi: 10.1007/s11665-018-3694-y
22 Chen S Y, Chen K H, Peng G S, et al. Effect of heat treatment on strength, exfoliation corrosion and electrochemical behavior of 7085 aluminum alloy[J]. Mater. Design, 2012, 35: 93
doi: 10.1016/j.matdes.2011.09.033
23 Zhang J Q. Electrochemical Testing Technique[M]. Beijing: Chemical Industry Press, 2010
23 张鉴清. 电化学测试技术[M]. 北京: 化学工业出版社, 2010
24 Wen L, Wang Y M, Zhou Y, et al. Corrosion evaluation of microarc oxidation coatings formed on 2024 aluminium alloy[J]. Corros. Sci., 2010, 52 (08):2687
doi: 10.1016/j.corsci.2010.04.022
25 Wang S C, Starink M J. Two types of S phase precipitates in Al-Cu-Mg alloys[J]. Acta Mater., 2007, 55(03): 933
doi: 10.1016/j.actamat.2006.09.015
26 Wang S C, Starink M J. Precipitates and intermetallic phases in precipitation hardening Al-Cu-Mg-(Li) based alloys[J]. Acta Mater., 2005, 50(04):193
27 Parel T S, Wang S C, Starink M J. Hardening of an Al-Cu-Mg alloy containing types I and II S phase precipitates[J]. Mater. Design, 2010, 31:S2
doi: 10.1016/j.matdes.2009.12.048
28 Wang S C, Starink M J. The assessment of GPB2/S'' structures in Al-Cu-Mg alloys[J]. Mat. Sci. Eng. A-Struct., 2004, 386(1-2): 156
doi: 10.1016/S0921-5093(04)00913-X
29 Li H Z, Liu R M, Liang X P, et al. Effect of pre-deformation on microstructures and mechanical properties of high purity Al-Cu-Mg alloy[J]. T. Nonferr. Metal. Soc., 2016, 26 (06): 1482
doi: 10.1016/S1003-6326(16)64253-X
30 Marceau R K W, Sha G, Lumley R N, et al. Evolution of solute clustering in Al-Cu-Mg alloys during secondary ageing[J]. Acta Mater., 2010, 58: 1795
doi: 10.1016/j.actamat.2009.11.021
免责声明:本网站所转载的文字、图片与视频资料版权归原创作者所有,如果涉及侵权,请第一时间联系本网删除。
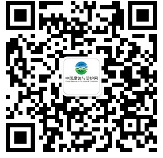
官方微信
《腐蚀与防护网电子期刊》征订启事
- 投稿联系:编辑部
- 电话:010-62316606
- 邮箱:fsfhzy666@163.com
- 腐蚀与防护网官方QQ群:140808414