摘要
通过EIS和动电位极化曲线的测量,并结合SEM观察、EDS和XPS分析,研究了模拟压水堆核电站 (PWR) 二回路服役水环境异常工况 (100 μg/L DO+100 μg/L Cl-+ETA) 中溶液温度 (150~285 ℃) 对690合金电化学腐蚀行为的影响机理。结果表明:温度升高,690合金自腐蚀电位降低,腐蚀电流密度增加,钝化电位区间缩短;表面氧化膜厚度增加,颗粒增大,双层氧化膜特征越明显,但致密度和稳定性降低,导致其耐蚀性降低,合金腐蚀速率增加。
关键词: 690合金 ; 压水堆 ; 高温电化学腐蚀 ; 二回路
1 前言
蒸汽发生器 (SG) 是压水堆核电站 (PWR) 中连接一回路与二回路的枢纽,其良好运转对整个核电站的安全运营至关重要。优化二回路水环境不仅能改善二回路中传热管材的耐蚀性能,而且能减少腐蚀产物在二回路传热管中的沉淀堆积以及向一回路中的转移扩散,避免传热管传热效率下降。早期的PWR核电站SG传热管材主要采用304不锈钢、316不锈钢和镍基600合金[1,2]。根据实际运行经验发现,SG传热管的主要失效方式是应力腐蚀开裂 (SCC)。镍基690合金由于具有优异的抗腐蚀和抗应力腐蚀性能,逐渐替代镍基600合金成为PWR核电站SG传热管的首选材料。
早期由于高温高压水环境中的电化学测试存在诸多问题,如密封、电极绝缘及参比电极的稳定性,导致电化学测试限于室温条件。伴随着这些问题的不断解决,模拟核电材料实际服役工况的电化学测试逐渐成为研究热点。不同水化学参数,如温度、溶解氧 (DO)、溶解氢 (DH)、Zn和pH值等对核级合金材料腐蚀行为的影响已有广泛的报道[3,4]。然而,由于实验条件不一致,得出的结论也存在差异。如Huang等[3]在模拟二回路缝隙环境中发现,随着溶液温度的升高,690合金的自腐蚀电位降低,钝化区缩小;而Abraham等[4]得出:690合金在300 ℃的LiOH溶液中形成的表面氧化膜比在250和275 ℃形成的更稳定。
目前,PWR二回路及其相应冷却系统使用的水和天然海水含有大量的电解质和溶解氧,尽管对二回路冷却水进行了严格的前期处理,但仍有少量溶解氧和氯化物保存下来,且在反应堆启动、停止时存在有空气漏入、回水器泄漏或海水漏入等问题[5]。故本实验采用向高温高压水中加入一定量DO (100 μg/L) 和Cl- (100 μg/L) 的方式模拟PWR二回路服役水环境异常工况,研究了二回路水环境 (100 μg/L DO+100 μg/L Cl-+ETA) 中温度对核级商用690合金的电化学行为的影响,本实验结果可以为核电运行和选材提供数据支持。
2 实验方法
2.1 实验材料
选用核级商用690合金管,其化学成分 (质量分数,%) 为:Cr 27.52,Fe 10.36,C 0.023,Si 0.24,Mn 0.74,Ti 0.25,Co 0.017,Ni 余量。为获得相同的电极表面,将长为10 mm的管状试样 (外径Φ=17.48 mm,厚度d=1.02 mm,见图1),均匀切成4片,并对试样6个表面依次用400#,800#,1200#,2000#和4000#砂纸打磨,最后在无水乙醇中清洗,烘干。每次准备两个试样放入釜中,一个作为浸泡实验试样,一个用于电化学测量试样。
图1 试样示意图
2.2 实验条件
实验采用自行搭建的高温高压动态循环釜装置 (图2)。在线监测高压釜进口和出口的水化学参数,如DO,pH值和电导率。起始时按照配比计算并通过加药系统向储水箱中加入100 μg/L Cl-,电加热系统使釜内温度波动控制在±0.1 ℃,加药系统将入口pH值控制在 (9.5±0.05),向储水箱持续鼓入混合气体控制釜中DO的浓度,实验时流速控制在4 L/h。
图2 实验回路示意图
电化学测试单元为三电极体系:工作电极由纯镍丝一端与试样一端点焊构成,镍丝用热缩聚四氟乙烯 (PTFE) 与釜体绝缘;对电极由10 mm×20 mm Pt片与用PTFE绝缘的Pt丝点焊构成;采用内置Ag/AgCl (0.1 mol/L KCl参比溶液) 为参比电极,其电极电位与标准氢电极 (SHE) 满足以下公式[6]:
(1)
式中,ESHE为相对于标准氢电极电位,t为实验温度 (℃),[Cl-]为参比溶液中Cl-的浓度,F为Faraday常数,R为气体常数。
2.3 测试方法
电化学实验均采用三电极系统和CorrTest电化学工作站,待温度稳定之后,测量开路电位 (OCP),当测完20 h开路电位后,开始测试试样的电化学阻抗谱 (EIS),设置频率从105~10-2 Hz,交流幅值为10 mV。随后,以0.5 mV/s的扫描速率从-1.3~1.5 V (vs SHE) 扫描得到动电位极化曲线。实验结束待高压釜冷却后取出试样吹干并对浸泡试样进行扫描电镜 (SEM,FEI Sirion 200) 观察、能谱 (EDS,OXFORD X-Act) 和X射线光电子能谱 (XPS,Kratos AXIS UltraDLD) 分析,记录试样表面形貌、氧化物形态、成分等基本信息。XPS深度分析采用单色铝靶Al Kα射线为激发源,电压14.0 kV,功率75 W,通能160 eV,溅射速率相对于Ta2O5 0.025 nm/s。用Casaxps (Version 2.3.15) 软件进行数据处理。在实验条件下,以样品表面污染碳的C 1s结合能 (284.8 eV) 和Ar (241.9 eV) 定标并校正荷电效应。
3 结果与讨论
3.1 EIS分析
690合金在模拟PWR二回路高温高压异常工况水中 (100 μg/L DO+100 μg/L Cl-+ETA) 不同温度下的EIS谱见图3。根据文献[7,8],并结合本实验结果,采用如图4所示的R(QR)(Q(RW)) 型等效电路,使用CorrTest电化学测试系统自带的阻抗谱数据分析软件对不同温度中所得的EIS结果进行拟合。其中,R1表示溶液电阻,由于电极/电解液界面性质的不均匀性以及高温高压环境中形成双层氧化膜结构的复杂性,使固体电极的双电层电容的频响特性与“纯电容”并不一致,故使用常相位角元件 (CPE) 来代替理想电容。常相位角元件CPE1与外层氧化膜阻抗 (R2)并联反映外层疏松且不稳定的氧化膜与溶液之间的电化学特性,常相位角元件CPE2则反映了内、外层氧化膜的界面特性。同时,由于内层氧化膜致密稳定,溶液中的OH-与金属基体中的Fe2+/Ni2+通过扩散穿过内层氧化膜更为困难,离子扩散过程逐渐成为整个电极腐蚀反应的控制过程,故采用电阻R3和表征离子扩散特性的Warburg阻抗W1串联的方式来表示内层氧化膜的Farady过程。
图3 690合金在模拟PWR二回路高温高压水 (100 μg/L DO+100 μg/L Cl-+ETA) 中不同温度下的EIS谱
图4 拟合690合金EIS结果的等效电路图
由图3中实验结果和拟合结果的Nyquist图可见,690合金在不同温度下,EIS曲线呈现相似的规律,曲线形状相同。在测试起始高频区均出现一个压缩的容抗弧,说明此时电极反应主要由溶液及电极表面的电荷转移控制,伴随着电极腐蚀的不断进行和频率的降低,逐渐在电极表面形成疏松氧化层,阻碍了溶液中OH-向基体扩散和基体溶解的Fe2+/Ni2+/Cr2+等金属离子向溶液中扩散,电极反应逐渐转向由物质扩散控制,因此在Nyquist图的低频区出现接近45°的直线段,呈现典型的Warburg阻抗特性。对比不同温度下的Nyquist图,系统阻抗特性呈现显著的区别。随着温度的升高,曲线整体左移,直线段变短,溶液电阻和Warburg阻抗显著降低,说明溶液温度升高既加速了溶液中氧化剂离子和基体金属离子向溶液和金属界面的转移,也使金属内部粒子内能和晶界能量增加,使更多的晶粒内部粒子向晶界转移并脱离晶界溶解于溶液中。拟合所得的溶液电阻和电极极化阻抗结果见图5。高温高压水环境中温度对690合金的阻抗影响显著,温度越高,氧化膜越疏松不稳定,腐蚀越剧烈。
图5 690合金的溶液电阻和极化电阻随温度的变化
3.2 动电位极化曲线
690合金在模拟PWR二回路高温高压水中不同温度下的动电位极化曲线见图6。已有研究[9]表明,随着DO的升高,高温高压下304和316L合金的自腐蚀电位向正方向移动。说明高温高压水环境中一定浓度的DO有助于690合金表面钝化膜的修补和形成,从而使腐蚀电位有所升高,耐腐蚀性能增强,这也是本实验中自腐蚀电位较高的原因。Huang等[10,11]发现,690合金在高温高压碱性水环境下,由于690合金中金属元素所呈现的活化-钝化特性,即随着所施加电位的升高,最先形成的Cr2O3膜逐渐溶解,而新的FeCr2O4和NiFe2O4氧化膜逐渐形成,使得极化曲线上均出现两个明显的钝化区,而在本实验中二次钝化区并不明显,这可能与溶液中Cl-有关。
图6 690合金在模拟PWR二回路水中不同温度下的极化曲线
本实验所得的690合金的电化学参数随温度的变化曲线见图7。比较图6和7可知,随着温度的升高,690合金的自腐蚀电位 (Ecorr) 由-0.258 V逐渐降低至-0.393 V,耐腐蚀性能显著降低;过钝化电位 (Etp) 下降,钝化电位区间显著缩短,腐蚀电流密度 (Icorr) 和维顿电流密度 (Ip) 均增加,上述参数的变化均说明了高温高压水环境中温度对690合金的电化学腐蚀行为影响显著,且随着温度的升高,钝化膜的稳定性和保护性减弱,耐腐蚀性能显著降低,腐蚀速率明显增加。
图7 690合金的电化学参数随温度的变化
图8 钝化电流密度Ip与温度的Arrhenius关系
通常认为,金属在水介质中的腐蚀本质上是一个电化学过程。为研究高温高压水环境中电化学电极反应的主要控制方式,本研究取Ip的对数和温度的倒数 (1/T) 作图,发现两者呈明显的直线关系,如图9所示。由此可知Ip与实验温度满足Arrhenius关系式:
(2)
图9 690合金在模拟PWR二回路水中不同温度下浸泡30 h后的氧化膜形貌
其中,A为因子常数,Q为活化能 (kJ/mol),T为热力学温度 (K)。通过计算可得到试样在150~285 ℃范围内,氧化膜生长的活化能为17.86 kJ/mol。已有研究[12]表明,690合金的活化能低于离子在液相中的迁移活化能 (41.84 kJ/mol)。显然,本实验模拟高温高压水环境中 (100 μg/L DO+100 μg/L Cl-+ETA) 690合金钝化膜的形成过程由离子在液相中的扩散过程控制。
3.3 SEM像和EDS结果
电化学实验结束并待温度降至30 ℃以下 (共30 h) 之后,打开高压釜取出用于浸泡实验的试样,清洗吹干,用SEM和EDS进行表面氧化膜形貌观察和表面不同位置处的腐蚀产物元素测定。氧化膜形貌和标定点处氧化膜的成分分析结果分别如图9和表1所示。可见,不同温度下试样表面形貌差距较大。结合EDS分析结果可知,150 ℃时表面零散分布的小球和多边形状颗粒为氧化产物 (图9a中点1) ,而光滑平整的区域 (图9a中点2) 为690合金基体。200 ℃时,表面已形成了内外双层氧化膜,内层氧化膜 (图9b中点1) 的氧化物颗粒细小,膜均匀致密;外层氧化膜 (图9b中点2) 还未形成完整的膜,颗粒状氧化物不断生成,长大,聚集成片。到250 ℃时,外层氧化物逐渐由零散多边形颗粒演变为成片的树叶状氧化膜完整地覆盖在内层氧化膜上 (图9 c)。随着温度进一步升高到285 ℃时,成片的树叶状氧化膜 (图9d中点1) 颗粒尺寸变大变厚,呈胞状结构,颗粒间的间隙也增大,部分区域甚至出现氧化膜的成片脱落,从而露出较为致密的内层氧化膜 (图9d中点2)。综上可见,随温度的升高,双层氧化膜演变规律明显,即随温度升高逐渐变厚但同时也逐渐变疏松,氧化膜对基体的保护能力随着溶液温度的升高呈减弱变化趋势,这与试样的极化曲线中随温度升高,钝化区缩小,腐蚀电流密度增加,腐蚀加快的变化趋势一致。Huang等[10,11]和Douglas等[13]也发现了类似的现象,并一致认为钝化膜的致密与稳定性远比其厚度对合金的保护性能重要。因此,温度升高虽然增加了氧化膜的厚度,但却降低了膜层的致密度和稳定性,腐蚀速率必然显著增加,这与EIS和动电位极化曲线测量结果相吻合。
表1 690合金在模拟PWR二回路水中不同温度下氧化膜的EDS结果
由上述SEM氧化膜形貌观测和EDS腐蚀产物元素测定结果可知,690合金表面在高温高压碱性环境中形成了内密外疏的双层氧化膜。进一步比较表1所得的元素原子分数变化规律可见,氧化膜由外向内,O含量逐渐降低;Fe含量稍有增加,Ni则显著增加,但Cr与Ni均低于基体中的含量。但250 ℃时,由于外层形成了完整的氧化膜,故EDS点分析时所得元素分布结果基本相同。内外层氧化膜中Fe,Cr与Ni含量的这一变化可能与3种金属离子在氧化膜中的移动速度有关。已有研究[9]表明,Fe,Cr与Ni 3种金属离子在氧化膜中的迁移速度比较:Fe2+>Ni2+≥Cr3+,因此Fe和Ni优先由基体逐渐迁移到氧化膜/溶液界面处发生反应,但又由于反应产物选择性溶解,大部分的含Ni腐蚀产物溶解于溶液中,而含量较少的含Fe的腐蚀产物沉积在氧化膜表面。因此Fe和Cr含量均呈现出随氧化膜由内向外无显著变化而Ni含量却明显降低的趋势。外层氧化膜中存在大量的O,这不仅由于外层氧化膜存在大量的氢氧化物,还可能由于溶液中的OH-和部分O2-附着在外层氧化膜表面。
比较不同温度下内外层氧化膜主要金属元素含量的变化不难发现,随着系统温度升高,外层氧化膜的Fe和Ni含量均有所减少,而Cr含量有所增加。但内层氧化膜中3种元素含量均变化不明显。这主要由于随温度升高,Fe和Ni金属离子扩散速度增加,含Fe和Ni腐蚀产物溶解于溶液的速度均显著增加,同时由于氧化膜厚度增加,外层氧化膜间隙增大,致密度降低,导致部分OH-,O2及O2-穿过外层氧化膜,在内外层氧化膜之间与由基体扩散出并穿过内层致密氧化膜的Fe2+和Ni2+提前反应生成Fe(OH)3和Ni(OH)2沉淀,从而造成外层氧化膜的Fe和Ni含量均有所减少,Cr含量相对增加的现象。相反,内层氧化膜由于连续致密的Cr2O3和 (Ni,Fe)Cr2O4对基体的覆盖保护作用,因此内层氧化膜中3种元素含量均无明显变化。
3.4 XPS分析
由于285 ℃浸泡后形成了稳定的双层氧化膜,故对其做XPS分析,进一步验证其表面双层氧化膜结构。在对氧化膜成分做XPS分析时,由于Ni的俄歇峰 (LMM) 与Fe2p的峰发生重合[14],且690合金为镍基合金,Ni的含量较高,对Fe2p的影响很显著,因此选用Fe3p作为Fe含量的分析依据。图10为690合金在模拟285 ℃的二回路水环境中腐蚀30 h后氧化膜主要化学成分Cr,Fe和Ni相对原子分数随氧化膜深度的变化趋势。氧化膜中Cr的含量明显高于基体的,并随着氧化膜深度逐渐降低至基体含量;相反,Ni的含量在氧化膜中很低,这与上述EDS结果相符。由于反应产物选择性溶解,大部分的含Ni腐蚀产物溶解于溶液中,从而导致外层氧化膜Ni含量很低,但随着溅射深度的增加逐渐升至基体含量。
图10 690合金氧化膜中主要组成元素的原子分数随溅射深度的变化
图11为690合金在模拟285 ℃的二回路水环境中腐蚀30 h后氧化膜中Cr,Fe,Ni和O的XPS谱及其相应的分峰图。由文献[15]可知,Cr0,Cr2O3和Cr(OH)3的结合能分别为574.0,576.2和577.1 eV。根据图11a可知,外层氧化膜中Cr(OH)3的含量较高,内层Cr2O3成为Cr的主要存在形式,基体Cr含量随着溅射深度的增加而升高。Fe0,Fe2+和Fe3+的结合能分别约为 (53±0.1),(53.7±0.1) 和 (55.6±0.1) eV[16]。图11b表明,在氧化膜/溶液界面上,Fe主要以Fe3+存在,随后Fe2+成为主要形式,可知氧化膜中Fe的存在形式逐渐由Fe(OH)3过渡到Fe3O4并最终变为稳定性强的Fe2O3。图11c为Ni2p3/2的分价谱图。Ni0,NiO,Ni(OH)2和NiFe2O4的结合能分别为:(852.2±0.1) eV (卫星峰 (857.9±0.4) eV),(854.0±0.15) eV (卫星峰 (860.5±0.2) eV), (855.6±0.3) eV (卫星峰 (861.8±0.2) eV) 和 (855.4±0.2) eV[17]。Ni的4种氧化物均存在于表面氧化膜中。而氧化膜表面Ni0的出现可能是由于Ni,Cr和Fe的化学活性依次为:Cr>Fe>Ni。从热力学上说,Ni的氧化物比其他元素在溅射中更容易被还原的缘故[18]。根据图11c能谱的变化得知,NiFe2O4的能谱只存在于氧化膜/溶液界面附近,随着溅射深度增加,Ni(OH)2的主导地位逐渐被NiO和Ni0取代。图11d显示,O1s的能量峰主要由O2-和OH-两种峰组成,结合能分别为 (530.1±0.1) 和 (531.5±0.3) eV,OH-主要存在于外层氧化膜,O2-大多存在于内层氧化膜,这也很好地印证了外层氧化膜中氢氧化物 (如Cr(OH)3和Ni(OH)2等) 的存在,内层为连续致密的Cr2O3和Fe2O3氧化膜。
图11 690合金氧化膜中主要元素的XPS谱
4 腐蚀机理分析
4.1 氧化膜形成机理
镍基合金氧化膜的形成机理目前已有广泛的报道[19-26],Ni-Cr-Fe合金的表面在高温高压碱性水环境中会形成AB2O4(A代表Fe2+和Ni2+,B代表Fe3+和Cr3+) 尖晶石类型的双层氧化膜:连续致密富Cr的内层和分散疏松富Fe的外层。已有研究[7-11]提出,由于Fe2+和Ni2+在高温高压水环境中选择性溶解以及Fe2+,Ni2+与Cr3+ 3种离子对O的亲合力不同,Cr(OH)3首先成为氧化膜的成核中心,接着高温脱水生成分散的Cr2O3核,并不断长大形成连续致密的Cr2O3氧化膜:
Cr2O3氧化膜形成后能有效阻碍Cr3+的转移,但由于Fe2+和Ni2+的离子半径比Cr3+的小,且Fe/Ni离子及Fe/Ni的氧化物,如FeO,Fe2O3,Fe3O4和NiO等,在Cr2O3中有较高的固溶度,其对Fe2+和Ni2+的阻碍作用并不明显,仍然可以通过Cr2O3氧化层扩散至表面同氧化剂离子反应生成Fe/Ni的氧化物,随后这些氧化物同Cr2O3固溶形成 (Fe,Ni)Cr2O4尖晶石 (式5)。同时外层的NiO和可以与溶液中溶解的Fe3+结合生成NiFe2O4尖晶石结构氧化膜 (式6)。最终形成内层由Cr2O3和 (Fe,Ni)Cr2O4尖晶石组成,外层由NiFe2O4尖晶石、Ni(OH)2和NiO组成的内密外疏的双层氧化膜结构,如图12所示。温度主要影响每层氧化膜中各腐蚀产物生成量大小、厚度、分布以及最终氧化膜致密度与稳定性,对内外两层氧化膜上腐蚀产物种类影响不大。
图12 690合金双层氧化膜结构示意图
4.2 温度的影响
从物质扩散角度分析,随着系统温度的升高,一方面,金属基体晶格内能和晶粒内部金属原子动能增加,晶界稳定性下降,从而使金属原子更容易从晶粒内部扩散到晶界并逸出;另一方面,逸出的金属离子和溶液中的氧化剂离子OH-,O2-及溶解的O2等扩散速度显著增加,使氧化膜厚度不断增加,金属腐蚀加剧。从氧化膜结构和形貌角度分析,随着系统温度升高,内层氧化膜中掺杂的Fe2+和Ni2+含量增加导致形成的膜更加不均匀,因此氧化膜的稳定性、致密度和对基体的保护性能都大为降低,必然造成腐蚀电流密度和腐蚀速率增加,腐蚀加剧,这些与动电位极化曲线所得结果一致 (图6)。此外,Huang等[10,11]和Douglas等[13]发现温度升高后,氧化膜表面生成的氢氧化物Fe(OH)3和Ni(OH)2等高温脱水反应速度增加,从而造成腐蚀电流密度显著增加。
5 结论
(1) 随着溶液温度的升高,690合金的自腐蚀电位下降,自腐蚀电位增加,钝化电位区间缩小,且氧化膜生长的活化能为17.86 kJ/mol,腐蚀速率主要受离子在溶液中移动速率控制。
(2) 在高温高压碱性水环境中,690合金表面生成AB2O4 (A代表Fe2+和Ni2+,B代表Fe3+和Cr3+) 尖晶石类型的内密外疏的双层氧化膜。
(3) 温度对690合金的影响主要体现在氧化膜致密度与稳定性方面,对内外双层氧化膜上腐蚀产物种类影响不大,且温度越高,氧化膜越厚,氧化物颗粒间隙越大,孔隙和缺陷越多,膜的稳定性和致密度越低,基体材料的腐蚀加剧。
The authors have declared that no competing interests exist.
免责声明:本网站所转载的文字、图片与视频资料版权归原创作者所有,如果涉及侵权,请第一时间联系本网删除。
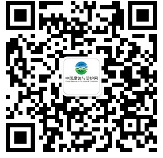
官方微信
《腐蚀与防护网电子期刊》征订启事
- 投稿联系:编辑部
- 电话:010-62316606-806
- 邮箱:fsfhzy666@163.com
- 腐蚀与防护网官方QQ群:140808414