树脂基纤维增强复合材料广泛应用于现代飞机结构中,这些复合材料结构件在服役过程中经常受到热损伤,如雷击、意外起火、武器尾烟烘烤等。 飞机树脂基复合材料的热损伤是一个发展的过程。早期阶段的热损伤,也称初始热损伤,是指在温度较低、时间较短的情况下造成的损伤。此时,材料的外表面几乎没有可察觉的变化,但其力学性能却可下降80%,因此初始热损伤的隐蔽性强、危害性大。 针对飞机树脂基复合材料的热损伤检测,叶亮、任小珍研究了碳纤维增强复合材料在电热作用下的损伤机制。樊茂华研究了复合材料层压板在火灾环境下的热响应。韩耀璋等研究了玻璃纤维增强环氧树脂基复合材料热老化性能的影响。东巳宙研究了高温环境下复合材料层合板与蜂窝板的力学性能。郭小弟等针对玻璃纤维增强复合材料提出了基于太赫兹光谱的检测方法。某公司推出了一种基于红外光谱分析的检测设备。虽然相关的研究成果比较多,但与工程实践的需求还存在一些差距,比如:基于热-弹原理的检测方法还停留在实验室原理研究阶段,没有成熟的检测设备;基于太赫兹光谱的检测方法只能适应玻璃纤维增强复合材料,且只能检测内部已经产生明显机械损伤的情况;基于红外光谱分析的检测方法主要反映材料树脂基体官能团的变化,与材料力学性能的变化不完全同步。 针对飞机树脂基热损伤检测的迫切需求和现有研究成果的局限性,侯日立等研究人员采用热损伤试验、力学性能测试、扫描电镜(SEM)分析、孔隙率检测、硬度测试等方法,研究了飞机树脂基复合材料在热作用下的性能退化规律,分析了初始热损伤的产生机制,提出了一种基于硬度测试的初始热损伤检测方法。
1 热作用下的材料力学性能退化规律 以飞机结构中常用的树脂基碳纤维增强复合材料为研究对象,根据飞机复合材料结构的典型受力环境,开展了不同条件热损伤后的拉伸试验和压缩试验。 材料的铺层方式为 [45,0,-45,90,0,45]s,在120,150,180,210,240,270,300,330,360℃下各加热1h,0°拉伸试验采用ASTM D3039—2017 《聚合物基复合材料拉伸性能的标准试验方法》标准,0°压缩试验采用ASTM D6641—2016《使用组合加载压缩(CLC)测试夹具的聚合物基复合材料的压缩性能标准测试方法》标准。试验结果如图1~4所示。 由图1~4可知:随着加热温度的升高,材料的抗拉强度和抗压强度是不断下降的,即材料在高温下发生了力学性能的退化。 值得注意的是,材料的力学性能随加热温度的变化是非单调的,呈先上升、后下降、再上升、再下降的变化规律。其规律主要表现在以下几个方面:①在材料的固化温度(200℃)以下,温度对材料性能的影响比较轻微,基本可以忽略;②在材料的玻璃化转变温度(255℃)附近,材料的强度有一个上升的反常变化;③加热温度对材料弹性模量的影响较小,虽然有波动,但基本不影响使用性能。
2 材料初始热损伤机制分析 为了进一步分析材料的初始热损伤机制,对未经加热处理的材料进行热重-差示扫描量热法试验,对不同加热条件下的材料开展了孔隙率检测和扫描电镜分析,结果如图5~7所示。 从图5可以看出:试样第一个吸热峰在350℃左右,同时伴随有失重的现象,说明此时基体材料发生了表面侧链、侧基的碎片断裂与逸出。 从图6可以看出:随着加热温度的升高,材料孔隙率呈增加趋势。温度小于150℃时的变化比较平缓,主要是材料中的水分逸出造成的;温度在150~250℃时材料的孔隙率变化比较显著,主要是基体材料中小分子组分逸出和热应力导致的裂纹造成的;在温度大于250℃时,孔隙率有一个小的下降,可能与“后固化”作用有关。 从图7可以看出:未经热作用的原试样,即室温下,其树脂是紧紧覆盖在纤维表面的,没有特别明显的界面;随着温度的升高,树脂体系的表面开始出现气孔,并且随着温度的升高,逐渐出现纤维与基体之间的贯穿性分离和纤维断裂现象。 综合上述试验和材料力学性能测试结果,飞机树脂基复合材料的初始热损伤机制如下所述。 材料的受热温度在原结构材料的固化温度(200℃)以下时,力学性能的变化是以下3种作用的结果:一是加热过程中,材料内部的水分逸出,原本由水分引发的溶胀、塑化作用减弱,导致力学性能指标上升;二是水分和基体残留小分子逸出时,在材料中产生孔隙,导致力学性能下降;三是纤维、基体热膨胀系数不匹配导致纤维/基体界面产生微裂纹,进而导致材料整体力学性能下降。当受热温度小于120℃时,材料性能主要受水分逸出,溶胀、塑化作用减弱主导,表现为强度轻微上升;当受热温度为120~150℃时,材料性能主要受基体小分子逸出、产生孔隙所主导,表现为强度下降,但变化幅度较小,对承载能力不构成威胁;当受热温度大于150℃时,除了基体小分子逸出外,热应力导致的微裂纹也开始起主导作用,导致材料中孔隙率明显上升,力学性能明显下降。这也是该种材料的最高服役温度规定为150℃的原因。 材料的受热温度在原结构材料的固化温度(200℃)与玻璃化转变温度(260℃)之间时,热应力产生的微裂纹、界面分离是主导材料性能的主要因素,表现为孔隙率急剧上升,强度明显下降,下降约15%左右。 材料的受热温度在原结构材料的玻璃化转变温度(260℃)附近时,材料力学性能出现一个反常的上升。在该温度区域,基体材料中未完全反应的小分子链继续发生交联反应,对基体材料有一定的“治愈”效果。 材料的受热温度大于原结构材料的玻璃化转变温度后,材料力学性能开始急剧单调下降。此时,主导材料力学性能变化的因素为:热应力导致的裂纹乃至纤维断裂;基体高分子材料的裂解。
3 材料初始热损伤的检测方法 3.1 人工缺陷试块的制作 研究人员制作了一批含不同程度热损伤的人工缺陷试块。从上述力学性能试验中可以看出:树脂基复合材料的热损伤程度随热损伤温度和热损伤时间的变化而变化。为了便于与强度测试结果相对应,人工缺陷试块的制作选定120,150,180,210,240,270,300,330,360℃等9个温度点,加热时间为1h。 3.2 基于硬度测试的热损伤检测 热损伤检测的目的是了解材料力学性能的衰减程度以及损伤的波及范围,以便为后续的损伤评估与修理提供依据,但力学性能参数需要由专门的试验确定,难以现场原位实施。从复合材料初始热损伤的机制看,对材料力学性能退化起主导因素的是基体,以及基体和纤维界面力学性能的退化。材料的硬度反映的是材料抵抗塑性变形的能力,因此可用硬度测试法检测材料热损伤的可能性,而且可应用于飞机金属结构热损伤检测中。 研究人员利用含不同程度热损伤的人工缺陷试块,开展了基于洛氏、巴氏硬度测试和基于纳米压痕的维氏硬度测试。其中,洛氏硬度按照标准GB/T 3398.2—1988 《塑料洛氏硬度试验方法》实施,巴氏硬度按照GB/T 3854—2017 《增强塑料巴柯尔硬度试验方法》标准实施,试验结果如图8,9所示。采用纳米压痕仪进行维氏硬度测量,按压式压头直径为20nm,测试结果如图10所示。 从上述几种硬度测试的结果看,随着加热温度的变化,材料的3种硬度都有明显变化,且与前面介绍的材料力学性能同步。因此从原理上看,3种硬度测试方法可以用来检测材料的热损伤。从检测的精度看,基于纳米压痕的维氏硬度对加热温度的变化最敏感,这主要是因为该方法测量的是显微硬度,作用力小,反映的是基体以及基体与纤维界面的性能,正好与复合材料的初始热损伤机制符合。对于巴氏硬度和洛氏硬度,由于材料变形的范围较宽,测量结果受纤维的干扰比较大。从检测的可操作性看,巴氏硬度测试是单面的,可在现场原位实施。洛氏硬度测试虽然也有可在现场原位实施的便携式设备,但由于需要双面加载,检测范围受设备尺寸限制。纳米压痕检测虽然很灵敏,但目前尚不能实施原位检测。 在现有设备条件下,可以采用洛氏或巴氏硬度测试的方法来检测树脂基复合材料的初始热损伤。在利用该方法实施检测时,应首先通过试验,分别制作材料力学性能与加热温度、硬度与加热温度的关系曲线,将该两种曲线放在同一个坐标系中(见图11),便建立了材料力学性能与硬度的关系。实际检测时,只需要进行硬度测试,并获得硬度(图11中a点的值),即可反推材料的力学性能(图11中c点的值)。结合相应修理手册中的评估标准,即可确定损伤的程度。需要特别注意的是:材料的硬度随加热温度的变化规律为非单调变化,因此检测时应从烧伤的区域开始,第一个临界点即为损伤的边界点。
4 结语 对飞机树脂基复合材料热损伤的机制进行了初步探讨,提出的基于硬度测试的方法操作简单,并能得到检测参数与材料力学性能之间的对应关系,具有较好的应用前景。
免责声明:本网站所转载的文字、图片与视频资料版权归原创作者所有,如果涉及侵权,请第一时间联系本网删除。
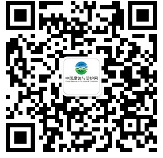
官方微信
《腐蚀与防护网电子期刊》征订启事
- 投稿联系:编辑部
- 电话:010-62316606-806
- 邮箱:fsfhzy666@163.com
- 腐蚀与防护网官方QQ群:140808414