在保证汽车的强度和安全性能的前提下,尽可能地降低汽车的整备质量,从而提高汽车的动力性能,减少燃料消耗,降低排气污染。据相关数据统计整车重量减少100Kg相应油耗降低0.4L/100Km,CO2排量降低-10g/100km,因此轻量化已经成为世界汽车发展的潮流和趋势[1]。
汽车轻量化技术是设计、材料与制造技术的集成应用,实现汽车轻量化主要途径主要有两个途径:(1)新材料应用:主要采用轻量化材料和轻量化材料成型技术,以达到减轻零部件重量的目的。(2)结构优化设计:使零部件薄壁化、中空化、小型化、复合化以及对零部件进行结构和工艺改进等。其中材料轻量化包括高强钢、镁合金、铝合金、工程塑料及其复合材料和陶瓷材料等应用[2]。
本文主要从材料轻量化(高强度钢)和结构优化设计两个方面探讨高强钢在汽车底盘零部件方面的设计与应用,从而实现整车的轻量化。
随着汽车材料技术的飞速发展,现代汽车制造材料的构成也在不断发生变化。以现代轿车用材为例,按照重量换算,钢材占汽车自重的55%~60% ,铸铁占5%~12%,有色金属占6%~10%,塑料占8%~12%,橡胶占4%,玻璃占3%,其他材料(油漆、各种液体等)占6%~12%。汽车应用材料比例如图1所示。
图1 汽车应用材料比例图
由于钢铁材料在强度、塑性、抗冲击能力、回收使用及低成本方面具有综合的优越,其在汽车材料中的主导地位仍是不可动摇的。但高强度钢和超高强度钢的应用,如汽车车身、底盘、悬架、转向等零部件上,将继续有较大增长。据相关数据统计,高强度钢在汽车底盘件上应用相对于普通钢材减重约30%,相对铝合金成本约低于30%。
高强度钢在汽车零部件应用优势主要体现在两个方面:(1)采用高强度钢板可以达到减薄车身用板的厚度和重量的目的, 在轻量化的同时,增加了安全性能。据相关资料数据表明,当钢板厚度分别减小0.05mm、0.01mm和0.15mm时,车身减重分别为6%、12%和18%。(2)高强度钢一般是指冷轧340MPa、热轧490MPa以上的钢,这些新型高强度钢板具有较低的屈强比、较好的应变分布能力和较高的应变硬化特性,同时高强度钢板的力学性能更加均匀,从而具有更好的碰撞特性和更高的疲劳寿命。
高强钢可分为传统高强钢(CHSS)和先进高强(AHSS。常用的先进高强度钢主要有复相(CP)钢、双相(DP)钢、相变诱发塑性(TRIP)钢和孪生诱发塑性(TWIP)钢等几种。传统的高强钢多是通过固溶处理和晶粒细化达到强化效果的。目前常用的传统高强钢为:高强度 IF 钢(HSIF)、烘烤硬化(BH)钢、冷轧各向同性(IS)钢、冷轧高强度含 P 钢和高强度低合金(HSLA)钢。
超高强度钢在汽车底盘零部件中的应用是比较广泛的,以汽车前悬架中工况较复杂的前悬架摆臂设计为例。某车型前摆臂方案设计CAE性能分别以L1和L2级工况为输入条件,L1和L2级工况分别见表1、表2。
表1 前悬架摆臂L1级工况要求
表2 前悬架摆臂L2级工况要求
前悬架摆臂设计过程中摆臂本体可以通过选择不同的材料进而采用不同的结构设计方法,满足L1和L2级工况要求[3]。以下对前悬架摆臂本体分别采用高强度钢、超纲强度钢进行不同的结构设计进行研究,设计思路见表3:
表3 前悬架摆臂设计思路
以下针对两种思路分别进行设计分析研究:
(1)思路一:前悬架摆臂本体材料常用的高强度刚SAPH370、SAPH400、SAPH440、QStE360、QStE380、QStE420、QStE460,经过性能、成本、工艺等因素综合要求[5][6],选取材料QStE460及双片扣合结构形式经CAE分析满足要求[7],CAE仿真分析如下。
L1级工况分析如下:
图2 L1级载荷Fx向塑性应变云图
图3 L1级载荷Fy向塑性应变云图
图4 L1级载荷Fz向塑性应变云图
图5 L1级载荷MZ_LE向塑性应变云图
图6 L1级载荷MZ_TE向塑性应变云图
图7 L1级载荷nFZ向塑性应变云图
根据CAE仿真选取前悬架摆臂在L1级工况下,选取Fx、Fy、Fz、MZ_LE、MZ_TE、nFZ各个方向塑性变形最大值与L1级工况塑性应变应要求对比分析结果如表4所示。
表4 L1级工况塑性应变分析结果
L2级工况分析如下:
图8 L2级载荷Fx向应力云图
图9 L2级载荷Fy向应力云图
图10 L2级载荷Fz向应力云图
图11 L2级载荷nFZ向应力云图
根据CAE仿真选取前悬架摆臂在L2级工况下,选取Fx、Fy、Fz、nFZ各个方向应力最大值与应力要求对比分析结果如表5所示。
表5 L2级工况应力分析结果
前悬架摆臂本体采用材料QStE460及双片扣合结构形式在满足L1、L2级工况下,结构图示及设计重量见表6:
表6 某前悬架摆臂高强度钢应用情况
(2)思路二:前悬架摆臂本体材料常用的超高强度刚SAPH590、SAPH780、SAPH440、QStE550、QStE600、780HB,经过性能、成本、工艺等因素综合要求,选取材料780HB及单片式的结构形式经CAE分析满足要求,经双片式结构分析可以看出风险工况为L1、L2级工况Fx、Fy向,现将风险工况仿真分析结果例举如下。
L1级工况分析如下:
图12 L1级载荷Fx向塑性应变云图
图13 L1级载荷Fy向塑性应变云图
根据CAE仿真选取前悬架摆臂在L1级工况下,风险工况方向Fx、Fy各个方向塑性变形最大值与L1级工况塑性应变应要求对比分析结果如表7所示。
表7 L1级工况塑性应变分析结果
L2级工况分析如下:
图14 L2级载荷Fx向应力云图
图15 L2级载荷Fy向应力云图
根据CAE仿真选取前悬架摆臂在L2级工况下,选取风险工况方向Fx、Fy各个方向最大应力与要求值对比分析结果如表8所示。
表8 L2级工况应力分析结果
前悬架摆臂本体采用材料780HB及单片式的结构形式在满足L1、L2级工况下,结构图示及设计重量见表9:
表9 某前悬架摆臂超高强度钢应用情况
在同等工况及重量要求下,分别采用高强度钢和超高强度钢对某车型前摆臂进行设计与分析得出以下结果:
(1)采用高强度钢QStE460和超高强度钢780HB进行结构设计分析均可以满足L1、L2级工况要求;
(2)采用高强度钢时需要采用上、下两个片体进行设计,应力集中及塑性变形强的区域还需要局部增加加强件等措施,而采用超高强度钢进行设计时则直接采用单片式的结构设计,在应力集中及塑性变形强的区域只需要修改该区域曲面造型增强强度即可。
(3)采用超高强度钢设计前悬架摆臂重量比采用高强度钢设计后的重量要减轻约21.2%,提升了底盘件在轻量化设计的应用。
(1)同等工况下,超高强度钢与高强度钢在前悬架摆臂设计上更好体现出零部件薄壁化、中空化、小型化、复合化以及对零部件进行结构和工艺改进更能实现。
(2)同等条件下,超高强度钢与高强度钢在不同结构优化之下,前者设计重量能够比后者减轻21.2%,提供了高强度钢在底盘件上的轻量化解决方案。
(3)根据材料本身性能相比而言,超高强度钢延伸率不及高强度钢。因此在冲压成型时拉延深度比较大的零部件容易出现开裂等缺陷,因此采用超高强度钢在产品设计之初就需要更加关注冲压CAE成形分析。
免责声明:本网站所转载的文字、图片与视频资料版权归原创作者所有,如果涉及侵权,请第一时间联系本网删除。
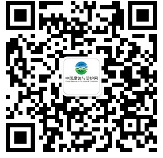
官方微信
《腐蚀与防护网电子期刊》征订启事
- 投稿联系:编辑部
- 电话:010-62316606-806
- 邮箱:fsfhzy666@163.com
- 腐蚀与防护网官方QQ群:140808414