海水循环泵是压水堆核电站海水循环系统(CRF)的关键能动设施,齿轮箱作为其中的重要部件,其作用为:将电机通电后产生的高转速、低扭矩动能转换为低转速、高扭矩动能,并将该动能传递到海水循环泵叶轮,使海水流向凝汽器、闭式冷却水换热器等设备,完成对相关设备的充分冷却。连接螺栓是保证齿轮箱安全稳定承载和传递运动的关键机械零件,这些螺栓往往为8.8或10.9级的高强螺栓。作为一种典型的多缺口零件,高强螺栓在服役时多承受拉应力,且应用于振动设备上螺栓的受力情况更为复杂,其服役过程中除受到预紧拉应力外,还要承受因设备振动而产生的周期性脉动载荷和冲击载荷。与同材料的其他缺口件相比,因螺纹的存在,螺栓的疲劳强度明显偏低,因此高强螺栓在交变载荷的作用下,在螺纹处发生疲劳断裂的可能性较大。吴玉枝等发现汽车前桥紧固件10.9级高强螺栓因调质处理时气氛碳势过高,表层形成了渗碳层,以及牙底圆弧半径较小导致螺栓承载时产生了应力集中,并发生疲劳断裂。GONZ?LEZ等研究了螺钉的裂纹起源,发现螺钉多断裂于螺纹的根部,螺钉中氢元素降低了其抗疲劳性能,最终导致螺栓因静态过载而断裂。王荣等研究发现,螺栓制造过程中产生的锻造折叠,及经过拉拔而产生的线状缺陷分布,容易使螺栓产生应力集中,在强大的淬火应力作用下螺栓易沿轴向发生开裂。针对10.9级高强度六角螺栓服役过程中R角处断裂失效的案例研究则少有报道。
某10.9级高强度齿轮箱连接螺栓发生断裂,其规格为42mm×430mm(外径×长度),来自福建宁德核电有限公司和苏州热工研究院的廖雪波、蒲晶菁等研究人员采用宏观观察、化学成分分析、硬度测试、金相检验、扫描电镜(SEM)及能谱分析等方法对该螺栓断裂的原因进行了分析,为在交变载荷下高强螺栓的工程应用及其服役寿命评估提供了参考。
1 理化检验
1.1 宏观观察
断裂螺栓的宏观形貌如图1所示。由图1可知:螺栓断裂于头部R角处,螺杆及六角头部位未见明显的塑性变形,呈现脆性断裂特征;断口较平整,整体呈灰色,可观察到明显的裂纹源区、裂纹扩展区及瞬断区;扩展区平坦、光滑且颜色较暗,呈半月形,且逐渐由边缘向心部扩展,面积约为断口总面积的25%,呈现疲劳扩展形态;断裂螺栓的R角半径为1867μm,符合GB/T 5783—2016 《六角头螺栓 全螺纹螺栓》的要求(≥1200μm)。
1.2 金相检验
对断裂螺栓裂纹处(六角头断口起源位置)及螺纹处进行金相检验,结果如图2,3所示。由图2可知:六角头表面显微组织与心部组织存在较大差异,表面存在半脱碳层,表面组织为索氏体+铁素体;心部组织为回火索氏体;断口下方存在二次裂纹,裂纹平直,起源于表面,向螺栓心部扩展;在裂纹源附近存在部分细小裂纹,细小裂纹均位于螺栓表面半脱碳层位置。由图3可知,螺纹处未见脱碳层,表明六角头位置的半脱碳并非产生于螺栓热处理过程中,
而是产生于六角头成形过程中。
螺栓六角头多采用镦头成形的加工方式,在镦头成形过程中,螺栓的加热方式为局部加热。在加热过程中,加热速率过慢或在高温区域停留时间过长会使Fe3C在高温下与O2,H2O等发生反应,表面组织中Fe3C减少使螺栓边缘及R角处的铁素体含量增加,造成六角头位置表面半脱碳,形成厚度约为100μm~150μm的铁素体+索氏体层。铁素体的存在降低了材料表面的硬度,使得R角处容易因摩擦而发生划伤,同时还降低了螺栓表面的疲劳强度,使螺栓产生疲劳裂纹。
1.3 化学成分分析
采用火花光谱仪对螺栓靠近断口的杆部进行化学成分分析,根据实验结果可知断裂螺栓的元素含量符合GB/T 3098.23—2020 《紧固件机械性能螺栓、螺钉和螺柱》对10.9级碳钢的要求。
1.4 硬度测试
对断裂螺栓R角处半脱碳区域进行硬度测试,结果如表1所示。由表1可知,R角处半脱碳区域硬度分布不均匀,半脱碳区域中铁素体含量较多的位置(表面)硬度较低,索氏体含量较多的位置(次表面)硬度较高。
表1 断裂螺栓R角处半脱碳区域硬度测试结果
1.5 SEM及能谱分析
图4为断口的SEM形貌。由图4a),4b)可知:裂纹起源于R角根部,呈台阶状,由螺栓外表面向内部扩展;裂纹源区侧面(靠近断口的R角根部)存在严重的摩擦及挤压痕迹,摩擦处呈现平行或垂直于螺栓轴线的沟壑状,摩擦或挤压区域存在大量微裂纹,裂纹多垂直于螺栓轴线方向,少数裂纹与螺栓轴线方向呈一定角度分布。
由图4c),4d)可知:裂纹扩展区呈半月状,表面光滑,无明显的塑性变形,扩展区靠近边缘位置存在大量疲劳辉纹,辉纹细腻紧密,说明裂纹扩展速率较慢,呈疲劳特征;随着扩展区向内部推进,疲劳辉纹呈短粗状分布,断口呈准解理特征分布。
由图4e)可知:终断区面积较大,约占断口总面积的3/4,表面呈颗粒状,颗粒形态呈现由过渡区向螺栓另一端撕裂状,为典型的过载瞬断断口形貌。断口特征为等轴状韧窝,少数韧窝中存在非金属夹杂物,可见该裂纹扩展时主要承受拉伸-弯曲交变应力。疲劳断面与瞬断断面之间分界明显,可见螺栓疲劳开裂后,在某一瞬间因承受过载应力而突然断裂。
图5为断口侧面的EDS分析结果,可知靠近断口侧面主要元素为Fe,未见Zn元素,随着与断口的距离变大,Zn元素含量逐渐增加。表明螺栓表面存在镀锌层,该区域发生了严重摩擦现象,表面镀锌层因摩擦而发生脱落。
2 综合分析
上述理化检验结果表明,该断裂螺栓的化学成分、硬度及力学性能均满足GB/T 3098.23—2020对10.9级螺栓的要求。金相检验结果显示,螺栓心部组织与边缘及R角处的组织存在较大差别,心部组织为回火索氏体,边缘及R角处的组织为索氏体+铁素体,表明六角头边缘及R角处发生了脱碳。螺栓螺纹处脱碳层检测结果显示,六角头边缘及R角处脱碳并非产生于螺栓热处理过程中,而是产生于六角头热镦成形过程中,且这一过程中六角头加热缓慢或在高温处停留时间过长,导致Fe3C在高温下与O2,H2O等发生反应,使螺栓内部的Fe3C减少,从而增加了螺栓边缘及R角处的铁素体相,引起了脱碳。脱碳层的存在使得螺栓边缘处疲劳强度降低,容易引发微裂纹。
根据螺栓断口宏观及微观分析结果可知,断口呈疲劳断裂特征。裂纹源区侧面存在严重的摩擦及挤压痕迹,摩擦处呈现平行或垂直于螺栓轴线的沟壑状。发生摩擦或挤压的区域内存在大量微裂纹,裂纹多垂直于螺栓轴线方向分布。结合EDS分析可知,未发生摩擦或挤压区域的表面存在镀锌层,而发生摩擦或挤压区域的金属裸露在外,未发现镀锌层。由此可推断,裂纹源区侧面摩擦或挤压痕迹为安装或服役过程中产生的,摩擦或挤压区域位于六角头脱碳部位,脱碳层的存在使材料表面硬度及耐磨性降低,导致R角在与法兰螺栓孔边缘接触过程中,因摩擦而产生折叠或微裂纹,这些折叠或微裂纹成为螺栓早期裂纹形成与扩展的疲劳源。
该螺栓用于齿轮箱内齿圈与箱体法兰,长期承受持续的振动应力和循环交变应力,造成了R角微裂纹处应力叠加或应力集中,从而导致疲劳裂纹的产生。当疲劳裂纹扩展面积约占表面的25%时,剩余面积无法承载因螺栓紧固及振动而产生的拉应力,最终导致螺栓过载断裂。
3 结论
该10.9级螺栓的断裂性质为疲劳断裂,断裂原因为螺栓表面脱碳层中铁素体的存在降低了螺栓的表面硬度和耐磨性,螺栓在拆装过程中与螺栓孔边缘发生摩擦并产生了折叠或微裂纹,这些折叠或微裂纹成为螺栓早期裂纹形成与扩展的疲劳源。
免责声明:本网站所转载的文字、图片与视频资料版权归原创作者所有,如果涉及侵权,请第一时间联系本网删除。
相关文章
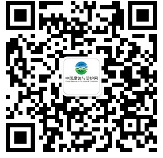
官方微信
《腐蚀与防护网电子期刊》征订启事
- 投稿联系:编辑部
- 电话:010-62316606-806
- 邮箱:fsfhzy666@163.com
- 腐蚀与防护网官方QQ群:140808414
点击排行
PPT新闻
“海洋金属”——钛合金在舰船的
点击数:8211
腐蚀与“海上丝绸之路”
点击数:6536