石化行业面临的安全压力
响水事件现场图
★石化是设备腐蚀的重灾区★
★工艺设备联动是防腐的★
不二法则
从国内外炼油装置的防腐经验与所采取的防腐技术看,对付炼油装置高温部位腐蚀均以材料防腐为主、工艺防腐为辅,为对付低温部位则是以工艺防腐为主、材料防腐为辅;
高硫、高酸原油加工装置选材导则(SH/T3096及SH/T3129)的颁布与实施,基本消除了炼油装置高温部位由于材料选择导致的腐蚀问题;
但是,受制于加工原料性质多变、工艺操作波动较大以及工艺防腐的实施细节影响因素较多等多重因素影响,炼油装置的低温腐蚀(盐酸露点腐蚀、铵盐结晶)控制难以达到令人满意的效果;
常减压装置低温部位的腐蚀问题,受原料来源多变、工艺防腐措施的执行存在偏差以及工艺操作波动等诸多因素的影响,难以得到良好的控制;
有的塔顶注水量稍显不足,在注入点没有形成足够的液态水,消除露点的腐蚀;
有的企业采用40℃以下的冷回流19吨/小时,冷回流汽化吸收大量热,造成局部温度过低引起局部盐酸凝结,造成塔壁腐蚀;
缓蚀剂的筛选与评价存在问题,应依据塔顶油气的具体冷凝冷却工艺过程,分温度段评价才能筛选出符合实际情况性能优良的缓蚀剂;
塔顶回流对于控制与调整塔顶温度十分灵敏,一方面因为其温度较低,更主要的是塔顶回流在塔顶汽化,需要吸收大量的相变热,虽然这对于调节塔顶温度十分有益,但是同时可导致塔顶部位局部的低温区,不但导致盐酸的凝结,也会提高氯化铵结晶的可能性;
关于铵盐:原油中的含氮化合物在常减压装置分解率较低,防止积盐的重要途径是控制原料携带的NH3含量并阻止其在分馏塔顶聚集;
防止常压塔铵盐沉积的方法应注意控制氨的引入,最好采用初馏塔工艺。
在焦化原料热裂解过程中,油品中的含硫化合物可分解生成硫化氢,含氮化合物可分解生成氨,氨在热的作用下可进一步反应生成CN-。因此焦化分馏塔塔顶冷凝冷却系统与富气压缩机机间和出口冷却系统H2S-HCN-H2O腐蚀环境,同时含有大量的NH3和少量的氯离子。如果pH值过高,会导致积盐和结垢,引起垢下腐蚀。因此,需要注水,稀释腐蚀性物质,并降低溶液的pH值;
焦化装置分馏塔铵盐沉积不但影响正常生产,而且对铵盐的冲洗,对设备、管道的安全运行也带来了严重威胁;
焦化装置分馏塔铵盐沉积主要是由于常减压装置无机盐未彻底水解或焦化装置掺炼含氯污油引起,所以控制焦化装置分馏塔铵盐沉积的方法应注意控制进入焦化装置的氯;
焦化装置低温系统的腐蚀问题主要发生在分馏塔及其塔顶冷凝冷却系统,和富气压缩机系统。主要腐蚀类型为H2S-NH3-H2O腐蚀及铵盐结晶问题。
硫、氯、氮平衡分析
★关注石化设备防腐重点★
(以常减压装置为例)
控制进装置原油性质与设计原油相近,且原油的硫含量、酸值,原则上不能超过设计值。
露点腐蚀:控制排烟温度,确保管壁温度高于烟气露点温度5℃以上,硫酸露点温度可通过露点测试仪检测得到或者烟气露点计算方法估算。
★石化腐蚀预测技术★
大数据分析
以上相关数据,炼油企业均具有成熟的手段进行调控或采集,在发现腐蚀隐患和指导解决腐蚀问题方面起到了良好的效果。
针对海量的数据,企业通常利用信息化方式将其进行分析处理。
然而,如某炼化公司统计,其在各个装置运行期间,DCS系统每天会产生过程归档数据约4.7亿个,2015年10月期间产生各类报警信息约8500条,工艺操作记录约9500条,这些工艺管理、设备管理和安全管理的基础信息,使用率却不及每天归档的4.7亿个的10%。
DCS系统产生的庞大数据量,同类信息的时间跨度存在不同,且腐蚀监测系统是典型的多源传感器系统,分布在不同的控制系统和不同的生产装置中,技术管理人员在横向统计分析时耗时耗力,很可能错过发现隐患和解决问题的时机。
此外,国内大部分石化企业通常采用OPC加实时数据库的方式,将这些原始数据采集到专门的管理平台,若工艺条件发生变化,数据不能及时得到更新,无法真实同步反应工厂各装置的实时情况。
国外的炼化企业早在90年代就开始将炼油传统的挂片检测、壁厚检测升级到在线电化学监测,并开始意识到需要针对腐蚀相关数据进行分析和有效利用,建立模型用于间接推测腐蚀状态,先后出现了BP神经网络预测模型、Fe2+/Fe3+预测模型、Hemandez人工神经网络预测模型等。
近年来,国内一些研究机构(如青岛安工院)开发了一套集在线、离线监检测数据于一体的为腐蚀分析提供便利的腐蚀数据管理系统,其次运用深度学习方法对炼化企业累积的海量数据进行深度分析,关键装置的工艺参数和水质分析数据进行学习训练,建立关键信息与其他监测之间的黑盒模型,达到根据工艺状态快速、准确的预测目的,为指导企业腐蚀防护工作奠定理论和技术基础。
腐蚀预测模型避免了受成本和技术限制,生产中难以对腐蚀关键参量进行实时掌控的问题,及时的数据预测可为切实指导装置防腐工作提供技术支持。
★技术需求与建议★
免责声明:本网站所转载的文字、图片与视频资料版权归原创作者所有,如果涉及侵权,请第一时间联系本网删除。
相关文章
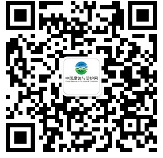
官方微信
《腐蚀与防护网电子期刊》征订启事
- 投稿联系:编辑部
- 电话:010-62316606-806
- 邮箱:fsfhzy666@163.com
- 腐蚀与防护网官方QQ群:140808414
点击排行
PPT新闻
“海洋金属”——钛合金在舰船的
点击数:8188
腐蚀与“海上丝绸之路”
点击数:6503