摘要
氧化石墨烯(GO)作为一种典型的二维层状材料在表面防护领域具有较大的应用潜力,然而其团聚现象和表面大量纳米孔隙的存在往往会削弱其对基体的保护作用。将硬脂酸(SA)接枝到 GO 片层并采用自组装的方法,在 AZ31B 镁合金表面制备 SA-GO 复合涂层。采用 SEM、XRD 和 FT-IR 表征涂层的表面形貌、结构以及官能团;采用接触角测试仪、电化学工作站和摩擦磨损试验机分别表征涂层的润湿性、耐蚀性以及耐磨性。电化学测试结果表明,该复合涂层的引入使得腐蚀电流密度降低了约三个数量级,显著提高了镁合金基体的耐蚀性,这与涂层孔隙率的降低以及疏水性的增加有关。摩擦测试结果表明:与镁合金基体相比,SA-GO 涂层的磨损率降低了 99.3%,摩擦因数降低了 83.1%,这与 SA 的自润滑性能以及 GO 层间距增加导致 GO 片层更易滑移有关。研究成果为实现金属表面防腐/耐磨一体化防护研究提供了实验依据和理论基础。
关键词: 镁合金 ; 氧化石墨烯 ; 硬脂酸 ; 防腐性 ; 耐磨性
0 前言
镁合金以其低密度、高比强度、优越的生物相容性和电磁屏蔽性能等,在工业上有着极大的应用潜力[1-3]。然而,镁的化学性质活泼,且自然形成的氧化层主要由MgO/Mg(OH)2 组成,质地疏松多孔,不能为基体提供有效的保护[4-5]。因此,耐蚀性和耐磨性差极大地影响了镁合金的使用寿命,限制了其应用范围。目前,已经开发了多种表面处理技术来提高镁合金的防腐性能,如化学转化、阳极氧化、物理气相沉积和有机涂层等[6-8]。其中,有机涂层因其成本低、污染小、操作简单等优点受到广泛关注。然而,单一的有机涂层力学性能较差,易出现微裂纹或小缺陷,使其性能急剧恶化[9]。制备有机/无机复合涂层是克服这一缺点的有效方法。
石墨烯是典型的二维纳米级材料,由于其独特的性能(包括不透气性、耐酸/碱性、良好的力学性能和高的比表面积等[10-12])而备受关注。陈宁宁等[13]通过石墨烯/硬脂酸(SA)混合溶液对微弧氧化层进行封孔处理,进而提高镁合金的耐腐蚀性能。然而,石墨烯片层表面缺乏可键合的官能团,简单的机械混合容易导致涂层结合力差以及成分分布不均匀等问题。而氧化石墨烯(GO)作为石墨烯的化学衍生物,其表面具有丰富的含氧基团,例如羟基、环氧化物和羧基官能团等,这使其与基体的化学键合成为可能[14-15]。但是,GO表面上这些氧化区域导致其表面存在许多固有的纳米微孔,并能通过氢键的相互作用使得水分子或其他腐蚀性离子得以渗透进入基体表面[16-19]。因此,单一的GO涂层难以为金属提供长期的耐腐蚀性。幸运的是,有机和无机方法的结合可以改善这种情况。CHU等[20]报道了在镁合金上制备类似“砖砂浆”结构的rGO-PVA组成的复合涂层,在一定程度上提高了镁合金的耐蚀性和磨损率。WANG等[21]在AZ31B镁合金表面上开发了硅烷/GO/硅烷复合涂层,有效阻止了腐蚀性Cl离子和H2O分子的渗透,表现出优异的耐腐蚀性。SA具有良好的疏水性和润滑性,分子链上的羧基可以与GO表面的羟基反应并附着在表面的氧化区域上,具有进一步改进镁合金的抗腐蚀和耐磨性的潜在应用前景[22-23]。
本文将SA接枝到GO片层上,通过自组装法在AZ31B镁合金表面制备SA-GO复合涂层,以提高镁合金的耐腐蚀和耐磨性能。SA分子链可以填充GO片层表面固有的纳米微孔,并提高其完整性和疏水性。结果证明,SA-GO涂层表现出良好的抗腐蚀和抗磨损性能,在镁合金表面保护方面具有广阔的应用前景。
1 试验
1.1 镁合金预处理
AZ31B镁合金购自广东红旗金属材料有限公司。将镁合金板切成10mm×10mm×2mm的尺寸,然后依次用粒度为800~2 400的SiC砂纸打磨所有镁合金基体样品,并将其表面粗糙度控制在338nm左右。依次用丙酮、乙醇和去离子水分别超声清洗5min。然后,将镁合金基体浸入到6.0M NaOH溶液中3h,以生成均匀的氢氧化物层(Mg-OH)。
1.2 涂层制备
GO是通过改良的Hummers方法[24]由天然石墨粉制成。SA由国药集团化学试剂有限公司提供。首先,将SA粉末(40mg)分散在乙醇(20mL)中以形成溶液A;然后将GO粉末(20mg)在20mL乙醇中以40W超声处理1h,形成溶液B。接下来,将溶液A和B在烧杯中混合,并在80℃下水浴搅拌11h。之后,将混合溶液离心并用乙醇反复洗涤以除去过量的硬脂酸,将产物干燥并以1wt%的含量在去离子中水超声处理(40W,1h)。最后,使用自组装方法将SA-GO复合材料逐渐沉积在羟基化的镁合金衬底表面上,并在80℃下真空干燥。
1.3 性能表征
通过扫描电子显微镜(SEM,JSM-IT100,JEOL) 表征样品的表面形貌。采用能量分散谱仪(EDS) 确定样品表面成分。利用表面轮廓仪(ContourGT, K0)测试样品表面粗糙度(Ra),测试范围为475 μm × 360 μm。通过X射线衍射仪(XRD,MAX2500VB3 +/PC,Rigaku)对涂层进行表面结构分析。通过傅里叶变换红外光谱(FT-IR)的全反射方法检测涂层的官能团。
使用电化学工作站(CS350,Corrtest)在标准NaCl溶液(3.5wt%)中进行电化学测试。电化学测试均使用传统的三电极法进行,每个样品进行3次测试,最终数据为3次的平均值。在经过300s的开路电势测试后测量样品的电化学阻抗谱,扫描频率为105~10 2 Hz。在10mV·s 1 的扫描速率下进行电位动力学极化试验。使用塔菲尔外推法计算腐蚀电位 (E corr)和腐蚀电流密度(i corr)并评估其耐蚀性。腐蚀速率(Pi)可通过式(1)计算得出[25-26]:
(1)
通过摩擦磨损试验机(UMT-2,CETR,美国) 在室温环境下以点-盘接触模式、0.01m/s的滑动速度、100mN的负载下对制得的样品进行摩擦学性能测试。采用振幅为5mm的往复运动,对偶试样为直径3mm的AISI5200轴承钢球,湿度约为60%。所有测试均进行3次,最终数据为3次的平均值。通过表面轮廓仪测试磨损情况(同样条件下对摩30min)并计算其磨损率,用SEM观察磨损痕迹的形态,并通过EDS确定磨痕处的成分。试样的磨损率可以用公式(2)计算得出:
(2)
式中,δ 为磨损率(mm 3/N·m);A 为试样横截面处的磨损面积(mm 2);L 为磨痕长度(mm);F 为垂直载荷(N);T 为摩擦时间(min);f 为频率(Hz)。
2 结果与讨论
2.1 表面形貌与组成成分
图1 为得到的镁合金表面GO涂层和SA-GO复合涂层的表面以及横截面的SEM形貌图及EDS谱图。可以看到,镁合金基体表面已经分别被GO(图1a)以及SA-GO(图1b)覆盖。在图1a中,GO涂层平整致密,厚度约为2.12 μm,其 Ra 值约为207nm。同时,可以观察到许多波纹和褶皱出现在涂层表面,这归因于GO大的比表面积所引起的片层团聚现象[27]。由EDS谱图可以看出一定含量的C元素和O元素的存在,进一步证明GO涂层的成功制备。此外,通过所制备样品的SEM图可以发现,GO涂层易出现起翘,与基体结合差的情况。这与GO片层的高表面能引起的团簇有关。相比之下,SA-GO涂层的样品表面更加平坦致密(图1b),厚度约为2.81μm,其 Ra 值约为125nm。这与SA与GO片层表面的羟基官能团的反应有关,大大削弱了GO片层之间氢键以及范德华力的作用,从而从一定程度上阻碍了GO片之间的吸引力相互作用。EDS谱图中C元素含量的显著增加也说明了SA的成功接枝。于此同时,接枝后的SA分子附着在GO片层表面可填充GO表面存在的纳米微孔。因此,在接枝SA分子链后,复合涂层能为基底提供更好的耐蚀性能。
图1 不同涂层的SEM图像及EDS谱图
图2 为不同涂层的XRD图谱。结合布拉格方程(2d sin θ=nλ),可以得出,在接枝SA后,GO的片层间距从0.904nm (2θ ≈ 9.78°)增加到0.975nm (2θ ≈ 9.06°)。这是由于在改性后,SA分子会填充到GO片层间,从而增大了片层间距。片层间距的增加使得GO在摩擦过程中更易剥落填充到摩擦副间,从而起到减磨效果。从图中还可以观察到, SA-GO涂层中SA的特征衍射峰尖锐且清晰,证明SA成功附着在GO片层的表面[28]。
图2 不同涂层的XRD图谱
图3为SA粉末、GO涂层和SA-GO涂层的FTIR光谱。可以看到,GO涂层和SA-GO涂层在3 250~3 404cm1 的波峰处都出现宽峰,这对应于GO上的羟基的拉伸振动峰。此外,与GO涂层相比,SA-GO涂层在3 404cm -1 处的峰强度减弱,这与接枝SA有关,使其表面羟基减少。SA-GO涂层在2 923cm 1 和2 848cm 1 处的峰分别对应于-CH2-的不对称和对称拉伸振动峰。SA-GO涂层在1 737cm 1 处的强峰归因于改性后C=O的对称拉伸振动 [29]。在1 561cm 1 和1 379cm 1 处出现的峰对应于涂层和基材之间羧酸盐的形成,这两个峰对应于结构的反对称和对称拉伸振动[20]。因此,SA成功接枝到GO的表面。
图3 不同涂层的FT-IR图谱
2.2 SA-GO复合涂层结合力分析
采用十字划格法对SA-GO复合涂层的结合力进行测试,测试结果如表1所示。可以看到涂层脱落面积在5%~7%,达到国标的1至2级合格水平。说明该复合涂层与基底之间具有较好的结合力。
表1 SA-GO涂层结合力测试
2.3 涂层润湿性能分析
镁合金基体、GO涂层和SA-GO涂层的水接触角如图4所示。与镁合金基体相比,GO涂层的水接触角为4.5°,远小于70.5°,这与其表面上具有丰富的含氧基团以及大的比表面积有关。而在涂覆SA-GO涂层后,水接触角增加到98°,这是由于GO表面被SA化学接枝后导致复合涂层的疏水性增加。疏水性的增加能从一定程度上减少涂层与腐蚀性介质的接触,从而降低腐蚀发生的机率[30]。
图4 不同样品的水接触角
2.4 耐蚀性能分析
将所制备样品浸入3.5wt%NaCl溶液中进行电化学性能测试,图5所示为所得到的样品的动电位极化曲线图,表2为相应的极化曲线的Tafel拟合数值。从图中可以观察到,由于表面缺少有效防护,镁合金基体在极化过程中,电流密度快速升高。而GO和SA-GO样品很快进入钝化区,但由于钝化电流很低,在 0.72V和 0.26V附近出现了点蚀。但镁合金基体的腐蚀电流很高,一直增加,在0V时依然要高于GO和SA-GO样品,腐蚀更严重。另外, SA-GO样品的钝化区比GO更宽,钝化电流更低, SA-GO比GO具有更好的对镁合金的保护性能。因此,GO和SA-GO涂层都可以为镁合金提供一定的防护作用,且SA-GO的防护效果更好。但是随着所加极化电位的进一步升高,不可避免地有少部分腐蚀性阴离子渗透涂层到基体表面,导致点蚀的发生。此外,通过对比发现,在涂覆GO涂层后,腐蚀电位有一定程度的升高,且腐蚀电流密度降低了约一个数量级。这与GO良好的屏蔽作用有关,但是表面氧化微孔的存在以及其超亲水性使得耐蚀性能提升有限。而在涂覆SA-GO涂层后,样品表现出最高的 E corr、最低的 i corr 和最低的 Pi。而且与镁合金基体相比,SA-GO涂层的 E corr 提高了300mV,i corr 降低了近2个数量级,Pi 减少了99.5%。这与复合涂层疏水性的提升以及在GO层间填充SA后致密性得到提高有关。因此,SA-GO涂层表现出最佳的防腐性能。
图5 不同样品的动电位极化曲线
表2 动电位极化曲线的塔菲尔拟合结果
图6 为涂层的Nyquist图和Bode图以及等效电路图。通常,高频区域的电容回路与样品和电解质之间界面处的电荷转移反应有关;低频回路表示金属-电解质界面的电荷转移电阻和双层电容[31]。由图6a可以看出,与镁合金基体相比, GO和SA-GO涂层试样的高频电容环直径大小明显增加,这表明镁合金的耐蚀性得到了改善,并且SA-GO能为基底提供最佳的耐蚀效果。裸露的镁合金呈现出低频感应环路,表明镁基底受到严重腐蚀,并且镁基体出现弛豫现象[32]。但是,GO和SA-GO涂层可以有效限制Mg合金的腐蚀。在Bode图中,较低频率下的阻抗模量(|Z|0.01Hz)通常用作评估涂层防腐性能的重要半定量指标[33]。可以看出,所有样品中,SA-GO的|Z|0.01Hz 值最高,表明所制备的SA-GO复合涂层可以为Mg合金提供最佳的耐腐蚀性能。由图6c可以观察到, SA-GO复合涂层在中频或高频时表现出最高的相角和一个宽峰,这表明腐蚀性离子很难渗透到涂层和基体之间的界面。因此,SA-GO复合涂层能为镁合金提供最佳的耐蚀性能。
图6 不同样品的电化学阻抗测试结果
等效电路以及相应的拟合结果分别如图6d和表3所示。CPE f和 CPE dl表示样品表面涂层和电解质溶液界面处的双电层容量。R s 是溶液电阻,R t 代表电荷转移电阻,R f 是涂层电阻。R t 值通常可以反映Mg基质的溶解速率,因此 R t 越高表明耐腐蚀性越好。在涂敷SA-GO涂层后,样品的 R t 值从126.8 ·cm 2 增加到40.5k ·cm 2,表明该复合涂层的耐蚀性得到显著提高。GO涂层的引入可以在一定程度上延长Cl-和H2O的扩散路径,这与GO的片层状结构和大的比表面积有关。但是,GO表面的富氧基团能够通过氢键与水分子相互作用逐渐形成通路,不能长时间有效地阻碍水分子或其他腐蚀性离子的渗透过程。而通过在GO上接枝SA可以有效改善复合涂层的疏水性,并与GO表面羟基反应堆积在片层的富氧区域,使水分子和腐蚀性Cl-离子难以扩散到达基材表面,从而大大减小了腐蚀速率。因此,SA-GO复合涂层可以表现出最佳的防腐性能。
表3 EIS图谱的拟合结果
R s: Solution resistance; CPE f: Capacity of the surface coating; R f: Coating resistance; CPE dl: Electric double layer capacitance; n f, n dl: Diffusion coefficient; R t: Charge transfer resistance.
2.5 耐磨性能
图7 显示了在100mN下的镁合金基体、GO涂层和SA-GO涂层的摩擦因数与测试时间的关系曲线。显然,镁合金基体的摩擦因数值逐渐稳定在0.43~0.48,摩擦学性能较差。与镁合金基体相比,GO涂层的摩擦因数值在初始阶段下降到约0.14,然后开始增加,最终稳定到约0.24。而SA-GO涂层的摩擦因数一直稳定在0.075~0.077,与镁合金基体相比,降低了约83.1%,展现了最好的摩擦学性能。图8a显示了通过3D表面轮廓仪得到的不同涂层的横截面磨损曲线;可以看出,Ra 对其相应表面的磨损率计算影响不大。计算了其磨损率,并显示在图8b中。结合图1中涂层的厚度数据可以发现,GO涂层的磨损曲线已触及到镁合金基体表面。而SA-GO的涂层并未磨穿,表现出极佳的耐磨性能。与镁合金基体相比,通过涂覆GO后,磨损率降至2.1×10 -4 mm 3 ·N 1 ·m 1。而在涂覆SA-GO涂层后,磨损率降低了99.3%(从4.7×10 -3 降至3.5×10 -5 mm 3 ·N 1 ·m-1),大大提高了镁合金的耐磨性。
图7 样品的摩擦因数曲线
图9显示了被测样品表面的磨损表面的SEM图像和EDS光谱。在镁合金基体的磨损痕迹中可以观察到大量凸脊和凹槽的存在,表现出典型的磨料磨损行为[34]。与镁合金基体相比,GO以及SA-GO涂层样品的磨损痕迹的面积和凸脊数量明显减少,这与其表面 Ra 的降低以及涂层的减磨作用有关。然而,可以看出,GO涂层在摩擦试验后发生破裂。相比之下,SA-GO涂层仍然完好无损,表明SA-GO复合涂层可以有效地抑制磨损过程并为镁合金提供良好的抗磨性能。此外,磨损痕迹的EDS分析表明了表面的元素分布。通过与图1a对比可以发现,在GO涂层的磨损区域中C元素比例有所下降而Mg元素比例大大升高,这归因于在摩擦过程中涂层的破裂。此外,GO涂层磨痕处C元素的存在说明仍有一定量的GO片层在磨损过程中填充在摩擦副之间,起到了一定的减磨作用,这与磨痕横截面分析结果相一致。对于SA-GO涂层样品,在磨损区域中检测到的Mg元素含量降低到19.27%,C元素的含量增加到64.39%,O元素的含量增加到16.11%,与SA-GO涂层完整区域的EDS数据基本一致,这表明磨损测试后涂层仍然保持了良好的完整性(图1b和图9c)。显然,SA-GO涂层可以更有效的保护基材免受磨损。
图8 不同样品的磨痕截面曲线以及磨损率
图9 不同样品的磨痕的SEM图像和EDS能谱图
涂层的耐磨损机理如图10所示。GO涂层表现出一定的耐磨性是因为摩擦过程中的局部残余应力会因不同GO片的滑移、运动或微塑性变形而逐渐释放,这有助于降低摩擦因数[35]。然而,GO的高比表面积以及片层之间的范德华力相互作用通常会导致不可逆的团聚和许多褶皱的产生,如图10中所示。因此,这些原因会导致GO片层滑移所需的力增加,并最终导致在摩擦试验期间涂层的破裂。而在接枝SA后,涂层更加平整致密,而且GO的层间距增加(图2),可以使GO片层更容易产生滑移,且位于滑动区域的剥落的GO可充当薄的润滑膜,以减少剪切应力并避免对应部分的直接接触。另外,接枝在GO上的硬脂酸根具有良好的自润滑性。因此,SA-GO涂层能为镁合金提供最佳的抗磨性能。
图10 不同涂层的耐磨机理
3 结论
(1)采用简便有效的方法将SA接枝到GO片层表面,并通过自组装的方法在镁合金表面制备了SA-GO复合涂层。用SA接枝后,GO涂层的疏水性和致密性得到提高,使得水和腐蚀性阴离子难以侵入镁合金基底。因此,复合涂层能为镁合金提供良好的耐蚀性能。
(2)SA-GO复合涂层表现出优异的摩擦学性能,显著降低了镁合金的磨损率。这与SA分子自润滑性能以及在接枝SA后GO层间距增加,并导致GO片层更易滑移并填充到磨痕表面有关。
参考文献:略
免责声明:本网站所转载的文字、图片与视频资料版权归原创作者所有,如果涉及侵权,请第一时间联系本网删除。
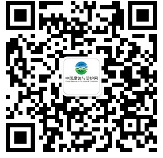
官方微信
《腐蚀与防护网电子期刊》征订启事
- 投稿联系:编辑部
- 电话:010-62316606-806
- 邮箱:fsfhzy666@163.com
- 腐蚀与防护网官方QQ群:140808414