摘要
通过机械合金化 (MA) 和放电等离子烧结 (SPS) 制备了Cr2O3颗粒强化的超细晶结构镍基高温合金 (ODS合金)。对比研究了不添加氧化物颗粒合金 (Base合金) 和ODS合金样品的微观结构和高温氧化行为。结果表明,在1200 ℃烧结过程中,Cr2O3完全转变为Al2O3。由于SPS快速烧结及弥散分布的原位Al2O3颗粒钉扎,抑制了晶粒长大,ODS合金具有十分细小的晶粒结构,其平均晶粒尺寸为0.98 μm;Base合金平均晶粒尺寸稍大,为1.54 μm。ODS合金在900 ℃下具有较好的抗氧化性能和较低的氧化速率,得益于其表面迅速生成了连续致密的内层α-Al2O3膜,能有效地阻止Ti和Cr向外扩散,表面生成少量保护性较差的TiO2和NiCr2O4。而Base合金表面则生成了以Al2O3为内层,TiO2和Cr2O3为中间层以及NiCr2O4为外层的多层结构氧化膜,并且其在初期的氧化速率较快,为1.66×10-7 mg2·cm-4·s-1,是ODS合金的2倍多。
关键词: 高温合金 ; 氧化物弥散强化 ; 细晶结构 ; 高温氧化 ; 放电等离子烧结
随着我国工业技术水平的逐步提高航空航天领域和能源领域也得到了快速发展,而高温结构材料是支撑航空航天领域和能源领域的重要的耐热材料之一,具有重要的意义。多数高温结构部件在服役期间,不仅承受较高的温度和应力,还面临热气腐蚀等复杂环境的考验[1,2]。氧化物弥散强化 (ODS) 镍基高温合金是针对这种复杂苛刻环境而开发的新型结构材料,通常利用机械合金化 (MA) 的方法将合金粉末与惰性氧化物混合均匀,然后再通过粉末冶金 (PM) 的方法固结成型[3,4]。这种特殊组合实现了氧化物弥散强化和γ′相析出强化的双重强化效果,使合金能承受更高的温度和具有更优良的高温性能,为镍基高温合金的深入发展开辟了一条新途径。
ODS高温合金具有良好的高温持久强度和抗氧化性能,可用于航空发动机和燃气涡轮机的导向叶片、涡轮叶片以或燃烧室等热端部件[3,5,6]。常见以Y2O3为弥散体的代表性ODS合金有MA6000[6,7]、PM2000[8]、MA956[9]等。ODS合金在服役环境中的高温氧化行为引起了广泛的研究。Guttmann等[7]研究了MA6000合金在900~1050 ℃高温氧化行为,表明MA6000合金在长时期 (1100 h) 暴露下形成了连续的氧化铝内层以致其表现出良好的抗氧化性能。其在900 ℃下氧化100 h后,氧化增重约为0.8 mg·cm-2。该合金的抗氧化性能明显优于与其成分接近的IN738合金 (不含Y2O3)[10]。Weinbruch等[8]通过恒温氧化实验研究了PM2000合金分别在900~1300 ℃下的高温氧化行为并探讨了Y对氧化膜结构的影响。表明该合金在900~1200 ℃范围内合金氧化都遵循抛物线规律,抛物线速率常数随温度升高而增大,还总结了在不同温度区间,抛物线速率常数 (kp) 与温度 (T) 的函数关系式。可以看出,PM2000合金在1100 ℃下具有良好的抗氧化性能。他们还分析了不同时间段下氧化膜的腐蚀产物及元素分布,明确了弥散体影响ODS合金的高温氧化的本质,即抑制阳离子向外扩散,并且这种保护机制会因氧化膜内的Y耗尽而终止。Sun等[11]研究了添加不同含量Y2O3的Ni-20Cr-5Al合金在1150 ℃下的高温氧化行为。结果表明,该合金的抗氧化性能随着Y2O3含量的增加呈下降趋势,Y2O3的含量为0.2% (质量分数) 时合金的抗氧化性最佳,其氧化80 h后的增重约为0.28 mg·cm-2。研究还表明,氧化后合金表面均生成NiCr2O4和少量的NiO,并且当Y2O3的含量超过0.4%后,开始有YCrO3生成。由此可以确定添加Y2O3可以显着提高合金的抗氧化性。可见,在这类ODS合金在高温下形成多层结构的氧化膜,由外部的富Cr或富Ti的非保护性氧化物以及内部的Al2O3组成。并且Y2O3还会与合金中的Al反应,形成多种复杂结构Y-Al-O氧化物团簇[12],进一步消耗了合金中的Al,增加了ODS合金表面成完整的连续氧化铝膜的难度。甚至Y-Al-O还会促进其周围Cr和Ti等元素的氧化,导致合金发生失稳氧化。可以认为,第二相粒子对合金性能的影响须发挥积极作用,而不能有害于合金的高温抗氧化性能或强度。α-Al2O3不仅结构稳定,还是高温下最具有保护作用的氧化物之一,以它作为第二相强化粒子,具有很大的应用潜力和研究价值。但目前α-Al2O3弥散强化高温合金的报道较少,尤其是对于这类合金在高温下氧化行为以及氧化机制理论也十分缺乏。
本文采用Cr2O3高温下原位合成Al2O3,在烧结温度高于1100 ℃时,仅会形成具有良好的热稳定性和化学稳定的密排六方结构的α-Al2O3,避免了非稳态氧化物的形成而产生对合金性能不利的影响。并通过调整合金粉末中Al和Cr的含量保证了反应后合金成分与基体一致,利用MA和放电等离子烧结 (SPS) 技术获得了具有细晶结构的α-Al2O3原位强化镍基高温合金。考虑到MA会对粉末细化以及引入杂质,因此对比研究了相同球磨时间但不加Cr2O3颗粒的基体合金 (Base) 的相组成和微观结构。最后通过恒温氧化实验,初步探索了细晶结构ODS合金的氧化行为,探讨了细晶结构ODS合金的氧化机制。
1 实验方法
采用由中科院金属所提供的FGH4097气雾化合金粉末,粉末粒径分布在25~75 μm,其成分见表1。选用粒径小于1 μm的亚微米球形Cr2O3作为弥散体,添加量为2% (体积分数)。然后借助行星式球磨机分别对添加Cr2O3的合金粉末 (powder-2) 和标准合金粉末 (powder-1) 进行球磨细化,并加入少量硬脂酸避免合金粉末在球磨的过程中冷焊粘罐,球磨工艺为球料比10∶1,球磨时间50 h,球磨机转速300 r/min。为防止合金粉末的氧化,选用真空不锈钢球磨罐,并在手套箱中进行抽真空并充入氩气,此过程反复进行3次。采用HP D 250-C放电等离子烧结系统对球磨后的两种粉末进行固结,烧结压力、温度以及时间分别为40 MPa、1200 ℃和15 min,升温速率为100 ℃/min。最后得到尺寸为φ40 mm×15 mm的两种烧结态合金。随后使用线切割将两种合金加工为15 mm×10 mm×2 mm的片状样品,并用SiC砂纸逐级打磨至2000#后并做倒边、倒角处理,然后依次用丙酮和酒精超声清洗,冷风吹干后放于干燥器中待用。
表1 FGH4097合金粉末的化学成分
恒温氧化实验采用马弗炉,在900 ℃的空气中进行。将带有样品的坩埚放入炉中,并分别在氧化时间为5、20、40、60、80、100 h将样品取出,待样品冷至室温却后称量并且每组样品有3个平行样,采用Secura125-1CN (精度0.01 mg) 电子天平多次称量后取平均值。需要注意的是实验用的坩埚为氧化铝坩埚,已在1200 ℃烧至恒重。
采用Smartlab X射线衍射仪 (XRD) 对样品的物相结构进行分析。采用Inspect F50场发射扫描电子显微镜 (SEM) 观察样品的微观结构并通过配备的能谱分析仪 (EDS) 确定样品的主要化学成分。通过配有电子背散射衍射 (EBSD) 探头的JSM 7001F扫描电镜对样品微观结构特征进行表征。采用JEM 2100F透射电镜 (TEM) 进一步表征了烧结态ODS合金的微观结构。
2 实验结果
2.1 烧结态合金的微观结构
图1为两种烧结态合金的XRD分析结果。从中可以看出,两种合金主要由γ′/γ相构成。并检测到微弱的Cr6C23的衍射峰,这可能是因添加硬脂酸导致合金中引入了C而形成。因为添加的Cr2O3含量较少,所以XRD并不能检测到ODS合金中的氧化物。
图1 两种烧结态合金的XRD图谱
图2所示为两种烧结态合金的微观结构及特征。从BSE像中可以看出 (图2a和c),两种合金结构致密,无明显孔隙,并析出了大量的γ′相,体积分数超过50%。Base合金中可见许多碳化物,根据XRD结果推测其可能是Cr6C23。ODS合金中有许多尺寸~1 μm的黑色颗粒,推测其为氧化物。但是其在晶界处的γ′相尺寸相对较大,这是因为在冷却过程中γ′相会优先在晶界析出并生长,同时合金内部大量的陶瓷颗粒会导致材料冷却速率降慢,进而造成γ′相粗大。EBSD结果显示,两种合金均无明显的取向关系,并且两种合金的晶粒尺寸相差不是很大,其中Base合金的平均粒径为1.54 μm,晶粒分布大小不一,而ODS合金的晶粒尺寸分布较均匀,平均粒径为0.98 μm。这是因为在烧结过程中氧化物能有效的阻碍晶界迁移,抑制晶粒长达,实现晶粒细化的效果。
图2 两种烧结态合金的微观结构及特征
图3为ODS合金的TEM元素面扫结果。可以看出,合金中的弥散体表现出Al和O的富集,而并没有出现Cr的富集,可以确定Cr2O3在高温下转变为Al2O3。大多数的Al2O3的粒径分布50~250 nm之间,但也有个别Al2O3的尺寸超过500 nm。此外,还发现有Ti和Nb的富集,可能是 (Ti,Nb)C,尺寸约200 nm。
图3 ODS合金的TEM元素面扫结果
2.2 氧化动力学
图4为两种合金在900 ℃下氧化100 h的动力学曲线。结果表明,两种细晶结构的合金均表现出较低的氧化速率,以及良好的抗剥落性。氧化前20 h,Base样品的增重速率要比ODS样品快许多,导致其在20 h的氧化增重高达0.11 mg·cm-2,占总增重一半以上。随着氧化进行至100 h,两者的增重速率均有所降低,但ODS合金的增重随时间增长的更慢,此时Base合金和ODS合金的增重分别为0.17和0.13 mg·cm-2 (图1a)。当氧化膜的生长通过氧化膜的扩散控制时,质量增加遵循抛物线定律:y2=kp·t,其中y是样品单位面积的氧化增重,kp是抛物线速率常数,t是氧化时间。如图1b显示了y2与t的函数关系,其中虚线为拟合结果,其斜率则为kp值。结果表明,两种样品在不同的氧化阶段表现出不同的氧化物速率 (kp)。ODS合金在前20 h的氧化速率仅为7.98×10-8 mg2·cm-4·s-1,随后的20~100 h中氧化速率转向平稳,较前20 h降低了1.3倍,为3.47×10-8 mg2·cm-4·s-1。而Base合金在前20 h的氧化速率是1.66×10-7 mg2·cm-4·s-1,后期则为5.20×10-8 mg2·cm-4·s-1,可见Base合金在前期的氧化速率约是ODS合金的2.1倍,而后期两者氧化速率虽都有所降低,但前者的氧化速率仍是后者的1.5倍。
图4 两种合金在900 ℃下氧化100 h的动力学曲线
2.3 氧化形貌及成分分析
图5所示为两种合金样品在900 ℃下氧化100 h的XRD图谱。可以得出,两种合金样品的氧化膜均检测到了Al2O3、Cr2O3、TiO2以及NiCr2O4。根据衍射峰强度,可判断出Base合金的氧化程度更为严重,表面生成的Cr2O3和NiCr2O4数量较多。
图5 两种样品在900 ℃下氧化100 h后的XRD图谱
图6为两种合金样品在900 ℃下氧化100 h的微观表面形貌。由图可见,两种合金样品的表面有明显不同:Base合金表面形成大面积的氧化物凸起,而且在这类氧化物表面还有极不致密,表面产生有很多孔洞,甚至有开裂现象;相较于Base合金,ODS合金表面的氧化物凸起相对较少,绝大部分表面生成了一层晶粒细小且十分致密氧化膜 (图6a和c)。对图中放大区域进行了EDS分析并结合XRD结果,明确这类氧化物凸起主要由NiCr2O4、Cr2O3和TiO2组成,而ODS合表面形成的主要是Al2O3及少量的Cr2O3。
图6 两种合金在900 ℃下氧化100 h后表面形貌及EDS分析
图7为两种合金样品在900 ℃氧化100 h后的截面微观形貌。可以看出,两种合金样品的氧化膜有明显差异:Base合金表面形成了由多种氧化物构成的多层结构,氧化产物层较厚,约为3.7 μm;而ODS合金膜厚不到1 μm,分层情况不明显,基本可视为单层膜结构。结合XRD和EDS分析,可以确定:Base合金外层主要氧化为NiCr2O4,中间层以为Cr2O3和TiO2的混合氧化物为主,以及内层的Al2O3;ODS合金的氧化膜则主要为致密的Al2O3内层,以及极薄的Cr2O3外层,几乎没有生成保护性较差的TiO2和NiCr2O4,表明钉扎在合金和氧化膜界面的Al2O3弥散相对氧化膜的结构有重要影响。此外,Base合金内有轻微的内氧化,说明生成的氧化膜不够致密,氧化膜中孔隙较多。
图7 两种合金样品在900 ℃氧化100 h后的截面微观形貌
图8为两种合金样品在在900 ℃氧化20 h后的表面微观形貌。由图可见,两者合金样品的表面腐蚀程度较轻相较于100 h的氧化表面。但在Base合金表面发现了较多数量呈针状的θ-Al2O3,表面已有较大的Cr2O3和NiCr2O4凸起生成。而ODS合金表面几乎均匀为鳞片状的α-Al2O3,很难看到θ-Al2O3的存在,并且氧化物凸起较小。
图8 两种合金样品在900 ℃氧化20 h后的表面微观形貌
图9为两种合金样品在900 ℃氧化20 h后的截面微观形貌,与表面氧化物凸起相对应。由图可见,氧化前20 h,Base合金内已经形成较厚的氧化物凸起,凸起主要由较厚的Cr2O3层以及少量的NiCr2O4构成,并且下方产生较多的Cr2O3和TiO2,也不难发现此时并未形成连续的Al2O3内膜。与Base合金相比,ODS合金生成了连续的Al2O3内膜,表面生成较少的TiO2和Cr2O3,几乎没有发现NiCr2O4尖晶石的存在。
图9 两种合金样品在900 ℃氧化20 h后的截面形貌
3 讨论与分析
通过动力学曲线表明,细晶结构的ODS合金比Base合金表现更好的高温抗氧化性能。并且不难发现无论ODS合金还是Base合金的增重差异主要源于最初的20 h氧化,而此时Base合金的氧化速率是ODS合金的2.1倍 (图4),而之后两者的氧化速率虽都有所降低,但ODS合金仍表现出低于Base合金的氧化速率,此时的增重则主要来源于氧化膜的生长。并且通过实验结果,可知Base合金的主要的氧化物产物为Cr2O3,而Al在内部被氧化[13]。相反,ODS合金可在初始氧化阶段会在表面形成独特的α-Al2O3氧化膜。这是ODS合金的抗氧化性高于Base基体的根本原因。
根据Wagner理论,只有当Al的浓度超过一个临界值时,才能保证外部Al2O3膜的形成,该理论可表达为[14]:
(1)
式中,g为形成外部氧化皮所需的Al2O3体积分数;NO为氧化膜-合金界面处的氧摩尔分数;DO为氧在合金中的扩散系数;DAl为Al合金中的扩散系数;VM和VOX分别为合金和氧化物Al2O3的摩尔体积。由 公式 (1) 可知,随着Al扩散率的增加或晶界数量的增加,能够降低形成外部Al2O3氧化膜的Al临界浓度。也就是说,增加Al的含量或降低其临界值 (NAl) 都可以促进外部Al2O3氧化膜的形成。而本文制备的ODS合金具有均匀的细小晶粒,其平均晶粒尺寸仅为0.98 μm (图2),因此其内部含有大量的晶界,有利于Al的选择性氧化。
与此同时,ODS合金中含有许多弥散分布的α-Al2O3颗粒,能够作为α-Al2O3的形核质点,促进α-Al2O3晶核的形核和横向生长,加速氧化铝膜的生成速度,减少形成连续的α-Al2O3膜的时间[15-17] (图7b)。因此,ODS合金表面能够在相当短的时间内形成连续的α-Al2O3膜,有效阻碍O的向内扩散,并且合金中的弥散体能一定程度减缓Cr和Ti元素的向外扩散的速率,减少了样品表面氧化物凸起的形成,进而降低了氧化速率,所以表现出更好的高温抗氧化性能。
相反,Base合金表面生成Cr2O3氧化膜,而Al在内部被氧化,不能迅速形成保护性最好的Al2O3内膜,并且还会因氧化铝膜的生长,Al被迅速消耗,进一步降低了合金中的Al含量,导致合金中形成较深的贫铝区,并会有一些其他元素在合金/氧化皮界面处偏析,尤其是Ti,其具有很高的亲氧力,O在α-Ti中的溶解度随温度升高而增加,只要Ti含量增加到界面附近的临界值,Al被氧化后Ti随后就会被氧化[14]。也因此导致Base合金的氧化膜中生成了大量保护作用较差的TiO2,而TiO2的PBR (1.73) 较大,也会导致氧化膜内部产生较大的应力,诱发氧化膜的破坏。在高温氧化过程中NiCr2O4尖晶石通常以下方式形成:
(2)
由上式可知,尖晶石是表层NiO与其下方的Cr2O3反应而得,NiO其主要来源于在氧化最初合金表面的瞬态氧化,最终导致样品表面形成大量的NiCr2O4尖晶石,而NiCr2O4尖晶石结构疏松不致密,不具备保护作用,甚至还会引起氧化膜的剥落或开裂。
此外,亚稳态的氧化铝在氧化初期的氧化速率较快,最后才会逐渐转变为稳态的α-Al2O3。我们在Base样品的氧化表面可以看到较多数量θ-Al2O3,而ODS合金中θ-Al2O3数量较少 (图8),这也是氧化物初期,ODS合金氧化速率较低的另一原因。因此,我们认为α-Al2O3弥散体会促进氧化膜直接形成α-Al2O3氧化内膜,而不是亚稳态的θ-Al2O3氧化膜,进而改善镍基合金的高温抗氧化性能。综上,可以证明α-Al2O3为弥散相能改变氧化膜的生长机制,提高合金的抗氧化性能,可应用于高温合金领域。
本文在两种合金氧化100 h的样品表面都观察到了氧化物凸起,但是ODS合金中的数量要少很多且较薄,针对这种现象分析了两种合金氧化初期的腐蚀形貌 (图8和9)。认为凸起形成的主要原因是Ti和Cr的向外扩散,导致在合金/氧化膜界面处形成较厚的 (Cr,Ti)O x 层,进而导致Cr的向外扩散而形成较厚的Cr2O3外层。对于ODS合金,大量均匀分布的Al2O3弥散体能有效地降低Ti和Cr向外扩散的速率,能够在较短的时间内阻止这种现象加剧,所以凸起较小。反之,正如Base合金内部,这种情况较为严重,因此表面可观察到大面积的富含 (Ni,Cr,Ti)O x 的氧化物凸起。
4 结论
本文通过原位固相反应与放电等离子烧结 (SPS) 制备出具有细晶结构的原位氧化铝弥散强化镍基高温合金,并研究了ODS合金和Base合金的微观结构及其在900 ℃下空气中的高温氧化行为,得到如下结论:
(1) 烧结过程中,初始添加的Cr2O3能够完全转变为Al2O3,并且原位生成的Al2O3能够有效地抑制晶粒长大,所以ODS合金具有更均匀且细小的晶粒尺寸,平均粒径为0.98 μm;而不添加氧化物的Base合金的平均粒径则为1.54 μm,约是ODS合金的1.5倍。
(2) 在900 ℃空气中,ODS合金比Base合金表现出更好的抗氧化性能。这归因于ODS合金表面能快速生成一层连续且致密的α-Al2O3氧化膜,而Base合金表面则生成以Al2O3为内层,TiO2和Cr2O3为中间层以及NiCr2O4为外层的多层结构氧化膜。
(3) 两种合金的增重差异主要来源于氧化初期,此阶段Base合金的氧化速率高达1.66×10-7 mg2·cm-4·s-1,超过ODS合金的2倍。而ODS合金表现出较低的氧化速率较,得益于弥散分布的α-Al2O3颗粒能够有效阻碍Cr和Ti向外扩散,极大程度减少了保护性较差的NiCr2O4和TiO2的形成。
参考文献
1 Williams J C, Starke Jr E A. Progress in structural materials for aerospace systems [J]. Acta Mater., 2003, 51: 5775
doi: 10.1016/j.actamat.2003.08.023
2 Murty K L, Charit I. Structural materials for Gen-IV nuclear reactors: Challenges and opportunities [J]. J. Nucl. Mater., 2008, 383: 189
doi: 10.1016/j.jnucmat.2008.08.044
3 Gessinger G H. Powder Metallurgy of Superalloys [M]. London: Butterworths, 1984: 213
4 Suryanarayana C. Mechanical alloying and milling [J]. Prog. Mater. Sci., 2001, 46: 1
doi: 10.1016/S0079-6425(99)00010-9
5 Heilmaier M, Maier H J, Jung A, et al. Cyclic stress-strain response of the ODS nickel-base, superalloy PM 1000 under variable amplitude loading at high temperatures [J]. Mater. Sci. Eng., 2000, 281A: 37
6 Howson T E, Mervyn D A, Tien J K. Creep and stress rupture of a mechanically alloyed oxide dispersion and precipitation strengthened nickel-base superalloy [J]. Met. Tran., 1980, 11A: 1609
7 Guttmann V, González-Carrasco J L, Fattori H. Oxidation behavior of ODS alloy MA 6000 [J]. Oxid. Met., 1999, 51: 159
doi: 10.1023/A:1018810420729
8 Elzey D M, Arzt E. Oxide dispersion strengthened superalloys: the role of grain structure and dispersion during high temperature low cycle fatigue [A]. Proceedings of the Sixth International Symposium on Superalloys [C]. The Metallurgical Society of AIME, PA: 1988, 595
9 Weinbruch S, Anastassiadis A, Ortner H M, et al. On the mechanism of high-temperature oxidation of ODS superalloys: significance of yttrium depletion within the oxide scales [J]. Oxid. Met., 1999, 51: 111
doi: 10.1023/A:1018806319821
10 Zhang H, Liu Y, Chen X, et al. Microstructural homogenization and high-temperature cyclic oxidation behavior of a Ni-based superalloy with high-Cr content [J]. J. Alloy. Compd., 2017, 727: 410
doi: 10.1016/j.jallcom.2017.08.137
11 Sun D J, Liang C Y, Shang J L, et al. Effect of Y2O3 contents on oxidation resistance at 1150 ℃ and mechanical properties at room temperature of ODS Ni-20Cr-5Al alloy [J]. Appl. Surf. Sci., 2016, 385: 587
doi: 10.1016/j.apsusc.2016.05.143
12 Schaffer G B, Loretto M H, Smallman R E, et al. The stability of the oxide dispersion in INCONEL alloy MA6000 [J]. Acta Metall., 1989, 37 (9) : 2551
doi: 10.1016/0001-6160(89)90053-9
13 Jalowicka A, Nowak W, Naumenko D, et al. Effect of nickel base superalloy composition on oxidation resistance in SO2 containing, high pO2 environments [J]. Mater. Corros., 2014, 65: 178
14 Sun W Y, Chen M H, Bao Z B, et al. Breakaway oxidation of a low-Al content nanocrystalline coating at 1000 ℃ [J]. Surf. Coat. Technol., 2019, 358: 958
doi: 10.1016/j.surfcoat.2018.12.034
15 Huang Y, Peng X. The promoted formation of an α-Al2O3 scale on a nickel aluminide with surface Cr2O3 particles [J]. Corros. Sci., 2016, 112: 226
doi: 10.1016/j.corsci.2016.07.029
16 Huang Y C, Peng X, Chen X Q. TiO2 nanoparticles-assisted α-Al2O3 direct thermal growth on nickel aluminide intermetallics: template effect of the oxide with the hexagonal oxygen sublattice [J]. Corros. Sci., 2019, 153: 109
doi: 10.1016/j.corsci.2019.03.025
17 Huang Y C, Peng X, Chen X Q. The mechanism of θ- to α-Al2O3 phase transformation [J]. J. Alloy. Compd., 2021, 863: 158666
doi: 10.1016/j.jallcom.2021.158666
免责声明:本网站所转载的文字、图片与视频资料版权归原创作者所有,如果涉及侵权,请第一时间联系本网删除。
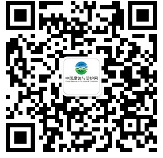
官方微信
《腐蚀与防护网电子期刊》征订启事
- 投稿联系:编辑部
- 电话:010-62316606-806
- 邮箱:fsfhzy666@163.com
- 腐蚀与防护网官方QQ群:140808414