摘要
微弧氧化 (PEO) 涂层属于陶瓷性涂层,表面不具有催化活性,需使用金属Pd活化后,再进行化学镀镍。为替代昂贵的Pd活化工艺,分别开发了Cu活化和Ag活化方法。利用场发射扫描电镜对浸镀后Cu/Ag活化复合涂层的镀层表面和截面形貌观察可见,Ag活化后PEO涂层表面镀层更加均匀致密,且厚度更大。经电化学测试表明,Ag活化复合涂层与传统Pd活化复合涂层的耐蚀性能相近,且明显优于Cu活化复合涂层。因此,Ag活化方法在保证复合涂层的耐蚀性能的同时,降低了活化成本。
关键词: AZ91D镁合金 ; Cu/Ag活化 ; 微弧氧化 ; 化学镀 ; 复合涂层
镁合金具有低密度、高的比强度、尺寸稳定性好、优良阻尼特性、导热导电性能好等众多优点,已成为装备制造业轻量化发展的首选材料;而且,无论在储量、特性、应用范围、循环利用以及节能环保等方面,镁合金均展现出了其独特的优越性[1,2]。近些年,依靠上述优点镁合金在航空航天、汽车及电子通讯等领域的消耗量在快速增长,已成为最受关注的金属材料之一[3,4]。然而,Mg的化学性质活泼,有较大的腐蚀倾向,腐蚀过程中存在析氢反应,具有“一点击破,全盘崩溃”的特点,并且镁合金表面生成的氧化膜疏松多孔,无法阻隔腐蚀介质的渗入,严重地限制了镁合金的应用范围[5,6]。为扩大镁合金的应用范围,通常采用制备防护涂层的方式来应对镁合金的腐蚀,目前主要的表面防护手段有化学镀、阳极氧化、微弧氧化和化学转化膜[7-10]。
镁合金在航空航天电子设备和通讯设备等领域的应用,对镁合金防护涂层提出了一些功能性要求,而兼顾导电性、耐磨性和低磁性特征的化学镀涂层最容易同时满足工业界的要求。但是,在使用过程中,由于化学镀层与镁合金基体之间电势差较大,且结合力较低,一旦镀层部分区域发生磨损脱落,镁合金会受到严重的电偶腐蚀[9,11]。为解决化学镀层电偶腐蚀风险高和附着力较差的问题,可采用微弧氧化 (PEO) 涂层作为基体与化学镀层的中间物理阻隔层,构造化学镀复合涂层。然而,化学镀层必须沉积在具有催化活性的材料表面上,PEO涂层是陶瓷性涂层,其表面不具有催化活性,需进行活化处理,在涂层表面形成具有催化活性的位点,诱导镀液中镍离子的沉积[12]。
PEO涂层的传统活化方法为金属Pd活化,但是钯成本较高,不适合大规模使用[13]。近期研究显示,相关学者采用混合酸活化、TiB2环氧活化等方法来代替Pd活化法,但是混合酸活化法采用HF和H3PO4对PEO涂层进行处理,极大地损害了PEO涂层的完整性,而TiB2环氧活化法引入了新的中间环氧层,导致镀层结合力下降[14]。因此,现阶段亟需开发一种价格低廉、不损伤PEO涂层、结合力较高且活化效果好的PEO涂层活化方法。
为此,本研究尝试性开发了PEO涂层Cu活化方法和Ag活化方法。同时,通过电化学测试方法,探究了两种方法诱导沉积的镀层相对于传统金属Pd活化法诱导沉积的镀层在耐蚀性能方面的表现。
1 实验方法
本文所用的材料为商用铸态AZ91D镁合金,其化学成分采用电感耦合等离子发射光谱法 (ICP-OES) 测得,成分 (质量分数,%) 为:Fe 0.0014,Cu 0.0018,Mn 0.21,Al 9.23,Si 0.029,Zn 0.73,其他元素<0.05,Mg余量。
将AZ91D镁合金切成20 mm×20 mm×5 mm的矩形试样。依次用400#、600#、1000#的SiC砂纸打磨矩形试样的表面,后用酒精冲洗试样,冷风吹干。
PEO涂层样品制备:将打磨后的AZ91D镁合金置于20.0 g/L Na2SiO4·9H2O、2.0 g/L NaOH和4.0 g/L KF·2H2O的碱性电解液中,在脉冲模式下进行微弧氧化处理,处理时电压为500 V、电流密度为2 A/dm2、占空比为30%,制备时间20~30 min。
PEO-Cu/Ag/Pd涂层样品制备过程为:(1) Cu分步活化,先将PEO涂层试样置于10 g/的CuSO4·5H2O溶液中进行敏化处理 (30 ℃,15~20 min),随后在去离子水中浸洗,最后在10.0 g/L NaBH4和2.0 g/L NaOH的溶液中进行活化 (50 ℃,10~20 min);(2) Ag分步活化,先将PEO涂层试样置于2.0 g/L的AgNO3溶液中进行敏化处理 (25 ℃,30~60 s),随后在去离子水中浸洗,最后在10.0 g/L NaBH4和2.0 g/L NaOH的溶液中进行活化 (28 ℃,30~60 s);(3) Pd分步活化,先将PEO涂层试样置于1 g/L PdCl2和1 g/L α-吡啶胺混合溶液中进行敏化处理 (25 ℃,30~60 s),随后在去离子水中浸洗,最后在30 g/L的NaH2PO2溶液中进行活化 (28 ℃,30~60 s)[15]。
将活化后的PEO-Cu/Ag/Pd涂层样品浸入碱性预镀液中进行预镀处理,去离子水冲洗,随后浸入酸性化学镀液中进行化学镀处理,最终得到PEO-Cu/Ag/Pd-EN复合涂层,强镀液的成分 (g/L) 为:NiSO4·6H2O 20.0~30.0,NaH2PO2·H2O 30.0~50.0,Na3C6H5O7·2H2O 20.0~30.0,Na2CO3 20.0~35.0,NH4HF 9.0~14.0 pH 8.8~9.2,60 ℃,15~20 min,镀液的成分 (g/L) 为:NiSO4·6H2O 20.0~25.0,NaH2PO2·H2O 20.0~35.0,Na3C6H5O7·2H2O 20.0~40.0,CH3COONa·3H2O 20.0~30.0,NH4HF 9.0~15.0,C18H29NaO3S 0.01~0.15,pH 4.8~5.2,80 ℃, 80~120 min。
利用XL-30FG场发射扫描电镜 (FE-SEM) 和X射线能谱仪 (EDS) 对涂层的微观形貌、元素分布及组成进行分析。利用PW1700配备铜靶的X射线衍射仪 (XRD) 对涂层相组成进行分析,参数设置为:λ=0.15406 nm,30 mA,40 kV,扫描角度为10°~80°,扫描速度4°/min。
利用X射线光电子能谱仪 (XPS,Thermo Fisher Scientific) 对样品的成分进行分析,射线源为Al-Ka (1486.6 eV) 射线,施加电流为1 μA,电压为1 kV,测试面积为300 μm×700 μm。
利用Zahner电化学工作站,在 (30±1) ℃的3.5%(质量分数) NaCl溶液中对试样进行动电位极化和电化学阻抗测试。测试采用三电极体系,其中对电极为铂电极,参比电极为饱和甘汞电极 (SCE),试样为工作电极。
测试时阴、阳极极化曲线分开进行测量。待测样品在3.5%NaCl溶液中浸泡15 min,待开路电位 (OCP) 稳定后,进行动电位极化曲线测试,阴极极化测试由OCP开始扫描至相对开路电位-300 mV,阳极极化测试由OCP开始扫描至电流密度达到1 mA/cm2即停止,扫描速率为0.333 mV/s。电化学阻抗谱测试的频率范围为105~10-2 Hz,扰动幅度为10 mV。为保证测试的准确性,每组实验至少重复3次。
盐雾实验参照ASTM B117-03标准进行,实验过程中盐雾试验箱采用连续喷雾模式,喷雾溶液为5% (质量分数) NaCl溶液,溶液pH为6.5~7.2,箱内温度设置为 (35±2) ℃,经24 h喷雾后,80 cm2水平面积的收集器中的盐雾沉降速度为1.0~2.0 ml/h。测试过程中试样待测表面与垂直方向成15°~30°,每种样品放置3个平行样,并使用相机记录腐蚀过程中的宏观形貌。
2 结果与讨论
2.1 PEO涂层活化后表面的微观结构与成分
2.1.1 微观形貌与EDS分析结果
图1为PEO涂层的表面宏观形貌和SEM形貌。PEO涂层宏观表面呈灰白色,SEM图像显示涂层表面存在大量的微孔,微孔呈典型的“火山口”微观结构,尺寸在0.5 μm至10 μm之间。“火山口”状微孔的形成可能是微弧氧化过程中的火花放电以及表面气泡排出导致。利用SEM对PEO涂层的截面进行观察发现,部分微孔纵向贯穿了PEO涂层 (图1d),而这些微孔为腐蚀介质穿透涂层进入基体提供了通道,使PEO涂层部分区域丧失了对基体的防护作用。
图1 PEO涂层的宏观形貌,表面SEM像和截面SEM像
图2显示了PEO涂层进行Cu敏化和Cu活化处理后的表面宏观形貌和SEM形貌。PEO涂层经过硫酸铜溶液敏化处理后,涂层由灰白色转变为淡蓝色 (图2a)。利用SEM观察表面可见,PEO涂层表面生成了大量棒状的颗粒,长度在1~2 μm之间,除PEO孔隙外其他区域几乎被棒状的颗粒完全覆盖 (图2b,c)。
图2 Cu敏化和Cu活化处理后PEO涂层的表面宏观形貌和SEM像
利用EDS对PEO涂层表面的元素和棒状颗粒组成分析表明 (表1),PEO涂层主要成分包括O、Mg、Al、Si,而硫酸铜敏化液处理后的PEO涂层中除O、Mg、Al、Si外,还含有Cu和S。利用EDS对棒状物质 (点A) 进行点分析可见,PEO涂层表面生成的棒状颗粒主要由Cu和S构成。
表1 EDS分析结果
图2d为Cu活化处理后PEO-Cu涂层的表面宏观形貌,经Cu活化处理后,涂层由淡蓝色转变为粉红色。SEM观察可见,PEO-Cu涂层表面的棒状颗粒消失,生成了大量尺寸不均匀的球状颗粒,且直径大多不超过1 μm (图2e,f)。利用EDS对球状物质 (点B) 进行点分析可见,涂层经Cu活化处理后表面生成的球状颗粒含38.20%Cu。利用EDS对Cu活化后涂层的元素分布进行分析,结果如图3所示。PEO-Cu涂层主要由O、Mg、Al、Si和Cu组成,且Cu集中分布于球状颗粒处,这与EDS点分析结果一致 (表1)。
图3 经Cu活化处理后PEO涂层表面主要元素分布图
图4为PEO涂层Ag敏化和Ag活化处理后的表面宏观形貌和SEM像。经过Ag敏化处理后,PEO涂层样品表面宏观颜色没有发生明显变化。SEM观察发现,PEO涂层表面也生成了大量棒状的颗粒,长度约为1 μm,但是由于Ag敏化处理时间相对Cu敏化较短,表面棒状颗粒的密度较Cu敏化后更小。利用EDS对棒状颗粒 (点C) 的元素组成进行点分析发现,棒状颗粒除含有O、Mg、Al、Si外,还含有6.99%Ag (表1)。
图4 Ag敏化和Ag活化处理后PEO涂层的表面宏观形貌和SEM像
图4d为Ag活化处理后PEO-Ag涂层的表面宏观形貌,经Ag活化处理后,涂层由灰白色转变为暗黄色。SEM观察表明,PEO-Ag涂层表面的棒状颗粒消失,生成了亚微米级球状颗粒 (图4e,f)。利用EDS对球状物质 (点D) 进行点分析表明,其含Ag为9.50 %。利用EDS对Ag活化后涂层的元素分布进行分析,结果如图5所示。PEO-Ag涂层主要由O、Mg、Al、Si和Ag组成,且Ag集中分布于亚微米级球状颗粒处,这与EDS点分析的结果一致。
图5 Ag活化处理后PEO涂层表面主要元素分布图
经对比发现Cu活化处理后的PEO涂层表面Cu含量 (6.70 %) 较高,而Ag活化处理后PEO涂层表面Ag含量 (1.72%) 略低,这归因于Ag敏化处理时间较短,以避免处理过程中Ag+发生置换反应。
2.1.2 XRD测试结果
利用XRD对PEO涂层和Cu/Ag活化处理后的涂层表面进行物相分析,结果如图6所示。PEO涂层主要由MgO与Mg2SiO4构成,由于PEO涂层的多孔结构以及存在的通孔,X射线可穿透膜层到达基体,XRD谱线中可观察到大量的镁基体的特征峰[16]。经Cu活化处理后,PEO的XRD谱线中出现单质Cu的特征峰,结合EDS结果分析,PEO涂层表面生成的球状颗粒应主要为单质Cu。经Ag活化处理后,PEO涂层的XRD谱线上却没有发现Ag的特征峰,这主要归因于PEO膜层上Ag的含量较低,低于XRD仪器的灵敏度。
图6 PEO涂层及不同活化处理后PEO涂层的XRD图谱
2.1.3 XPS测试结果
为了进一步确定Cu和Ag活化过程中PEO涂层表面Cu和Ag的价态变化,分别对Cu和Ag敏化处理和活化处理后的PEO涂层进行XPS测试,利用XPS-Peak软件对各峰进行分析拟合,测试结果如图7所示。经CuSO4溶液敏化处理后,PEO涂层中Cu主要以Cu2+的形式存在 (图7a),其中CuSO4为溶液中溶质物理吸附于PEO涂层表面产生。由于敏化过程中,涂层中MgO会与H2O反应生成OH-,因而溶液Cu2+与OH-结合生成了Cu(OH)2,反应方程如式 (1, 2) 所示。图7b为Cu敏化PEO涂层经Cu活化处理后的XPS谱,结合XRD谱分析,932.4和952.45 eV两处的较强峰应为Cu单质,而953.70、943.00 和934.60 eV处的较弱峰为CuO,由于其含量较低,因而XRD测试时并未发现CuO。Cu活化处理后,PEO涂层表面的Cu2+被活化液中BH4-大量还原为Cu单质,其反应方程如 式 (3) 所示。
图7 经过不同敏化/活化处理后,PEO涂层的XPS图谱
图7c为PEO涂层在AgNO3溶液中进行Ag敏化处理后的XPS图谱,经AgNO3溶液敏化处理后,PEO涂层表面出现大量Ag2O。在Ag敏化过程中,涂层中MgO和H2O反应生成的OH-与Ag+结合生产Ag(OH)2,Ag(OH)2随后水解产生Ag2O,反应方程如式 (1)、(4) 和 (5) 所示。图7d为Ag敏化PEO涂层经Ag活化处理后的XPS测试结果,涂层表面的一价Ag被BH4-还原为Ag单质,如 式 (6) 所示。
2.2 不同活化方法对后续化学镀层生长过程的影响
为探究不同活化方法对后续化学镀镍涂层生长过程的影响,分别对Cu活化处理、Ag活化处理和Pd活化处理后的PEO涂层进行化学镀镍处理,利用SEM对不同浸镀时间 (3、10和30 min) 的镀层表面形貌和浸镀30 min的镀层截面形貌进行了观察。
如图8所示,浸镀3 min后,Cu活化处理的涂层表面生成了许多花椰菜状结节,结节分布不均且大小不一,未能覆盖整个表面。然而,经Ag活化处理和Pd-活化处理的涂层浸镀3 min后,除孔洞处未被覆盖,剩余位置被均匀细小的结节覆盖。浸镀10 min后,Cu活化处理的涂层表面结节直径增大,但结节的直径依然相差较大,同时有少量区域未被结节覆盖。此时,Ag活化处理和Pd活化处理的涂层表面被镀层完全覆盖,PEO涂层表面的孔洞被完全填充,结节直径明显增大,但结节之间存在缝隙。在化学镀30 min后,3种活化方法处理的涂层表面结节直径进一步增大,且结节之间缝隙消失。但是,通过观察浸镀30 min镀层的截面SEM图发现,Cu活化处理后涂层表面的镀层较薄 (3 μm) 且不均匀,且未能完全填充PEO涂层孔隙。而Ag活化处理和Pd活化处理的涂层表面的镀层厚度更厚 (5 μm左右),且更加致密均匀。因此,Ag活化处理后PEO涂层的表面活性和Pd活化处理处理后PEO涂层的表面活性相近,并优于Cu活化处理后PEO涂层的表面活性,以Ag活化处理方法诱导沉积的化学镀层结节均匀,致密性好。
图8 Cu/Ag/Pd活化处理后浸镀3、10和30 min后镀层表面和浸镀30 min后镀层截面的SEM像
对Cu/Ag/Pd活化诱导沉积30 min的化学镀复合涂层进行XRD测试,结果如图9所示。测试结果表明,3种复合涂层表面的镀层均由Ni单质组成,呈微晶或非晶的结构。
图9 PEO-Cu-EN、PEO-Ag-EN和PEO-Pd-EN复合涂层的XRD图谱
2.3 不同活化方法对化学镀复合涂层耐蚀性的影响
2.3.1 动电位极化测试
通过电化学测试方法,对比了AZ91D镁合金和PEO-Cu-EN、PEO-Ag-EN、PEO-Pd-EN3种复合涂层在耐蚀性能方面的表现。图10为镁合金基体和三种复合涂层的动电位极化测试曲线。根据极化曲线可以得到膜层的自腐蚀电流密度 (Icorr)、自腐蚀电位 (Ecorr)。为避免镁合金的负差数效应带来的误差,Icorr的数值由极化曲线阴极部分Tafel外推法确定[17],表2汇总了极化曲线的拟合结果。与AZ91D镁合金相比,PEO-Cu-EN、PEO-Ag-EN和PEO-Pd-EN复合涂层的自腐蚀电位有了显著提升,自腐蚀电流密度也出现明显下降,这表明化学镀复合涂层提高了镁合金的耐腐蚀性能。在3种复合涂层中,PEO-Cu-EN复合涂层的自腐蚀电流密度略高于PEO-Ag-EN和PEO-Pd-EN复合涂层,同时,其自腐蚀电位又略低于PEO-Ag-EN和PEO-Pd-EN复合涂层,而PEO-Ag-EN和PEO-Pd-EN复合涂层的自腐蚀电位和自腐蚀电流密度相接近。因此,Ag活化得到的PEO-Ag-EN涂层耐蚀性能与传统Pd活化得到的PEO-Pd-EN涂层耐蚀性相近,优于Cu活化得到的PEO-Cu-EN涂层。
图10 镁合金及不同涂层的动电位极化测试曲线
表2 图10中动电位极化曲线的拟合结果
2.3.2 电化学阻抗谱
图11为AZ91D镁合金和PEO-Cu-EN、PEO-Ag-EN、PEO-Pd-EN三种复合涂层的电化学阻抗谱。电化学阻抗数据采用如图12所示的等效电路进行拟合计算,拟合结果如表2所示。
图11 镁合金及不同涂层的电化学阻抗谱
图12 拟合电化学阻抗谱的等效电路
当交流电干扰信号的频率无穷大和无穷小时,阻抗与实轴的交点为极化电阻 (Rp),而其倒数 (1/Rp) 与腐蚀速率成正比[18,19]。根据表3中的拟合结果,可利用公式 (7)、(8) 求得AZ91D镁合金和PEO-Cu-EN、PEO-Ag-EN、PEO-Pd-EN三种复合涂层的极化电阻 (Rp)[20],得到1/Rp的递减次序为:AZ91D (1.39×10-3 Ω-1·cm-2)>>PEO-Cu-EN (3.50×10-5 Ω-1·cm-2)>PEO-Pd-EN (2.12×10-5 Ω-1·cm-2)≈PEO-Ag-EN (2.05×10-5 Ω-1·cm-2)。因此,PEO-Pd-EN和PEO-Ag-EN复合涂层耐蚀性能相接近,并优于PEO-Cu-EN复合涂层,这与极化曲线得到的结果一致。因此,使用Ag活化方法替代传统Pd活化方法活化PEO涂层,可以在保证化学镀复合涂层的耐蚀性能的同时,降低了活化成本。
表3 电化学阻抗谱的拟合结果
2.3.3 中性盐雾实验
利用中性盐雾实验综合评估了PEO-Cu-EN和PEO-Ag-EN两种复合涂层的耐蚀性能,测试结果如图13所示。经盐雾实验336 h后,PEO-Cu-EN涂层表面已出现黑色的腐蚀点,并且可观察到较为明显的腐蚀产物堆积,而此时PEO-Ag-EN涂层表面仍未出现腐蚀点。在经受盐雾672 h后,PEO-Ag-EN涂层表面发生腐蚀,出现腐蚀产物堆积。结合中性盐雾实验和前文中电化学测试的结果,可以得出PEO-Ag-EN复合涂层耐蚀性能优于PEO-Cu-EN涂层
图13 两种涂层在中性盐雾过程中的宏观形貌
对Cu、Ag活化处理后涂层的表面形貌进行SEM观察表明,Cu活化处理后表面的含Cu球状颗粒大小不一、且分布不均 (图2和3),而Ag活化处理后表面的含Ag棒状颗粒较为细小并分布均匀 (图4和5);Cu、Ag活化处理后涂层表面的化学镀层生长过程进行观察表明,Cu活化处理后表面生成的镀层结节分布不均匀,结节直径相差较大,浸镀30 min后,仍未完全填充PEO涂层的孔隙,而Ag活化处理后表面生成了均匀致密的镀层结节,完整地覆盖了PEO涂层 (图8)。因此,经Ag活化处理后,PEO涂层表面分布均匀、细小的含Ag棒状颗粒可促进镀层均匀生长,形成了耐蚀性能更为优异的化学镀复合涂层。
3 结论
(1) 对不同浸镀时间PEO-Cu/Ag/Pd涂层表面的镀层形貌和浸镀30 min后镀层的厚度分析表明,Ag活化处理的PEO表面和传统Pd活化处理的PEO表面活性相近,且均优于Cu活化处理的PEO表面活性。
(2) PEO-Ag-EN复合涂层耐蚀性能优于PEO-Cu-EN涂层,同时与PEO-Pd-EN涂层耐蚀性相近。因此,使用Ag活化处理替代传统Pd活化处理PEO涂层,可以在保证镁合金表面化学镀复合涂层的耐蚀性能的同时,降低了活化成本。
参考文献: 略
免责声明:本网站所转载的文字、图片与视频资料版权归原创作者所有,如果涉及侵权,请第一时间联系本网删除。
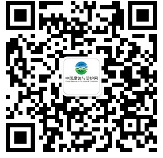
官方微信
《腐蚀与防护网电子期刊》征订启事
- 投稿联系:编辑部
- 电话:010-62316606-806
- 邮箱:fsfhzy666@163.com
- 腐蚀与防护网官方QQ群:140808414