案件背景
金属零部件在外加载荷的作用下,当应力达到材料的断裂强度时,发生断裂。其中80%以上的断裂是由于疲劳引起的,极易造成人身事故以及经济损失。因此认识疲劳现象,研究疲劳破坏规律,防止疲劳失效是非常重要的。我司昆山实验室收到客户委托,客户产品为45#钢倾油缸接头,在模拟使用条件下进行加速实验约2万次时,发生断裂现象,委托优尔鸿信检测分析其断裂原因。
测试方案
断口形貌观察:样品断口形貌分析,初步判断其断裂形式;
显微金相组织分析/洛氏硬度测试:查看其热处理工艺;
化学成分测试:分析判断其含量是否符合国家标准。
SEM断口形貌
2#-20X
5#-20X
扫描电镜观察断口形貌,通过SEM扫描照片可知:图2#-20X和5#-20X为样品断口裂纹源低倍形貌,可见样品外缘存在多个台阶,呈明显的线源特征,结合样品宏观形貌,肉眼可见断口边缘区域有挤压摩擦变亮痕迹,可判断裂纹起源于轴根部外表面螺纹凹痕处,该断口属多源且有应力集中现象。将裂纹源附近放大后观察,可见明显的疲劳辉纹,呈疲劳断裂特征。
1#到6#位置SEM照片可以看出样品内部存在明显的疲劳辉纹及大量的二次裂纹,在部分区域可观察到机械损伤的犁痕和氧化特征,犁痕方向与断裂过程的受力方向基本一致。疲劳辉纹的扩展方向大部分由断口表面两侧向中间位置扩展。7#位置中部发现韧窝结构,因此中间轴区域为最终断裂阶段。大致断裂方向如图箭头所示。
金相组织分析
样品断口附近取样,经过研磨机械抛光制成金相试样,用4%硝酸酒精溶液腐蚀后,用金相显微镜观察金相组织可见:材料内部存在夹杂物及孔洞,断口附近金相组织主要由网状铁素体+少量块状铁素体+珠光体组成,不符合调质组织。
洛氏硬度分析
将样品表面漆层打磨掉,用洛氏硬度计测试样品硬度值可知,洛氏硬度值为86.3HRB,硬度偏低。
化学成分分析
备注:所给成分结果为质量百分比
将样品表面漆层打磨掉,用火花原子放射光谱仪测试化学成分可知,化学成分符国家标准中45#钢成分要求。
原因分析
断口宏观和微观分析结果表明:裂纹源位于螺纹凹痕位置外表面,裂纹源存在多个台阶,呈明显的线源特征,断口上可见明显疲劳辉纹,因此可判定样品断裂模式为多源疲劳断裂,且有应力集中现象。
断口台阶是多个疲劳源萌生的裂纹交汇台阶,一般在高应力集中疲劳断口中
常见,加速实验过程中,螺纹凹痕处造成应力集中,使凹痕根部的最大实际应力远大于零件所能承受的名义应力。在循环应力作用下,凹痕截面上的应力状态发生变化,从而影响试件的力学性能,对零件产生疲劳破坏。较大尺寸的非金属夹杂物也是疲劳裂纹的启裂源。
试样内部存在孔洞及夹杂物、组织分布不均匀、热处理不当等因素可导致试样的实际承载能力和安全性能大大降低。金相组织存在网状铁素体和少量块状铁素体,造成材料软点,硬度偏低。
结合以上试验结果,对样品发生疲劳断裂的原因分析如下:
(1)热处理不当
材料的微观组织与工艺、性能密切相关,原材料可能未经调质处理或调质处理不当,造成该试样的力学性能较低。
(2)应力集中
试样在加速实验过程中承受双向弯曲载荷的作用,螺栓螺牙处应力集中使局部区域的应力值超过了该轴按预定寿命所能承受的应力水平,致使裂纹在轴表面萌生。
建议
为避免倾油缸接头发生类似断裂失效问题,应从材料热处理工艺、表面加工质量等方面层层把关,严格执行标准技术要求。
免责声明:本网站所转载的文字、图片与视频资料版权归原创作者所有,如果涉及侵权,请第一时间联系本网删除。
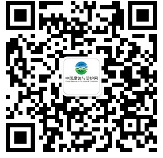
官方微信
《腐蚀与防护网电子期刊》征订启事
- 投稿联系:编辑部
- 电话:010-62316606-806
- 邮箱:fsfhzy666@163.com
- 腐蚀与防护网官方QQ群:140808414