摘要:为了提高汽轮机叶片的可靠性预防电厂中汽轮机叶片疲劳断裂的发生首先提出了叶片应力和动态特性的数值分析方法然后基于动态应力分析结果考虑了影响汽轮机叶片失效的各种因素引入Neuber 准则和雨流计数法建立了汽轮机叶片的疲劳寿命预测模型并分析了一个5片成组的851mm 叶片疲劳寿命状况.结果表明:提出的汽轮机叶片动态应力三维有限元分析模型具有良好的工程精度叶片疲劳寿命预测可以定量地分析影响叶片安全运行的各种因素和叶片的疲劳寿命为现实中叶片的设计制造及汽轮机运行提供了参考.
关键词:汽轮机;叶片振动;动态应力;高周疲劳;疲劳寿命;数值分析
汽轮机叶片的运行环境十分复杂叶片事故时有发生叶片的检修费用占汽轮机检修费用的505%[1]其中大部分是由于叶片的疲劳断裂所致[2].目前汽轮机叶片设计和安全性考核主要采用的是建立在材料力学基础上的许用应力为基准的静强度准则和以安全倍率为标准的动强度准则.这些准则对于汽轮机叶片的设计发挥了重要的作用但许用应力方法无法精细考虑叶片局部的应力和由于交变载荷产生的疲劳失效而安全倍率方法是基于叶片事故统计数据的对于影响叶片安全性的许多因素如激振力、结构特点、阻尼等无法定量估算其方法是比较粗糙的.随着社会发展对于汽轮发电机组制造和运行的进一步要求以上准则已经不能完全满足需要.本文以叶片的三维动态应力分析为基础考虑了多种对叶片疲劳寿命有影响的因素建立了汽轮机叶片的疲劳寿命分析模型最后分析了5片成组的851mm 叶片的疲劳寿命.
1 叶片三维有限元动态应力分析
动态应力分析是叶片疲劳寿命分析的基础有许多的学者如朱宝田[3]、郑润生[4] 等人发展了各种叶片的动态应力分析方法并且取得了很大的成果.但是他们或者是对叶片的一个部分进行分析或者人为地忽略了叶片结构的某些因素不能反映叶片的整体应力状况分析模型距离真实叶片尚存在一些差距.因此有必要发展出一种适合于叶片动态应力分析的真实三维有限元分析模型.
1.1 叶片计算的三维有限单元
线性八节点协调单元在承受弯曲载荷时由于寄生剪切效应计算变形比实际结构应该产生的变形要小有时可能会使计算结果发生严重失真因此对于汽轮机叶片尤其是长叶片这种单元模型是不太合适的.三维八节点非协调单元[5] 是在线性八节点协调单元的基础上在单元内部增加了9个自由度大大改善了单元的抗弯性能保证了使用此单元对叶片进行应力分析结果的正确性.本文采用非协调单元进行分析获得了良好的计算精度.
1.2 叶片动态应力场的求解
转动叶片的运动微分方程[6]为
(1)
式中:[ M]是质量矩阵;[ C]是阻尼矩阵;[ MG ]是陀螺矩阵;[ Kc ]是离心力刚度矩阵;[ K0]是线性刚度矩阵;VeNL是叶片单元考虑二次项后的非线性应变能;{Qc}是叶片的离心力载荷向量;{Qp}是叶片表面上的气流力向量;{F( t)}是作用在叶片上的非稳态力;{δ¨}、{δ· }、{δ}是加速度、速度和位移向量.忽略叶片几何大变形的影响上式中叶片的非线性应变能可以写为
(2)
式中:{εl}是非线性应变;[ Kσ]是初应力刚度矩阵.对于汽轮机叶片的静力计算由式(1)可以得到以下方程
(3)
又由静力计算方程可以得到转动叶片的动频计算方程为
(4)
式中:[Φ]是特征向量;[Λ]是特征值即叶片的动频.
在分析得到叶片的动频和其特征向量以后就可以使用振型迭加法求得叶片的稳态响应.通过傅里叶分解处理作用于汽轮机叶片上的激振力则汽轮机叶片的稳态响应为
(5)
其中
(6)
式中:i 代表某一阶模态;K 代表某阶激振力;ζi 为模态阻尼比.
由叶片的响应值很容易得到叶片的动态应力.各个位移响应就是某个时刻叶片所处的位移场根据位移场可以由下式
求得各时刻叶片有限元模型各个节点处的应力而叶片各个节点应力随时间的变化就是结构的动应力.
2 叶片疲劳寿命分析方法
从本质上来说疲劳断裂是由于承受动态载荷所产生的即使在动应力数值远远小于材料的静强度的情况下仍然可能造成疲劳损坏[7].一般将零件或部件的疲劳寿命划分为疲劳裂纹初始寿命(简称为始裂寿命)和疲劳裂纹扩展寿命.汽轮机叶片的大部分寿命都是消耗在疲劳裂纹起始上面所以研究中一般都把裂纹的起始寿命定义为叶片的疲劳寿命[6]在疲劳寿命分析中使用的“局部应力应变法”所研究的就是叶片的致裂寿命.在一般的情况下虽然名义应力处于弹性范围但从局部微观角度看塑性变形仍然存在而使用有限元方法要分析到很细致的局部微观应力其人力和物力的消耗是极其巨大的所以本文采用具有良好的工程精度、使用起来十分方便的Neuber 准则[8] 来分析叶片的局部应力应变分析中用到的名义应力就是由本文前面三维有限元模型计算得出的.在分析完局部应力应变后本文采用雨流计数法进行计数.这种方法从计数原则上看与材料的应力应变迟滞回线相一致能够反映随机载荷的全过程.
局部应力应变法是在低周疲劳寿命估算方法的基础上发展起来的在对汽轮机叶片进行高周疲劳寿命分析时需要进行一些必要的改进.本文中的模型考虑了尺寸效应(使用尺寸系数εd 表示)、叶片表面加工和表面处理(使用表面状态系数β来表示β=βsβcβpβs 是表面加工系数、βc 是腐蚀系数、βp 是表面强化系数)、微动磨损等方面的影响(使用微动疲劳系数αf 表示).以上系数的一些具体数值可以参考文献[9]选取.考虑到以上疲劳强度和平均应力的影响对Manson-Coffin 曲线的弹性线进行修正[10],取
(8)
将弹性线中的b 以b′代替引入Morrow 对Manson-Coffin 曲线的修正可以得到修正的应变-寿命曲线用下式表示
(9)
本文在进行疲劳累积损伤分析时使用以下修正线性累积损伤公式进行计算
(10)
考虑到叶片的实际情况根据文献[9]的建议取α为068.
3 5片成组的851mm 叶片疲劳寿命分析
作为实例本文对某国产300MW 汽轮机组的末级5片成组的851mm 叶片进行了分析.5片叶片通过叶顶Z 型围带和相对叶高为055处的Z 型拉筋焊接成组.叶片组的有限元计算网格见图1.中间叶片的静态应力场分布如图2.本文分析得出叶片的前3阶动频见表1同时给出了实验值进行对比.因为动频的计算与叶片的静态初应力场及单元模型的选取是密切相关的从表1可看出动频良好的计算精度这也从另一方面说明了本文所提供的分析叶片静态应力场模型的精确性.叶片的第2和第3阶振型如图3所示.根据表1动频分析结果本文对叶片组进行了三维动态应力分析获得了叶片型线、拉金和围带上危险点的等效应力随时间的变化.图4是型线部分危险点的应力状态随时间变化的曲线.获得动应力状态后就可以进行叶片的疲劳寿命分析了.
图1 叶片组网格图
图2 中间叶片静态应力分布
表1 5片成组的851mm 叶片的动频值
(a)第2阶 (b)第3阶
图3 851mm 叶片组的第2阶和第3阶振型
图4 叶型上危险点的等效应力时域图
根据851mm 叶片的材料特性数据和所处的工作环境对Manson-Coffin 曲线进行修正在其中取尺寸系数εd =05表面加工系数βs =10表面强化系数βp =10因叶片位于湿蒸汽区取腐蚀疲劳系数βc=06得到叶片的应变-寿命曲线如下
(11)
在汽轮机的运行过程中如果由于水质不良将使叶片的腐蚀疲劳系数进一步下降因此又选取腐蚀疲劳系数βc =0 5进行了分析分析结果见表2.
表2 851mm 成组叶片寿命分析结果
从表2的分析结果可以看出对于851mm 的成组叶片来说型线部分寿命最短正常运行状况时为691 1a可见正常使用的851mm 成组叶片是一个使用寿命比较长的叶片.
以上的分析涉及到了影响叶片寿命的各个因素并且通过具体的寿命计算分析了它们对叶片寿命的影响从中可以看出叶片材料的性能、叶片表面加工及热处理工艺、叶片的运行工况及环境是影响叶片寿命的重要因素.
4 结 论
(1)本文所提出的叶片动态应力三维有限元分析模型具有良好的工程精度能够得到令人满意的结果.
(2)本文建立的汽轮机叶片疲劳寿命预测模型考虑了汽轮机叶片制造和运行中的多种因素(如腐蚀环境、表面加工状况等)对于叶片寿命的影响叶片寿命的分析结果不但可以得到一些定性方面的概念还具有一定程度的量化指导意义.
(3)本文基于叶片三维有限元动态应力结果和金属材料疲劳理论所提出的汽轮机叶片疲劳寿命预测方法不仅为汽轮机叶片设计提供了一个从寿命消耗方面评价叶片安全性的新评估方法并且为在汽轮机运行方式日益复杂的情况下进行叶片寿命管理提供了新思路及实用工具.
参考文献:
[1] 丁有宇周宏利徐 铸等.汽轮机强度计算[M].北京:水利电力出版社1985.220~226.
[2] 吴厚钰.透平零件结构和强度计算[M].北京:机械工业出版社1982.56~60.
[3] 朱宝田.汽轮机叶片振动、激振力和动应力特性及其优化研究[D].西安:西安交通大学能源与动力工程学院1993.
[4] 郑润生吴厚钰.采用扭杆单元分析汽轮机长叶片振动的有限元法[J].西安交通大学学报199125(3):99~110.
[5] 谢永彗安 宁王乐天等.汽轮机叶片三维有限元应力分析系统[J].西安交通大学学报199730(8):56~61.
[6] 谢永慧.汽轮机叶片疲劳失效、寿命预测及设计分析系统的研究[D].西安:西安交通大学能源与动力工程学院1997
[7] Naeem MSingh RProbert D.Implication of enginedeterioration for a high-pressure turbine blade′s low-cyclefatigue (LCF) life-consumption [J].Interna-tional Journalof Fatigue199921:831~847.
[8] Fuchs H OStephens R I.Metal fatigue in engineering[M].New York:John Wiley & Sons Inc1980.141~144.
[9] 赵少汴.抗疲劳设计[ M ].北京:机械工业出版社1994.114~120.
[10] Newport AGlinka G.Effect of notch-strain calculationmethod on fatigue-crack-initiation life predictions [J ].Experimental Mechanics199030(2):208~216.
免责声明:本网站所转载的文字、图片与视频资料版权归原创作者所有,如果涉及侵权,请第一时间联系本网删除。
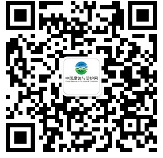
官方微信
《腐蚀与防护网电子期刊》征订启事
- 投稿联系:编辑部
- 电话:010-62316606-806
- 邮箱:fsfhzy666@163.com
- 腐蚀与防护网官方QQ群:140808414