摘 要:等离子-物理气相沉积(PS-PVD)是制备高温防护涂层和功能涂层的一种新方法,既可涵盖等离子喷涂和电子束物理气相沉积工艺,还可实现涂层宏观/介观/微观等跨尺度结构的定制化设计与制备,在热障涂层(TBCs)、环境障涂层(EBCs)、环境热障涂层(TEBCs)、透氧薄膜、燃料电池和太阳电池电极薄膜等领域具有广泛应用前景,尤其在航空发动机和燃气轮机防护涂层领域被视为高性能TBCs/EBCs 制备技术发展的新方向。比较分析了PS-PVD 等离子射流膨胀流动、材料快速加热气化离化和长距离多模式输运沉积的全流程过程,介绍了PS-PVD 原理与设备系统,面向等离子射流参数快速无损检测分析的目标,建立了基于光学发射光谱学(OES)的等离子射流和材料特性非接触式检测与诊断装备系统,发展了射流和材料特性参数的定量表征和精确诊断方法。依据电子数密度等检测结果,进一步计算分析等离子温度分布规律。基于射流与材料检测结果,研究了粉末材料在等离子射流中的多相态转变行为,归纳了调控沉积单元多相态转变的工艺控制参数集。这些硬件平台和表征检测方法的建立,为构建PS-PVD 理论和研制新型高性能热防护涂层提供了坚实的理论基础和必要的条件支撑。
关键词:等离子-物理气相沉积;沉积系统;非接触检测系统;光学发射光谱;输运机理;热防护涂层
航空发动机和燃气轮机制造技术是衡量一个国家工业水平的重要标志,并在国民经济中发挥着重要作用。热障涂层(TBCs)是一种主要应用于热端构件表面,起隔热作用的功能涂层,是先进航空发动机和燃气轮机研制的三大关键技术之一[1-3]。通过将低热导率的高熔点TBCs 涂覆于高温合金表面,从而避免高温工作介质直接作用在金属基体表面,可降低合金表面温度(80~150 ℃)[4-8]。目前应用广泛的TBCs制备技术是大气等离子喷涂(APS)与电子束物理气相沉积(EB-PVD)技术[9-10]。APS 技术是最常用的等离子喷涂方法,具有沉积效率高[11-13]、工作稳定和经济可行的优点,因此在航空发动机和燃气轮机的静部件上(如燃烧室和涡轮盘)有广泛的应用。APS 采用由气体电离产生的热等离子体作为热源,可以熔化大部分金属与陶瓷材料。材料在APS 中加热至熔化或者半熔化,沉积形成具有层间孔隙的层状结构涂层,可以有效阻止热量传导,因此具有低的热导率(~0.94 W/(m·K)),然而热循环过程中不断累积的热应力导致涂层极易剥落失效[14-16]。EB-PVD 技术相对于APS,主要利用电子束将材料加热蒸发,材料以气相形式沉积,制备的涂层为具有纵向间隙的柱状结构,可在热循环过程中释放应力,具有更高的应变容限,热循环寿命提高数倍,主要用于航空发动机和燃气轮机的高压涡轮工作叶片,但是EB-PVD 沉积效率低(1~3 μm/min),涂层热导率较高(1.5~1.9 W/(m·K))[17-18]。
等离子-物理气相沉积(PS-PVD)被认为是基于等离子喷涂(PS)和物理气相沉积(PVD)两项强大的涂层与薄膜制备技术结合而产生的新兴涂层与薄膜制备技术,由于具有可在形状复杂零件表面绕镀均匀制备涂层、沉积速率高等突出特点,已成为国内外研究热点。国际上,苏尔寿美科公司率先基于低压等离子技术,开发了PS-PVD 系统与技术,紧接着包括德国于利希、法国贝尔福在内的众多国际科研院所对PS-PVD 在制备热障涂层方面的潜在优势进行了大量的研究与报道。由于PS-PVD 低的腔室压力,PS-PVD的等离子射流被拉长至约1~2 m,直径扩张至0.2~0.4 m(图1a—c),可以沉积形成类APS 的层状结构涂层、类EB-PVD 的柱状结构涂层以及气固共沉积的复合结构涂层(图1d—f)[19-21]。国内在PS-PVD 研究方面已取得众多进展,广东省新材料研究所、北京航空航天大学、北京矿冶研究总院、航天材料及工艺研究所、上海硅酸盐研究所等相继从Sulzer Meltco公司、Medicoat 公司引进了PS-PVD 设备。在PS-PVD技术蓬勃发展的同时,广东省新材料研究所、北京航空航天大学、北京矿冶研究总院、西安交通大学大学等单位开展了PS-PVD 等离子射流特性、材料输运行为(材料与等离子射流的相互作用)、涂层微结构形成机理等基础研究,为推进国内PS-PVD 技术的进步与未来产业化应用做出了重要贡献。
目前,PS-PVD 研究的关注焦点是涂层结构的调控[22-29]。研究人员分别研究了送粉率、等离子气体组成和沉积距离等工艺参数对涂层结构的影响:1)当送粉率由小到大时,涂层结构将由全气相沉积的柱状结构向气相/cluster 共沉积的类柱状、再到液相沉积为主的层状结构转变;2)当以Ar/H2 为等离子气体时,主要获得的是以液滴沉积的扁平粒子致密结构涂层,而当以Ar/He 为等离子气体时,主要获得团簇与气相原子共同沉积的类似EB-PVD 的柱状结构涂层;3)随沉积距离由近及远的变化,涂层结构分别呈现致密层状结构、紧密填充的柱状结构、具有更多颗粒的准柱状结构、类EB-PVD 柱状结构、表面光滑而柱之间有较大的间隙的准纳米级柱状结构。而从构成涂层微观结构的基本单元的角度来看,沉积单元的类型决定了涂层的结构,例如层状结构涂层主要由液相沉积单元组成,柱状结构以气相沉积为主,而复合结构则融合了气液固的多相沉积。事实上,对于PS-PVD常用的喷涂粉末M6700(YSZ, Sulzer Metco),其初始粒径尺寸为70~130 nm,而团聚后粒径尺寸为5~22 μm,在注入喷嘴进行加热和蒸发之后,必须经过长距离输送才能最终沉积在基体表面。当材料在射流中运输时,材料的特性(即沉积单元的特性)将受到等离子体射流特性的影响。在PS-PVD 过程中,等离子气体与沉积单元一起离开喷嘴,并在明显低于喷嘴压力的腔室压力下形成等离子射流,射流呈现典型的膨胀不足现象(如图1c 所示)[30-32]。由于高的功率输入以及低的腔室压力,等离子体能量高、克努森数大,处于类自由分子流状态,因此与传统的等离子喷涂工艺相比,PS-PVD 等离子体射流中的温度和速度更高,分布更均匀,而等离子体射流与材料的相互作用却非常弱。
图1 不同压力下等离子射流扩张图像与PS-PVD 技术制备的涂层结构[19-20]
由于PS-PVD 特殊的工作条件,等离子射流特性与材料特性难以用常规手段进行检测。本文主要综述了目前在PS-PVD 射流与材料特性方面的研究进展,并着重介绍了西安交通大学对PS-PVD 原理和设备系统、射流与材料特性的非接触检测系统的研究,并基于设备系统,研究建立的射流与材料特性的定量表征方法以及基于光谱学诊断阐明的PS-PVD 射流与材料交互作用规律、材料输运机理等,旨在为发展PS-PVD涂层制备理论提供测量表征的手段和依据。
1 PS-PVD 原理与设备系统
PS-PVD 技术采用大流量真空泵,真空容器内的动态工作压力可降到1~2 mbar,等离子射流长度可达到2000 mm,直径为200~400 mm,由于其配置大功率喷枪(>120 kW),射流温度能达到6000~10 000 K[33]。此外,该技术具有非视线沉积的特点,可以沉积几何形状复杂的部件,沉积方式不仅有液相沉积,还有纳米团簇和气相沉积,这为获得先进的微观结构提供了新的途径,从而满足现代功能涂层不断增长的需求,为热喷涂技术的应用提供了新的机遇。目前,Oerlikon 和Medicoat 两家公司[34-35]均可提供PS-PVD设备,为国内广东省新材料研究所、北京航空航天大学、北京矿冶研究总院、航天材料及工艺研究所、上海硅酸盐研究所等多家单位提供了服务。
在先进材料和高端装备基础研究规划资助下,西安交通大学在探索PS-PVD 原理的过程中,自主设计研发了首台具有真空机器人控制系统的PS-PVD 系统样机,如图2 所示。系统包括:主动冷却真空室、全自动真空系统、真空机器人与工装系统、测量及控制系统,可在真空度为50~90 000 Pa 的密封真空室内进行涂层沉积或材料合成,可实现PS-PVD、PS-CVD、LPPS/VPS(真空等离子喷涂)等功能。压力检测位置位于工作台处,等离子喷枪置于密闭真空环境下,由自主研制的真空机器人夹持,与旋转工作台配合使用,可实现6 轴联动。将粉末材料送入经电离产生的等离子体射流中,使粉末颗粒在其中加速、熔化或气化,在机械手操作下喷射到工件表面,在冲击力的作用下,气化、半熔化或以塑性状态射流在基底上凝固形成涂层。系统配备相应的除尘、冷却等附属装置,为测温测速等外加检测等预留多个窗口,并加装有专门用于热红外成像仪的透红外专用窗口。
图2 PS-PVD 系统
2 等离子射流与材料特性的定性检测方法
在低压下,PS-PVD 射流较常压下被显著拉长、剧烈膨胀,这种被显著不同于原有大气等离子和真空等离子的射流特性,使其内部材料的输运行为产生巨大变化。因此,必须采用有效手段深入研究射流和材料特性。
2.1 射流内粉末气化前的颗粒状态检测
DPV-2000 在PS-PVD 射流特性与材料特性诊断中的应用相对较少, 在早期对低压等离子喷涂(LPPS)的研究中,M. Gindrat 等人[36]利用DPV-2000研究了射流中粒子速度的分布,如图3 所示。西安交通大学引进了Tekna 公司的DPV-2000 系统,用于检测射流内粉末气化前的颗粒速度/温度,如图4 所示。由于DPV-2000(检测直径10~300 μm)只能探测飞行中尺寸大于~10 μm 的熔融颗粒,故对于PS-PVD中粉末气化后的状态无法监测。
图3 DPV-2000 系统在LPPS 研究中用于测试射流内粉末气化前的状态[36]
图4 DPV-2000 系统
2.2 等离子射流热焓测量方法
等离子射流热焓主要是利用热焓探针进行测量,热焓探针技术发展于20 世纪60 年代,最初以探头设计研究为主,后逐步应用于APS 的焓值测量。随着最近几年低压等离子喷涂技术的发展,热焓探针技术的研究主要集中在低压等离子喷涂中射流的特性诊断[37-40]。热焓探针技术可以在己知混合气体成分组成的情况下,确定等离子射流的温度和速度,以便对喷涂工艺参数进行优化,获得可靠的涂层结构。张楠楠等[37,41]使用改造后的热焓探针对等离子射流的焓值、温度和热流量进行了检测,如图5 所示。然而,热焓探针前部在低压等离子体射流内会形成激波,而且在高温高速射流下,热焓探头稳定性不足,探头寿命大大缩短。因此,在PS-PVD 工艺下,很难通过诸如静探针法或特定焓探针测量的诊断,获得关于等离子体射流的精确数据和信息,并且会极大地增加热焓探针在PS-PVD 检测中的成本。
图5 利用改造后的热焓探针诊断等离子射流[37]
2.3 射流与材料特性的非接触定性表征方法
针对PS-PVD 的特殊操作环境,目前主要利用非接触式诊断技术—光学发射光谱(OES),对等离子射流与材料特性进行检测[30,42-43]。
2.3.1 射流特性的定性表征
研究人员首先利用OES 定性地研究了PS-PVD射流特性受等离子气体组成的影响,图6 所示为不同等离子气体组成下,等离子射流图片与OES 诊断结果[20,44]。由等离子射流图片中的辐射强度可以明显地看到,当等离子气体组成中含有氢气时,等离子射流的径向温度分布会变宽,而当氦气作为等离子气体组成之一时,由于氦气的高黏度,可以有效地聚束射流,而且从光谱图结果可以看到,Ar/He 组合的等离子气体具有更高的谱峰强度。根据上面的分析,谱峰强度是处于激发态粒子含量的表现形式之一,因此它反映了等离子射流所具有的能量高低,这也说明Ar/He 组合的等离子气体更适合作为PS-PVD 用等离子气体,从而更好地气化材料。
图6 利用OES 定性研究等离子射流特性(A—D 为不同等离子气体组成下等离子射流实物图片与不同等离子气体在射流内沿径向的分布)[20]
2.3.2 射流中材料的定性表征
利用OES 除了可以实现对等离子射流的诊断外,还可以对射流中的材料特性进行定性表征,而通过结合OES 诊断结果与涂层结构的关系,可以定性地反映出等离子射流特性通过影响材料特性而决定涂层结构。图7 的A—C 显示了不同等离子气体组成对涂层材料粒子轨迹的影响,这些轨迹可以用锆的蓝色辐射特性来识别[20]。显然,氦气不仅对等离子气体流动有很好的聚束作用,而且对涂层材料粒子束流也有明显的聚束作用。另外,氢气的加入使等离子温度分布变宽,这严重影响了涂层材料粒子的加热效果。等离子气体组成在粒子的热历史中的显著影响被大量可沉积的涂层微结构所证实,因为改变等离子气体组成时,可以得到由液滴沉积的致密涂层、由纳米结构团簇和气相共同沉积的柱状结构涂层,甚至可以得到由完全气相原子沉积的柱状结构涂层,这反映出等离子射流特性通过影响涂层材料状态而影响涂层结构。当等离子气体中使用H2 而不是He 时,未蒸发的液滴的量增加,基于图7D 中不同等离子气体的热焓值可以看出,这主要是由于Ar/H2 的等离子体温度显著低于Ar/He 等离子体。
图7 利用OES 定性研究等离子射流内材料特性(A—C 为加入材料后射流图片与材料
在射流内沿径向的分布,D 为不同等离子气体的比焓)[20研究者在利用OES 检测到的特征光谱线强度定性说明粉末粒子气化与否的基础上,建立了OES 特征光谱线强度与沉积的涂层结构之间的关系。Gindrat等[36]采用OES 对PS-PVD 沉积Zn 工艺过程中的等离子射流进行检测,在检测结果中出现了Zn 的特征光谱线,定性判断Zn 气化了。Niessen 等[30]对PS-PVD工艺中的等离子射流进行OES 检测,对比了柱状结构涂层沉积工艺和非柱状结构涂层沉积工艺中检测到的OES 光谱线强度。发现在OES 检测的YSZ 特征光谱线(如图8 所示)中,当YSZ 的特征光谱线强度高时,沉积的涂层为柱状结构,反之则为非柱状结构。作者据此来定性说明气相沉积的发生与OES 特征光谱线强度大小之间的关系,进一步说明了粉末粒子气化量足够大的时候,才能够由气相沉积得到柱状结构涂层。此外,Mauer 等[20]通过OES 表征不同送粉速度条件下Zr 的特征光谱线强度,发现了等离子射流中粒子状态的变化规律(如图9 所示)。研究发现,送粉速度小于1 g/min 时,等离子射流能够完全气化送入的YSZ 粒子;随送粉速度增大,等离子射流中YSZ 粒子的状态变化规律为气相→团簇→粒子态→液态。进一步通过理论计算发现,喷枪出口处等离子射流的温度为10 000 K,喷枪出口内侧的温度则更高(>12 000 K);喷枪出口处等离子射流速度最高达到6000 m/s;喷枪出口处等离子射流的热交换能力达到108 W/m2。通过研究发现,采用现有的设备及参数,超低压下等离子射流的热交换能力能够气化1 μm 以下的YSZ 粒子,且粒子的气化主要发生在送粉口至喷枪出口这段距离。当等离子射流离开喷枪出口后发生扩张,等离子射流的温度和速度均出现显著降低,这与上一小节中等离子射流的研究结论相同。
图8 YSZ 谱线强度与涂层结构关系[30]
图9 不同送粉速度条件下粉末粒子状态变化规律[20]
3 PS-PVD 射流特性检测系统与定量测试方法
从以上研究结果可以看出,虽然研究者对等离子射流特性有一定的研究,同时可以定性地解释粒子的气化程度,但对于不同区域内材料特性的变化及进一步对涂层结构的影响与调控仍然没有深入地研究,而这却是PS-PVD 沉积机理的重要组成部分,同时是调控涂层结构的基础理论支撑。为此,本课题自主设计了PS-PVD 射流特性OES 检测系统,基于非接触式光谱诊断,建立了PS-PVD 等离子射流内材料特性研究方法与基于射流特性与材料特性的涂层结构调控方法。
3.1 射流特性检测系统的设计研制
随着研究的不断深入,OES 被广泛地应用于检测由等离子气体以及材料激发而发射出的不同波长的光,以研究等离子射流与材料的特性。OES 具有响应速度快、不容易受到流场干扰的优点,可以获得等离子体的一些基本特征,如射流的电子数密度、电子温度、局部热平衡状态等。OES 的系统组成主要包括汇聚镜头、色散系统和检测系统,为便于检测,收光汇聚镜头被用于收集等离子激发态粒子发射出的光线,再通过光纤与发射光谱仪相连接,将光信号传输到色散系统的光栅,分散成不同波长的光谱,检测系统对不同波长的光线进行检测并进行相应的处理,最终通过电脑输出测量结果。
对于每个原子或离子而言,都有特定的一组稳定量子态,其具有的一组分立的特征能量或电子结合能为Ek,当一个粒子(原子或离子)的轨道电子从高能级Ej 跃迁到低能级Ei 时,会辐射出频率为ν 的光子。在光谱实验中有:
式中,γ 为波长,c 为光速,Ej 与Ei 分别代表能级j、i 的激发能。
OES 输出的谱线强度代表了单位时间源体积所辐射的总能量(实际上,由于光子传输等造成的能量损失以及其他实验测试误差,实际谱线强度与OES输出的谱线强度存在偏差),因此粒子轨道电子从高能级j 至低能级i 跃迁得到的谱线强度Iji 可近似地以公式(2)计算:
式中,Aji 为粒子从高能级j 至低能级i 跃迁的跃迁几率,nj 是处于较高能级j 的粒子数目,h 为普朗克常数(6.62×10?34 J·s),Iji 为能级j→i 跃迁所发出光谱的强度。对于等离子体而言,不同的粒子可以利用光谱波长的不同进行鉴别,而从公式(2)可以看出,光谱线的强度取决于三个因素:受激发的粒子含量、跃迁几率和辐射频率。因此,可以进一步地利用光谱线的强度计算各种粒子的含量。事实上,由于上面提到的光路损失及其他测试误差的原因,OES 输出的谱线并不能用来定量地计算各种粒子的含量。
图10 光谱仪与OES 检测系统
图11 OES 检测区域
西安交通大学自主研发PS-PVD 系统以来,便从Priceton 公司购买了Acton SP2750 光学发射光谱仪,并自主搭建了OES 诊断系统,图10 为光谱仪与自主搭建的OES 检测系统。系统由收光镜头(ModelFC-446-030)、光纤与带有CCD 摄像头(PIXIS-2KBUV)的光谱仪(Acton SP2750, Priceton)组成,并由装有WinSpec32 软件的计算机输出光谱结果。基于此系统,本课题组开展了PS-PVD 等离子射流特性的系统研究,并建立了基于光谱诊断的射流中材料特性研究方法与材料多相态调控理论,从PS-PVD 材料相态调控的本质机理上发展了涂层结构调控理论。基于本课题组的研究发现,从等离子射流中发射出的光线通过汇聚镜头接收,汇聚镜头的检测范围并不是射流中的一个点,而是如图11 所示的类柱状检测区域。检测区域内粒子辐射出的光信号被汇聚镜头收集后,通过光纤传输到发射光谱仪。光信号通过入射狭缝A,经过准直光镜B 反射后,变成平行光到达分光设备C光栅进行分光。本课题组的光谱仪系统有三个光栅可用于选择,分别是300、1200、2400 grooves/mm,光栅分光是利用光的衍射现象进行分光,通过多缝干涉和单缝衍射一起产生作用。其中,多缝干涉与光谱线的空间位置有关,单缝衍射则决定了各级光谱线的强度。经过分光设备后,入射光被分解为不同波长的谱线,分解后的光经聚焦镜聚焦D 后,传入检测系统CCD 摄像机,通过光电转换器件将光信号转换为电信号,通过软件处理后便会输出光谱谱线。图12 为利用OES 采集的PS-PVD 等离子射流光谱图,在此基础上,研究了等离子射流的电子数密度与温度,结果如图13 所示[45-46]。目前,通过OES 对PS-PVD 等离子体射流特性的诊断已经进行了大量的研究,接下来的部分中,将对本课题在光谱诊断PS-PVD 射流及材料特性方面的研究进展进行介绍,并着重介绍基于OES 光谱诊断建立PS-PVD 射流中材料特性的研究方法与涂层结构调控方法。
图12 PS-PVD 的OES 典型光谱图[45]
图13 PS-PVD 射流的电子数密度、温度[46]
3.2 射流特性定量测试方法
在PS-PVD 过程中,由于其高功率、低室压的特点,涂层材料除被气化形成气态原子或分子外,还有大量的材料连同等离子气体一起被激发为不同价态的离子状态,这些原子与离子在高温低压下被激发到不同的高能级,由高能级向低能级跃迁过程中便会向外辐射具有特征波长的光,这正为OES 检测PS-PVD等离子射流特性提供了可能。通过OES 检测PS-PVD射流的粒子特性,首先利用收光镜头,检测区域内待分析原子及离子由高能激发态向低能级跃迁过程中辐射出的特征光线,再经光谱仪分析,输出一系列与不同原子和离子辐射的特征波长的光具有对应关系的特征光谱。由于OES 输出的光谱代表了发射这些辐射光的原子和离子的特征,是这种粒子和它的电离状态的本质固有特性,因此通过改变激发条件,只会改变特定谱线的强度,而谱线代表的固有特征波长或频率不会发生改变。此外,对于不同原子或离子的能级谱图以及同种原子或离子不同能级之间跃迁产生的光谱也各不相同,因此只要在OES 输出的光谱中辨认出各种粒子所对应的特征光谱图形,就能定性地鉴别PS-PVD 射流的粒子构成。
对于电子数密度的研究主要采用对OES 特征谱线进行展宽分析的方法。根据谱线的形态划分,谱线展宽可分为自然展宽、Doppler 展宽和Stark 展宽。自然展宽由于其他因素产生的谱线变宽要比它大得多,导致在实际实验条件下难以观测;多普勒展宽与多种因素有关,如光源温度、原子量、波长等,其值大约为1~8 pm (1 pm=10?3 nm),而实际光谱仪的分辨率往往大于多普勒展宽(本课题组光谱的分辨率为0.058 nm),因此在实际计算中,其展宽效应往往被忽略。利用Stark 展宽计算电子数密度不会受等离子体是否处于平衡状态的限制,即使非热平衡体系的电子数密度,同样可以测量计算。Stark 展宽由等离子体中的不均匀强电场以及高速运动中的高密度的带电粒子、离子和电子引起,根据相关理论计算,Stark展宽的误差为±5%,因此在未知等离子射流热力学状态之前,采用Stark 展宽计算电子数密度比较合理。理论上说,用于计算电子数密度的谱线可以为任一谱线,然而在所有谱线中,氢光谱巴耳末系的第二条谱线Hβ 线相对较稳定,波长为486.1 nm,可以用于等离子体的测量和计算。在计算电子数密度时,以Hβ 谱线的“半高宽”Δλ1/2 (谱线高度一半处的宽度表示谱线的宽度)进行计算,它与原子结构及等离子体的温度、场强有关,与光谱仪无关。在PS-PVD 工艺条件下,普遍采用Ovsyannikov 和M. F. Zhukov 的经验公式(式(3))[47-48]:
式中,Ne 为电子数密度(cm?3),Δλ1/2 为谱线半高宽(?)对于电子温度的研究,主要采用双谱线法进行分析计算。双谱线法也称强度比较法,它是采用一个原子的两条谱线测量温度。处于激发态的原子向低能级跃迁,将产生具有一定波长的光,并反映在光谱上,两条原子光谱线的辐射强度比满足式(4)[42,48-49]:
式中,Iji 为由j 能级向i 能级跃迁产生的光谱强度,Ikl 为由k 能级向l 能级跃迁产生的光谱强度,λji为由j 能级向i 能级跃迁产生的光谱波长(nm),λkl为由k 能级向l 能级跃迁产生的光谱波长(nm),Aji为由j 能级向i 能级跃迁的迁移率(s?1),Akl 为由k能级向l 能级跃迁的迁移率(s?1),gj 为j 能级的统计权重,gk 为k 能级的统计权重,Ej 为j 能级的激发能(eV),Ek 为k 能级的激发能(eV),kB 为玻尔兹曼常数。这些数据中,光强可在实验中测得,其余均可在NIST 数据库中查得。在PS-PVD 电子温度计算中,通常采用氢光谱巴耳末系的两条谱线Hα 线和Hβ 线进行计算。
图14 PS-PVD 射流不同位置处的电子数密度、电子温度和重粒子温度[50]
本课题组基于自主搭建的PS-PVD 系统和OES光谱诊断系统,对PS-PVD 射流的电子数密度、等离子温度进行了研究,如图13 所示。结果显示,整个射流内电子数密度维持在1014 cm?3 数量级的范围,通过对比粉末粒子的加入与否对电子数密度的影响发现,粉末粒子加入对电子数密度影响较小。而随着等离子射流的不断扩张,电子温度降低。除此之外,德国于利希研究所、法国贝尔福研究所、广东新材料研究所等利用OES 研究了PS-PVD 射流的电子数密度和电子温度。德国于利希的Mauer 等人[50]研究了射流不同位置处的电子数密度、电子温度和重粒子温度,结果如图14 所示。依据这些研究结果,Mauer等进一步计算了等离子气体与涂层材料粒子的相互作用,考虑到离子化程度低以及接近局部热平衡,并且假设等离子体射流中的压力为腔室压力200 Pa,温度由OES 确定,计算结果显示,对于所有研究的参数集合,等离子射流内涂层材料粒子所受阻力较喷嘴中小3~4 个量级,传递的热量也较喷嘴内少4~5 个量级。计算表明等离子气体与涂层材料粒子的相互作用几乎可以忽略不计。Mauer 等认为这意味着涂层材料在等离子射流中的飞行过程中没有显著加热和加速,而另一方面,作者据此来定性说明等离子射流下游的涂层材料粒子的冷却和减速也降低。
4 PS-PVD 射流中材料输运与沉积机理研究
4.1 射流中的材料加热行为与气化机理
OES 虽然从定性的角度反映了射流内材料与涂层结构的关系,然而,射流内材料特性的变化规律、射流特性对材料特性的影响行为及其对涂层结构的调控机制仍然是困扰PS-PVD 研究的难题,而解决这些问题是PS-PVD 沉积理论的基石,是对PS-PVD 技术的基础支撑,更是实现目标结构涂层可控制备的关键科学问题。本课题组基于自主搭建的PS-PVD 系统与OES 诊断系统,针对射流中材料特性的重要作用,开展了基于光谱诊断的材料特性研究,并在此基础上建立了PS-PVD 射流内材料多相态调控方法。
基于自主设计与搭建的PS-PVD 系统与OES 诊断系统,本课题组对PS-PVD 射流特性与沉积单元多相态调控进行了深入的研究,除图13 对等离子射流中心处的特性研究外,还进一步对射流的局部热平衡状态进行了研究,依据局部热平衡的判断条件,计算得到其临界电子数密度为 1014 cm?(3 如 15a),PS-PVD射流内的电子数密度为1015 cm?3,在局部热平衡假设的基础上,进一步对射流温度沿轴向与径向的分布进行研究,建立等离子射流温度沿轴/径分布模型,如图15b 所示[45]。
基于等离子射流电子数密度与等离子温度的分布,建立了凝聚态材料与等离子体热/质交互作用模型(如图16 所示)[48]:
其中,m 为凝聚态材料的剩余质量,Cp 为凝聚态材料的比焓(Cp=87.864 J/(K·mol)),dT 是加热与蒸发过程中凝聚态材料的温度变化,dQconv 是等离子射流对凝聚态材料的传热,dm 是凝聚态材料的蒸发质量(即传质过程),Q0 是凝聚态材料的蒸发潜热。
图15 等离子射流电子数密度、等离子温度沿轴/径分布模型[45]
图16 凝聚态材料与等离子体热/质交互作用模型[48]
根据等离子射流电子数密度与等离子温度的分布结果与凝聚态材料与等离子体热/质交互作用模型,求解出了等离子射流沿轴向方向的热流密度分布及传递给凝聚态材料的热焓随凝聚态材料尺寸的变化规律,如图17 所示。研究发现,凝聚态材料的尺寸越小,传热量越高。这是由于尺寸小的凝聚态材料颗粒比尺寸大的颗粒具有更大的比表面积,小尺寸颗粒比大尺寸颗粒具有更高的传热系数,因此导致等离子气体对小尺寸颗粒的热焓传递大于对大尺寸颗粒的热焓传递。在该研究所使用的参数条件下,从图中可以明显地看出,射流对凝聚态材料的热焓传递足以使尺寸为0.28 μm 的颗粒完全蒸发。进一步地通过不同的凝聚态材料(涂层粉末)尺寸与传输距离对凝聚态材料蒸发行为的影响研究发现,凝聚态材料在等离子射流输运过程中,随着射流不断地对其传热,凝聚态材料不断蒸发,尺寸不断减小。图18 直观地给出了凝聚态材料尺寸随等离子射流轴向距离变化的规律,尺寸小于0.28 μm 的凝聚态材料会在轴向距离450 mm 以内完全蒸发。相反,尺寸大于0.28 μm 的凝聚态材料不能在轴向距离450 mm 以内完全蒸发,可能会在更远的射流距离内才能完全蒸发。因此,通过粉末初始尺寸与沉积距离可以实现凝聚态材料相态转变调控,最终形成通过调控粉末初始尺寸与沉积距离实现涂层结构调控的方法。
图17 热流密度分布及传递给凝聚态材料的热焓随凝聚态材料尺寸的变化规律[48]
图18 初始尺寸与沉积距离对凝聚态材料蒸发行为的影响[48]
4.2 射流中的材料长程跨域输运机理
对于PS-PVD 沉积柱状涂层,其必要条件是在自由等离子射流中有较高的气相涂层材料含量,通过凝聚态材料蒸发行为的控制,可以实现涂层材料在射流内的高效蒸发,而对于凝聚态材料蒸发后形成的气相材料,在等离子射流输运过程中会与等离子气体相互作用,在PS-PVD 射流长1~2 m 的输运距离上,气相材料粒子的状态会受等离子射流性质的影响而发生变化,因此要得到以气相沉积为主的柱状结构涂层,必须对等离子射流中涂层材料气相粒子与等离子气体的相互作用进行研究。为此,本课题组进一步基于OES 诊断表征的等离子射流三维特性,形成了通过评估等离子射流特性约束气相材料容纳量来调控涂层结构的方法。对于射流中输运的气相材料,它受自身饱和蒸气压与射流压力的作用,其热力学过饱和行为由式(6)决定:
式中,S 代表气相材料过饱和度,S=Pp/Pv,Pp是等离子射流中的气相材料的分压,Pv 是气相材料的饱和蒸气压;kB 是玻尔兹曼常数(1.38×10?23 J/K);Ω 是分子的体积。
根据等离子射流电子数密度与等离子温度的分布结果,在计算气相材料分压与饱和蒸气压后,结合超低压条件下气相材料的离解行为,阐明了等离子射流不同轴向位置处的气相材料热力学容纳量,结果如图19 所示。根据图19 的结果,要实现涂层材料在整个等离子射流内时刻以气相的形式存在,气相材料的
图19 等离子射流气相材料容纳量[45]
含量应该小于射流中最小气相材料容纳量位置处的材料量,即材料以气相存在时,整个等离子射流的气相材料含量由容纳气相量最小位置处的气相量(450 mm 处的5.6 g/min)决定,只有这样才能保证在整个射流内材料呈气相状态。
气相材料的容纳量除受自身饱和蒸气压限制外,还受到气相材料在等离子射流内的分压限制。根据道尔顿定律,腔室压力等于气态氧化锆的分压和等离子气体的分压之和:
其中,P 是Ar、H 和气相材料的总压力;PAr、PH 和Pvapor 分别是Ar、H 和气相材料的分压。由式7 可知,气相材料的分压明显低于腔室压力。实际上,当腔室压力即总压P 越高时,相应允许的气相材料的分压也就越高,也就是说当等离子气体组成、送气量以及送粉率一定时,各成分的分压与其初始的摩尔分数有关,改变总压,各分压也会按各自比例相应地发生变化。因此,为了研究实际压力对等离子射流气相材料容纳量的影响规律,可以使用腔室压力而不是气相材料的分压来定性地研究等离子射流各位置应该具有的气相材料容纳量,结果如图20所示。
图20 不同腔室压力下的等离子射流的气相材料容纳量[45]
在图9 中,Mauer 等的研究给出了一个送粉率控制射流中气相材料状态的例子,在以YSZ 为研究对象的实验中发现,当送粉率在1 g/min 以内时,等离子射流内为完全气化的YSZ 粒子,而随着送粉率逐渐增大至1~5 g/min,等离子射流中YSZ 粒子发生由气相→团簇的变化,本部分的研究恰恰在理论层面上揭示了这种现象的本质,即送粉率实际上是通过控制等离子射流的气相材料热力学容纳量,最终决定射流中气相材料相态的转变。此外,等离子射流的气相材料容纳量受腔室压力的影响:腔室压力在低至一定值时,射流气相材料的容量会随腔室压力的降低而减小。这主要是由于腔室压力一定,射流压力在稳定后材料分压组成,总压降低,气相材料分压相应降低。因此,腔室压力成为决定射流中气相材料量除送粉率以外的另一个关键参数。通过送粉率/腔室压力参数集的调控,可以实现射流内气相材料量状态及涂层结构的调控,如要实现全气相沉积的涂层,可以使用较低的送粉率与相对较高的腔室压力,而要使涂层中存在团簇类的沉积单元,可以使用较高的送粉率与相对较低的腔室压力,这种送粉率/腔室压力参数集的联合调控对调控PS-PVD 涂层结构具有重要的理论指导价值。
4.3 材料沉积机理与涂层结构
4.3.1 气相材料沉积的微观视线模型
在热障涂层的应用中,PS-PVD 以其强大的气相沉积能力而受到广泛的关注,目前虽然通过涂层形貌及经典型形核理论对PS-PVD 的沉积机理进行了研究,但是PS-PVD 的气相沉积机理仍然没有得到明确的阐明。为此,本课题组建立了PS-PVD 气相沉积的微观视线沉积模型,如图21 所示[51]。
图21 PS-PVD 气相材料沉积的微观视线模型[51]
由于在沉积之前,气相材料和等离子体气体之间的随机碰撞,导致其将以不同的角度向基体沉积。当气相材料到达并与基体碰撞时存在两种情况:一种情况是气相材料在与基体或涂层碰撞后回弹(图21 中的单元a),另一种是沉积(图21 中的单元b)。对于反弹的气相材料,又会有两种行为:一种是再沉积,另一种是随等离子气体一起远离基体。反弹的气相材料对沉积没有贡献,并且仅影响沉积效率。对于沉积的气相材料,将在合适的基体温度下发生扩散,进而移动到理想的晶格位置,形成涂层。为了只考察材料的微观视线沉积行为对涂层结构的影响,在实际模拟时并没有考虑扩散对涂层结构的影响。
4.3.2 气相材料的微观视线沉积机理与涂层结构
基于上述模型,利用Monte Carlo 方法模拟气相材料的微观视线沉积行为,沉积过程模拟及模拟结果与实际涂层结果进行对比的结果如图22 所示[51]。通过对比模拟与实际的涂层结构可以看到,涂层具有柱状结构,而由于模拟过程没有考虑扩散对涂层结构的影响,因此实际涂层结构要比模拟结果更加致密,也正因如此,模拟结果更加准确地反映了气相材料的微观视线性沉积行为。图a—d 为气相沉积的过程示意图,可以看到,在沉积的初始阶段,基体表面就开始产生波动,由光滑变得粗糙,而进一步沉积,柱状结构开始出现,随着沉积的持续进行,柱状结构不断长大。
图22 沉积过程模拟及实际涂层结构[51]
5 结论与展望
PS-PVD 技术作为未来高性能高温防护涂层和功能涂层制备技术的发展方向,得到了国内外众多机构与学者的关注。西安交通大学自主研发了首台具有真空机器人控制系统的PS-PVD 系统,并自主组建了用于等离子射流与材料特性非接触检测的光学发射光谱(OES)系统,在此基础上开展了深入的等离子射流特性与材料特性研究,建立了PS-PVD 射流中材料输运与沉积机理的研究方法,归纳了调控沉积单元多相态转变的工艺控制参数集。这些硬件平台和表征检测方法的建立,为构建PS-PVD 理论和研制新型高性能热防护涂层提供了坚实的理论基础和必要的条件支撑。
目前,PS-PVD 热障涂层基础研究已经取得显著进展,但尚未能工程应用,未来PS-PVD 技术的重点研究方向主要有:1)更加完整的材料调控与沉积机理;2)可定制化结构涂层制备与调控;3)超高温高隔热、长寿命一体化热障涂层研究;4)复杂形貌、多联体部件均一化涂层沉积;5)环境障涂层;6)大面积功能性薄膜沉积,如透氧薄膜、燃料电池和太阳电池电极薄膜等。
参考文献:
[1]LIG R, WANG L S. Durable TBCs with self-enhanced thermal insulation based on co-design on macro- and mi-crostructure[J]. Applied surface science, 2019, 483: 472- 480.
[2]LIG R, YANG G J. Understanding of degradation-resistant behavior of nanostructured thermal barrier coatings with bimodal structure[J]. Journal of materials science & technology, 2019, 35: 231-238.
[3]LIG R, WANG L S, YANG G J. A novel composite- layered coating enabling self-enhancing thermal barrier performance[J]. Scripta materialia, 2019, 163: 142-147.
[4]PADTURE, NITIN P. Advanced structural ceramics in aerospace propulsion[J]. Nature materials, 2016, 15(8): 804-809.
[5]CHEN L, JIANG Y H, CHONG X Y, et al. Synthesis and thermos-physical properties of RETa3O9 (RE=Ce, Nd, Sm, Eu, Gd, Dy, Er) as promising thermal barrier coatings[J]. Journal of the American Ceramic Society, 2018, 101: 1266-1278.
[6]CHEN L, WU P, SONG P, et al. Potential thermal barrier coating materials: RE3NbO7 (RE=La, Nd, Sm, Eu, Gd, Dy) ceramics[J]. Journal of the American Ceramic Society, 2018, 101: 4503-4508.
[7]CHEN L, SONG P, FENG J. Influence of ZrO2 alloying effect on the thermophysical properties of fluorite-type Eu3TaO7 ceramics[J]. Scripta materialia, 2018, 152: 117- 121.
[8]CHEN L, HU M Y, WU P, et al. Thermal expansion performance and intrinsic lattice thermal conductivity of ferroelastic RETaO4 ceramics[J]. Journal of the American Ceramic Society, 2019, 102(8): 16328.
[9]LIG R, XIE H, YANG G J, et al. A comprehensive sintering mechanism for TBCs-Part I: An overall evolution with two-stage kinetics[J]. Journal of the American Ceramic Society, 2017, 100: 2176-2189.
[10]LIG R, XIE H, YANG G J, et al. A comprehensive sintering mechanism for TBCs-Part II: Multiscale multipoint interconnection-enhanced initial kinetics[J]. Journal of the American Ceramic Society, 2017, 100: 4240-4251.
[11]LI Q L, YUAN X H, XU H, et al. Microstructure and fracture toughness of in-situ nanocomposite coating by thermal spraying of Ti3AlC2/Cu powder[J]. Ceramics international, 2019, 45(10): 13119-13126.
[12]LI Q L, SONG P, XUAN H, et al. Plastic metallic-barrier layer for crack propagation within plasma-sprayed Cu/ ceramic coatings[J]. Surface and coatings technology, 2019, 360: 259-268.
[13]LI Q L, SONG P, LüK, et al. Fracture behaviour of ceramic-metallic glass gradient transition coating[J]. Ceramics international, 2019, 45: 5566-5576.
[14]CHENG B, YANG N, ZHANG Q, et al. Sintering induced the failure behavior of dense vertically crack and lamellar structured TBCs with equivalent thermal insulation performance[J]. Ceramics international, 2017, 43: 15459-15465.
[15]LI G R, CHENG B, YANG G J, et al. Strain-induced stiffness-dependent structural changes and the associated failure mechanism in TBCs[J]. Journal of the European Ceramic Society, 2017, 37: 3609-3621.
[16]CHENG B, ZHANG Y M, YANG N, et al. Sintering- induced delamination of thermal barrier coatings by gradient thermal cyclic test[J]. Journal of the American Ceramic Society, 2017, 100: 1820-1830.
[17]RENTERIA A F, SARUHAN B, SCHULZ U, et al. Effect of morphology on thermal conductivity of EB-PVD PYSZ TBCs[J]. Surface and coatings technology, 2006, 201: 2611-2620.
[18]CHEN S, QU S J, LIANG J, et al. Effects of heat treatment on mechanical properties of ODS nickel-based superalloy sheets prepared by EB-PVD[J]. Rare metals, 2011, 30: 76-80.
[19]VON N K, GINDRAT M. Plasma spray-PVD: A new thermal spray process to deposit out of the vapor phase[J]. Journal of thermal spray technology, 2011, 20: 736-743.
[20]MAUER G, HOSPACH A, VASSEN R. Process develop-ment and coating characteristics of plasma spray-PVD[J]. Surface and coatings technology, 2013, 220: 219-224.
[21]HARDER B J, ZHU D. Plasma spray-physical vapor deposition (PS-PVD) of ceramics for protective coatings[J]. Advanced ceramic coatings and materials for extreme environments, 2011, 32(3): 73-84.
[22]DENG Z Q, LIU M, MAO J, et al. Stage growth of colu-mnar 7YSZ coating prepared by plasma spray-physical vapor deposition[J]. Vacuum, 2017, 145: 39-46.
[23]ZHANG X F, ZHOU K S, LIU M, et al. Mechanisms governing the thermal shock and tensile fracture of PS-PVD 7YSZ TBC[J]. Ceramics international, 2017, 44(4): 3973- 3980.
[24]ZHANG X F, ZHOU K S, DENG C M, et al. Gas- deposition mechanisms of 7YSZ coating based on plasma spray-physical vapor deposition[J]. Journal of the European Ceramic Society, 2016, 36: 697-703.
[25]GAO L H, WEI L L, GUO H B, et al. Deposition mec-hanisms of yttria-stabilized zirconia coatings during plasma spray physical vapor deposition[J]. Ceramics international, 2016, 42: 5530-5536.
[26]ZHANG B P, WEI L L, GUO H B, et al. Microstructures and deposition mechanisms of quasi-columnar structured yttria-stabilized zirconia coatings by plasma spray physical vapor deposition[J]. Ceramics international, 2017, 43: 12920- 12929.
[27]YANG X, WEI L, LI J, et al. Microstructural evolution of plasma spray physical vapor deposited thermal barrier coatings at 1150 ℃ studied by impedance spectroscopy[J]. Ceramics international, 2018, 44(9): 10797-10805.
[28]CHEN Q Y, LI C X, WEI T, et al. Controlling grain size in columnar YSZ coating formation by droplet filtering assisted PS-PVD processing[J]. RSC advance, 2015, 5: 102126-102133.
[29]CHEN Q Y, LI C X, ZHAO J Z, et al. Microstructure of YSZ coatings deposited by PS-PVD using 45 kW shrou-ded plasma torch[J]. Advanced manufacturing processes, 2015, 31: 1183-1191.
[30]VON N K, GINDRAT M, REFKE A. Vapor phase deposition using plasma spray-PVD (TM)[J]. Journal of thermal spray technology, 2010(19): 502-509.
[31]VAUTHERIN B, PLANCHE M P, BOLOT R, et al. Vapors and droplets mixture deposition of metallic coatings by very low pressure plasma spraying[J]. Journal of thermal spray technology, 2014, 23: 596-608.
[32]LIU M J, ZHANG K J, ZHANG Q, et al. Thermodynamic conditions for cluster formation in supersaturated boundary layer during plasma spray-physical vapor deposition[J]. Applied surface science, 2019, 471: 950-959.
[33]DENG Z Q, ZHANG X F, ZHOU K S, et al. 7YSZ coating prepared by PS-PVD based on heterogeneous nucleation[J]. Chinese journal of aeronautics, 2018, 31: 820-825.
[34]高丽华, 于月光, 贾芳, 等. 等离子物理气相沉积热障涂层研究进展[J]. 热喷涂技术, 2017, 9(2): 1-8.GAO Li-hua, YU Yue-guang, JIA Fang, et al. Progress in plasma spray-physical vapor deposition thermal barrier coatings[J]. Thermal spray technology, 2017, 9(2): 1-8.
[35]石佳, 魏亮亮, 张宝鹏, 等. 等离子物理气相沉积热障涂层研究进展[J], 航空材料学报, 2018, 38(2): 1-9.SHI Jia, WEI Liang-liang, ZHANG Bao-peng, et al. Re-search process in plasma spray physical vapor deposited thermal barrier coatings[J]. Journal of aeronautical ma-terials, 2018, 38(2): 1-9.
[36]GINDRAT M, REFKE A, SCHMID R. Process chara-cterization of LPPS thin film processes with optical diagnostics[C]// Proceedings of the Seventh ITSC. Beijing: China surface engineering association, 2007.
[37]张楠楠. 超低压等离子喷涂中的等离子焰流检测及涂层制备[D]. 大连: 大连理工大学, 2012.ZHANG Nan-nan, Diagnostics of plasma jet and coating deposited by very low pressure plasma spray[D]. Dalian: Dalian Uiversity of Technology, 2012.
[38]GAO Y, YANG D M, GAO J. Characteristics of a plasma torch designed for very low pressure plasma spraying[J]. Journal of thermal spray technology, 2012, 21: 740-744.
[39]REFKE A, BARBEZAT G, DORIER J L, et al. Chara-cterization of LPPS processes under various spray condi-tions for potential applications[C]// International thermal spray conference. USA: [s. n], 2003.
[40]BLAIS A, JODOIN B, DORIER J L, et al. Inclusion of aerodynamic non-equilibrium effects in supersonic plasma jet enthalpy probe measurements[J]. Journal of thermal spray technology, 2015, 14: 342-353.
[41]ZHANG N N, SUN F, ZHU L, et al. Measurement of specific enthalpy under very low pressure plasma spray condition[J]. Journal of thermal spray technology, 2012, 21: 489-495.
[42]ZHANG N N, SUN F, ZHU L, et al. Characteristics of Cu film deposited using VLPPS[J]. Journal of thermal spray technology, 2010, 20: 351-357.
[43]MAUER G, VAßEN R. Plasma spray-PVD: Plasma cha-racteristics and impact on coating properties[J]. Journal of physics: Conference series, 2012, 406: 012005.
[44]GORAL M, KOTOWSKI S, NOWOTNIK A, et al. PS-PVD deposition of thermal barrier coatings[J]. Surface and coatings technology, 2013, 237: 51-55.
[45]LIU M J, ZHANG M, ZHANG Q, et al. Gaseous material capacity of open plasma jet in plasma spray-physical vapor deposition process[J]. Applied surface science, 2018, 428: 877-884.
[46]CHEN Q Y, PENG X Z, YANG G J, et al. Characteriza-tion of plasma jet in plasma spray-physical vapor deposi-tion of YSZ using A <80 kW shrouded torch based on optical emission spectroscopy[J]. Journal of thermal spray technology, 2015, 24: 1-8.
[47]ZHANG N N, SUN F, ZHU L, et al. Electron temperature and density of the plasma measured by optical emission spectroscopy in VLPPS conditions[J]. Journal of thermal spray technology, 2011, 20: 1321-1327.
[48]LIU M J, ZHANG M, ZHANG Q, et al. Evaporation of droplets in plasma spray-physical vapor deposition based on energy compensation between self-cooling and plasma heat transfer[J]. Journal of thermal spray technology, 2017, 26: 1641-1650.
[49]CUI J H, XU Z F, ZHANG J L, et al. Online diagnosis of electron excitation temperature in CH4+H2 discharge plasma at atmospheric pressure by optical emission spectra[J]. Science in China, 2008, 51: 1892-1896.
[50]MAUER G, JARLIGO M O, REZANKA S, et al. Novel opportunities for thermal spray by PS-PVD[J]. Surface and coatings technology, 2015, 268: 52-57.
[51]LIU M J, ZHANG M, ZHANG X F, et al. Transport and deposition behaviors of vapor coating materials in plasma spray-physical vapor deposition[J]. Applied surface science, 2019, 486: 80-92.
免责声明:本网站所转载的文字、图片与视频资料版权归原创作者所有,如果涉及侵权,请第一时间联系本网删除。
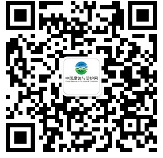
官方微信
《腐蚀与防护网电子期刊》征订启事
- 投稿联系:编辑部
- 电话:010-62316606-806
- 邮箱:fsfhzy666@163.com
- 腐蚀与防护网官方QQ群:140808414