摘要: 基于对钛合金应用及研究报道的梳理,综述了钛合金深海应力腐蚀产生原因及机理,探讨了静水压力、溶解氧含量、pH值和温度等深海环境因素对应力腐蚀开裂的影响,以期为今后钛合金深海应力腐蚀开裂等局部腐蚀行为及机制的深入研究提供参考,为优化钛合金组织性能,建立深海先进钛合金材料体系提供支撑。
关键词: 钛合金 ; 深海 ; 环境因素 ; 应力腐蚀开裂 ; 耐蚀性
海洋蕴藏着丰富的资源,近年来,海洋环境得到了广泛的重视[1]。我国在“十三五”规划纲要中指出,要加强深海、深地、深空和深蓝领域的高技术部署,我国要建设成海洋强国[2]。深海不仅是石油、天然气和矿产资源勘探、开发的阵地,也是各国海洋科学探索和先进深海技术比拼的主战场,许多国家已加快了深海装备的研制和部署[3-5]。然而深海的环境复杂严酷,深海除了具有较高的静水压力外,温度、盐度、pH、溶解氧等因素也与浅海环境差异巨大,这就为深海装备带来了未知的腐蚀失效风险。同时,苛刻的深海环境也为深海装备的应用以及材料的深海腐蚀研究带来了挑战。
比强度高、密度较小的钛合金与不锈钢、铝合金等耐蚀材料相比,拥有更好的耐点蚀、缝隙腐蚀、晶间腐蚀和耐均匀腐蚀性能。而且在高速流动的海水中,其耐腐蚀性能依旧保持良好。钛合金还是唯一在海水和空气中的疲劳极限几乎无显著差别的高强度材料。所以钛合金被称为海洋金属[6,7]。虽然钛合金导热性、耐磨性、焊接性欠佳,存在热加工吸氢等问题,但其优异的综合性能仍使它成为重要的海洋材料,在深海装备上的应用与日俱增,并且逐渐由零部件向关键结构方向发展,对钛合金深海腐蚀行为的研究和耐蚀性评价已成为研究热点。
尽管钛合金在表层海水中表现出十分优异的耐蚀性能,但随其服役水深的不断增加,受深海低温、低氧、高压的影响,钛合金钝化性能降低,这将增加材料发生局部腐蚀,特别是应力腐蚀开裂的风险。Pang和Blackwood[8]研究表明,TA2和TC4在低氧条件下会表现出一定的缝隙腐蚀倾向。杨小佳等[9]通过电化学方法和U型弯实验在模拟深海环境下对TA2的电化学行为以及应力腐蚀行为进行了研究,结果表明,静水压力对TA2的阳极溶解及阴极析氢反应都会产生促进作用。另一方面,钛合金合金化后也会引起微观组织结构变化。Pilchak等[10]通过研究Ti-8Al-1Mo-1V合金表明,晶体学取向的刻面是通过合金开裂而产生的。董月成等[11]研究了TC4 ELI钛合金在海洋环境下的服役性能,结果表明组织结构对钛合金的服役性能有着重要的影响。此外,焊接、加工等后处理过程带来的组织缺陷和内应力,及其与腐蚀电化学的协同作用,也是引起钛合金深海应力腐蚀的重要因素。
随着钛合金应用广度和深度的不断增加,对钛合金深海环境主要服役性能的认识愈加紧迫。因此,探索装备用钛合金的深海环境效应,揭示钛合金深海应力腐蚀规律和机制,是当前亟需解决的重要课题之一。本文针对钛合金在深海应用中可能存在的应力腐蚀问题进行了评述,并就深海环境因素的影响进行了探讨。
1 钛合金的分类与应用
1.1 钛合金的分类
钛合金主要分为α型、α+β型和β型。α钛合金中的TA1、TA2、TA3为工业纯钛,TA7为典型的α型钛合金。α型钛合金的优点为组织比较稳定,有良好的焊接性能,并且热强性也较好。它的缺点是室温下塑性较差,容易被压裂,但在加热时塑性会有一定的改善。α型钛合金一般用于500 ℃以下长期工作的各种构件以及有耐蚀性要求的零件等。β钛合金常用的有TB1和TB2,具有强度高、冷加工性能好、塑性好等优点。但也存在焊接性能不够稳定,容易吸气等问题。β钛合金主要用于重载旋转零件,如压气机叶片、轴、轮盘等。相比α型,α+β钛合金耐热性及焊接性能较差,而室温强度和其他性能则会比α型强。α+β钛合金中用量最大的是TC4 (Ti-6Al-4V)。这种钛合金拥有较高的热强度、热塑性,适合热压锻造,同时低温韧性与综合力学性能也较好。但是在较高温度下,组织稳定性比退火后的弱,所以通常情况下不用于热处理强化,一般以退火态使用。α+β钛合金主要用于制造导弹及飞机上有高温强度要求的发动机零件、压气机盘、叶片等结构零件,此外,潜艇耐压壳体等要求高强度的构件,以及火箭、导弹和液氢的燃料箱也用α+β钛合金。
1.2 钛合金的应用
1.2.1 在舰艇装备上的应用
舰船是最重要的海洋装备之一,长期浸泡在海水中的船体部件很容易受到海水腐蚀,所以对舰船材料的使用标准要求也比较高,需要具备优良的强度、韧性以及耐海洋环境腐蚀的能力。在实际的建造过程中,材料还需要有极好的加工性与可焊接性。钛合金能够充分满足船舶材料的要求,其发展前景十分可观[12]。钛材的使用可以减小船体质量,解决腐蚀问题,确保抗冲击性和抗疲劳性,从而延长舰船使用寿命。用钛合金代替不锈钢或铜镍合金,用来制造舰船动力系统的热交换器、冷凝器、反应堆壳体、推进轴、螺旋桨等,可大大提高动力系统的使用寿命和安全可靠性[13]。1985年,日本建造了全钛游艇,成为世界第一艘全钛船舶。
1.2.2 在水下装备上的应用
钛合金是建造大深度潜艇及深潜器耐压壳体的理想材料。法国的SM97号使用TC4 ELI钛合金,日本的“深海2000”号、美国的Aivin号和Sea-Cliff号深潜器的壳体都采用了钛合金。近年,Breddermann等[14]借助增材制造技术,采用钛合金制造了深海航行器耐压外壳。2016年,我国自主设计建造的载人潜水器“蛟龙”号[15]成功进行了7000 m级深潜试验;2017年,我国完成了首台国产化率达95%的载人深潜器“深海勇士”号4500 m下潜试验;2020年,我国“奋斗者”号载人深潜器在马里亚纳海沟成功坐底,完成万米海试,标志着我国拥有了全海深载人深潜能力。除这些深海装备,还有“海斗”号等无人潜水器都是采用钛合金耐压结构。钛合金在海水管路中的应用也成为一个重要方向。俄罗斯是世界上最早在船舶制造业中大规模使用钛合金的国家,并且几乎所有潜艇都采用了钛合金管道。2003年,我国在某型号潜艇的海水冷却系统、消防系统和生活海水系统上使用钛合金管材,这也是我国首次在海水管路系统中使用钛合金[16,17]。
1.2.3 在海洋油气开采装备上的应用
上世纪70年代,美国将钛合金运用在近海石油平台支柱上。上世纪90年代初,Conoco公司首次将钛合金应用于平台的提升装置,自此以后钛合金提升管开始大量应用在石油、天然气开采行业[18]。另外,为了降低成本和减轻重量,海底开采石油也已经运用钛合金制造高压采油管,海上平台的热交换器也已使用钛合金[19]。目前,钛合金在海洋油气开采装备中主要应用于换热器、提升装置、结构件等。
目前,钛合金在海洋工程和装备上的应用还比较少,服役期还较短,腐蚀问题还没有完全显现出来。随着钛合金在深海工程关键装备结构及部件上应用的不断增多和服役时间的延长,可能进入一个装备材料腐蚀问题的爆发期,钛合金可能面临的深海局部腐蚀破坏,特别是应力腐蚀问题愈发不容忽视。因此,适时开展钛合金深海应力腐蚀开裂行为及机理的预先探索,明确应力腐蚀的发生原因及其与服役环境的关系,对于提高钛合金深海装备的抗腐蚀失效风险能力至关重要。
2 钛合金深海应力腐蚀机理
2.1 残余应力
钛合金有40%的事故与锻造、加工、焊接、热处理等过程中引入的残余应力所造成的应力腐蚀开裂有关。残余应力是指当外力的作用消失后,在材料内部存在并且可以保持平衡状态的内应力[20],可将之分为两类,宏观残余应力和微观残余应力。研究残余应力作用下的电化学腐蚀行为对于研究材料的失效行为具有很重要的意义。点蚀和应力腐蚀是残余应力作用下两种主要的腐蚀形式[21]。王军等[22]指出,只有在较低的应力水平、常规的介质环境条件下,耐蚀材料突出的抗Cl-应力腐蚀开裂性能才能充分显现。上述条件一旦被突破,特别是高应力下 (如厚件大面积堆焊所产生的大范围、高峰值残余应力),即使像2507这样的超级双相不锈钢,其抗应力腐蚀开裂的能力也将严重降低。焊接导致的残余拉应力可使受拉区域表面活化能减小,从而增加了材料表面活性,导致耐蚀性降低[23]。由于焊接残余应力的堆积,造成材料耐蚀性的降低,诱发裂纹萌生和扩展的研究报道屡见不鲜[24]。朱江[25]研究了不同深冷时间对TC4钛合金电子束焊接接头的性能影响,通过残余应力测试,认为了残余应力与焊接接头应力腐蚀之间的关系。随着深冷时间的增加,残余应力减小,接头的耐蚀性能增强。此外,服役环境下产生的外应力或由于腐蚀产物体积效应而造成的不均匀应力等,都是产生应力的来源。应力水平越高,出现应力腐蚀裂纹的时间越短。
2.2 表面组织结构
在海洋环境下,钛合金会表面生成的氧化膜能减缓其自身的腐蚀[26],然而钛合金在高浓度氯化物、低氧环境下,如点蚀、缝隙、裂纹等闭塞区,这层氧化膜会遭到破坏,同时产生可吸附氢,导致应力腐蚀开裂[27]。钛合金表面状态和组织结构对应力腐蚀发生的几率和速率有较大影响。钛合金光滑试样在3.5% (质量分数) NaCl溶液中或海水中不发生应力腐蚀开裂,而一旦试样上有了裂纹,应力腐蚀很快就发生。α相对应力腐蚀开裂敏感,β相不敏感,因此,β相含量高的两相钛合金具有较高的应力腐蚀抗力[28]。Pustode等[29]研究表明,裂纹最初形成于α相与β相界面,主要是穿过初生α晶粒和沿转变β组织中的α/β界面生长 (图1)。当钛合金用于深海承压结构时,由于承压结构形式复杂,焊接不可避免,然而焊接过程会通过改变钛合金焊接接头组织结构而显著影响材料耐蚀性,应格外关注。对于α或近α钛合金,在焊缝中均保留α或α'马氏体组织,其形态取决于β向α或α'转变的冷却速度:在高的冷却速度下,形成针状α或α'相;在较低的冷却速度下,形成宽而长的片状相[30]。针状晶粒带来的表面应力,以及晶界杂质偏析引起的钝化膜不均匀,仍然会造成晶界处钝化膜被优先溶解,形成多孔层[31]。片层结构产生的电偶作用会加速腐蚀。柱状晶表现出强烈的取向性,平行生长的晶粒界面上,以及两个生长方向垂直的界面碰撞都会发生溶质偏析。溶质偏析导致焊缝的化学性质不均匀,使其腐蚀电位较母材区更负[32]。在焊接表面应力和电偶腐蚀效应共同作用下,焊缝在海水中发生阳极溶解,产生氢吸附,导致裂纹的萌生,同时氢扩散诱导α'相界及α'相内发生位错塞积,进而使裂纹在更低的应力水平下发生扩展[33]。
图1 IMI 834钛合金应力腐蚀开裂形貌[29]
2.3 合金元素
合金元素也是影响钛合金应力腐蚀敏感性的关键因素。当合金元素形成氧化物时,这些氧化物将以分散的团簇形式嵌入钛基体中。若合金元素均匀地分布在每个相中,则氧化物团也会均匀地分布在基体中,最终会产生稳定的钝化膜。可见,造成合金元素不均匀分布的处理方式,例如焊接后的焊缝区和热影响区,都不利于稳定钝化膜的形成。例如,Ti-Al-V钛合金,V的氧化物可溶于水溶液中,且Cl-会促进其溶解。钝化膜中空穴的扩散和形成受到V的氧化物的溶解的影响。因此,合金元素V不能改善钝化膜耐蚀性,它在各相中的不均匀分布会导致腐蚀敏感区形成,合金的耐蚀性也会随之降低。由此可见,造成钛合金耐蚀性变化的根本原因是合金元素在各相中的分布及其氧化物的形成程度[34]。特定合金元素的适量添加,可以改善钛合金的应力腐蚀抗力。研究表明,Mo可以提高Ti-Al-Sn-Zr-Nb-Mo-W-Si系高温钛合金在700 ℃下的抗拉强度,适量添加Nb和W可以提高合金的屈服强度,同时减轻其应力腐蚀敏感性[35]。Nb的钝化膜主要成分为Nb2O5,较TiO2可在更大的电势范围内表现为介电行为,能够显著提高钛合金钝化膜的腐蚀电位,降低其扩散系数[36]。微量铂族金属 (如Pd、Ru) 添加至TC4钛合金中可起到阴极改性的作用,提高腐蚀电位,并通过使TiO2钝化膜增厚的方式阻碍腐蚀的进行[37]。Mn是一种强β相稳定元素,随Mn含量的增加,马氏体转变起始温度 (Ms) 升高,β相稳定性提高,抑制应力诱导马氏体转变及晶界针状α''的析出,从而提高了钛合金的抗应力腐蚀开裂性能[38]。此外,O含量低于0.13%时,钛合金的应力腐蚀敏感性大大降低。
2.4 阳极溶解与氢致开裂
高强材料的应力腐蚀开裂可分为阳极溶解型和氢致开裂型两类。阳极溶解机理认为,应力腐蚀裂纹的形核和扩展受到阳极的持续溶解能力的影响[39]。但时,关于阳极金属如何溶解以及应力的影响,存在着不同的看法。一些认为应力作用下的塑性变形会导致局部钝化膜破裂,暴露的新鲜金属会瞬间溶解,然后再次钝化,在应力作用下钝化膜再次破裂,该过程往复,最终导致应力腐蚀裂纹的形核或者扩展。还有一部分认为,选择性溶解产生点蚀,点蚀诱发裂纹形核。裂纹的扩展可以视为一种溶解导致的氧化物形成和随后再重组的腐蚀过程[40]。在反应历程上表现为,Ti的阳极溶解,H的析出和Ti的氢化物的形成,其反应式为:
应力腐蚀裂纹尖端基体金属主要发生阳极溶解反应。裂尖阳极溶解使氢离子浓度增加,为保持电中性,裂纹外的Cl-迁入裂尖,进一步促进裂尖金属的溶解和溶液的酸化,抑制钝化膜的再生[41]。并且随着应变量的增大,应力腐蚀敏感性增加,裂纹尖端会发生位错堆积,促进裂纹扩展[42]。Yang等[43]认为外加载荷 (应力) 增加了裂纹尖端的腐蚀速率,加速了裂纹扩展,但是裂纹尖端的腐蚀产物会沉积,沉积也会在一定情况下减缓腐蚀,然而,进一步增大应力仍然会引起局部阴阳极分化,加速裂纹扩展。Chang等[44]对含有中心裂纹的密排六方 (HCP) 钛单晶在I型加载条件下的裂纹尖端进行了原子尺度模拟,结果表明Ti本质上是一种延性金属,因在裂纹尖端通常可见塑性变形,裂尖塑性变形归因于基面滑移或柱面滑移的激活。通过比较不同条件下裂纹尖端扩展增量发现,脆性模式下裂纹扩展最快,其次是孪晶主导的裂纹扩展,位错滑移主导的裂纹扩展速率最低。由此可见,任何不利于维持钛合金塑性的因素对其抗应力腐蚀开裂性能都是有害的。其中,最重要的因素之一就是氢。
黄显亚等[45]用微电极法和pH试纸法直接测定了Ti-5Al-2.5Sn和Ti-5Al-4V在近中性3.5%NaCl水溶液中应力腐蚀裂纹顶端溶液的pH值,认为裂尖pH值至少达到1.7~2.1,或者可能更低,具备着析氢反应的条件。应力腐蚀形核过程主要是选择性阳极溶解,而一旦Ti离子局部水解使裂纹尖端溶液pH降到足够低,以及浓聚的Cl-使裂尖金属电位降到足够低,使大量氢生成并进入裂纹前端区域,应力腐蚀开裂过程则转为以氢脆机制为主的过程。
氢致开裂理论认为,腐蚀过程中产生H,H在拉应力作用下扩展到裂纹尖端从而导致氢脆[46]。H的扩散聚集及氢化物的形成对钛合金的应力腐蚀具有重要作用。一方面,H在位错处的环境敏感镶嵌能较低,易于在位错处聚积,形成H原子气团。位错对H原子气团的“钉扎”作用使钛合金局部硬化,导致位错运动受阻,并且会形成微裂纹。刘贵立等[47]通过递归法模拟并揭示了钛合金的应力腐蚀机理,认为H在位错处聚集的能量要低于α相内所聚集的能量,所以最终在位错处氢会偏聚,从而形成Cottrell气团,而位错的运动又会受到Cottrell气团与位错的交互作用的影响,引起位错塞积,阻碍塑性变形,最终导致微裂纹形核。裂纹尖端Fermi能级高于裂纹其他区域,电子从裂纹尖端流向裂纹其他区域造成电位差,在电解质作用下裂纹尖端阳极溶解腐蚀。拉应力与裂纹处的氢气压使裂纹解理或沿晶延伸,促进应力腐蚀的发展。也有研究认为,氢首先促进局部塑性变形,并通过位错的滑移形成解理裂纹核心,然后在裂纹内部H会聚集形成氢气,产生巨大的氢气气压,从而导致内外应力共同作用下的裂纹快速扩展[48]。另一方面,在应力腐蚀过程中,H很容易被Ti吸收,产生不同类型的氢化物。氢化物的生成会在其附近产生内应力或由于自身脆性引发开裂,并且片状氢化物更易于致脆[49]。Madina和Azkarate[50]通过阴极极化充氢发现了Ti Gr-12表面氢化物层的形成及其相关的脆性裂纹。燕辉等[51]研究了氢化物对TA10腐蚀的影响,结果表明氢化物的增多加剧了TA10钛合金的腐蚀。郭敏等[52]研究表明,TA2在海水中的氢脆属于氢化物型氢脆,并且氢化物的形成会使TA2的钝化膜稳定性下降,容易发生腐蚀。罗强等[53]研究证实了氢会在TA16合金中形成氢化物TiHx,随着TA16钛合金含氢量的增加,其氢脆敏感性随之增大。王得明等[54]通过超高压透射电镜原位观察发现,即使在3.57~4.46 mg/m3含氢量时,也有可能由于氢化物的积聚而发生脆性开裂。当氢含量低于0.134 mg/m3时,可以防止发生氢脆,但是可逆氢脆仍然很难避免[55]。氢在α相中的溶解度和扩散率低于β相,因此钛合金由氢化物所致的氢脆敏感性因β相含量的不同而存在差异,但其作用方式仍需做进一步的研究[48,56]。Qiao等[57]研究表明,Ti-4Al-2V-1Mo-1Fe合金充氢后,α相中会形成γ-TiH和δ-TiH2氢化物,促使α相发生选择性溶解,由此破坏了其钝化能力,最终导致氢致裂纹的萌生与扩展。詹思远等[58]通过有限元模拟研究了在应力诱导作用下,环境压强对于深海环境中的带裂纹钛合金裂尖处的氢浓度分布情况的影响,结果表明氢在裂尖处聚集,压强越大情况越严重,更容易导致裂纹扩展。
此外,深海微生物也可能是引起钛合金氢损伤的重要因素。其中研究较多的是硫酸盐还原菌 (SRB),SRB是一类广泛存在于自然环境中可以利用硫酸盐类物质作为呼吸代谢电子受体的厌氧类微生物,是造成金属腐蚀破坏和设备故障的主要原因之一[59]。SRB的代谢产物中产生浓度较大的H2S、HS-和S2-等,它们既促进H的生成,降低H的复合速率,又促进H渗透扩散至高应力区,诱发裂纹萌生,加速裂纹扩展。此时SRB有类似氢化物的作用。与无S钝化膜相比,含S钝化膜更容易被Cl-穿透而加速腐蚀,因此SRB新陈代谢产生的硫化物为Cl-穿透提供了“通道”,进而为应力腐蚀开裂提供了诱发点。点蚀坑底部往往出现次生点蚀坑,表明SRB诱发了二次点蚀,二次点蚀可使宽浅坑的应力集中程度增大,从而导致“二次开裂”[60]。
应力腐蚀是钛合金在深海中所面对的最主要的风险之一,了解应力腐蚀的机理以及造成应力腐蚀的原因不仅可以减小应力腐蚀对于钛合金的影响,并且对钛合金在深海中的应用研究有着很重要的意义。
3 深海环境因素对钛合金应力腐蚀的影响
在深海环境下深海静水压力、溶解氧含量、pH、温度等都会影响金属材料的应力腐蚀行为[61,62]。深海与浅海环境的显著不同,也导致金属材料腐蚀规律的差异。研究表明[63,64],随着海水深度的增加,活性金属的腐蚀减轻,钝性金属的活化和钝化性质转变,金属的均匀腐蚀速率降低,但是点蚀、应力腐蚀开裂等局部腐蚀形式更加显著。
3.1 静水压力
高静水压力是深海与表层海水的最大区别。随海水深度的增加,静水压力也随之增大,并且静水压力是制约材料腐蚀机制的重要因素,也是一直以来,深海环境因素与材料应力腐蚀相关性研究的热点。在实际深海环境试验中,耐蚀合金 (如铁素体不锈钢) 的点蚀深度与静水压力间表现出极大的关联,随静水压力的升高,点蚀深度增加[65]。Yang等[66,67]认为静水压力会使材料的耐点蚀性能降低,并且加速点蚀萌生。Beccaria等[68,69]认为造成上述结果的原因是,在较高海水压力下,Cl-的活性增加,更容易渗透进入钝化膜,使钝化膜氧化物和氢氧化物转变为可溶性的氯氧化物,从而加速点蚀的发生。刘杰等[61]和孙海静等[70]证实了高静水压力对电极阴极过程影响不大,但能够提高Cl-活性,加快阳极溶解速度。Zhang等[64]基于统计学方法和随机理论研究了静水压力对材料点蚀的影响,结果表明,静水压力的增加会提高材料的亚稳态点蚀发生的频率,并且增大向稳态点蚀发展的倾向,但是却未改变点蚀的产生机制。除了对钝化膜性质及点蚀的影响外,静水压力还会通过影响腐蚀产物的性质影响材料的腐蚀速率和腐蚀形态。如高静水压力会使铝合金腐蚀产物膜更致密,从而导致更好的保护性。表面腐蚀产物的界面性质会因交变压力的作用而改变,从而加剧材料的腐蚀[71]。Liu等[72]采用慢应变速率拉伸试验研究了2 ℃下3.5%NaCl溶液中,静水压力对TC4应力腐蚀开裂的影响。在0.1和20 MPa静水压力条件下,应力腐蚀开裂的敏感性分别为3.4%和11.8%,表明静水压力越高,应力腐蚀开裂敏感性也越高。在20 MPa下,去除钝化膜的U型弯曲试样的开路电位 (OCP) 比在0.1 MPa下更负,且初始电位回复更加缓慢,表明在较高的静水压力下,TC4的钝化能力变差。因此,静水压力通过加速阳极溶解、破坏钝化膜、促进点蚀萌生、改变腐蚀产物的保护作用等方式影响材料的耐蚀性,并且随着静水压力的增大,钛合金的耐腐蚀性会减小。
3.2 溶解氧含量
溶解氧含量是影响金属深海耐蚀性的又一关键因素。随着海水深度的增加,溶解氧含量降低,在经历700~800 m深度下的最低含氧区后,溶解氧含量小幅上升并趋于稳定。在溶解氧含量较高的浅层海水中,腐蚀过程的阴极反应倾向于吸氧反应,而在溶解氧含量较低的深海中,吸氧反应将受到抑制,使得腐蚀速率降低。美国海军实验室研究[73]表明,对于发生均匀腐蚀的材料,其深海腐蚀速率与溶解氧含量成线性关系。对于依靠自身钝化而耐蚀的材料来说,溶解氧含量的作用更多地体现在对钝化膜耐蚀性的影响上。Berthaud等[74]研究了溶解氧含量对α钛合金钝化行为的影响,结果表明,溶解氧含量越大,越容易形成钝化膜。龚敏等[75]和王晶等[76]研究表明,在氧含量高的卤盐溶液中,不锈钢具有更高的点蚀电位,这说明高氧含量使不锈钢表面钝化膜更加致密,自愈能力更强,因而能够对点蚀形核起到有效的抑制作用。彭文才[77]在模拟不同深度溶解氧含量的条件下,对5083铝合金进行的电化学测试表明,随着溶解氧含量的降低,自腐蚀电位变负,钝化膜稳定性也随之降低。Ti-6Al-4V和Ti-6Al-7Nb钛合金具有类似的现象[78],如图2所示,在无氧条件下,腐蚀电位比在开放的有氧环境下低0.2 V。钛合金上的钝化膜主要由Ti的氧化物组成,溶解氧含量的降低造成Ti氧化不完全,大量低价态Ti(II) 和Ti(III) 在致密的TiO2膜层中掺杂,导致钝化膜点缺陷密度增加,最终形成疏松多孔层。研究表明,Ti-Al-Nb-Zr-Mo钛合金在深海中的钝化能力较在表层海水中降低1个数量级[79]。所以,溶解氧对于维持保护性钝化膜的生长是必不可少的。但是,钛合金深海耐蚀性的降低并不是必然会引起钛合金的严重腐蚀。经2 a的深海暴露试验表明,TC4的平均腐蚀速率仅为约0.1 μm/a。由此推测,钛合金在深海环境中应力腐蚀裂纹的萌生将十分缓慢。但在特定条件下,仍有可能表现出应力腐蚀敏感性。例如当钛合金处于临界应变时,裂纹开始慢速扩展,扩展速率受应变速率控制;达到临界晶界氢含量时 (深海低氧条件导致析氢反应倾向增大,加之微裂纹内氢聚集),裂纹开始快速扩展,扩展速率受氢的扩散控制[80]。溶解氧含量的降低和氢的扩散累积使钛合金由韧性断裂转变为解理脆性断裂[39]。罗强等[81]研究了TA16和TA17钛合金在高温高压水中的应力腐蚀行为,结果表明,随着溶解氧含量的增加,TA16和TA17钛合金的应力腐蚀敏感指数增大。对于在深海热液区使用的钛合金来说,这十分值得注意。
图2 纯Ti、Ti-6Al-4V和Ti-6Al-7Nb钛合金在开放环境下和在无氧环境下的腐蚀电位[78]
3.3 pH
海水中的pH一般在7.7~8.3,深海有机物和生物活动都会影响海水的pH。浅层海水由于与空气进行对流以及植物的光合作用,通常pH大于8,而随着深度增加,pH先下降后升高,最终达到一个稳定值。Wataha等[82]指出,当材料服役环境pH降低时,环境中的H+增多,伴随着更多的金属离子溶解出来,金属的腐蚀速率也将明显的加快。当pH小于4时,Ti的钝化膜开始溶解,同时产生TiHx腐蚀产物。在含Cl-的溶液中,这种表面溶解作用随pH减小而更趋于均匀化,表现为活性面积增加,局部蚀坑内外腐蚀电池效应减弱[83]。高浓度的酸性环境能够显著增加钛合金的应力腐蚀敏感性。即使是在腐蚀性极弱的无水乙醇中,随着阳极过程中大量乙酸的产生,溶液pH急剧减小,TC4仍能发生强烈的阳极溶解,同时应力腐蚀开裂显著加快,如图3所示,试样断口截面上可见穿越氧化物膜层的裂纹[84]。Zhang等[85]研究表明,随着pH的增加,TC4的耐蚀性逐渐增强。而在pH大于12的H2O2溶液中,Ti反而具有较高的应力腐蚀倾向。总之,任何削弱钛合金钝态的因素 (如升高温度或黏度、合金化、引入Cl-或醇、降低pH) 都将增加应力腐蚀开裂敏感性;那些有助于钛合金钝化的因素 (如增加氧化膜厚度、高pH、引入磷酸根离子) 都将有利于抑制应力腐蚀开裂[86]。与钛合金深海应力腐蚀裂纹扩展直接相关的是裂尖区溶液环境。通过微电极法测量了模拟深海环境中裂尖区的溶液特性,初步探明了裂尖区溶液Cl-浓聚和酸化现象。深海环境因素对裂尖溶液Cl-浓度和pH的影响程度不同:溶解氧含量对pH的影响最大,温度对Cl-浓度的影响最大;深海低温、低氧和高压条件对裂尖区溶液Cl-浓聚和酸化存在协同作用,推测这与深海环境对裂尖金属电化学反应动力学规律的影响有关,还需进一步研究。
图3 TC4钛合金在无水乙醇中的应力腐蚀开裂断口截面形貌[84]
3.4 温度
温度对钛合金应力腐蚀开裂的影响决定于金属表面钝化膜的形成和溶解的竞争过程,因所处的溶液环境及原始的表面状态而异。一般来说,反应速率受到温度的影响,当温度升高时,反应就会加快,这里所说的反应既有可能是腐蚀溶解,也有可能是钝化成膜。大量的腐蚀试验结果表明,钛合金处在钝化条件下,温度与腐蚀速率没有明显的关系,在室温下已经形成的氧化膜在高温条件下稳定性依旧很高[87]。然而,在高温下,钛合金新鲜表面不易发生钝化;在强酸或强碱环境中,钛合金可能会处于活化状态,此时的腐蚀则会随着温度的升高而明显加快。de Souza等[88]采用电化学方法研究了硫酸溶液中,Ti及Ti-Ta在不同温度下的腐蚀行为,结果表明,材料在室温下耐蚀性最高,随着温度的升高,耐蚀性逐渐降低。研究表明,钛合金在高温 (>250 ℃) 氯化物溶液中将发生沿晶型应力腐蚀开裂[89]。海水温度随着深度的增加而降低,当深度达到4000 m左右时降低到2.4 ℃,然后几乎不变。由此推测,对于钝化膜完好的钛合金,低温下腐蚀缓慢,应具有较低的应力腐蚀敏感性;但对于钝化膜遭到破坏的活化体系,以及点蚀、微裂纹、缝隙等闭塞结构,低温和低氧不利于金属钝化,使局部无膜区成为阳极,产生电偶腐蚀效应。而且,腐蚀介质可以与裸露的金属基体直接接触,因此加快了腐蚀溶解和H的吸附和渗透,应力腐蚀敏感性可能增大。研究表明,氢化物的形成是钛合金海水环境应力腐蚀机制中的重要组成部分,塑性变形、化学浸蚀、高温条件下吸氢等都可以成为氢化物的来源[90]。在较高温度下溶解在钛合金晶格中的氢,在室温及以下温度时将析出硬脆的氢化物。低温下H在α-Ti中的扩散缓慢,因此,相较于氢促进解理来说,氢化物的形成更加有优势,加之深海高压的作用使H难以排出,也为氢化物的形成提供了有利条件。含氢量较低时氢化物主要分布在晶界,含氢量较高时晶粒内部也出现氢化物,并以惯析面析出,使材料的韧性降低[91]。在应力作用下,大量氢化物的相继断裂促进了应力腐蚀裂纹的扩展[92]。
4 结语
随着钛合金在深海工程和装备上应用需求的不断增长,我国钛合金材料领域已得到长足的进步,但在应用中尚存在诸多亟待解决的问题,这包括材料成本高、材料体系不健全、缺乏设计评价标准。而制约深海钛合金材料开发和应用的核心问题是基础研究不足。通过总结可见,钛合金在海洋环境中的耐蚀性优异,但在特殊环境中仍能表现出应力腐蚀敏感性。钛合金自身合金成分、相组成、结构类型等材料因素,焊接、热处理等加工过程,以及服役环境和工况条件都是影响其应力腐蚀开裂行为和机制的重要方面。因此,未来钛合金深海环境应力腐蚀研究方向应包含以下几个方面:
(1) 对合金元素和杂质元素含量以及组织构成比例等对钛合金应力腐蚀性能的影响进行量化描述,有助于准确评估钛合金的深海环境失效风险,为优化钛合金成分组织、提高抗应力腐蚀性能提供支撑。
(2) 随着钛合金结构向着大型化和复杂化方向发展,其在深海服役时将承受多重载荷的耦合作用,如深海压力,极端浪涌和深浅交变带来的周期性低频载荷,焊接等后处理过程带来的内应力,碰撞、爆炸等冲击载荷,这极易造成局部应力集中,加之复杂苛刻的深海腐蚀环境,使材料的应力腐蚀风险成倍增加。因此,揭示深海复杂腐蚀环境—多重载荷工况对钛合金应力腐蚀的协同效应,对于推动钛合金深海装备新结构、新工艺的应用和发展具有重要的科学价值和实际意义。
(3) 应用研究表明,海洋生物附着对钛合金的腐蚀影响不大,但会显著降低钛合金构件的工作效率;深海环境中宏观生物较少,微生物则可能成为影响钛合金抗应力腐蚀性能的主要生物因素,特别是微生物新陈代谢诱导H的生成和渗透,可能加速钛合金的氢致开裂。但是由于微生物活动的复杂性,生物膜内SRB与金属表面的相互作用缺乏深入的研究,其诱导腐蚀机理和腐蚀过程尚不清楚。因此,包括钛合金在内的深海合金材料的应力腐蚀开裂与深海微生物的相关性也是今后需解决的关键问题。
参考文献
1 Lin J H, Dan Z H, Lu J F, et al. Research status and prospect on marine corrosion of titanium alloys in deep ocean environments [J]. Rare Met. Mater. Eng., 2020, 49: 1090
1 林俊辉, 淡振华, 陆嘉飞等. 深海腐蚀环境下钛合金海洋腐蚀的发展现状及展望 [J]. 稀有金属材料与工程, 2020, 49: 1090
2 Guo W M, Sun M X, Qiu R, et al. Research progress on corrosion and aging of materials in deep-sea environment [J]. Corros. Sci. Prot. Technol., 2017, 29: 313
2 郭为民, 孙明先, 邱日等. 材料深海自然环境腐蚀实验研究进展 [J]. 腐蚀科学与防护技术, 2017, 29: 313
3 Brown A, Wright R, Mevenkamp L, et al. A comparative experimental approach to ecotoxicology in shallow-water and deep-sea holothurians suggests similar behavioural responses [J]. Aquat. Toxicol., 2017, 191: 10
4 Fan W J, Zhang Y, Tian H W, et al. Corrosion behavior of two low alloy steel in simulative deep-sea environment coupling to titanium alloy [J]. Coll. Interf. Sci. Commun., 2019, 29: 40
5 Kark S, Brokovich E, Mazor T, et al. Emerging conservation challenges and prospects in an era of offshore hydrocarbon exploration and exploitation [J]. Conserv. Biol., 2015, 29: 1573
6 He C Y, Zhang L J. Development and application of high temperature titanium alloy at home and abroad [J]. World Nonferr. Met., 2016, (1): 21
6 何春艳, 张利军. 国内外高温钛合金的发展与应用 [J]. 世界有色金属, 2016, (1): 21
7 Zhao Y Q, Ge P. Current situation and development of new titanium alloys invented in China [J]. J. Aeronaut. Mater., 2014, 34(4): 51
7 赵永庆, 葛鹏. 我国自主研发钛合金现状与进展 [J]. 航空材料学报, 2014, 34(4): 51
8 Pang J J, Blackwood D J. Corrosion of titanium alloys in high temperature near anaerobic seawater [J]. Corros. Sci., 2016, 105: 17
9 Yang X J, Liu Z Y, Zhang D W, et al. Stress corrosion cracking behavior of industrial pure titanium TA2 in sulfide containing deep seawater environment [J]. China Surf. Eng., 2019, 32(4): 17
9 杨小佳, 刘智勇, 张达威等. 工业纯钛TA2在含硫化物深海水环境中的应力腐蚀行为 [J]. 中国表面工程, 2019, 32(4): 17
10 Pilchak A L, Young A H, Williams J C. Stress corrosion cracking facet crystallography of Ti-8Al-1Mo-1V [J]. Corros. Sci., 2010, 52: 3287
11 Dong Y C, Fang Z G, Chang H, et al. Service performance of titanium alloy in marine environment [J]. Mater. China, 2020, 39: 185
11 董月成, 方志刚, 常辉等. 海洋环境下钛合金主要服役性能研究 [J]. 中国材料进展, 2020, 39: 185
12 Wu J X. Application of titanium alloy material on marine material [J]. Marine Equip./Mater. Market., 2020, (8): 5
12 吴建新. 钛合金材料在船舶材料上的应用 [J]. 船舶物资与市场, 2020, (8): 5
13 Yu Y, Li J Q. Current application and prospect of titanium alloys in marine engineering [J]. Dev. Appl. Mater., 2018, 33(3): 111
13 于宇, 李嘉琪. 国内外钛合金在海洋工程中的应用现状与展望 [J]. 材料开发与应用, 2018, 33(3): 111
14 Breddermann K, Drescher P, Polzin C, et al. Printed pressure housings for underwater applications [J]. Ocean Eng., 2016, 113: 57
15 Li D Q, Wang S S, Bao E D. Titanium alloy material in the ship in the material application and development [J]. World Nonferr. Met., 2015, (9): 127
15 李德强, 王树森, 包恩达. 钛合金材料在船舶材料上的应用与发展 [J]. 世界有色金属, 2015, (9): 127
16 Li L S, Xu W S, Chen W H, et al. Application of titanium alloy in seawater piping of aluminum alloy warship [J]. Ship Boat, 2016, 27(3): 27
16 黎理胜, 徐文珊, 陈万宏等. 钛合金在铝合金舰船海水管路系统的应用 [J]. 船舶, 2016, 27(3): 27
17 Song D J, Niu L, Yang S L. Research on application technology of titanium alloy in marine pipeline [J]. Rare Met. Mater. Eng., 2020, 49: 1100
17 宋德军, 牛龙, 杨胜利. 船舶海水管路钛合金应用技术研究 [J]. 稀有金属材料与工程, 2020, 49: 1100
18 Leyens C, Peters M. Titanium and Titanium Alloys: Fundamentals and Applications [M]. Weinheim: Wiley-VCH, 2003: 491
19 Li X J, Wang G, Yang Y L, et al. The development and application of titanium and titanium alloys in ocean and land oil & gas exploiting industry [J]. China Titanium Ind., 2011, (2): 18
19 李献军, 王镐, 羊玉兰等. 钛及钛合金在海洋和大陆油气开采工业中的开发和应用 [J]. 中国钛业, 2011, (2): 18
20 Withers P J. Residual stress and its role in failure [J]. Rep. Prog. Phys., 2007, 70: 2211
21 Chen H, Lu L. Effect of residual stress on localized corrosion behavior of metallic materials [J]. Chin. J. Eng., 2019, 41: 929
21 陈恒, 卢琳. 残余应力对金属材料局部腐蚀行为的影响 [J]. 工程科学学报, 2019, 41: 929
22 Wang J, Jin T, Ma Y M, et al. Stress corrosion cracking behavior of 2507 duplex stainless steel under high residual stress [J]. Pressure Vessel Technol., 2020, 37(3): 50
22 王军, 靳彤, 马一鸣等. 高残余应力下2507双相不锈钢应力腐蚀开裂行为 [J]. 压力容器, 2020, 37(3): 50
23 Bai L Y, Jiang K B, Gao L, et al. Influence mechanism of residual stress on stress corrosion behavior of welded structure [J]. Hot Work. Technol., 2017, 46(21): 168
23 白林越, 江克斌, 高磊等. 残余应力对焊接结构应力腐蚀行为影响机理研究 [J]. 热加工工艺, 2017, 46(21): 168
24 Pan W W, Chen M C, Li B, et al. Analysis of the influence mechanism of residual stress on the stress corrosion behavior of welded structure [J]. Equip. Technol., 2019, (4): 118
24 潘文伟, 陈民昌, 李兵等. 残余应力对焊接结构应力腐蚀行为影响机理分析 [J]. 装备维修技术, 2019, (4): 118
25 Zhu J. Study on the effects and mechanism of deep cryogenic treatment time on organization and properties of electron-beam-welded TC4 joints [D]. Tianjin: Tianjin University, 2017
25 朱江. 深冷处理时间对TC4钛合金电子束焊接接头组织、性能的影响及机理研究 [D]. 天津: 天津大学, 2017
26 Yu C Y. Development of corrosion resistant titanium alloys [J]. Titanium Ind. Prog., 2003, (1): 12
26 余存烨. 耐蚀钛合金的发展 [J]. 钛工业进展, 2003, (1): 12
27 Atapour M, Pilchak A L, Shamanian M, et al. Corrosion behavior of Ti-8Al-1Mo-1V alloy compared to Ti-6A1-4V [J]. Mater. Des., 2011, 32: 1692
28 Yang W T, Long X Q. Special corrosion types of titanium alloy used in civil aircraft [J]. Total Corros. Contr., 2008, 22(2): 42
28 杨文涛, 隆小庆. 飞机上钛合金的特殊腐蚀形式 [J]. 全面腐蚀控制, 2008, 22(2): 42
29 Pustode M D, Raja V S, Paulose N. The stress-corrosion cracking susceptibility of near-α titanium alloy IMI 834 in presence of hot salt [J]. Corros. Sci., 2014, 82: 191
30 Jiang C Y, Wang T, Yan Q, et al. Research on welding application of titanium alloy used in ships [J]. Dev. Appl. Mater., 1992, (6): 16
30 蒋成禹, 汪汀, 严铿等. 舰船用钛合金的焊接应用研究 [J]. 材料开发与应用, 1992, (6): 16
31 Shamir M, Junaid M, Khan F N, et al. A comparative study of electrochemical corrosion behavior in Laser and TIG welded Ti-5Al-2.5Sn alloy [J]. J. Mater. Res. Technol., 2019, 8: 87
32 Karimzadeh F, Heidarbeigy M, Saatchi A. Effect of heat treatment on corrosion behavior of Ti-6Al-4V alloy weldments [J]. J. Mater. Proc. Technol., 2008, 206: 388
33 Fang W P, Xiao T, Zhang Y P, et al. Stress corrosion crack sensitivity of ultra-thick TC4 titanium alloy electron beam welding joints [J]. Trans. China Weld. Instit., 2019, 40: 121
33 房卫萍, 肖铁, 张宇鹏等. 超厚板TC4钛合金电子束焊接接头应力腐蚀敏感性 [J]. 焊接学报, 2019, 40: 121
34 Shukla A K, Balasubramaniam R, Bhargava S. Properties of passive film formed on CP titanium, Ti-6Al-4V and Ti-13.4Al-29Nb alloys in simulated human body conditions [J]. Intermetallics, 2005, 13: 631
35 Diao Y W. The study on tensile behavior of Ti-Al-Sn-Zr-Mo-Nb-W-Si high temperature titanium alloy at 700 ℃ [D]. Beijing: General Research Institute for Nonferrous Metals, 2019
35 刁雨薇. Ti-Al-Sn-Zr-Mo-Nb-W-Si高温钛合金700 ℃拉伸行为研究 [D]. 北京: 北京有色金属研究总院, 2019
36 Shi K Y, Wu W J, Zhang Y, et al. Electrochemical properties of Nb coating on TC4 substrate in simulated body solution [J]. J. Chin. Soc. Corros. Prot., 2021, 41: 71
36 史昆玉, 吴伟进, 张毅等. TC4表面沉积Nb涂层在模拟体液环境下的电化学性能研究 [J]. 中国腐蚀与防护学报, 2021, 41: 71
37 Wang L, Yi D Q, Liu H Q, et al. Effect of Ru on corrosion behavior of Ti-6Al-4V alloy and its mechanism [J]. J. Chin. Soc. Corros. Prot., 2020, 40: 25
37 王乐, 易丹青, 刘会群等. Ru对Ti-6Al-4V合金腐蚀行为的影响及机理研究 [J]. 中国腐蚀与防护学报, 2020, 40: 25
38 Wu X F, Yang H Q, Wang C Y. Effect of manganese addition on microstructure and mechanical properties of Ti-Mo biomedical alloys [J]. Chin. J. Nonferrous Met., 2017, 27: 1902
38 武晓峰, 杨会齐, 王春雨. Mn对生物医用Ti-Mo合金组织与力学性能的影响 [J]. 中国有色金属学报, 2017, 27: 1902
39 Zhang R. The study on susceptibility to stress corrosion carcking and hydrogen embrittlement of titanium and titanium alloy in seawater [D]. Hohhot: Inner Mongolia University of Technology, 2013
39 张睿. 钛及钛合金在海水中的应力腐蚀及氢脆敏感性研究 [D]. 呼和浩特: 内蒙古工业大学, 2013
40 Sun Z J, Wang Y. Research status and prospect of the stress-corrosion of titanium alloys [J]. Dev. Appl. Mater., 2020, 35(2): 94
40 孙志杰, 王洋. 钛合金应力腐蚀研究现状及展望 [J]. 材料开发与应用, 2020, 35(2): 94
41 Liu J H, Hao X L, Li S M, et al. Resistance to stress corrosion cracking of new Al-Mg-Cu alloy containing Sc [J]. Chin. J. Nonferrous Met., 2010, 20: 415
41 刘建华, 郝雪龙, 李松梅等. 新型含钪Al-Mg-Cu合金的抗应力腐蚀开裂特性 [J]. 中国有色金属学报, 2010, 20: 415
42 Li Y. Stress corrosion cracking behavior and mechanism of E690 steel and welded joint in simulated seawater [D]. Beijing: University of Science and Technology Beijing, 2019
42 李永. E690钢及焊接接头模拟海水环境中应力腐蚀行为与机理研究 [D]. 北京: 北京科技大学, 2019
43 Yang Y, Cheng Y F. Effect of stress on corrosion at crack tip on pipeline steel in a near-neutral pH solution [J]. J. Mater. Eng. Perform., 2016, 25: 4988
44 Chang L, Kitamura T, Zhou C Y. Atomic simulation of the orientation effects on crack tip behavior in titanium single crystal [J]. Theoret. Appl. Fract. Mech., 2020, 110: 102791
45 Huang X Y, Zhu Z F, Wang D M, et al. A study of the mechanism of scc of titanium alloys [J]. J. Chin. Soc. Corros. Prot., 1982, 2(4): 37
45 黄显亚, 朱祖芳, 王得明等. 钛合金应力腐蚀开裂机理的研究 [J]. 中国腐蚀与防护学报, 1982, 2(4): 37
46 Zhao P, Su Y. Research progress in stress corrosion cracking of high-strength aluminum alloy [J]. Equip. Environ. Eng., 2016, 13(1): 130
46 赵鹏, 苏艳. 高强铝合金应力腐蚀开裂研究进展 [J]. 装备环境工程, 2016, 13(1): 130
47 Liu G L. Study of stress corrosion mechanism of Ti alloys by recursion method [J]. Acta Metall. Sin., 2007, 43: 249
47 刘贵立. 递归法研究钛合金应力腐蚀机理 [J]. 金属学报, 2007, 43: 249
48 Zhang J S. Strength of Materials [M]. Harbin: Harbin Institute of Technology Press, 2014: 322
48 张俊善. 材料强度学 [M]. 哈尔滨: 哈尔滨工业大学出版社, 2014: 322
49 Zhang T J. Electron microscopy study on phase transformation of titanium alloy (Ⅵ)—Hydride in titanium alloy [J]. Rare Met. Mater. Eng., 1990, (1): 75
49 张廷杰. 钛合金相变的电子显微镜研究 (Ⅵ)—钛合金中的氢化物 [J]. 稀有金属材料与工程, 1990, (1): 75
50 Madina V, Azkarate I. Compatibility of materials with hydrogen. Particular case: Hydrogen embrittlement of titanium alloys [J]. Inter. J. Hydr. Energy, 2009, 34: 5976
51 Yan H, Liu H Y, Xi Y F, et al. Failure analysis for hydrogen embrittlement corrosion of TA10 pipe [J]. Petro Chem. Equip., 2019, 22(9): 94
51 燕辉, 刘鸿彦, 郗运富等. TA10换热管氢脆腐蚀的失效分析 [J]. 石油和化工设备, 2019, 22(9): 94
52 Guo M, Peng Q, Cui C J. Absorption hydrogen on the cathode effects on corrosion-resisting property of Ti in sea water [J]. Total Corros. Contr., 2002, 16(2): 9
52 郭敏, 彭乔, 崔昌军. 阴极充氢对钛在海水中耐蚀性能的影响 [J]. 全面腐蚀控制, 2002, 16(2): 9
53 Luo Q, Wang L, Liu S W. Effects of hydrogen on the performance of the TA16 titanium alloy [J]. Ordnan. Mater. Sci. Eng., 2011, 34(2): 51
53 罗强, 王理, 刘思维. 氢对TA16钛合金性能影响研究 [J]. 兵器材料科学与工程, 2011, 34(2): 51
54 Wang D M, Huang X Y, Zhu Z F. Study on the mechanism of hydrogen-induced damage in titanium by ultra-high pressure electron microscopy [J]. Rare Met., 1983, (5): 22
54 王得明, 黄显亚, 朱祖芳. 用超高压电镜研究钛中氢致破坏机理 [J]. 稀有金属, 1983, (5): 22
55 Xin S W, Zhao Y Q, Zeng W D. Inductions and discussions of solid state phase transformation of titanium alloy (Ⅱ)—eutectoid and ordering transformation [J]. Titanium Ind. Prog., 2008, 25(1): 40
55 辛社伟, 赵永庆, 曾卫东. 钛合金固态相变的归纳与讨论 (Ⅱ)—共析和有序化转变 [J]. 钛工业进展, 2008, 25(1): 40
56 Zhong Q P, Zhou Y, Zhang Z. Crackology [M]. Beijing: Higher Education Press, 2014: 136
56 钟群鹏, 周煜, 张峥. 裂纹学 [M]. 北京: 高等教育出版社, 2014: 136
57 Qiao Y X, Xu D K, Wang S, et al. Effect of hydrogen charging on microstructural evolution and corrosion behavior of Ti-4Al-2V-1Mo-1Fe alloy [J]. J. Mater. Sci. Technol., 2021, 60: 168
58 Zhan S Y, Zheng B L, Xi Q. Analysis of hydrogen induced stress corrosion of cracked titanium alloy pressure vessel in deep sea environment [A]. 2017 Fourth Conference on Marine Materials and Corrosion Protection Proceedings [C]. Beijing, 2017: 6
58 詹思远, 郑百林, 席强. 带裂纹钛合金压力容器在深海环境中的氢致应力腐蚀分析 [A]. 2017第四届海洋材料与腐蚀防护大会论文集 [C]. 北京, 2017: 6
59 Dong X C, Guan F, Xu L T, et al. Progress on the corrosion mechanism of sulfate-reducing bacteria in marine environment on metal materials [J]. J. Chin. Soc. Corros. Prot., 2021, 14: 1
59 董续成, 管方, 徐利婷等. 海洋环境硫酸盐还原菌对金属材料腐蚀机理的研究进展 [J]. 中国腐蚀与防护学报, 2021, 14: 1
60 Wang X T, Chen X, Han Z Z, et al. Stress corrosion cracking behavior of 2205 duplex stainless steel in 3.5%NaCl solution with sulfate reducing bacteria [J]. J. Chin. Soc. Corros. Prot., 2021, 41: 43
60 王欣彤, 陈旭, 韩镇泽等. 硫酸盐还原菌作用下2205双相不锈钢在3.5%NaCl溶液中应力腐蚀开裂行为研究 [J]. 中国腐蚀与防护学报, 2021, 41: 43
61 Liu J, Li X B, Wang J. Effect of hydrostatic pressure on the corrosion behaviors of two low alloy steels [J]. Acta Metall. Sin., 2011, 47: 697
61 刘杰, 李相波, 王佳. 模拟深海压力对2种低合金钢腐蚀行为的影响 [J]. 金属学报, 2011, 47: 697
62 Zhou J L, Li X G, Cheng X Q, et al. Research progress on corrosion of metallic materials in deep sea environment [J]. Corros. Sci. Prot. Technol., 2010, 22: 47
62 周建龙, 李晓刚, 程学群等. 深海环境下金属及合金材料腐蚀研究进展 [J]. 腐蚀科学与防护技术, 2010, 22: 47
63 Raoof M, Davies T J. Axial fatigue design of sheathed spiral strands in deep water applications [J]. Int. J. Fatigue, 2008, 30: 2220
64 Zhang T, Yang Y G, Shao Y W, et al. A stochastic analysis of the effect of hydrostatic pressure on the pit corrosion of Fe-20Cr alloy [J]. Electrochim. Acta, 2009, 54: 3915
65 Wang X H, Fan L, Ding K K, et al. Pitting corrosion of 2Cr13 stainless steel in deep-sea environment [J]. J. Mater. Sci. Technol., 2021, 64: 187
66 Yang Y G, Zhang T, Shao Y W, et al. Effect of hydrostatic pressure on the corrosion behaviour of Ni-Cr-Mo-V high strength steel [J]. Corros. Sci., 2010, 52: 2697
67 Yang Y G, Zhang T, Shao Y W, et al. New understanding of the effect of hydrostatic pressure on the corrosion of Ni-Cr-Mo-V high strength steel [J]. Corros. Sci., 2013, 73: 250
68 Beccaria A M, Poggi G, Gingaud D, et al. Effect of hydrostatic pressure on passivating power of corrosion layers formed on 6061 T6 aluminium alloy in sea water [J]. Br. Corros. J., 1994, 29: 65
69 Beccaria A M, Poggi G, Castello G. Influence of passive film composition and sea water pressure on resistance to localised corrosion of some stainless steels in sea water [J]. Br. Corros. J., 1995, 30: 283
70 Sun H J, Liu L, Li Y, et al. Effect of hydrostatic pressure on the corrosion behavior of a low alloy steel [J]. J. Electrochem. Soc., 2013, 160: C89
71 Hu Y L, Wang Z Q, Zhao X, et al. Effect of alternation of hydrostatic pressure on corrosion behavior of high strength hull steel [J]. J. Naval Univ. Eng., 2018, 30(5): 69
71 胡裕龙, 王智峤, 赵欣等. 静水压力交变对高强度船体钢腐蚀行为的影响 [J]. 海军工程大学学报, 2018, 30(5): 69
72 Liu R, Cui Y, Liu L, et al. A primary study of the effect of hydrostatic pressure on stress corrosion cracking of Ti-6Al-4V alloy in 3.5% NaCl solution [J]. Corros. Sci., 2020, 165: 108402
73 Wang J, Meng J, Tang X, et al. Assessment of corrosion behavior of steel in deep ocean [J]. J. Chin. Soc. Corros. Prot., 2007, 27: 1
73 王佳, 孟洁, 唐晓等. 深海环境钢材腐蚀行为评价技术 [J]. 中国腐蚀与防护学报, 2007, 27: 1
74 Berthaud M, Popa I, Chassagnon R, et al. Study of titanium alloy Ti6242S oxidation behaviour in air at 560 ℃: Effect of oxygen dissolution on lattice parameters [J]. Corros. Sci., 2020, 164: 108049
75 Gong M, Huang W H, Zou Z, et al. Effect of dissolved oxygen in bittern on pitting behavior of 2205D stainless steel at different temperatures [J]. Mater. Prot., 2009, 42(10): 23
75 龚敏, 黄文恒, 邹振等. 2种温度下O2对2205DSS在盐卤介质中点蚀行为的影响 [J]. 材料保护, 2009, 42(10): 23
76 Wang J, Shang X C, Lu M X, et al. Pitting nucleation of 316L stainless steel in different environments [J]. J. Mater. Eng., 2015, 43(9): 12
76 王晶, 尚新春, 路民旭等. 316L不锈钢在不同环境中点蚀形核研究 [J]. 材料工程, 2015, 43(9): 12
77 Peng W C. Study of corrosion performance of aluminium alloy in seawater [D]. Changsha: Hunan University, 2010
77 彭文才. 铝合金在海水中的腐蚀性能研究 [D]. 长沙: 湖南大学, 2010
78 Nakagawa M, Matsuya S, Udoh K. Effects of fluoride and dissolved oxygen concentrations on the corrosion behavior of pure titanium and titanium alloys [J]. Dent. Mater. J., 2002, 21: 83
79 Dong J J, Fan L, Zhang H B, et al. Electrochemical performance of passive film formed on Ti-Al-Nb-Zr alloy in simulated deep sea environments [J]. Acta Metall. Sin. (Eng. Lett.), 2020, 33: 595
80 Hall Jr M M. Effect of variable stress intensity factor on hydrogen environment assisted cracking [J]. Metall. Mater. Trans., 2011, 42A: 304
81 Luo Q, Wang L, Chen X, et al. Studies on the corrosion behavior of TA16 and TA17 titanium alloys in high temperature and high pressure water [J]. Light Met., 2012, (2): 56
81 罗强, 王理, 陈新等. TA16和TA17钛合金在高温高压水中的腐蚀行为研究 [J]. 轻金属, 2012, (2): 56
82 Wataha J C. Principles of biocompatibility for dental practitioners [J]. J. Prosthet. Dent., 2001, 86: 203
83 Ran D, Meng H M, Liu X, et al. Effect of pH on corrosion behavior of 14Cr12Ni3WMoV stainless steel in chlorine-containing solutions [J]. J. Chin. Soc. Corros. Prot., 2021, 41: 51
83 冉斗, 孟惠民, 刘星等. pH对14Cr12Ni3WMoV不锈钢在含氯溶液中腐蚀行为的影响 [J]. 中国腐蚀与防护学报, 2021, 41: 51
84 Jiang Y, Wu Y, Wang K. Acetic acid-direct corrosive mediator in SCC of titanium/ethanol system [J]. Mater. Corros., 2006, 57: 418
85 Zhang H W, Man C, Dong C F, et al. The corrosion behavior of Ti6Al4V fabricated by selective laser melting in the artificial saliva with different fluoride concentrations and pH values [J]. Corros. Sci., 2021, 179: 109097
86 Aladjem A, Aucouturier M, Lacombe P. Anodic oxidation and stress corrosion cracking (SCC) of titanium alloys [J]. J. Mater. Sci., 1973, 8: 787
87 Schutz R W. Environmental behavior of beta titanium alloys [J]. JOM, 1994, 46(7): 24
88 De Souza K A, Robin A. Influence of concentration and temperature on the corrosion behavior of titanium, titanium-20 and 40% tantalum alloys and tantalum in sulfuric acid solutions [J]. Mater. Chem. Phys., 2007, 103: 351
89 Brown B F, Beachem C D. A study of the stress factor in corrosion cracking by use of the pre-cracked cantilever beam specimen [J]. Corros. Sci., 1965, 5(11): 745
90 Sanderson G, Scully J C. Room temperature stress corrosion cracking of Titanium alloys [J]. Nature, 1966, 5045: 179
91 Zhang Y K, Wang S C, Zhang Y H, et al. Effect of hydrogen on structure and properties of TC4 alloy in cyclic temperature field [J]. J. Funct. Mater. Contents, 2004, 35(suppl.): 3340
91 张云琨, 王树臣, 张艳鸿等. 循环温度场下氢对TC4钛合金组织和性能的影响 [J]. 功能材料, 2004, 35(): 3340
92 Scully J C, Powell D T. The stress corrosion cracking mechanism of α-titanium alloys at room temperature [J]. Corros. Sci., 1970, 10: 719
免责声明:本网站所转载的文字、图片与视频资料版权归原创作者所有,如果涉及侵权,请第一时间联系本网删除。
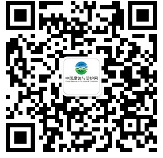
官方微信
《腐蚀与防护网电子期刊》征订启事
- 投稿联系:编辑部
- 电话:010-62316606-806
- 邮箱:fsfhzy666@163.com
- 腐蚀与防护网官方QQ群:140808414