在内部流体介质冲刷与腐蚀作用下,油气井口装置易出现腐蚀减薄缺陷,形成潜在的泄漏风险。干耦合压电传感方法因具有高稳定性和高可靠性,可应用于井口装置腐蚀在线监测与评价中。实际作业过程中,流体介质状态与环境温度变化会导致被测井口装置工作温度发生变化,从而影响腐蚀测量精度。
压裂是指在采油或采气过程中,利用水利作用使油气层形成裂缝的一种方法。压裂作业中,井口装置及注入管线内壁会因承受高速压裂液中固体颗粒的冲蚀而出现损伤,形成安全隐患。因此,为保证安全生产,需要对井口装置腐蚀状况进行监测。
目前压裂井口装置的腐蚀检测主要是通过人工定期超声测厚的方式进行;且因安全问题在压裂工作过程中无法实施检测,从而无法掌握检测间隔期井口装置的实际腐蚀状况。
因此,亟需开展压裂井口装置腐蚀状况的远程、在线、持续、高精度监测,以代替人工定期检测。
与长输管道不同,压裂结构装置由各种三通、弯头等连接结构组成,井口装置空间狭窄,结构复杂。监测方法需适应变形、变径、狭窄空间等测量与安装要求;工作过程中因内部输送高压液体,整个装置会发生幅度较大的高频振动,对传感器工作的稳定性带来巨大挑战。
因此,光纤、导波、场指纹法、声发射、腐蚀挂片等方法均难以应用于井口装置腐蚀情况的实时在线监测和预警。
在实际使用过程中,井口装置一般工作在野外,而在新疆地区等昼夜与季节温差变化剧烈的环境下,井口装置温度会发生剧烈变化;同时,内部流体介质的温度、流速、摩擦作用也会导致管道温度发生变化,进一步影响井口材料与耦合材料的声速,使得不同温度下井口装置腐蚀监测与评价结果不同,降低腐蚀监测精度。因此,新疆油田分公司实验检测研究院和四川大学机械工程学院的技术人员研究了温度变化对井口材料声速与耦合材料性能的影响规律,在此基础上构建基于实时温度测量的壁厚补偿算法,以提高井口装置的腐蚀监测精度。
01 井口装置干耦合压电传感腐蚀监测方法
基于干耦合压电传感的压裂井口装置腐蚀在线监测系统主要包括腐蚀传感器、温度传感器、监测主机、腐蚀监测平台与软件4部分。
图1 压裂井口装置腐蚀在线监测系统整体框架
布置于压裂井口装置不同腐蚀监测点的干耦合压电传感器与温度传感器将管道腐蚀情况与温度通过信号线集中汇入到现场监测主机内。现场监测主机内包含电源管理模块、主控模块、通信模块、超声激励与信号处理模块、温度测量模块等。根据防爆以及野外电源供电限制工况,设备通过防爆铅蓄电池供电。腐蚀监测信号在主机内完成处理,然后根据现场网络条件通过有线或者无线网络传输至云平台进行存储与分析。
腐蚀监测系统为BS(浏览器/服务器)架构,用户可在客户端通过网络方式对云平台数据进行查看、调用与操作。软件可显示不同监测点的腐蚀实时数据与变化曲线,并可通过设置不同阈值进行预警。
干耦合压电传感腐蚀监测方法的核心是干耦合剂。受高低温变化以及抖动等影响,传统的液态耦合剂在长期监测过程中容易挥发和流失,无法长期稳定工作。为此,针对液态耦合剂不稳定的问题,开发了一种干耦合材料代替液体耦合剂。
图2 干耦合压电传感器实物
干耦合剂材料以聚二甲基硅氧烷为主要原料,辅以交联剂、填料、增塑剂、偶联剂、催化剂等混合而成,在常温下通过与空气中的水蒸气发生反应,从而达到固化的效果。该干耦合剂材料具备安装施工前为糊状半液态,施工后转化成固态的特点,可轻易地排除耦合间隙的空气,且无需较大的耦合压紧力,同时可耐户外自然老化。经试验对比,干耦合剂与传统耦合剂甘油的耦合效果相当。
实际安装时,首先对管道表面进行处理,然后将干耦合剂放置于管道与传感器之间,针对不同工况利用传感器工装将传感器定位并固定在管道表面,以保证长期稳定的耦合效果。
02 温度变化对干耦合压电监测精度的影响
温度变化会影响金属管道材料与干耦合材料中的声速,因此井口装置温度变化是影响腐蚀监测精度的主要因素。基于井口装置工作温度变化范围,开展了温度对压电腐蚀监测精度的影响规律研究。
图3 试验平台实物
搭建的试验平台由标准试块、单晶探头、单晶探头工装、钢扎带、测厚仪(38DLP型)等组成。采用加热台与低温试验箱实现对试件的加热与降温,以模拟井口装置的实际工作温度变化,采用红外热成像仪精确测量试件温度。试件材料为45号钢,标准厚度为80.46 mm。
温度变化对金属材料声速的影响
为了消除温度对测量精度的影响,需获得钢材料在不同温度下的声速变化规律,为温度补偿奠定基础,进行了不同温度下的钢材声速测量试验,采用5 MHz单晶探头进行测量,利用回波-回波模式,消除耦合剂耦合状态变化对测量结果的影响。
将测厚仪中的声速设定为30 ℃下钢中的纵波声速V30,取5948 m/s;利用测厚仪对试件进行测厚,获得不同温度下的测量厚度hT,从而计算出声波在试件中的实际传播时间tT。由于井口装置温度变化引起的试件变形较小,壁厚变化可忽略不计,h0始终为80.46 mm。最终,可获得不同温度下声速变化计算公式:
VT = 2h0/tT = 2h0/ (2hT/V30) = h0/hT·V30 (1)
式中:T为试件温度;VT为T温度下声速;h0为试件实际厚度;hT为T温度下的测量厚度;tT为T温度下声波传播时间。
根据井口装置的实际温度工况,测试温度设定为-30~80 ℃,利用式(1)计算不同温度下钢中的纵波声速,可知温度从-10 ℃变化到75 ℃时,试块厚度从80.14 mm变化到80.81 mm,即温度每升高85 ℃,测量厚度增大0.67 mm。因此,温度每升高100 ℃,声速变化导致的厚度测量值约增大1%。基于此建立不同温度下钢中声速变化曲线,如图4所示。
图4 不同温度下钢中声速变化曲线
由图4可以看出,随着温度的增加,声速近似成线性降低,可构建如下式所示的声速-温度关系:
VT = V30+ [(30-T)/100] ×60 (2)
在实际工作过程中,可利用温度传感器测量井口装置被测点的当前温度T,根据式(2)计算获得当前温度下的准确声速,最后实现井口装置厚度的精确测量。
温度变化对干耦合剂材料性能的影响
当压裂井口装置温度发生变化时,与钢管紧密贴合的干耦合材料中的声速与性能会发生变化,影响以始波-回波测量方式的壁厚测量精度。
为此,开展了不同温度下不同厚度耦合材料的检测试验。利用不同厚度的干耦合材料,在不同温度下以始波-回波测量方式测量试件厚度,测量温度变化引起的测量值与信号幅值变化。
干耦合剂厚度为0.1,0.2,0.3,0.4,0.5 mm;钢板试件厚度为7.0 mm;检测温度为20~100 ℃,测量温度间隔为10 ℃,每种温度状态保持10 min,以保证探头和耦合剂温度与检测温度相同,测量获得不同温度以及不同干耦合材料厚度下的钢板试件厚度。
试验发现,随着温度的增加信号幅值不断降低,为对比温度造成的检测幅值变化规律,每次测量时调整增益使得信号峰值始终处于显示范围80%处,干耦合压电传感的始波-回波测量界面如图5所示,由不同温度及不同干耦合材料厚度下的钢板试件厚度测量结果可以看出,当温度从20 ℃逐渐增加到100 ℃,5种厚度干耦合材料所需的增益波动较小,说明干耦合材料在不同温度条件下具有稳定的耦合性能。
图5 干耦合压电传感的始波-回波测量界面
进一步分析利用不同厚度干耦合材料进行耦合时,在不同温度下测量的钢板厚度变化规律,干耦合压电传感时始波-回波测量厚度曲线如图6所示。
图6 干耦合压电传感时始波-回波
测量厚度曲线
可以看出,一方面,干耦合材料会引起一定的零位偏差,并且随着耦合剂厚度增加,偏差逐渐增大;另一方面,厚度测量值均存在随着温度增加而增大的现象,这是由碳钢材料和干耦合材料中声速随温度变化的叠加效应引起的,且耦合材料厚度越大,差异越大,这表明干耦合材料中的声速受温度影响较大。
另外,0.1 mm干耦合材料引起的测厚值总体增加了0.2 mm,减去碳钢件受温度影响的测厚值变化(约为0.1 mm),即干耦合材料受温度影响的测厚数据变化约为0.1 mm。
上述结论在采用始波-回波测量模式进行测量时需要加以考虑。此外,如采用回波-回波测量模式,则干耦合材料不会影响测厚精度,只会影响信号增益。
03 现场试验
采用干耦合压电腐蚀监测系统在新疆克拉玛依油田、塔里木油田等多个井场进行了井口装置腐蚀监测试验,其现场如图7所示。
图7 井口装置腐蚀监测现场
腐蚀监测传感器布置在直角弯和三通等易发生腐蚀的位置,利用回波-回波方式对管道壁厚进行测量,并利用铂热敏电阻吸附在管道表面进行测温。测厚数据与温度数据经4G无线网络传输至云平台进行处理,并按照式(2)对测量壁厚进行校准。
某井口装置壁厚监测曲线如图8所示。经过周期为1年的持续测试,进行温度补偿后,该变化温度条件下的井口装置腐蚀在线监测方法测量精度较高,稳定性较好,可消除温度对壁厚测量结果的影响。
图8 某井口装置壁厚监测曲线
04 结论
1 井口装置温度变化会影响钢材料中的声速,造成测量值产生偏差。因此,需要布置温度传感器测量监测点位的温度,进一步对监测结果进行声速校准与厚度补偿。
2 利用回波-回波模式,可消除干耦合剂造成的测量误差;利用始波-回波模式需考虑干耦合剂造成的测量误差;温度变化会影响信号幅值,检测时需要根据温度变化调整增益,进而达到最佳的测量效果。
免责声明:本网站所转载的文字、图片与视频资料版权归原创作者所有,如果涉及侵权,请第一时间联系本网删除。
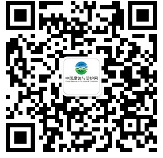
官方微信
《中国腐蚀与防护网电子期刊》征订启事
- 投稿联系:编辑部
- 电话:010-62316606-806
- 邮箱:fsfhzy666@163.com
- 中国腐蚀与防护网官方QQ群:140808414