摘要:
南海某油田油管多次发生腐蚀穿孔,本文通过失效部位宏观分析、微观分析、理化检验和腐蚀产物分析对腐蚀机理进行研究。结果表明,该油管物理化学性能均符合标准,腐蚀失效的主要原因是二氧化碳腐蚀,碳钢耐二氧化碳腐蚀差,建议更换含Cr管材。
关键词: 腐蚀失效,元素分析,CO2腐蚀
0 引言
该失效油管位于中国南海,该油井在1997年曾发生过多个管柱腐蚀穿孔,经过失效分析与一些腐蚀控制手段,已有十余年未再发生管柱腐蚀穿孔,但随着该油田进入开发后期,进入特高含水采油期,平台生产水管线多次发生腐蚀泄漏,严重威胁油田安全生产[1]。
碳钢油管广泛应用于油气井生产中,而油管管体处发生内壁腐蚀穿孔的事件时有发生。为了更好针对目标研究对象的失效分析,对国内外相关案例进行调研分析,大量的失效案例表明,碳钢油管管体腐蚀失效主要有以下原因:高矿化度腐蚀介质;二氧化碳及硫化氢气体;微观组织结构的不均匀性;基体表面的非金属夹杂(硫化物、磷化物、氧化铝等)等。
1 失效管件宏观分析
失效管件的材质为碳钢,图1是失效管件的宏观形貌,可以看到管件外表面腐蚀较均匀,不存在局部腐蚀情况,而管件内部腐蚀严重,整个内表面几乎全被腐蚀,形成很多蚀坑,局部腐蚀严重但没有明显的垢层,可以判断腐蚀发生在内表面,且不存在垢下腐蚀。0条笔记
图1 失效管件宏观形貌
2 失效部位的微观分析
2.1 管材的理化检验
2.1.1 化学成分分析
针对管件上不规律分布的腐蚀孔洞和壁厚不均匀的情况,对失效管件的腐蚀区域和未腐蚀区域分别取样并进行化学成分分析,确定腐蚀原因是否为基体材质成分不均。
金属腐蚀失效是材料和环境共同作用的结果。因此,针对目标失效管件,我们首先从材质角度,分析失效的内因。图2为失效管件腐蚀区域基材的SEM及能谱分析,表1为对应的能谱分析结果。结果表明,失效管件腐蚀区域基材的元素主要由C、Cr、Fe组成,未发现明显的P、S等易导致夹杂物的元素存在。
图2 腐蚀区域样品EDS取样及元素分布图
表1 腐蚀区域样品EDS结果
图3为失效管件未腐蚀区域基材的SEM及能谱分析,表2为对应的能谱分析结果。结果表明,失效管件未腐蚀区域基材的元素仍然主要由C、Cr、Fe组成,未发现明显的P、S等易导致夹杂物的元素存在。
图3 未腐蚀区域样品EDS取样及元素分布图
表2 未腐蚀区域样品EDS结果
从表1、表2腐蚀区域、未腐蚀区域样品EDS结果可以看到,两个区域的基体材质在元素种类上一致,都只含有C、Mn、Fe,含量几乎一样。从而从化学成分这个角度可以排除腐蚀并非由于基体材质分布不均引起的。结果表明该管线化学成分符合API Spec 5CT规定,材质因素不是导致腐蚀失效的原因。
2.1.2 金相组织分析
金相组织观测可以得知构成金属管材的微观组织是否符合规范。因此,我们采用4%硝酸酒精溶液浸蚀,金相结构如图4所示。结果表明,显微组织为铁素体+珠光体。符合API Spec 5CT规定,未见到明显的晶粒粗大现象。
2.1.3 管材硬度测试
对于管材硬度的测量,实验使用仪器SEMI-BRINELL HARDNESS TESTER,硬质合金球直径为2.5mm,试验力为1000N,试验力保持时间为10s。测量结果如表3所示,平均硬度为HB213.45MPa。API标准中对材质硬度并无明确要求。该管材应力范围符合碳钢典型应力分布范围,硬度值适中,不易导致典型的应力腐蚀。0条笔记
图4 失效管件金相组织图
表3 失效管件硬度测试结果(单位:HBW)
2.2 腐蚀产物的微观分析
针对管线失效部位,取下腐蚀产物样品,对其形貌(SEM)、元素组成(EDS)及物相(XRD)进行分析,力图通过材料微观表征技术,得到腐蚀失效的本质原因。0条笔记
2.2.1 样品预处理
取失效管件内部腐蚀产物,其形貌如表4所示,至于研钵中制成粉末,如表4所示。
表4 处理前后样品图片
2.2.2 腐蚀产物分析
SEM微观形貌观测和EDS元素分析使用德国卡尔蔡司公司生产的型号为EVOMA15。XRD物相分析使用荷兰飞利浦公司的X'Pert Pro MPD进行测试。
三种分析测试都使用的是试样固相作为测试分析样品。其中,图5为腐蚀产物的微观形貌图。从图中可以看到,该颗粒呈无定形状,无明显的晶体形状,无典型晶面。颗粒之间聚集较多。
深入的EDS分析如图6及表5所示。能谱面扫表明,腐蚀产物主要由C、O、Cl、Ca、Fe及Cr等元素组成。其它原始的存在,表明腐蚀产物主要可能是碳酸钙(CaCO3)、碳酸亚铁(Fe CO3)及氧化物(FexOy)组成。其中的氧化物可能源于管线样品存放和运输过程中的曝氧所致。而从这些元素的含量来看,碳元素较高。
图5 腐蚀产物SEM图
图6 腐蚀产物EDS取样及元素分布图
图7 腐蚀产物XRD图
X R D分析进一步证实了腐蚀产物主要是碳酸盐,如图7所示。
2.3 荧光显微镜探测
荧光显微镜探测可以了解样品表面是否具有SRB,从而确定是否因为细菌腐蚀导致管材失效。荧光显微镜是以紫外线为光源,用以照射被检物体,使之发出荧光,然后在显微镜下观察物体的形状及其所在位置。样品置于载玻片上进行观测,其结果如下:00条笔记
图8 样品荧光探测图
如图8所示,样品荧光探测图中无任何荧光显示,说明其腐蚀产物中无细菌,从而排除掉管线的腐蚀孔洞是由细菌引起的。
综合以上分析,可以得出该管线腐蚀失效的主要原因是CO2腐蚀,它在油气工业领域中也被称为Sweet
Corrosion,这种腐蚀实质是CO2气体溶解在水中生成H2CO3,金属表面接触H2CO3溶液发生电化学腐蚀。对于CO2的腐蚀机制,有很多学者进行了研究,目前学界对CO2腐蚀的主流解释是这样的过程:00条笔记
表5 腐蚀产物EDS结果
当CO2气体接触水时,一部分的CO2将溶解在水中,形成具有一定浓度的CO2溶液,CO2在水中的溶解度主要取决于CO2分压和环境温度。溶液中CO2的浓度和CO2的分压成一定比例[2]。
溶解在水里的CO2和水反应生成碳酸:
碳酸分两步水解:
第一步水解:
第二步水解:
因为H2CO3第二步水解非常微弱,甚至可忽略不计,所以可以认为溶液中的H2CO3是以H+和HCO3-存在的。因此,反应生成物中的大多数物质不是Fe CO3而是Fe(HCO3)2[3],
Fe(HCO3)2在高温下不稳定,发生分解:
其中,阳极反应为:
它是分多步完成的。
阴极反应为:
在产生CO2腐蚀时,金属失效的基本特征是局部腐蚀,这种腐蚀形态往往表现为台地状腐蚀、坑点腐蚀及癣状腐蚀,这和CO2腐蚀过程中生成的Fe CO3膜的沉积有关。当Fe CO3膜均匀且致密地分布于金属上时,便可以对金属提供保护,而当其疏松分布或由于冲刷等作用导致膜的局部破损时,将使金属表面遭受更为严重的局部腐蚀。
3 结论与建议
3.1 结论
(1)失效管件腐蚀产物中C、O、Fe含量较高,含有少量的Ca、Cl、Cr。主要腐蚀产物就是Fe CO3,少量CaCO3,但表面结垢情况不明显,没有垢下腐蚀现象,二氧化碳腐蚀是主要因素;
(2)基体材质在腐蚀区域、未腐蚀区域只含有C、Cr、Fe三种元素,腐蚀孔洞和厚度极不均匀的壁厚不是因为化学成分分布不均引起的,而是接触腐蚀介质不均匀的原因;
(3)管件的金相显微结构与硬度符合要求;
(4)样品荧光探测图中无任何荧光显示,说明其腐蚀产物中无细菌,从而排除掉管件的腐蚀是由细菌引起的。
3.2 建议
(1)应投加抗CO2腐蚀的缓蚀剂;
(2)使用耐CO2材料的油管,即增加油管材料中的Cr含量,由于含水量已经较高,建议根据现场工况进行3Cr,9Cr和13Cr的材质评价实验。
参考文献
[1]谭四周,杨浩波,王维锋.陆丰13-2DPP平台生产分离器的腐蚀与防护[J].涂料工业, 2017, 47(02):63-66.
[2]万家瑰. N80钢在模拟油田CO_2环境中的腐蚀实验[J].全面腐蚀控制, 2017, 31(04):72-74.
[3]丁楠,廖柯熹,张淳.湿气管道内腐蚀直接评价方法[J].管道技术与设备, 2013(03):42-44+52.
免责声明:本网站所转载的文字、图片与视频资料版权归原创作者所有,如果涉及侵权,请第一时间联系本网删除。
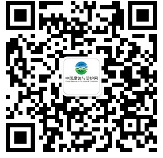
官方微信
《中国腐蚀与防护网电子期刊》征订启事
- 投稿联系:编辑部
- 电话:010-62316606-806
- 邮箱:fsfhzy666@163.com
- 中国腐蚀与防护网官方QQ群:140808414