摘要
综述了镍基高温合金上抗高温氧化的Pt改性β-(Ni,Pt)Al涂层和γ-γ′型涂层,重点介绍了Pt改性铝化物涂层制备工艺,不同工艺条件下涂层的微观结构,Pt增强铝化物涂层抗氧化性能的作用机理,Al对涂层高温氧化性能的影响,并从元素互扩散、相变、表面起伏等方面描述了涂层退化过程,最后对Pt改性铝化物涂层发展进行展望。
关键词: Pt改性铝化物涂层 ; 微观结构 ; 高温氧化性能 ; 研究展望
经历了上百年的技术突破和行业变革,目前航空发动机叶片材料以铁基、钴基和镍基高温合金为主,其中镍基高温合金在航空发动机热端部件的应用最为广泛[1,2],其主要成分为Ni、Cr、Co、Mo、W、Ta、Nb、Al等[3]。高温防护涂层技术随着高温合金在发动机服役温度不断提高[4]而快速发展,其中铝化物涂层以其优异的综合性能,及可以单独使用或作为热障涂层系统中的粘结层使用而得到广泛应用。制备铝化物涂层的工艺方法有很多种,包括包埋渗铝、气相渗铝、化学气相沉积 (CVD) 渗铝等[5]。包埋渗铝渗剂与样品表面直接接触,涂层内易引入杂质[6]。气相渗铝在涂层涂覆均匀性、工艺稳定性等方面存在着不足,且工艺参数难以控制[7]。CVD渗铝相比包埋渗铝和气相渗铝的优越性在于它能够适用复杂型腔及微小冷却通道表面渗铝,并且可通过调控反应参数 (反应温度、反应时间、反应气体和渗剂种类) 制备出不同结构、不同性能的 (改性) 铝化物涂层[8,9]。近年来,国内外研究者大多采用CVD制备铝化物涂层[10-15]。
然而单一铝化物涂层在长期高温氧化环境中表面易剥落,通过添加Pt、Si、Hf、Pd、稀土等元素制备改性铝化物涂层,以提高抗高温氧化性能[16-19]。在镍基高温合金上制备的Pt改性铝化物涂层已成功应用在航空发动机叶片[20-29],研究者仍不断探索涂层的抗高温氧化机理和退化过程,并不断优化涂层的成分、组织结构及制备工艺,以期进一步提高其抗高温氧化性能。本文对镍基高温合金上抗高温氧化的Pt改性β-(Ni,Pt) Al涂层和γ-γ‘型铝化物涂层重点进行阐述,并综述了其制备工艺及微观结构、氧化行为的研究现状及展望。
1 Pt改性铝化物涂层的制备过程及微观结构
1.1 制备过程
Pt改性的铝化物涂层制备过程一般包括四个步骤[15]。(1) 制备镀Pt层:采用电镀、熔盐电沉积或物理气相沉积 (PVD) 等方法在基体表面沉积一层Pt (3~10 μm);(2) 预扩散处理:对镀Pt后的样品进行真空退火,以提高Pt层与基体合金的结合力,同时降低样品表面Pt浓度;(3) 扩散渗铝:采用包埋渗铝、气相渗铝或CVD方法进行渗铝处理,引入Al形成Pt改性铝化物涂层;(4) 后续热处理 (根据工艺需要):进一步完成涂层的形成,提高基体合金与涂层的结合力,同时有助于基体合金恢复渗铝过程中损失的力学性能。通过调整预扩散处理和扩散渗铝的温度、时间以及渗铝工艺的类型,可获得传统的β-(Ni,Pt)Al涂层和新型的γ-γ’型涂层。
1.2 Pt改性铝化物涂层的微观结构
1.2.1 β-(Ni,Pt)Al涂层
传统的β-(Ni,Pt)Al涂层微观结构与单一铝化物涂层的微观结构相似。单一铝化物涂层根据制备过程中扩散机理不同,可分为向内生长型 (低温高活性) 渗铝和向外生长型 (高温低活性) 渗铝[30-32]。在向内生长型涂层制备过程中,涂层形成机制是通过Al原子向内扩散与Ni原子反应而生长的。涂层的微观结构如图1a所示[30],涂层由三层组成,外层和中间层由β-NiAl组成,外层含有大量细小的沉淀相,中间层为析出相;内层是互扩散区,该层分布有含β基体相的大量复杂沉淀相。在向外生长型涂层制备过程中,涂层形成机制是以基体合金表面为初始界面向外生长。涂层的微观结构如图1b所示[30],涂层由两层组成,外层由β-NiAl组成,内层互扩散区成分与向内生长型涂层互扩散区类似。
图1 单一铝化物涂层的典型微观结构[30]
制备向内生长型β-(Ni,Pt)Al涂层,通常包括两个步骤[33-36],(1) Al化处理:在相对较低的温度 (700~850 ℃) 下进行,将Al原子从反应室扩散进入到基体合金中;(2) 后续热处理:对渗铝样品进行高温 (通常高于1000 ℃) 热处理,使涂层中各种原子发生再分布形成最终的涂层组织。涂层的微观结构如图2所示[35,36],涂层由外层、中间层和互扩散区三层组成。互扩散区分布有大量复杂沉淀相,中间层有一些细小的析出相以及有一定量的Pt固溶在β-NiAl相中,外层富Pt层根据工艺条件不同有不同的微观结构。第一种情况如图2a所示,外层由单相ξ-PtAl2组成;第二种情况如图2b所示,外层为Pt固溶的单相β-NiAl结构;图2c所示为介于第一和第二种情况之间,外层由ξ和β相组成的两相组织。
图2 向内生长型的Pt改性铝化物涂层中的微观结构[35,36]
制备向外生长型β-(Ni,Pt)Al涂层通常是在1000 ℃以上一步进行,多采用气相渗铝或CVD渗铝方法[37-41]。涂层的微观结构如图3所示[42],涂层外层由Pt固溶的β-NiAl相和互扩散区 (与向内生长型类似) 两层结构组成,涂层表面呈网状结构。与向内生长型涂层相比,向外生长型涂层的外层β-(Ni,Pt)Al成分纯净,几乎不包含任何沉淀相,而且互扩散区较厚。
图3 向外生长型的Pt改性铝化物涂层中的微观结构[41]
1.2.2 Pt改性γ-γ‘型铝化物涂层
镍基高温合金基体含有一些难熔元素 (如Re、W、Mo),传统的β-(Ni,Pt)Al涂层中Al含量较高,在渗铝或服役过程中富含难熔元素的有害拓扑密堆积 (TCP) 相在基体合金中析出[42];同时涂层中较高的Al和较低的Ni含量使涂层与基体合金之间产生互扩散,形成二次反应区 (SRZ),导致基体合金沿晶胞边界开裂引起蠕变性能退化[43,44]。且在服役过程中,随着涂层中Al的消耗,涂层内部发生β-(Ni,Pt)Al向γ和γ′相的马氏体相变,从而引起体积变化,导致涂层表面产生“起伏”现象;当β-(Ni,Pt)Al作为热障涂层粘结层使用时[20,45],“起伏”现象产生的界面应力导致陶瓷层脱落[20]。为了克服β-(Ni,Pt)Al涂层存在的问题,近年发展了一种由γ和γ′相组成的新型Pt改性铝化物涂层,称为Pt改性γ-γ’型涂层,此涂层与基体合金的化学和机械相容性得到提高[46-49]。
制备Pt改性γ-γ′型涂层的方法与传统的β-(Ni,Pt)Al涂层相似,在基体合金表面制备一层Pt,不同的是渗铝过程中使用NaCl等稳定的活化剂,并适当地保持渗铝介质中的Al含量,使涂层的Al含量足够低 (通常为27%,原子分数),涂层中就会形成γ-γ′相结构[50]。渗铝过程中使用的活化剂是实现涂层γ-γ′相结构的关键,使用NH4X (X=Cl,Br,I) 作为活化剂会导致β-NiAl相的形成,因为在渗铝的初始阶段,Al的沉积速度很高[51]。图4为一种典型的Pt改性γ-γ′型涂层的微观结构[52],该涂层呈两层结构,类似于向外生长型的β-(Ni,Al)Pt涂层。与β-(Ni,Al)Pt涂层不同的是,γ-γ′型涂层的外层主要由γ′相组成,互扩散区由γ和γ′相组成,由于难熔元素在γ′相中的溶解度相对γ相较低,沉淀相主要在互扩散区的γ′相中形成。此外,与β-(Ni,Al)Pt涂层相比,由于难熔元素在γ′中的溶解度比在β-NiAl相中的溶解度高,所以γ-γ′型铝化物涂层的互扩散区中形成了更少的沉淀相。
图4 镍基高温合金上Pt改性γ-γ′型铝化物涂层典型微观结构[52]
2 Pt改性铝化物涂层的高温氧化行为
2.1 Pt对抗氧化性能的作用
Pt可以显著提高铝化物涂层抗高温氧化性能,目前Pt的主要作用机理包括以下几个方面。(1) Pt的钉扎作用:在扩散型[53]和MCrAlY (M=Fe/Ni/Co) 型[54]涂层中,Pt形成的氧化物通过钉扎生长从涂层进入基体,使涂层和基体界面结合更加紧密,增强了Al2O3保护膜的粘附性,提高了铝化物涂层抗高温氧化性能。(2) 影响元素扩散:Pt能促进Al的选择性氧化形成Al2O3保护膜,具体表现[55,56]为Pt促进Al从基体扩散到涂层中,补充Al的选择性氧化所需的Al;由Ni-Al-Pt三元相图[48]和第一性原理研究[57]结果可知,在保持相中Al含量不变的情况下,Pt能取代γ′-Ni3Al相中的Ni,减少β-(Ni,Pt)Al相转化为在高温氧化环境中形成氧化膜易剥落的γ‘-Ni3Al相;此外Pt能抑制Al的内扩散、Ni的外扩散、难熔元素Mo、V、W等的外扩散,维持涂层中所需的Al、Ni,降低难熔元素在涂层表面形成氧化物,得到更加纯净的Al2O3保护膜[58-61]。(3) 抑制涂层界面孔洞的形成:基于第一性原理与密度泛函理论的研究结果表明,Pt能降低β-NiAl中点缺陷和缺陷群形成所需的能量来提高涂层整体扩散系数,增加Al扩散进入β-NiAl中的几率,补充因元素互扩散造成Al空位所需的Al,从而抑制涂层界面Al2O3保护膜形成孔洞[62];Pt还能增加氧化物和金属之间的接触面积,抑制涂层界面孔洞的形成,减少Al2O3保护膜的剥落[63]。此外,在高温环境中1 mg/L S就会从涂层中扩散至氧化膜界面处富集而产生微孔洞[64],使得氧化膜结构疏松多孔以及降低氧化膜粘附性。对于Pt改性铝化物涂层,Pt能减少一定量的S在界面上的偏析[65,66],改善涂层粘附性。但S含量过高仍会导致Al2O3保护膜粘附性变差[67]。
2.2 Al在高温氧化行为中的影响
在Pt改性铝化物涂层中Al形成Al2O3保护膜及增加涂层厚度,适当增加Al浓度能提高涂层的抗高温氧化性能。β-(Ni,Pt)Al涂层 (高活性渗铝制备的RT-22涂层) 1050 ℃高温循环氧化试验结果表明,含52% (原子分数) Al的涂层抗高温氧化性能优于含30% (原子分数) Al的涂层[68];低活性渗铝制备的β-(Ni,Pt)Al涂层1200 ℃高温循环氧化试验结果表明,随着Al浓度的增加涂层的厚度不断增加,当Al浓度达到一定范围时涂层的抗高温氧化性能最佳,超过此范围涂层太厚不利于叶片实际使用,且涂层的抗高温氧化性能不再增加[69]。
2.3 Pt改性铝化物涂层的退化
虽然Pt改性铝化物涂层的综合性能较稳定,但长期暴露在高温氧化环境中,涂层的抗高温氧化性能仍会发生退化,以下为涂层退化的主要机理及过程。
2.3.1 元素互扩散
渗铝后,涂层中的Al含量比基体中的Al含量高,Ni含量则较低,因而涂层与基体之间形成浓度梯度,导致Al、Ni和其他元素在涂层和基体之间发生相互扩散。CM247 (LC) 镍基高温合金上高活性渗铝制备的Pt改性铝化物涂层1100 ℃恒温氧化试验结果表明[43],Ni从基体向外扩散到涂层表面,导致互扩散区厚度增加,从而增加整个涂层的厚度,涂层外层Al2O3保护膜不够致密是涂层退化的主要原因。CMSX-4镍基单晶高温合金基体上采用高活性渗铝制备的不同镀Pt层的SS82A涂层和RT22涂层,1050 ℃高温氧化试验结果表明[70],Al从互扩散区向基体表面扩散,导致Co,Cr等难熔金属在互扩散区析出,且Ni从基体向涂层表面扩散,涂层中的β-NiAl相转变为γ′-Ni3Al相,导致涂层发生退化。相比于单一铝化物涂层,Pt改性铝化物涂层中元素在互扩散区层互扩散有所改善,且针尖状TCP析出量显著减少[71,72]。
2.3.2 相变
在高温氧化环境中,伴随着氧化温度的改变和Al的消耗,涂层中的物相会发生以下两种相变。第一种相变是由温度引起的[73],采用CVD渗铝工艺制备的β-(Ni,Pt)Al涂层1150 ℃×100 h恒温氧化实验结果发现,涂层组织由B2-CsCl结构的单相β相完全转变为fctL10结构的马氏体相,这种相变使涂层表面起伏开裂,导致涂层发生退化。第二种相变是由Al消耗引起的[74],随着Al向基体内扩散,同时Al向外扩散形成Al2O3保护膜,涂层中的Al含量不断降低,使β-(Ni,Pt)Al相转变为γ′-(Ni,Pt)3Al相,导致涂层表面部分Al2O3保护膜剥落,涂层退化。
2.3.3 涂层表面起伏
文献[45,63,75-77]对Pt改性铝化物涂层的表面起伏现象进行了研究。涂层表面产生起伏的原因主要有:其一,由于涂层中Al的消耗和难熔元素从基体扩散进入涂层形成氧化物,导致β-(Ni,Pt) Al相的分解,Al2O3保护膜剥落,涂层局部体积发生变化 (图5);其二,高温氧化周期长、氧化速率高、涂层表面粗糙度大等因素也会使涂层表面起伏;其三,涂层组织由B2-CsCl结构的单相β相完全转变为fctL10结构的马氏体相,也会使涂层表面产生起伏;其四,涂层与基体的热膨胀系数差异而产生的热应力成为涂层表面起伏的驱动力。近年来关于涂层表面起伏新的研究结果表明,Pt改性铝化物涂层中由于Pt的加入形成具有良好致密性的Al2O3保护膜,且当涂层中添加Hf、Y等元素共改性时,涂层氧化速率明显降低,涂层与基体的结合力显著增加,涂层表面起伏得到很好的改善[78]。
图5 涂层氧化过程中主要扩散通量以及导致起伏和孔洞形成的微观结构[73]
2.3.4 涂层退化的其他变化
高温氧化环境中,高活性渗铝制备的Pt改性铝化物涂层中,β-(Ni,Pt)Al相内有细小的NiO、CoO等氧化物析出,这些析出物在氧化过程中有的会溶解在Al2O3保护膜中导致其致密度下降,有的会长大粗化导致涂层表面开裂[33]。此外。随着氧化过程中Al、Ni和其他元素在基体和涂层之间发生相互扩散,由于基体和涂层两侧原子扩散通量不相等,导致在基体和涂层界面附近产生柯肯达尔孔洞[45]。
3 结论与展望
本文综述了在镍基高温合金上制备的Pt改性β-(Ni,Pt)Al涂层和γ-γ’型涂层制备工艺、微观结构和抗高温氧化性能的研究进展。通常,γ-γ‘型涂层较β-(Ni,Pt)Al涂层含有更少的Al,且γ-γ’型涂层与基体合金的化学和力学相容性较好。在β-(Ni,Pt)Al涂层中,根据渗铝过程中生长机理的不同,可分为向内生长型涂层和向外生长型涂层。其次,介绍了Pt增强铝化物涂层抗氧化性的作用机理,Al对涂层抗氧化性能的影响,并从元素互扩散、相变、表面起伏等方面描述了涂层退化过程。
为了进一步探究Pt改性铝化物涂层,未来的研究工作重点在于:(1) 优化镀Pt工艺,减少镀Pt时杂质的引入;采用PVD方法镀Pt,完善CVD渗铝过程中可调控参数,制备出高纯的Pt改性铝化物涂层。
(2) 研究Pt结合活性等元素进行多元改性,探索其涂层的微观结构、抗高温氧化性能及作用机理。
(3) 不断探究新型Pt改性γ-γ‘型涂层的作用机理,涂层的退化过程;并不断优化涂层的成分及制备工艺,以期进一步提高涂层的抗高温氧化性能。
免责声明:本网站所转载的文字、图片与视频资料版权归原创作者所有,如果涉及侵权,请第一时间联系本网删除。
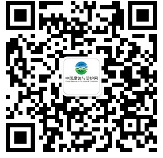
官方微信
《中国腐蚀与防护网电子期刊》征订启事
- 投稿联系:编辑部
- 电话:010-62316606-806
- 邮箱:fsfhzy666@163.com
- 中国腐蚀与防护网官方QQ群:140808414