摘要
采用电化学测试技术以及浸泡实验对含硫化物夹杂的铁基块体非晶合金在HCl溶液中的腐蚀行为进行了研究。结果表明,该非晶合金在不同浓度以及不同温度的HCl溶液中均呈现出明显的钝化特征,其耐蚀性能随着溶液浓度和温度的升高而逐渐降低;Nyquist曲线均只有一个容抗弧,电极系统的Faraday过程均由电极电位控制。浸泡腐蚀后的SEM形貌特征表明:硫化物颗粒对铁基非晶合金的腐蚀无明显影响,未诱发明显点蚀。
关键词: 硫化物夹杂 ; 铁基非晶 ; 耐蚀性能 ; HCl溶液
铁基块体非晶合金以其优异的软磁性能、高强度、高硬度,尤其是高耐蚀性而广为人知,并且被认为是在工业侵蚀环境中应用最有前景的潜力材料之一[1,2]。自Lu等[3]的开创性工作以来,已证实多种铁基非晶合金的耐蚀性可以与不锈钢媲美。Zohdi等[4]研究了铁基非晶及纳米晶合金在模拟人体环境中的腐蚀行为,结果表明二者的耐蚀性能均高于316L不锈钢,而铁基非晶的耐蚀性能显著优于铁基纳米晶合金;陈庆军等[5]研究了块体非晶合金Fe41Co7Cr15Mo14C15B6Y2部分晶化后的腐蚀行为,结果表明该合金在未晶化前的耐蚀性能最好,而部分晶化后,其耐蚀性能呈现降低的趋势。Botta等[6]研究了化学成分对Fe基非晶合金在酸性、中性以及碱性溶液中腐蚀性能的影响,表明合金成分对铁基非晶合金的耐蚀性能起着至关重要的作用;含Cr的FeCrNiB合金因形成了宽的钝化区间而拥有最好的耐蚀性能。Li等[7]研究了添加不同含量微量元素Mo的 (Fe0.76Si0.096B0.084P0.06)100-xMox块体非晶合金在1 mol/L H2SO4溶液中的腐蚀行为,表明随着微量元素Mo的添加,非晶合金的耐蚀性得到了显著的提升。Souza等[8]对Fe-M-B-Cu(M=Zr,Nb,Mo) 非晶合金的腐蚀行为进行了研究,显示添加Nb的非晶合金耐蚀性最好,而只添加了Mo的耐蚀性最差,组合添加Nb和Mo的耐蚀性在二者之间。通常认为非晶合金的高耐蚀性主要归因于两点[9]:(1) 化学及结构均匀性,几乎没有容易遭受化学侵蚀的晶粒、晶界、位错以及偏析等;(2) 合适的化学成分,如钝化元素Cr、Mo、Mn和P等,能在材料遭遇腐蚀时,快速形成钝化膜阻碍腐蚀的进行。为降低制备成本,诸多科研工作者尝试采用工业原材料制备铁基块体非晶合金[10,11]。但是,原材料的采用不可避免地会引入各类杂质,必然影响非晶成分的均匀性,进而影响其耐蚀性。当前,铁基非晶合金腐蚀行为的研究主要集中于合金元素、纳米化、部分晶化对其腐蚀性能及行为的影响等方面,鲜有关于含夹杂物铁基非晶合金腐蚀行为的研究,且不清楚夹杂对非晶合金腐蚀行为的影响规律。
鉴于此,本文以采用工业原材料制备的含硫化物夹杂的铁基块体非晶合金Fe66.6C7.1Si3.3B5.5P8.7Cr2.3Mo2.5Al2.0Co1.0S1.0为研究对象,探讨了HCl溶液浓度及其温度对该非晶合金的腐蚀行为影响,并且对硫化物夹杂对该非晶合金腐蚀行为的影响进行了分析。
1 实验方法
采用真空电弧熔炼炉将工业纯铁及其合金炼制成名义成分为Fe66.6C7.1Si3.3B5.5P8.7Cr2.3Mo2.5Al2.0Co1.0S1.0 (原子分数,%) 的合金锭,原材料化学成分如表1所示。为保证成分均匀,每个合金锭需进行多次熔炼。然后在纯氩气保护下,采用水冷铜模吸铸法制备出直径约为2 mm的圆棒。采用D8ADVANCE型X射线衍射仪 (XRD、CuKα) 对所铸合金的相组成进行表征,利用扫描电子显微镜 (SEM,Hitachi,S-2500C) 和能谱仪 (EDS,Hitachi,S-2500C) 分析非晶棒材的显微组织及成分。
表1 工业原材料的化学成分表
采用电化学测试设备CHI 660E工作站 (三电极体系:辅助电极-Pt、参考电极-饱和甘汞电极SCE、工作电极-待测合金试样) 对该铁基块体非晶合金的电化学腐蚀行为进行研究。为使开路电位稳定,每次测试前将工作电极浸泡在HCl溶液中30 min。所测动电位极化曲线扫描速率为1 mV/s,选取阳极极化时的钝化区电位作为恒电位阳极极化曲线的初始电位,电化学阻抗谱初始电位为开路电位,交流正弦激励信号幅值为5 mV,测试频率范围105~10-2 Hz。室温条件下,将非晶铸棒试样放置于0.5 mol/L的HCl溶液中浸泡7 d,采用SEM观察该非晶合金试样所含硫化物颗粒的腐蚀形貌变化。
2 结果与讨论
图1所示为所铸试样的XRD谱。可以清楚地看到一个“馒头峰”,没有其它晶体衍射峰,表明铸棒为非晶结构。图2是非晶铸棒显微断口形貌,显然在断口中可以清楚地看到,在基体中有圆形颗粒出现,EDS分析结果表明夹杂的颗粒为 (Fe,Al)S相,如图3所示。由于所含夹杂颗粒比例极低 (<5%,质量分数),在上述XRD谱中并未被检测出。
图1 块体非晶铸棒的XRD谱
图2 块体非晶铸棒断口形貌和内部A区放大图
图3 夹杂颗粒的EDS分析结果
图4是非晶铸棒在不同浓度的HCl溶液中的动电位极化曲线。显然非晶铸棒在不同浓度溶液中均表现出高的自腐蚀电位Ecorr、低的自腐蚀电流密度Icorr和宽的钝化区间Epit-Epass;当HCl溶液溶度为0.1 mol/L时,自腐蚀电流密度为9.57 μA·cm-2;随着溶液浓度的增加,自腐蚀电流密度逐渐增大,4 mol/L时为524.81 μA·cm-2。钝化电流也呈现出随溶液浓度升高,不断增大的趋势,具体数值见表2。此外,自腐蚀电位、钝化电位和过钝化电位随浓度变化均未表现出明显的变化。钝化区间宽度高达1.0 V,表明具有强的自钝化能力。通常,化学成分是决定材料腐蚀性能的主要因素,适度添加钝化元素能促进合金的自发钝化,进而改善合金的耐蚀性能[12]。王莉等[13]认为在腐蚀过程中,含Cr等致钝元素的非晶合金能快速形成富含Cr的氧化物或氢氧化物,覆盖在合金表面上,进而阻碍阳极的溶解。诸多研究表明非金属夹杂物是诱发点蚀的最主要因素[14,15]。然而在阳极极化过程中,硫化物夹杂并未引起腐蚀电流的波动。为进一步证实这一现象,选取动电位极化曲线钝化区电位500 mV作为初始电位,对非晶铸棒的恒电位阳极极化条件下电流密度的演变过程进行测试 (见图5)。可以看到,在腐蚀的初始阶段,非晶铸棒的腐蚀电流密度均随时间的延长而急剧下降,最终达到一个相对稳定的电流密度值。这是因为在腐蚀初期,钝化膜的形核及生长比其溶解过程更快;而随着时间的延长,瞬时电流达到一个相对稳定的状态则是因为形成的钝化膜在长时间的腐蚀过程中未发生破裂[16]。当HCl浓度为0.1 mol/L时,稳态电流密度约为20 μA·cm-2,随着HCl溶液浓度增大,稳态电流密度也逐渐增大,最终在4 mol/L时为180 μA·cm-2。这是因为随着HCl溶液浓度的增大,钝化膜的松散程度增加,其孔隙率也越大,进而促使稳态电流密度增大[9]。此外,从图5还可以看到,在长时间的腐蚀过程中,均未见电流突然变大的现象,说明硫化物夹杂物并未诱发明显的点蚀,与动电位极化曲线测试结果一致。
图4 非晶铸棒在不同浓度的HCl溶液中的动电位极化曲线
表2 非晶铸棒在不同浓度的HCl溶液中动电位极化曲线和电化学阻抗谱的电化学参数拟合结果
图5 非晶铸棒在不同浓度HCl溶液中的恒电位阳极极化曲线
图6所示为非晶铸棒在不同浓度HCl溶液中的电化学阻抗谱 (EIS) 和相应的等效电路。可以看到,实测曲线与拟合曲线基本吻合,所有Nyquist曲线均由单一容抗弧构成,即只有一个时间常数,表明其电极系统的Faraday过程主要由电极电位控制。此外,随着溶液浓度的增加,容抗弧曲率半径呈现逐渐减小的趋势,表明非晶铸棒的耐蚀性能也逐渐降低。图6b所示等效电路由溶液电阻Rs、电化学反应电荷转移电阻Rp、常相位角元件CPE (即双电层电容) 组成。由等效电路拟合的部分腐蚀参数见表2,可以看到随HCl溶液浓度的增加,Rs和Rp均逐渐减小,Rs的减小是因为溶液中参与导电的离子增多[11],而Rp的减小则是腐蚀介质对钝化膜的侵蚀作用所致。当HCl溶液浓度为0.1 mol/L时,CPE为14.28 F·cm-2;随着溶液浓度的增加,其值不断增大,表明非晶铸棒表面的钝化膜孔隙开始逐渐增多[17]。较高的Rp值和较低的CPE值表明非晶铸棒拥有良好的耐蚀性能。研究认为点蚀诱导期的阻抗谱特征由高频容抗弧与低频感抗弧组成[18]。而非晶铸棒的阻抗谱均由单一容抗弧组成,这也证实了上述硫化物未诱发点蚀的结论。
图6 非晶铸棒试样在不同浓度HCl溶液中的电化学阻抗谱及其等效电路
为进一步研究该非晶铸棒的腐蚀行为,对其在不同温度1 mol/L HCl溶液中的耐蚀性能进行了电化学测试。图7为非晶铸棒的动电位极化曲线,可以看到在不同温度下的HCl溶液中非晶铸棒也表现出高的Ecorr、较低的Icorr和宽的Epit-Epass。当温度为20 ℃时,Icorr为33.88 μA·cm-2;随着环境温度的增加,Icorr逐渐增大,在60 ℃时高达125.31 μA·cm-2。钝化电流密度Ipass也随环境温度的升高,而不断增大,Epit-Epass略有变窄,反映出非晶铸棒的耐蚀性能有所降低,相关腐蚀参数如表3所示。因为非晶铸棒在HCl溶液中过电位减小,加速了腐蚀过程的进行[19]。然而,Ecorr随温度变化却无明显变化。从动态极化曲线测试结果还可以看到,随着HCl溶液浓度的增大,非晶铸棒的钝化能力也呈现出下降的趋势。此外,在阳极极化的钝化区未出现电流急剧增大的现象,说明硫化物夹杂对非晶铸棒在不同温度下的HCl溶液中的腐蚀行为几乎没有影响。图8为该非晶铸棒在不同环境温度下的1 mol/L HCl溶液中的恒电位阳极极化条件下电流密度的演变过程,显然在不同温度的恒电位阳极极化曲线基本相似,且均未见电流暂态峰,进一步证实了上述结论;20 ℃时,在腐蚀初始阶段,腐蚀电流密度急剧降低,达到约75 μA·cm-2时保持基本稳定,这反映了钝化膜的形成与生长的过程[20];而在40和60 ℃时,腐蚀电流密度降低至某一值后又分别急剧增大至717和1420 μA·cm-2后保持基本稳定。这可能是因为化学吸附以及氧化反应通常为放热反应,温度越低,越有利于吸附过程及氧化反应,从而更有利于形成钝化膜[21]。此外,在40和60 ℃时的HCl溶液侵蚀性较强,非晶铸棒表面开始生成的钝化膜不足以阻碍HCl溶液的侵蚀,钝化膜迅速破裂,之后随着进一步的侵蚀,非晶铸棒快速进入二次钝化,形成稳定的钝化膜,从而电流密度 (Iss) 保持相对稳定,这也充分体现了该非晶铸棒极强的自钝化能力[22]。
图7 非晶铸棒试样在不同温度的HCl溶液中的动电位极化曲线
表3 非晶铸棒试样在不同温度下HCl溶液中动电位极化曲线和电化学阻抗谱的部分拟合结果
图8 非晶铸棒试样在不同温度的HCl溶液中的恒电位阳极极化曲线
图9所示为非晶铸棒在20,40以及60 ℃时的EIS结果。可以看到,实测曲线与拟合曲线基本吻合,3条Nyquist曲线也由一个容抗弧组成,表明电极系统的Faraday过程主要由电极电位控制;容抗弧的曲率半径随温度的升高而变小,则说明极化电阻越来越小,非晶的耐蚀性也越差。其等效电路如图6b所示,说明非晶铸棒在不同浓度和不同温度的HCl溶液中的腐蚀机理均未发生改变。由等效电路所拟合的腐蚀参数详见表3。显然,随着环境温度的升高,CPE的阻值和Rp均逐渐减小,反映出非晶铸棒的耐蚀性能变差。此外,Nyquist曲线只有一个容抗弧,说明硫化物夹杂没有诱发点蚀,这与之前测试结果一致。
图9 非晶铸棒试样在不同温度的HCl溶液中的EIS谱
图10所示为室温条件下,铁基块体非晶合金铸棒在0.5 mol/L的HCl溶液中浸泡0,24,72和168 h后的SEM像。可以看到:浸泡前 (图10a),非晶基体的表面光滑平整,还有两个直径约为数微米硫化物颗粒紧密镶嵌在非晶基体内,以及与硫化物颗粒相连呈白色亮线的剪切带;随着溶液侵蚀时间的延长,剪切带中的局部应变集中致使裂纹优先萌生于剪切带边界处,并顺延着剪切带向外,以及向宽度和厚度方向扩展,裂纹尺寸逐渐增大。与此同时,垂直于剪切带方向的粒子边缘处也逐渐有细小裂纹萌生;在浸泡至168 h时,裂纹已十分密集,基本贯穿整个粒子。纵观整个腐蚀过程,除浸泡至24 h时,硫化物发生了轻微局部腐蚀外,没有观察到因硫化物夹杂的存在而出现的点蚀坑,表明硫化物颗粒未成为点蚀萌生的诱发源。考虑到该非晶铸棒成分和结构均匀,除硫化物颗粒外并无其他明显的区域特征,裂纹可能出现于非晶铸棒的腐蚀产物层,而其形成是由于试样的干燥,且进一步暴露于高真空的扫描电镜样品室内所致[16]。
图10 非晶铸棒试样在0.5 mol/L HCl溶液中浸泡不同时间后的腐蚀形貌
3 结论
(1) 铁基非晶合金在不同浓度及温度的HCl溶液中均呈现出较为优异的耐蚀性能,但其耐蚀性能随HCl溶液浓度增加以及温度的升高而降低。
(2) 铁基非晶合金在不同浓度及温度的HCl溶液中的腐蚀机理一致,电极系统的Faraday过程主要由电极电位控制。
(3) 在HCl溶液中浸泡过程中,硫化物夹杂对铁基非晶合金的腐蚀行为无明显影响,未诱发明显点蚀。
参考文献
[1] Inoue A, Shen B L, Takeuchi A.Fabrication, properties and applications of bulk glassy alloys in late transition metal-based systems[J]. Mater. Sci. Eng., 2006, A441: 18
[2] Hashimoto K.2002 W.R. Whitney award lecture: In pursuit of new corrosion-resistant alloys[J]. Corrosion, 2002, 58: 715
[3] Lu Z P, Liu C T, Thompson J R, et al.Structural amorphous steels[J]. Phys. Rev. Lett., 2004, 92: 245503
[4] Zohdi A, Bozorg M, Arabi R, et al.Corrosion performance and metal ion release of amorphous and nanocrystalline Fe-based alloys under simulated body fluid conditions[J]. Mater. Lett., 2013, 94: 193
[5] Chen Q J, Yu H Y, Zhou X L, et al.Effect of crystalline behavior on corrosion resistance of Fe-based bulk amorphous alloy[J]. Hot Work. Technol., 2012, 41(8): 1(陈庆军, 余慧燕, 周贤良等. 晶化行为对Fe基块体非晶合金腐蚀性能的影响[J]. 热加工工艺, 2012, 41(8): 1)
[6] Botta W J, Berger J E, Kiminami C S, et al.Corrosion resistance of Fe-based amorphous alloys[J]. J. Alloy. Compd., 2014, 586: S105
[7] Li X, Qin C L, Kato H, et al.Mo microalloying effect on the glass-forming ability, magnetic, mechanical and corrosion properties of (Fe0.76Si0.096B0.084P0.06)100-xMox bulk glassy alloys[J]. J. Alloy. Compd.,2011, 509: 7688
[8] Souza C A C, May J E, Bolfarini L, et al. Influence of composition and partial crystallization on corrosion resistance of amorphous Fe-M-B-Cu(M=Zr, Nb, Mo) alloys[J]. J. Non-Cryst. Solids, 2001, 284: 99
[9] Wang Y, Zheng Y G, Wang J Q, et al.Passivation behavior of Fe-based amorphous metallic coating in NaCl and H2SO4 solutions[J]. Acta Metall. Sin., 2015, 51: 49(王勇, 郑玉贵, 王建强等. 铁基非晶涂层在NaCl和H2SO4溶液中的钝化行为[J]. 金属学报, 2015, 51: 49)
[10] Wang S L, Cheng J C, Yi S H, et al.Precipitation of sulfide particle in situ formed in Fe-based bulk metallic glass[J]. Foundry, 2013, 62: 491(王善林, 成京昌, 李承勋等. 大块铁基非晶中硫化物析出行为研究[J]. 铸造, 2013, 62: 491)
[11] Li H X, Lu Z P, Yi S.Estimation of the glass forming ability of the Fe-based bulk metallic glass Fe68.8C7.0Si3.5B5.0P9.6Cr2.1Mo2.0Al2.0 that contains non-metallic inclusions[J]. Met. Mater. Int., 2009, 15: 7
[12] Li G, Huang L, Dong Y G, et al.Corrosion behavior of Fe65.5Cr4Mo4Ga4P12C5B5.5 bulk amorphous alloys in different media[J]. Sci. Sin. Phys., Mech. Astron., 2010, 40: 717(李工, 黄蕾, 董雁国等. Fe65.5Cr4Mo4Ga4P12C5B5.5块体非晶合金不同介质中的腐蚀行为[J]. 中国科学: 物理学力学天文学, 2010, 40: 717)
[13] Wang L, Chao Y S.Corrosion behaviors of bulk amorphous Fe41Co7Cr15Mo14C15B6Y2 alloy in NaOH solution[J]. J. Funct. Mater., 2010, 41: 1849(王莉, 晁月盛. 铁基块体非晶合金在NaOH溶液中的腐蚀行为[J]. 功能材料, 2010, 41: 1849)
[14] Qin H P, Chen H T, Lang Y P, et al.Mechanism of induced pitting corrosion in 439M ferritic stainless steel[J]. Iron Steel, 2015, 50(9): 81(覃怀鹏, 陈海涛, 郎宇平等. 439M铁素体不锈钢点蚀诱发机理[J]. 钢铁, 2015, 50(9): 81)
[15] Zhang C Y, Zhang Q, Li J G, et al.Micro-corrosion test research on pitting initiation site of the inclusions of carbon steel and low alloy steel in chlorine ion solution[J]. Metall. Anal., 2014, 34(1): 22(张春亚, 张奇, 李继高等. 碳钢及低合金钢在氯离子溶液中夹杂物诱发点蚀位置显微腐蚀实验探讨[J]. 冶金分析, 2014, 34(1): 22)
[16] Wang Y, Jiang S L, Zheng Y G, et al.Electrochemical behaviour of Fe-based metallic glasses in acidic and neutral solutions[J]. Corros. Sci., 2012, 63: 159
[17] Guo R Q, Zhang C, Yang Y, et al.Corrosion and wear resistance of a Fe-based amorphous coating in underground environment[J]. Intermetallics, 2012, 30: 94
[18] Hu L H.Pitting features of 1Cr18Ni9Ti stainless steel in the NaCl solution [D]. Nanchang: Nanchang Hangkong University, 2006(胡丽华. 1Cr18Ni9Ti不锈钢在NaCl介质中的点蚀特征研究 [D]. 南昌: 南昌航空工业学院, 2006)
[19] Zuo Y, Xiong J P.Engineering Materials and Corrosion Resistance[M]. Beijing: China Petrochemical Press, 2008: 12(左禹, 熊金平. 工程材料及其耐蚀性 [M]. 北京: 中国石化出版社, 2008: 12)
[20] Lekatou A, Marinou A, Patsalas P, et al.Aqueous corrosion behaviour of Fe-Ni-B metal glasses[J]. J. Alloy. Compd., 2009, 483: 514
[21] Liu D X.The Corrosion and Protection of Materials [M]. Xi'an: Northwestern Polytechnical University Press, 2006: 108(刘道新. 材料的腐蚀与防护 [M]. 西安: 西北工业大学出版社, 2006: 108)
[22] Zhou Q C, Xu N X, Shi S T.Study on the passivation film of the nickel surface by ellipsometry[J]. J. Chin. Soc. Corros. Prot., 1990, 10: 287(周庆初, 徐乃欣, 石声泰. 椭圆偏振法研究镍表面的钝化膜[J]. 中国腐蚀与防护学报, 1990, 10: 287)
免责声明:本网站所转载的文字、图片与视频资料版权归原创作者所有,如果涉及侵权,请第一时间联系本网删除。
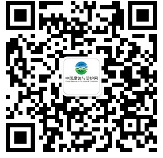
官方微信
《中国腐蚀与防护网电子期刊》征订启事
- 投稿联系:编辑部
- 电话:010-62316606-806
- 邮箱:fsfhzy666@163.com
- 中国腐蚀与防护网官方QQ群:140808414