摘要
对微米级SiC/Ni-Co-P复合镀层用作代铬镀层进行了研究。采用恒电流沉积的方法在钢片上成功制备了微米级SiC/Ni-Co-P复合镀层。采用单因素实验分别讨论电镀液组成对镀层宏观形貌、微观形貌、复合量、硬度等的影响,获得硬度 (HV) 为646.11的微米级SiC/Ni-Co-P复合镀层;研究了不同表面处理的微米级SiC对镀层形貌及微粒复合量的影响,结果显示,表面强负电性的微米级SiC参与电镀得到的微米级SiC/Ni-Co-P复合镀层,表面微裂纹少且更加平整无孔隙,微粒含量较表面带正电性和弱电性的SiC更高。探究了微米级SiC通过电沉积的方式进入镀层的过程及界面行为,解释了微米级碳化硅表面处理对其进入镀层的影响。
关键词: 碳化硅-镍基复合材料 ; 碳化硅改性 ; 镍基合金电沉积 ; 碳化硅含量
传统的电镀铬技术通常采用六价铬 (铬酸) 作为镀液的主要成分。六价铬镀层具有光亮度好、硬度高、耐热性好、耐磨性好等特点,在大气的条件下,能长久地保持原来的光泽;在酸、碱中都具有很高的化学稳定性,是一种理想的镀层,在装饰性和功能性方面都得到了满意的效果[1-3]。但与此同时,六价铬电镀有着无法避免的缺点[4]:阴极电流效率低,仅为8%~16%,即有将近90%的能量损耗,同时析出的大量氢气所形成的的酸雾,对环境和工人的健康造成损害;六价铬自然降解能力差,会在生物体内蓄积,造成长期危害。
随着人们环保意识的增强,寻求了诸多替代铬镀层的工艺。代铬镀层主要分为装饰性代铬镀层和代硬铬镀层两类[5]。常见的有三价铬电镀[6-8]、锡基合金电镀[5]、镍基合金电镀[9-11]、复合电镀[12,13]等工艺。其中,三价铬电镀具有低毒、低污染的优点,无铬雾溢出,但三价铬镀层的厚度有限,电镀一定时间后,镀件表面的镀层便不会再增厚;锡基合金镀层的外观与铬镀层相似,耐蚀性优于普通铬镀层,但锡基合金镀层的硬度普遍较低,不适合代硬铬;目前常用于替代硬铬镀层是复合镀,复合镀是由合金-第二相微粒共沉积在镀件表面。复合镀层的制备方法可分为3类:复合电沉积技术,复合化学沉积技术和复合电刷镀技术。复合电沉积技术作为新型电沉积技术,有着广泛的应用前景。常用于复合电沉积的增强体有金刚石[14]、Si3N4[15]、Al2O3[16]、WC[17]、SiC[18]等微粒,可根据镀层不同的用途选用不同的增强体。
本文提出了在钢材表面电沉积复合镀微米级SiC/Ni-Co-P合金镀层替代铬镀层。其中,Ni-Co-P合金基体具有优良的耐磨性和耐腐蚀性,在镀层中添加Co这一合金成分有助于细化晶粒,降低摩擦因数,提高合金镀层的耐磨损性能。通过优化镀液配方,在钢基材表面获得具有一定形貌分布特征的微米级SiC/Ni-Co-P复合镀层。由于微米级SiC难以复合进入镀层,本文通过添加不同表面活性剂对微米级SiC表面进行改性,系统地研究了改性后的微米级SiC对复合镀层的影响。
1 实验方法
电沉积基础溶液为含钴离子的硫酸镍电镀液其成分 (g/L)为:六水硫酸镍200~350,六水氯化镍20~40,七水硫酸钴20~40,硼酸30,次亚磷酸钠2。每片基材电镀所用的镀液均为300 mL批量新配制的镀液,电镀时,镀液中的各个阳离子含量与实际进入镀层的阳离子量相差大,短时间内电镀可将镀液中阳离子含量视为不变。阳极采用纯镍阳极,阴极采用9Cr2Mo钢基体 (2 cm×3 cm),阴极电流密度为2 A/dm2。第二相颗粒为上海杳田新材料科技有限公司生产的纯度99.9%、粒径8 μm的微米级SiC。微米级SiC经过水洗、酸洗 (质量分数10%的硫酸,50 ℃,20 min)、水洗、酸洗 (体积分数20%的盐酸,30 min)、水洗和表面处理 (表面活性剂10 mg/L,60 min) 后加入基础溶液,搅拌超声1 h,制备出各自添加阳离子表面活性剂十六烷基三甲基溴化铵 (CTAB)、阴离子表面活性剂十二烷基苯磺酸钠 (SDBS)、非离子表面活性剂聚乙烯吡咯烷酮 (PVP) 的SiC悬浮镀液。在70 ℃下,镀液的pH值保持在5.0~5.5之间进行电沉积。在电沉积过程中,溶液以250 r/min的速度不断进行磁力搅拌。在研究每个条件的影响时,只改变条件,固定其他条件不变。
采用Zetasizer粒度电位仪对碳化硅微粒进行分散能表征,测量其粒径分布和Zeta电位;通过宏观形貌观察,检查镀层的宏观结合力,观察是否有起皮、剥落、毛刺、烧焦等现象;检查镀层的表面均匀程度和表面色泽;利用水冷法 (从200 ℃至室温) 对试样进行热震稳定性测试,记录试样表面镀层变化情况;使用ZEISS-SUPRA55场发射扫描电子显微镜 (SEM) 对镀层微观形貌进行分析;使用自带的能谱仪 (EDS) 表征镀层元素含量。
2 实验结果
2.1 微米级SiC/Ni-Co-P复合镀层的影响因素
2.1.1 硫酸镍含量的影响
3组实验中硫酸镍浓度分别为250、300和350 g/L时对镀层的外观、微观形貌、镀层结合力的影响如图1所示。经过水冷法测试,3个样品的镀层并未出现脱落及起皮等现象,镀层结合力良好。镀层的宏观形貌相对均匀。
图1 不同硫酸镍浓度镀层的表面及SEM形貌
2.1.2 氯化镍含量的影响
氯化镍在镀液中起到了阳极活化剂的作用。分别研究了镀液中氯化镍浓度为20、30、40 g/L时镀层的外观、微观形貌、镀层结合力,结果如图2所示。经过水冷法测试,3个样品的镀层并未出现脱落及起皮等现象,镀层结合力良好。由图2a~c可知,氯化镍含量为40 g/L时的镀层的宏观形貌较为粗糙,其余样品相对均匀;对应图2d~f可知,当氯化镍浓度为40 g/L时,活化效果强,阳极溶解快,导致产生阳极泥增多,进而使得镀层粗糙,镀层内应力增加,微观形貌表现出镀层脆裂;但当氯化镍浓度过低时,Cl-的阳极活化效果减弱,容易发生钝化,影响镀液稳定性。
图2 不同氯化镍浓度镀层的表面及SEM形貌
2.1.3 碳化硅含量的影响
碳化硅作为镀层中的异质相微粒,起到了细化镀层晶粒的作用,进而进一步影响镀层性能。镀液中碳化硅的含量变化,会对镀液中碳化硅的悬浮能力、镀液导电性等产生影响。分别研究了镀液中碳化硅含量在5、10、20、30、50和70 g/L时镀层的微观形貌、镀层结合力和镀层Si含量。经过水冷法测试,6个样品的镀层并未出现脱落及起皮等现象,说明镀层结合力良好,如图3所示。采用EDS对镀层进行元素分析后,以Si含量标记镀层中SiC的含量,如图4所示。由图3和4可知,镀层中的SiC含量随镀液中SiC浓度的增加而增加,但其增加趋势逐渐放缓,是由于在镀液中悬浮SiC微粒的比率会随镀液中SiC含量的增加而减少;当SiC含量过大时,镀液中SiC不易分散,且过高含量的SiC会影响镀液的导电性,影响镀层表面形貌。在SiC浓度范围为10~50 g/L时,镀层硬度与镀液中SiC浓度呈正相关,其硬度 (HV) 最大值达到了646。
图3 不同碳化硅浓度镀层的SEM像
图4 碳化硅浓度对镀层中SiC质量分数和镀层硬度的影响
2.2 表面活性剂处理SiC微粒对复合镀层的影响
2.2.1 SiC微粒的表征
根据上节分析,SiC微粒在镀层中的含量直接影响了镀层的形貌。使用不同种类的表面活性剂:阳离子表面活性剂十六烷基三甲基溴化铵 (CTAB)、阴离子表面活性剂十二烷基苯磺酸钠 (SDBS)、非离子表面活性剂聚乙烯吡咯烷酮 (PVP) 对SiC微粒进行表面处理,使用Zetasizer粒度电位仪测试其粒径分散度及微粒带电特性。图5显示了含有SDBS、CTAB和PVP的电镀液中SiC微粒的粒径分布。结果表明,与CTAB和PVP相比,SDBS作为表面活性剂时SiC微粒的分散性更好,当使用SDBS时,SiC微粒显示出较小的尺寸范围以及单一的峰值,这种窄的粒径分布和单一峰值表明,在此种情况下,当三者用量相等时,SDBS是一种比CTAB和PVP更好的分散剂。
图5 不同离子表面活性剂处理后的微粒粒径分布图
采用电位仪对经过不同表面处理的SiC微粒进行分散能表征,测量其Zeta电位。结果如图6所示。从图可知,经过SDBS和CTAB处理后的SiC微粒表现出完全相反的电性。SiC微粒经表面活性剂处理后,影响了其表面的双电层,从而表现出不同的电性,对随后参与电镀起到一定作用。经PVP处理后的SiC微粒由于非离子表面活性剂的水合作用,在SiC表面形成了较厚的水化层,与未经处理的SiC微粒相比,电性更为接近。
图6 不同表面活性剂处理后的SiC微粒的Zeta电位
2.2.2 微观结构与物相分析
将经过不同表面活性剂进行表面处理的SiC加入镀液中,制备出各自添加SDBS、CTAB和PVP的SiC悬浮镀液,在基材上进行电镀,制备复合镀层。图7分别为SiC经过不同表面处理的复合镀层的表面形貌SEM图。可以看出,SiC的沉积量随着不同种类表面活性剂的处理而改变。图7a经过阴离子表面活性剂处理后的SiC表面呈负电性,并存在一定量的活化点,吸引Ni、Co等阳离子在表面进行沉积,并且同时促进SiC的金属化,更容易沉积进入镀层;图7b经过非离子表面活性剂处理的SiC,表面的水化使得微粒间减少聚合,起到了一定的分散作用;图7c镀层的SiC明显减少,阳离子表面活性剂对微粒表面的作用,降低了微粒对镀层的吸附以及离子的包埋,减少了镀层中的SiC含量。表1中列出的镀层Si含量也直接证明了这一点。其中,镀层A中SiC经过了阴离子表面活性剂的处理,其平均Si含量高。镀层B、C、D中的SiC分别为非离子表面活性剂处理、阳离子表面活性剂处理和未经处理,其Si含量与镀层A相比,不同程度的减少。因此,阴离子表面活性剂SDBS能够促进微米级SiC在电镀过程中进入镀层,增加微米级SiC的复合量。
图7 SDBS,PVP,CTAB及无表面活性剂处理后的SiC微粒共沉积的复合镀层表面形貌
表1 不同镀层元素原子分数
SiC在镀层中的沉积,是SiC表面电性和其物理运动共同决定的,如图8所示。图8a是晶核在SiC表面生长的初始过程,图8b是SiC表面大量生长金属镀层,微粒即将被包埋的过程。SiC微粒伴随着镀液的搅拌随机碰撞在阴极表面,携带有负电荷的SiC微粒使得金属镀层能够在其表面生长,使这部分SiC被包埋得以进入镀层;晶核难以在携带有正电荷或弱负电荷的SiC微粒表面形成并生长,得以进入镀层的SiC微粒少,表现出的即为镀层中SiC含量低。
图8 晶核在SiC表面的生长及SiC被包埋的SEM像
3 结论
微米级SiC可通过电镀的方式沉积进入Ni-Co-P复合镀层,是一种有望替代铬镀层的复合镀层。通过不同的表面活性剂处理改变微米级SiC表面携带的电荷种类,能够改变微米级SiC在镀液中的分散程度;在电镀过程中微米级SiC进入镀层由其物理撞击和化学包埋共同决定。阴离子表面活性剂处理微米级SiC对其进入镀层有促进作用,增加复合量;阳离子和非离子表面活性剂处理微米级SiC会降低其复合量。
参考文献
1 Qin Q X, Guo H T, Liu S L, et al. Principle and Process of Electroplating [M]. 2nd ed. Tianjin: Tianjin Science and Technology Press, 1993: 65
1 覃奇贤, 郭鹤桐, 刘淑兰等. 电镀原理与工艺 [M]. 2版. 天津: 天津科学技术出版社, 1993: 65
2 Mandich N V. Practical problems in bright and hard chromium electroplating—Part I [J]. Met. Finish., 1999, 97: 100
3 Fujita M, Jomjunyong S, Itoh Y. Predicting service life of a bright Ni-Cr electroplating system on steel subjected to the CASS test [J]. Trans. IMF, 1997, 75: 98
4 Weng Y H. New Electroplating Process [M]. Hangzhou: Zhejiang Science and Technology Press, 1988: 69
4 翁元浩. 电镀新工艺 [M]. 杭州: 浙江科学技术出版社, 1988: 69
5 Subramanian B, Mohan S, Jayakrishnan S. Selective area deposition of Tin-Nickel alloy coating-an alternative for decorative chromium plating [J]. J. Appl. Electrochem., 2007, 37: 219
6 El-Sharif M, Chisholm C U. Characteristics of electrodeposited chromium [J]. Trans. IMF, 1997, 75: 208
7 Snyder D L. Decorative chromium plating [J]. Met. Finish., 2001, 99: 215
8 El-Sharif M. Replacing hexavalent chromium in electroplating [J]. Trans. Inst. Met. Finish., 1997, 75: B143
9 Zhu L Q, Xue Z, Wu K H. Effect of electroplating process on color of Ni-W decorative deposits alternative to chromium [J]. J. Jiangsu Univ. (Nat. Sci. Ed.), 2008, 29: 34
9 朱立群, 薛振, 吴坤湖. 电镀工艺对Ni-W装饰性代铬镀层色泽的影响 [J]. 江苏大学学报 (自然科学版), 2008, 29: 34
10 Haseeb A S M A, Arita M, Hayashi Y. Thermal decomposition study of electrodeposited Fe-C and Fe-Ni-C alloys by differential scanning calorimetry [J]. J. Mater. Sci., 2001, 36: 4739
11 Panagopoulos C N, Plainakis G D, Lagaris D A. Nanocrystalline Ni-W coatings on copper [J]. Mater. Sci. Eng., 2011, 176B: 477
12 Pushpavanam M, Manikandan H, Ramanathan K. Preparation and characterization of nickel-cobalt-diamond electro-composites by sediment co-deposition [J]. Surf. Coat. Technol., 2007, 201: 6372
13 Wang J C, Cheng X D, Li D H, et al. Study on Ni-W-SiC nanometer electrodeposition process [J]. J. Mater. Eng., 2006, (3): 25
13 王晋春, 程旭东, 李丹虹等. Ni-W-SiC纳米复合电镀工艺的研究 [J]. 材料工程, 2006, (3): 25
14 Lee E C, Choi J W. A study on the mechanism of formation of electrocodeposited Ni-diamond coatings [J]. Surf. Coat. Technol., 2001, 148: 234
15 Shi L, Sun C F, Zhou F, et al. Electrodeposited nickel-cobalt composite coating containing nano-sized Si3N4 [J]. Mater. Sci. Eng., 2005, 397A: 190
16 Wang F, Yu H Y, Sun D B, et al. Study on the wear resistance performance of Ni-P-nano-Al2O3 composite coatings [J]. Electroplat. Finish., 2007, 26(3): 1
16 王芳, 俞宏英, 孙冬柏等. Ni-P-纳米Al2O3复合镀层耐磨性能研究 [J]. 电镀与涂饰, 2007, 26(3): 1
17 Surender M, Basu B, Balasubramaniam R. Wear characterization of electrodeposited Ni-WC composite coatings [J]. Tribol. Int., 2004, 37: 743
18 Yu J, Liu J P, Zhao G P, et al. Pyro-oxidation resistance of Ni-SiC nano-composite coating [J]. Surf. Technol., 2004, 33(6): 31
18 于杰, 刘建平, 赵国鹏等. Ni-SiC纳米复合镀层的耐高温氧化性能 [J]. 表面技术, 2004, 33(6): 31
免责声明:本网站所转载的文字、图片与视频资料版权归原创作者所有,如果涉及侵权,请第一时间联系本网删除。
-
标签: 碳化硅-镍基复合材料, 碳化硅改性, 镍基合金电沉积, 碳化硅含量
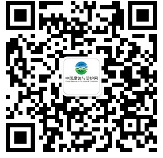
官方微信
《中国腐蚀与防护网电子期刊》征订启事
- 投稿联系:编辑部
- 电话:010-62316606-806
- 邮箱:fsfhzy666@163.com
- 中国腐蚀与防护网官方QQ群:140808414