摘要
利用电化学测试、表面分析及失重分析技术,研究了模拟高铁动态交流干扰下管道钢的腐蚀行为和规律及阴极保护的有效性。结果表明,动态交流干扰下,阴极保护电位向负方向偏移,交流干扰增大管道的阴极保护电流密度;动态交流干扰下,随干扰水平增加,管道钢腐蚀程度增加,点蚀坑明显加深。阴极保护明显减缓交流干扰试样的腐蚀程度,腐蚀速率降为不施加阴极保护试样的一半;本实验条件下,-1.0 V阴极保护电位可充分保护低于水平100 A/m2的动态交流干扰腐蚀。
关键词: 管道钢 ; 杂散电流 ; 交流干扰 ; 交流腐蚀 ; 阴极保护
近年来我国油气管道和电气化铁路建设发展迅猛,截至2020年底,中国铁路营业里程达14.6×104 km,其中高速铁路3.8×104 km;《新时代交通强国铁路先行规划纲要》明确指出,到2035年,全国铁路网运营里程20×104 km,其中高速铁路7×104 km。由于地理位置的限制,埋地管道与电气化铁路平行或交叉铺设情况越来越多,形成了错综复杂的能源输送网和电气化铁路网,来自高铁的杂散电流干扰问题日益普遍和严重,引起地下管道直接腐蚀或氢损伤,导致管道泄露、爆炸等安全事故,干扰腐蚀案例国内外均有大量报道[1-3]。
我国高铁采用工频单相25 kV交流供电制式,额定频率50 Hz,一般采用AT供电方式[1]。使用轨道和大地作为返回路径返回牵引变电站。铁路可能通过容性耦合、阻性耦合和感性耦合等方式干扰地下管道。不同于电感耦合引起的电力系统的稳态交流干扰[3],铁路牵引电力系统的干扰是电感耦合与电阻耦合作用下的瞬时交流干扰[4, 5]。无有效保护措施或长期干扰下,管线会产生严重腐蚀,危及运输和运行安全,并对附近的人员和与之连接的设备造成危害[6]。
人们对稳态交流干扰下的腐蚀行为及风险评估进行了大量研究,取得了较大进展[7-11]。Lalvani和Zhang[12]指出,交流干扰可以减少阳极和阴极极化,降低金属的钝化,增加腐蚀速率。Song等[13]的研究表明,阴极保护电位低于-1.0 V (vs. CSE) 时,交流腐蚀速率不受交流电压影响,而主要受频率和交流电流密度影响。Weng和Wang[14]的研究结果表明,碳钢的交流腐蚀速率与交流电流密度 (0~250 A/m2) 遵循幂函数关系;涂层存在微缺陷或表面破损时,交流干扰下即使采用阴极保护,管道的腐蚀也可能非常严重[15]。现有的研究结果不能有效地预测碳钢的交流腐蚀。不同于高压交流输电线路的稳态交流干扰,高铁对管道的干扰是动态的,其干扰特征与牵引供电方式和机车运行状态密切相关。动态交流干扰影响因素和影响过程复杂,除了干扰强度、频率及干扰时间等因素外,还与管线阴极保护水平密切相关。目前人们对动态交流干扰下金属/土壤界面电化学过程、金属腐蚀行为规律等仍缺乏深入了解。
本研究构建动态交流干扰管道腐蚀模拟实验装置,利用电化学和失重方法研究动态交流干扰下管线钢电化学极化特征及腐蚀行为。利用扫描电子显微镜 (SEM) 和激光共聚焦显微镜 (CLSM) 对腐蚀产物和腐蚀形貌进行表征。研究动态交流干扰强度及阴极保护水平等对管道钢腐蚀的影响,为受高铁线路干扰管道的评估及防护措施的制定提供依据。
1 实验方法
实验基材为X65管线钢。试样切割成面积为1 cm2、厚度5 mm的圆形试片。用于电化学极化测试的试样由环氧树脂封固,裸露工作面积为1 cm2,在试样背部焊接导线并将除工作面外其余表面采用环氧树脂密封。用于长期试验并进行失重测试的试样采用特制的有机玻璃盒封装,背面用铜线连接,工作面暴露面积为1 cm2。试样工作面用砂纸逐级打磨至1000#,用去离子水和无水乙醇清洗,冷风吹干,备用。
实验介质采用土壤模拟溶液饱和的石英砂 (80~100目),土壤模拟溶液为含5 mmol·L-1 Na2SO4+2.5 mmol·L-1 NaHCO3+10 mmol·L-1 NaCl的去离子水溶液。
根据高铁动态交流干扰特点,设计了动态交流干扰模拟电路及试验装置,如图1所示。电路包括交流电源、循环时间继电器、电容、电感、恒电位仪、辅助电极、参比电极和X65钢工作电极。通过交流电源施加交流电流并使用继电器控制连接或断开交流干扰电源或直流阴极保护电源,模拟动态交流干扰。
图1 动态交流干扰实验装置示意图
动态交流干扰下管线钢极化测量采用三电极体系,X80钢为工作电极,铂网为辅助电极,饱和甘汞为参比电极 (SCE)。采用交流电源对试样分别施加0、30、100和300 A/cm2等不同水平交流电干扰,在施加交流干扰过程中测试管线钢的极化曲线。极化曲线使用Gamry 600+进行测试,扫描速率为1 mV/s,扫描范围为±250 mV (OCP)。
图2是动态交流干扰实验原理图,交流干扰采用恒电流模式,每周期10 min:单次干扰时间4 min,间隔时间6 min。交流干扰电流密度分别为100和300 A/m2。实验参数如表1所示。阴极保护电位通过恒电位仪施加。实验过程中,使用uDL2数据记录仪采集工作电极电位。
图2 不同的交流电流密度干扰实验原理图
表1 动态交流干扰条件下的实验参数设置
实验后,取出试样并使用无水乙醇脱水。干燥后,用FEG XL30扫描电子显微镜 (SEM) 观察管线钢试样表面腐蚀产物。试样用添加缓蚀剂的盐酸 (500 mL HCl,500 mL去离子水和20 g六次甲基四胺) 清洗液除去腐蚀产物,用去离子水和无水乙醇清洗,干燥。用SEM和Zeiss LSM 510激光共聚焦显微镜 (CLSM) 观察试样微观腐蚀形貌,利用Rigaku-D/max 2500PC X射线衍射仪 (XRD) 分析腐蚀产物的组成。对实验前后试样精确称重,采用下式计算试样的腐蚀速率vCR (mm/a):
(1)
其中,ΔW是试样实验前后质量损失 (g),S是试样暴露表面 (m2),t测试持续时间 (d)。
2 结果与讨论
2.1 交流干扰下管道钢的极化行为
不同交流电流密度IAC干扰下试样的极化曲线如图3所示。可见,交流电干扰使自腐蚀电位和极化曲线偏移。无交流干扰时,自腐蚀电位为-0.599 V;IAC较小时,随交流干扰电流密度的增加试样的自腐蚀电位 (Ecorr) 负移。IAC为100 A/m2时,Ecorr为-0.909 V。IAC为300 A/m2时,自腐蚀电位正向移动。随IAC增大,阴极电流和阳极电流增加,腐蚀电流增大,反应处于混合控制下,试样表面溶液中Fe2+和O2的浓度会影响试样的腐蚀速率[11,16,17]。动态交流干扰也涉及氧的消耗和扩散[15],阴极保护电流导致氧的还原消耗,动态交流干扰过程中阴极保护的周期性施加,则Fe2+和O2很难扩散到样品表面。因此,在这种条件下的腐蚀情况类似于稳定交流干扰[18]。
图3 试样在不同交流电流密度干扰水平下的极化曲线
阴极保护管道钢试样施加100和300 A/m2的动态交流干扰时电位变化如图4所示。施加100和300 A/m2交流干扰时,试样交流电位分别为15.3和22.6 V。动态交流干扰使试样保护电位负向偏移,100 A/m2交流干扰施加瞬间试样出现一较大负向电位脉冲,电位负向偏移较大,而后电位逐步升高,干扰停止后电位继续上升。300 A/m2交流干扰时电位向负向偏移,干扰停止时电位出现负向脉冲,而后逐步上升。两种交流干扰均显著增大了试样的阴极保护电流密度ICP。无交流干扰时ICP约为0.09,100和300 A/m2交流干扰下ICP分别为0.19和23.1 A/m2。
图4 动态交流干扰下管道钢试样的阴极保护电位和交流电压的变化
2.2 动态交流干扰下管道钢腐蚀产物分析
无阴极保护动态交流干扰5 d后表面腐蚀产物形貌示于图5。试样表面腐蚀产物主要呈颗粒状和鳞片状[19]。XRD分析 (图6) 表明,腐蚀产物主要成分为γ-FeOOH、Fe3O4和Fe2O3[20]。腐蚀产物随干扰电流的增加而增加,腐蚀产物表面均存在局部开裂现象,这可能是由于试样表面干湿交替的环境所导致。电流使试样表面的水分蒸发,但动态交流干扰间隔时,溶液又扩散到试样表面,形成干湿交替环境。
图5 无阴极保护管道钢试样动态交流干扰试验后表面腐蚀产物形貌
图6 试样表面腐蚀产物XRD谱
石英砂中阴极保护试样动态交流干扰实验5 d后试样的宏观照片和SEM形貌分别示于图7和8。试样表面的白色颗粒是石英砂,动态交流干扰下,试样表面产生一些黑色和黄棕色腐蚀产物。图8显示腐蚀产物分为两层,其中底部腐蚀产物为黑色,而上层为黄褐色。随着交流干扰电流密度的增加,表面腐蚀产物变厚,表明施加动态交流干扰会加速试样的腐蚀。去除腐蚀产物后可以明显看出大电流密度交流干扰下点蚀坑更深。
图7 阴极保护管道钢动态交流干扰X65钢试验后试样宏观形貌
图8 阴极保护管道钢动态交流干扰试验后试样表面腐蚀产物形貌
2.3 动态交流干扰管道钢腐蚀形貌
4种实验条件试样去除腐蚀产物后的表面腐蚀形貌示于图9。可见,随干扰电流密度增加,试样表面腐蚀程度增加,点蚀坑明显加深。阴极保护使管道钢试样的腐蚀速率明显降低,但点蚀坑深度与无阴极保护条件相比未见显著减小。
图9 动态交流干扰试验后管道钢试样表面腐蚀形貌SEM图
使用激光共焦扫描电子显微镜 (CLSM) 对点蚀形态进行表征,如图10所示。100和300 A/m2干扰下,无阴极保护时的最大点蚀坑深分别为45.7和 61.1 μm;而施加阴极保护时的最大点蚀坑深分别为38.9和57.9 μm。
图10 动态交流干扰试验后管道钢试样表面腐蚀坑CLSM形貌图
由失重法计算得管道钢试样的腐蚀速率数值列于表1。100和300 A/m2动态交流干扰下,无阴极保护试样腐蚀速率分别为0.046和0.195 mm/a;而施加阴极保护试样的腐蚀速率分别为0.024 mm/a (<0.025 mm/a) 和0.092 mm/a (>0.025 mm/a)。腐蚀速率随交流干扰电流密度的增加而增加,干扰电流密度300 A/m2下试样腐蚀速率约是100 A/m2时的3倍;相同水平交流干扰条件下,无阴极保护试样的腐蚀速率约是阴极保护试样的2倍。
据NACE SP0169-2013 (埋地或水下金属管道系统的外腐蚀控制) 准则中规定的0.025 mm/a的腐蚀速率限值,本实验条件下,-1.0 V阴极保护电位可有效保护干扰水平低于100 A/m2的动态交流干扰,而不能有效保护300 A/m2水平的动态交流干扰。
2.4 动态交流干扰下管道钢腐蚀机理分析
交流电是以一定频率周期性交替变化的阳极和阴极电流。交流电的正半周期内产生阳极电流对管道进行阳极极化,管道金属被氧化,表面生成钝化膜 (如Fe2O3);交流电负半周期内过多的阴极电流对管道进行阴极极化,促使点蚀电位负向偏移并使电极表面膜层的状态发生改变,钝化膜被还原成非保护性的二价多孔氢氧化物膜层,如Fe(OH)2,此腐蚀产物层没有保护作用且膜层可能不会再次转换为钝化膜,且腐蚀产物在管道钢表面的粘附状态会在交变电场的影响下发生变化,从而导致腐蚀产物膜变松并且孔隙率增加[21]。在接下来的循环过程中,随着钢电极表面钝化膜的氧化和还原,金属和氢氧化物之间生成新的钝化膜[22],Fe2+被还原且反应不可逆,每一循环都导致腐蚀产物产生,结果管道基体不断被氧化腐蚀。
阴极保护作用下,形成高pH局部环境,管道钢表面可形成钝化膜,而当阴极保护和交流干扰共同作用时,交流电流提高了腐蚀电流的密度、减少膜层厚度、降低稳定性。同时瞬时变化的电位在膜层表面电场和界面张力的作用下导致钝化膜的机械破损,影响钝化膜的致密性,使无保护的钢基底直接暴露在腐蚀离子中加速管道的腐蚀。
3 结论
(1) 施加交流干扰电流时,管道钢试样阴极保护电位向负方向偏移。随交流干扰电流密度的增加,促进阳极和阴极反应,导致腐蚀电流增加。交流干扰增大管道的阴极保护电流密度。
(2) 动态交流干扰下,管道钢试样腐蚀产物主要为颗粒状和鳞片状,主要成分为γ-FeOOH、Fe3O4和Fe2O3。随干扰水平增加,管道钢腐蚀程度增加,点蚀坑明显加深。
(3) 动态交流干扰下,阴极保护试样的交流腐蚀程度明显减缓,腐蚀速率约为不施加阴极保护的一半。本实验条件下,-1.0 V阴极保护电位可以有效保护100 A/m2水平的动态交流干扰,但不能保护300 A/m2水平的动态交流干扰。
(4) 交流干扰下,阴极保护状态下的管道钢发生局部阳极溶解,这归因于交流电流正半周期中产生的阳极电流优先腐蚀钢表面的活性部位破坏金属钝化膜,进而导致局部腐蚀。交流干扰情况下,即使符合阴极保护标准,也可能发生腐蚀。
参考文献
1 Matta V, Kumar G. Unbalance and voltage fluctuation study on AC traction system [A]. Electric Power Quality and Supply Reliability [C]. Chennai, India, 2014: 315
2 Mariscotti A. Distribution of the traction return current in AC and DC electric railway systems [J]. IEEE Trans. Power Deliv., 2003, 18: 1422
3 Ouadah M, Touhami O, Ibtiouen R, et al. Corrosive effects of the electromagnetic induction caused by the high voltage power lines on buried X70 steel pipelines [J]. Int. J. Elec. Power, 2017, 91: 34
4 Charalambous C A, Demetriou A, Lazari A L, et al. Effects of electromagnetic interference on underground pipelines caused by the operation of high voltage AC traction systems: the impact of harmonics [J]. IEEE Trans. Power Deliv., 2018, 33: 2664
5 Brenna A, Ormellese M, Lazzari L. Electromechanical breakdown mechanism of passive film in alternating current-related corrosion of carbon steel under cathodic protection condition [J]. Corrosion, 2016, 72: 1055
6 Micu D D, Christoforidis G C, Czumbil L. AC interference on pipelines due to double circuit power lines: A detailed study [J]. Electr. Power Syst. Res., 2013, 103: 1
7 Funk D, Schoeneich H G. Probleme bei der Bewertung der Wechselstrom-Korrosions-gefaehrdung von Rohrleitungen mit Probeblechen [J]. 3R International, 2002, 41: 582
8 Floyd R. Testing and mitigation of AC corrosion on 8 Line: A field study [A]. Corrosion 2004 [C]. New Orleans, Louisiana, 2004
9 Liang Y, Du Y X. Research progress on evaluation criteria and mechanism of corrosion under cathodic protection and AC Interference [J]. J. Chin. Soc. Corros. Prot., 2020, 40: 215
9 梁毅, 杜艳霞. 交流干扰和阴极保护协同作用下的腐蚀评判标准与机理研究进展 [J]. 中国腐蚀与防护学报, 2020, 40: 215
10 Hanson H R, Smart J. AC corrosion on a pipeline located in a HVAC utility corridor [A]. Corrosion 2004 [C]. New Orleans, Louisiana, 2004
11 Wang X L, Yan M C, Shu Y, et al. AC interference corrosion of pipeline steel beneath delaminated coating with holiday [J]. J. Chin. Soc. Corros. Prot., 2017, 37: 341
11 王晓霖, 闫茂成, 舒韵等. 破损涂层下管线钢的交流电干扰腐蚀行为 [J]. 中国腐蚀与防护学报, 2017, 37: 341
12 Lalvani S B, Zhang G. The corrosion of carbon steel in a chloride environment due to periodic voltage modulation: Part I [J]. Corros. Sci., 1995, 37: 1567
13 Song H S, Kho Y T, Kim Y G, et al. Competition of AC and DC current in AC corrosion under cathodic protection [A]. Corrosion 2002 [C]. Denver, Colorado, 2002
14 Weng Y J, Wang N. Carbon steel corrosion induced by alternating current [J]. J. Chin. Soc. Corros. Prot., 2011, 31: 270
14 翁永基, 王宁. 碳钢交流电腐蚀机理的探讨 [J]. 中国腐蚀与防护学报, 2011, 31: 270
15 Büchler M. Alternating current corrosion of cathodically protected pipelines: Discussion of the involved processes and their consequences on the critical interference values [J]. Mater. Corros., 2012, 63: 1181
16 Zhang R, Vairavanathan P R, Lalvani S B. Perturbation method analysis of AC-induced corrosion [J]. Corros. Sci., 2008, 50: 1664
17 Ghanbari E, Iannuzzi M, Lillard R S. The mechanism of alternating current corrosion of API grade X65 pipeline steel [J]. Corrosion, 2016, 72: 1196
18 Chen L, Du Y X, Liang Y, et al. Research on corrosion behaviour of X65 pipeline steel under dynamic AC interference [J]. Corros. Eng. Sci. Technol., 2021, 56: 219
19 Wang X H, Yang Y, Chen Y C, et al. Effect of alternating current on corrosion behavior of X100 pipeline steel in a simulated solution for soil medium at Korla district [J]. J. Chin. Soc. Corros. Prot., 2020, 40: 259
19 王新华, 杨永, 陈迎春等. 交流电流对X100管线钢在库尔勒土壤模拟液中腐蚀行为的影响 [J]. 中国腐蚀与防护学报, 2020, 40: 259
20 Xiao Y W, Du Y X, Tang D Z, et al. Study on the influence of environmental factors on AC corrosion behavior and its mechanism [J]. Mater. Corros., 2018, 69: 601
21 Wan H X, Song D D, Liu Z Y, et al. Effect of alternating current on corrosion behavior of X80 pipeline steel in near-neutral environment [J]. Acta Metall. Sin., 2017, 53: 575
21 万红霞, 宋东东, 刘智勇等. 交流电对X80钢在近中性环境中腐蚀行为的影响 [J]. 金属学报, 2017, 53: 575
22 Büchler M, Scho?neich H G. Investigation of alternating current corrosion of cathodically protected pipelines: Development of a detection method, mitigation measures, and a model for the mechanism [J]. Corrosion, 2009, 65: 578
免责声明:本网站所转载的文字、图片与视频资料版权归原创作者所有,如果涉及侵权,请第一时间联系本网删除。
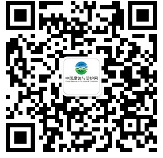
官方微信
《中国腐蚀与防护网电子期刊》征订启事
- 投稿联系:编辑部
- 电话:010-62316606-806
- 邮箱:fsfhzy666@163.com
- 中国腐蚀与防护网官方QQ群:140808414