在国家能源战略、环境保护、经济发展形势等多重因素的促进下,液化天然气(LNG)产业得到大力发展,截至2019年10月,我国已建成投产21座LNG接收站,实际接收能力为8955×104t/a。虽然LNG接收站中的主要工艺介质如LNG、天然气(NG)、闪蒸气(BOG)无明显腐蚀性,但是随着服役时间的延长,站内压力容器、压力管道等承压设备均可能产生不同程度的损伤,及时发现承压设备上的损伤,关系到整个接收站的运营安全和区域能源的稳定供应。
TSG 21-2016《固定式压力容器安全技术监察规程》和TSG D7005-2018《压力管道定期检验规则 工业管道》等安全技术规范明确要求,压力容器、压力管道等特种设备须在一定周期内实施停车检验,但是迫于区域能源调峰保供的压力和承压设备保冷层的存在,站内大多数承压设备不具备停车检验的基本条件。
从部分实施过定期检验的接收站的反馈来看,站内压力容器的定期检验实施情况良好,首次检验能按规范要求及时进行;但压力管道的定期检验实施时困难较多,首次检验一般不能及时进行,即使实施了首次检验,也仅是抽查了部分氮气、空气和极少量的LNG、NG管线的管件,检验时主要以宏观检查为主,壁厚测定、表面缺陷及埋藏缺陷检测等测试和现行规范的要求并不相符且缺乏针对性。
部分企业在保障能源供应平稳的前提下,考虑到安全生产的需要,相继采用了基于风险的检验(RBI)技术对站内承压类特种设备的检验周期进行了适当延长,但到期后检验困境依旧存在。据调研,目前仍未系统性地开展过关于LNG接收站承压类特种设备的典型损伤机理、风险点及基于损伤模式的检验方法研究。
为此,中国特种设备检测研究院和中海石油气电集团有限责任公司的技术人员开展了瞬变电磁、脉冲涡流、数字射线等在线检测技术在深冷环境中的可靠性对比分析,提出一种适用于LNG接收站承压设备服役现状的检验方法,为站内承压设备在不停车状态下实现科学、合理、有效的检验,更好地控制站内承压设备运行风险,节约检维修成本,促进行业健康发展提供参考。
LNG接收站工艺流程
LNG接收站作为远洋运输液化天然气的终端、陆上天然气供应的气源,主要由卸料系统、LNG储存系统、BOG回收处理系统、LNG加压气化系统、NG计量外输系统和LNG装车/船系统等组成。
LNG运输船到达码头后,通过卸料臂将LNG输送到LNG储罐,罐内低压泵将LNG升压后输送到低压LNG总管。然后,一部分LNG被输送到再冷凝器和高压泵,经高压泵加压后输送到气化器加热、气化并外输;另一部分LNG被输送到槽车装车撬,再充装到LNG槽车并外输。
目前,国内LNG接收站通常以开架式气化器(ORV)或中间介质气化器(IFV)为主,考虑到调峰或ORV、IFV维修时的供应平稳,一般会以浸没燃烧式气化器(SCV)辅助备用。IFV气化器由三个管壳式换热器组成:E-1段为中间丙烷气化器,E-2段为液化天然气气化器,E-3段为天然气调温加热器。
站内除高压外输系统采用不带保温的碳钢外,其他主工艺系统均在深冷工况下工作,因此几乎都采用覆盖有聚异氰脲酸酯绝热层的奥氏体不锈钢。
考虑到主工艺介质中不存在腐蚀性物质,系统中也不易形成水汽等易腐蚀环境,同时接收站中主要发生的是物理变化,不存在中间过程生成腐蚀性物质的可能,因此站内由介质本身引起压力容器、压力管道的腐蚀微乎其微。
在线检测技术可靠性分析
传统定期检验一般以宏观检验、壁厚测定和安全附件的检验为主,必要时增加表面缺陷检测、埋藏缺陷检测等项目,检验项目的选取及检验部位的确定取决于检验人员的水平和经验,具有一定的盲目性。
实施RBI检验时,需根据各评价单元的损伤机理、风险大小,通过有针对性的检验来降低或控制各评价单元的运行风险。
基于目前检测技术发展水平,拟构建红外热成像+瞬变电磁/脉冲涡流+数字射线的检测体系,以涵盖宏观检验、壁厚测定和无损检测等检验项目,各检验项目的具体要求可参考相关规范。
在低温深冷环境中,分析瞬变电磁、脉冲涡流、数字射线等可应用到在线检验的检测技术的可靠性。模拟LNG接收站低温管道的服役工况,选取DN250以下各种管径的304不锈钢焊接成测试件,每一测试件包含一个弯头和两段直管,如图1所示。
图1 测试件示意图
依据某LNG接收站技术文件选取绝热层材料的性能及厚度。试验介质为液氮,绝热层材料使用深冷型硬聚异三聚氰脲酸酯(PIR)及不锈钢金属保护层,采用粘贴、捆扎结构进行安装,如图2所示。
图2 测试件绝热层安装示意图
首先,在测试件未安装绝热层及充装液氮时,用超声波测厚仪对各测试件不同部位的壁厚进行标定,再用数字射线对在各测试件上加工的腐蚀和焊接缺陷进行标定。
(1)瞬变电磁检测技术
瞬变电磁检测技术(TEM)是利用被测区域内各物质电导率的不同,依据反馈回来的瞬变衰减特征差异来计算被测物体金属损失的一种检测技术,其结构和工作原理如图3所示。
图3 瞬变电磁检测系统的结构和工作原理示意图
由于试验中测试件结构包覆有绝热层,金属基体与绝热层的电磁特性差异显著,所以在归一化的瞬变响应曲线上会具有明显的时间可分性。在选定的瞬变响应时窗范围内,通过反演模拟确定出瞬变时间常数,从而得到测试件的平均剩余厚度。
当在测试件上安装绝热层并充装液氮后,用瞬变电磁检测系统对超声波测厚仪标定部位壁厚进行测定,结果显示TEM测厚与传统超声波测厚相比,误差小于5%,且总体上弯头误差比直管段大,符合弯头、直管厚度的变化规律。因此,瞬变电磁检测技术在隔着绝热层测量不锈钢壁厚方面具有较高的准确性。
瞬变电磁检测的局限性主要在于以“平均剩余厚度”来反映所测壁厚。用瞬变电磁检测技术检测基体腐蚀状况时,对已探测到的腐蚀点具有较高的准确性;对于存在严重点蚀现象,但腐蚀面积不大、金属损失量较小的管段,其准确性较差。因此,对于局部腐蚀缺陷,瞬变电磁检测具有一定的不确定性。现场检测过程中,对于疑似减薄部位,探头移动距离应尽可能的小,以找出局部腐蚀边界。
此外,由于现场条件和技术的局限,检测数据的修正是建立在公称壁厚基础上,但实际壁厚可能由于各种原因和公称壁厚有所偏差,这可能会对瞬变电磁检测结果造成影响,因此所得数据的误差范围除受仪器精度影响外,还与实际壁厚和公称壁厚的偏差相关。如果加大检测频率,或者再次检验时以第一次检测数据为基准对测定结果进行修正,通过多次检测,因无法采用实际壁厚对数据进行修正的影响会减到最小。
(2)脉冲涡流检测技术
脉冲涡流检测(PECT)技术是通过分析由激励电流产生的感应电压信号波形,获得被测试件的厚度,检测系统的结构和工作原理如图4所示。理论和试验研究均已证明该技术对不锈钢管道减薄缺陷的有效性。
图4 脉冲涡流检测系统的结构和工作原理示意图
当所有测试件安装绝热层并充装液氮后,用MAXWELL PECT在役脉冲涡流检测系统对超声波测厚仪标定直管段部位壁厚进行测定,结果显示PECT测厚与传统超声波测厚相比,误差小于4%,且精度比同部位瞬变电磁检测精度更高。
但是,由于弯管段的曲面形状复杂,探头覆盖区域内的管壁金属体积与直管段的金属体积不同,且会随周向位置的变化而不同,因此,常规探头在该段存在盲区或检测精度降低。
此外,相比于直管段,弯管段绝热层施工时外部金属保护层搭接重叠区较密,搭接部位具有一定高度,脉冲涡流感应信号受其影响较大,所以如不拆除金属保护层也不使用适合弯管段的特殊探头,PECT只适用于直管段或容器的检测。
同时,脉冲涡流检测的壁厚是探头线圈面积下的平均厚度,对于较大面积的腐蚀缺陷,检测灵敏度高,但对于较小面积的点蚀,检测灵敏度相对较低。因此,对于隔热层下大面积的腐蚀减薄,脉冲涡流是一种非常好的快速筛查手段。
(3)数字射线检测技术
数字射线(DR)检测是通过成像探测器接收由射线源发出的射线,实现射线光子到数字信号再到数字图像的转换过程,最终实现对缺陷的观察和分析,检测系统工作原理如图5所示。
图5 数字射线检测系统工作原理示意图
氨制冷装置的工程应用表明,数字射线检测是一种可以及时发现缺陷隐患的有效在线检测手段。但是对于LNG接收站低温管线,在线数字射线检测依旧缺乏系统性的精确定量研究。
图6为数字射线检测现场照片。在测试件覆盖绝热层、充装液氮前后分别用XRS-4数字射线检测系统对各测试件中加工的可能影响安全状况等级评定且具有临界尺寸的缺陷如腐蚀、裂纹、咬边、错边、未熔合、未焊透、圆形和条形等进行全面分析验证。结果表明,当管道不带保冷层、无介质时,数字射线检测结果具有高度可靠性;对于低温气态管线,数字射线检测可以有效检测出圆形、条形、未熔合、未焊透等缺陷,较为有效地检测出咬边缺陷;对于低温液态管线,数字射线检测可以有效检测出未焊透缺陷,DN200以下规格中的圆形、条形和未熔合等缺陷。同时,数字射线检测可以隔着绝热层有效反映管道的腐蚀信息。
(a)覆盖绝热层、未充装液氮前
(b)覆盖绝热层、充装液氮后
图6 数字射线检测覆盖绝热层、充装液氮前后测试件
因此,数字射线检测技术对可能存在的影响安全运行的腐蚀及焊接缺陷具有较高的识别率,是一种有效的在线检测技术。
基于损伤模式的检测方法分析
相关规范标准要求,LNG接收站中输送LNG、NG介质的不锈钢管道焊缝应进行100%射线或超声检测、100%渗透检测并经监督检验合格,因此站内低温容器、管道满足相关设计、安装及验收规范,不存在影响安全运行的原始焊接缺陷以及可能产生的敏化现象。从风险控制的角度分析,站内承压设备运行期间的风险主要由使用过程中的腐蚀、机械损伤及工艺波动等因素主导,压力容器和压力管道的损伤模式、损伤机理及主要分布工段如下表所示。
大气环境中服役的容器、管道都可能发生大气腐蚀(有/无隔热层),尤其在以下情况:操作温度较低导致设备外表面形成湿气,油漆或涂层施工质量差,操作温度在环境温度和较高温度或较低温度之间循环,长期停用或闲置但又没有正确封存,隔热层破损。
某LNG接收站典型设备检验数据如下:
在不考虑制造误差时,LNG、NG对设备内表面腐蚀轻微,设备的腐蚀大多来自设备的外表面腐蚀。结合在线检测技术分析结果,对带隔热层的容器、管道剩余壁厚的测定可以采用瞬变电磁或脉冲涡流检测技术,隔着隔热层进行壁厚测定时检测部位的选取很关键,故可通过红外热成像技术检测设备保冷层是否存在跑冷,以此来确定壁厚测定的重点部位。对不带隔热层的容器、管道剩余壁厚的测定可以采用传统的超声波测厚方法,但从安全角度考虑,推荐采用不需要打磨的电磁超声检测技术。
图7为LNG接收站工艺流程及损伤机理分布示意图:
图7 LNG接收站工艺流程及损伤机理分布
根据站内管线的腐蚀回路确定LNG接收站不同部位的检测策略:
1 站内与泵、压缩机相连的管线、高压天然气外输管线等,在振动载荷或不稳定流体流动等动态载荷作用下,易引起交变应力,从而存在发生振动疲劳的可能。对低温管线可以采用DR技术进行检测,对常温管线如高压天然气外输管线可以采用磁粉检测或渗透检测等。
2 IFV海水系统中的冷却水腐蚀、微生物腐蚀主要集中在中间丙烷气化器及天然气调温加热器的管程、管束等部位;对管程剩余壁厚的测定推荐采用不需要打磨的电磁超声检测技术,必要时辅助以超声C扫,对于管束剩余壁厚则主要通过工艺指标间接进行监控。ORV海水系统中的冷却水腐蚀、微生物腐蚀主要集中在LNG总管及距LNG总管一定范围内的翅片管上,腐蚀程度和外部涂层质量密切相关,因此,除定期目视宏观检查外,必要时可以用涡流式膜厚计对涂层厚度进行检测。
3 输送流动介质的所有设备都易发生冲刷,管道系统多见于弯头、三通、异径管、调节阀和限流孔板的下游部位,设备系统主要集中在泵、压缩机、换热器管束、出入口接管等部位。对于有隔热层的设备可以选取瞬变电磁或脉冲涡流检测技术进行重点部位的壁厚测定;对于无隔热层设备,推荐采用电磁超声检测技术。
4 IFV、ORV主要是将LNG转化为NG,相变过程中气泡的溃灭会持续对中间丙烷气化器壳程、液化天然气气化器壳程顶部内表面和ORV的LNG管及距LNG管一定范围内的翅片管产生撞击,从而造成气蚀损伤破坏。此外,潜液泵及其进液管线、高压泵及其入口管线也易发生气蚀。对中间丙烷气化器壳程和液化天然气气化器壳程、潜液泵进液线和高压泵入口线的壁厚测定可以采用瞬变电磁或脉冲涡流检测技术;对ORV气化器的LNG管及翅片管的壁厚监测可以采用传统的超声波测厚仪和涡流式膜厚计进行间接验证。
RBI策略确定
RBI是被广泛采用并得到认可的设备管理检验技术。我国相关安全技术规范也明确了压力容器、压力管道的定期检验可以采用RBI技术。LNG接收站承压设备采取RBI技术,可减少过度检验及无效检验,有效降低保冷层拆除比例,控制检验时间和成本,使检验检测工作既能达到合理使用检验资源、降低检修费用的目的,又能满足检验检测的深度和针对性要求,同时解决传统定期检验不分重点的问题,实现站内承压设备的不停机检验。基于损伤机理的站内典型设备推荐的RBI策略如下表所示:
结论与建议
1 LNG接收站压力容器、压力管道的损伤机理分析表明,由于介质的清洁性,站内低温压力容器、压力管道不存在明显的腐蚀性,LNG接收站腐蚀直观上表现为大气腐蚀。
2 与传统超声波测厚相比,瞬变电磁、脉冲涡流检测误差不超过5%,可以在不停机状态下准确测定设备壁厚;对于低温气态管线,数字射线检测可以有效地检测出圆形、条形、未熔合、未焊透等缺陷,较为有效的检测出咬边缺陷;对于低温液态管线,数字射线检测可以有效地检测出未焊透缺陷,DN200以下规格中的圆形、条形和未熔合等缺陷。
3 通过腐蚀回路的划分,可以有效降低站内压力管道的抽检比例,节省检验时间和节约检维修成本。
4 LNG接收站压力容器、压力管道采用基于RBI技术的在线检验方法可以科学把控接收站运营风险,解决站内承压类特种设备不能进行停机检验的困境,实现经济性与安全性的统一。
免责声明:本网站所转载的文字、图片与视频资料版权归原创作者所有,如果涉及侵权,请第一时间联系本网删除。
相关文章
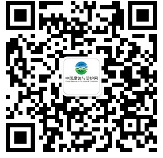
官方微信
《中国腐蚀与防护网电子期刊》征订启事
- 投稿联系:编辑部
- 电话:010-62316606-806
- 邮箱:fsfhzy666@163.com
- 中国腐蚀与防护网官方QQ群:140808414
点击排行
PPT新闻
“海洋金属”——钛合金在舰船的
点击数:7130
腐蚀与“海上丝绸之路”
点击数:5741