深海通常指500 m以下更大深度的海洋,占海洋总体积的3/4.深海是人类科学探索和资源需求的宝库和未来。据统计,目前世界深海油气探明储量已占海洋油气储量的65%以上;天然气水合物在海洋中的总量为(1~5)×1015 m3;多金属结核在海洋中约5 000亿吨,主要富集在4 000~6 000 m深度;富钴结壳在海洋中含量达10亿吨,主要分布在500~4 000 m深度;上百处海底热液多金属硫化物矿床含量达6亿吨,分布在1 500~4 000 m深度;深海已发现数千种新生物,绝大部分物种是深海环境所独有的[1].深海是高压、低温或局部高温(400 ℃)环境[2],深海并不平静,经常出现类似于陆地上飓风等的激流——深海“风暴”。虽然深海“风暴”的流速仅有50 cm/s左右,但能量巨大,甚至可以改变海底地形。其巨大的破坏力会对海底的科学仪器、通讯电缆等造成毁坏,甚至可能危及海上石油钻井平台等。深海的腐蚀和磨损常常是耦合发生的[3],高压[4-7]、低温(或热液区高温)[8-11]、极端微生物附着[12-13]、毒性气体[14-15]都会加剧海水对服役材料的腐蚀,更会加剧海底“风暴”涌动的磨蚀及毁损过程,并随着海底“风暴”的冲击在金属表面产生“犁沟”,形成新的裸露表面而进一步被腐蚀。
深海苛刻的环境对于服役金属材料的蚀损机制研究一直是我国材料研究的空白。一般物质在经历高压过程中会产生相变,因而在深海高压环境下,材料的组织和性能可能会发生出人意料的变化。材料在深海环境中服役时,其在高压下的摩擦系数、热衰退及热稳定性等与常温常压下不同,所表现出的腐蚀、磨损机制也与常压环境下不同,尤其在深海环境中温度梯度较大时, 金属材料的腐蚀速率、摩擦系数及磨损均会加剧。随着油气勘探向地质条件和环境更加复杂的深海区域发展,一些高H2S和CO2、高含硫深海热液环境区域成为油气勘探的重点。因而,研究材料在深海高压有毒气体等环境下的蚀损行为也显得极其重要。
深海蕴藏着世界未来发展所必须的丰富能源与战略资源。目前,我国深海装备关键材料90%以上依赖进口,随着我国海洋强国建设的加速,海洋科技向着深远化进军,石油钻采向着深海延伸以及南海可燃冰的勘探和开采,我国对于深海装备国产化的需求更为迫切,如果无法建立一套完整的深海服役材料的腐蚀评价体系,将会严重影响深海装备的安全性和可靠性,从而成为深海战略发展的“瓶颈”。
1 国内外研究现状
1.1 金属材料的深海腐蚀行为
各国科研工作者对各种材料深海腐蚀做了大量工作[16],许多研究机构也对各种材料进行了大量、长时间的实海挂片实验[17-20].1962~1970年间,加利福尼亚的海军工程中心(Naval Construction Battalion Center)在怀尼米港西南方向81海里及西部方向75海里的海水对475种合金材料、20000多种试样进行了挂片实验,试样包括钢、铸铁、不锈钢、铜、镍、铝等多种材料,挂片深度分别为762和1 829 m.实验结果表明,除了铝合金在深海中的点蚀深度加大并出现了缝隙腐蚀,而浅海挂片试样未出现缝隙腐蚀外,水深对其他材料腐蚀的影响要么可以忽略,要么就是减轻了[21].Venkatesan等[22]将表面不会形成钝化膜的低碳钢浸泡于500~5 100 m深的海水中68 d后,发现深海中低碳钢的腐蚀速率明显低于浅海中低碳钢的腐蚀速率,而在所有深海挂片试样中,500 m深处的腐蚀速率最低,归因于此处的溶解氧最小。需要注意的是,不同海域溶解氧随水深的变化规律是不一样的,Venkatesan等进行试验的海域为印度洋,而我国南海实测数据显示,水深750 m左右时海水中含氧量最低,约为2.5 mg/L.Beccaria等[23]研究发现,随着静水压的升高,Al及6061-T6铝合金发生局部腐蚀的倾向均有所增加,并且6061-T6铝合金的点蚀深度增加,而由于Mg-Al氧化层的形成,总体上腐蚀有所减少。实验室模拟方面,Yang等[24]发现,随着静水压的增加,Ni-Cr-Mo-V高强钢的腐蚀速率增加,且极化曲线表明,阴极过程和静水压关系不大,而腐蚀电位负移,腐蚀电流加大;通过腐蚀形貌的观察及压力的有限元分析,认为静水压将使得点蚀更易于向点蚀周边轮廓的法向方向扩展,进而使得相邻的点蚀相互连通并由此发展为全面腐蚀,而点蚀的深度则与静水压关系不大[25].和实海挂片相比,实验室模拟除了模拟试验易于开展、投入较少外,另一明显的优点就是可以方便地进行在线电化学性质的测试,对于深入研究腐蚀机制有很大的帮助[26].
1.2 深海微生物腐蚀行为
关于深海微生物腐蚀,由于深海微生物取样、保种、培养等方面需要较高技术水平,因此这方面研究报道较少,但就微生物腐蚀机制及其和局部腐蚀的关系,则有较多文献报道。如Mehanna等[27]选择1145低碳钢,403铁素体钢和304L、316L奥氏体钢,G. sulfurreducens为腐蚀菌种,通过开路电位的检测,发现浸泡数小时后1145钢、403钢、304L钢的开路电位正移了300 mV,而316L钢的开路电位正移较少,开路电位的正移和细菌的富集相关,这表明G. sulfurreducens的附着可直接从材料攫取电子,增加了铁素体钢和低碳钢的局部腐蚀。San等[28]选择A. eucrenophila在Ni-Cu合金表面进行试验,极化曲线分析表明,细菌附着后极化曲线发生了偏移,5 h后腐蚀电位发生了正移,腐蚀电流增加,EDS元素分析表明合金表面有明显的NiO和CuO产物。Nercessian等[29]选择P. fluorescens, 研究其对铜的腐蚀,通过检测微生物膜生长过程中RNA和DNA量比随时间的变化关系,结合极化曲线和阻抗谱的检测,分析了微生物代谢过程与腐蚀速率的关系,认为微生物的呼吸加速了铜的腐蚀。 Bhaskar等[30]研究发现, 微生物的胞外分泌物对重金属离子可选择性地固定,结果表明:每毫克EPS固定的Cu2+要多于Pb2+,且在酸性溶液中会吸收更多的Cu2+和Pb2+; 然而,随着溶液中NaCl浓度的升高,微生物对Cu2+和Pb2+的吸收会随之减少。Bevilaqua等[31]通过检测Cu5FeS4在A. ferrooxidans培养液中浸泡不同时间的电化学噪声,对噪声电压和电流的平均值及其标准偏差、噪声电阻进行分析,结果表明, 细菌的生物活动可引起这些参数的明显变化。赵晓栋等[32]取青岛胶州湾海底泥中的SRB进行富集培养,研究其对Q235腐蚀的影响,结果表明, 硫酸盐还原菌可将腐蚀产物由球形的水合氧化铁转化为海绵状的球形铁硫化物。牛桂华等[33]对316不锈钢在无菌培养基介质和海水微生物接种培养有菌培养基介质中的腐蚀行为进行了研究,认为海洋微生物的附着和繁殖可加速316不锈钢的腐蚀。Yuan等[34]通过研究aerobic pseudomonas对Cu-Ni合金在海水中的腐蚀行为发现,当aerobic pseudomonas和EPS存在时, 可显著降低Cu-Ni合金的腐蚀速率,这可能是由于微生物的存在影响了材料腐蚀过程中的阴极反应。
基于目前深海微生物腐蚀的研究结果可知,深海微生物对材料腐蚀的影响结果有多样性、复杂性,这与深海中微生物种类的多样性及复杂性有密切的关联。
1.3 深海装备材料
高的静水压是深海环境的特点之一,静水压随着海深的增加而增加,因而对于深海装备而言,最重要的材料是耐压性能好的结构材料。它们应具有较高的屈服强度和弹性模量,目前,高强度合金钢、钛合金、陶瓷及陶瓷基复合材料等是深海装备所使用的主要结构材料[35].其中, 高强度合金钢是最重要、最关键的深海装备用结构材料。以潜艇耐压壳体材料为例,潜艇耐压壳体用钢材的屈服强度等级由第二次世界大战前的450 MPa级替换为第二次世界大战后的600 MPa级,其下潜深度得到提升;现代的潜艇耐压壳体用钢材的屈服强度等级多为1 000 MPa级,因而其下潜深度进一步增加。
美、日、英、俄等国家自第二次世界大战后就开始建立深海装备结构钢体系。美国研制了HY系列高强度合金钢,日本研制了NS系列高强度合金钢,英国研制了QT系列高强度合金钢,俄罗斯研制了AK系列高强度合金钢[35].我国也成功研制了屈服强度等级为400、450、600和800 MPa级的高强度合金钢[35].
深海装备用高强度合金钢在提高强度的同时,还须保证足够的韧性。在韧性评价时除夏比冲击试验外,往往还需要由爆炸试验或落锤试验来确定其止裂行为。另外,随着强度的提高,高强度合金钢焊接接头的延迟裂纹亦是一个重大问题[36].因此,在追求高强度时应严格限制甚至降低高强度合金钢中的含碳量,同时应通过增加适量的镍元素来保证其良好的韧性;加入适量的铬、钼、钒等元素改善其淬透性和抗回火软化性;在炼钢时应对铁水预脱硫脱磷,并采用真空精炼等措施以降低硫、磷和有害气体对高强度合金钢力学性能的危害。为保证装备的强度和韧性,在深海装备用高强度合金材料焊接时还要控制好道间温度和热输入焊接工艺参数。
钛合金材料具有高比强度、低密度、耐高温、耐腐蚀、无磁、透声和抗冲击振动等特点, 是具有研发前景的深海装备结构材料。俄罗斯的钛合金研究和应用水平处于国际领先地位,研发了船用钛合金系列,且用钛合金建造了首个潜艇耐压壳。目前, 深海潜水器的耐压壳体材料多采用钛合金材料,如俄罗斯阿尔法级攻击型核潜艇及塞拉级多用途核潜艇的耐压壳体均采用钛合金建造,其下潜深度可达800 m[35];美国“海崖”号深潜器的耐压壳体材料为Ti6Al2Nb1Ta0.8Mo钛合金,其下潜深度可达6 100 m;日本“深海6500”的耐压壳体材料为Ti6Al4VELI钛合金,其下潜深度可达6 500 m.此外,一些知名的深潜器的耐压壳体材料也都采用了钛合金,如法国的“鹦鹉螺”号、俄罗斯的“和平”号和我国的“蛟龙”号。
陶瓷材料具有高强度、大弹性模量、低密度、耐腐蚀、耐高温、电绝缘、非磁性和可透过辐射等特点,也是具有研发前景的深海装备结构材料。然而,陶瓷材料往往具有较大的脆性,在很大程度上限制了其应用。近年来的研究表明:利用高纯度超细原料粉末配合特殊的制备工艺可以获得性能更优的先进陶瓷材料;通过在陶瓷中合理添加第二相, 制备的陶瓷基复合材料的韧性可以得到大幅提升。这些先进陶瓷及陶瓷增韧技术的发展为陶瓷及陶瓷基复合材料在深海中的应用创造了必要的前提条件。美国海军利用氧化铝陶瓷基复合材料成功制成了深潜船壳,这类船壳不仅具备载人所需的安全性及可靠性,还具有一定的浮力。研究表明:潜深深度为6 096 m时,氧化铝陶瓷材质的耐压壳体的质量与排水量比值小于0.60,小于钛合金材质的耐压壳体的0.85;排水量相同时,氧化铝陶瓷比Ti6Al4V钛合金材质的壳体的有效载荷高166%;有效载荷相同时,相比于氧化铝陶瓷材质的耐压壳体,钛合金材质的耐压壳体的排水量必须增加50%,而其对应的质量则会增加83%[35-37].2009年,美国伍兹霍尔海洋研究所采用特制的新型轻量级陶瓷基复合材料研制的“海神”号机器人潜艇成功抵达了马里亚纳海沟最深处,下潜深度达10 902 m.
作者研究的Fe3Al/ZrO2(3Y)复合材料也是一类非常有应用潜力的深海装备用结构材料。氧化锆增韧陶瓷(ZTC)中室温力学性能最高的是四方氧化锆陶瓷(TZP),其抗弯强度和断裂韧性可达1.5 GPa和15 MPa·m1/2.然而,TZP材料除了自身的脆性外,由于应力诱导相变对温度因素很敏感,因而高温将增加TZP的稳定性,使相变增韧失效,其在低温环境下时效亦会导致其强度和韧性下降, 且其抗热震性能较差,因而大大限制了其应用[38].Fe3Al金属间化合物具有良好的热强塑性、较高的热导率、耐蚀性和耐磨性,但氢脆和加工性差是其产业化的严重障碍。Fe3Al与ZrO2的热膨胀系数比较接近,界面残余热应力小,将Fe3Al金属间化合物与ZrO2陶瓷复合, 过程如下:首先利用ZrO2颗粒对金属间化合物的间隔作用,阻止氢的扩散,抑制Fe3Al金属间化合物的氢脆;再利用这些消除了氢脆的金属间化合物颗粒对ZrO2陶瓷增韧和稳定形成一种两组元“互补增韧”的效应。设计制备的Fe3Al/ZrO2(3Y)复合材料的断裂韧性高达30 MPa·m1/2,为单相ZrO2(3Y)的2倍,抗弯强度达1.2 GPa,较单相ZrO2(3Y)提高了29%.
1.4 深海油气开发用材料现状
在深海油气资源开发的技术领域,20世纪70年代前,世界海洋油气开采水深不足100 m,到80年代初海洋油气开采水深提高到了300 m.目前,先进国家海洋油气开采水深已突破3 000 m,且生产水深可达2 500 m[39].深海油气勘探技术、深海油气钻井技术、深海油气开采技术、深海油气储运技术等都属于深海油气资源开发技术[40].目前,这项开发技术水平最先进的国家是美国。我国已经大规模开发的海上油气田主要集中在浅海区域,如面积7.7万平方公里、平均水深仅18 m的渤海海湾和包括涠洲油田、东方气田等南海海域近海的区域。此外,仅有唯一一个钻采深度超过3 000 m的荔湾油气田,但更为广阔的南海中部、西部和南部深海海域的油气资源开发还依然为0.
在深海石油钻采过程中,钻采部件将经受高压海水环境下的磨蚀与H2S、CO2等腐蚀介质的严重侵蚀,其耦合作用将使诸多部件在此严酷环境下的寿命甚至只有几个小时。如无磁钻铤的寿命只有200~500 h,是消耗品。国内市场目前对无磁钻铤的需求量为每年5 000余支,随着海洋资源钻采工程项目的不断增加,规模不断扩大,对高性能无磁钻铤等产品的需求还将增加。与国外同类型奥氏体氮强化不锈钢的无磁钻铤相比,国产无磁钻铤采用的Cr-Mn-N奥氏体不锈钢的最大问题是晶间腐蚀合格率和力学性能指标偏低。通过对比中原特钢W1813N和W2014N不锈钢与国外主流同类型产品的化学成分,可以看出二者之间的主要差异在于Cr、Mo、N含量明显偏低。中原特钢生产的W1813N和W2014N中,Cr、Mo、N的质量分数上限分别仅为14.0%、1%、0.35%,而大多数国外主流同类型产品中Cr的质量分数下限均高于18%;Mo的质量分数一般都控制在1%甚至2%以上,且N的质量分数下限一般都已达到0.5%~0.6%,甚至达到1%.Cr、Mo含量的增加可提升材料的耐腐蚀性能;N含量增加不仅可以增加材料的强度性能,还可以显著改善该类型不锈钢的抗局部腐蚀性能[16].
我国在深海油气资源开发技术领域使用材料的研发和国外先进国家之间的差距是显著的,国产相关材料的性能及使用深度远不及同类先进材料,这也直接制约了我国对深海油气资源开发的步伐。
1.5 固体浮力材料
固体浮力材料主要为水下作业装备提供所需的浮力,为适应深海高压的环境,高强度固体浮力材料从20世纪60年代末开始得到研制。美国、日本和俄罗斯等深潜技术发达的国家目前已经攻克了水下6 000 m用固体浮力材料的技术难题,并且已形成了系列标准。如美国Emerson & Cuming公司利用空心玻璃微珠与聚合物树脂复合研发出TG和DS型两种新型的两相复合泡沫材料,其中, DS型最大使用深度超过11 000 m[41].
在深海用固体浮力材料的研究开发方面,我国与深潜技术发达国家相比存在较大差距。研制初期,我国的浮力材料主要为聚氨酯泡沫、环氧树脂泡沫或其他发泡塑料,虽然其成本较低,但其耐压强度低,吸水率高,可靠性差,最大工作深度仅能达到400 m左右[42].随后,哈尔滨船舶工程学院采用空心树脂球、空心玻璃微珠、环氧树脂研制了密度0.55 g/cm3的泡沫复合固体浮力材料,其抗压强度为28.87 MPa.海洋化工研究院研制的可加工轻质复合材料亦有较好的性能,当复合材料的密度为0.55 g/cm3时,抗压强度为50 MPa,因而可用作4.5~5.0 km水深的浮力材料。国家海洋技术中心通过研发,目前已经在高强度轻质浮力材料的配方、工艺、成型技术等核心关键技术方面取得了突破,其成果已在深海领域得到广泛应用[43].笔者所在课题组采用一种具有独立知识产权的聚合物中空微球与聚合物树脂、空心玻璃微珠以适当比例混合,制备出一系列三组分固体浮力材料,密度为0.39~0.60 g/cm3,抗压强度为8.27~39.41 MPa,可满足用于0~3 500 m水深的海洋装备的浮力补偿。
1.6 深海防护材料
在防腐方面,目前主要的防腐措施有涂层防护技术、牺牲阳极技术等,涂层防护技术约占市场份额的95%左右,其中有机涂层占近九成, 因此,研究、开发、使用有机涂层对金属进行防护具有重要的实际意义。有机涂层在腐蚀过程中往往有如下作用:1)屏蔽作用,涂层阻止了腐蚀介质和材料界面的接触,隔断腐蚀电池的通路,增加腐蚀电阻;2)钝化作用,在涂料中加入某些钝化金属的物质,使金属表面形成金属的钝化膜防腐;3)牺牲阳极的作用,在涂料中加入活泼金属,当腐蚀介质进入涂层后将优先与这些活泼金属反应,保护基体金属。然而,现有涂料、涂层防护技术不能满足深海装备防护要求[44].在深海中,海水的巨大静水压使腐蚀介质在涂层中的渗透性增强,海水会进入涂层后会使活泼金属发生腐蚀,活泼金属在腐蚀后形成的产物往往使体积膨胀,且在产物与金属基体以及产物与周围树脂之间形成应力并会产生裂隙,裂隙的延伸、扩展使涂层粉化、脱离基体金属表面,从而使其防护作用失效[45-46].另外,深海特种海洋微生物、毒性气体亦会对涂层有较大的破坏作用。研制高性能的深海防护材料需要同时考虑材料的防腐蚀、防污着性能,还需要满足高静水压、温度变化等因素对防护材料的影响。因而,深海防护材料的研制已成为深海极端环境服役材料研制的热点之一。
多年来,笔者所在团队开展了深海材料蚀损模拟平台、钻采装备及部件防护材料与防护技术的研发,并取得了一些初步成果。另外,北京科技大学、钢铁研究总院、中国科学院金属研究所、东北大学、厦门大学、中国海洋大学、上海交通大学等团队也都在不同领域为深海装备材料的研发做出了重要贡献,并取得了一些重要进展,但总体而言,这方面的研究还没有形成一个完整的体系。
2 国内外研发趋势
进入21世纪,海洋科学技术发展十分迅猛,并呈以下发展趋势:1)研究方法趋于多学科交叉、渗透和综合,如从材料科学到装备制造,从基因技术到生物药物工程,从数值模拟技术到立体全球大生态等多学科的综合渗透交叉;2)研究重点趋向资源、环境等与人类生存与发展密切相关的重大问题,如在深海资源勘探利用、海洋空间利用、海洋生物基因、海洋环境监测等领域的问题;3)研究手段不断采用高新技术,并趋于全覆盖、立体化、自动化和信息化,如从卫星遥感、航空遥感、船舶监测、浮标,到潜标、深潜器, 再到海底的实时观测,形成全天候、全覆盖、立体的观测体系。但总体上,我国海洋科技水平与发达国家相比差距约10~15年,海洋科技对海洋经济的贡献率低;科技成果的转化率低;海洋科技投入不足;海洋科技力量和资源利用整合度低[47].其最直接的原因就是装备材料难以适应海洋特别是严酷的深海环境,适用于深海极端环境服役材料的研究和开发不足是制约深海技术发展的瓶颈。
深海材料研发的瓶颈在于研究深海环境试验平台的缺乏。因而,破解瓶颈的关键必须从深海研究平台的研发开始[48].2013年,上海市海洋局深海装备材料与防护工程技术研究中心在上海海事大学正式揭牌成立,这是国内首个深海材料研发平台。随后,中科院海洋新材料与应用技术重点实验室、中国科学院深海科学与工程研究所、浙江省海洋材料与防护技术重点实验室等与深海材料研发相关的平台陆续成立。这些深海材料研发平台的成立,对实验室开展深海材料的研发奠定了基础。
深海复杂严酷环境涵盖了物理极端环境、化学极端环境和生物极端环境。如此极端的恶劣环境,是深海服役材料与装备部件寿命极低的主因。由于深海环境自身的特点,因而要求深海材料必须具有高强度、高韧性、耐海水热液腐蚀、抗硫化腐蚀、抗微生物附着等特点[16].香山科学会议第423次学术讨论会以“深海极端环境下材料腐蚀科学理论与关键实验技术”为主题,首次明确地将深海极端环境服役材料的研发提到了研究日程[49];次年,中国工程院召开的“海洋工程材料研发、生产及应用研讨会”也明确指出进研发深海服役材料的迫切性;“十三五”国家深海高技术发展专项规划也已将“深海材料技术”列为发展重点。目前关于深海探索,虽然一些材料已经进入实际应用,但对材料的深海腐蚀规律与失效机制仍停留在表观认识,缺乏系统的研究,因此不能指导深海材料的制备与开发。这主要是由于深海的腐蚀因素众多,如高压、温度、pH值、化学成分、流速、生物环境等等,而这些参数都会对材料的腐蚀产生影响。因此,进一步准确研究材料的深海腐蚀规律与失效机制,对深海的开发意义重大。
蚀损是磨蚀和腐蚀共同作用对材料毁损的总称[16].深海的腐蚀和磨损常常是耦合发生的,而深海苛刻的环境对于服役金属材料的蚀损机制研究一直是我国材料研究的空白。尽管科研工作者已从浅海和小于3 000 m海深层面上开展了细致有效的研究工作,但很少报道在深海高压、低(高)温、有毒气体、极端微生物、大于3 000 m海深苛刻环境下服役金属材料的耦合蚀损行为研究。进一步进行深海苛刻环境金属材料蚀损机理的深入探索不仅具有重大的材料科学理论价值,而且也为我国深海工程金属材料的设计、制备、遴选提供理论和实验依据。
在深海极端环境服役材料研发时,应该联合实验室研究和深海实测实验技术对材料的服役安全性及服役寿命进行评价,这种联合实验技术对于材料深海服役机理的揭示有非常重要的意义;研发新型深海材料,提高其在深海中的适用深度,使其在深海极端环境下有更加优异的综合服役性能;进一步研发深海用防护材料,使其防腐、防污及适应深海复杂环境的能力进一步优化。
3 结语
深海极端环境服役材料的研发是深海战略发展的“瓶颈”。深海极端环境服役材料的研发需要基于更加完善的深海研究平台,通过在大于3 000 m海深以上的深海条件下进行研究,建立完善的金属材料深海蚀损机理;开展深海环境复杂因素耦合下的多因素耦合蚀损机理研究;研究深海装备结构材料在力学条件下的深海腐蚀及蚀损的机理;深海微生物菌样的培养也是深海极端环境服役材料研发的一个必要前提。
参考文献
[1]周云, 刘伯洋, 范春华。一种深海耐压氧化铝陶瓷空心浮球: ZL201410169989.9[P]. 2016-03-30.
[2]冯军, 李江海, 陈征, 等。 “海底黑烟囱”与生命起源述评[J]. 北京大学学报(自然科学版), 2004, 40(2): 318-325.FENG Jun, LI Jianghai, CHEN Zheng, et al. A review on black smokers and its implication for origin of life[J]. Acta Scientiarum Naturalium Universitatis Pekinensis, 2004, 40(2): 318-325. DOI:10.13209/j.0479-8023.2004.043
[3]WANG J, CHEN J, CHEN B, et al. Wear behaviors and wear mechanisms of several alloys under simulated deep-sea environment covering seawater hydrostatic pressure[J]. Tribology International, 2012, 56(3): 38-46. DOI:10.1016/j.triboint.2012.06.021
[4]ZHANG T, YANG Y, SHAO Y, et al. A stochastic analysis of the effect of hydrostatic pressure on the pit corrosion of Fe-20Cr alloy[J]. Electrochimica Acta, 2009, 54(15): 3915-3922. DOI:10.1016/j.electacta.2009.02.010
[5]BECCARIA A, POGGI G. Effects of some surface treatments on kinetics of aluminium corrosion in NaCl solutions at various hydrostatic pressures[J]. British Corrosion Journal, 2013, 21(1): 19-22. DOI:10.1179/000705986798272433
[6]BECCARIA A, POGGI G, ARFELLI M, et al. The effect of salt concentration on nickel corrosion behavior in slightly alkaline solutions at different hydrostatic pressures[J]. Corrosion Science, 1993, 24(35): 989-1005.
[7]BECCARIA A, POGGI G, CASTELLO P. Influence of passive film composition and sea water pressure on resistance to localized corrosion of some stainless steels in sea water[J]. British Corrosion Journal, 1995, 30(4): 283-287.
[8]屈少鹏, 程柏璋, 董丽华, 等。 2205钢在模拟深海热液区中的腐蚀行为[J]. 金属学报, 2018, 54(8): 1094-1104.QU Shaopeng, CHENG Bozhang, DONG Lihua, et al. Corrosion behavior of 2205 steel in simulated hydrothermal area[J]. Acta Metallurgica Sinica, 2018, 54(8): 1094-1104. DOI:10.11900/0412.1961.2017.00472
[9]SEEWALD J, CRUSE A, SACCOCIA P. Aqueous volatiles in hydrothermal liquids from the Main Endeavour Field, northern Juan de Fuca Ridge: temporal variability following earthquake activity[J]. Earth and Planetary Science Letters, 2003, 216(4): 575-590.DOI:10.1016/S0012-821X(03)00543-0
[10]DOUVILLE E, CHARLOU J, OELKERS E, et al. The rainbow vent fluids (36°14′N, MAR): the influence of ultramafic rocks and phase separation on trace metal content in Mid-Atlantic Ridge hydrothermal fluids[J]. Chemical Geology, 2002, 184(1): 37-48.
[11]JAMES R, GREEN D, STOCK M, et al. Composition of hydrothermal fluids and mineralogy of associated chimney material on the East Scotia Ridge back-arc spreading centre[J]. Geochimica et Cosmochimica Acta, 2014, 139: 47-71. DOI:10.1016/j.gca.2014.04.024
[12]VENKATESAN R, DWARAKADASA E, RAVINDRAN M. Biofilm formation on structural materials in deep sea environments[J]. Indian Journal of Engineering and Materials Science, 2003, 10(6): 486-491.
[13]BELLOU N, PAPATHANASSIOU E, DOBRETSOV S, et al. The effect of substratum type, orientation and depth on the development of bacterial deep-sea biofilm communities grown on artificial substrata deployed in the Eastern Mediterranean[J]. Biofouling, 2012, 28(2): 199-213. DOI:10.1080/08927014.2012.662675
[14]QU S, LI X, GAO K, et al. The effect of exposure angle on the corrosion behavior of low-carbon microalloyed steel under CO2 conditions[J]. Corrosion, 2015, 71(3): 343-351.
[15]ZHANG Y, PANG X, QU S. Discussion of the CO2 corrosion mechanism between low partial pressure and supercritical condition[J]. Corrosion Science, 2012, 59: 186-197. DOI:10.1016/j.corsci.2012.03.006
[16]尹衍升, 刘涛, 董丽华, 等。 深海极端环境服役材料[M]. 北京: 科学出版社, 2017.YIN Yansheng, LIU Tao, DONG Lihua, et al. Deep Sea Extreme Environmental Service Materials[M]. Beijing: Science Press, 2017.
[17]郭为民, 李文军, 陈光章。 材料深海环境腐蚀试验[J]. 装备环境工程, 2006, 3(1): 10-15.GUO Weimin, LI Wenjun, CHEN Guangzhang. Corrosion testing in the deep ocean[J]. Equipment Environmental Engineering, 2006, 3(1): 10-15. DOI:10.3969/j.issn.1672-9242.2006.01.002
[18]侯健, 郭为民, 邓春龙。 深海环境因素对碳钢腐蚀行为的影响[J]. 装备环境工程, 2008, 5(6): 82-84.HOU Jian, GUO Weimin, DENG Chunlong. Influences of deep sea environmental factors on corrosion behavior of carbon steel[J]. Equipment Environmental Engineering, 2008, 5(6): 82-84. DOI:10.3969/j.issn.1672-9242.2008.06.018
[19]LUCIANO G, LETARDI P, TRAVERSO P, et al. Corrosion behavior of Al, Cu, and Fe alloys in deep sea environment[J]. La Metallurgia Italiana, 2013, 105(1): 21-29.
[20]许立坤, 李文军, 陈光章。 深海腐蚀试验技术[J]. 海洋科学, 2005, 29(7): 1-3.XU Likun, LI Wenjun, CHEN Guangzhang. Deep sea corrosion test technique[J]. Marine Sciences, 2005, 29(7): 1-3. DOI:10.3969/j.issn.1000-3096.2005.07.001
[21]REINHART F M. Corrosion of metals and alloys in the deep ocean, TR-834[R]. California: Naval Construction Battalion Center, 1976.
[22]VENKATESAN R, VENKATASAMY M, BHASKARAN T, et al. Corrosion of ferrous alloys in deep sea environments[J]. British Corrosion Journal, 2002, 37(4): 257-266. DOI:10.1179/000705902225006633
[23]BECCARIA A, POGGI G. Influence of hydrostatic pressure on pitting of aluminium in sea water[J]. British Corrosion Journal, 2013, 20(4): 183-186.
[24]YANG Y, ZHANG T, SHAO Y, et al. Effect of hydrostatic pressure on the corrosion behaviour of Ni-Cr-Mo-V high strength steel[J]. Corrosion Science, 2010, 52(8): 2697-2706. DOI:10.1016/j.corsci.2010.04.025
[25]YANG Y, ZHANG T, SHAO Y, et al. New understanding of the effect of hydrostatic pressure on the corrosion of Ni-Cr-Mo-V high strength steel[J]. Corrosion Science, 2013, 73(8): 250-261.
[26]李世伦。深海超临界高温高压极端环境模拟与监控技术研究[D].杭州: 浙江大学, 2006. http://cdmd.cnki.com.cn/Article/CDMD-10335-2006175679.htm
[27]MEHANNA M, BASSEGUY R, DELIA M, et al. Effect of geobacter sulfurreducens on the microbial corrosion of mild steel, ferritic and austenitic stainless steels[J]. Corrosion Science, 2009, 51(11): 2596-2604. DOI:10.1016/j.corsci.2009.06.041
[28]SAN N, NAZIR H, DONMEZ G. Microbial corrosion of Ni-Cu alloys by aeromonas eucrenophila bacterium[J]. Corrosion Science, 2011, 53(6): 2216-2221. DOI:10.1016/j.corsci.2011.03.001
[29]NERCESSIAN D, DUVILLE F, DESIMONE M, et al. Metabolic turnover and catalase activity of biofilms of pseudomonas fluorescens (ATCC 17552) as related to copper corrosion[J]. Water Research, 2010, 44(8): 2592-2600. DOI:10.1016/j.watres.2010.01.014
[30]BHASKAR P, BHOSLE N. Bacterial extracellular polymeric substance (EPS): A carrier of heavy metals in the marine food-chain[J]. Environment International, 2006, 32(2): 191-198. DOI:10.1016/j.envint.2005.08.010
[31]BEVILAQUA D, ACCIARI H, BENEDETTI A, et al. Electrochemical noise analysis of bioleaching of bornite (Cu5FeS4) by acidithiobacillus ferrooxidans[J]. Hydrometallurgy, 2006, 83(1/2/3/4): 50-54.
[32]赵晓栋, 段继周, 武素茹, 等。 海水中硫酸盐还原菌作用下Q235钢表面腐蚀产物的形成和转化[J]. 中国腐蚀与防护学报, 2008, 28(5): 299-302.ZHAO Xiaodong, DUAN Jizhou, WU Suru, et al. Formation and transformation of surface corrosion products of Q235 steel influenced by sulfate-reducing bacteria in seawater[J]. Journal of Chinese Society for Corrosion and Protection, 2008, 28(5): 299-302. DOI:10.3969/j.issn.1005-4537.2008.05.009
[33]牛桂华, 尹衍升, 常雪婷。 海洋微生物对316不锈钢的电化学腐蚀行为[J]. 化学研究, 2008, 19(3): 83-90.NIU Guihua, YIN Yansheng, CHANG Xueting. Electrochemical corrosion behavior of 316 stainless steel in marine microbial medium[J]. Chemical Research, 2008, 19(3): 83-90. DOI:10.3969/j.issn.1008-1011.2008.03.023
[34]YUAN S, CHOONG A, PEHKONEN S. The influence of the marine aerobic pseudomonas strain on the corrosion of 70/30 Cu-Ni alloy[J]. Corrosion Science, 2007, 49(12): 4352-4385. DOI:10.1016/j.corsci.2007.04.009
[35]冯立超, 乔斌, 贺毅强, 等。 深海装备材料之陶瓷基复合材料的研究进展[J]. 热加工工艺, 2012, 41(22): 132-136.FENG Lichao, QIAO Bin, HE Yiqiang, et al. Development of ceramic matrix composite used in deep-sea equipment[J]. Material and Heat Treatment, 2012, 41(22): 132-136.
[36]尹士科, 何长红, 李亚琳。 美国和日本的潜艇用钢及其焊接材料[J]. 材料开发与应用, 2008, 23(1): 58-65.YIN Shike, HE Changhong, LI Yalin. Submarine steel and welding consumables used in American and Japan[J]. Development and Application of Materials, 2008, 23(1): 58-65. DOI:10.3969/j.issn.1003-1545.2008.01.015
[37]STACHIEW J, KURKCHUBASCHE R. Ceramics show promise in deep submergence housings[J]. Sea Technology, 1993, 34(12): 35-41.
[38]李嘉, 尹衍升, 刘俊友, 等。 3Y-TZP/Fe-Al复合材料化学相容性分析[J]. 无机材料学报, 2004, 19(4): 859-864.LI Jia, YIN Yansheng, LIU Junyou, et al. Chemically compatibility analysis of 3Y-TZP/Fe-Al composite[J]. Journal of Inorganic Materials, 2004, 19(4): 859-864. DOI:10.3321/j.issn:1000-324X.2004.04.025
[39]李成杰。深海阴极保护过程研究及其在温跃层环境下数学模型的建立[D].青岛: 中国海洋大学, 2014. http://cdmd.cnki.com.cn/Article/CDMD-10423-1014369114.htm
[40]刘淮。 国外深海技术发展研究(上)[J]. 船艇, 2006, 258(10): 6-18.LIU Huai. Research on development of overseas deep ocean technologies (I)[J]. Ships and Yachts, 2006, 258(10): 6-18.
[41]尹衍升, 黄翔, 董丽华。 海洋工程材料学[M]. 北京: 科学出版社, 2008.YIN Yansheng, HUANG Xiang, DONG Lihua. Marine Engineering Materials Science[M]. Beijing: Science Press, 2008.
[42]张德志。 国内外高强度浮力材料的现状[J]. 声学与电子工程, 2003(3): 45-47.ZHANG Dezhi. Current status of high strength float materials at home and abroad[J]. Acoustics and Electronics Engineering, 2003(3): 45-47.
[43]刘淑青。 高强度轻质浮力材料研究[J]. 海洋技术, 2007, 26(4): 118-120.LIU Shuqing. Research on high-intensity light buoyancy materials[J]. Ocean Technology, 2007, 26(4): 118-120. DOI:10.3969/j.issn.1003-2029.2007.04.031
[44]LIU L, CUI Y, LI Y, et al. Failure behavior of nano-SiO2 fillers epoxy coating under hydrostatic pressure[J]. Electrochimica Acta, 2012, 62: 42-50. DOI:10.1016/j.electacta.2011.11.067
[45]FAY F, CARTEAU D, LINOSSIER I, et al. Evaluation of anti-microfouling activity of marine paints by microscopical techniques[J]. Progress in Organic Coatings, 2011, 72(3): 579-585. DOI:10.1016/j.porgcoat.2011.04.002
[46]KANDEMIR E, ALYURUK H, CAVAS L. Fouling organisms on the rebars and protection by antifouling paint[J]. Anti-Corrosion Methods and Materials, 2012, 59(5): 215-219. DOI:10.1108/00035591211265442
[47]海洋科学和技术综合专题组。 2020年中国海洋科学和技术发展研究[C]//2020年中国科学和技术发展研究暨科学家讨论会。北京: [s.n.], 2004: 726-750.The Comprehensive Task Force of Marine Science and Technology. Research on China′s marine science and technology development in 2020[C]//Research on China′s Scientific and Technological Development in 2020-Scientists Symposium. Beijing: [s.n.], 2004: 726-750.
[48]屈少鹏, 范春华, 李雪莹, 等。上海海事大学关于深海材料腐蚀与防护研究平台与装备的进展[C]//第二届海洋材料腐蚀与防护大会。北京: [s.n.], 2015.QU Shaopeng, FAN Chunhua, LI Xueying, et al. Progress of the research platform and equipment for corrosion and protection of deep-sea materials in Shanghai Maritime University[C]//2nd Marine Materials Corrosion and Protection Conference. Beijing: [s.n.], 2015.
[49]杨炳忻。 香山科学会议第420-424次学术讨论会简述[J]. 中国基础科学, 2012, 14(4): 22-29.YANG Bingxin. Brief introduction to Xiangshan science conferences of Nos. 420-424[J]. China Basic Science, 2012, 14(4): 22-29. DOI:10.3969/j.issn.1009-2412.2012.04.004
免责声明:本网站所转载的文字、图片与视频资料版权归原创作者所有,如果涉及侵权,请第一时间联系本网删除。
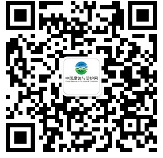
官方微信
《中国腐蚀与防护网电子期刊》征订启事
- 投稿联系:编辑部
- 电话:010-62316606-806
- 邮箱:fsfhzy666@163.com
- 中国腐蚀与防护网官方QQ群:140808414