0 前言
AA6061-T6铝合金因低密度、良好的可成型性、可焊接性和较高比强度等优势[1-2],越来越多的应用于汽车工业中,如汽缸体、汽车冷气设备、阀门和燃烧室等,这些零件工作环境的特殊性,易引发强烈的空化现象,导致零件表面发生空蚀破坏而失效[3]。零部件在液体环境中高速运动时,较大的压差变化导致零部件表面生成空化泡,空化泡反复生长和溃灭而引起的周期性冲击波造成零部件表面损伤,即空蚀现象[4]。空蚀是流体环境中合金表面常见的破坏方式之一,也是不可避免的问题。
先前的研究表明金属表面性能对抗空蚀性能有较大影响,可以通过增强合金的表面性能来改善合金的整体性能和可靠性[5]。因此,大量表面改性技术被应用于改善合金的抗空蚀性能,例如等离子渗氮[6]、高速氧燃料喷涂[7]、微弧氧化[8] 等表面涂层技术,但这些表面改性技术在工艺上存在一定的局限性,包括与基底的结合力弱、时间和能量消耗高、环境不友好、自动化困难和热处理程序复杂等[9]。相较于以上表面改性技术,塑性变形技术[10] 因操作简单、成本低等特点在工业中广泛应用,塑性变形技术通过在材料表面引入严重塑性变形,细化材料表层的晶粒、植入有益的残余压应力并增加位错密度来改善材料的表面性能。 TONG等[11] 采用LSP成功将AA5083的表面抗空蚀性能提升1.45~2.13倍,并认为强化后表面形成的细晶层和压缩残余应力提高材料的抗空蚀性能。 HAJIAN等[12] 采用FSP对AISI 316L进行强化,发现材料的抗空蚀性能随晶粒细化而增强,并认为空蚀是由包括晶界破坏、微裂纹和疲劳裂纹扩展在内的一组机制控制的。 LI [13]也证实晶粒细化可以提高材料的抗空蚀性能。超声波冲击技术[14-16](UIT)近年来也被应用于表面强化,研究表明该技术在制备纳米晶的同时还可以植入较高的残余压应力,消除表面的微观缺陷以增强材料表面的性能,但对材料抗空蚀性能的研究鲜有报道。
文中研究采用超声冲击技术对AA6061-T6进行表面强化处理,以改善其表面的抗空蚀性能。对超声冲击技术处理后的AA6061-T6试样表层微观组织、硬度及残余应力分布等进行表征和测定,并采用超声振动空蚀方法对其抗空蚀性能进行评价,分析强化后空蚀损伤机制。
1 试验
1.1 试验过程
试验材料选取AA6061-T6,其化学成分见表1, 尺寸为 Φ30mm×50mm。强化处理前使用2000号砂纸对端面进行打磨。图1为超声波冲击表面强化装置,通过三坐标移动平台来实现撞针和试样的相对运动。同时在超声波冲击强化过程中通入氩气以防止铝合金氧化。超声波冲击表面强化采用以下参数: 频率20kHz;振幅10 μm;撞针移动速度60mm/min; 相邻步距为0.07mm。
表1 AA6061-T6的化学成分
图1 超声波冲击表面强化示意图
1.2 微观组织及力学性能表征
用电火花线切割切取强化后的试样,并用环氧树脂镶嵌。将试样横截面分别用400~2000号砂纸打磨并抛光至镜面,用NaOH试剂进行蚀,然后采用金相显微镜观察表面改性层微观组织。通过X射线衍射仪(XRD)分析对强化前后试样表面进行物相鉴定及择优取向分析,X射线衍射仪采用Cu靶, 2θ 的范围是30°~100°。通过X射线衍射法(Proto LXRD微区应力仪)来测定试样残余应力,并结合电解抛光法测量试样不同深度的残余应力。使用PV-1000维氏硬度计对未处理和UIT试样进行表面和沿截面方向上的硬度进行测量,测量的时候采用100g的压力持续施加14s,测量数据为3次平均值。使用MTS G200纳米压痕仪测量未处理和UIT试样表面的弹性模量。
1.3 空蚀性能测试
抗空蚀性能评价采用超声振动空蚀测试方法。用电火花线切割机从未进行表面强化的试样和UIT表面强化处理后的试样切出 Φ15mm × 6mm圆柱。如图2所示,超声振动试验台的设计搭建参照标准ASTM G32-16 [17] 的规定,空蚀采用间接空蚀的方式。超声振子直径为 Φ20mm,振动频率为20kHz,振幅45 μm。试验时,超声振子端面伸入水面以下15mm,下端面距离空蚀试样上表面1mm [18],空蚀测试溶液为去离子水,并采用循环冷却水的方式将空蚀介质温度保持在(25±2)℃。在定期空蚀试验后,采用精度为0.01mg的天平称量试样质量损失,试样每次称重之前进行超声清洗并用电吹风烘干。为分析AA6061-T6的空蚀损伤机理,通过扫描电子显微镜S4800观察试验后试样的表面形貌。
图2 超声振动空蚀示意图
2 结果与讨论
2.1 微观组织分析
UIT试样的截面显微组织图如图3所示。试样的表层形成了约140 μm的塑性形变层,分别是厚度约为50 μm的晶粒细化层和90 μm的过渡层。研究表明塑性形变层对材料的机械性能具有重要影响[19]。在晶粒细化层内,NaOH试剂腐蚀后留下的腐蚀坑少于未处理试样内部的,且其尺寸也小于基体层内的。与此同时,晶粒细化层内的晶界未能腐蚀出来,而过渡层内的部分晶界较为清晰,其原因可能是晶粒细化导致塑性变形层和过渡层的耐腐蚀性能存在较大差异[20]。随着深度的增加,塑性变形逐渐减少,过渡层和基体层没有明确分界线。在过渡层内,可以明显地看到晶粒沿撞针移动方向被拉长弯曲的现象。
图3 超声波冲击后试样截面金相组织
如图4所示,未处理试样表面的择优取向为(200),而强化后表面的择优取向则变为(111),同时出现了少量的(220)和(222)取向,表明在超声波冲击强化过程中,材料表面发生严重塑性变形,导致原始取向逐渐减弱并形成新的取向。同时强化试样的(111)衍射峰变宽表明严重塑性变形会使试样表面晶粒细化。 UIT试样和未处理试样表层残余应力分布如图5所示,未处理试样表面均为较小的残余拉应力,而UIT强化后试样表面则有较大的残余压应力,最大残余压应力为表面的-259MPa,随深度增加残余应力逐渐减小,残余压应力层深度约为700 μm。
图4 UIT强化前后试样XRD图谱
图5 UIT强化前后残余应力
2.2 硬度分析
如图6所示,分别测量了未处理和UIT试样表面和沿深度方向的显微硬度。 UIT强化后材料的表面硬度达到168.3HV,比未处理试样表面硬度的93.1HV提高了80.7%。表2所示为UIT处理前后AA60-T6表面的弹性模量,结果表明UIT试样表面弹性模量由未处理时的65.7GPa变为UIT强化后的97.45GPa,提高了约48.3%。 UIT使得铝合金表面发生严重塑性变形,导致位错密度增大和晶粒细化,晶粒细化后增多的晶界有利于阻止位错运动,从而提高了金属的变形抗力,因此材料的表面硬度得到较大提升[21],UIT试样表面显微硬度压痕面积显著减小,同时UIT强化后的硬化层可达140 μm。
图6 AA6061-T6处理前后的显微硬度
表2 UIT处理前后表面弹性模量
2.3 空蚀性能分析
2.3.1 空蚀性能测试结果
未处理试样和UIT的试样空蚀累计损失质量如图7所示。累计质量损失的变化大致可以分为三个时期,即因表面塑性变形积累而质量损失几乎可以忽略的孕育期;孕育期过后,会经历一个重量损失迅速增加的上升期;质量损失最后进入一个稳定期,该阶段质量损失以及失重率达到稳定。从图7a可以看出,未处理试样几乎没有孕育期,也就是说未处理试样会在空蚀测试开始后迅速失去质量。但是, UIT试样的孕育期约为10min。这主要归因于晶粒细化导致表层材料的强度极限提高。试样在经过孕育期之后进入上升期,表面质量的损失迅速增加。而在稳定期中(120~300min),未处理试样和UIT试样表面的质量损失率均逐渐稳定下来。经过300min的空蚀,未处理试样、UIT的累积失重分别为215.26mg和91.28mg,UIT试样的抗空蚀性能约为未处理试样的2.36倍。在空蚀过程中,UIT试样表层的残余压应力会阻碍裂纹的产生和扩展,从而减少了空化损伤。通过XRD测试结果可以看出,UIT试样表面的择优取向为( 111) 晶面, 相对于(200)晶面,(111)晶面有利于增强铝合金的加工硬化指数,使得材料在塑性变形阶段可吸收更多变形能量,延缓表面损伤,这也是提高UIT试样抗空蚀能力的原因之一[22-23]。
图7 未处理试样与UIT试样空蚀累计失重
2.3.2 空蚀机制分析
如图8所示,从空蚀60min表面不难看出,UIT试样表面腐蚀程度明显优于未处理试样。试样表面质量损失均为局部表面损伤失重的累积。图8a为60min未处理试样表面的腐蚀形貌,可以看到表面蚀坑较多且尺寸较大,还分布着孔洞和裂纹;而强化后的试样表面则相对平整光滑,如图8b所示,试样表面局部有凹坑,但其尺寸相较于未处理试样要小很多,损伤深度也要更浅,UIT试样具有较大的表面显微硬度,空化泡破碎时难以对表面造成严重的损伤。 UIT试样表面有较多细小的水平方向裂纹,但未观察到明显的孔洞,表明UIT强化过程中严重塑性变形使得材料表层致密性增加,空蚀损伤过程中裂纹难以向下发展并造成孔洞。图8c所示,经过300min的空蚀,未处理试样表面被腐蚀掉了大量材料,腐蚀坑尺寸变小,但表面的孔洞、裂纹等缺陷增加,这些缺陷是空蚀作用的主要位置,可以加剧空蚀损伤现象。从表面塑性变形和裂纹来看,未处理试样的主要空蚀机理是韧性断裂破坏。而UIT试样表面蚀坑较浅,表面孔洞和裂纹较少,局部可以看到有条纹和凹坑的存在,证明空蚀过程中有塑性变形存在。同时还观察到一些碎屑,结合表面裂纹等现象, 可以看出空蚀过程中有脆性断裂。
图8 强化前后试样不同空蚀时间表面形貌
如图9所示,凹坑内部放大后还观察到疲劳条纹,这就表明UIT试样空蚀机理包括疲劳破坏, GOTTARDI [24]的铝合金空蚀研究也得到类似结论。空化泡在溃灭过程中引起的载荷反复冲击材料表面而引起疲劳破坏,在形成疲劳条纹的同时还会导致滑移带的产生,滑移带则是裂纹的成核位置,裂纹形成导致表面被腐蚀。所以,抑制滑移带的形成和发展有利于减少裂纹的成核位置,进而提高材料表面的抗空蚀性能。晶界的增多有利于阻止滑移带的扩展。 XRD结果显示UIT试样表层晶粒细化,晶粒细化后晶界明显增多,这就使得裂纹生长变得更加困难。
为了更加清晰地了解空泡腐蚀的破坏机理,对300min空蚀后的试样截面进行观察。如图10所示,所有表面都存在一些凹坑和众多微小的裂纹,未处理试样的表面轮廓起伏比UIT试样大。由图8c可看出,未处理试样表面存在较多由空蚀过程中造成沿深度方向的孔洞,在图10a观察到的孔也验证了这一现象,孔的形成为有利于空泡腐蚀过程中裂纹的传播,裂纹不断生长最终连接在一起造成材料的剥落。而UIT试样表面的凹坑尺寸较小,内部的裂纹较短,且多沿水平方向传播。 UIT试样由于表层晶粒细化和较高的残余压应力增强了表面塑性变形和应变硬化,从而抑制了裂纹深度方向的扩展和水平方向的聚合。由图10b可看出UIT试样空蚀6h后表面蚀坑深度约100 μm,而实际空蚀深度应该大于100 μm,这表明UIT制备的晶粒细化层被完全腐蚀,仅过渡层可能还有部分剩余,过渡层的抗空蚀能力较晶粒细化层有所下降,从图8d中也能看出表面局部蚀坑的尺寸明显增大,与图8a中蚀坑类似,表明UIT试样在塑性变形层大部分腐蚀后,其表面损伤与未处理试样的空蚀初期状态类似。截面形貌分析进一步证实UIT可以有效提高AA6061-T6的抗空蚀性能。
图9 UIT试样空蚀损伤特征
图10 未处理试样与强化试样300min空蚀截面形貌
3 结论
(1) UIT强化处理在材料表面形成了约50 μm组织致密、硬度较大的晶粒细化层和90 μm的过渡层。 XRD结果表明,UIT使得AA 6061-T6表面的晶粒细化,并使得材料表面的择优取向晶面由(200) 转变为(111)。
(2) 与未处理试样相比,UIT试样的空蚀性能提高了约2.36倍,表面较高的硬度和残余压应力提高材料的抗冲击载荷能力,延长试样的空蚀孕育期; 表层晶粒细化,减少表面气孔缺陷,裂纹扩展受到抑制,蚀坑尺寸减小。
(3) 未处理试样的空蚀损伤形式为韧性断裂破坏,而UIT强化后的试样则可以观察到脆性断裂和疲劳破坏的痕迹,表明UIT强化后提高了表层材料的强度极限。
参考文献
[1] TORBATI-SARRAF H,TORBATI-SARRAF S A,CHAWLA N,et al.A comparative study of corrosion behavior of an additively manufactured Al-6061 RAM2 with extruded Al-6061 T6 [J].Corrosion Science,2020,174:108838.
[2] ZHANG L,ZHONG H,LI S,et al.Microstructure,mechanical properties and fatigue crack growth behavior of friction stir welded joint of 6061-T6 aluminum alloy [J].International Journal of Fatigue,2020,135:105556.
[3] GOTTARDI G,TOCCI M,MONTESANO L,et al.Cavitation erosion behaviour of an innovative aluminium alloy for hybrid aluminium forging[J].Wear,2018,394-395:1-10.
[4] 李海斌,刘树龙,刘义,等.Ti-6Al-4V 合金表面渗层制备及空蚀性能研究[J].表面技术,2020,49(4):324-331.LI H B,LIU S L,LIU Y et al,Preparation and cavitation erosion of surface diffusion coating on Ti-6Al-4V alloy [J].Surface Technology,2020,49(4):324-331.(in Chinese)
[5] 郭辉,刘强,刘满平,等.6061 铝合金ECAP变形前后的空泡腐蚀试验研究[J].轻合金加工技术,2013,41(12):42-48.GUO H,LIU Q,LIU M P et al,The experimental study on the cavitation erosion of 6061 aluminum alloy before and after ECAP [J].Light Alloy Fabrication Technology,2013,41(12):42-48.(in Chinese)
[6] DONG Z,ZHOU T,LIU J,et al.Cavitation erosion behaviors ofsurface chromizing layer on 316L stainless steel[J].Ultrasonics Sonochemistry,2019,58:104668.
[7] LIU X,KANG J,YUE W,et al.Cavitation erosion behavior of HVOF sprayed WC-10Co4Cr cermet coatings in simulated sea water[J].Ocean Engineering,2019,190:106449.
[8] WEN L,WANG Y,ZHOU Y,et al.Microstructure and corrosion resistance of modified 2024 Al alloy using surface mechanical attrition treatment combined with microarc oxidation process[J].Corrosion Science,2011,53(1):473-480.
[9] KWOK C T,MAN H C,CHENG F T,et al.Developments in laser-based surface engineering processes:With particular reference to protection against cavitation erosion[J].Surface & Coatings Technology,2016,291:189-204.
[10] 尹雁飞,贾蔚菊,李思兰,等.剧烈塑性变形制备的纳米金属材料的力学行为[J].中国材料进展,2019,38(10):1030-1036.LUO Y F,JIA W J,LI S L,et al.Mechanical behavior of nanostructured metallic materials prepared by severe plastic deformation[J].Materials China,2019,38(10):1030-1036.(in Chinese)
[11] TONG Z P,JIAO J,ZHOU W,et al.Improvement in cavitation erosion resistance of AA5083 aluminium alloy by laser shock processing[J].Surface and Coatings Technology,2019,377:124799.
[12] HAJIAN M,ABDOLLAH-ZADEH A,REZAEI-NEJAD S S,et al.Improvement in cavitation erosion resistance of AISI 316L stainless steel by friction stir processing [J].Applied Surface Science,2014,308:184-192.
[13] LI Y,LIAN Y,SUN Y.Cavitation erosion behavior of friction stir processed nickel aluminum bronze[J].Journal of Alloys and Compounds,2019,795:233-240.
[14] ZAPOROZHETS I,MORDYUK B N,DORDIENKO N,et al.Influence of surface ultrasonic impact treatment on texture evolution and elastic properties in the volume of Zr1Nb alloy[J].Surface and Coatings Technology,2020,403:126397.
[15] DAAVARI M,SADOUGH VANINI S A.Corrosion fatigue enhancement of welded steel pipes by ultrasonic impact treatment [J].Materials Letters,2015,139:462-466.
[16] 曹小建,片英植,金江,等.超声冲击强化对TC4钛合金拉压疲劳性能的影响 [J].中国表面工程,2017,30(2):48-55.CAO X J,PYUN Y S,JIN J,et al.Effects of ultrasonic impact modification on tension-compression fatigue behavior of TC4[J].China Surface Engineering,2017,30(2):48-55.(in Chinese)
[17] American Society of Testing Materials.ASTM G32-2010. Standard test method for cavitation erosion using vibratory apparatus[S].PA:West Conshohocken,2010.
[18] CHEN F,DU J,ZHOU S.Cavitation erosion behaviour of incoloy alloy 865 in NaCl solution using ultrasonic vibration[J].Journal of Alloys and Compounds,2020,831:154783.
[19] SUN Y,WANG H,LIU W,et al.Improvement of surface resistance to cavitation corrosion of nickel aluminum bronze by electropulsing-assisted ultrasonic surface rolling process [J].Surface and Coatings Technology,2019,368:215-223.
[20] PANDEY V,SINGH J K,CHATTOPADHYAY K,et al.Influence of ultrasonic shot peening on corrosion behavior of 7075 aluminum alloy[J].Journal of Alloys and Compounds,2017,723:826-840.
[21] 王妍洁.7075 铝合金超声喷丸表面改性研究[D].济南:山东大学,2017.WANG Y J.Surface modification of 7075 aluminum alloy by ultrasonic shot peening[D].Jinan:Shandong University,2017(in Chinese).
[22] SUN Q Q,HAN Q Y,WANG S,et al.Microstructure,corrosion behaviour and thermal stability of AA 7150 after ultrasonic shot peening[J].Surface & Coatings Technology,2020,398:126127.
[23] 周琱玉.冷轧AA6061铝合金的织构、微米压痕与腐蚀性能研究[D].太原:太原理工大学,2018.ZHOU D Y.The textures,microindentation and corrosion properties of cold-rolled AA6061 aluminum alloy[D].Taiyuan:Taiyuan University of Technology,2018.(in Chinese)
[24] GOTTARDI G,TOCCI M,MONTESANO L,et al.Cavitation erosion behaviour of an innovative aluminium alloy for hybrid aluminium forging[J].Wear,2018,394-395:1-10.
免责声明:本网站所转载的文字、图片与视频资料版权归原创作者所有,如果涉及侵权,请第一时间联系本网删除。
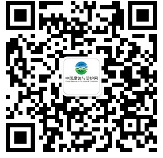
官方微信
《中国腐蚀与防护网电子期刊》征订启事
- 投稿联系:编辑部
- 电话:010-62316606-806
- 邮箱:fsfhzy666@163.com
- 中国腐蚀与防护网官方QQ群:140808414