高熵合金
由于独特的耐磨性,较高的强度,高温热稳定性,高伸长率,极大的抗疲劳和抗断裂性等,受到研究者的广泛关注。CANTOR和YEH等研究人员于2004年分别报道了多主元素合金和高熵合金(HEAs)。与传统的合金设计理念不同,高熵合金不仅基于一种或两种元素,而是至少含有五种主要元素,其原子分数相等或接近,溶质与溶剂之间没有明显差异,根据现有的物理冶金学和相图,这种多元素合金可能会产生许多相和金属间化合物,导致复杂的微观结构难以分析和设计,但实际上,高熵合金因熵高促进了具有简单结构的随机固溶体相的形成,例如面心立方(fcc)、体心立方(bcc)和密排六方(hcp)结构,进而降低了相数,同时具有优良的性能,故高熵合金的研究亟待广泛开展。
高熵合金的研究现状
1 高熵合金分类
高熵合金主要分为金属类高熵合金和复合类高熵合金两种。高熵合金在性能方面具有“鸡尾酒”效应,通过调整所含元素种类、配比,可得到具有轻质、难熔等优异性能的高熵合金。
金属类高熵合金主要有AlCrFeCoNiCu体系、VNbMoTaW体系以及其他金属体系,金属类高熵合金所含元素除了主要金属元素AlTiCrFeCoNiCu等外,还有类金属元素SiB等。复合类高熵合金通过引入细小硬质颗粒进一步增强多主元高熵合金的力学性能。主要有陶瓷增强相(TiCTiBTiB2B4C)、金属间化合物(TiAlTi3AlTi5Si3)、氧化物(Al2O3、稀土元素氧化物)以及氮化物(AlNTiN)等。
2 理论研究
由于合金元素种类过多会生成很多化合物尤其是脆性金属间化合物,增加合金脆性,因而合金元素种类越少越好,而合金元素过少又会降低合金性能,故合金元素种类及比例设计与合金性能的良好兼容就特别重要,需要通过理论分析、建模仿真等手段为合金成分试验提供理论基础。
高熵合金的建模仿真理论研究以材料计算为主,目前关于高熵合金计算模拟的方法主要有分子动力学第一性原理仿真(AIMD)、热力学第一性原理仿真(AITD)、密度泛函理论(DFT)、相图计算法(CALPHAD)、新相分计算法(New PHACOMP)等。
GAO等利用动力学第一性原理仿真法预测得出,化学相互作用和原子扩散系数与凝固过程中的初级结晶密切相关,且该方法可用于鉴定单相高熵合金的组成。
MA等利用热力学第一性原理仿真法研究了电子、振动、磁性熵对CoCrFeMnNi系高熵合金相稳定性的影响,结果表明仿真结果与试验结果一致。
ZHANG等应用密度泛函理论分析了AlCoCrCuFeNi系高熵合金的结合力及弹性。
MA等通过理论和试验相结合的手段评估了相图计算法对FexMn62-xNi30Co6Cr2高熵合金的预测效果,发现相图计算法可以非常稳定地评估相的稳定性,且与试验结果吻合良好。
GUO等利用新相分计算法根据高熵合金组成元素的基本特性预测了相稳定性,研究了高熵合金相稳定性与理化/热力学性质之间的关系,发现混合焓是控制固溶体或化合物形成的关键因素,且价电子浓度对高熵合金相稳定性具有一定影响。
3 性能研究
01.力学性能
高熵合金通常具有fcc结构,且具有良好的强度和延展性。具有bcc结构的高熵合金,其屈服强度非常高,与块状金属玻璃相当。具有双相结构的高熵合金不仅有更好的强度和延展性,还有良好的拉伸性能,但随着主要元素数量的增加,其强度由于固熔体硬化而增加,延展性降低。
MA等研究了AlCoCrFeNbxNi高熵合金(HEAs)的微观结构和性能,合金的微观结构从亚共晶变为过共晶,压缩屈服强度和维氏硬度随着Nb含量的增加呈近似线性增加。
OTTO等通过电弧熔化制备了CoCrFeMnNi高熵合金,当试验温度达到600℃时,屈服强度随着晶粒尺寸的减小而增加,晶粒尺寸越小,极限抗拉强度越大,但其增长程度小于屈服强度。随着温度的降低,合金显示出良好的屈服强度和极限抗拉强度,断后伸长率也有所增加。
研究表明,高熵合金薄膜涂层的性能也明显优于普通合金。
CHANG等通过改变衬底温度研究了直流反应磁控溅射技术制备的(AlCrNbSiTiV)N高熵合金薄膜涂层的结构、力学性能和切削加工性能。结果表明,薄膜涂层无微孔,具有典型的柱状微观结构和良好的黏结强度,使用(AlCrNbSiTiV)N合金涂层刀具进行车削后,加工表面粗糙度和刀具磨损明显减少。
02.物理化学性能
除了在力学性能方面具有优异的表现,高熵合金在磁性、耐蚀性、热稳定性等物理化学性能上也具有出色的发挥。
几乎所有的磁性合金都含有Co Fe Ni元素。CoFeNi合金是一种具有fcc结构的合金,具有磁性,同样含有Co Fe Ni的高熵合金也具有优异的磁性。
ZUO等采用定向凝固技术通过控制晶粒形态和晶体结构纹理来改善FeCoNiAl0.2Si0.2合金的软磁性能,研究表明,制备的FeCoNiAl0.2Si0.2合金具有柱状晶粒,施加不同方向的磁场,合金具有磁各向异性,当取出速度非常慢或快速取出时,可以获得优异的综合磁性能。
在耐蚀性方面,高熵合金的腐蚀电位较高,具有更好的耐蚀性。
YE等采用激光熔覆法制备了CrMnFeCoNi高熵合金涂层并对其性能进行了分析,结果表明,涂层的耐蚀性优于A36钢,其腐蚀电流密度低于304不锈钢。
在热稳定性方面,含有Nb Mo Ta W的高熵合金具有比耐火金属钨更好的热稳定性,这类合金是一种制造高温下运行的纳米级设备的新型材料。
HUANG等使用射频溅射系统将AlCoCrCu0.5NiFe高熵合金的溅射氧化膜沉积在硅晶片上,退火试验表明,氧化膜的电阻率和厚度都随氧含量的增加而降低,氧的质量分数为30%时硬度达到最大值,在退火过程中薄膜没有产生其他相,具有较好的热稳定性。
高熵合金的制备方法
1 电弧熔炼
电弧熔炼是电极之间或电极与物料之间通电产生电弧来熔炼金属的电热冶金方法,电弧可以通过施加交流和直流电流产生。但是,由于交流电不稳定,可能会中断熔炼,所以直流电在电弧熔炼中倍受青睐。
WU等通过电弧炉熔化纯金属来制备合金锭,然后将熔化的合金滴铸到水冷铜模具中,高温处理冷却后得到体心立方(bcc)结构的新型耐火Hf25Nb25Ti25Zr25高熵合金。研究表明,在氩气气氛中1300℃下恒温6h为最佳试验条件。
LIU等通过电弧熔化制备标称组成为Fe20Co20Ni20Cr20Mn20(原子百分比)的锭,将锭重新熔化四次得到了具有单面心立方结构的FeCoNiCrMn高熵合金,研究表明,当温度大于850℃时,晶粒粗化且表现出典型的幂律行为,晶界运动受溶质-阻力机制控制,随着晶粒生长,合金软化,合金的强度服从经典的Hall-Petch关系。
电弧熔炼是生产块状合金的主要方法,但由于合金组成的复杂性以及各元素熔点的巨大差异,在熔融固化和冷却过程中会发生明显的元素偏析,与传统合金相比,铸态样品会有明显的铸造缺陷,需要进行后续处理。电弧炉熔炼耗电多,但是熔化固体炉料的能力很强,在以后的发展中应多采用直流电弧炉,这种方式不会产生如三相交流电弧炉的较大闪烁,对电网冲击小,对电极损耗较低,且热效率高,大大较少了合金制备过程中的损耗。
2 感应熔炼
感应熔炼的原理是电磁感应,将导线绕成环状,施加电流,物体在线圈内,因电磁效应,被加热物体内产生与线圈反向的电流,进而形成涡流,物体因其自身电阻被加热升温,达到熔炼效果。
LAURENT等在水冷铜坩埚中(氦气气氛)采用高频电磁感应熔炼制备合金,最后通过抽吸铸造或双辊铸造以使CrMnFeCoNi铸锭成形。研究表明,CrMnFeCoNi合金为面心立方单相固溶体,且具有良好的高温稳定性。
MANZONI等在感应悬浮炉中(氩气气氛)等原子比熔化得到金属锭,重熔后在炉内冷却得到AlCoCrFeNi高熵合金。观察该合金的显微结构,枝晶和枝晶间结构清晰可辨。
感应熔炼由于有电磁搅拌作用,熔体的成分和温度都比较均匀,温度控制也比较方便,相对于电弧熔炼更加节能,没有电弧的高温作用和因电极而造成的杂质问题,也没有气体在高温下离解而易于被熔体吸收的问题。但是,由于电磁的搅拌作用,增强了熔体对炉衬的冲刷进而增大侵蚀强度,而且搅拌作用也会使熔体吸收气体的可能性增大,造成合金性能不稳定。
3 机械合金化
机械化学合成工艺是制备纳米化合物的新工艺,是通过球磨使多种金属材料相互作用形成复合纳米材料。该工艺由日本京都大学首次提出,最初目的是利用高能球磨,使粉末间相互作用合成铁氧体,随后应用于纳米复合材料的制备。
YOUSSEF等采用机械合金化法使用20∶1(质量比)的球粉在室温下球磨14h得到合金粉末,研究表明,得到的高熵合金粉末结构为单相fcc结构,晶粒尺寸为12nm,硬度为5.9GPa,不含O N元素的试样在500℃退火时转变为hcp结构,含有O N的试样不会转变,在800℃退火时表现出轻微的相分离。
ZADDACH等采用此法使用10∶1(质量比)球粉在高能球磨机中制备得到高熵合金粉末且发现堆垛层错能随着组分的增加而减少。
机械合金化法在制备高熵合金的过程中很好地解决了原料的选取问题,且操作较为简便,但采用该方法会出现原料混合不均匀、分散性不好的问题,而且产物纯度不够高,粒度大且不均一,反应时间长。原料预处理过程中超声波震荡方法的引入可以很好地解决原料混合和分散的问题。
4 磁控溅射
磁控溅射是气相沉积的一种,也是目前使用最广泛的一种,属于物理范畴。磁控溅射法是在真空环境中进行的,利用在阴极(靶)和阳极(镀膜室壁)之间施加的巨大电压,在镀膜室内产生磁控型异常辉光放电,高速移动的电子碰撞氩分子使氩气发生电离,氩离子被阴极加速并轰击阴极靶表面,靶表面原子被撞击溅射到基底表面上形成薄膜。
BRAECKMAN等制备了具有不同组成的四个靶来沉积AlCoCrCuFeNi薄膜,沉积试验得到了38个合金薄膜。检测表明,薄膜厚度为175~540nm,且通过增加膜中Al含量,合金结构从fcc变为bcc,BRAECKMAN提供了一种灵活的制备高熵合金的方法。
CHANG等采用直流反应磁控溅射的方法通过改变衬底温度得到了(AlCrNbSiTiV)N高熵合金薄膜。研究表明,合金薄膜具有典型的柱状微观结构和良好的黏结强度。
HUANG等采用此法使用射频溅射系统将AlCoCrCu0.5NiFe高熵合金的溅射氧化膜沉积在硅晶片上。研究表明,得到的薄膜结构简单,在退火过程中薄膜没有产生其他相,具有较好的热稳定性。
磁控溅射法对所用的靶材料和反应气体纯度要求很高,这有利于制备高纯度的化合物薄膜。薄膜的组分和厚度可以通过改变靶的材质和溅射时间来实现,薄膜的元素含量可以使用等离子发射谱监测来调节反应气体流量使等离子体放电电压稳定,从而使沉积速率稳定,得到分布均匀的薄膜。磁控溅射法具有镀膜层与基材的结合力强,镀膜层致密、均匀等优点,近年来发展了一系列稳定等离子体以控制沉积速率,等离子体密度越大,溅射率越高,操作简便且不易脱落,效率高,而且在低温下进行,危险低,缺点是只能生产薄膜。
5 电化学法
电化学法制备合金是通过施加电位,电解质中的离子在电势差的作用下定向移动,在阴阳极表面发生氧化还原反应,得到合金产物。
YAO等利用电化学方法通过制备BiFeCoNiMn高熵合金薄膜,研究表明,产物具有软磁性,经过退火试验,薄膜出现了磁各向异性。
GLUDOVATZ等采用电化学方法制备了NiFeCrCuCo高熵合金,试验表明,合金为fcc结构,平均粒径为26.7nm。电脱氧是电化学制备高熵合金的一种方式,也称为FFC-Cambridge工艺,是一种相对较新的冶金技术,可直接从纯固体和混合形式的固体氧化物中获得金属和合金。
SURE等证明了通过熔盐电化学还原法直接从金属氧化物合成TiNbTaZr和TiNbTaZrHf耐火高熵合金的可行性,研究表明,制备的合金结构为bcc型,具有显著的孔隙率,尽管存在大量的孔隙,其仍有较强的硬度。
电化学法的优点是反应从氧化物开始而不是从纯金属开始的,这大大降低了成本;反应在相对适中的温度下进行,所有反应均以固态进行;在反应期间,保留了固体氧化物前体的形状,提供了制备近网状金属的可能性。
6 定向凝固
定向凝固是一种较为精细的控制方法,通过控制温度梯度的方向,使熔体凝固方向与其相反,可以得到预期的晶粒取向,避免横向晶界的产生,产品的纵向力学性能可以得到显著提高。
ZHENG等采用定向凝固的方法制备CoCrFeNi高熵合金,研究表明在不同凝固速度下,固液界面和柱状晶粒不同,微观结构仅由fcc固溶体相组成,随着凝固速率的增加,屈服强度、极限抗拉强度显著提高,晶界的强化改善了其拉伸性能。
7 3D打印
高熵合金的3D打印是采用计算机技术,以预期产物的成分为原料,混合后通过打印机逐层打印的方式来进行的。
KENEL等利用此法将基于含氧化物纳米粉末(Co3O4+Cr2O3+Fe2O3+NiO)混合物的油墨还原成金属,相互扩散,在H2中烧结得到CoCrFeNi高熵合金,分析表明,合金为fcc结构,粒径低至100μm,在低温下具有出色的机械性能。
GAO等通过激光3D打印技术成功制造了块状CoCrFeMnNi高熵合金,试验表明,合金具有bcc fcc两种晶体结构,且具有优异的物理化学性能。
HAASE等将元素粉末混合物的热力学模型和3D打印相结合,应用元素粉末混合物的激光金属沉积(LMD)来制备CoCrFeMnNi高熵合金,该方法在改变合金化学组成时具有较高灵活性,易于生产等优势。
激光3D打印(LMD)是一种近净成型的制造工艺,操作简单,速度快,效率高,可以制造具有复杂几何形状的高熵合金元件,与常规铸造材料相比,LMD生产的合金密度均匀,无明显偏析,质地明显,机械性能优异。
总结及展望
高熵合金的理论研究对其应用提供了大量的理论依据与实践支持,为高熵合金在各个领域中的应用打下了坚实基础。
常见的高熵合金制备方法有传统的电弧熔炼和感应熔炼,新的制备方法包括3D打印、磁控溅射和定向凝固等,这些方法可以有效缩短制备周期。高熵合金在耐磨性、强度、热稳定性、抗疲劳和断裂性、磁性等方面都表现出色,对具备这些优异性能的高熵合金的研究亟待进一步拓展。高熵合金的应用研究应着重于高熵合金膜、块体制备工艺。应进一步加强研究该合金的熵、焓对于组织结构影响的规律,单相、多相及相变的形成机理及其稳定性规律,组织性能的可控性等。高熵合金在各个领域中必将具有更为广阔的应用空间。
免责声明:本网站所转载的文字、图片与视频资料版权归原创作者所有,如果涉及侵权,请第一时间联系本网删除。
相关文章
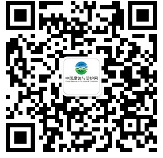
官方微信
《中国腐蚀与防护网电子期刊》征订启事
- 投稿联系:编辑部
- 电话:010-62316606-806
- 邮箱:fsfhzy666@163.com
- 中国腐蚀与防护网官方QQ群:140808414
点击排行
PPT新闻
“海洋金属”——钛合金在舰船的
点击数:7130
腐蚀与“海上丝绸之路”
点击数:5741