摘要
通过分析成品油输送管线腐蚀产物组成、酸溶特性,利用细菌培养法培养和测定了腐蚀产物中与金属材料微生物腐蚀相关的细菌如硫酸盐还原菌 (SRB)、铁细菌 (IOB) 的含量。模拟成品油输送管道厌氧环境和微量水存在情况,利用电化学极化曲线和电化学阻抗法、腐蚀失重法结合表面分析技术研究了X60管线钢在含SRB介质中的腐蚀行为。结果表明,多数管线腐蚀产物中存在SRB和IOB,管道沉积物以Fe3O4、FeS、Fe(OH)3、Fe2O3等形式存在。在含有成品油和SRB菌液的模拟实验中,X60钢表面形成大量疏松多孔的腐蚀产物和SRB细菌的聚集体,腐蚀程度较空白对照组严重,且腐蚀形态呈现点蚀特征,点蚀坑深度高达25.1 μm/14 d。
关键词: 成品油输送管线内腐蚀 ; 硫酸盐还原菌 ; 铁细菌 ; X60碳钢 ; 微生物腐蚀
随着成品油市场需求量的不断增大,因成品油管道具有运输成本低、管输量大等优点而发展迅速[1,2]。我国先后建成“兰成渝”等多条输油线路,截止2017年,投入使用的成品油管道已达2.79×104 km,成品油管道在新建管网中的比重越来越大,然而,管道面临严重内腐蚀的问题一直未得到较好的解决[3,4]。虽然成品油经过脱硫、脱水等工艺处理,但由于国内成品油管道投产时大多用水对管线进行清扫,导致低洼处存在局部沉积水的问题,同时,所输油品中也会含有微量水,在管线落差较大的部位,油相中重质组分或水滴等可能会逐渐沉积下来,导致含水量也相对提高,最终可能会促使亲油性的输油管道表面转变为亲水性,低洼处聚集的沉积物因富含充足的营养基质和适宜的温度有利于细菌菌落的形成,进而诱导微生物腐蚀 (MIC) 的发生[5-7]。
针对石油和天然气管道的MIC问题的研究报道日益增加[8,9],但是对成品油管道MIC的研究报道较少,每年因金属管材遭受腐蚀给国民经济造成了重大损失,而微生物参与该腐蚀过程而造成的损失约占金属腐蚀的20%,因此研究该腐蚀问题具有十分重要的现实意义[10-12]。王正泉等[13]采用高通量测序技术分析了华南一条成品油管道中参与腐蚀的微生物类型,对沉积物中微生物种群进行鉴定后共检出微生物10门17纲85属,认为在管道沉积物中细菌群落的协同作用下,柠檬酸杆菌属和鞘氨醇单胞菌属是该成品油管道发生MIC的主要菌群。敬加强等[14]在塔里木某输油管道的腐蚀产物中分离出硫酸盐还原菌 (SRB),测试表明生长周期内H2S增加了管线钢硫化物应力腐蚀开裂的可能性。Song等[15]研究了流速对SRB、铁氧化细菌 (IOB) 和腐生菌几种不同类型的细菌对成品油管道的腐蚀情况,表明即便在高流速下也很难冲刷掉表面粘附的细菌和腐蚀产物。城市汽柴油输送系统内部存在微量水、以及厌氧的环境等为微生物的生长代谢提供了适宜的条件,所以研究城市汽柴油输送管道内MIC现象和相应腐蚀机理有一定的必要性。
本文旨在调查成品油输送管线内MIC状况,主要运用微生物培养、电化学方法、失重分析以及腐蚀表面分析技术,通过实验室模拟研究成品油输送系统X60管线钢MIC程度及腐蚀特征,为管道的内腐蚀防护技术研究提供技术支持。
1 实验方法
管道沉积物分别取自建水、华南、茂名、昆明等地的某成品油管道之中,油样取自附近油站成品油,取样后即刻装入灭菌容器中封存,并随即展开实验进行分析处理。在超净工作台上取出沉积物进行预处理,迅速将其移置表面皿上,然后放入真空烘箱恒温4 h后研磨至80目,置于干燥器中备用,取出一部分样品用X射线衍射仪 (XRD) 分析其物质成分。为了较为全面地研究管道腐蚀沉积物的特性,对沉积物进行了酸溶实验,以便结合XRD分析腐蚀产物中能够发生溶解的成分,为后期腐蚀介质环境下缓蚀杀菌剂评价实验做准备,针对性的选择能够在腐蚀沉积物环境下稳定存在的缓蚀杀菌剂。分别称取一定质量的沉积物用盐酸溶液 (1 mol/L) 进行溶解,使碳酸盐及能被盐酸溶解的成分溶解,将不溶物过滤、洗涤、烘干、称重,计算酸不溶率。酸不溶率 (AIR) 计算公式如下 (1):
其中,W0和Wt为沉积物酸浸烘干前后的质量/g。
X60碳钢作为本次实验材料,其化学成分 (质量分数,%) 为:C 0.1、Si 0.4、Mn 1.3、S 0.025、P 0.02,余量为Fe。电极尺寸为?10 mm×10 mm的圆柱形试样,失重实验和形貌观察的试片尺寸为50 mm×10 mm×3 mm,失重实验计算的腐蚀速率公式如式 (2)。用导电性优良的铜丝焊接后再用环氧树脂涂封,使电极有效工作面积为0.785 cm2。实验前金属材料均需用SiC砂纸逐级打磨至1200#,并依次用去离子水、无水乙醇和丙酮进行清洗,然后在氮气条件下烘干并在紫外灯下照射30 min以达到对材料的灭菌处理。
其中,CR为腐蚀速率/mm·a-1;M0和M1为试片的初始质量及清除腐蚀产物后的质量/g;A为试片的表面积/cm2;t为腐蚀实验时间/h;ρ为金属材料的密度/kg·m-3。
电化学实验中所用的SRB菌种是从管道沉积物中培养后经过分离纯化得到,培养基的配方为:乳酸钠4.0 mL/L,酵母浸汁液1.0 g/L,维生素C 0.1 g/L,MgSO4·7H2O 0.2 g/L,K2HPO4 0.01 g/L,NaCl 10.0 g/L,蒸馏水1 L。将配好的新鲜培养基pH调节至7.2 左右,采用蒸汽压力灭菌锅在121 ℃下灭菌20 min,待冷却至常温后向培养基中加入紫外消毒的 (NH4)2SO4·FeSO4·6H2O 0.2 g后摇匀放置。空白组分为灭菌培养基和含油培养基,实验组为SRB菌液组和含油SRB菌液组。
在测试介质中浸泡14 d后,取出腐蚀试片用2.5%戊二醛固化8 h,确保试样表面的细菌和腐蚀产物稳固,然后用50%、70%、80%、90%、95%及100%乙醇溶液逐级脱水。用Gemini SEM300场发射扫描电镜 (FESEM) 及其自带的能谱 (EDS) 分析仪和3D显微镜 (VHX-1000E) 观察试样表面腐蚀形貌、分析元素含量。电化学测试采用标准的三电极体系,X60碳钢为工作电极,饱和甘汞电极 (SCE) 为参比电极,Pt电极为辅助电极,电化学测试在CorrTest (CS350) 电化学工作站上进行。EIS在自腐蚀电位下进行测试,激励信号为10 mV的正弦波,测试频率范围为105~10-2 Hz,动电位扫描速度为0.5 mV/s,电位扫描范围为相对于开路电位±200 mV,测试结束后分别用ZView2、CView2软件对实验数据进行拟合处理。
2 结果与分析
2.1 管道沉积物组成测定及腐蚀性微生物检测
将样品从保存瓶中取出,按照上述处理步骤预处理后,加入足量盐酸 (1 mol/L) 溶解样品,使含有的碳酸盐及能被盐酸溶解的成分完全溶解,将不溶物过滤、洗涤、烘干、称重,按照公式 (1) 计算酸不溶率,并记录溶解过程实验现象如表1所示。最终溶液颜色呈现浅绿色,表明酸溶后含有部分可溶性铁盐存在,但主要是一些不能溶解的沉淀物,性质较为稳定。菌量检测结果表明,细菌中SRB含量较高,而昆明未检测出细菌可能是样品储存不当导致失效,不排除细菌存在的可能。结合管道厌氧环境,后续模拟实验主要研究了SRB对管材腐蚀的影响。
表1 酸溶实验、XRD成分分析、微生物培养及细菌含量测定表
图1是几种管道腐蚀沉积物的XRD谱。可以看出,沉积物主要为Fe3O4、FeS、Fe(OH)3和少量的Fe2O3、FeOOH等。结合样品酸不溶率实验,溶解后颜色呈现浅绿色可以推断出产物中的FeS和Fe(OH)3等物质发生了溶解,FeS的产生通常认为与SRB密切相关,因成品油中S的含量不多,沉积物中含有的FeS可以认为是SRB参与了腐蚀产生的,而细菌的含量在一定程度上也可以体现腐蚀的程度强弱。昆明样品中未发现与SRB相关的标志性腐蚀产物可能与其管道服役时间和取样部位有关,也可能是样品储存过程保护不当而失效,但目前还不能排除不含细菌的可能。初步取得的结果已经可以表明大多数管线存在微生物腐蚀,考虑管道内部多处于厌氧环境,以及SRB细菌含量较多,后续模拟实验主要研究了SRB对于成品油管线钢的腐蚀试验。
图1 管道腐蚀沉积物的XRD图
2.2 成品油中X60钢微生物腐蚀模拟实验
2.2.1 成品油中管线X60钢表面微生物膜形成过程
图2为X60试样在含有成品油的SRB菌液中分别浸泡1、3、8和14 d后的表面生物膜形成过程SEM像。可以看出,浸泡初始表面还可以看到打磨的划痕,一些少量的颗粒物在表面沉积;在3 d时,细菌开始在金属表面吸附聚集,可以观察到大量的SRB细菌粘附在金属表面,说明此时SRB已经开始大量繁殖;在8 d时金属表面形成的生物膜已经较为致密;14 d时,生物膜变得更粗糙同时裂纹也比较明显,可以看到很多块状的腐蚀产物,大量的SRB细菌被生物膜所包覆。
图2 X60钢试样在含SRB菌液中浸泡不同时间的SEM像
2.2.2 模拟含成品油菌液体系X60钢的电化学腐蚀过程研究
图3是X60钢在4种介质中测试14 d的Nyquist图,阻抗弧的大小变化与电极表面腐蚀产物膜/生物膜的形成密切相关,由此可以反映金属表面的腐蚀情况。当出现较小的阻抗弧时,说明发生了较为严重的腐蚀,而金属表面形成致密的生物膜,或者被腐蚀产物完全覆盖时,则呈现出较大的阻抗弧。空白培养基中 (图3a) 和含油培养基 (图3b) 均呈现出阻抗弧先减小后增大的变化过程,在3~5 d时间段阻抗弧维持在一个较小的水平,原因可能是培养基中的腐蚀性离子对金属表面造成了侵蚀,破坏了表面的稳定性,使阻抗弧变小,腐蚀相对于初始状态较严重;8 d后,阻抗弧持续增大,原因是在电极表面形成了腐蚀产物膜,在一定程度上减缓了腐蚀的程度,含有成品油的培养基中阻抗弧在5~8 d急剧增大,说明成品油的存在促使金属表面较快地形成了腐蚀产物膜,但综合来看腐蚀程度略强于培养基组。在SRB菌液 (图3c) 和含油SRB菌液 (图3d) 中,相比于培养基体系阻抗弧明显变小,腐蚀较为严重。在SRB菌液中,阻抗弧先减小后缓慢增大,反映出随着细菌进入适应期后快速繁殖,在电极表面产生大量的代谢产物导致腐蚀程度加剧,而后缓慢变大,表明在电极表面形成了一层致密的生物膜,致密的生物膜对金属具有保护作用进而减缓了腐蚀。在含有成品油的菌液中,阻抗弧先变小后急剧增大、而后又减小的动态变化过程,说明与SRB菌液组相比,含有成品油的菌液体系生物膜的生长粘附速度更快,成品油为细菌生长代谢提供了能量;8d后阻抗弧有所减小,原因可能是金属表面的生物膜发生了局部破裂,导致腐蚀较纯菌液体系更为严重。图4是电化学阻抗拟合的等效电路图,电化学阻抗谱拟合效果较好,拟合误差在10%以内。图中Rs表示溶液电阻,Rf和Qf分别为生物膜/腐蚀产物膜阻抗和电容,Rct和Qdl分别是电荷传递电阻和双电层电容。表2为电化学阻抗拟合结果,其中Rp为极化电阻与腐蚀速率密切相关,通常认为Rp数值越小,腐蚀情况越严重。图5为Rp与时间的变化曲线,与阻抗分析结果一致。
图3 X60钢试样在4种不同测试体系中的电化学阻抗谱
图4 电化学阻抗拟合等效电路图
表2 4种测试体系中X60碳钢的电化学阻抗图拟合所得电化学参数
图5 X60碳钢在不同测试体系中电化学阻抗拟合Rp随时间变化图
从极化电阻随时间的动态变化可以看出,0~3 d SRB由于进入新的环境,细菌处于生长延滞期,因此二者极化电阻变化趋势一致都略有减小,说明此时金属的腐蚀与介质中水分含量有关,在3~8 d范围内,随着SRB进入对数生长期,细菌定植在管线钢表面,生物膜的致密性逐渐增加,含菌介质极化电阻开始增大,但含有成品油的菌液介质中极化电阻一直保持略高水平,可能的原因是含油介质中有机物的存在更有利于SRB生物膜的形成,使其率先达到一个快速生长的阶段,形成的生物膜对底层金属有一定的保护作用,此时间段内生物膜有一定阻碍腐蚀介质迁移的作用,而菌液环境这一阶段腐蚀速率高于含油体系,但是8 d后,菌液环境中形成了更为致密的生物膜,极化电阻明显增大,而含油体系中生物膜发生局部破坏,极化电阻略有减小,腐蚀速率开始比菌液中大。从上述现象可以看出,在实际管线中若被SRB菌污染,那么在近14 d的时间段内可以形成管线大面积污染。结合管道微生物缓蚀杀菌剂的投加工艺研究,可以确定投加周期要在8 d以内。
图6是X60钢在几种体系中浸泡14 d后的动电位极化曲线图,相应的拟合结果如表3。通过极化曲线可以看出,含有成品油的介质中腐蚀高于对应无油体系,含油菌液中腐蚀最严重,其次是菌液环境,空白培养基腐蚀最轻微;同时腐蚀电位也发生了较为明显的负移,通常认为腐蚀电位越负,金属发生腐蚀的可能性越大。从Tafel曲线外推法拟合的结果也可以看出,含有成品油的菌液体系腐蚀电流密度最大,是菌液环境中的3倍,培养基中腐蚀电流密度最小,与阻抗结果分析一致,表明含有成品油的条件下加速了SRB对X60碳钢的腐蚀速率。
图6 X60钢在4种不同体系中浸泡14 d后的动电位极化曲线
表3 X60钢在几种不同体系中浸泡14 d后的动电位极化曲线拟合结果
2.2.3 14 d模拟成品油腐蚀介质中微生物腐蚀产物膜分析
X60碳钢在4种腐蚀体系中分别浸泡14 d后的生物膜形貌如图7。可以看到,在培养基中浸泡的X60试片表面被一层腐蚀产物膜所覆盖,腐蚀产物膜较为均匀致密,与阻抗弧呈现较大的半径结果一致,说明培养基中腐蚀较轻,金属在腐蚀产物膜形成后得到了一定程度的保护。从图7c和d中可以看到,在SRB菌液中腐蚀产物相对于含油菌液中更加致密,凸起的腐蚀产物趋于更小的颗粒;含油的菌液中腐蚀产物颗粒更加粗糙,可以看到较多的SRB细菌存在。图8为在4种体系中浸泡14 d后试样表面腐蚀产物的元素分析,EDS结果表明,在培养基中浸泡后,表面腐蚀产物的元素种类相同,表明加入成品油并没有改变腐蚀产物的组成;图8c与d对比可以看出含油菌液中S的含量更高,结合形貌分析含有较多的SRB细菌,说明SRB在该体系得到了较好的生长代谢,参与了该腐蚀过程。同时可以看出SRB腐蚀实验中腐蚀产物主要以Fe、O、S等存在,可以推断出腐蚀后的产物主要是金属氧化物和铁硫化合物等形式,与最初的管道腐蚀沉积物分析具有一致性,可以认为管道中的SRB细菌参与了该过程的腐蚀,且含有成品油的条件下加剧了腐蚀过程,很好地验证了管道腐蚀沉积物分析的结果。
图7 X60碳钢在4种腐蚀体系中浸泡14 d后的腐蚀产物膜形貌图
图8 X60碳钢在几种腐蚀体系中浸泡14 d后的腐蚀产物EDS分析
2.2.4 14 d模拟成品油腐蚀介质中腐蚀失重和去除腐蚀产物后形貌分析
图9为去除腐蚀产物后X60试片表面的3D表面形貌。可以看出,在培养基中浸泡的X60试片表现较为均匀平整,腐蚀比较轻微;在菌液中腐蚀以点蚀为主,含油SRB菌液中浸泡的试片表面出现了较大的腐蚀坑,与菌液中相比,腐蚀坑深度更深,高达25.1 μm/14 d,表明腐蚀更为严重,这与阻抗和极化结果一致,说明含油体系,细菌能够通过代谢成品油中的烃类进行生长代谢,诱导金属发生更严重的点蚀。
图9 X60碳钢浸泡14 d后去除腐蚀产物后的3D形貌
图10是4种不同体系中X60碳钢浸泡14 d后通过失重结果计算的腐蚀速率。可以看出:在培养基中浸泡的试片腐蚀较为轻微,与含有成品油组区别不大;而在SRB存在的条件下,腐蚀速率急剧增加,在含有成品油的SRB菌液中腐蚀速率高达0.15 mm/a,高于SRB菌液0.09 mm/a,表明成品油体系对管材造成的腐蚀比较严重。
图10 X60钢试样在4种腐蚀体系中浸泡14 d后的失重图
3 结论
(1) 成品油输送管道内存在大量的管内沉积物,4种腐蚀沉积物在酸中均较为难溶,不溶物多数以Fe3O4的形式存在,除昆明样品外其他还含有较多的FeS。从沉积物中富集培养出了以SRB为主的细菌,细菌对于X60管线钢的腐蚀较为严重,有大量的SRB细菌粘附在基体表面。
(2) SRB存在时腐蚀较无菌体系严重,含油SRB菌液中浸泡14 d阻抗弧最小,极化电阻Rp最小,腐蚀最为严重;Tafel曲线外推法拟合的结果表明,含有成品油的菌液体系腐蚀电流密度最大,是菌液环境中的3倍,培养基中腐蚀电流密度最小,与阻抗结果分析一致,均表明含有成品油的条件下加速了SRB对X60碳钢的腐蚀速率。
(3) 腐蚀产物中含有较高的Fe、O、S等元素,与管内沉积物中元素分析一致,说明SRB参与了金属的微生物腐蚀过程;且含有成品油的菌液体系腐蚀产物中S含量更高,更利于细菌的增殖而加剧腐蚀。
(4) 在含有成品油的SRB菌液中腐蚀速率高达0.15 mm/a,远高于其他组的腐蚀;去除腐蚀产物后试片以点蚀为主,表面出现较多腐蚀坑,在含成品油的SRB菌液中腐蚀坑最大高达25.1 μm/14 d,与电化学测量数据分析一致,表明该条件下腐蚀最为严重。
参考文献
1 Xiong K J. Study on two-phase flow characteristics of diesel oil carrying water [D]. Chengdu: Southwest Petroleum University, 2017
1 熊柯杰. 柴油携水两相流动特性研究 [D]. 成都: 西南石油大学, 2017
2 Qiao H F. Analysis of the status quo of refined oil pipeline corrosion and the design protection systems [D]. Xi’an: Xi'an Shiyou University, 2014
2 乔焕芳. 延-西成品油管线腐蚀现状的分析及防护系统的设计 [D]. 西安: 西安石油大学, 2014
3 Zhu Q Z, Duan P X, Wang H J, et al. Current situations and future development of oil and gas pipelines in the world [J]. Oil Gas Storage Trans., 2015, 34: 1262
3 祝悫智, 段沛夏, 王红菊等. 全球油气管道建设现状及发展趋势 [J]. 油气储运, 2015, 34: 1262
4 Wang D Z, Liu J H, Wang C X, et al. Test and analysis on sediment in Lanzhou-Chengdu-Chongqing products pipeline [J]. Oil Gas Storage Trans., 2005, 24(2): 59
4 王德增, 刘井会, 王彩霞等. 对成品油管道中沉积物的分析 [J]. 油气储运, 2005, 24(2): 59
5 Been J, Place T D, Holm M. Evaluating corrosion and inhibition under sludge in large diameter crude oil pipelines [A]. Proceedings of the Corrosion 2010 [C]. San Antonio, 2010, 756
6 Liu M, Jiang Y W, Han S, et al. Internal corrosion cause analysis of a products pipeline before putting into operation [J]. Corros. Sci. Prot. Technol., 2018, 30: 496
6 刘猛, 姜有文, 韩朔等. 成品油管道投产前内腐蚀原因分析 [J]. 腐蚀科学与防护技术, 2018, 30: 496
7 Yustina M P, Wolfgang W S, Tjandra S, et al. Evaluation of Bio-Corrosion on carbon steel by Bacillus Megaterium in biodiesel and diesel oil mixture [J]. J. Eng. Technol. Sci., 2020, 52: 370
8 Zhang Y, Li Y. Microbiological corrosion and protection of oil and gas pipeline [J]. Equip. Environ. Eng., 2008, 5(5): 45
8 张燕, 李颖. 输油气管线的微生物腐蚀与防护 [J]. 装备环境工程, 2008, 5(5): 45
9 Liu H W, Xu D K, Wu Y N, et al. Research progress in corrosion of steels induced by sulfate reducing bacteria [J]. Corros. Sci. Prot. Technol, 2015, 27: 409
9 刘宏伟, 徐大可, 吴亚楠等. 微生物生物膜下的钢铁材料腐蚀研究进展 [J]. 腐蚀科学与防护技术, 2015, 27: 409
10 Liu H W, Liu H F, Qin S, et al. Investigation of biomineralization induced by sulfate reducing bacteria in sewage gathering pipelines in oilfield [J]. Corros. Sci. Prot. Technol, 2015, 27: 7
10 刘宏伟, 刘宏芳, 秦双等. 集输管线硫酸盐还原菌诱导生物矿化作用调查 [J]. 腐蚀科学与防护技术, 2015, 27: 7
11 Yu H H. Corrosion and corrosion protection of product oil tanks and long-distance pipelines [J]. Corros. Prot. Petrochem. Ind., 2013, 30(4): 17
11 余杭辉. 国内成品油储罐和长输管线腐蚀现状与防护 [J]. 石油化工腐蚀与防护, 2013, 30(4): 17
12 Liu L. Corrosion Behavior of Sulfate Reducing Bacteria in X52 Oil Pipeline [D]. Chengdu: Southwest Petroleum University, 2016
12 刘黎. X52输油管道硫酸盐还原菌腐蚀行为研究 [D]. 成都: 西南石油大学, 2016
13 Wang Z Q, Xu W C, Zhou Z Y, et al. Microbial corrosion behavior of X65 pipeline steel in product pipeline sediments [J]. Surf. Technol., 2020, 49(7): 245
13 王正泉, 徐玮辰, 周子扬等. X65管线钢在成品油管道沉积物中的微生物腐蚀行为 [J]. 表面技术, 2020, 49(7): 245
14 Jing J Q, Liu L, Xie J F, et al. Effect of sulfate reducing bacteria from corrosion scale of oil pipeline on corrosion behavior of Q235 steel [J]. Corros. Prot., 2018, 39(1): 6
14 敬加强, 刘黎, 谢俊峰等. 输油管道腐蚀垢样中硫酸盐还原菌对Q235钢腐蚀行为的影响 [J]. 腐蚀与防护, 2018, 39(1): 6
15 Song X Q, Yang Y X, Yu D L, et al. Studies on the impact of fluid flow on the microbial corrosion behavior of product oil pipelines [J]. J. Pet. Sci. Eng., 2016, 146: 803
免责声明:本网站所转载的文字、图片与视频资料版权归原创作者所有,如果涉及侵权,请第一时间联系本网删除。
-
标签: 成品油输送管线内腐蚀, 硫酸盐还原菌, 铁细菌, X60碳钢, 微生物腐蚀
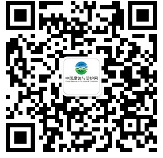
官方微信
《中国腐蚀与防护网电子期刊》征订启事
- 投稿联系:编辑部
- 电话:010-62316606-806
- 邮箱:fsfhzy666@163.com
- 中国腐蚀与防护网官方QQ群:140808414