摘要
利用旋转圆柱电极实验装置,在模拟油田采出液中,通过腐蚀失重、形貌观测和电化学分析等方法量化20号钢在不同砂粒粒径和温度下的冲刷腐蚀协同作用。结果表明,砂粒粒径增大对20号钢的冲刷磨损有明显的促进作用,这与形貌观测较符合。随砂粒粒径增大,腐蚀促进冲刷的作用和冲刷促进腐蚀的作用均先增加后减小。在砂粒粒径为40~70 μm到120~200 μm时,材料冲刷腐蚀以冲刷-电化学混合控制为主;砂粒粒径为200~300 μm时,以冲刷磨损为主导。在不同的温度下,20号钢的冲刷腐蚀均以冲刷-电化学为主要控制;温度越高,腐蚀对冲刷的促进作用越显著。
关键词: 20号钢 ; 冲刷腐蚀 ; 砂粒粒径 ; 温度 ; 协同作用
冲刷腐蚀在管道运输中屡见不鲜[1]。其不仅仅是电化学腐蚀与切削磨损的单一构成,而是两者间相互作用的结果[2-4]。冲刷腐蚀的作用有可能明显高于纯冲刷或纯腐蚀单独的作用。综合以往的研究成果,由于协同效应的存在,产生冲刷促进腐蚀和腐蚀促进冲刷作用,从而促使冲刷腐蚀的综合作用增强[5]。
已有研究成果对不同因素对不同材料的冲刷腐蚀行为的影响规律进行了研究,拓宽了冲刷腐蚀的研究体系,全面的概括了冲刷腐蚀行为,为材料的冲刷腐蚀的预防和控制提供了很好的理论指导作用。文献[6]研究了流速和显微组织对两相CK45钢冲刷腐蚀的影响,结果显示流速从5 m/s增加到16 m/s,相应的冲刷腐蚀速率增加了4~6倍;铁素体-贝氏体在研究的3种显微组织中受破坏最小。徐哲[7]研究了P110钢在液固两相流条件下的冲刷腐蚀行为,结果显示砂粒粒径、流速、NaCl浓度越大,冲刷腐蚀速率越大;3%的含砂量对冲刷腐蚀速率影响最大。但上述研究涉及协同作用的较少,未从机理方面研究材料在冲刷腐蚀过程中机械冲刷与电化学腐蚀之间的交互作用。因此在冲刷腐蚀方面虽已有大量研究工作,但冲刷腐蚀的协同作用机理尚不明晰。
对纯冲刷、纯腐蚀以及冲刷腐蚀及其协同效应的定量化研究,能够清楚的区分机械冲刷与腐蚀各自造成的损害,判定冲刷腐蚀过程中的主导因素[5]。Jeviera Aguirre等[8]研究了溶解铜离子对X65钢在模拟铜尾矿浆中冲刷腐蚀协同作用的影响,结果显示由于腐蚀和冲刷腐蚀协同作用的综合影响,溶解的500 mg/L铜离子使X65钢总重量损失增加至少30%。Khayatan等[9]采用泥浆冲击钻机研究了商业纯钛在不同冲击角度的冲刷腐蚀协同行为,认为协同作用速率在所有的冲击角上均明显高于纯冲刷速率;在40°冲击角下冲刷和冲刷腐蚀速率最大。张福祥等[10]研究了压裂过程中超级13Cr油管的冲刷腐蚀交互作用,认为液体排量大于3.7 m3/min时,冲刷腐蚀交互作用的主导因素由腐蚀变为冲刷磨损,并且交互作用在排量超过2.65 m3/min时明显增大。Owen等[11]在淹没式射流装置上研究了X65碳钢在CO2水环境中冲刷腐蚀交互作用,认为在实验条件下腐蚀促进冲刷作用最显著,加工硬化层的溶解和亚表层的裂纹是导致材料降解加剧的原因。鉴于目前对冲刷腐蚀各部分失重量 (纯冲刷失重量E0、纯腐蚀失重量C0、冲刷促进腐蚀失重量Ce和腐蚀促进冲刷失重量Ec) 的研究方法不同,其中C0大都以静态条件下的纯腐蚀失重量来表示,E0以含有相同固体量的非腐蚀性流体的纯冲刷失重量来表示[12],方法虽然简单直观,但此类纯腐蚀和纯冲刷试验结果缺乏精准性。以往的冲刷腐蚀研究试验大多采用自制旋转圆盘试验装置,使得试验结果差异较大,试验数据缺少可比性。目前石油天然气工程领域冲刷腐蚀研究涉及的金属材质主要为不锈钢和井下油套管钢,涉及油气集输管道用钢的研究内容较少,而随着油气田的不断开采,油气采出液中的含水量和含砂量越来越高,油气集输环境日趋复杂,油气集输系统的冲刷腐蚀问题日趋严重,20号钢作为油气集输管道常用钢,对其冲刷腐蚀特性及协同效应机理的研究极具必要性。因此,本工作选用PINE旋转圆柱电极实验装置,采用电化学、失重法等定量与定性方法研究了砂粒粒径和温度对20号钢在液固两相流条件下的冲刷腐蚀协同作用的影响规律,旨在探究20号钢冲刷腐蚀交互作用的机理,为预防和控制管道冲刷腐蚀提供理论支撑,保障管输技术的发展。
1 实验方法
实验在PINE旋转圆柱电极装置上进行。为防止砂粒因重力产生沉降,在旋转圆柱的末端配备了搅拌器。为了减小由于IR降导致的偏差,为参比电极配置Luggin毛细管。选用CHI920D电化学工作站进行电化学测试,采用三电极系统,其中Ag/AgCl作为参比电极,Pt作为辅助电极,20号钢作为工作电极。20号钢主要化学成分 (质量分数,%) 为:C 0.18,Mn 0.39,P 0.014,S 0.005,Si 0.18,Cr 0.01,Ni 0.01,Cu 0.01%,Fe余量。采用圆环形的工作电极,内径为9.53 mm,高度为6.39 mm,外径为15 mm,工作面积为3.01 cm2。实验介质选用模拟油田采出液,溶液介质 (g/L) 配比为:MgCl2 0.5、CaCl2 0.5,Na2SO4 0.4,NaHCO3 0.6。
使用200~800号砂纸对试样表面逐级打磨,经2000号砂纸抛光后,用丙酮和无水乙醇清洗,蒸馏水冲洗,放入恒温鼓风干燥箱干燥后,采用精度为0.1 mg的电子天平进行称重。为降低误差,每个试样进行5次称重,在去除最大值和最小值的情况下取剩余3次的平均值。实验时间为10 h。采用六次甲基四胺和盐酸配置清洗液。实验后,用清洗液清除腐蚀产物,经风干后称重,称重方法同实验前。另外取一个平行试样,采用相同的清洗和称重方法处理,用以校正清洗造成的失重,确定清洗导致的平均失重量为0.411 mg。最后采用Smart zoom 5超景深三维数码显微镜进行形貌观察。为了量化冲刷腐蚀之间的相互作用,在不同的砂粒粒径和温度下再进行纯冲刷和纯腐蚀实验,实验方法和条件与冲刷腐蚀实验一致。不同砂粒粒径下冲刷腐蚀和纯冲刷实验是在模拟油田采出液中固定流速、含砂量、Cl-浓度条件下进行,流速、含砂量、Cl-浓度分别为1.5 m/s、3%、2%,砂粒粒径变化范围为40~70 μm,70~120 μm,120~200 μm,200~300 μm。纯腐蚀实验则在固定流速和Cl-浓度条件下进行,流速和Cl-浓度分别为1.5 m/s和2%。而不同温度下的实验是在不同砂粒粒径的实验基础上增加不同温度条件,温度变化为20、40、60和80 ℃,其中冲刷腐蚀和纯冲刷实验固定砂粒粒径为70~120 μm。另外,在纯冲刷实验时须对试样进行阴极保护,由于无法进行电化学测量因此只进行失重量测量。为了使阴极保护度达到最优程度 (98%以上),实验时可将其电位控制在自腐蚀电位负250 mV以上[13]。根据3个平行试样的平均失重计算试样的纯冲刷、纯腐蚀以及冲刷腐蚀失重率。综合失重数据的变化范围,不同实验条件下的3个平行试样失重量的标准偏差范围为0.120~0.378 mg,其中中间水平为0.262 mg,近似为实验误差。
10 h后采用CHI920D电化学工作站进行电化学测试。电化学阻抗谱在腐蚀电位下,105~10-2 Hz频率范围内进行测量,扰动电压幅值为10 mV。为了得到电荷传递电阻值,应用ZSimpWin软件拟合阻抗谱数据。以1 mV/s的速率由阴极向阳极方向扫描进行极化曲线测试,腐蚀电位下±250 mV为扫描范围。为了得到阴、阳极Tafel斜率ba和bc,采用Origin软件拟合并分析极化曲线数据。根据Stern-Geary方程 (1) 得到的系数B结合电荷传递电阻值Rct,最后由公式 (2) 得到腐蚀电流密度Icorr,依此判定腐蚀程度[11]。
由下式对冲刷腐蚀各分量进行量化,更深入的分析砂粒粒径和温度对20号钢的冲刷腐蚀协同作用的影响。
式中,T是通过实验前后的失重得到的总的冲刷腐蚀质量损失,mg;C为由腐蚀引起的质量损失,通过式 (6) 从冲刷腐蚀电流密度转化为质量损失,mg;C0为纯腐蚀导致的质量损失,通过纯腐蚀实验前后失重获得,mg;Ce为冲刷促进腐蚀导致的质量损失,E为冲刷导致的质量损失,mg,E0为纯冲刷导致的质量损失,由纯冲刷实验前后失重获得,mg;Ec为腐蚀促进冲刷导致的质量损失,mg。
式中,I为电流密度,A/cm2;W为原子量,g/mol;A为试样面积,cm2;t为时间,s;F为Faraday常数,取96485 c/mol;n为原子数,取2。
2 结果及分析
2.1 砂粒粒径对20号钢冲刷腐蚀协同作用的影响
2.1.1 极化曲线测试
不同砂粒粒径下20号钢的冲刷腐蚀极化曲线如图1所示。可见各粒径的极化曲线特征大致相同,阳极电流随电势的改变服从半对数关系,金属进行正常的阳极溶解,表现为活性区腐蚀。由于是动态试验且冲刷腐蚀的影响因素较多,所以自腐蚀电位没有较确定的变化规律。从图1可以看出,随着粒径的增大,腐蚀电流增加,当砂粒粒径增大至200~300 μm时开始略有减小。表1为不同砂粒粒径下冲刷腐蚀极化曲线拟合数据[15]。拟合数据也具有类似规律,说明腐蚀速率随着砂粒粒径的增大先增加后减小,存在一个临界粒径。这主要是因为粒径增大,砂粒的冲击动能增强,对金属氧化膜的破坏作用增大,从而冲刷促进了腐蚀;而随着粒径再增大,砂粒易发生破碎,因此一定程度上降低对冲刷腐蚀的作用;同时腐蚀速率是由砂粒冲击动能和冲击频率共同决定的,砂粒固含量一定的条件下,砂粒粒径越大,砂粒数目越少,且冲击颗粒和回弹颗粒之间发生碰撞 (防止颗粒撞击表面) 的可能性越高,砂粒冲击壁面频率减小,即便大砂粒粒径具有较大的冲击动能,也不易对壁面造成大规模的冲击破坏,从而导致腐蚀速度减小[14,15]。
图1 20号钢在不同砂粒粒径下冲刷腐蚀极化曲线
表1 不同粒径下20号钢冲刷腐蚀极化曲线拟合数据
2.1.2 电化学阻抗谱测试
图2为在各种砂粒粒径条件下20号钢冲刷腐蚀的电化学阻抗谱图。由于砂粒对试样产生切削作用,促使点蚀坑的形成,导致低频区出现容抗弧,使得不同粒径条件下的电化学阻抗谱呈现出的频谱特征为双容抗弧。从图中可以看出,在40~70 μm至120~200 μm的粒径范围内,容抗弧半径随粒径增大而减小,腐蚀速率随粒径增大而增大;随着粒径再增大至200~300 μm时,容抗弧半径开始变大,腐蚀速率开始降低。这与姜志超等[16]的研究结果一致。
图2 不同粒径下20号钢冲刷腐蚀电化学阻抗谱
采用图3所示的等效电路[19]对20号钢在不同砂粒粒径下的电化学阻抗谱进行拟合。其中,Rs为溶液电阻,Q为常相位角元件,Rp1为整体极化电阻,Rp2为点蚀坑内的极化电阻。拟合数据如表2所示。可以看出,不同粒径下的溶液电阻Rs没有太大变化,都维持在2 Ω·cm2左右;电极整体极化电阻Rp1先减小后增大,表明随着砂粒粒径的增大,20号钢的腐蚀速率先升高后降低,同极化曲线的分析结果相符。
图3 不同粒径下20号钢的电化学阻抗谱拟合等效电路图
表2 不同粒径下20号钢的电化学阻抗谱拟合数据
2.1.3 失重数据分析
不同砂粒粒径下冲刷、腐蚀和冲刷腐蚀质量损失速率如图4所示。可以看出,冲刷和冲刷腐蚀的质量损失速率均呈现出先增大后减小的趋势,并且变化幅度大致相同。在40~70 μm至120~200 μm的砂粒粒径范围内,质量损失速率增大,可见砂粒粒径越大,腐蚀速率越大;随着粒径继续增大至200~300 μm,质量损失速率开始减小,腐蚀速率降低。另外可以看出,试样在不同砂粒粒径下冲刷质量损失速率均明显高于腐蚀质量损失速率,可知冲刷磨损的影响作用大于腐蚀的影响作用。不同砂粒粒径下的腐蚀质量损失速率变化不大,这是由于在不加入砂粒的情况下,流速、Cl-浓度等实验条件相同,腐蚀产生的影响作用变化不大。
图4 不同粒径下20号钢的质量损失速率
对不同砂粒粒径下冲刷腐蚀各分量进行量化,结果如表3所示。从表中可以看出腐蚀促进冲刷的作用先增大后减小,这是因为粒子的冲击动能随粒径的增大而增大,使得腐蚀过程中产生的腐蚀产物更易变成片层,随而滋生裂纹;当裂纹扩展到一定程度时腐蚀产物层从基体表面掉落,从而促进了冲刷[18]。而当粒径再增长时,由于砂粒较易破碎对腐蚀产物的冲击破坏作用减弱,因此腐蚀产物在材料表面形成致密的保护膜,抑制了冲刷。在不同的砂粒粒径下冲刷促进腐蚀的作用相接近,呈先增大后减小的趋势。这是由于固体粒子的冲击导致金属表面粗糙化,材料比表面积增加,加快腐蚀过程。当粒径增大到200~300 μm时,冲击壁面频率降低,材料表面粗糙化不明显,从而使得材料表面受到腐蚀作用的影响降低。根据Stack等[19]提出的关于冲刷腐蚀过程中主导因数判定表,如表4所示,可以看出在砂粒粒径为40~70 μm到120~200 μm时,材料冲刷腐蚀以冲刷-电化学混合控制为主,其中冲刷占据主导地位;砂粒粒径为200~300 μm时,以冲刷磨损为主导。
表3 不同粒径条件下冲刷腐蚀各分量定量分析结果
表4 冲刷腐蚀过程中主导因素判定表
2.1.4 腐蚀形貌
图5是试样在冲刷腐蚀试验10 h后的表面形貌。可以看出,在不同砂粒粒径下试样表面均出现了腐蚀坑;在粒径为40~70 μm时,试样表面腐蚀坑较少且较浅,说明砂粒对试样产生的冲刷作用不明显;随着砂粒粒径的增大,腐蚀坑逐渐增多并且加深,可见砂粒的冲刷作用影响变大;当砂粒粒径增大到200~300 μm时,试样表面的腐蚀坑有所变浅,砂粒对试样的冲刷作用变弱[16]。
图5 不同粒径下20号钢的冲刷腐蚀形貌
2.2 温度对20号钢冲刷腐蚀协同作用的影响
2.2.1 极化曲线测试
不同温度下冲刷腐蚀极化曲线如图6所示。各温度下金属阳极正常溶解,为活性区腐蚀。随着温度的升高,自腐蚀电位明显负移,说明温度越高腐蚀越容易[20]。
图6 不同温度下20号钢的冲刷腐蚀极化曲线
不同温度下冲刷腐蚀极化曲线拟合数据如表5所示。可知温度越高,腐蚀电流密度越大,因为阴、阳极的氧化还原反应控制腐蚀速率,温度升高,氧的传质速率增大,阴极极化率相应减小,因此促进了阴极还原反应和阳极氧化反应[21-24]。另外,温度升高,液体粘度降低,使得在液体中漂浮的颗粒在抵达试样表面时,更容易推开“液体膜”,分散掉积聚在试样表面的前进颗粒。在此过程中,固体颗粒的动能损耗减少,也就是“挤压膜效应”[25]减弱,固体颗粒撞击动能增大,电极表面的损坏程度加剧,从而试样的腐蚀速率随着温度的升高而增大。
表5 20号钢在不同温度下冲刷腐蚀极化曲线拟合数据
2.2.2 电化学阻抗谱测试
各温度下20号钢纯腐蚀电化学阻抗谱如图7所示。可见,温度越高,容抗弧半径越小,表明温度的上升使得20号钢的耐腐蚀性能变差,腐蚀速率增大。当温度增加到80 ℃时,容抗弧半径急剧减小,试样表面阻力大幅度降低,腐蚀速率急剧增加。还可以可以看出,60 ℃为临界温度。
图7 各温度下20号钢纯腐蚀电化学阻抗谱
图8为不同温度下冲刷腐蚀的电化学阻抗谱,所呈现出的频谱特征为双容抗弧,表明电极表面存在局部活化极化过程,这与形貌观察一致,存在点蚀坑。相比于纯腐蚀电化学阻抗谱,容抗弧半径整体较小,说明20号钢在不同温度下冲刷腐蚀的腐蚀速率比纯腐蚀的腐蚀速率高。由图可见温度越高,容抗弧半径越小,且减小幅度较大,表明试样的冲刷腐蚀行为受温度的影响较为显著,温度越高,腐蚀速率越大。
图8 各温度下20号钢冲刷腐蚀电化学阻抗谱
考虑到点蚀的存在,使用图9所示的等效电路,拟合数据如表6所示。由于近似拟合,拟合数据有一定的偏差,可以认为60和80 ℃下的溶液电阻基本相同。可以看出,温度越高,溶液电阻Rs越小。随着温度的上升,电极整体极化电阻Rp1大幅度下降,20 ℃下的整体极化电阻Rp1近似为80 ℃下的28倍,因此温度升高使得腐蚀速率剧增。
图9 不同温度下20号钢的拟合等效电路图
表6 不同温度下20号钢的电化学阻抗谱拟合数据
2.2.3 失重数据分析
不同温度下冲刷、腐蚀和冲刷腐蚀质量损失速率如图10所示。从图中可以看出,三者的质量损失速率均随温度的升高而增加,且冲刷和冲刷腐蚀的增加幅度较大,近似呈线性增加,表明温度对材料冲刷腐蚀的影响比较关键。质量损失速率增加除了上述分析的原因外,另一方面是由于金属表面膜的特性以及再钝化能力也会因为温度的升高而发生变化[26],从而导致材料抑制冲刷腐蚀的能力降低。这与张毅和董俊慧等[27]的研究结果一致。另外,材料的冲刷质量损失速率明显高于腐蚀的质量损失速率。
图10 不同温度下20号钢的质量损失速率
根据式 (3)~(6) 对冲刷腐蚀各分量进行量化,进一步分析温度对20号钢的冲刷腐蚀协同作用的影响,结果如表7所示。
表7 不同温度下的腐蚀数据分析
从表中可以看出,腐蚀对冲刷的促进作用随着温度的升高而增加。这是由于温度上升,腐蚀电化学反应增强,工作电极表面由于腐蚀而变得粗糙,并且材料的晶界、相界也随之减弱,导致材料的抗磨损性能降低,所以冲刷得到了促进[28]。根据主导因素判定表可以看出,在不同的温度下,材料的冲刷腐蚀均以冲刷-电化学为主要控制,其中冲刷磨损为主导。
2.2.4 腐蚀形貌
图11是试样在冲刷腐蚀10 h后的表面形貌。从图中可以看出,在不同温度下试样表面均出现了腐蚀坑,随着温度的升高腐蚀坑逐渐增多并且加深,说明冲刷切削作用加剧。此外,可以观察到温度越高,材料表面的冲刷切削痕迹越明显。
图11 不同温度下20号钢冲刷腐蚀形貌
3 结论
(1) 20号钢的腐蚀速率随砂粒粒径的增大先升高后降低。在所研究的四种砂粒粒径中,120~200 μm的粒径对试样的冲刷作用影响最大。
(2) 20号钢在冲刷腐蚀过程中,砂粒粒径为40~70 μm到120~200 μm时,以冲刷-电化学混合控制为主,其中冲刷占据主导地位;砂粒粒径为200~300 μm时,以冲刷磨损为主导。
(3) 温度变化对20号钢的冲刷腐蚀产生的作用比较明显,温度增高,腐蚀速率显著增大。
(4) 20号钢在不同温度下的冲刷腐蚀过程中均以冲刷-电化学混合控制为主。
参考文献
1 Dai Z, Shen S M, Ding G Q. Erosion-corrosion and protection of metals in fluids with solid particles [J]. Corros. Prot., 2007, 28: 86
1 代真, 沈士明, 丁国铨. 金属在固液两相流体中的冲刷腐蚀及其防护 [J]. 腐蚀与防护, 2007, 28: 86
2 López D, Falleiros N A, Tschiptschin A P. Effect of nitrogen on the corrosion-erosion synergism in an austenitic stainless steel [J]. Tribol. Int., 2011, 44: 610
3 Khan R, Ya H H, Pao W, et al. Erosion-corrosion of 30°, 60° and 90° carbon steel elbows in a multiphase flow containing sand particles [J]. Materials, 2019, 12: 3898
4 Xiang H L, Hu Y R, Cao H T, et al. Erosion-corrosion behavior of SAF3207 hyper-duplex stainless steel [J]. Int. J. Mine. Metall. Mater., 2019, 26: 1415
5 Malka R, Ne?i? S, Gulino D A. Erosion-corrosion and synergistic effects in disturbed liquid-particle flow [J]. Wear, 2007, 262: 791
6 Zadeh S A, Rashidi P. The effect of fluid velocity and microstructure on erosion corrosion of two-phase CK45 steel [J]. Results Mater., 2020, 6: 100077
7 Xu Z. Research on the erosion-corrosion behavior of P110 steel in liquid-solid two-phase flow [D]. Daqing: Northeast Petroleum University, 2011
7 徐哲. 液固两相流条件下P110钢冲刷腐蚀研究 [D]. 大庆: 东北石油大学, 2011
8 Aguirre J, Walczak M. Effect of dissolved copper ions on erosion-corrosion synergy of X65 steel in simulated copper tailing slurry [J]. Tribol. Int., 2017, 114: 329
9 Khayatan N, Ghasemi H M, Abedini M. Synergistic erosion-corrosion behavior of commercially pure titanium at various impingement angles [J]. Wear, 2017, 380/381: 154
10 Zhang F X, Ba D, Liu H T, et al. Study on the erosion and corrosion of super 13Cr tubing in fracturing [J]. China Pet. Mach., 2014, 42(8): 89
10 张福祥, 巴旦, 刘洪涛等. 压裂过程超级13Cr油管冲刷腐蚀交互作用研究 [J]. 石油机械, 2014, 42(8): 89
11 Owen J, Ramsey C, Barker R, et al. Erosion-corrosion interactions of X65 carbon steel in aqueous CO2 environments [J]. Wear, 2018, 414/415: 376
12 Zhang A F, Xing J D, Zhou X Y. A quantitative investigation on interaction between erosion and corrosion of carbon steel and stainless steel in corrosion slurry [J]. Foundry, 2003, 52: 260
12 张安峰, 邢建东, 周心艳. 碳钢与不锈钢在腐蚀浆料中冲刷腐蚀交互作用的定量研究 [J]. 铸造, 2003, 52: 260
13 Lin Y Z, Liu J J, Yong X Y, et al. Application of numerical method to study of flow-induced corrosion—(I) metal corrosion under laminar condition [J]. J. Chin. Soc. Corros. Prot., 1999, 19: 1
13 林玉珍, 刘景军, 雍兴跃等. 数值计算法在流体腐蚀研究中的应用—(I) 层流条件下金属的腐蚀 [J]. 中国腐蚀与防护学报, 1999, 19: 1
14 Li P. Study on erosion-corrosion behavior of stainless steel in acidic liquid-solid two-phase flow [D]. Wuhan: Huazhong University of Science and Technology, 2006
14 李平. 酸性液固两相流中不锈钢冲刷腐蚀行为的研究 [D]. 武汉: 华中科技大学, 2006
15 Cao X W, Xu K, Peng W S. Simulation and analysis of liquid-solid two-phase flow erosion failure in pipe bends [J]. Surf. Technol., 2016, 45(8): 124
15 曹学文, 胥锟, 彭文山. 弯管液固两相流冲蚀失效模拟分析 [J]. 表面技术, 2016, 45(8): 124
16 Jiang Z C, Yang Y, Peng H P, et al. Erosion corrosion behavior of X80 steel in multiphase flow with different sand particle sizes [J]. Corros. Prot., 2018, 37(11): 76
16 姜志超, 杨燕, 彭浩平等. X80钢在不同砂粒粒径下的多相流中的冲刷腐蚀行为 [J]. 腐蚀防护, 2018, 37(11): 76
17 Cao C N, Zhang J Q. An Introduction to Electrochemical Impedance Spectroscopy [M]. Beijing: Science Press, 2002
17 曹楚南, 张鉴清. 电化学阻抗谱导论 [M]. 北京: 科学出版社, 2002
18 Li Q. Study of local erosion-corrosion of pipeline steel under multiphase flow of oil/water/sand [D]. Qingdao: China University of Petroleum (East China), 2013
18 李强. 管线钢油/水/砂多相流冲刷局部腐蚀研究 [D]. 青岛: 中国石油大学 (华东), 2013
19 Stack M M, El Badia T M A. Mapping erosion-corrosion of WC/Co-Cr based composite coatings: particle velocity and applied potential effects [J]. Surf. Coat. Technol., 2006, 201: 1335
20 Zhang X Y, Zhu C, Sun L L, et al. Erosion-corrosion influence of sand particle size and chloride ions on P110 steel [J]. Chem. Eng. Mach., 2012, 39: 447
20 张旭昀, 朱闯, 孙丽丽等. 砂粒和氯离子对P110钢冲刷与腐蚀性能的影响 [J]. 化工机械, 2012, 39: 447
21 Hao L S, Zheng F, Chen X P, et al. Erosion corrosion behavior of aluminum in flowing deionized water at various temperatures [J]. Materials, 2020, 13: 779
22 Zhu J, Zhang Q B, Chen Y, et al. Progress of study on erosion-corrosion [J]. J. Chin. Soc. Corros. Prot., 2014, 34: 199
22 朱娟, 张乔斌, 陈宇等. 冲刷腐蚀的研究现状 [J]. 中国腐蚀与防护学报, 2014, 34: 199
23 Hu X, Neville A. The electrochemical response of stainless steels in liquid-solid impingement [J]. Wear, 2005, 258: 641
24 Neville A, Reyes M, Xu H. Examining corrosion effects and corrosion/erosion interactions on metallic materials in aqueous slurries [J]. Tribol. Int., 2002, 35: 643
25 Clark H M, Burmeister L C. The influence of the squeeze film on particle impact velocities in erosion [J]. Int. J. Impact Eng., 1992, 12: 415
26 Wang J C. Synergistic effect of erosion-corrosion of liquid-solid two-phase fluid [J]. J. Henan Sci. Technol., 2013, (10): 60
26 王建才. 液固两相流体冲刷腐蚀的协同作用 [J]. 河南科技, 2013, (10): 60
27 Zhang Y, Dong J H. Effect of dentist, temperature and scouring on the soda corrosion resistance performance of Ni-Cu alloy cast iron [J]. Found. Technol., 2011, 32: 642
27 张毅, 董俊慧. 烧碱浓度、温度、冲刷对镍铜合金铸铁耐碱腐蚀性能的影响 [J]. 铸造技术, 2011, 32: 642
免责声明:本网站所转载的文字、图片与视频资料版权归原创作者所有,如果涉及侵权,请第一时间联系本网删除。
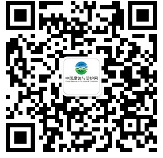
官方微信
《中国腐蚀与防护网电子期刊》征订启事
- 投稿联系:编辑部
- 电话:010-62316606-806
- 邮箱:fsfhzy666@163.com
- 中国腐蚀与防护网官方QQ群:140808414