微弧氧化(MAO) 是在电解质溶液中利用热化学、等离子体化学以及电化学方法在Al、Mg、Ti 等金属及其合金表面,通过产生火花放电而生成一种陶瓷膜层的方法,与化学转化、电镀、化学镀以及有机涂装等表面防护技术相比,MAO技术所制备的膜层具有优异防腐抗磨性能,引起了科学界浓厚的研究兴趣和工程界对应用开发的极大关注。MAO属于一种多因素控制技术,处理过程中将会受到诸如能量参数(包括电流密度、电压、频率、占空比及处理时间)、溶液特性(包括溶液成分、浓度、温度、电导率及pH 值) 及基体合金元素等多种因素的影响,并伴随化学、电化学、热化学以及等离子化学反应。因此,除了工艺和机理研究的复杂性外,涂层质量以及工程应用的可控性,都使该技术面临重重困难。迄今为止,学者们的研究内容主要包括:(1)MAO机理;(2) 电源特性、工作模式、电参数及氧化时间;(3) 电解液组成、温度、电导率、pH值及电解质浓度;(4) 镁合金基体组成、结构及前处理;(5) MAO膜后处理。相关研究动态和进展在文献中都有综述,本文将从以上几个方面就MAO技术及其在镁合金表面防护领域的研究动态进行简要综述,供同行参考。
1 微弧氧化
1.1 MAO发展历程
MAO 发展历程的示意图如图1 所示。早在1880 年,前苏联科学家Sluginov等就已经发现了浸入电解液中的金属通电后会产生发光现象。但直到1923 年,有专利记载Dunstan 等开始在铬酸盐溶液里对Al 及铝合金进行阳极氧化处理(Mg 及其合金的阳极氧化处理研究滞后约10 年)。1932 年,德国科学家Günterschulze 和Betz[的研究揭示了浸入电解液中的金属在高电场下会出现火花放电现象,但也指出火花对氧化膜具有破坏作用,从而认为“制备涂层的电压不应高于火花电压”,这在一定程度上限制了对该现象的深入研究。虽然在1941 年和1947 年的授权专利中提出使用大电流密度在酸性溶液中对Mg及其合金进行阳极氧化处理的方法,但有研究者认为MAO开始研究的时间应以20世纪60年代美国科学家McNeil和Gruss[14-16]利用这种阳极火花放电现象在金属表面沉积金属氧化物涂层为标志。着名的Mg及其合金阳极氧化工艺,如Cr-22、Dow17以及HAE,就是在这一时期报道的。
随后,美国Illinois 大学Brown 课题组、前苏联科学家Markov课题组和德国Karl-Marx-Stadt工业大学Kurze课题组先后开始了Al、Mg、Ti、Zr等阀金属表面火花放电沉积涂层的研究,并将这一方法分别命名为阳极火花沉积(ASD)、MAO和火花放电阳极氧化(ANOF)。20 世纪80 年代后,MAO技术已经成为美、德、俄、日等国家研究的热点,并将此项技术从实验室研究转向工业应用。20 世纪90 年代后,我国学者才逐步开展MAO相关技术研究,进一步丰富了MAO技术及其在金属表面处理领域的潜在应用,对该技术的发展和推广起到了很大的推动作用。
此外,根据液相等离子体的放电现象和作用原理,MAO还被称作等离子体电解氧化(PEO)、微弧放电氧化(MDO)、微等离子体氧化(MPO)。
从发表文献量来看,使用MAO和PEO 两种名称的文献居多。由于MAO只是等离子体氧化过程中电压较高时微弧放电的一个阶段,该名称叫法不妥,所以很多学者更青睐于PEO这个名称,但国内普遍使用“MAO”这一名称。
1.2 MAO过程及其机理
MAO过程中的实验现象、电压及电流之间的关系如图2 所示。MAO的基本工艺过程包括:钝化阶段、阳极氧化阶段、火花放电阶段、MAO阶段和弧光放电(或熄弧) 阶段。在临界击穿电位U3之前,材料表面依次发生普通钝化、普通阳极氧化,形成一层薄的绝缘氧化膜;当施加电压高过击穿电位U3后,绝缘氧化膜被击穿,材料表面出现无数细小的白色火花,即为火花放电阶段。当电压继续增加至U4时,表面会出现移动的较大红色弧点,并伴随大量细小的白色火花,此时才是MAO阶段。继续通电一段时间,红色弧点逐渐变大,颜色逐渐变深,最终形成橘红色的火花并伴有大量白色火花;随反应的继续进行,一些跳动的弧点不再移动,而是停在某一部位连续放电,并发出尖锐的爆鸣声,此为弧光放电阶段,是一个击穿破坏膜层的过程。若停止通电,红色弧点减弱,数量逐渐减少,直至完全消失,即为熄弧阶段。
由于MAO是将操作电压由低压Faraday 区引入到高压放电区域,整个过程涉及到化学、电化学、热化学及等离子体化学的共同作用,其放电原理及膜层生长机制非常复杂。科学家根据火花放电的现象,提出了多种假设和模型解释微弧放电机理。
1967 年,Wood 等提出“电子雪崩”模型,认为在较高电场的影响下,溶液中的电子或阴离子进入氧化膜,与膜层中其他原子发生碰撞后,电离产生新的电子,膜层中电子电流密度随之不断增加并引起火花放电。1971 年,Vijh的研究阐述了产生火花放电的原因,并利用“电子雪崩”模型对放电过程中的析氧反应进行了解释。随后不久,Ikonopisov提出了电“Schottky 隧道”模型,用定量的理论模型推测了电子被注入到氧化膜导带中的过程,以及引起火花放电的原因,从而解释引起“雪崩”电子的来源。
同时,他首次引入了击穿电位(UB) 的概念,指出了影响UB的主要因素,包括基体金属材料的性质、所使用电解液的配方以及溶液的导电性能等。由于电流密度、电极的形状以及升压方式等对UB的影响较小,从而建立了电导率和UB与溶液温度之间的函数关系。同时,Van 等进一步研究了火花放电的整个过程,指出“电子雪崩”总是在氧化膜层最薄弱、最容易被击穿的区域首先进行,而放电时的巨大热应力则是产生“电子雪崩”的主要动力。同年,Nikoiaev等认为,在氧化膜内部存在大量的放电通道,在放电通道与阻挡层表面接近的区域内产生放电现象,促进膜层生长,从而提出了微桥放电模型。
20 世纪80 年代中期,Albella 等认为进入膜层中的电解质是MAO放电过程的高能离子。在氧化过程中,电解质离子形成杂质放电中心,产生等离子体放电,使电解质离子、氧离子与基体金属材料形成强烈反应而结合在一起;同时产生大量的热被释放出来,使已经形成的膜层在基体金属材料的表面熔融和烧结后便形成具有陶瓷结构的MAO膜层。而且,他还进一步完善了“Schottky 隧道”模型,阐明了UB与电解质浓度,膜层厚度与电压之间的关系。Krysmann等认为MAO能够在各种形状的零件上形成膜层的原因,是因为在阳极材料表面附近形成了类阴极(电解液/气体界面),使得表面发生均匀极化的结果,从而揭示了膜层结构与对应电压间的关系,并提出了火花沉积模型。在以上放电理论模型基础上,Epelfeld 等提出了“孔内放电(discharge-in-pore)”模型,认为氧化膜微孔底部绝缘层的介电击穿,诱发微孔内的气体放电,从而产生微弧放电现象。随后,Yerokhin 等研究证实了微弧放电直径非常接近MAO 膜外层微孔的平均尺寸。而Hussein 等和Wang 等借助光发射光谱技术(OES) 也表明了微孔内存在气体放电现象。“孔内放电”模型定性地解释了厚MAO膜在低压条件也能稳定生长的原因。
最近,Mi 等根据金属和气体电子特点,提出了“热电子散射(thermal electron emission)”模型,分析认为由于电子隧道效应和杂质离子化,在微弧放电前的绝缘层表面能够产生电子电流,高能量电子电流引起热电子散射,散射出的电子与气泡内的原子碰撞并使其离化,从而形成等离子体放电。这一理论模型与他自己的实验结果很好地吻合,但还有待进一步的证实。
由此可见,MAO 过程的非Faraday 特性,以及伴随的放电现象和复杂的化学过程,至今还未形成一套全面而合理的模型解释放电现象。而关于膜层生长机理,在不同的电解液体系中存在差异,这在文献中有详细报道,这里不再赘述。
2 MAO应用于镁合金表面防护
2.1 电源特性
MAO处理高耗能是限制其广泛应用的主要瓶颈,而电源是MAO处理中可以灵活控制的系统环节,改进电源特性,优化电源电参数,是降低能耗并获得最佳涂层性能的重要途径。单一电源形成的MAO膜质量和性能不佳,因而先后出现了直流电源、交流电源、单脉冲电源、直流和交流复合电源、直流和脉冲复合电源、双脉冲电源、三角波电源等。
Jin等分别采用直流和高频双极性脉冲电源对AZ91D镁合金进行MAO处理。结果表明,处理时间相同时,双极性脉冲电源处理的膜层生长速率快,膜层更致密,硬度高,耐磨性更好。Wang 等研究也证实了双极性模式获得的膜层结构致密,防腐性能更佳。Hussein 等详细研究了单极、双极、单极+双极和双极+单极模式下的等离子体过程与膜层结构的关系,结果表明采用单极+双极的电源模式获得的膜层孔隙率最低,膜层致密。
因此,从工艺开发需求和电源开发趋势看,双极性不对称脉冲电源或混合电源将是电源发展的主流。
2.2 工作模式
不同电源均可通过恒流、恒压或恒功率等工作模式实现MAO处理。一般来说,恒流控制便于计算和控制能耗,但MAO的后期容易破坏膜层;恒压控制可以有效地解决恒流模式中电解液对基体钝化性能差的问题,能方便控制膜层的厚度及表面均匀度,但对电源功率的要求较高,存在MAO后期击穿不够,导致所制得的膜层较薄。研究人员在7 g/L NaOH+4 g/L (NaPO3)6+0.4 g/L 乙酸钙体系中比较了AZ91D镁合金在3 种电源模式(恒压、恒流和恒功率) 下涂层的结构及性能,结果见图3。表明,在相同时间内,恒压模式下的MAO膜具有最大的粗糙度、厚度和耐均匀腐蚀性能;而恒功率模式可获得表面粗糙度最低、致密及最佳耐点腐蚀能力的膜层。在硅酸盐体系中,本课题组的研究[54]进一步表明,与恒压模式相比,恒功率控制使得镁合金MAO初期在大电流的环境下起弧,而后期是在高电压环境下完成MAO,整个过程都是在较为极端的条件下进行,不容易控制,导致所形成的MAO膜具有较少的微孔,但较大的孔径和较快的生长速度,不利于提高膜层的防腐性能。
2.3 电参数
MAO电参数主要包括电流密度(恒流模式)、氧化电压(恒压模式)、频率(脉冲电源) 和占空比(脉冲电源) 等。不同电源类型或工作模式,各电参数对膜层厚度、表面结构及性能的影响规律基本一致。但由于电解液类型的不同,各参数的最佳工艺存在差异。
2.3.1 电压
在恒压模式下,随电压的升高,氧化膜生长速率增大,膜层厚度、表面孔隙率及防腐性均增加,但电压过高,易导致膜层局部击穿及防腐性能失效。在恒流模式下,存在起始电压与终止电压。Zhang等研究表明,工艺参数对耐蚀性影响程度从高到低的顺序为:终止电压>频率>占空比>电流密度。试样表面粗糙度随终止电压的升高而增加,与起始电压变化的关系不明显。当起始电压相等时,终止电压愈大,膜层越厚,但孔径增大,显微缺陷增多,耐蚀性下降。当终止电压相等时,起始电压愈高,膜层厚度也愈厚。
有研究表明,在恒压模式下施加负向电压,能中和绝缘膜层上的电荷积累,有利于膜层表面低温相和表面疏松物质的溶解,制备更致密的膜层,从而提高膜层的防腐性能。
董海荣等在硅酸盐电解液体系中采用恒压、变压两种加压方式研究AZ91D镁合金MAO膜层的厚度、表面形貌、物相组成及防腐性随时间的变化规律。结果表明,两种加压方式下,膜层结构随时间的变化规律基本相同,恒压加压方式下膜层的耐蚀性不断增强,变压加压方式下则先增大后减小;与变压加压方式相比,恒压加压方式下膜层生长前期的生长速率较大,更有利于工业化生产。
吕维玲等在恒压模式硅酸盐体系中研究了加压幅度和加压时间间隔对MAO膜层结构和性能的影响。结果表明,随着加压幅度和加压时间间隔的增大,膜层的厚度、孔隙率和结合力都呈先增大后减小的趋势;在加压幅度为25 V、加压时间间隔为150 s时,所获得的MAO膜层防腐性能最佳。
可见,采用不同的加压方式、加压幅度以及负向电压等工艺,为恒压模式电参数工艺优化提高MAO膜防腐性能提供了有效途径。
2.3.2 电流密度
在恒流控制模式下,电流密度是决定氧化过程能否进行的重要指标,是影响膜层性能和质量的决定性因素。研究表明,随着电流密度的增大,微弧放电能量增大,熔融物增多,放电微孔孔径增大,氧化膜层生长速率增大,膜层厚度随之增加,粗糙度增大,晶化程度增大。防腐性能和硬度随电流密度升高而增大。但超过极限值时,膜层生长速率下降,致密性变差,防腐性能降低。依据文献数据,电流密度参数主要集中在0.2~20 A/dm2之间。
2.3.3 频率
频率是指单位时间脉冲震荡的次数。无论是恒压模式或恒流模式,作用在膜层上的能量相差不大,电场的驱动力也近似相同,膜层生长速率基本不变,因此对膜层厚度的变化影响较小。
但随频率的升高,单位时间脉冲震荡的次数增加,单位时间发生击穿区域的数量增多,单脉冲能量也就越小,发生一次击穿时能量也小,膜层表面放电微孔孔径较小,膜层较致密,耐蚀性较好。最近,苏立武等研究得到了相反的结果。如图4 所示,在脉宽和脉冲电流不变的条件下,随着脉冲频率增加膜层表面火山堆状微孔数量减少,孔径增大。分析认为,脉冲频率的增加并不影响单脉冲能量,而是增加了单位时间内试样表面的总能量,导致多次重复击穿的熔融产物数量增多,所需放电通道直径变大。
关于该实验结果及该作用下膜层的防腐性是否提高,还有待于进一步证实。
2.3.4 占空比
占空比是在一个脉冲周期内电流导通时间与整个周期的比值,它决定了单脉冲的放电时间。研究表明,占空比低于45%时,对膜层的防腐性能影响不大。但高于此值时,膜层孔径增大,表面出现击穿破坏,从而导致防腐性能降低。
这是由于占空比越大,导致单脉冲放电时间越长,样品表面能量过大,会使膜层局部发生强烈放电,引起膜层表面烧损;同时,表面能量增加导致热析出增大,放电区的温度迅速升高,在放电区膜层的熔融量增多,熔融物在快速凝固时形成较大气孔,从而导致其致密性下降,防腐性能降低。孙磊等研究了恒流模式下阶段占空比对膜层结构和性能的影响,分析认为MAO初期应采用较大占空比有利于钝化膜击穿,MAO中期适当降低占空比有利于膜层平稳生长,膜层生长后期采用较小占空比可以较好地修复膜层,从而可获得微观结构均匀致密的耐蚀膜层。
2.4 电解液
MAO电解液的主要作用有:作为电流传导的介质;以含氧盐的形式提供所需要的氧;电解质的组分通过电化学反应进入膜层,改善MAO膜性能。一般来说,电解液由成膜剂和添加剂两类物质组成。
成膜剂往往是Mg的钝化剂,由氟化物、氢氧化物、碳酸盐、硼酸盐、磷酸盐、硅酸盐和铝酸盐等物质中的一种或几种组成,它们能与Mg2+形成稳定沉淀,是阳极氧化膜的主要成分。添加剂是以改变工艺参数或改善膜层性能为目的而添加的物质,如醇、羧酸和有机胺可以降低电流密度或起弧电压,Al2O3,SiO2和ZrO2等纳米颗粒可以增强膜层耐磨性能。
2.4.1 常用电解液及影响因素
目前,常用电解液主要有硅酸盐体系、磷酸盐体系、铝酸盐体系以及它们之间的混合体系。但磷酸盐电解液污染环境,而铝酸盐、硅酸盐体系更易成膜,制备的膜层防腐性能较好。Chai 等分别研究了以Na2SiO3,Na3PO4,NaAlO2和Na2MoO4为成膜剂的电解液体系,认为硅酸盐体系得到的膜层耐蚀性最佳。随后,Ghasemi等的研究也证实了在KOH 与Na2SiO3,Na3PO4 和NaAlO2中任意单一组合电解液中,膜层对MAO处理液中的离子吸附具有选择性,吸附性最强的是SiO32-,且在硅酸盐体系中获得的膜层最厚,并具有最小的孔密度和最佳的耐蚀性能。然而,Seyfoori等研究表明,AZ31 镁合金在磷酸盐体系中获得的MAO膜比硅酸盐体系中的更厚、更耐蚀。Bai 等比较了AZ91D 镁合金在磷酸盐体系、硅酸盐体系及磷酸-硅酸盐体系电解液中表面MAO膜层的性能,结果表明,在0.1 mol/L 的磷酸盐体系中引入0.08 mol/L 的Na2SiO3时,便使电解液的起弧电压从磷酸盐体系的400 V降到了200 V,且膜层孔隙率降低,微孔直径减小,耐蚀性增强。Mori 等研究了磷酸盐与硅酸盐浓度比(100∶0~0∶100) 对MAO膜结构和性能的影响,结果表明,当磷酸盐与硅酸盐浓度比为20% (即P∶Si=20∶80) 时,在AZ31B镁合金表面获得的MAO膜具有最佳的腐蚀防护能力。因此,以硅酸盐为主的复合电解液已成为当前研究的主要体系。
电解液的电导率及电解质浓度一直被认为是MAO过程中影响起弧电压的关键因素,也决定着膜层的结构和性能。研究认为,硅酸盐体系以及硅酸盐-磷酸盐复合体系溶液的电导率为4~6 (Ω·m)-1时,所得膜层的防腐性能最佳。张龙等的研究认为电解质浓度,尤其是主盐如硅酸钠,显着影响镁合金微弧等离子体的诱发过程和膜层的微观结构。分析也表明溶质离子种类才是诱发微弧等离子体和促进膜层生长的最主要因素,pH值和电导率并不是本质因素。姚力夫等研究表明,电解质浓度影响MAO膜的厚度、表面结构及性能,在硅酸盐电解液中引入5 g/L (NaPO3)6时在镁合金表面获得的膜层耐蚀性最佳。Simchen 等证实MAO的起弧电压取决于电解液中阴离子的类型及浓度,而不是电解液电导率,这与文献的研究结果一致。Ono等也进一步证实相同电参数条件下,MAO膜的厚度和耐蚀性取决于电解质浓度,而与电流密度无关。可见,电解质的浓度过低,MAO过程难以进行;电解质的浓度过高会加速氧化膜的溶解,且影响膜层的致密性和防腐性能,必须控制在一个合适的范围内。
除了电解质种类、浓度及其溶液电导率外,电解液温度和pH值也会影响MAO过程的成膜速率和膜层质量。电解液温度对溶液电导率的影响较大,温度每升高10 ℃,电解液电导率约增加12%。而电导率的增加会减小膜层的起弧电压,促进膜层生长,增大表面微孔尺寸,容易降低膜层防腐性能。此外,过高的温度还会造成膜层表面过烧现象。但过低的温度,MAO膜的生长速率慢,性能较差。因此,电解液温度通常控制在20~40 ℃之间,尤以约30 ℃获得的膜层性能最佳。对于镁合金MAO电解液的pH值一般控制在10~12之间,过高的pH值会加速膜层的溶解,降低膜层的致密性。此外,过高的pH值,容易缩短电解液的使用寿命,增加MAO处理成本。
2.4.2 添加剂
电解液添加剂可以分为有机添加剂和无机添加剂两大类。有机添加剂如醇类、有机胺类、有机硅氧烷、有机酸类及它们的盐等物质,这类添加剂主要是在MAO过程中起到抑弧作用,从而获得表面微孔分布均匀的氧化膜,提高膜层的致密性和防腐性;同时可起到降低能耗的效果,见表1。无机添加剂如石墨烯、Al2O3、SiO2等物质,这类添加剂在MAO过程中可以参与成膜,从而提高膜层的防腐、抗磨等性能,见表2。关于添加剂的种类和作用,在文献中都有详细分析,这里仅列表比较部分添加剂的作用,以供参考,不再详细赘述。
2.5 后处理
由于微弧放电作用导致MAO膜具有微观多孔的结构,这种结构特征大大降低了膜层对基体的防腐抗磨性能。因此,必须对MAO膜进行封孔或复合涂层处理来提高其对镁合金基体腐蚀磨损的防护能力。
2.5.1 封孔处理
封孔的主要方法有沸水、铬酸盐、硅酸盐、磷酸盐、碳酸盐、溶胶-凝胶、石蜡以及有机物封孔等。蒋百灵等对MAO 膜用石蜡、丙烯酸和沸水溶液进行封孔处理,分析表明,石蜡封孔耐蚀性效果最好。Kim 等比较了NaOH和Al(OH)3溶液对AZ91 镁合金MAO膜封孔的耐蚀性能,研究表明,1 mol/L NaOH在373 K处理30 min的封孔效果最佳。但袁兵等对MAO样品分别进行浸石蜡、喷涂聚苯乙烯泡沫银粉漆、电泳处理,经研究表明,MAO膜与电泳漆结合膜层的耐蚀性最佳。Jiang 等、Zhang 等以及本课题组利用MAO技术在镁合金表面构筑微纳结构,然后进行疏水改性,有效地提高了镁合金的耐蚀性能。图5 为MAO膜改性前后的表面形貌及其表面接触角,改性后涂层表面表现出超疏水性能。Cui 等利用聚甲基三甲氧基硅烷封孔MAO处理的AZ31 镁合金,在表面获得了自愈合MAO/聚硅烷复合涂层,有效提高了MAO膜的长效腐蚀防护能力。陈宁宁等将石墨烯与硬脂酸共混溶液滴涂在MAO处理的AZ91镁合金表面,获得静态接触角达到162°的超疏水膜层,有效地提高了MAO 膜对基体的腐蚀防护能力。然而,这些封孔及表面疏水改性,主要依靠物理吸附作用,效果持久性和耐磨性能较差。
最近,环境友好的铈盐封孔处理引起了很多学者的注意。Mohedano等研究了铈盐浓度和封孔时间对MAO膜层防护性能的影响。结果表明,MAO处理的AM50 镁合金在10 g/L Ce(NO3)3·6H2O+0.3 g/LH2O2溶液中30 ℃封孔3 h,获得的膜层封孔效果最佳。如图6 所示,封孔过程中产生的CeO2进入了氧化膜微孔内,从而提高了膜层的致密性,进一步提高了膜层的腐蚀防护能力。随后,Van Phuong 等采用两次封孔工艺密封MAO处理的AZ31 镁合金样品。首先在0.023 mol/L Ce(NO3)3·6H2O+0.25 mol/LH2O2溶液中(25±1) ℃封孔20 min,然后在0.1 mol/LNaH2PO4溶液中(90±1) ℃封孔20 min。结果显示,单一封孔处理的样品在0.5 mol/L NaCl 溶液中浸泡仅5 d 便出现明显的腐蚀特征,而复合封孔处理的样品浸泡20 d 未见腐蚀现象。
韩恩厚团队利用电解液中金属复盐在高温时发生分解参与成膜的原理,先后开展了氟锆酸盐、氟钛酸盐自封孔MAO技术。如图7 所示,MAO膜表面微孔内填充了物质,封住了微孔。随后,本课题组通过在硅酸盐体系中引入K2ZrF6,也获得了自封孔的MAO膜。这种自封孔MAO样品的耐蚀性比普通微弧氧化膜高,表面无需涂覆有机涂层就可以为Mg基体提供良好的腐蚀防护。
此外,陈宏等利用外加电场作用下胶体粒子向工件表面移动的原理,提出外加电场和MAO相结合的方法获得了自封孔MAO膜。如图8 所示,通过外加电场驱动带负电的Zr(OH)4胶体粒子进入微孔实现了微孔封闭的MAO膜。研究也表明,这种自封孔MAO膜样品的耐蚀性与膜层孔隙率及封孔填充物的成分和形态具有极大的相关性,且可通过调整外加电场强度和时间实现对自封孔的调控,从而改善防腐性能。Rehman等研究了两步MAO处理AZ91D 镁合金工艺。研究表明,第一步在Na2SiO3体系中氧化15 min,然后在含有K2ZrF6的硅酸盐复合体系中氧化10 min 时,涂层样品具有优异的耐蚀性能。如图9 所示,分析认为第二步MAO优先在第一步MAO膜的微孔区域发生击穿放电,从而实现对一次MAO膜的封孔,涂层致密化(表面孔隙率从5.6%降至1.2%),进一步提高了膜层的硬度和防腐性能。
由此可见,通过电解液掺杂,或外加电场,或多次工艺复合,都可实现封孔MAO膜。但相关的形成机理、优化工艺及性能强化仍需深入研究。
2.5.2 复合涂层处理
基于MAO膜与镁合金基体呈冶金结合及其表面微观多孔的特性,将物理气相沉积、有机涂层、大气等离子喷涂、化学镀/电镀等技术与MAO复合,可制备性能优异的功能涂层。如近期开展的工作:Yang 在镁合金表面构筑MAO/(Ti:N)-DLC 耐磨涂层;本课题组在镁合金表面构筑硬质涂层;Fan 等在MB26 镁合金表面制备MAO/(APS)Yb2SiO5热障涂层。这些复合涂层处理大大提高了MAO膜对镁合金基体的防腐抗磨性能。有关这方面的工作,在文献中有详细综述,这里不再赘述。
2.6 前处理
MAO处理前,对材料表面进行适当的前处理来改变其表面的组织结构,对后续的MAO处理及膜层的性能影响也是非常重要的。Wang 等通过含有Al(NO3)3 的溶液对AZ91D 镁合金进行超声预处理,结果提高了MAO膜均匀性,增强了膜层的腐蚀防护能力。Krishna 等首次采用冷喷涂技术在AZ91 镁合金表面预沉积Al 层,然后对其进行MAO处理,结果获得了梯度成分分布的镁铝尖晶石结构涂层,表现出了良好的防腐性能。Cai 等首先对AZ91D镁合金进行硝酸铈化学转化处理,然后进行MAO处理,获得了CeO2掺杂的致密MAO膜,并表现出优异的耐蚀性能。Hariprasad 等比较了铈盐转化作为MAO前处理和后处理对膜层防腐性能的影响。分析表明,铈盐转化膜前处理能够提供均匀的表面结构,进一步增强了后续MAO膜的致密性,从而提高了其对基体的腐蚀防护能力。可见,基体表面微结构或表面状态对MAO膜性能有显着的强化作用。
宋东福等研究表明,基体表面粗糙度影响MAO过程及膜层的防腐性能,与表面喷砂(Ra 2.2 μm) 相比,砂纸打磨(Ra 0.5 μm) 样品的耐蚀性能提高了40% 。Gheytani 等利用表面机械研磨技术(SMAT) 实现AZ31B镁合金表面纳米化(5~10 nm),再经MAO 处理所得膜层样品的极化电阻增加了700%,耐磨性增加了105%。由于表面机械研磨需要在真空环境中进行,限制了样品尺寸,加之环境粉尘和噪音污染,不利于大规模应用。Chen 等采用表面超声冷锻工艺(UCFT) 对镁合金进行表面纳米化(48.67 nm),分析结果也证实表面纳米化细化了AZ31B 镁合金表面晶粒,降低了表面粗糙度,获得了致密耐蚀的MAO膜。可见基体表面晶粒细化影响MAO膜层的致密性。
Wang 等通过激光表面熔融技术对AZ91D镁合金进行预处理,然后再进行MAO处理。研究表明激光表面熔融处理促进了镁合金表面晶粒细化、Al 富集以及第二相粒子(Mg17Al12) 的重新分布,增加了MAO膜层的致密性,显着提高了复合膜层的耐蚀性能。Wei 等研究了Al 含量对MAO膜结构及性能的影响。结果表明,随着Al 含量增加,镁合金中β相和共晶(α+β) 相数量增多,膜层孔隙率先减小后增加,从而影响了膜层的耐蚀性。随后,该课题组的Chen 等[证实了第二相粒子的尺寸影响MAO膜的结构。尺寸越细小,分布越均匀,所得膜层就越致密,耐蚀性就越好。
此外,基体表面微观结构构筑,如微米凹槽,对MAO能耗、膜层生长速率、硬度及耐蚀性能影响较大,但在镁合金表面报道较少,有待于进一步开展相关研究。
3 存在的问题与建议
从国内第一篇镁合金表面微弧氧化文献报道至今,经过二十多年的研究,镁合金表面MAO处理技术已经有了长足的发展,但MAO技术及其在镁合金表面的理论研究和应用仍存在许多不足,亟待进一步完善。
(1) MAO机理:仍无法用清晰的理论模型阐明MAO的火花放电及成膜过程,亟待从热力学、动力学角度及现代高科技分析技术,深入分析并完善理论模型,用于指导微弧氧化。
(2) 镁合金基体:基体的元素组成及表面状态,显着影响MAO膜的形成过程及性能,但由于镁合金基体组成的多元化、MAO前处理的多途径及研究的分散性,缺乏对某一合金MAO前处理的系统性研究。
(3) MAO电源:电源决定着不同工作模式下各电参数的特性,但各研究机构采用的电源或是企业成熟的设备技术或是自己研发的设备,加之在部分文献中对电源设备的各参数描述不够详细,导致各文献之间所得膜层与影响因素的关联性存在差异,数据的有效性和可参考性不足。
(4) 电解液:电解质种类及浓度显着影响MAO过程的起弧电压与膜层性能,但不同电源电参数调控下的电解液组成及电解质浓度差异较大,各组成尤其是阴离子对膜层某一性能(如防腐性) 的有益贡献和作用机理不清楚,加之文献中所采用的浓度单位或是g/L,或是mol/L,导致部分优化配方对理论研究或大规模工业化应用的可参考性不足。
(5) MAO膜性能强化:为强化MAO膜性能,可通过电解液掺杂、多步MAO处理、MAO辅助、MAO膜封孔及复合涂层等技术实现,但这些强化技术之间相对独立,对MAO膜性能的强化程度缺乏比较,且在机理、工艺优化及性能关联性等方面的研究不够完善。
此外,也期望国内知名机构或学者,建立MAO处理技术相关数据库,实现各电源、MAO工艺之间的数据共享,提高各数据的有效性和参考性,促进MAO技术的研究及其在工业中的大规模应用。
免责声明:本网站所转载的文字、图片与视频资料版权归原创作者所有,如果涉及侵权,请第一时间联系本网删除。
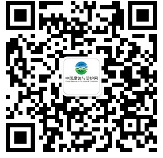
官方微信
《中国腐蚀与防护网电子期刊》征订启事
- 投稿联系:编辑部
- 电话:010-62313558-806
- 邮箱:fsfhzy666@163.com
- 中国腐蚀与防护网官方QQ群:140808414