1 前言
金属腐蚀过程为典型的多电极过程,至少为阴极和阳极组成的二电极过程。表面同时存在耦合的阴极过程和阳极过程,导致表面电化学状态分布不均匀。金属表面宏观和微观差异导致腐蚀局部过程普遍存在,如电化学活性差异引起的电偶腐蚀、溶解氧浓度差异诱发的氧浓差电池,钝化膜缺陷诱发的点蚀,焊缝区材料不均匀诱发焊缝腐蚀,应力集中诱发的应力腐蚀开裂等等。涂层失效过程也发展于局部缺陷,微生物附着也会诱发局部腐蚀。即使通常认为低碳钢为均匀腐蚀,其表面也处于时间和空间的不均匀状态。
金属腐蚀过程不均匀性起因于金属相、溶液相和界面相的不均匀。这些不均匀状态均体现在界面微区电化学状态不均匀分布,可以用电位、电流和阻抗等电化学参量来描述。
常规电化学方法测定的电化学参量均为整个电极表面平均值。如果局部表面过程比较弱,它的作用则因平均化而被忽略,即使能够测到也无法定位局部构成的位置和强度。而这些信息对深入认识金属局部腐蚀行为和机理具有重要的价值。
为了满足不均匀电化学过程研究的需要,近年来局部电化学研究方法获得了快速发展,主要体现在扫描振动参比电极 (SVET)、扫描Kelvin探针 (SKP)、局部电化学阻抗 (LEIS) 和扫描电化学显微镜 (SECM) 等4种技术。此外,还有扫描微探针 (微参比电极、微离子选择电极) 方法。
这些设备的主要结构为三维精密移动平台和微电极探针。这些方法的共同特点是精密移动平台操作控制方法基本相同,差别在于不同方法采用不同的行程、分辨率和驱动技术。SKP行程为100 mm,分辨率在1 μm以上,通常采用步进电机或伺服电机驱动;而SECM等要求分辨率在纳米以下时,常采用压电驱动技术。
这些方法的不同点在于采用不同的探针技术和不同的参量进行测量。SVET采用振动微电极测量溶液中金属表面电流分布;LEIS采用双电极技术测量金属表面阻抗分布;SKP采用振动电容方法测量气相环境中金属表面电位分布;SECM则利用超微电极非线性扩散技术测量溶液相电化学活性粒子分布。研究人员可根据各自的研究需要进行合理的选择。通常可以采用同一套三维精密移动平台配合不同的探针、电解池和软件技术来进行上述4种微区电化学测量和数据解析。
电化学阻抗技术 (EIS) 是向工作电极和参比电极之间施加一个小振幅正弦交变信号进行扰动,测定其间的阻抗谱响应,来获得电极过程信息。因而EIS反映的是电极界面的平均信息,无法提供局部过程信息。涂层降解、点蚀等很多腐蚀电化学过程发生在局部表面,如果这些局部过程初期较弱,面积较小,则很难在常规EIS谱中展现出来[1,2]。
随着近期电化学设备灵敏度的提高、微电极技术的发展[3,4]和LEIS信息的需求,LEIS技术应运而生,弥补了传统电化学阻抗法的不足[5]-[11]。在近年来获得了快速发展,不仅完善和发展了多种测量和数据解析方法,而且在金属腐蚀局部过程研究中获得了持续增加的应用,已经成为一种有广阔发展前景的新技术。
2 原理和装置
LEIS技术是向被测电极施加微扰电压,从而感生出交变电流,通过使用两个Pt微电极[12]确定金属表面上局部溶液交流电流密度来测量局部阻抗的技术。
LEIS技术有两种工作模式:局部电化学阻抗谱LEIS (localized electrochemical impedance spectroscopy) 和局部电化学阻抗分布图LEIM (localized electrochemical impedance mapping)。LEIS用于测量某点在不同频率下的阻抗响应。将尖端微米级的Pt探针置于试样上方,在电极上施加微小的扰动交流信号,进行点对点局部阻抗测量。LEIM用于单频率下对离散点的绘图测量。通过探针在试样指定区域的x-y平面上进行光栅扫描,确定特定频率下的阻抗分布[13]。
图1 用于局部交流阻抗的五电极结构示意图[12]
图1所示的五电极系统包含一个典型的三电极装置 (工作电极、对电极和参比电极) 和两个微参比电极。前者用于控制交流电压,用交流信号激发界面电位;后者用于检测溶液中试样表面的局部电位梯度[12]。
局部交流电流密度Ilocal可以根据两个Pt探针的电压差用Ohm定律求得[14], 再通过测定工作电极和参比电极之间的电压,得到局部电化学阻抗Zlocal,
。式中:κ为电解溶液的导电率;d为两个Pt电极之间的距离;Δφ是两个Pt微电极之间的交流电压差;ΔVapplied为参比电极和工作电极之间所施加扰动电压的大小。
LEIS测试装置如图2所示[15,16]。主要有恒电位仪、锁相放大器、电解池、x-y-z平台、控制系统、恒电势器、锁相放大器及计算机等。由计算机控制x-y-z平台可以调节微探针与电极间的距离和位置,恒电位仪向系统提供微扰电压,得到的信号经锁相放大器进入计算机,进行分析处理。
目前,该技术已经有商业产品,如Ametek公司的VersaScan系统和BioLogic公司的M370系统。
3 发展
20世纪80年代,Isaacs等[10]首先使用了扫描探针阻抗技术,用一个小的盘形探针 (包含微参比电极和对电极) 对被测电极进行局部极化。为了限制局部极化产生的电流,利用薄层电解池的几何形状,也就是使盘形探针与电极表面相隔30 μm。虽然该技术可以产生定性结果,但无法产生定量的局部电化学阻抗结果。而且,薄层电解池的几何形状可能显著影响自然腐蚀过程,例如改变传质过程。
图2 局部电化学阻抗技术装置图[15]
90年代,Lillard等[17]提出了一种新的测量局部阻抗谱的方法,前提是在传统三电极测试中,工作电极附近溶液的交流电密度与电极的局部阻抗成比例。通过测量两个探针电极间的交流电势差,获得了探针尖端的电流密度。再根据参比电极和工作电极之间所施加扰动电压的大小及Ohm定律得到局部交流阻抗值。
Zou等[18]使用直径10 μm的高分辨率Pt探针 (含有两个垂直于电极表面的微电极),测量具有恒电流密度或等电位分布的盘形电极附近的电流分布。将测得的交流电流密度与分析方程和计算机模拟得到的数据进行比较,发现二者比较吻合。同时发现,探针的空间分辨率随着探针的高度和两个微电极之间的距离的改变而改变,且对高度的改变比较敏感。
Frateur等[19,20]研究了电极几何结构和探针距盘形电极高度的影响。结果表明,盘形电极的几何形状影响电流和电压分布,进而影响频率分散及对Ohm阻抗的虚部贡献。当存在吸附物时,会发生低频分散[21,22]。Ferrari等[23]研究了局部电流密度的垂直和径向分布对LEIS图的影响。数值模拟结果表明,电极边缘附近径向电流对阻抗响应的影响显著,电极表现出阻塞和感应电流行为。电极中心的径向电流可忽略不计。Sánchez等[24]评估了电化学微电极几何特征对Cu腐蚀的影响,发现毛细管半径越大,对电极和工作电极之间的距离越长,Cu电极表面上形成的腐蚀产物越多。
Pilaski等[25]基于微毛细管电池技术[26]发展了LEIS系统,优点是可以测量与周围材料无关的一个小的表面区域,缺点是容易受周围环境的影响 (例如电耦合)。Bayet等[6,7,27]利用SVET装置发展了LEIS测试技术,利用探针的小尺寸减少了探针的屏蔽效应,还提出了通过测量局部电压和局部电流来定义局部阻抗[6]。该方法利用一个探针测量了两个位置的电压,但最大的缺点是探针在电极表面附近的振动引起了强制对流。
Annergren等[1]研究了不锈钢的点蚀行为,并测得了点蚀不同阶段的局部阻抗谱。该技术的不同之处是可以用某一频率下的绘图模式确定点蚀区域,或者用局部阻抗谱研究点蚀不同阶段的阻抗变化,分析动态界面的改变。点蚀的发展伴随着腐蚀点周围溶液阻抗的大幅降低。应用局部阻抗技术,在某一频率下测量金属表面各处的阻抗值,做出LEIM图,进而确定点蚀位置。Wittmann等[28]发现有机涂层的缺陷可以在肉眼观察之前用该技术鉴别。
Huang[29]-[31]等重新研究了LEIS的机理,并定义了3个阻抗值:局部表面阻抗 (Z0),包含穿过扩散双电层的局部电流密度和局部电压降;局部Ohm阻抗 (Ze),包含从扩散双电层外部到参比电极的局部电流密度和局部电压降;局部阻抗 (Z),是Z0和Ze之和。
值得注意的是,为了特殊的用途需要发展特定的装置。例如,为了研究聚合物电解质燃料电池[32][33],发展了一个允许LEIS响应同步记录和测量的实验装置。该装置在Hall效应电流传感器的基础上,使用了零电阻的Ampere计进行电流检测,通过局部测试方法观察到了水分和干燥因素的影响。
Bandarenka等[34]将LEIS技术与AC-SECM技术相结合,描述了固/液界面二维分布,改进了与频率有关的常规LEIS,并提出了观察界面处局部过程的独特方法。
Montoya等[35]使用有限元方法 (FEM) 求解了Laplace方程和适当的边界条件 (BC)。同时,当近似不均一的Neumann边界条件存在时,不能选择输入的交流阻抗信号。并用LEIM的实验结果证实了这一理论。
4 应用
LEIS/LEIM可以得到电流、电位、阻抗或导纳的二维彩色分布图象;阻抗谱的线、面扫描 (固定频率);阻抗谱点分析 (频率扫描,Bode,Nyquist等);三维彩色阻抗或导纳图像等。
因此,LEIS可以精确确定局部区域固/液界面的阻抗行为及相应参数,如不锈钢局部腐蚀速率,涂层完整性和均匀性 (如分层、缺陷、鼓泡区),涂层下或与金属界面间的局部腐蚀,缓蚀剂性能及不锈钢钝化/再钝化等多种电化学界面特性。
4.1 腐蚀机理研究
Xiao等[36]用LEIS研究了Fe-Cr合金在含有Cl-和SO42-的溶液中及3种不同pH值下的腐蚀行为。结果表明,Fe-Cr合金的高腐蚀阻抗是由于钝化膜的作用。当合金包含大量Cr时,钝化膜更易生成。但是,它的腐蚀阻抗值随pH值的变化而改变,特别是在最初腐蚀时。同时,腐蚀性Cl-作为导电介质也会破坏金属表面的保护膜。过程如下:
。这说明大气腐蚀中,Cl-会引起Fe(OH)2膜的溶解,如紧密氧化膜中产生的微小裂纹。腐蚀介质穿过裂缝进入基质加速腐蚀。
图3 在1 mmol/L Na2SO4溶液中暴露24 h的AZ91合金的SEM像 (黑色和亮色区分别对应α相和β相)[38]
早期常相元素 (CPE) 行为研究中使用的是理想极化电极,因此,CPE被认为是电容分散的影响。现在可以使用局部和整体阻抗法研究非理想极化电极。Jorcin等[37]利用LEIS技术分析了二维分布 (AZ91Mg合金) 和三维分布 (纯Al) 对CPE行为的影响。LEIS是评估CPE行为局部变化影响的较好方法,很容易观察到二维和三维分布的区别。Al电极相对于中心值进行标准化后的回归参数R和Q均与半径的位置有关,说明R和Q的变化与局部微观结构特征无关,而与盘形电极上的电流和电压分布有关。R和Q的分布说明存在阻抗的半径分布。整体阻抗是局部阻抗的二维分布,而各个局部阻抗具有固有的三维特征。因此,Al电极上的CPE行为是三维分布的结果,与Al的氧化物的三维不均一性有关。在二维分布 (AZ91Mg合金) 的情况下,CPE行为取决于高频阻抗的分布,该分布与盘形电极几何形状有关,但是电容与位置无关。
图4 腐蚀电压下在1 mmol/L Na2SO4溶液中暴露2 h的AZ91Mg合金LEIS响应的Nyquist图[38]
4.2 腐蚀影响因素研究
Galicia等[38]研究了纯Mg和AZ91 Mg合金在低腐蚀介质Na2SO4溶液中的电化学行为,以确定合金两相的反应活性。结果表明,之前建立的纯Mg腐蚀模型在Mg合金腐蚀中也占有一定比例。组成合金的两相腐蚀机理相同,由Mg的分解控制。但是,β相 (69.6%Mg,27.45%Al,质量分数) 分解的动力要比α相 (96.5%Mg,3.05%Al,质量分数) 低,这与扫描电镜 (SEM) 观察到的结果一致 (如图3)。图4表明β相的阻抗振幅大约是α相的3倍,高频电容回路的时间常数比α相小10倍。说明β相的腐蚀速率比α相小,这是由于主要合金元素Al的影响。
Jin等[39]利用LEIS技术原位测量了API X100钢的杂质在近中性溶液中的微电化学活性,发现杂质和临近的钢基体之间存在电化学异质性,因此,会形成电偶,导致局部优先溶解。杂质的局部电化学活性取决于其组成。富硅杂质具有高电化学活性,杂质 (阳极) 比临近的钢基体 (阴极) 活泼,杂质的优先溶解生成局部微孔,进而引起点蚀。富含Al2O3的杂质 (阴极) 比相邻的钢基体 (阳极) 更稳定。钢铁上发生的优先溶解,会造成杂质的“急降”,产生腐蚀坑。碳化物杂质的阻抗要比碳钢基体的高,说明碳化物要比碳钢基体稳定,没有出现界面阻抗的下降可能是由于在进行LEIS测试时界面处的优先溶解还未发生。
Meng等[40]用LEIS,SVET,EIS及表面分析技术研究了中性溶液中X70钢的腐蚀产物沉积对随后阴阳极反应的影响。新鲜暴露表面 (图5b) 上的电感回路比沉积物覆盖表面 (图5a) 小,说明钢电极表面覆盖一层腐蚀产物时,自催化作用会加强,这与中间产物在沉积物上的吸附有关。
图5 沉积物覆盖表面和新鲜暴露表面的LEIS图[40]
4.3 局部腐蚀研究
Zhang等[41]用EIS,LEIS,动电位极化曲线和原电池电流法研究了X65管线钢在模拟的CO2饱和油田地层水中的腐蚀和局部腐蚀行为,用SEM和能量色散X射线分析研究了腐蚀膜的形态和成分,并建立了概念模型说明钢在膜下的局部腐蚀。原电池电流法和LEIS测试结果表明,裸钢 (阳极) 和膜覆盖钢 (阴极) 之间存在原电池效应。大阴极小阳极结构会加速局部腐蚀。膜的稳定性随时间而增加,而膜下钢的局部腐蚀机理也随着时间而改变。电极上膜覆盖区与裸露区面积比的增加加速了裸钢的阳极溶解。同时,导致了较强的电偶腐蚀效应,并引发局部腐蚀。
图6 在100 mmol/L NaCl中测得开路电压下合金A的Nyquist图 [42]
Annergren等[42]将LEIS与传统EIS相结合研究了合金A (Cr13.5%,Mn0.3%,质量分数) 和合金B(Cr 13.5%,Mn0.3%,Mo1.0%,质量分数) 点蚀萌生和扩展的动力学规律,发现LEIS能够得到与人工点蚀技术相似的点蚀扩展信息。但是,LEIS能够探测钝化区的微小点蚀坑,而人工点蚀技术只能测量宏观尺度的点蚀。LEIS可以测量点蚀萌生的动力学和点蚀扩展的控制机理,而EIS只能得到平均化的信息。
在开路电位下,用EIS和LEIS同时测量Fe-Cr合金A和B点蚀的开始阶段。由图6a和7a可以看出,传统EIS图是一种典型的钝化行为,即高阻抗区具有电容性,低阻抗区点较分散。而LEIS的阻抗值要比EIS低,形状也不同,它同时具有电容回路和电感回路。合金B的谱图在低频区折回负实轴,可能是由于合金中的Mo在该阶段会促进腐蚀。图6b和7b则揭示了点蚀开始阶段溶解和腐蚀间复杂的竞争行为。
de Lima-Neto等[43]用双循环电化学电位再激活技术 (DLEPR) 和LEIS两种无损探伤技术,研究了焊接AISI 304不锈钢敏化区的扩展。LEIS测试结果显示,两种情况下的图谱都包含一个高频容抗弧和一个低频电感回路 (由于两种材料之间的电耦合),且探针在焊缝处时,两个图谱相似。随着探针远离焊缝,阻抗谱的低频区表现出纯电容性。当探针位置改变时,阻抗谱低频区发生频率的移动。LEIS上出现的感应线圈表明,焊缝 (阳极) 和焊接不锈钢板 (阴极) 间出现了电偶对,这不利于焊接体系的耐腐蚀性。
图7 在100 mmol/L NaCl中测得开路电压下合金B的Nyquist图[42]
Mouanga等[14]用LEIS技术结合伏安法和常规电化学方法研究了NaCl溶液中碳钢和Zn之间的电耦合。固定频率下的电化学测试显示,Zn溶解对Zn/Fe界面影响更大。Zn表面的局部阻抗图在低频区有一个大的电感回路。用有限元方法进行数值模拟,消除了电偶电流的径向影响,使Zn试样得到的数据具有可靠性。对Zn/Fe表面进行直线扫描发现,高频模值出现在Zn/Fe界面区。
4.4 应力腐蚀研究
Li等[44]研究了X70管线钢的腐蚀随应力分布的变化,证明了LEIS是一种能够用来图形化描述管线钢应力分布的有前景的技术。
Tang等[13]利用LEIS和SVET定量研究了近中性溶液中应力和H对X70管线钢裂纹尖端局部阳极溶解的协同作用。结果表明,LEIS在光滑试样和预裂纹试样上的测量结果都含有两个半圆,即与界面电荷转移反应有关的低频半圆和与腐蚀产物层在电极表面的沉积有关的高频半圆。
4.5 涂层降解研究
传统的EIS可以描述溶液中有机涂层的降解动力学,但是不能说明涂层失效的位置、原因及方式。而涂层降解通常发生在局部区域。在使用传统的阻隔性能方法作为度量标准,测量涂层长期行为时,缺陷的形成和愈合可能是误差的来源之一。局部电化学探头和绘图可以系统地检测、定位和表征缺陷,并且对控制亚稳态并最终控制有机涂料的功能和寿命的因素进行更详细的分析。它既可以通过使用高频交流电降低介电界面的阻抗,也可以用一系列激励频率全面描绘某点的阻抗谱。
Zou等[45]用LEIS研究了有机涂层的降解。由于是高频扫描,体系阻抗完全取决于涂层电容。因此,电流增加与涂层阻抗降低无关,而与涂层电容的变化有关。用LEIS和EIS分别测量鼓泡区和整个涂层的电容随浸泡时间的变化,结果显示鼓泡区电容变化要比整个涂层的快,说明在鼓泡区水或其他腐蚀介质能比较快地扩散到涂层内,进而改变了涂层电阻率。因此,涂层电容的变化可直接与鼓泡生成相关。在评价涂层/金属界面粘结力的损失上,LEIS可得到比EIS更定量的结果。
Jorcin等[15]用LEIS研究了有机涂层的剥离。研究发现,传统的EIS图不能分析涂层的剥离过程,也不能确定缺陷区域。于是,在缺陷附近进行了LEIS扫描。可以看出,缺陷处由于露出了金属基体,其导纳要比别的地方高。腐蚀20 d后,缺陷边缘处出现了一个台阶。随着腐蚀时间的增加,台阶逐渐增高。在腐蚀50 d后,台阶消失,但是整个图谱的基线升高,说明扫描区域不够大,未显现出台阶。
4.6 带缺陷涂层下的腐蚀研究
基于交流性质的阻抗更适合检测有机涂层基质的局部信息,更容易观察到加工和制造过程中的外在缺陷。LEIS/LEIM也被用于观察内在缺陷,是研究局部电化学活动的有用方法。
Taylor[12]发现,在发展的早期阶段,这些缺陷显示了非直观的导纳下降,可能是由于水在金属/涂层界面的成核,或是一个电阻式的腐蚀产物的形成。LEIS可用于测量起泡的发生及水扩散到有机涂层的速度,还可以给出带缺陷涂层处腐蚀发生的有用信息。
Zhong等[46]发现带缺陷涂层的LEIS响应取决于缺陷的尺寸大小。当缺陷较小时,局部腐蚀过程和机理随时间变化;当缺陷比较大时,腐蚀行为不受扩散影响,与时间无关。传统的EIS方法反映的是涂层和缺陷的平均阻抗,小缺陷处的局部腐蚀过程和机理被忽略,大缺陷处的涂层阻抗也被“平均化”了。因此,LEIS可以检测出涂层破坏时碳钢的局部电化学腐蚀行为。
Dong等[47]研究了阴极保护下涂层缺陷处钢的局部腐蚀情况。LEIS谱包括与电荷转移有关的高频半圆和O2扩散控制腐蚀反应的低频45°角直线。O2的扩散通常由缺陷几何形状和腐蚀产物沉积决定,这是由于细而深的缺陷会阻隔一部分阴极极化,但是腐蚀产物的影响在碱性条件和有效阴极保护下可忽略。因此,在合适的阴极极化电压下,阴极反应主要由O2的扩散控制。即使在非常负的电压下,阻抗谱也包含扩散控制的电荷传递过程。
Snihirova等[48]将含有不同添加剂的改性环氧“智能”涂料应用于AA2024合金,在微尺度下研究了“智能”添加剂对不同尺寸和几何形状的缺陷进行腐蚀抑制的能力。结果表明,添加剂可以有效抑制各种尺寸的缺陷的腐蚀。此外,LEIS测量还给出了每个系统与抑制机制和动力学有关的重要信息。
5 LEIS研究方法的特点、局限和测试与数据解析技术
5.1 技术特点
电化学阻抗方法的基本思路是AC电位扰动电极界面,同时测量其整个电极表面的平均电流响应及阻抗响应。如果表面存在较弱特定局域过程,可能会被平均化而无法获知,或即使获知也无法定位。
与常规EIS测量界面电流响应不同,LEIS方法用两个微探针测量扰动后局部表面上方溶液中的电流响应和阻抗响应。在电极表面电极过程不均匀分布时,可以获得局部区域的阻抗响应LEIS及其在特定频率时的分布状态LEIM。根据这些信息,不仅可以获知局部电化学行为的性质和机制,而且可以获知该局部电化学行为的定位、分布、转移等常规EIS方法无法获取的信息。这对于深入了解表面局部过程不均匀分布及其作用机制具有重要价值。此外,LEIS同样适用于采集高阻抗体系极弱的电化学过程信息,有助于获取高阻抗体系局部失效过程,如涂层渗水、局部腐蚀诱导期等早期过程发展和转移的重要信息。
LEIS方法的另一重要价值体现在检测局部与整体的耦合作用。通常电化学不均匀表面因各局域活性差异会发生电化学耦合作用诱导表面电流。常规EIS方法无法检测到这种过程,而LEIM则可以根据阻抗分布获知表面电流的分布和耦合强度。这对于了解局部过程的形成、发展具有重要价值。
和EIS方法相同,LEIS也是小幅值扰动技术,对表面电化学状态影响小,在接近表面初始状态下测量,也属于准稳态测试技术。
局域AC电流测量和特定频率的选择是能否获取局部界面过程信息的关键。显然,若干预实验先行获取局部过程初步信息,为进一步精确定位测量提供条件是非常重要的。
5.2 EIS和 LEIS信息一致性和差异
EIS获得的是参比电极和整个工作电极之间的平均AC电流和平均AC电位关系;而LEIS是反映了LEIS两探针之间局部AC电流和局部AC电位的关系。两种方法获得信息的差异则来源于这两种不同采样方式。LEIS下探针和上探针分别相当于EIS的工作电极和参比电极。因此,下探针位置和与上探针距离应为影响信息的关键因素。此外,由于不均匀分布电化学表面横向耦合电化学过程的影响也是需要考虑的重要因素。相邻区耦合很难完全避免,可以根据电位分布了解不均匀分布的程度。
(1) LEIS电流组分是根据探针间电位和溶液电导计算获得,微探针电极过程阻抗在远低于溶液电阻时可以忽略。如果溶液电导过高则探针电位差过小,探针电极过程影响增大,电流信号过弱和复杂性增大会导致偏差增大。探针面积影响可因系统偏差抵消。
(2) 工作电极的双层电容,扩散,表面膜,产物积累而二次反应等过程信息能够从EIS信息中获得,由于下探针不会进入工作电极表面区域,这些差异对获取信息的影响需要关注。
(3) 探针与表面距离过远则仅有部分信号流过探针之间,分辨率和灵敏度低。
(4) 不均匀溶液电导影响。
(5) 表面平整度会影响探针与表面距离和阻抗的垂直分辨率。
(6) LEIS信息解析的难度在于电流密度面积归一化计算。
(7) 相邻区域耦合作用相当于测定区存在偏置电流的极化作用。
为了获得可靠的局部电化学信息,这些差异必须在设计实验和数据解析时加以合理考虑。
5.3 LEIS实验技术
为了可靠测量、解析和理解LEIS信息,需要合理安排测试方法和数据解析方法。
在数据测试方面,需要注意的有:与EIS实验共同的问题,测量点局域定位,电极平整度粗糙度影响,平均方法EIS和LEIM及LEIS方法结合,电位/电流分布与LEIS结合,稳态方法和LEIS结合,LEIM测量频率的选择,LEIS数据可靠性认定,组合测试技术,噪声控制等。
(1) 同时运用LEIS-LEIM方法和多种全局和微区电化学技术,获得多视角信息,有助于全面深入认识局部腐蚀电化学过程。
(2) 合理设定分辨率:分辨率越高,探针与表面距离越近,对表面平整度和水平度要求越高;同一扫描面积,分辨率越高,步长越小,测试时间越长,状态变化会影响测试结果分析,根据研究需要选择合适的分辨率。
(3) 必要时采用辅助定位技术:微小检测点定位技术,长焦望远显微技术。
(4) 长周期连续实验设计技术:样品连续测试,样品精密定位。
(5) 环境噪声控制:LEIS为微弱信号测量技术,必须控制环境噪声水平。实验体系接地技术,屏蔽实验箱,实验室接地线和屏蔽网。
(6) 微区电化学信息数据解析:三维图谱解析-剖面二维曲线提取,噪声统计分析技术,面积归一化,微区信息和全局信息融合度和一致性,电位、电流和阻抗信息相关性。
在数据解析方面,需要注意的有:与EIS解析方法共同的问题,阻抗数据面积归一化引起的参数定量解析的难度,双层电容、极化/电荷迁移电阻、异质相邻区域影响的数据分离难度;LEIS谱中局域过程强化,扩散和萎缩过程、膜过程、吸脱附过程等复杂过程的响应特征和响应的等效电路模型的特征化等。
6 总结
LEIS技术最早可以追溯到1938年扫描参比电极,是为了满足不均匀表面局部反应活性研究的需要而建立的,可以测量与周围材料无关的一个小的表面区域。该技术可以证实实验与设想之间的一致性,如LEIS证实了设想的局部Ohm阻抗的存在。
局部电化学阻抗谱 (LEIS) 或局部电化学阻抗分布图 (LEIM),除了提供与测试和界面有关的局部电阻、电容、电感等信息外,还能给出局部电流和电位的线、面分布以及二维、三维彩色阻抗或导纳图像,能精确确定局部区域固/液界面的阻抗行为及相应参数。
LEIS容易操作,可以通过测量溶液中的局部电压差,计算出局部电流。使用一个复合频道频率响应分析仪可以同时测量整体和局部行为。
局部电化学阻抗技术弥补了传统电化学阻抗法的不足,不仅完善和发展了多种测量和数据解析方法,而且在金属腐蚀局部过程研究中获得了持续增加的应用,已经成为一种有广阔发展前景的新技术。
参考文献
[1] Annergren I, Thierry D, Zou F. Localized electrochemical impedance spectroscopy for studying pitting corrosion on stainless steels[J]. J. Electrochem. Soc., 1997, 144(4): 1208
[2] Gabrielli C, Huet F,?Keddam M, et al. A review of the probabilistic aspects of localized corrosion[J]. Corrosion, 1990, 46(4): 266
[3] Wightman R M. Microvoltammetric electrodes[J]. Anal. Chem., 1981, 53(9): 1125A
[4] Sun P, Laforge F O, Mirkin M V. Scanning electrochemical microscopy in the 21st century[J]. Phys. Chem. Chem. Phys., 2007, 9(7): 802
[5] Isaacs H S, Kissel G. Surface preparation and pit propagation in stainless steels[J]. J. Electrochem. Soc., 1972, 119(12): 1628
[6] Bayet E, Huet F, Keddam M, et al. A novel way of measuring local electrochemical impedance using a single vibrating probe[J]. J. Electrochem. Soc., 1997, 144(4): L87
[7] Bayet E, Huet F, Keddam M, et al. Local electrochemical impedance measurement: scanning vibrating electrode technique in AC mode[J]. Electrochim. Acta, 1999, 44(24): 4117
[8] Gabrielli C, Joiret S, Keddam M, et al. Development of a coupled SECM-EQCM technique for the study of pitting corrosion on iron[J]. J. Electrochem. Soc., 2006, 153(3): B68
[9] Davoodi A, Pan J, Leygraf C, et al. Probing of local dissolution of Al-alloys in chloride solutions by AFM and SECM[J]. Appl. Surf. Sci., 2006, 252(15): 5499
[10] Isaacs H S, Kendig M W. Determination of surface inhomogeneities using a scanning probe impedance technique[J]. Corrosion, 1980, 36(6): 269
[11] Schreiber A, Schultze J W, Lohrengel M M, et al. Grain dependent electrochemical investigations on pure iron in acetate buffer pH 6.0[J]. Electrochim. Acta, 2006, 51(13): 2625
[12] Taylor S R. Incentives for using local electrochemical impedance methods in the investigation of organic coatings[J]. Prog. Org. Coat., 2001, 43(1-3): 141
[13] Tang X, Cheng Y F. Quantitative characterization by micro-electrochemical measurements of the synergism of hydrogen, stress and dissolution on near-neutral pH stress corrosion cracking of pipelines[J]. Corros. Sci., 2011, 53(9): 2927
[14] Mouanga M, Puiggali M, Tribollet B, et al. Galvanic corrosion between zinc and carbon steel investigated by local electrochemical impedance spectroscopy[J]. Electrochim. Acta, 2013, 88: 6
[15] Jorcin J, Aragon E, Merlatti C E L, et al. Delaminated areas beneath organic coating: A local electrochemical impedance approach[J]. Corros. Sci., 2006, 48(7): 1779
[16] Zhang N, Sun Z H, Zhang Q, et al. Application of local electrochemical impedance spectroscopy (LEIS) on assessing the environmental failure of organic coatings[J]. Equip. Environ. Eng., 2007, 4(1): 75 (章妮, 孙志华, 张琦等.局部阻抗测试技术在评定有机涂层环境失效中的应用[J]. 装备环境工程, 2007, 4(1): 75)
[17] Lillard R S, Moran P J, Isaacs H S. A novel method for generating quantitative local electrochemical impedance spectroscopy[J]. J. Electrochem. Soc., 1992, 139(4): 1007
[18] Zou F, Thierry D, Isaacs H S. A High-resolution probe for localized electrochemical impedance spectroscopy measurements[J]. J. Electrochem. Soc., 1997, 144(6): 1957
[19] Frateur I, Huang V M, Orazem M E, et al. Experimental issues associated with measurement of local electrochemical impedance[J]. J. Electrochem. Soc., 2007, 154(12): C719
[20] Frateur I, Huang V M, Orazem M E, et al. Local electrochemical impedance spectroscopy: Considerations about the cell geometry[J]. Electrochim. Acta, 2008, 53(25): 7386
[21] Wu S, Orazem M E, Tribollet B, et al. Impedance of a disk electrode with reactions involving an adsorbed intermediate: Local and global analysis[J]. J. Electrochem. Soc., 2009, 156(1): C28
[22] Wu S, Orazem M E, Tribollet B, et al. Impedance of a disk electrode with reactions involving an adsorbed intermediate: experimental and simulation analysis[J]. J. Electrochem. Soc., 2009, 156(7): C214
[23] Ferrari J V, de Melo H I L G, Keddam M, et al. Influence of normal and radial contributions of local current density on local electrochemical impedance spectroscopy[J]. Electrochim. Acta, 2012, 60: 244
[24] Sánchez M, Aouina N, Rose D, et al. Assessment of the electrochemical microcell geometry by local electrochemical impedance spectroscopy of copper corrosion[J]. Electrochim. Acta, 2012, 62: 276
[25] Pilaski M, Hamelmann T, Moehring A, et al. Impedance spectroscopy in micro systems[J]. Electrochim. Acta, 2002, 47(13): 2127
[26] Krawiec H, Vignal V, Oltra R. Use of the electrochemical microcell technique and the SVET for monitoring pitting corrosion at MnS inclusions[J]. Electrochem. Commun., 2004, 6(7): 655
[27] Bayet E, Huet F, Keddam M, et al.Adaptation of the scanning vibrating electrode technique to AC mode: Local electrochemical impedance measurement[J]. Mater. Sci. Forum, 1998, 57: 289
[28] Wittmann M W, Leggat R B, Taylor S R. The detection and mapping of defects in organic coatings using local electrochemical impedance methods[J].?J. Electrochem. Soc., 1999, 146(11): 4071
[29] Huang V M, Vivier V, Orazem M E, et al. The apparent constant-phase-element behavior of a disk electrode with faradaic reactions a global and local impedance analysis[J]. J. Electrochem. Soc., 2007, 154(2): C99
[30] Huang V M, Vivier V, Orazem M E, et al. The apparent constant-phase-element behavior of an ideally polarized blocking electrode a global and local impedance analysis[J]. J. Electrochem. Soc., 2007, 154(2): C81
[31] Huang V M, Vivier V, Frateur I, et al. The global and local impedance response of a blocking disk electrode with local constant-phase-element behavior[J]. J. Electrochem. Soc., 2007, 154(2): C89
[32] Schneider I A, Kuhn H, Wokaun A, et al. Study of water balance in a polymer electrolyte fuel cell by locally resolved impedance spectroscopy[J]. J. Electrochem. Soc., 2005, 152(12): A2383
[33] Schneider I A, Kramer D, Wokaun A, et al. Spatially resolved characterization of PEFCs using simultaneously neutron radiography and locally resolved impedance spectroscopy[J]. Electrochem. Commun., 2005, 7(12): 1393
[34] Bandarenka A S, Eckhard K, Maljusch A, et al. Localized electrochemical impedance spectroscopy: visualization of spatial distributions of the key parameters describing solid/liquid interfaces[J]. Anal. Chem., 2013, 85(4): 2443
[35] Montoya R, García-Galván F R, Jiménez-Morales A, et al. Effect of conductivity and frequency on detection of heterogeneities in solid/liquid interfaces using local electrochemical impedance: Theoretical and experimental study[J]. Electrochem. Commun., 2012, 15(1): 5
[36] Xiao K, Zhang X, Dong C, et al. Localized electrochemical impedance spectroscopy study on the corrosion behavior of Fe-Cr alloy in the solution with Cl- and SO42-[J]. J. Wuhan Univ. Technol. Mater., 2012, 27(1): 27
[37] Jorcin J, Orazem M E, Pébère N, et al. CPE analysis by local electrochemical impedance spectroscopy[J]. Electrochim. Acta, 2006, 51(8): 1473
[38] Galicia G, Pébère N, Tribollet B, et al. Local and global electrochemical impedances applied to the corrosion behaviour of an AZ91 magnesium alloy[J]. Corros. Sci., 2009, 51(8): 1789
[39] Jin T Y, Cheng Y F. In-situ characterization by localized electrochemical impedance spectroscopy of the electrochemical activity of microscopic inclusions in an X100 steel[J]. Corros. Sci., 2011, 53(2): 850
[40] Meng G Z, Zhang C, Cheng Y F. Effects of corrosion product deposit on the subsequent cathodic and anodic reactions of X-70 steel in near-neutral pH solution[J]. Corros. Sci., 2008, 50(11): 3116
[41] Zhang G A, Cheng Y F. Localized corrosion of carbon steel in a CO2-saturated oilfield formation water[J]. Electrochim. Acta, 2011 56(3): 1676
[42] Annergren I, Zou F, Thierry D. Application of localised electrochemical techniques to study kinetics of initiation and propagation during pit growth[J]. Electrochim. Acta, 1999, 44(24): 4383
[43] de Lima-Neto P, Farias J P, Herculano L F G, et al. Determination of the sensitized zone extension in welded AISI 304 stainless steel using non-destructive electrochemical techniques[J]. Corros. Sci., 2008, 50(4): 1149
[44] Li M C, Cheng Y F. Corrosion of the stressed pipe steel in carbonate-bicarbonate solution studied by scanning localized electroche-mical impedance spectroscopy[J]. Electrochim. Acta, 2008, 53(6): 2831
[45] Zou F, Thierry D. Localized electrochemical impedance spectroscopy for studying the degradation of organic coatings[J]. Electrochim. Acta, 1997, 42(20-22): 3293
[46] Zhong C, Tang X, Cheng Y F. Corrosion of steel under the defected coating studied by localized electrochemical impedance spectroscopy[J]. Electrochim. Acta, 2008, 53(14): 4740
[47] Dong C F, Fu A Q, Li X G, et al. Localized EIS characterization of corrosion of steel at coating defect under cathodic protection[J]. Electrochim. Acta, 2008, 54(2): 628
[48] Snihirova D, Liphardt L, Grundmeier G, et al. Electrochemical study of the corrosion inhibition ability of “smart” coatings applied on AA2024[J]. J. Solid State Electrochem., 2013, 17: 2183
免责声明:本网站所转载的文字、图片与视频资料版权归原创作者所有,如果涉及侵权,请第一时间联系本网删除。
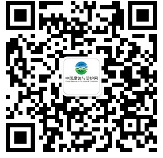
官方微信
《中国腐蚀与防护网电子期刊》征订启事
- 投稿联系:编辑部
- 电话:010-62316606-806
- 邮箱:fsfhzy666@163.com
- 中国腐蚀与防护网官方QQ群:140808414