摘要
通过静态腐蚀及SEM/EDS、EPMA等分析表征技术,研究了304和316H不锈钢在700 ℃ LiF-NaF-KF (FLiNaK) 熔盐中的腐蚀行为。结果表明,这两种不锈钢在FLiNaK熔盐中的主要腐蚀形式是表面和近表面晶界处Cr的选择性流失。316H不锈钢由于含有Mo,腐蚀深度及失重均低于304不锈钢。腐蚀后,两种不锈钢的表面均出现了富集Ni和Fe的腐蚀层,而近表面区域均出现了大量的纳米级析出相。EDS分析结果显示,这些析出相是Cr和Al的氮化物或碳氮化物,析出相显著提高了材料的硬度。
关键词: 304不锈钢 ; 316H不锈钢 ; 氟化物熔盐 ; 晶间腐蚀 ; 纳米级析出相
熔盐堆 (MSR) 是“第四代核能国际论坛”中提出的6种先进反应堆型之一,具有固有安全性、经济性、可持续性、防核扩散性和高效率利用核燃料等优点[1,2,3]。MSR选用碱金属或碱土金属的氟化物作为核燃料载体和冷却剂,其中三元共晶熔盐LiF-NaF-KF (46.5%-11.5%-42%,摩尔分数,FLiNaK) 是候选熔盐之一,具有高比热、高热传导、高沸点、低饱和蒸气压等优点[4]。
金属材料在熔盐中的腐蚀行为是决定材料使用寿命及安全性的关键因素。已有研究[5,6,7]表明,镍基合金具有很好的耐氟化物冷却剂腐蚀性能,其中Hastelloy-N合金更是迄今为止唯一被实际用于建造熔盐实验堆的合金材料。然而该合金价格昂贵,且并未被收录进ASME核用材料标准中,无法直接用来建造商业熔盐堆。304及316奥氏体不锈钢具有良好的高温力学性能及经济性,同时具备ASME高温堆核用材料资质,因此是熔盐堆的重要备选材料[8]。然而相对于镍基合金,不锈钢的耐氟化物熔盐腐蚀性较弱,且相关研究也较少。
Sellers等[9]研究了316L不锈钢和Hastelloy-N与石墨在850 ℃的FLiNaK盐中的腐蚀行为,结果表明石墨加速了Cr的腐蚀。Zheng[10]比较了316L和Hastelloy-N在700 ℃下FLiBe熔盐中的腐蚀行为,表明在没有石墨的情况下其年腐蚀率分别为12.0和17.2 μm/a。丁祥彬等[11]的研究表明,Hastelloy-N与316L不锈钢在FLiNaK熔盐中,前者表现出明显的均匀腐蚀,后者发生了晶间腐蚀;1000 h后Hastelloy-N合金未见明显的腐蚀,而316L不锈钢的腐蚀深度达到了40 μm。美国橡树岭国家实验室 (ORNL) 的研究人员将304L不锈钢在LiF-BeF2-ZrF4-ThF4-UF4 (70%-23%-5%-1%-1%,摩尔分数) 动态熔盐中腐蚀5 a,由于熔盐中含燃料,发现腐蚀非常严重,腐蚀孔洞深度达到250 μm[12]。上述研究大多是针对316L不锈钢和Hastelloy-N合金的,对于304不锈钢的研究相对缺乏,尤其缺少304与316在冷却剂熔盐 (FLiBe或FLiNaK) 中的腐蚀性能对比研究。Kondo等[13]对比了304L和316L在600 ℃下FLiBe熔盐中的腐蚀行为,由于测试体系选择不佳,测试时间也很短,无法得出明确的结论。ORNL研究人员的测试结果[14]表明,FLiNaK具有路易斯碱的特性,比FLiBe的腐蚀性略强。因此,本研究比较304及316H两种不锈钢在FLiNaK中的腐蚀行为,以得出两种不锈钢明确的腐蚀抗力差异性。
1 实验方法
实验使用的材料为304及316H不锈钢热轧板材,成分如表1中所示。采用线切割从原始不锈钢板材上切取尺寸为15 mm×10 mm×2 mm的片状腐蚀试样,并采用激光打标仪标记每一块试样。腐蚀实验前,先采用水磨砂纸将片状试样逐级打磨至1500#,以去除试样表面可能存在的氧化物杂质。然后,将试样依次放入去离子水和无水乙醇中进行超声清洗,并采用电吹风冷风吹干试样表面。最后,采用游标卡尺及精密天平对试样的实际尺寸及重量进行测量。实验使用的FLiNaK盐事先经过H2-HF纯化处理,以除去原料中的杂质。纯化后盐的主要杂质成分 (mg/kg) 如下:Fe 8.04,Cr 0.94,Ni 218.3,Mo 0.13,Cl- 16.4,NO- 31.4,PO43- 12.1,SO42- 16.4,O 276。其中,金属元素由电感耦合等离子体发射光谱法 (ICP-OES) 测得,阴离子由离子色谱仪测得,氧含量由氧分析仪 (leco ro600测得)。盐从纯化后至实验前始终存放在水、氧含量均低于10 mg/L的充Ar的手套箱中,避免污染。
表1 304和316H不锈钢的化学成分
腐蚀实验采用静态浸泡的方法,浸泡用容器如图1所示。该容器由双层坩埚构成:内层为石墨坩埚,用于盛装样品及熔盐;外层为不锈钢坩埚,用于密封,隔绝外界气氛。实验前,先用无水乙醇清洗石墨坩埚及石墨坩埚盖,然后转移到700 ℃的真空炉中烘干24 h,以尽可能去除石墨中吸附的水分和氧气。待真空炉冷却至室温,迅速将石墨坩埚转移到手套箱中备用。不锈钢坩埚则先使用去污粉和自来水去除表面的油污,再使用去离子水和无水乙醇清洗,然后转移到120 ℃的真空干燥箱中干燥2 h,冷却后转移至手套箱中备用。
图1 不锈钢静态腐蚀浸泡实验容器示意图
在手套箱中将304及316H不锈钢片状腐蚀试样分别置于两个容器内,每个容器中放3个平行对比样。为了避免因试样与石墨连接而产生的电偶腐蚀[15,16,17],在石墨坩埚顶部放置绝缘陶瓷杆,试样通过316不锈钢丝悬挂在绝缘陶瓷杆上,保持试样与石墨之间的绝缘性。向每个悬挂好试样的石墨坩埚中装约220 g的FLiNaK盐后,将石墨坩埚盖上放入外层不锈钢坩埚内,并在手套箱中对外层坩埚进行焊接密封,以避免实验过程中被外界气氛污染。最后,将焊接好的腐蚀容器从手套箱中取出并放入高温炉中,进行700 ℃恒温保持400 h的腐蚀实验。
腐蚀实验结束后,分别采用1 mol/L的Al(NO3)3水溶液和去离子水超声清洗,以去除样品表面残留的盐。采用精密天平 (感量0.01 mg) 进行腐蚀后的重量测试,以计算单位面积的腐蚀失重。采用Merlin Compact场发射扫描电子显微镜/X射线能谱仪 (FE-SEM/EDS) 和EPMA-1720电子探针显微分析仪 (EPMA) 研究腐蚀后试样的形貌、微观结构和元素分布。采用Spectro arcos型ICP-OES分析腐蚀后FLiNaK盐中的主要合金元素含量。
2 实验结果
2.1 腐蚀后材料失重及熔盐成分分析
在700 ℃下FLiNaK熔盐中腐蚀400 h后,304和316H两种不锈钢单位面积腐蚀失重分别为 (4.97±0.18) 和 (2.5±0.1) mg/cm2。可见,304不锈钢的单位面积失重比含Mo的316H不锈钢的大约1倍,意味着304不锈钢遭受了更加严重的腐蚀。
腐蚀后熔盐中的主要合金元素浓度如表2所示。对比腐蚀前后熔盐中主要合金元素的浓度可见,腐蚀后合金中的主要元素在熔盐中的含量均有上升,表明在熔盐腐蚀的作用下,这些元素发生了由合金中向盐中的迁移。304不锈钢腐蚀后的盐中的合金元素总量比316H不锈钢腐蚀后盐中的多,表明304不锈钢的腐蚀更加严重。其中,Fe增加的最多,304不锈钢腐蚀后的盐中Fe增加了约1200 mg/L,而316H不锈钢腐蚀后的盐中Fe增加了约480 mg/L。304不锈钢腐蚀后的盐中Cr增加了约240 mg/L,316H不锈钢腐蚀后的盐中只增加了约160 mg/L。Ni增加较少,304和316H不锈钢腐蚀后熔盐中Ni增加分别为177和72 mg/L。Mo增加最少,304不锈钢中不含Mo,因此304不锈钢试样腐蚀后的盐中Mo的增加来自于悬挂试样用的316不锈钢丝。
表2 腐蚀实验后FLiNaK盐中主要合金元素含量的ICP-OES分析结果
2.2 腐蚀后不锈钢的表面形貌
图2为两种不锈钢在700 ℃下FLiNaK熔盐中腐蚀400 h后的表面SEM像。可以看出,304不锈钢表面存在大量腐蚀孔洞,且在某些区域还存在由于腐蚀孔洞相互连接而造成的表面剥落现象。316H不锈钢的表面也存在腐蚀孔洞,但是孔洞密度更低,且没有出现明显表面剥落。
图2 经700 ℃的FLiNaK熔盐腐蚀400 h后304和316H不锈钢的表面SEM形貌
2.3 腐蚀后不锈钢截面的元素及微观组织分析
图3为304和316H不锈钢腐蚀后截面Cr,Fe和Ni的EPMA面扫描分析结果。可以看出,这两种不锈钢腐蚀孔洞主要分布在表面及近表面的晶界上,304不锈钢的腐蚀孔洞数量比316H不锈钢的多,且腐蚀孔洞向合金内部的分布深度也更深。并且这两种合金腐蚀后,在表面及近表面晶界处都出现了明显的Cr贫化现象,而且在Cr贫化区域出现了Ni和Fe的富集。其中,304不锈钢贫Cr较严重,沿晶界贫Cr的深度约为90 μm;316H不锈钢也出现了沿晶界贫Cr现象,但是贫Cr深度较小,约为40 μm。很显然,这些近表面的元素分布变化是由熔盐腐蚀造成的,304不锈钢的贫Cr深度远大于316H不锈钢的,说明304不锈钢的腐蚀更加严重,这与失重和熔盐分析的结果一致。
图3 304和316H不锈钢在FLiNaK熔盐中腐蚀400 h后截面的Cr,Fe和Ni的EPMA面扫描分析结果
图4为腐蚀后304和316H不锈钢截面的背散射电子图像与内部未受腐蚀影响区的EDS线扫结果。可以看出,304和316H不锈钢在700 ℃的FLiNaK熔盐中腐蚀400 h后,表面都存在一层灰白色的区域,且这些区域沿着合金晶界向内部延伸。在靠近灰白色区域的合金晶粒内部,还存在大量的黑色析出相。这些析出相从靠近合金表面灰白色区域处一直向合金内部分布;随着深度的变化,析出相的分布也越来越少,直至距合金表面约350 μm的位置处 (如图4所示),才无法观察到黑色析出相。从图4中高倍数背散射电子图像可以看出,304和316H不锈钢的腐蚀影响区域的微观组织相似,均由灰白色腐蚀层与黑色析出相组成。而两种材料在内部未受腐蚀影响的区域,虽然晶粒内部均不存在明显的黑色析出相,但晶界上的析出相形态略有差别,304不锈钢内部晶界上的析出相数目低于316H不锈钢的,但尺寸更大。
图4 304和316H不锈钢腐蚀后截面的背散射像以及内部未受腐蚀影响区EDS线扫结果 (对应高倍像中的黑线)
为进一步研究可能的相组成,利用EDS对表面灰白色腐蚀层、近表面黑色析出相区域、合金未受腐蚀影响区域的晶粒内部以及晶界处的成分进行了分析,结果汇总于表3及图4。从表3可以看出,两种材料的成分变化相似,表面灰白色腐蚀层相对于内部未受腐蚀影响区域,均是明显富集Fe和Ni,而流失Cr。其中,腐蚀层中的Fe和Ni相对于未受腐蚀影响区绝对值增加约13%及4%;而Cr流失较为严重,由未受腐蚀影响区的约17%流失至约2%。316H和304两种不锈钢灰白色腐蚀层与内部未受腐蚀影响区中的N含量几乎为0;而在黑色析出相区域N的富集明显,N含量分别约为3%及5%。Al在黑色析出相区也有少量的富集,而Cr的含量几乎与未受腐蚀影响区的含量一致,说明黑色析出相有可能是Cr和Al的氮化物。从图4的未受腐蚀区晶界处的线扫分析中可看出,两种合金的晶界析出相中均富集Cr和C,含Mo的316H不锈钢的晶界上还有明显的Mo富集,表明晶界析出相应该是这些合金元素的碳化物。
2.4 腐蚀后合金内部的硬度变化
为确认腐蚀引起的近表面黑色析出相是否会对合金的力学性能产生影响,采用显微维氏硬度计,对腐蚀后两种合金截面试样的近表面黑色析出相区域和内部未受腐蚀影响区域进行了硬度测量,结果如下:304不锈钢析出相区与未受腐蚀影响区的维氏硬度分别为 (541.33±8.08) 和 (228.67±3.51),316H不锈钢析出相区与未受腐蚀影响区的维氏硬度分别为 (536.67±8.08) 和 (206±1.73)。可以看出,两种合金近表面黑色析出相区域的硬度均明显大于内部未受腐蚀影响区域的,表明析出相对合金有明显的硬化作用。
3 分析与讨论
早期研究[18]认为,在氟化物熔盐体系中,保护性钝态氧化膜无法稳定存在,因而合金的腐蚀由其主要元素氟化物相对于熔盐组分或杂质的热力学稳定性决定。不锈钢中主要元素的氟化物CrF3,FeF2,FeF3,NiF2和MoF3在700 ℃的标准形成Gibbs自由能分别约为-880,-820,-790,-780和-700 kJ/mol (等效1 mol F2情况下)[11],因此这几种元素在氟化物熔盐中易被腐蚀的程度依次为Cr>Fe>Ni>Mo,合金中的Cr在FLiNaK熔盐中最易发生选择性溶解腐蚀。因为FLiNaK盐本身组分的热力学稳定性远高于合金元素的氟化物,所以该熔盐对合金的腐蚀主要是由其中的杂质引起的[18]。当熔盐中存在Fe、Ni等比Cr惰性的杂质金属离子时,将通过反应式 (1)~(3) 腐蚀合金中的Cr。此外,存在杂质离子Ni2+,还会通过反应式 (4) 和 (5) 腐蚀合金中的Fe,这些因腐蚀而溶解进熔盐的Fe2+或Fe3+又会对合金中的Cr造成二次腐蚀,因此熔盐中的Ni2+将对不锈钢造成严重的腐蚀。
如表2所示,本次实验使用的FLiNaK盐中的初始Ni含量较高,因此对两种不锈钢中的Cr及Fe都产生了腐蚀。伴随着腐蚀的进行,Cr的选择性溶解腐蚀导致合金中贫Cr区的形成,而在贫Cr区Ni和Fe相对富集。与此同时,合金在熔盐中的腐蚀反应生成的Ni和Fe原子将部分沉积在样品表面,并向合金内部扩散。因此,在这两者的相互作用下形成如图4所示的灰白色腐蚀层。从表3可以看出,相对于未受腐蚀影响的基体,腐蚀层中的Fe和Ni含量均有增加,而Cr浓度大大降低,验证了式 (1)~(5) 反应的发生。除了惰性金属离子外,盐中含有的水杂质则会通过反应式 (6) 产生HF,从而通过反应式 (7) 对合金造成腐蚀[19]。腐蚀反应生成的氟化物在FLiNaK中均为可溶的,置换反应 (1)~(5) 产生的金属原子无法全部沉积、结合在不锈钢表面,且反应 (7) 产生的是H2,因此随着腐蚀反应的进行,合金表面会因为元素的大量流失而产生腐蚀孔洞。相较304不锈钢,316H不锈钢的Ni含量更高,且含有Mo,这两种元素抗氟化物腐蚀能力较强,因此316H不锈钢表面的腐蚀孔洞数目少于304不锈钢的。随着腐蚀孔洞密度增大,有些孔洞会连接起来,从而造成合金表面腐蚀层的局部剥落。从实验后的熔盐分析结果 (表2) 可以看出,腐蚀后熔盐中Cr、Fe、Ni含量均有增加。在实验针对的两种铁基合金中,Fe占据着较大比重,所以Fe的溶解占据合金腐蚀失重的主要部分。而腐蚀后盐中Ni含量增多,可能是石墨坩埚中残留有一部分未除尽的残留水 (尽管严谨按照要求进行了坩埚除水处理,但是仍然会存在一些未除去的残留水),在水和Ni等金属杂质离子加速合金腐蚀的作用下,尽管在腐蚀过程中有部分Fe和Ni沉积到合金表面,但是Fe和Ni溶解的量远大于沉积到合金表面的量。因此,腐蚀后熔盐中Fe和Ni含量均增加,其中Cr的增加主要是通过腐蚀反应本身造成;而Fe和Ni的增加除了源自腐蚀反应本身外,还有部分可能来自于表面腐蚀层的剥落,在自身腐蚀与腐蚀层剥落的共同作用下导致腐蚀后盐中Fe和Ni含量显著增加。
表3 304和316H不锈钢腐蚀后内部各区域EDS元素分析 (括号内的数字对应图4中的相应区域)
当合金表面的Cr通过腐蚀反应溶解进熔盐中后,内部的Cr会向表面扩散,使腐蚀持续进行,同时造成合金近表面区域Cr的贫化。从图3可以看出,304和316H不锈钢近表面区域的Cr贫化都集中在晶界上,表明这两种不锈钢都发生了明显的晶间腐蚀。由于本实验的实验温度处于奥氏体不锈钢的敏化温度区间,两种材料在实验后均出现了敏化现象,晶界上析出了大量碳化物,如图4所示。敏化生成的富Cr晶界碳化物将导致晶界周围形成贫Cr区,从而使晶粒-晶界形成钝化-活化微电偶结构,这样的“贫Cr理论”是关于水溶液环境中奥氏体不锈钢晶间腐蚀最广为接受的机理[20]。然而在贫氧的高温氟化物熔盐环境并不存在Cr2O3钝化膜,且高Cr区域反而容易受到腐蚀,因此传统的“贫Cr理论”并不适用。考虑到氟盐中的合金腐蚀过程受到Cr的扩散控制[18],而在700 ℃下Cr在不锈钢中晶界处的扩散速率远高于在晶粒内部的[21],晶间腐蚀可能是由于晶界促进了Cr的快速扩散而导致。除了Cr本身的沿晶扩散之外,关于敏化产生的晶界碳化物对不锈钢在熔融氟盐中晶间腐蚀的影响,目前并不明确。Olson等[22]比较了几种高温合金在850 ℃的FLiNaK熔盐中的腐蚀行为,认为对于Cr含量在20%~23% (质量分数) 的合金,其腐蚀程度与合金的C含量成正比,因此推断晶界富Cr碳化物会促进合金在熔融氟盐中的晶间腐蚀。Zheng[10]对比研究了不含C的模型合金与316不锈钢在700 ℃的FLiBe熔盐中的腐蚀行为,认为模型合金的腐蚀深度远高于316不锈钢的,因此推测316不锈钢晶界上的富Cr碳化物能减慢Cr沿晶界向外扩散的速率。本研究的两种不锈钢虽然Cr含量及C含量非常接近,但304不锈钢的沿晶腐蚀深度却是316H不锈钢的2倍以上,这是由两种材料晶界碳化物的差异所造成。304和316H不锈钢的晶界碳化物均为M23C6型,但对于304来说,M主要是Fe和Cr,而316H不锈钢中M还包括Mo[23]。本实验中未受腐蚀影响区域晶界的EDS线扫结果 (图4) 也支持了该结果。由于这些碳化物具有远高于基体的Cr含量,其本身可能容易受到熔盐腐蚀。由于Mo本身不易被熔盐腐蚀,Mo在晶界碳化物中的富集可能增加了这些碳化物抵抗熔盐腐蚀的能力,从而减轻了316H不锈钢的晶间腐蚀程度。
除了表面的腐蚀层及近表面的晶间贫Cr之外,熔盐腐蚀还导致两种不锈钢在近表面区域形成了大量的纳米级析出相,如图4所示。类似的析出相在Zheng等[24]关于316不锈钢在FLiBe熔盐中腐蚀的文章也有报道,认为这些近表面析出相是由于石墨坩埚中的C向合金中扩散所形成的Cr7C3和Al4C3。而从本实验中析出相区域的EDS分析结果可以看出,两种合金的析出相区域相对于合金基体均有明显的N含量升高和Fe含量减少的现象,而Cr和Ni含量变化不大。此外,316H不锈钢的析出相区中的Al含量明显增加,Mo含量略微增加,而304不锈钢析出相区域的Al含量也微弱增加。析出相区显著的N富集表明除了碳化物外,这些析出相可能还包含氮化物或碳氮化物。由于不锈钢中的Al和Cr为强的氮化物形成元素,而Cr和Mo为强的碳化物形成元素,因此从外界扩散进入合金的N和C容易和这些合金元素结合在近表面区域形成析出相。本实验中C的来源可能是实验采用的石墨坩埚,而N的来源可能是FLiNaK盐中初始含有的NO3-或坩埚在手套箱中的密封过程中引入的N2 (因为手套箱有一定的漏率,而它的循环净化装置仅能除去漏入空气中的H2O和O2,所以不可避免的会含有一定的N2)。除了腐蚀环境中元素的内扩散外,合金中Cr沿晶界的快速扩散溶解也能使合金晶界的成分、微观结构等发生改变,从而可能导致沿合金局部区域形成内碳化物、氮化物等。因此,合金腐蚀后在近表面形成的析出相可能受到外部元素内扩散及合金自身元素流失的共同作用。和材料的腐蚀深度相比 (304不锈钢的约90 μm,316H不锈钢的约40 μm),在腐蚀过程中形成的析出相在两种不锈钢中的分布深度 (约350 μm) 要更深。而从硬度分析的结果可以看出,这些析出相明显提高了两种材料的硬度,进而可能影响材料在服役过程中的性能。因此,在实际使用氟化物熔盐的相关工程设计过程中,除了要评估熔盐对不锈钢的直接腐蚀外,还必须考虑熔盐浸泡引起的材料微观组织结构的变化,后者在特定条件下可能对材料服役性能的影响更大。受限于SEM的空间及元素分辨率 (无法准确测定轻元素C的含量),本研究并没能够确定这些析出相的具体成分及结构,将在今后通过TEM进行更深入的分析。
4 结论
(1) 304和316H不锈钢在700 ℃下FLiNaK熔盐中的腐蚀形式主要表现为表面和近表面晶界处Cr的选择性流失,以及因局部元素流失而产生了腐蚀孔洞。
(2) 316H不锈钢的腐蚀深度及腐蚀失重均明显低于304不锈钢的,表明其具有更好的耐FLiNaK熔盐腐蚀性能。原因是316H不锈钢含有少量的Mo,从而提高了不锈钢基体及晶界碳化物的抗FLiNaK熔盐腐蚀性能。
(3) 304和316H不锈钢在腐蚀后均出现了富集Ni和Fe的表面腐蚀层,可能是合金中Cr的择优溶解形成贫Cr区,从而在贫Cr区出现了Ni和Fe的相对富集,以及熔盐中的Ni和Fe杂质离子在材料表面与钢中的Cr和Fe发生置换反应导致Ni和Fe在材料表面的沉积并向内部扩散。
(4) 两种不锈钢腐蚀后在近表面区域均出现了大量可能是Cr和Al的氮化物或碳氮化物的纳米级析出相,这些析出相显著提高了不锈钢的硬度。
免责声明:本网站所转载的文字、图片与视频资料版权归原创作者所有,如果涉及侵权,请第一时间联系本网删除。
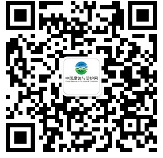
官方微信
《中国腐蚀与防护网电子期刊》征订启事
- 投稿联系:编辑部
- 电话:010-62316606-806
- 邮箱:fsfhzy666@163.com
- 中国腐蚀与防护网官方QQ群:140808414