摘要
通过开路电位、动电位极化、电化学阻抗谱、X射线光电子能谱 (XPS)、扫描电镜 (SEM) 等分析手段研究了酸性含氯溶液pH的变化对汽轮机末级叶片用钢14Cr12Ni3WMoV电化学腐蚀行为的影响。结果表明:随着酸性含氯溶液pH的减小,材料表面阻抗减小,腐蚀速率和点蚀敏感性均增大;点蚀发生时,pH的减小会导致蚀坑沿纵向的发展减缓,而在无明显均匀腐蚀时其沿径向的发展加快;当溶液pH5时,不锈钢钝化膜主要由Fe和Cr相应的氧化物和氢氧化物组成,pH2时,钝化膜主要由Cr的氢氧化物、氧化物和高价态Mo6+的相应化合物组成,含氯溶液pH的减小,会显著加速不锈钢钝化膜中Fe的溶解,从而钝化膜的稳定性降低,材料的耐蚀性下降。
关键词: 电化学腐蚀 ; 不锈钢 ; 汽轮机叶片 ; pH ; 钝化膜 ; 点蚀
汽轮机作为发电原动机,在现代火力发电厂中起着重要作用。汽轮机的末级叶片是其重要的组成部分,在实际运行过程中末级叶片较其它叶片来说更容易出现腐蚀失效,严重时甚至出现断裂,导致整个机组无法正常运行,造成严重的经济损失[1]。
为了保证汽轮机高效安全运行,降低末级叶片的腐蚀,汽轮机给水中的杂质浓度被严格控制,但在实际运行过程中还是会存在一定量的酸性物质和盐类物质。在超临界条件下,蒸汽会将这些杂质带入到汽轮机中,随着高温高压蒸汽逐级膨胀做功,蒸汽会在低压缸的威尔逊线区形成初凝水,初凝水对叶片造成很强的冲刷作用,同时由于盐类物质和酸性物质在蒸汽中的分配系数相对于液相来说更低,其会更倾向溶解于初凝水中,使初凝水具有酸性盐溶液的特性,结合冲刷作用造成末级叶片更容易出现腐蚀损伤[1-5]。目前,针对末级叶片的腐蚀研究主要是通过对已出现腐蚀或者断裂的叶片进行失效分析来推测腐蚀影响因素和腐蚀过程等[5-10]。Adnyana[6]通过研究前缘表面出现损伤且存在裂纹的叶片,发现叶片的失效主要是由于空泡腐蚀和疲劳造成,且在叶片表面发现了加速腐蚀坑形成的微量元素Cl、K、Na、Si等。张涛等[10]利用化学成分分析、显微组织分析和断口分析等方法对断裂叶片进行分析,发现叶片断裂是由于叶片表面形成了腐蚀坑,然后在循环载荷和腐蚀介质长期作用下,腐蚀坑处出现应力集中,随即发展成腐蚀裂纹,随着腐蚀裂纹的延伸而造成叶片断裂。然而,汽轮机末级叶片常用材料在酸性溶液条件下pH等的变化对其电化学腐蚀的影响规律及其机理的研究鲜有报道,即氯离子、pH、温度、冲刷等腐蚀因素影响的基础研究未被系统开展。
14Cr12Ni3WMoV马氏体不锈钢因其优异的耐蚀性、耐磨性和疲劳性能,被广泛用于汽轮机末级叶片。本文采用开路电位、动电位极化、电化学阻抗谱等电化学测试方法,同时结合CLSM和SEM对腐蚀形貌进行观察,并用XPS对不锈钢钝化膜成分进行分析,研究了酸性条件下溶液pH的变化对14Cr12Ni3WMoV电化学腐蚀的影响规律及其机理,以期明确具有酸性盐溶液特性的初凝水如何对末级叶片材料造成腐蚀。
1 实验方法
实验材料为14Cr12Ni3WMoV不锈钢,其化学成分 (质量分数,%) 为:C 0.12,Cr 11.43,Ni 2.41,W 1.003,Mo 1.06,V 0.20,Mn 0.74,Si 0.12,P 0.019,Fe余量。将材料加工成10 mm×10 mm×10 mm的小方块并对其表面的油污进行清洗、吹干,随后采用环氧树脂对其进行密封,露出1 cm2的工作面和导电面,并使用全自动抛磨机对工作面逐级打磨至光亮,随后用去离子水将工作面冲洗干净,无水乙醇脱除残留水分、冷风吹干放入干燥皿中待用。
电化学测试在PARSTAT 4000型电化学工作站上进行,采用三电极体系,其中14Cr12Ni3WMoV不锈钢为工作电极,饱和甘汞电极 (SCE) 为参比电极,20 mm×20 mm的大面积铂网为辅助电极。测试前,工作电极在pH2、pH3、pH4和pH5的0.1 mol/L NaCl溶液中浸泡72 h,并同时通入高纯氩气除氧。溶液pH通过盐酸和氢氧化钠溶液进行调节。实验时工作电极先在开路电位 (OCP) 下稳定900 s,随后进行相应的电化学测试,其中动电位极化初始电位为-0.4 V (vs OCP),以1 mV/s的速率进行正向扫描,当电流密度达到1 mA/cm2后自动反扫;电化学阻抗谱 (EIS) 测试在开路电位下进行,测试频率为105~10-2 Hz,交流幅值为10 mV,用ZSimpWin软件对阻抗数据进行分析。采用JSM-6490LV扫描电镜 (SEM) 观察极化后的工作电极表面,然后使用OLYMPUS OLS5000激光共聚焦显微镜对表面腐蚀坑进行三维形貌观察。
将试样放入pH2和pH5的0.1 mol/L NaCl除氧溶液中浸泡72 h,然后取出洗净吹干,采用单色Al Kα (hυ=1486.6 eV) 为光源的X射线光电子能谱仪 (XPS,AXIS-UltraDLD) 对试样表面生成的钝化膜进行元素分析,用C 1s (248.6 eV) 为校准峰进行荷电校正。分别对Fe 2p、Cr 2p、W 4f和Mo 3d进行测试。采用XPS Peak4.1软件对数据进行处理。
2 结果与讨论
2.1 开路电位分析
14Cr12Ni3WMoV不锈钢在不同pH的0.1 mol/L NaCl溶液中的开路电位测试曲线如图1所示。由图可知,开路电位都在900 s左右趋于稳定,且随着pH不断减小,稳定后的开路电位从-0.110 V (vs SCE) (pH5) 负移到了-0.376 V (vs SCE) (pH2)。开路电位越负,材料的腐蚀倾向越大[11,12]。说明14Cr12Ni3WMoV不锈钢随着溶液pH的减小,其腐蚀倾向会增大,这是因为pH越小,溶液中的H+浓度越大,造成材料表面活性增强,腐蚀倾向增加。
图1 14Cr12Ni3WMoV不锈钢在不同pH下0.1 mol/L NaCl溶液中的开路电位
2.2 循环极化曲线
14Cr12Ni3WMoV不锈钢在不同pH的0.1 mol/L NaCl溶液中的循环极化曲线如图2a所示。从图中可以看出阳极极化过程都出现了钝化特征,以阳极极化曲线上电流密度迅速增至100 μA/cm2时对应的电位值为点蚀电位[13]。表1为循环极化曲线对应的电化学参数。由表可知,不同pH下的自腐蚀电位低于稳定后的开路电位 (见图1),这是由于动电位极化过程中先对试样进行阴极极化造成;进一步分析可以发现随着含氯溶液pH的减小,试样腐蚀电流密度从0.25 μA/cm2 (pH5) 增大到3.42 μA/cm2 (pH2),同时点蚀电位发生负移 (见图2b),说明材料腐蚀速率增大,点蚀敏感性增加,钝化膜易被破坏,材料耐蚀性下降。随着含氯溶液pH的减小,14Cr12Ni3WMoV不锈钢表现出此规律的腐蚀特性,分析其原因是当含氯溶液pH减小时,溶液中的H+浓度增大,H+会加速材料表面钝化膜中起到保护性作用的氧化物和氢氧化物 (如FeOOH、Fe2O3、Cr2O3、Cr(OH)3等) 的溶解,尤其是在酸性条件下稳定性较差的Fe的氧化物和氢氧化物[14],从而钝化膜厚度减小,稳定性降低;与此同时,溶液中电负性大且原子半径小的Cl-会选择性吸附在钝化膜上,改变吸附处钝化膜的成分,使其生成易溶性的氯化物,加剧了钝化膜破坏[15]。值得注意的是当实验溶液pH2时,腐蚀电流密度会明显增大,从0.6 μA/cm2以下 (pH3、pH4、pH5) 增大到3.42 μA/cm2,点蚀电位也负移明显,降低到-52 mV (vs SCE) 左右,这说明当14Cr12Ni3WMoV不锈钢处于溶液环境为pH2时,其耐蚀性极差,点蚀也易于发生。
图2 14Cr12Ni3WMoV不锈钢在不同pH下0.1 mol/L NaCl溶液中电化学测试结果
在不同pH下进行循环极化回扫时,在相同的极化电位下,回扫电流密度大于正向扫描电流密度,即出现了滞后环 (pH2见图2a中放大图)。这是因为当极化电位大于点蚀电位时,钝化膜出现破裂,点蚀发生,腐蚀产物因迁移速度较慢而在蚀坑处发生聚积,闭塞区形成,由于闭塞区内金属阳离子的浓度不断增加,电负性大且原子半径小的Cl-会不断向孔内迁移、富集,造成孔内Cl-浓度升高,同时孔内产生的金属阳离子发生水解,生成大量的H+,使蚀坑内溶液出现酸化,从而闭塞区内金属基体处于更强的活化溶解状态,此外蚀坑外处于相对钝化状态,蚀坑内外就构成了活化—钝化局部腐蚀电池,进一步促进了蚀坑内金属基体的腐蚀[16,17]。从而在相同的极化电位下,回扫时的电流密度更大。值得注意的是,当含氯溶液pH2时,其回扫滞后环明显小于其它pH溶液 (pH3,pH4和pH5) 下形成的滞后环,这是因为溶液pH2时,溶液中含有高浓度的H+,蚀坑形成时,腐蚀产物易被溶解而不易在蚀坑处发生聚集,闭塞区形成程度低,蚀坑内Cl-的富集、金属阳离子的水解也会受阻,与此同时,由于本体溶液中H+浓度高,蚀坑外的金属也处于相对活性溶解的状态,从而局部腐蚀电池形成程度低,蚀坑形成前后,材料表面活性变化不明显,即出现极小的滞后环。
2.3 电化学阻抗谱
14Cr12Ni3WMoV不锈钢在不同pH的0.1 mol/L NaCl溶液中的电化学阻抗谱如图3所示。随着含氯溶液pH的减小,图3a容抗弧和图3b阻抗模值|Z|均有明显减小的趋势,说明14Cr12Ni3WMoV不锈钢表面阻抗降低,材料耐蚀性下降。可以发现,在不同pH的0.1 mol/L NaCl溶液中Nyquist图均表现出一个容抗弧特征,且与不锈钢的钝化膜相关。理论上处于腐蚀溶液中的不锈钢应存在2个容抗弧特征,分别对应于钝化膜电容和双电层电容,而在此腐蚀环境下双电层容抗弧未表现出,这可能是因为双电层电阻远小于钝化膜电阻,且双电层电容远大于钝化膜电容,从而导致双电层的容抗弧可以被忽略[18,19]。因此用图4所示的等效电路对电化学阻抗谱进行解析 (见表2)。其中Rs、CPE(Qf) 和Rf分别对应于溶液电阻、钝化膜电容和钝化膜电阻。CPE(Q) 一般用于不锈钢表面因粗糙度高等而引起弥散效应的情况下,其阻抗值可用式 (1) 计算:
图3 14Cr12Ni3WMoV不锈钢在不同pH下0.1 mol/L NaCl溶液中测得的电化学阻抗谱
图4 等效拟合电路
表2 等效电路各参数值
其中,Y0为CPE的导纳模量;ω为角频率;n为CPE的弥散指数[20]。从表2中可以看出,在溶液pH5时,14Cr12Ni3WMoV不锈钢的Rf最大为1.16×106 Ω·cm2,随着pH的减小,Rf逐渐减小,表明钝化膜阻抗变小,对基体的保护能力减弱。进一步分析发现,不锈钢钝化膜的电容值随着pH的减小,表现出增大的趋势,而钝化膜厚度与其电容之间存在反比的关系[21],说明不锈钢钝化膜变薄,同时弥散系数n表现出减小的趋势,说明H+浓度的增加不仅会使不锈钢钝化膜减薄还会导致钝化膜粗糙度增大,均匀性降低[22]。等效电路拟合出的材料耐蚀性与动电位极化测试结果具有较好的一致性。
2.4 腐蚀形貌观察
14Cr12Ni3WMoV不锈钢在不同pH的0.1 mol/L NaCl溶液中动电位极化后的腐蚀形貌如图5所示。由图可知,材料在酸性含氯溶液中的腐蚀特征为点蚀,值得注意的是当溶液pH2时,除存在点蚀特征以外,材料表面相对于pH3、pH4和pH5环境下还表现出明显的均匀腐蚀特征 (见图5a),这说明在强酸性 (如pH2) 的含氯溶液中,14Cr12Ni3WMoV不锈钢不仅会出现点蚀还存在明显的全面腐蚀现象,这也解释了在对应溶液中进行动电位极化时,其腐蚀电流密度明显增大的原因。为了进一步分析溶液pH对材料表面点蚀坑的影响,在不同pH下极化后的试样表面随机选取5个点蚀坑,通过激光共聚焦显微镜获取其三维形貌 (见图5),测量出其孔径和深度 (见图6)。由图6可知,当溶液pH2时,点蚀坑的深度和孔径分别最小为36和37 μm左右,随着pH的增大,其深度存在逐渐变大的趋势,而其孔径会先增大后减小,不过相对于pH2来说点蚀坑的孔径和深度都明显变大,说明当溶液酸性很强时,点蚀坑虽然容易形成,但其生长和发展会受阻,这可能是因为强酸溶液中含有大量的H+,腐蚀产物易被溶解,蚀坑闭塞区难以形成,坑内酸化和Cl-富集程度都会减弱[16],同时坑外也处于活性溶解状态,坑内坑外活化-钝化腐蚀电池形成程度低,蚀坑内的溶解速率减小。而当溶液中H+浓度不能导致材料表面处于活性溶解状态时,坑内坑外会形成明显的活化-钝化腐蚀电池,蚀坑内的腐蚀速率会增大,在此条件下如果H+浓度增加,即pH3、pH4相对于pH5,蚀坑沿径向的腐蚀速率会增大,而沿纵向的腐蚀速率减小,这主要是因为本体溶液中H+增多时,蚀坑边缘的H+也会增加,蚀坑底部和孔径处的H+浓度差就会减小,从而深度方向的腐蚀速率会有所减小,而径向的腐蚀速率会增加[23]。
图5 14Cr12Ni3WMoV不锈钢在不同pH下0.1 mol/L NaCl溶液中的腐蚀形貌及其三维形貌
图6 14Cr12Ni3WMoV不锈钢在不同pH下0.1 mol/L NaCl溶液中点蚀坑的深度和孔径
2.5 XPS分析
14Cr12Ni3WMoV不锈钢在溶液pH5和pH2的环境下形成的钝化膜中Fe 2p3/2、Cr 2p3/2、W 4f、Mo 3d的XPS图谱如图7和8所示。根据NIST的原子谱数据库和相关文献[14,23-27]对图谱进行分峰拟合,表3为各元素相应的结合能。当溶液pH5时,钝化膜中Fe 2p3/2的XPS图谱可以分解为5个峰,分别对应于Fe、FeO、Fe3O4、Fe2O3和FeOOH,其中FeO和Fe2O3对应峰的面积更大 (见图7a),说明钝化膜中的Fe更倾向于生成相对稳定的FeO和Fe2O3;Cr 2p3/2的XPS图谱可以分解为4个峰,分别对应于Cr、Cr2O3、Cr(OH)3和CrO3,其中Cr2O3和Cr(OH)3对应峰的面积更大 (见图7b),说明钝化膜中的Cr更倾向于生成相对稳定的Cr2O3和Cr(OH)3。当溶液pH2时,钝化膜中Fe和Cr也都主要生成相对稳定的FeO、Fe2O3、Cr2O3和Cr(OH)3 (见图8a和b),说明溶液pH的减小即H+浓度的增加不会对Fe和Cr在钝化膜中的主要存在形式造成明显的影响。值得注意的是,当溶液pH5时,钝化膜中Mo 3d的图谱没有明显的波峰 (见图7c),然而在pH2的时候,Mo 3d的波峰却很明显 (见图8c)。为了进一步分析不同pH下钝化膜中Mo存在的明显差异,需对不同pH下钝化膜中Cr、Fe、Mo和W之间原子含量 (Cx) 进行计算。
图7 14Cr12Ni3WMoV不锈钢在pH5的0.1 mol/L NaCl溶液中浸泡72 h后形成钝化膜的XPS谱
表3 钝化膜中主要组成物质的结合能
图8 14Cr12Ni3WMoV不锈钢在pH2的0.1 mol/L NaCl溶液中浸泡72 h后形成钝化膜的XPS谱
图9为不同pH下钝化膜中Cr、Fe、Mo和W之间原子含量比 (Cx),其计算公式如式 (2) 所示:
式中Ix元素峰强度,可用对应的峰面积表示;Sx为元素灵敏度因子[23,24]。单色Al靶测定时Cr 2p、Fe 2p、Mo 3d、W4f的灵敏度因子分别为2.427、2.957、3.321、3.523。由图3可知,不锈钢钝化膜在pH5和pH2的酸性含氯溶液中各元素原子含量规律如下,pH5:CFe(66.1%)>CCr(33.1%)>CW(0.8%)>CMo(0%);pH2:CCr(48.2%)>CMo(39.8%)>CFe(7.4%)>CW(4.6%)。上述结果表明当溶液pH为5时,钝化膜主要由Fe和Cr对应的氧化物和氢氧化物组成。而pH为2时,钝化膜主要由Cr的氧化物和氢氧化物和高价态Mo6+的化合物组成。钝化膜主要组成物质出现如此差异这可能是因为当溶液pH减小时,H+浓度增大,钝化膜中Cr、Fe、Mo和W相应化合物发生选择性溶解,稳定性相对较差的Fe的氧化物和氢氧化物溶解速率较快,而耐蚀性较好的Cr、Mo和W相应的化合物溶解缓慢并出现一定程度的富集,从而出现钝化膜中的Fe原子含量急剧下降,而Cr、Mo和W的含量明显上升,这说明Cr、Mo和W对提高不锈钢材料在酸性溶液中的耐蚀性有着重要的作用[27]。
图9 14Cr12Ni3WMoV不锈钢在pH2和pH5的0.1 mol/L NaCl溶液中浸泡72 h后形成钝化膜的元素含量
3 结论
(1) 末级叶片用钢14Cr12Ni3WMoV随着含氯溶液pH的减小,开路电位负移,点蚀电位和阻抗值均下降,说明材料表面钝化膜稳定性降低,对材料基体的保护能力减弱,从而腐蚀倾向增加,腐蚀速率增大,点蚀易发生。
(2) 随着酸性含氯溶液pH的减小,不锈钢表面点蚀坑的深度存在减小的趋势,而其孔径会先增大后减小,且在pH2时,点蚀坑的深度和孔径最小且同时存在明显的均匀腐蚀。这表明酸性含氯溶液pH的减小会减缓点蚀坑沿纵向的发展,而在无明显均匀腐蚀时会加快其沿径向的发展。
(3) 当含氯溶液pH5时,14Cr12Ni3WMoV不锈钢钝化膜主要由Fe和Cr对应的氧化物和氢氧化物组成,当pH2时,钝化膜主要由Cr的氢氧化物、氧化物和高价态Mo6+相应化合物组成,表明溶液pH的减小,及H+的浓度增大,会造成钝化膜中Fe、Cr、Mo和W发生选择性溶解,其中Fe溶解较快,而Cr、Mo和W溶解相对缓慢且在钝化膜中出现富集,一定程度上延缓腐蚀。
参考文献
1 Zhou J Y. Corrosion causes analysis and surface protection treatment of low-pressure final stage steam turbine blades [J]. New Technol. New Prod. China, 2009, (13): 112
1 周景云. 汽轮机低压末级叶片腐蚀原因分析及其表面防护处理 [J]. 中国新技术新产品, 2009, (13): 112
2 Wang F T, Wang N N, Chang L, et al. Corrosion characteristic of steam turbine blade 1Cr13 steel in simulated initial-condensate water [J]. Corros. Prot., 2018, 39: 489
2 王锋涛, 王娜娜, 常亮等. 汽轮机叶片用1Cr13钢在初凝水中的腐蚀特性 [J]. 腐蚀与防护, 2018, 39: 489
3 Hu P. Development of anti-erosion surface treatments used in last blades of steam turbine [J]. Surf. Technol., 2008, 37(6): 78
3 胡平. 汽轮机末级叶片表面防水蚀处理工艺及发展 [J]. 表面技术, 2008, 37(6): 78
4 Zhou W Y, Zhu Z X, Wang P, et al. Analysis on water-erosion of moving blade in low-pressure control stage of a steam turbine [J]. Corros. Prot. Petrochem. Ind., 2012, 29(6): 43
4 周文远, 朱正写, 王鹏等. 汽轮机低压调节级动叶片水蚀分析 [J]. 石油化工腐蚀与防护, 2012, 29(6): 43
5 Li H P. Fracture mechanism analysis of steam turbine blade [J]. Equip. Manuf. Technol., 2016, (6): 205
5 李海鹏. 汽轮机叶片断裂机理分析 [J]. 装备制造技术, 2016, (6): 205
6 Adnyana D N. Corrosion fatigue of a low-pressure steam turbine blade [J]. J. Fail. Anal. Prev., 2018, 18: 162
7 Katini? M, Kozak D, Gelo I, et al. Corrosion fatigue failure of steam turbine moving blades: A case study [J]. Eng. Fail. Anal., 2019, 106: 104136
8 Fu X X, Zhang M, Lu L L. Analysis on fracture reasons of steam turbine blades [J]. Phys. Test. Chem. Anal. (Part A: Phys. Test.), 2017, 53: 812
8 付星星, 张梅, 卢柳林. 汽轮机叶片断裂原因分析 [J]. 理化检验 (物理分册), 2017, 53: 812
9 Kim H. Crack evaluation of the fourth stage blade in a low-pressure steam turbine [J]. Eng. Fail. Anal., 2011, 18: 907
10 Zhang T, Tian F, He F X, et al. Failure analysis of low-pressure rotor blade of 300 mw steam turbine [J]. Inner Mongolia Electr. Power, 2014, 32(5): 41
10 张涛, 田峰, 贺飞雄等. 300 MW汽轮机低压转子动叶片断裂分析 [J]. 内蒙古电力技术, 2014, 32(5): 41
11 Stefanoni M, Angst U, Elsener B. Local electrochemistry of reinforcement steel-Distribution of open circuit and pitting potentials on steels with different surface condition [J]. Corros. Sci., 2015, 98: 610
12 Arjmand F, Zhang L F, Wang J M. Effect of temperature, chloride and dissolved oxygen concentration on the open circuit and transpassive potential values of 316L stainless steel at high-temperature pressurized water [J]. Nucl. Eng. Des., 2017, 322: 215
13 Rui J Q, Li J, Sun H D, et al. Influence of pH on the electrochemical bahavior of 00Cr15Ni7Mo2Cu2 supermartensitic stainless steel in 3.5%NaCl solutions [J]. Adv. Mater. Res., 2012, 581/582: 1058
14 Lodhi M J K, Deen K M, Haider W. Corrosion behavior of additively manufactured 316L stainless steel in acidic media [J]. Materialia, 2018, 2: 111
15 Wang Y F, Xie F Q. Corrosion behaviors of super 13Cr tubing steels in NaCl solution with different concentration [J]. Mater. Rev., 2018, 32: 2847
15 王毅飞, 谢发勤. 超级13Cr油管钢在不同浓度Cl-介质中的腐蚀行为 [J]. 材料导报, 2018, 32: 2847
16 Wang B, Du N, Zhang H, et al. Accelerating effect of pitting corrosion products on metastable pitting initiation and the stable pitting growth of 304 stainless steel [J]. J. Chin. Soc. Corros. Prot., 2019, 39: 338
16 王标, 杜楠, 张浩等. 304不锈钢点蚀产物对亚稳态点蚀萌生和稳态蚀孔生长的加速作用 [J]. 中国腐蚀与防护学报, 2019, 39: 338
17 Ai Y J, Du N, Zhao Q, et al. Effect of temperature on initiation of metastable pits and geometric features of stable pits for 304 stainless steel [J]. J. Chin. Soc. Corros. Prot., 2017, 37: 135
17 艾莹珺, 杜楠, 赵晴等. 温度对304不锈钢亚稳蚀孔萌生和稳态蚀孔几何特征的影响 [J]. 中国腐蚀与防护学报, 2017, 37: 135
18 Li Y, Cheng Y F. Passive film growth on carbon steel and its nanoscale features at various passivating potentials [J]. Appl. Surf. Sci., 2017, 396: 144
19 Wang Z, Feng Z, Zhang L, et al. Current application and development trend in electrochemical measurement methods for the corrosion study of stainless steels [J]. Chin. J. Eng., 2020, 42: 549
19 王竹, 冯喆, 张雷等. 电化学方法在不锈钢腐蚀研究中的应用现状及发展趋势 [J]. 工程科学学报, 2020, 42: 549
20 Wang Z. Investigation of the corrosion behavior and passive film degradation for austenitic stainless steel in H2S-containing environment [D]. Beijing: University of Science and Technology Beijing, 2018
20 王竹. 奥氏体不锈钢在H2S环境下的腐蚀行为与钝化膜演化研究 [D]. 北京: 北京科技大学, 2018
21 Lv N X, Liu K P, Yin C X, et al. Effect of HCO3- on passivation and pitting behavior of super 13Cr martensitic stainless steel [J]. Surf. Technol., 2019, 48(5): 36
21 吕乃欣, 刘开平, 尹成先等. HCO3-对超级13Cr马氏体不锈钢钝化行为及点蚀行为的影响 [J]. 表面技术, 2019, 48(5): 36
22 Popova A, Sokolova E, Raicheva S, et al. AC and DC study of the temperature effect on mild steel corrosion in acid media in the presence of benzimidazole derivatives [J]. Corros. Sci., 2003, 45: 33
23 Sun M, Xiao K, Dong C F, et al. Effect of pH on semiconducting property of passive film formed on Ultra-High-Strength Corrosion-Resistant steel in sulfuric acid solution [J]. Metall. Mater. Trans., 2013, 44A: 4709
24 Liu C T, Wu J K. Influence of pH on the passivation behavior of 254SMO stainless steel in 3.5%NaCl solution [J]. Corros. Sci., 2007, 49: 2198
25 Guo L Q, Lin M C, Qiao L J, et al. Duplex stainless steel passive film electrical properties studied by in situ current sensing atomic force microscopy [J]. Corros. Sci., 2014, 78: 55
26 Guo Q, Liu J H, Yu M, et al. Effect of passive film on mechanical properties of martensitic stainless steel 15-5PH in a neutral NaCl solution [J]. Appl. Surf. Sci., 2015, 327: 313
27 Fan X H, Yu Y, Zhang Z R, et al. Pitting and repassivation behavior of 316l austenitic stainless steel under different potentials [J]. Surf. Technol., 2020, 49(7): 287
27 樊学华, 于勇, 张子如等. 316L奥氏体不锈钢在不同电位下的点蚀和再钝化行为研究 [J]. 表面技术,2020, 49(7): 287
免责声明:本网站所转载的文字、图片与视频资料版权归原创作者所有,如果涉及侵权,请第一时间联系本网删除。
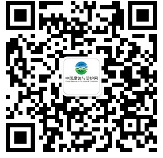
官方微信
《中国腐蚀与防护网电子期刊》征订启事
- 投稿联系:编辑部
- 电话:010-62316606-806
- 邮箱:fsfhzy666@163.com
- 中国腐蚀与防护网官方QQ群:140808414