在油田天然气井丛管网的检修中,发现一些焊缝根部及母材内壁有腐蚀坑存在,其主要形状为孔蚀和片蚀,对管道的安全运行构成了极大隐患,因此需要对腐蚀深度进行精确测量,作为RBI(基于风险评估的设备检验)分析的依据。传统的超声检测、相控阵检测、涡流检测等技术往往难以确定内壁小面积腐蚀坑的最大腐蚀深度位置,且对焊缝及其邻近区域的腐蚀坑测量可靠性低。
X射线射入金属材料时会发生衰减,衰减量与穿透厚度具有函数关系,数字X射线摄影(DR)技术可把不同的透照射线强度以灰度记录下来形成数字图像。利用该原理,吉林亚新工程检测有限责任公司和包头市北国无损检测技术有限公司的技术人员通过模拟试验建立了厚度-灰度数学模型,采用算法计算得出了腐蚀坑深度,下面让我们来详细了解一下吧。
模拟试验
选择与天然气管道形状、材料相近的钢管,加工不同深度的平底孔作为模拟试块,如图1所示,设置的平底孔参数如表1所示。
图1 模拟试块结构示意
表1 模拟试块上设置的平底孔参数
采用X射线对模拟试块不同深度的平底孔进行透照,透照时采用相同的透照布置、曝光参数,采集图像后测量平底孔及相邻母材部位的灰度,平底孔编号顺序如图2所示,灰度测量结果如表2所示。
图2 平底孔编号顺序示意
表2 灰度测量结果
数据归一化处理
理论上相同的曝光条件下,母材的灰度应是相同的,但是在实际检测中焦距、照射方向的厚度差异会引起母材的灰度差异,亦会引起腐蚀坑的灰度差异,可以通过归一化计算法降低该偏差,归一化计算结果如表3所示。
表3 归一化灰度处理结果
由曲线斜率k的计算公式k=ΔG/Δh(ΔG为灰度差,Δh为平底孔深度)得出平均斜率图片=1262,数据相对偏移量为-1.20%~15.82%,绝对偏移量为-0.12~0.32mm,数据统计结果如表4所示。
表4 曲线斜率及不确定度统计结果
腐蚀坑深度h的计算公式为:h=ΔG×图片。通过数据分析,灰度差与平底孔深度呈线性关系,其关系曲线如图3所示。
图3 灰度差与平底孔深度关系曲线
现场检测
按照操作指导书采集DR图像。在选择灰度测量点时,首先应着重考虑散射线的影响,尽可能选择散射比接近的两点作为参考点,降低散射比不同引起的灰度差。散射比与焦距、照射场、射线能量、穿透厚度、焊缝余高、钢管曲率等均有关系;其次,要考虑射线束偏离中心导致的透照厚度的变化,射线束偏心对透射率也有一定的影响。
母材腐蚀坑测量
受射线检测几何布置特点的影响,钢管圆周方向穿透厚度的变化较大,测量点越偏离管子中轴线,厚度变化就越大,而轴向的穿透厚度变化较小。因此在选择母材腐蚀坑测量点时,第1点选择在被测腐蚀坑中灰度值最大的部位,第2点选择在轴向偏移一定距离的母材完好部位,根据工件情况也可在腐蚀坑上下对称部位取两点(第2点,第3点)的平均灰度作为母材灰度的测量值,母材腐蚀坑测量点位置如图4所示。
图4母材腐蚀坑测量点位置
熔合线附近腐蚀坑测量
射线透照焊缝时,较薄部位的射线会向较厚部位散射,不同部位的散射比变化复杂,难以量化,因此需要通过选择合适的测量点来降低散射比的影响。熔合线附近腐蚀坑测量点的选择主要考虑内外余高叠加引起的透照厚度的变化。因此在选择测量点时,第1点选择在腐蚀坑灰度最大的部位,第2点选择在该点附近沿着焊缝偏移至无腐蚀的部位,熔合线附近腐蚀坑测量点位置如图5所示。
图5熔合线附近腐蚀坑测量点位置
焊缝腐蚀坑测量
选择焊缝腐蚀坑测量点时,应主要考虑焊缝余高的变化、内外余高叠加、双壁透照时两个焊缝叠加等引起的透照厚度和散射比的变化。第1点选择在腐蚀坑灰度最大的部位,第2点选择在该点附近沿着焊缝偏移至无腐蚀的部位;在选择第2点时也应考虑射线束偏离中心带来的透照厚度的变化,随着测量点远离曝光中心点,厚度偏差变大,因此将曝光中心设在第1点和第2点的中间位置可降低该因素的影响,焊缝腐蚀坑测量点位置如图6所示。
图6焊缝腐蚀坑测量点位置
数据整理
根据测量的灰度数据,按上述计算方法得出腐蚀坑深度,腐蚀坑灰度及深度数据如表5所示。
表5腐蚀坑灰度及深度数据
结语
在役管道腐蚀坑深度的DR检测中,图像灰度与工件厚度、射线能量、材料吸收系数、散射线、照射场、管内介质、腐蚀坑内容物等均有关;透照部位偏离射线束中心的程度也会对透照厚度和射线透射率产生影响;受钢管曲率的影响图像各个部位的散射比也不同,在实际应用中只有综合考虑上述因素,才能提高管道腐蚀坑深度的测量精度。
免责声明:本网站所转载的文字、图片与视频资料版权归原创作者所有,如果涉及侵权,请第一时间联系本网删除。
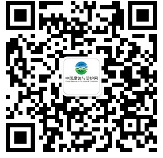
官方微信
《中国腐蚀与防护网电子期刊》征订启事
- 投稿联系:编辑部
- 电话:010-62316606-806
- 邮箱:fsfhzy666@163.com
- 中国腐蚀与防护网官方QQ群:140808414