摘要
利用U形弯试样浸泡实验和电化学测试技术研究了两种油套管钢在CO2注入井环空环境中的应力腐蚀开裂行为。结果表明,TP110TS钢和P110钢在注入井环空环境 (大量CO2-微量H2S) 下存在一定的应力腐蚀敏感性,其应力腐蚀机制为阳极溶解和氢脆协同作用机制。在CO2-H2S环境下,咪唑啉类缓蚀剂的浓度对TP110TS和P110油套管钢的应力腐蚀产生不同的影响,添加足量的缓蚀剂对P110钢的应力腐蚀行为产生较好的抑制效果;但当添加量不足时,缓蚀剂会增加P110钢发生应力腐蚀的倾向性。而TP110TS钢的应力腐蚀敏感性随着缓蚀剂浓度的增加而减小,相对更适用于添加缓蚀剂的CO2-H2S环境。
关键词: TP110TS钢; P110钢; 环空环境; 应力腐蚀; CO2注入井
当前油气田生产中,越来越多的新型技术被用来提高生产效率,其中CO2驱注技术就因其具有更好的采收优势而被广泛用于取代传统水驱注[1,2]。然而,由于油管中所注入的CO2、污水 (含Cl-,SO42-等) 等易通过环空管泄漏,从而导致环空液的pH值降低,并且在这种密闭的环空环境下,硫酸盐还原菌 (SRB) 的存在会导致管内H2S含量升高。这种严苛的环境极易导致油套管的断裂损坏,造成重大的经济损失和安全事故,严重影响石油开采的安全运行[3,4,5]。在这种H2S/CO2共存环境下,服役的油套管具有极高的应力腐蚀开裂 (SCC) 危险性[6,7,8,9,10]。目前,虽然CO2或H2S环境中的腐蚀行为被广泛研究[10,11,12,13],但实际生产过程中为了防止或减缓这种环境下的腐蚀问题,国内外油气田中多采用加注缓蚀剂的方法。而在各种缓蚀剂中,咪唑啉缓蚀剂以其低毒性、较好的防腐性和热稳定性成为国内外油气田中常用的缓蚀剂,其在H2S/CO2共存环境下表现出较好的耐蚀性能[14,15,16]。但对于含有缓蚀剂与H2S/CO2共存环境下油套管的腐蚀研究,大多数只关注油管内的腐蚀问题,对于这种复杂油套管间CO2-H2S环空环境体系中的腐蚀问题有待进一步研究。
本文利用静载荷应力腐蚀实验和电化学测试技术,研究了咪唑啉缓蚀剂对TP110TS和P110油套管在CO2-H2S环空环境体系下的应力腐蚀行为,为CO2注入井环空环境腐蚀防护方法的建立提供参考和依据,更为复杂环境下服役材料的选择提供一定的数据支撑。
1 实验方法
实验材料为P110和TP110TS油套管钢,其化学成分如表1所示。参照测试标准GB/T13298-2015《金属显微组织检验方法》[17]对P110和TP110TS钢进行金相组织观察。实验所用溶液为根据现场提取的某油田CO2驱注井环空保护液成分配置的模拟溶液。其母液成分 (g/L) 为:NaHCO3 2.71,NaCl 6.15,Na2SO4 0.33,使用0.5% (质量分数) CH3COOH溶液调节溶液pH值至4,所用试剂均为化学纯。配置溶液前,先通入高纯N2除氧,以防止硫化物氧化。所用缓蚀剂为某商用咪唑啉类缓蚀剂。电化学实验试样尺寸为10 mm×10 mm×3 mm,并使用环氧树脂密封,浸泡实验试样采用U形弯试样。实验前将试样用砂纸逐级打磨至2000#,然后用丙酮清洗试样表面并吹干备用。每组实验取3个平行样品进行实验。实验条件为:气体总压9 MPa,其中,H2S分压为0.2 MPa,CO2分压为4 MPa;溶液pH值为4,实验温度为室温。
表1 TP110TS和P110油管钢的化学组成
电化学测量采用三电极体系,Ag/AgCl电极为参比电极,Pt电极为辅助电极,试样为工作电极。实验前,用丙酮将试样和Pt电极表面除油,装入溶液介质,将电极组装好后连接到高压釜内。密闭高压釜,并通入N2除氧2 h,然后依次通入H2S,CO2和N2至所需分压。加压后静置30 min,以保证开路电位稳定。然后,在PARSTAT-2273电化学工作站上进行极化曲线和阻抗测量。极化曲线测试电位扫描由阴极向阳极进行,电位扫描范围为-500~800 mV (vs OCP),扫描速率为0.5 mV/s;电化学阻抗测试频率范围为105~10-2 Hz,激励电位为10 mV。
U形弯浸泡实验与电化学实验的测试条件相同。首先将U形弯平板试样压弯至张角为10°±1°自然回弹,然后用螺栓加载至张角为0° (U形)。对螺栓部位密封并将试样表面进行除油后,将试样置于高压釜中进行浸泡,浸泡时间为720 h。浸泡结束后,先利用线切割机切下观察部位并用丙酮进行除油。然后,将试样置于除锈液 (500 mL HCl+500 mL H2O+3.5 g六次甲基四胺) 中超声清洗去除腐蚀产物,再用丙酮清洗并吹干。利用FEI Quanta200型扫描电镜 (SEM) 对浸泡后试样的表面形貌进行观察。
2 实验结果
2.1 显微组织
P110和TP110TS钢的金相组织如图1所示。可见,P110和TP110TS钢的金相组织均为马氏体+部分铁素体,组织相对均匀,没有明显的轧制织构特征。钢中的夹杂物不明显,其密度相对较低、尺寸较小,未发现扁平状或点链状夹杂物。比较P110和TP110TS钢的金相组织,虽然都为马氏体加部分铁素体,但组织的大小和均匀程度还存在一定的差别。比较而言,TP110TS钢的组织更加均匀,经过回火处理之后马氏体板条结构退化、粒状渗碳体析出增多。
图1 P110和TP110TS油管钢的金相组织
2.2 静载荷应力腐蚀实验
2.2.1 宏观形貌分析
图2是U弯试样在不同浓度缓蚀剂条件下浸泡720 h后的表面宏观形貌图。从图2a和b中可以看出,当不添加缓蚀剂时,TP110TS和P110钢表面均发生了严重的腐蚀,并且试样均发生了断裂。这说明两种材料在该环境下均易发生SCC,具有很高的应力腐蚀敏感性。而当添加浓度1 g/L咪唑啉缓蚀剂时,TP110TS和P110钢表面腐蚀较为轻微,没有明显的腐蚀产物,表面依然有金属光泽。缓蚀剂的添加对P110和TP110TS试样SCC均产生了一定的抑制效果。
图2 TP110TS和 P110钢在添加不同浓度缓蚀剂条件下浸泡720 h后的宏观形貌
进一步对不同实验条件下的U弯试样SCC情况进行统计,结果见表2。结果表明,在无缓蚀剂时,每组试样均发生了断裂,试样表面发生严重的腐蚀。不同的是,P110钢试样表面具有明显的均匀腐蚀和裂纹的形貌,而TP110TS钢主要是以点蚀坑居多。这可能与两种材料本身的耐蚀性能具有一定的相关性。随缓蚀剂浓度的增加,P110和TP110TS钢表面的点蚀情况均得到了改善;当缓蚀剂浓度达1 g/L时,两种材料的应力腐蚀均得到了明显抑制。
表2 不同缓蚀剂浓度条件下两类油套管钢U形弯腐蚀及开裂情况对比
2.2.2 U形弯应力腐蚀微观形貌
图3是U弯试样在不同浓度缓蚀剂条件下浸泡720 h,去除表面腐蚀产物后的表面微观形貌。可以看出,在不添加缓蚀剂时,两种材料的试样表面都存在着严重的点蚀坑和裂纹。这说明在不添加缓蚀剂情况下,TP110TS和P110钢在上述环境服役时均有发生严重SCC的倾向性。而当添加一定浓度咪唑啉缓蚀剂时,对TP110TS钢试样腐蚀产生了一定的抑制效果,并且这种效果随着缓蚀剂浓度的增加,试样表面点蚀坑的深度和数量均呈现出明显减少的趋势。当添加缓蚀剂浓度为0.4 g/L时,P110钢表面几乎不发生均匀腐蚀,但有大量的点蚀坑分布;而TP110TS钢试样表面的点蚀坑数量和深度呈现明显减少的趋势。当缓蚀剂浓度达到1 g/L时,P110钢表面的点蚀数量和深度锐减;而TP110TS钢表面发生了轻微的点蚀,几乎不腐蚀。当缓蚀剂浓度大于0.4 g/L时,两种材料的SCC和点腐蚀情况明显减轻,试样的腐蚀情况逐渐减弱,耐腐蚀能力逐渐加强。
图3 P110和 TP110TS钢在不同浓度缓蚀剂条件下浸泡720 h除锈后的微观形貌
2.3 电化学测试结果
为了进一步分析不同浓度缓蚀剂对两种材料SCC的影响机理,测试了P110钢和TP110TS钢在不同浓度缓蚀剂下的极化曲线和电化学阻抗谱。图4是不同缓蚀剂浓度下TP110TS和P110钢的极化曲线图。表3为极化曲线拟合结果。可以看出,TP110TS钢的自腐蚀电位 (Ecorr) 随缓蚀剂浓度的增加不断提高,并且腐蚀电流密度也呈现出减小的趋势。这与U弯浸泡实验结果相似,缓蚀剂的加入减缓了TP110TS钢的腐蚀行为,进而对SCC产生了影响。对于P110钢,当缓蚀剂浓度大于0.4 g/L时,自腐蚀电流密度下降,而自腐蚀电位上升,这可能是由于P110钢发生均匀腐蚀向点蚀转变导致的。并且,通过极化曲线也可以看出,咪唑啉缓蚀剂对P110钢的阴极过程有较明显的抑制作用。
图4 不同缓蚀剂浓度下TP110TS和P110钢的极化曲线
表3 不同缓蚀剂浓度下TP110TS和P110钢的极化曲线拟合结果
图5为TP110TS和P110钢在不同浓度缓蚀剂溶液中的EIS曲线,其拟合电路如图6所示。其中,Rs 代表溶液电阻,Qf为腐蚀产物层电容的常相位角元件,Rf表示腐蚀产物电阻,Qdl为双电层电容的常相位角元件,Rct表示电荷转移电阻。表4为EIS拟合的电化学参数。从图5中可以看出,缓蚀剂浓度的变化对TP110TS钢和P110钢的电化学过程均产生较大的影响,对于TP110TS钢,随缓蚀剂浓度的增大,电化学阻抗谱形状未有变化,但容抗弧半径增大。这说明对于TP110TS钢,缓蚀剂浓度越大,耐腐蚀能力越强。缓蚀剂浓度增大,腐蚀电流呈减小的趋势,说明缓蚀剂浓度越大,腐蚀速率越低。缓蚀剂的添加使得双电层传质过程受到明显的抑制,并抑制了硫化物吸附和H的析出过程,导致腐蚀性介质通过缓蚀剂膜的阻力相应增大。而对于P110钢,当缓蚀剂添加量大于0.4 g/L时,阻抗值明显增大。这与极化曲线中的结果相一致。对比TP110TS和P110钢的Nyquist图可以看出,阻抗值的变化规律为:P110-1 g/L>TP110TS-1 g/L>TP110TS-0.4 g/L>P110-0.4 g/L,这与极化曲线中的自腐蚀电流密度结果相一致。这也表明,缓蚀剂的添加能有效增加双电层的电阻,抑制腐蚀介质与材料的反应,从而提高了材料的耐蚀性能。
图5 不同缓蚀剂浓度下TP110TS和P110钢的电化学阻抗谱
图6 不同缓蚀剂浓度下TP110TS和P110钢EIS的等效电路图
表4 不同缓蚀剂浓度下TP110TS和P110钢的电化学等效电路图拟合结果
3 讨论
当前研究[18,19,20]表明,CO2驱驻井下油管钢的腐蚀机理是一种典型的高H2S-CO2-Cl-环境的应力腐蚀开裂。在实际的生产过程中,油管钢会发生一些刺漏现象,这种现象会随着服役时间的延长变得更为严重,由于漏点的存在会导致CO2等进入环空液,致使环空液pH值降低。又由于油管钢的服役环境处于封闭状态,导致SRB的大量增加,从而促进了硫化物的转变。因而在该环境下,油管钢腐蚀过程主要是H+的还原反应和铁与硫化物、碳酸盐等进行的反应。具体如下[21,22]:
因此,在不添加缓蚀剂的条件下,在CO2,Cl-和H2S的作用下,油管钢表面会产生大量的Hasd,导致油管钢发生严重的SCC,如图2和表2中所示,试样易发生断裂。其SCC机制具有一定的氢脆 (HE) 特征。
而当在模拟环空溶液环境中添加咪唑啉类缓蚀剂后,缓蚀剂能够在试样表面形成一层具有较强结合力的吸附层,腐蚀产物与缓蚀剂相互结合,从而提升了表面腐蚀产物膜的致密性。另一方面,缓蚀剂还可以与铁离子等形成络合,进而增强了产物膜中分子间的结合力。通过上述两种机制能够有效地抑制双电层的电化学反应,降低腐蚀速率。而在添加不同浓度缓蚀剂条件下,TP110TS和P110两种油管钢的腐蚀行为并不一致。当缓蚀剂浓度较低时,P110钢的表面不能完全被缓蚀剂所覆盖,这会导致存在局部点暴露在溶液中,在一些活性离子 (Cl-) 作用下,产生局部腐蚀,从而导致局部阳极溶解的存在,因而在图3中可以看到较多的点蚀坑的出现。这些局部点蚀坑的存在,进一步加速了P110钢的SCC行为。而TP110TS钢基体在模拟溶液中表现出较P110钢更好的耐蚀性能,如图3d所示。随着缓蚀剂浓度的进一步增大,P110钢表面的活性点被缓蚀剂进一步抑制,缓蚀剂与试样表面形成更为紧密的吸附膜,进而抑制了表面点蚀坑的数量,并且这一结果也体现在图4的结果中。当缓蚀剂浓度在1 g/L时,P110钢和TP110TS钢的腐蚀电流密度都远小于在0.4 g/L情况下的,通过电化学阻抗谱也可以看出其极化电阻呈现出明显的增大现象 (图5)。因此,在CO2注入井环空环境下,足量的咪唑啉缓蚀剂能有效抑制SCC,但当用量不足时,缓蚀剂的添加会增大P110钢发生应力腐蚀的倾向性,其SCC机制为氢脆与局部阳极溶解的混合机制。而TP110TS钢则不会出现该现象,其SCC敏感性随着缓蚀剂浓度的增加而不断减小。
4 结论
(1) TP110TS钢和P110钢在CO2注入井环空环境中均会发生应力腐蚀,为阳极溶解和氢脆混合反应机制。
(2) 咪唑啉类缓蚀剂浓度对TP110TS钢和P110钢的应力腐蚀行为具有不同的影响作用。当缓蚀剂浓度不足时,P110钢的应力腐蚀敏感性有增大的趋势。而对于TP110TS钢,随着缓蚀剂含量增加,耐应力腐蚀能力增强。TP110TS钢较P110钢更适合用于添加缓蚀剂的CO2-H2S环境。
免责声明:本网站所转载的文字、图片与视频资料版权归原创作者所有,如果涉及侵权,请第一时间联系本网删除。
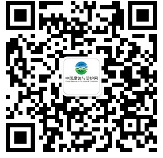
官方微信
《中国腐蚀与防护网电子期刊》征订启事
- 投稿联系:编辑部
- 电话:010-62316606-806
- 邮箱:fsfhzy666@163.com
- 中国腐蚀与防护网官方QQ群:140808414