摘要
围绕应力腐蚀行为的实验研究方法、影响因素以及应力腐蚀机制的理论分析等几个方面综述了核电结构材料应力腐蚀研究的现状,讨论了研究中亟待解决的问题,指出了研究的发展方向与趋势。
关键词: 核电结构材料 ; 高温高压水 ; 应力腐蚀 ; 冷加工 ; 焊接件
1 核电结构材料的应力腐蚀现象
核电作为一种可持续供应的清洁能源,是我国能源的重要组成部分,安全高效地发展核电是我国能源发展战略的方针。 《国家核电中长期发展规划(2011-2020年)》指出,到2020年我国核电装机总容量将达到5800万千瓦,核电占全部电力装机容量的比重将提高到4%以上。
核电发展的最重要前提始终是核电运行的安全性和经济性,福岛核事故之后尤其如此。核电站关键结构材料在高温高压水和辐照环境下长期服役的可靠性和稳定性是影响核电站的安全性和经济性的重要因素。
我国目前在建和运行的核电站反应堆以压水堆为主,其常用结构材料包括镍基690合金及其焊接金属镍基52/152合金,304和316奥氏体不锈钢,低合金钢,800合金和碳钢等。这些结构材料的服役环境为流动的高温高压水,承受复杂的工作应力,堆芯部位服役的材料还承受强烈辐照。苛刻的服役环境使材料对环境损伤的敏感性大大增加。研究 [1~3]
及电站运行经验表明,主回路焊接部位的应力腐蚀开裂与环境疲劳、压力容器的辐照脆化与环境疲劳、蒸汽发生器传热管的腐蚀与应力腐蚀开裂、二回路的流动加速腐蚀及主管道的热老化等是影响电站运行安全性与经济性的主要材料环境损伤模式。
在上述环境损伤模式中,应力腐蚀开裂 (SCC)是压水堆中焊接接头与蒸汽发生器传热管材料失效的主要原因。例如,欧美日等国的压水堆核电站主回路接管安全端及压力容器顶部贯穿管等部位的焊接接头已发生多起SCC失效,造成冷却介质的泄露 [4] 。
图1所示的统计结果表明,美国核电站蒸汽发生器传热管发生的失效中,SCC所占比例远高于其它模式。一回路是反应堆中最重要的压力边界,焊接接头是一回路中的关键结构,而蒸汽发生器传热管占一回路与冷却剂接触总截面积的75% [5] 。因此,SCC的发生对电站运行安全带来极大威胁,修复发生失效的材料及其部件也给电站造成很大的经济损失。
研究 [7] 表明,高温高压水中的SCC是由敏感的材料结构、腐蚀性介质和应力的共同加速作用下的腐蚀行为造成的一个裂纹由局部缺陷萌生到缓慢稳态扩展的过程,因而,材料、水化学和应力是影响高温高压水SCC的3个主要因素。而腐蚀是SCC发生的基本过程。对SCC的研究需要围绕材料、水化学与力学等影响因素,研究SCC萌生与扩展行为,揭示各因素影响SCC的机制,阐明SCC发生条件下腐蚀的动力学过程,进而澄清SCC的机制。SCC研究的最终目的是建立SCC行为定量评价与预测的模型和方法,发展抑制、缓解SCC的应用性技术以服务于核电的安全高效发展。
本文围绕SCC行为的实验研究方法、影响因素以及SCC机制的理论分析等几个方面综述了核电结构材料SCC开裂研究的进展,讨论了研究中亟待解决的问题,指出了研究的发展方向与趋势。
2 SCC行为的实验研究
SCC的形成与发展过程主要包括两个阶段,即裂纹的萌生与扩展。相应的SCC行为的实验研究主要包括以下两个内容:SCC裂纹的萌生和扩展。
图1 美国核电站蒸汽发生器600合金传热管失效模式与年度失效数量
2.1 SCC裂纹萌生实验
裂纹萌生实验的最主要评价指标是裂纹的萌生时间,其它指标还包括裂纹数目和长度等。SCC裂纹在实际服役环境下的萌生时间一般较长,在实验室条件下通常需要采用加速实验,对试样施加一定的拉应力/应变以促进裂纹的萌生。常用方法有慢应变速率拉伸 (SSRT) 和U弯实验等。
SSRT实验是在高温高压水环境下以一个缓慢的应变速率对试样施加应变,直至试样断裂。该方法可以较快地对比不同材料或同种材料不同环境下的SCC敏感性,是一种定性或半定量的实验方法。如文献[8] 采用该方法研究轧后退火态 600 合金(600MA) 在不同pH值含Pb水中的SCC敏感性。
U弯实验是指将样品弯成U型,保证试样部分表面的初始拉应力到达屈服点,然后将试样暴露在腐蚀介质中进行实验。在此过程中,材料不同部位受到不同程度的应力,从而加速其SCC过程。一般对大量试样进行平行实验,并定时地中断实验观察各试样的裂纹萌生情况,以得到裂纹萌生时间。本方法尤其适用于蒸汽发生器U型弯管的SCC裂纹萌生行为研究。
由于SCC是材料在静态应力条件下发生的开裂,因而SSRT实验对试样采用动态加载方式在某些条件下会造成实验结果的误差。如对316不锈钢在超临界水中进行SSRT实验,发现材料具有裂纹萌生敏感性。而在恒定应力条件下对该材料进行裂纹扩展实验则得到了极低的裂纹扩展速率,说明材料在超临界水环境中具有较高SCC抗性。研究 [9] 认为这是由于材料的快速氧化导致裂纹尖端钝化造成的。
2.2 SCC裂纹扩展实验
SCC引起的材料失效主要是由于裂纹萌生继而扩展,最终导致材料的失稳断裂。因此研究裂纹扩展行为是分析材料SCC失效的基础之一,而研究的重点在于精确地测量裂纹扩展的长度,进而计算出裂纹的扩展速率。
裂纹扩展行为的研究,一般采用紧凑拉伸(CT) 试样,在高温高压水环境中对试样施加应力,同时应用电位降法对裂纹扩展长度进行原位测量。电位降法包括直流电位降 (DCPD) 与交流电位降(ACPD) 两种方法,其中,DCPD得到了最广泛的应用。该方法的原理是在试样的上下表面施加恒定电流,使之在试样厚度方向上产生恒定的电场。在恒定电流下,利用裂纹两表面间的电位降差与裂纹扩展长度之间的函数关系,将所测量的电位降值转换成对应的裂纹长度。
Andresen等 [10,11] 应用此方法系统研究了镍基合金和不锈钢等核电材料在模拟服役环境下的SCC裂纹扩展行为及其影响因素。测量时,采用固态继电器使电流方向周期交替变化消除热电偶效应和放大漂移的影响,从而进一步提高了测量精度。Ritter等 [12] 也采用定期转变电流方向的DCPD法研究了低合金钢及异种焊接件腐蚀疲劳的裂纹扩展行为。在异种金属焊接件过渡区中,由于材料的化学成分不均匀性导致材料电阻随裂纹扩展的变化而造成裂纹扩展长度测量的较大误差。Seifert等 [13] 采用有限元方法通过模拟异种焊接件过渡区的直流电场,对DCPD的测量结果进行了修正。
3 SCC的影响因素研究影响
SCC的因素如上所述,包括材料自身的敏感结构、应力和水化学环境等。目前的工作主要是通过表征材料的微观结构研究材料因素对SCC的影响,通过研究不同应力、水化学环境下的SCC行为揭示力学以及水化学因素对SCC的影响,并结合高温高压水环境腐蚀行为的研究为阐明SCC的机制提供基础。
3.1 材料因素的影响
影响SCC的材料因素包括晶界化学与碳化物、晶界结构、屈服强度和残余应力/应变的分布等。
3.1.1 晶界化学与碳化物影响
核电结构材料最常见的SCC模式是沿晶开裂 (IGSCC)。由于偏析,材料晶界处的化学成分和块体中可能有显著的不同。对于氧化性水环境和还原性水环境,晶界偏析、沉淀和碳化物的分布对于材料SCC的影响也各不相同。
文献 [14] 对不同C和P含量的600合金,设计了不同的热处理工艺得到了不同的Cr在晶界的贫化程度,并在还原性水环境中进行了SCC敏感性实验。结果显示,C在固溶体中的存在会在很大程度上降低SCC敏感性;P在固溶体中会阻碍位错运动,从而轻微降低合金的SCC敏感性;虽然Cr的贫化对还原性水环境中的抗SCC能力并无影响,但在氧化性水环境中,轻微的Cr贫化会明显地促进沿晶开裂 [15~17] 。文献 [18] 研究了182合金枝晶间SCC行为与枝晶面上和穿枝晶面上的微观化学成分分布的关系,发现穿枝晶面上Cr含量较多,而枝晶面上P偏聚严重,这可能是182合金较多发生枝晶间SCC的原因之一。
关于晶界碳化物的微观特征及其分布对SCC的影响已开展了大量研究。研究 [19] 发现,600MA合金中的晶界碳化物主要为Cr 7 C 3 ,而经热处理的600合金 (600TT) 其晶界碳化物主要为Cr 23 C 6 ,该碳化物与晶界一侧的基体共格,与晶界结合强度高,因而明显改善了材料在压水堆一回路水中的 IGSCC 抗力。文献 [20] 研究了经过和未经过TT热处理的600合金中碳化物的分布对SCC行为的影响,发现还原性高温高压水中呈网格状连续分布的晶界碳化物会使SCC抗性增强,而晶内碳化物的分布会增加SCC的敏感性。对182合金的研究发现 [21] ,较高的C/Nb比例会导致较多连续的晶界碳化物形成,其存在可以降低 IGSCC 的敏感性,但增加了产生热裂纹的几率。此外,晶界碳化物还可能导致局部的应力集中,从而增加SCC开裂倾向 [22,23] 。
3.1.2 晶界结构
晶界结构对IGSCC行为有显著影响。根据文献 [24,25] ,晶界结构分为随机大角晶界、重合位置点阵 (CSL) 晶界与小角晶界等。研究 [26] 表明,小角晶界和CSL晶界SCC抗性较好,而随机大角晶界易发生SCC。研究合金的晶界特征与结构,通常采用电子背散射衍射 (EBSD) 技术,其是基于扫描电镜中电子作用于倾斜的样品表面所形成的Kikuchi花样来确定晶体结构、取向以及其它信息的方法 [27] 。
一般镍基600和690合金所含的CSL晶界中,有很大一部分是 Σ 3孪晶界。由于 Σ 3晶界的晶界能很低 (约为随机晶界的1/50),因而几乎不发生沿晶开裂现象 [26] 。虽然具有大量 Σ 3孪晶界的材料SCC抗性可能较好,但由于 Σ 3孪晶界不处于晶界主要网络上,未阻断大角晶界的连通性,因而其抗性改善并不是直接由于 Σ 3孪晶界的作用。研究 [28,29] 表明,由于 Σ 3孪晶界与大角晶界作用,在相交处生成CSL晶界,这些具有良好SCC抗性的CSL晶界处在主要晶界网络上,阻断了大角晶界的连通性,因而材料的SCC抗性得到了改善。由此可知,材料是否具有较强的SCC抗性,仅以 Σ 3孪晶界的含量来判断是不充分的 [29] 。
此外,CSL晶界的偏差角也是一项非常重要的参数。偏差角存在的原因是在一定的范围内引入位错调整界面上原子的排列,使原子位置尽可能少的被扰乱。这种位错是晶界位错 (重合位置点阵的位错),相当于原来的CSL晶界上叠加了小角度晶界。据文献 [26] 报道,在镍基合金和不锈钢等材料中,偏差角较大的 Σ 3晶界也会发生SCC。
3.1.3屈服强度的影响
不锈钢和镍基合金等核电常用结构材料受到冷加工或辐照的影响时屈服强度的增加会使材料的SCC敏感性上升 [5,30] 。如对316和304不锈钢的研究 [30] 发现,冷加工程度与屈服强度的增加呈正比关系,屈服强度的增加会使SCC裂纹扩展速率以指数形式增加。又如对304不锈钢的研究 [31] 表明,辐照导致的位错环结构会使材料的屈服强度增加,进而导致SCC敏感性上升。
3.1.4 残余应力/应变的分布
材料内部存在的应力超过一定阈值时,会引发SCC现象。残余应力和应变的存在会增加材料的SCC敏感性,是诱发SCC的主要因素之一 [32] 。在SCC萌生实验中,微小裂纹更容易在残余应变 (即局部取向差) 较大的地方萌生 [33] 。残余应力/应变产生的主要原因是焊接和冷加工。需要提到的是,在晶界附近的残余应变等微观结构损伤是分析残余应变分布的一项重要参数 [34] ,这是因为奥氏体合金的SCC裂纹在很多条件下沿晶界扩展。
以上论述了材料因素对SCC行为的影响。材料的微观结构特征并不只是各自独立影响材料的SCC行为,还存在耦合作用。如焊接热影响区中的Σ 3晶界附近会产生较大的残余应变,导致 Σ 3晶界出现较大的偏差角,使其SCC抗性降低 [35] 。
3.2 力学和水化学因素的影响
SCC行为是力学和水化学因素共同作用的结果,力学作用如残余应力和工作应力等可以使材料结构敏感处在一定水化学条件下萌生裂纹,继而裂纹在力学与水化学共同作用下发生扩展。力学作用显著影响 SCC 的萌生和扩展过程。Couvant等 [36] 研究了182合金在模拟一回路水环境下的裂纹萌生敏感性,结果表明,循环加载时SCC的萌生敏感性比恒定加载时高,且温度越低,应力越大,敏感性差距也越大。基于实验所得数据,提出了一种预测裂纹萌生时间的模型。对SCC裂纹扩展的研究 [37,38] 发现,不锈钢的裂纹扩展速率 (CGR) 与应力强度因子 K 呈指数关系。根据实验得到的CGR数据,文献 [39,40] 考虑了裂尖应变率的影响,提出了一个计算不锈钢在氧化性高温高压水中的裂纹扩展速率方程。
服役环境的水化学参数对核电结构材料的腐蚀与SCC行为有着重要影响,如腐蚀电位 (ECP)、溶氢、溶氧、pH值和离子浓度等。研究水化学对SCC行为的影响有助于优化电站水化学参数,抑制SCC的萌生与扩展行为。
腐蚀电位升高,SCC敏感性随之升高。溶氧增加会使腐蚀电位上升,从而增加SCC敏感性。An-dresen [41] 将镍基合金和不锈钢等材料的CGR与ECP关系的实验数据进行了总结,发现在高温高压纯水中,随着腐蚀电位的降低,裂纹扩展速率减小。但对于镍基合金,在腐蚀电位降低到Ni/NiO相转变附近时,裂纹扩展速率出现一个峰值。如图2所示,在288 ℃的纯水中腐蚀电位约为-550 mV时,182合金的裂纹扩展速率比腐蚀电位为-400~-500 mV条件下的提高了约15倍。该现象可能与Ni/NiO相转变附近氧化膜稳定性的变化有关 [42,43] 。关于一回路中溶氢量对镍基合金SCC裂纹萌生和扩展行为的影响,学者已开展了大量的研究 [44~48] 。
溶氢可以影响腐蚀的热力学和动力学过程,从而影响SCC的敏感性。Rocher等 [45] 和Norring [46] 对600合金在330 ℃下,溶氢量13~44 mL/kg之间的SCC萌生敏感性进行了研究,发现溶氢为25 mL/kg时具有最低的裂纹萌生敏感性。西屋公司的研究 [47] 结果也表明330 ℃下,溶氢为25 mL/kg时,SCC抗性最高。
Cassange等 [48] 的研究表明,当温度高于290 ℃,溶氢量非常低 (低于10~20 mL/kg) 时,600合金抗SCC萌生的性能更高。对于裂纹扩展行为,通常认为溶氢对镍基合金SCC裂纹扩展速率的影响与Ni/NiO相转化有关,在与相转化对应的溶氢量附近裂纹扩展速率达到峰值 [41,48] 。例如,Andresen [41] 研究发现,325 ℃条件下,溶氢量为10 mL/kg时182合金裂纹扩展速率最大。溶氢量大于此值时,CGR随着溶氢量上升而下降。
由以上对溶氢量的研究可知,溶氢量对SCC裂纹萌生和扩展影响存在不一致性,因而在实际应用中通过优化溶氢量抑制SCC尚需进一步研究。
一回路水中的H 3 BO 3 和LiOH含量对600合金的SCC临界应力强度因子和裂纹扩展速率 [49,50] 几乎没有影响。而二回路中杂质离子Pb的存在会大大增加600和690合金的SCC倾向,其开裂方式表现为穿晶开裂 [51,52] 。SO 4 2- 和Cl - 在一回路水环境中的存在也会使合金的SCC敏感性上升 [53] 。
图2 裂纹扩展速率与ECP关系
3.3 高温高压水环境腐蚀的影响
高温高压水环境腐蚀在合金表面产生氧化膜。氧化是最基本的腐蚀行为,同时也是SCC的重要过程,氧化膜的结构和成分与SCC裂纹的萌生和扩展过程有着密切的联系 [54] ,因此,分析研究氧化膜的结构与成分有助于揭示氧化过程的机制,进而为阐明SCC的机理提供基础。
目前, 对于不锈钢和镍基合金等主要核电材料在高温高压水环境中产生氧化膜的化学成分和微观结构已进行了大量研究 [55~63] 。结果表明,不锈钢的氧化膜具有双层结构,内层连续致密,对基体金属具有保护作用,而外层为不连续的大颗粒氧化物。
Ziemniak等 [64] 研究了304不锈钢在高温水中的氧化行为,发现材料发生非选择性腐蚀形成了双层氧化膜,外层尖晶石结构氧化物的化学组成具有非化学计量比的特点。文献 [57] 对316不锈钢的氧化膜进行了分析,发现氧化膜内层为致密的富Cr尖晶石结构,外层为疏松的富Fe尖晶石结构,金属和氧化物的界面存在富Ni现象。文献 [58] 对该条件下的氧化行为作了进一步研究,发现氧化膜在氧化1 min时为非晶态,2 min时是纳米晶,5 h之后为单晶态。该文献还研究了应变与氧化的关系:若应变只发生在氧化之前,界面会以晶体学的局部错配形式相适应,界面处的扩散形式为短路扩散;若应变在氧化过程中增加,氧化行为就在应力最大处集中,扰乱钝化层的完整结构,可能导致SCC裂纹的萌生。
对于镍基合金高温高压水中形成的氧化膜的研究结果还存在分歧。多数研究 [65~68] 认为,镍基合金在高温高压水中生成的氧化膜类似于不锈钢的氧化膜,为两层结构,内层富Cr、致密,外层由FeCr尖晶石组成,较为松散。有的学者 [69~71] 则认为生成的氧化膜为3层,除了富Cr的致密内层和具有FeCr尖晶石结构的松散中间层之外,在中间层上还分散分布着零星的大尺寸尖晶石结构的氧化物,这些氧化物构成了最外层氧化膜。
通过研究氧化膜的结构和成分,澄清了氧化过程的机制。内层氧化膜生长是一种固体生长机制,外层的氧化膜是扩散到溶液中的金属离子在基体表面发生的再沉积反应形成的 [55,62] ,属于溶解-沉积机制。
4 SCC机制的理论分析
对于SCC的机理和速率控制步骤,目前进行了许多研究,提出了一些模型,但迄今为止还没有完整而统一的论述。这是因为SCC裂尖处于大块金属中,无法在原子尺度被直接观察到;断裂表面常常被腐蚀,因而无法观察到裂纹尖端的动态变化过程。
SCC裂纹萌生是一种材料表面组织结构、受力情况以及环境因素相互作用的过程。裂纹通常可能在材料的缺陷、晶界以及夹杂物处萌生。如对镍基合金氧化膜的分析认为,晶界处Cr的选择性氧化使O可以向内传输,进而发生沿晶氧化,裂纹萌生。研究中通常将裂纹萌生时间定义为观察到裂纹的时间,或是恒应变时应力松弛到一定量的状态所对应的时间。
对于SCC裂纹扩展机理的研究目前主要提出了滑移氧化-膜破裂模型 [72~74] 、环境耦合断裂模型 [75]和内氧化模型 [76] 等。
滑移氧化-膜破裂模型是被普遍接受的一个模型。该模型认为:在裸露的金属表面形成的氧化层在应变作用下发生破裂,基体金属溶解使裂纹向前推进。随后,裂纹尖端氧化膜逐渐重新形成,导致再钝化,裂纹扩展停止。但在裂尖应变的作用下氧化膜再次发生破裂并不断重复上述过程。据此模型可知,腐蚀和力学作用均促进裂纹扩展。裂纹扩展与氧化膜破裂后暴露在高温高压水介质中裸露金属表面的溶解及钝化过程的电流密度有关。根据滑移氧化-膜破裂模型得到的裂纹扩展速率 ( V t ) 表达式为:
式 中 , M 为 原 子 量 (g/mol); F 为 Faraday 常 数(96500 C/mol); ρ 为金属密度 (g/cm 3 ); Z 为离子价态,2或3; Q f 为参与溶解/氧化过程的电荷密度 (C/cm 2 );ε f 为裂尖氧化膜破裂应变,εct 为裂尖应变率。其中,裂尖应变由蠕变、外加应变或穿过塑性变形区的裂纹扩展产生。
环境耦合断裂模型 [75] 认为:在腐蚀开裂过程中电荷守恒,即裂纹内的电流密度与H的氧化、O的还原以及金属溶解产生的电流密度总和为零。该模型可以解释很多实验中观察到的现象,如溶解氧含量、电导率、应力强度因子等对裂纹扩展速率的影响,并预测了Cl - 在裂尖处的聚集和裂尖环境的酸化。
内氧化模型是针对一回路水环境下镍基合金的SCC而提出的 [77] 。此模型认为在氧通过氧化膜/金属界面向金属晶格中的扩散过程中,由于Cr的活性较高,在靠近界面的部分Cr优先氧化并在其周围导致贫Cr。由于镍基合金在高温高压水中主要生成Cr和Ni的氧化物,而Ni氧化物的结构疏松,难以阻碍O向金属内部扩散,使得上述Cr的优先氧化过程得以重复。
上述这些模型中除滑移氧化-膜破裂模型外,涉及到的参数大部分难以直接测量,为定量计算SCC裂纹扩展速率带来了困难。而基于滑移氧化-膜破裂模型则成功提出了计算 SCC 裂纹扩展速率的公式。
通过对裂纹尖端的观察研究,可以更直观地了解SCC裂纹扩展的机理。Bruemmer等 [78,79] 总结出,不锈钢的裂尖形貌与水化学条件无关,不锈钢裂尖存在与金属基体同取向的氧化膜,其宽度约为数个纳米,存在大量的变形结构如剪切带等,并存在与裂纹交叉的滑移带,这种形貌说明不锈钢的SCC遵循滑移氧化-膜破裂机制。而镍基合金的裂尖形貌明显受水化学条件影响,其在氧化性水中形成的裂尖形貌与不锈钢相似,而在还原性水中的裂尖形貌则显著不同。如600合金的沿晶裂纹尖端区域充满了多孔纳米晶的富Cr氧化物,裂尖前端晶界处由于Cr的选择性氧化产生了疏松的富Ni结构,并且裂尖处不存在明显塑性变形,以上特征表明SCC裂纹的扩展遵循内氧化机制。
5 近期研究热点
5.1 冷加工影响
SCC的机制如前所述,冷加工可以增加材料的屈服强度,进而增加材料的SCC敏感性。近期的研究 [80] 发现,冷加工会在材料中造成应变的不均匀性,尤其会在晶界处产生应变集中,这种应变集中可能是影响IG-SCC敏感性的主要机制。又如,对冷加工程度影响SCC 行为的研究 [81] 结果表明,8%和 20%冷加工的600合金,由于其内部存在晶界的应变集中,晶界与晶内应变梯度较大,晶界处残余应变的集中会导致晶界硬化,进一步促进沿晶开裂行为的发生。40%冷加工的600合金由于其变形量非常大,材料内部残余应变分布均匀,使得沿晶和穿晶开裂共同发生,裂纹扩展速率降低。
5.2 焊接件的SCC
焊接工艺被广泛运用于加工制造核电站中的各种关键构件。在焊接件的焊接接头部位,不可避免地会引入微观结构的缺陷和残余应力等,这些因素都会增加材料SCC的敏感性 [13,82] ,进而影响到核电站的运行安全。其中,又以异种焊接接头的SCC敏感性较高,影响其SCC敏感性的因素除了上述微观结构的缺陷和残余应力之外,还有材料和结构的不均匀性,主要是母材与焊材之间的成分与结构不一致导致微观结构不均匀 [13,83] ;焊接过程中受热分布不均匀使得在熔合线 (FB) 附近存在不均匀的残余应变,导致FB两侧存在机械性能梯度等 [84,85] 。
对于焊接件中SCC裂纹萌生与扩展行为已进行了大量研究。研究 [13,86] 发现,在镍基合金/低合金钢异种焊接件中裂纹在焊接合金内萌生后向焊接熔合线方向扩展,到达熔合线后受到阻碍而停止扩展。但在水中溶氧量较高或添加SO 4 2- ,Cl - 条件下,裂纹可能再启动,穿过FB进入低合金钢基材中继续扩展 [83] 。上述研究主要集中在由焊材内萌生的裂纹扩展的研究,对于母材内萌生的裂纹扩展行为研究较为少见。
6 目前问题与研究趋势
综上所述,研究者为了探究SCC的行为规律与内在机理,采用不同研究方法研究了SCC的萌生和扩展行为,对SCC的材料、力学、环境3个重要影响因素均进行了大量的研究,并提出了SCC的机制与模型,进而通过实验对这些模型进行了验证,取得了较大进展。但仍存在下述问题亟需得到解决。
在实验研究方面,首先对裂纹萌生临界长度的定义还存在争议,而SCC的萌生行为研究目前主要采用加速实验,如何应用裂纹萌生时间这一定量指标评估实际服役条件下的裂纹萌生时间,尚缺乏一种有效的评估方法。另外,采用SSRT和U弯等实验方法无法对裂纹萌生时间进行精确在线监测。
在对压水堆一回路安全端焊接件等的SCC裂纹扩展行为实验研究方面,目前的实验设计都是使裂纹在焊材中萌生后向焊接熔合界面与基材扩展。
而在实际服役条件下,裂纹也可能在基材热影响区中萌生后向焊材扩展。如在Kashiwazaki Kariwa核电站的堆芯围筒中就发现了此种裂纹萌生-扩展方式,这说明需要不断完善相关实验设计。
在SCC机制研究方面,现有研究结果已基本阐明,镍基合金在压水堆一回路水中的SCC行为遵循内氧化机制,而不锈钢在沸水堆中的SCC遵循滑移氧化-膜破裂机制。但目前已开展的研究对某些材料和环境组合条件下的SCC机制尚无定论,如不锈钢在压水堆一回路水环境中的SCC遵循滑移氧化-膜破裂机制还是内氧化机制尚需进一步研究。
为进一步阐明SCC的机制,未来的研究应该在更微观的层次上探究局部腐蚀向裂纹萌生的转变过程和裂纹前沿微纳米尺度上的扩展机制 [87] ,同时,利用实验数据与现场数据建立材料失效数据库,同时建立材料服役行为评价模型,实现对SCC行为的定量评价。另一方面,需要进一步开发缓解、预防SCC的应用性技术手段。通过这些工作,优化核电关键材料及其部件的服役寿命,为保障核电站运行安全提供更可靠的技术基础。
参考文献
[1] Staehle R,Gorman J. Quantitative assessment of submodes of stress corrosion cracking on the secondary side of steam generator tubing in pressurized water reactors: Part 1 [J]. Corrosion, 2003, 59(11): 931-994
[2] Horn R M, Gordon G M, Ford F P, et al. Experience and assessment of stress corrosion cracking in L-grade stainless steel BWR internals[J]. Nucl. Eng. Des., 1997, 174(3): 313-325
[3] Andresen P L, Ford F P, Solomon H D, et al. Monitoring and modeling stress-corrosion and corrosion fatigue damage in nuclear-reactors[J]. JOM-J. Min. Met. Mat. Soc., 1990, 42(12): 7-11
[4] Bamford W, Hall J. Cracking of alloy 600 nozzles and welds in PWRs: review of cracking events and repair service experience [A]. Proceedings of 12th International Conference on Environmental Degradation of Materials in Nuclear Power Systems Water Reactors [C]. Warrendale, PA: TMS, 2005: 959-966
[5] Zinkle S J, Was G S. Materials challenges in nuclear energy[J]. Acta Mater., 2013, 61(3): 735-758
[6] EPRI. Steam Generator Progress Report [M]. Palo Alto, CA: Electric Power Research Institute, 2011
[7] Crum J R, Nagashima T. Review of Alloy 690 Steam Generator Studies [M]. LaGrange Park: American Nuclear Society, 1997
[8] Hwang S S, Kim H P, Lee D H, et al. The mode of stress corrosion cracking in Ni-base alloys in high temperature water containing lead[J]. J. Nucl. Mater., 1999, 275(1): 28-36
[9] Peng Q J, Teysseyre S, Andresen P L, et al. Stress corrosion crack growth in type 316 stainless steel in supercritical water[J]. Corrosion, 2007, 63(11): 1033-1041
[10] Andresen P L, Emigh P W, Morra M M, et al. Effects of PWR primary water chemistry and deaerated water on SCC [A]. Proceedings of the 12th International Conference on Environmental Degradation of Materials in Nuclear Power Systems Water Reactors [C]. Houston, TX: NACE, 2005: 989-1008
[11] Andersen P L, Morra M M, Hickling J, et al. PWSCC of alloys 690, 52 and 152 [A]. Proceedings of the 13th International Conference on Environmental Degradation of Materials in Nuclear Power Systems Water Reactors [C]. Toronto: CNS, 2007
[12] Ritter S, Seifert H P. Effect of corrosion potential on the corrosion fatigue crack growth behaviour of low-alloy steels in high-temperature water[J]. J. Nucl. Mater., 2008, 375(1): 72-79
[13] Seifert H P, Ritter S, Shoji T, et al. Environmentally-assisted cracking behaviour in the transition region of an alloy182/SA 508 Cl.2 dissimilar metal weld joint in simulated boiling water reactor normal water chemistry environment[J]. J. Nucl. Mater., 2008, 378(2): 197-210
[14] Was G S, Sung J K, Angeliu T M. Effects of grain-boundary chemistry on the intergranular cracking behavior of Ni-16Cr-9Fe in high-temperature water[J]. Metall. Mater. Trans., 1992, 23(12)A: 3343-3359
[15] Was G S, Rajan V B. The mechanism of intergranular cracking of Ni-Cr-Fe alloys in sodium tetrathionate[J]. Metall. Mater. Trans., 1987, 18(7)A: 1313-1323
[16] Bruemmer S M. Linking grain boundary structure and composition to intergranular stress corrosion cracking of austenitic stainless steels[A]. Materials Research Society Symposium Proceedings [C]. Warrendale, PA: Materials Research Society; 2004: 101-110
[17] Bruemmer S M, Was G S. Microstructural and microchemical mechanisms controlling intergranular stress-corrosion cracking in light-water-reactor systems[J]. J. Nucl. Mater., 1994, 216: 348-363
[18] Peng Q J, Yamauchi H, Shoji T. Investigation of dendrite-boundary microchemistry in alloy 182 using auger electron spectroscopy analysis[J]. Metall. Mater. Trans., 2003, 34(9)A: 1891-1899
[19] Was G S, Lian K. Role of carbides in stress corrosion cracking resistance of alloy 600 and controlled-purity Ni-16%Cr-9%Fe in primary water at 360 ℃[J]. Corrosion, 1998, 54: 675-688
[20] Leonard F,Cottis R A,Vaillant F,et al. Mechanistic studies of stress corrosion cracking of nickel-based alloys in high temperature high pressure PWR environment [A]. Proceedings of the 14th International Conference on Environmental Degradation of Materials in Nuclear Power Systems Water Reactors [C]. LaGrange Park, IL: American Nuclear Society, 2009: 45-54
[21] Peng Q J, Hou J, Takeda Y, et al. Effect of chemical composition on grain boundary microchemistry and stress corrosion cracking in alloy 182[J]. Corros. Sci., 2013, 67: 91-99
[22] Bruemmer S M, Charlot L A, Henager C H. Microstructure and microdeformation effects on IGSCC of alloy-600 steam-generator tubing[J]. Corrosion, 1988, 44(11): 782-788
[23] Kozaczek K J, Sinharoy A, Ruud C O, et al. Micromechanical modelling of microstress fields around carbide precipitates in alloy 600[J]. Model Simul. Mater. Sci., 1995, 3(6): 829-843
[24] Randle V. The coincidence site lattice and the 'sigma enigma'[J]. Mater. Charact., 2001, 47(5): 411-416
[25] Lin P, Palumbo G, Erb U, et al. Influence of grain-boundary-character-distribution on sensitization and intergranular corrosion of alloy-600[J]. Scr. Mater., 1995, 33(9): 1387-1392
[26] Randle V. Electron backscatter diffraction: strategies for reliable data acquisition and processing[J]. Mater. Charact., 2009, 60(9): 913-922
[27] Gertsman V Y, Bruemmer S M. Study of grain boundary character along intergranular stress corrosion crack paths in austenitic alloys[J]. Acta Mater., 2001, 49(9): 1589-1598
[28] Lehockey E M, Brennenstuhl A M, Thompson I. On the relationship between grain boundary connectivity, coincident site lattice boundaries and intergranular stress corrosion cracking[J]. Corros. Sci., 2004, 46: 2383-2404
[29] Kumar M, King W E, Schwartz A J. Modifications to the microstructural topology in F.C.C. materials through thermomechanical processing[J]. Acta Mater., 2000, 48(9): 2081-2091
[30] Terachi T, Yamada T, Miyamoto T, et al. SCC growth behaviors of austenitic stainless steels in simulated PWR primary water[J]. J. Nucl. Mater., 2012, 426(1-3): 59-70
[31] Jiao Z, Was G S. Impact of localized deformation on IASCC in austenitic stainless steels[J]. J. Nucl. Mater., 2011, 408(3): 246-256
[32] Couvant T, Moulart P, Legras L, et al. Effect of strain-hardening on stress corrosion cracking of AISI 304Lstainless steel in PWR environment at 360 degree [A]. Proceedings of the 12th International Conference on Environmental Degradation of Materials in Nuclear Power Systems Water Reactors [C]. Warrendale, PA: TMS, 2005: 1069-1079
[33] Kamaya M. Influence of bulk damage on crack initiation in low-cycle fatigue of 316 stainless steel[J]. Fatigue Fract. Eng. Mater. Struc., 2010, 33(2): 94-104
[34] Couvant T, Legras L, Pokor C, et al. Investigations on the mechanisms of PWSCC of strain hardened austenitic stainless steels [A]. Proceedings of the 13th International Conference on Environmental Degradation of Materials in Nuclear Power Systems [C]. Toronto, CN: CNS, 2007: 1-16
[35] Hou J, Shoji T, Lu Z P, et al. Residual strain measurement and grain boundary characterization in the heat-affected zone of a weld joint between alloy 690TT and alloy 52 [J]. J. Nucl. Mater., 2010, 397(1-3): 109-115
[36] Couvant T, Vaillant F. Initiation of PWSCC of weld alloy 182 [A]. Proceedings of the 15th International Conference on Environmental Degradation of Materials in Nuclear Power Systems Water Reactors [C]. Warrendale, PA: TMS, 2011: 1141-1151
[37] Andresen P L, Ford F P. Fundamental modeling of environmental cracking for improved design and lifetime evaluation in BWRs[J]. Int. J. Pres. Ves. Pip., 1994, 59(1-3): 61-70
[38] Andresen P L, Ford F P. Life prediction by mechanistic modeling and system monitoring of environmental cracking of iron and nickel-alloys in aqueous systems[J]. Mater. Sci. Eng., 1988, A103(1): 167-184
[39] Peng Q J, Kwon J, Shoji T. Development of a fundamental crack tip strain rate equation and its application to quantitative prediction of stress corrosion cracking of stainless steels in high temperature oxygenated water[J]. J. Nucl. Mater., 2004, 324(1): 52-61
[40] Shoji T, Lu Z, Murakami H. Formulating stress corrosion cracking growth rates by combination of crack tip mechanics and crack tip oxidation kinetics[J]. Corros. Sci., 2010, 52(3): 769-779
[41] Andresen P L, Reid R, Wilson J. SCC mitigration of Ni alloys and weld metals by op-timizing dissolved hydrogen [A]. Proceedings of the 14th Internati-onal Conference on Environmental Degradation of Materials in Nuclear Power Systems Water Reactors [C]. Warrendale, PA: TMS, 2009: 345-372
[42] Peng Q, Hou J, Sakaguchi K, et al. Effect of dissolved hydrogen on corrosion of inconel alloy 600 in high temperature hydrogenated water[J]. Electrochim. Acta, 2011, 56(24): 8375-8386
[43] Combrade P, Scott P, Foucault M, et al. Oxidation of Ni base alloys in PWR water oxide layers and associated damage to the base metal [A]. Proceedings of the 12th International Conference on Environmental Degradation of Materials in Nuclear Power System Water Reactors [C]. Warrendale, PA: TMS, 2005: 883-890
[44] Meng F, Lu Z, Shoji T, et al. Stress corrosion cracking of uni-directionally cold worked 316NG stainless steel in simulated PWR primary water with various dissolved hydrogen concentrations[J]. Corros. Sci., 2011, 53(8): 2558-2565
[45] Rocher A, Cassagne T, Durbec V, et al. The influence of chemical factors on the initiation of primary side IG-SCC in alloy 600 steam generator tubing [A]. Colloque International [C]. Fontevraud, 1994: 337-346
[46] Norring K. Influence of LiOH and H2 on Primary side IGSCC of Alloy 600 Steam Generator Tubes [M]. Studsvik AB: Studsvik Energy, 1990
[47] Jacko R, Economy G, Pement F. The influence of dissolved hydrogen on primary water stress corrosion cracking of alloy 600 at PWR steam generator operating temperatures [A]. Proceedings of the 5th International Conference on Environmental Degradation of Materials in Nuclear Power Systems-Water Reactors [C]. LaGrange Park, IL: American Nuclear Society, 1992: 613-620
[48] Cassange T, Fleury S, Vaillant F, et al. An update on the influence of hydrogen on the PWSCC of nickel base alloys in high temperature water [A]. Proceedings of the 9th International Conference on Environmental Degradation of Materials in Nuclear Power Systems Water Reactors [C]. LaGrange Park, IL: American Nuclear Society, 1997: 307-315
[49] Rebak R B,Szklarskasmialowska Z. Influence of stress intensity and loading mode on IASCC of alloy 600 in primary water of pressurized water reactors [J]. Corrosion, 1994, 50(5): 378-393
[50] Andresen P L, Hickling J, Ahluwalia A, et al. Effects of hydrogen on stress corrosion crack growth rate of nickel alloys in high-temperature water[J]. Corrosion, 2008, 64(9): 707-720
[51] Hwang S S, Kim H P, Lim Y S, et al. Transgranular SCC mechanism of thermally treated alloy 600 in alkaline water containing lead[J]. Corros. Sci., 2007, 49(10): 3797-3811
[52] Agrawal A K, Paine J P N. Lead cracking of alloy 600-a review [A]. Proceedings of the 4th International Conference on Environmental Degradation of Materials in Nuclear Power Systems Water Reactors [C]. Houston, TX: NACE, 1989: 7-1-7-17
[53] Yang I J. Effect of sulphate and chloride ions on the crevice chemistry and stress corrosion cracking of alloy 600 in high temperature aqueous solutions[J]. Corros. Sci., 1992, 33(1): 25-37
[54] Lu Y H, Peng Q J, Sato T, et al. An ATEM study of oxidation behavior of SCC crack tips in 304L stainless steel in high temperature oxygenated water[J]. J. Nucl. Mater., 2005, 347(1/2): 52-68
[55] Stellwag B. The mechanism of oxide film formation on austenitic stainless steels in high temperature water[J]. Corros. Sci., 1998, 40(2/3): 337-370
[56] Wang S C, Takeda Y, Shoji T, et al. Observation of the oxide film formed in high temperature water by applying electroless Ni-P coating[J]. J. Nucl. Sci. Technol., 2004, 41(7): 777-779
[57] Terachi T, Fujii K, Arioka K. Microstructural characterization of SCC crack tip and oxide film for SUS 316 stainless steel in simulated PWR primary water at 320 ℃[J]. J. Nucl. Sci. Technol., 2005, 42(2): 225-232
[58] Soulas R, Cheynet M, Rauch E, et al. TEM investigations of the oxide layers formed on a 316L alloy in simulated PWR environment[J]. J. Mater. Sci., 2013, 48(7): 2861-2871
[59] Kuang W J, Wu X Q, Han E-H. Influence of dissolved oxygen concentration on the oxide film formed on 304 stainless steel in high temperature water[J]. Corros. Sci., 2012, 63: 259-266
[60] Kuang W J, Han E-H, Wu X Q, et al. Microstructural characteristics of the oxide scale formed on 304 stainless steel in oxygenated high temperature water[J]. Corros. Sci., 2010, 52(11): 3654-3660
[61] Kuang W J, Wu X Q, Han E-H. The oxidation behaviour of 304 stainless steel in oxygenated high temperature water[J]. Corros. Sci., 2010, 52(12): 4081-4087
[62] Li X H, Wang J Q, Han E-H, et al. Corrosion behaviour for alloy 690 and alloy 800 tubes in simulated primary water[J]. Corros. Sci., 2013, 67: 169-178
[63] Liu X H, Wu X Q, Han E-H. Influence of Zn injection on characteristics of oxide film on 304 stainless steel in borated and lithiated high temperature water[J]. Corros. Sci., 2011, 53(10): 3337-3345
[64] Ziemniak S E, Hanson M. Corrosion behavior of 304 stainless steel in high temperature, hydrogenated water[J]. Corros. Sci., 2002, 44(10): 2209-2230
[65] Neves C F C, Alvial G M, Schvartzman M M A, et al. Characterisation of oxide films formed on alloy 600 in simulated PWR primary water[J]. Energ. Mat., 2008, 3(2): 126-131
[66] Liu J H, Mendonca R, Bosch R W, et al. Characterization of oxide films formed on alloy 182 in simulated PWR primary water[J]. J. Nucl. Mater., 2009, 393(2): 242-248
[67] Machet A, Galtayries A, Marcus P, et al. XPS study of oxides formed on nickel-base alloys in high-temperature and high-pressure water[J]. Surf. Interface Anal., 2002, 34(1): 197-200
[68] Machet A, Galtayries A, Zanna S, et al. XPS and STM study of the growth and structure of passive films in high temperature water on a nickel-base alloy[J]. Electrochim. Acta, 2004, 49(22/23): 3957-3964
[69] Panter J, Viguier B, Cloue J M, et al. Influence of oxide films on primary water stress corrosion cracking initiation of alloy 600[J]. J. Nucl. Mater., 2006, 348(1/2): 213-221
[70] Zhang Z M, Wang J Q, Han E-H, et al. Influence of dissolved oxygen on oxide films of alloy 690TT with different surface status in simulated primary water[J]. Corros. Sci., 2011, 53(11): 3623-3635
[71] Huang F, Wang J, Han E-H, et al. Microstructural characteristics of the oxide films formed on alloy 690 in pure and primary water at 325 ℃[J]. Corros. Sci., 2013, 76: 52-59
[72] Vermilye D A. A theory for propagation of stress-corrosion cracks in metals[J]. J. Electrochem. Soc., 1972, 119(4): 405-407
[73] Turnbull A. Modeling of environment assisted cracking[J]. Corros. Sci., 1993, 34(6): 921-960
[74] Ford F P. Quantitative prediction of environmentally assisted cracking[J]. Corrosion, 1996, 52(5): 375-395
[75] Macdonald D D, Urquid-Macdonald M. A coupled environment model for stress-corrosion cracking in sensitized type-304 stainless-steel in LWR environments[J]. Corros. Sci., 1991, 32(1): 51-81
[76] Rebak R B, Szklarskasmialowska Z. The mechanism of stress corrosion cracking of alloy 600 in high temperature water[J]. Corros. Sci., 1996, 38(6): 971-988
[77] Scenini F, Newman R C, Cottis R A, et al. Alloy oxidation studies related to PWSCC [A]. Proceedings of the 12th International Conference on Environmental Degradation of Materials in Nuclear Power System Water Reactors [C]. Warrendale, PA: TMS, 2005: 891-902
[78] Bruemmer S M, Thomas L E. Insights into Environmental Degradation Mechanisms from High-Resolution Characterization of Crack Tips [M]. Warrendale: Minerals, Metals & Materials Society, 2001
[79] Bruemmer S M,Thomas L. Insights into stress corrosion cracking mechanisms from high-resolution measurements of crack-tip structures and compositions [A]. MRS Proceedings [C]. Cambridge University Press, 2010: 1264-BB01-09
[80] Kamaya M, Haruna T. Influence of local stress on initiation behavior of stress corrosion cracking for sensitized 304 stainless steel[J]. Corros. Sci., 2007, 49(8): 3303-3324
[81] Hou J, Peng Q J, Lu Z P, et al. Effects of cold working degrees on grain boundary characters and strain concentration at grain boundaries in alloy 600[J]. Corros. Sci., 2011, 53(3): 1137-1142
[82] Lu B T, Chen Z K, Luo J L, et al. Pitting and stress corrosion cracking behavior in welded austenitic stainless steel[J]. Electrochim. Acta, 2005, 50(6): 1391-1403
[83] Peng Q J, Shoji T, Ritter S, et al. SCC behaviour in the transition region of an alloy 182-SA 508 Cl.2 dissimilar weld joint under simulated BWR-NWC conditions [A]. Proceedings of the 12th International Conference on Environmental Degradation of Materials in Nuclear Power Systems Water Reactors [C]. Warrendale, PA: TMS, 2005: 589-599
[84] Kim J W, Lee K, Kim J S, et al. Local mechanical properties of alloy 82/182 dissimilar weld joint between SA508 Gr.1a and F316 SS at RT and 320 ℃[J]. J. Nucl. Mater., 2009, 384(3): 212-221
[85] Lee H T, Wu J L. Correlation between corrosion resistance properties and thermal cycles experienced by gas tungsten arc welding and laser beam welding alloy 690 butt weldments[J]. Corros. Sci., 2009, 51(4): 733-743
[86] Peng Q J, Xue H, Hou J, et al. Role of water chemistry and microstructure in stress corrosion cracking in the fusion boundary region of an alloy 182-A533Blow alloy steel dissimilar weld joint in high temperature water[J]. Corros. Sci., 2011, 53(12): 4309-4317
[87] Han E-H. Research trends on micro and nano-scale materials degradation in nuclear power plant[J]. Acta Metall. Sin., 2011, 47(7): 769-776
[87] (韩恩厚. 核电站关键材料在微纳米尺度上的环境损伤行为研究—进展与趋势[J]. 金属学报, 2011, 47(7): 769-776)
免责声明:本网站所转载的文字、图片与视频资料版权归原创作者所有,如果涉及侵权,请第一时间联系本网删除。
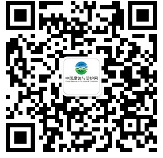
官方微信
《中国腐蚀与防护网电子期刊》征订启事
- 投稿联系:编辑部
- 电话:010-62316606-806
- 邮箱:fsfhzy666@163.com
- 中国腐蚀与防护网官方QQ群:140808414