摘要
研究了喷丸与未喷丸处理的Super304H钢在650 ℃/27 MPa的超临界蒸汽中的氧化行为。氧化1000和2000 h后,用金相显微镜 (OM)、扫描电镜 (SEM) 及能谱仪 (EDS) 分析氧化膜表面及横截面形貌、微观结构和元素分布,用X射线衍射仪 (XRD) 对氧化膜物相进行表征。结果表明:喷丸处理试样的抗蒸汽氧化性能要远优于未喷丸的试样,喷丸处理可显著提高Super304H钢的抗蒸汽氧化性能并提高表面氧化膜的抗剥落性能。对Super304H钢施以喷丸处理,可使材料表面晶粒细化,引入的晶界、亚晶界和位错等缺陷,加速Cr原子在高温氧化过程中向表面扩散,促进材料表面致密富Cr氧化层 (Cr2O3) 的形成和生长。
关键词: Super304H ; 蒸汽氧化 ; 喷丸 ; 显微分析
Super304H 钢是在 ASME SA213 TP304H 基础上发展起来的一种新型细晶粒耐热钢,该钢通过降低Mn含量上限,加入约3% (质量分数) 的Cu、0.45%Nb和微量的N,使其在服役运行时产生细小弥散Nb (C,N)和沉淀于奥氏体内的富铜相,从而达到高温强度、高温塑性及抗高温氧化的最佳组合。由于其高温许用应力大,在锅炉上应用时比目前国内大量使用的TP347H钢成本约低40%,其组织和力学性能稳定,是超超临界 (USC) 锅炉高温部件的重要候选材料之一。在超超临界工况下,材料高温蒸汽氧化问题变得严重,导致机组失效,材料的最高使用温度也受到限制。据相关文献报道,在超 (超) 临界工况下,Super304H氧化膜的外层容易发生剥落,氧化膜的剥落会威胁机组的安全运行。为了进一步提高材料的抗水蒸汽氧化性能,可对Super304H钢管进行内壁喷丸处理。
喷丸处理能在材料表面引入压应力、提高表面硬度,从而延长材料结构的疲劳寿命和提高抗应力腐蚀性能。利用喷丸提高奥氏体钢的抗氧化性能已在工程上得到运用[5,6,7,8,9],但超超临界工况下,喷丸处理对材料的蒸汽氧化性能影响的机理尚需要研究。本文运用自制的超 (超) 临界水蒸汽氧化试验装置,对喷丸和未喷丸处理Super304H钢在650 ℃/27 MPa的蒸汽中进行氧化实验,以研究喷丸处理对Super304H钢蒸汽氧化行为的影响。
1 实验方法
实验用Super304H耐热钢的化学成分 (质量分数,%) 为:C 0.08,Mn 0.78,Si 0.25,Cr 18.66,Ni 8.64,Nb 0.5,Cu 2.91,Fe余量。试样取自外径50.5 mm,壁厚8.5 mm的钢管。采用0.5 MPa的喷丸压力,采用线切割取包含内壁曲面的喷丸和未喷丸瓦片状试样,见示意图1。喷丸和未喷丸瓦片状试样 (内壁) 曲面不做任何处理,其它5个平面都经2.5 μm金刚石抛光膏进行抛光,所有试样在无水乙醇中进行超声清洗并烘干。
水蒸汽氧化实验在自制的超 (超) 临界水蒸汽氧化试验装置中进行。为模拟锅炉传热管内的蒸汽介质,采用去离子水并通入氩气除氧,水蒸汽的含氧量小于100 μg/L,水的蒸发量为2×10-3 m3/h,蒸汽参数为650 ℃/27 MPa,实验时间为1000和2000 h。实验完成后,用光学显微镜 (OM)、扫描电镜 (SEM,S-3400N),电子背散射衍射仪 (EBSD,Bruker e-Flash) 及能谱仪 (EDS,QUANTAX 200-10) 分析氧化膜表面及截面形貌、微观结构和元素分布,用X射线衍射仪 (XRD,D8 Advance) 分析氧化物的物相组成。
2 结果与讨论
2.1 氧化膜表面形貌观察与分析
氧化膜表面形貌见图2。可知,未喷丸的Super304H钢氧化1000 h时,表面形成结晶状氧化物,氧化物沿不同的方向生长,生成取向不同的多角状氧化膜晶粒;而氧化2000 h时,表面氧化膜形貌发生了较大的变化,氧化膜演变为团簇颗粒状,并且局部氧化膜发生了剥落;EDS分析表明,Super304H钢仅发生了外层富Fe氧化膜的剥落,而内层富Cr氧化膜并未剥落,见表1。相比而言,喷丸的Super304H钢试样氧化到2000 h,表面未形成明显的结晶状氧化物,氧化物的颗粒非常细小,并且喷丸过程造成的表面“涟波”或“折叠”仍然可见。EDS分析表明,喷丸试样表面形成了富Cr的氧化物,并且随着氧化时间的延长 (从1000 h到2000 h),表面氧化物中Cr的含量有所升高,可以推测喷丸的Super304H钢试样氧化膜的保护性能在一段时间内随着时间的延长而增加。
表1 未喷丸和经喷丸处理的Super304H耐热钢氧化不同时间后表面氧化物主要元素分布
对氧化2000 h的Super304H钢喷丸与未喷丸试样表面氧化膜进一步观察 (图3) 可见,喷丸试样表面“涟波”或“折叠”处边缘形成较大的氧化膜颗粒,而其它区域氧化膜颗粒保持细小的尺寸,其颗粒尺寸小于3 μm,见图3a和b。而未喷丸试样表面氧化物颗粒粗大,氧化膜颗粒表面有较多的细小孔洞,氧化膜剥落处也观察到较多细小的孔洞。据文献报道,这种氧化膜中的细小孔洞会成为氧和水分子的快速扩散通道,孔洞的存在会促进氧在氧化膜中扩散。
2.2 氧化膜横截面形貌观察与分析
氧化后的Super304H钢试样横截面形貌见图4。可知,未喷丸的Super304H钢试样表面形成了较厚的氧化膜,同时可以观察到氧化膜外层有较多的孔洞,比较疏松;氧化膜与金属基体的界面高低起伏,原因是氧化膜沿着晶界的生长速率与沿着晶内的不同。而喷丸处理的Super304H钢表面形成了很薄的氧化膜,厚度仅仅几个微米,并且原始喷丸处理造成的“波浪”状特征依然清晰可见。
图5为喷丸与未喷丸Super304H钢试样氧化2000 h时氧化膜横截面形貌以及对应的元素分布。元素线扫描结果表明,氧化膜分为两层,靠近蒸汽侧的氧化膜 (外层氧化膜) 富含Fe,而靠近金属基体的氧化膜 (内层氧化膜) 富含Cr和Ni;两层氧化膜的界面上Fe和Cr含量出现突变,O在内外层氧化膜中分布比较均匀,见图5a。相比之下,喷丸试样只形成了富Cr的氧化膜薄层。
氧化膜中各元素的面分布情况见图6。可知,未喷丸Super304H钢试样氧化膜外层主要是Fe的氧化物,而氧化膜内层富含Cr和Ni,条带状的富Cr氧化层与金属表面平行,富Cr氧化层与金属基体之间存在局部的贫Cr区域;Ni的面分布结果显示,其在内氧化层中局部富集,而不是均匀分布在内氧化层中。从喷丸试样氧化层元素面分布情况来看,喷丸的Super304H钢试样蒸汽侧只形成了很薄的富Cr氧化层,这种富Cr的薄氧化层具有很好的保护性,能有效的减少金属基体的氧化。
2.3 XRD分析
对氧化后的喷丸与未喷丸的Super304H钢进行XRD分析,结果表明:喷丸试样氧化后形成的氧化物包括Cr2O3 和Fe2O3,见图7a和b;而未喷丸的试样形成的氧化物包括Fe2O3、Fe3O4、(Fe,Cr)3O4和 Cr2O3,见图7c和d。结合元素分布曲线和元素面分布的分析结果可知,喷丸试样表面形成的氧化物为Cr2O3 和Fe2O3,氧化物未发生明显的分层,而未喷丸试样氧化物分为两层,外层为Fe2O3和Fe3O4,内层为 (Fe,Cr)3O4和Cr2O3。
3 讨论
3.1 喷丸对Super304H钢组织与性能的影响
经喷丸处理后,Super304H钢近表面会引入喷丸变形层,表层组织会发生变化,硬度的变化能够很好地表征喷丸前后组织的差异。喷丸表面硬度为422 HV,未喷丸表面的硬度为203 HV,喷丸区域表面的硬度要远大于未喷丸区域表面的硬度,这表明喷丸表面发生了形变强化。
喷丸的Super304H钢试样经过磨抛和腐蚀后,在金相显微镜下观察喷丸变形层,见图8。可知,喷丸处理后试样的组织可分为3个不同区域,喷丸表面 (见图Ⅰ区) 的晶粒细小,平均晶粒尺寸约为3 μm,此区域为喷丸主要影响区;近喷丸表面区 (Ⅱ区) 晶粒大小不均,平均晶粒尺寸约为10 μm,此区域为喷丸次主要影响区;而远离喷丸表面区域的组织受喷丸影响很小,晶粒尺寸未发生明显变化,代表未受喷丸影响的基体区域 (Ⅲ区),此区域平均晶粒尺寸为40 μm。
3.2 喷丸处理对Super304H钢抗蒸汽氧化性能的影响
喷丸处理能够有效提高Super304H钢的抗蒸汽氧化性能,这种作用主要源于喷丸处理显着细化了材料表面的晶粒 (图8),从而增加了晶界的体积分数。晶界数量的增加引入更多的快速扩散通道,这有利于氧化初期富Cr氧化物的形核和生长。晶界数量的增加使得有效的形核位置增多,减少了形成连续富Cr氧化物所需的时间,Cr的快速扩散保证了富Cr氧化层的稳态生长。实际上,未喷丸试样表面不易形成致密的富Cr氧化物,主要原因包括两个方面:一是氧化过程中未喷丸试样表面的Cr扩散速率相对较低;二是维持富Cr氧化膜生长的Cr难以从基体中得到补充。结果导致基体中大量的Fe与O发生反应生成Fe氧化物,最终形成的氧化物为双层结构,包括Fe2O3,Fe3O4,(Fe,Cr)3O4和Cr2O3 4种物相,这与文献中的研究结果一致。
喷丸处理使Super304H钢试样表面引入了晶界、亚晶界和位错等缺陷[15],试样表面晶粒得到细化,这增加了Cr的扩散路径和扩散速率,减小了合金形成富Cr氧化层所需Cr含量,在氧化初期促进试样表面优先形成细小致密的Cr2O3氧化物,Cr2O3氧化物的快速横向生长最终形成致密的Cr2O3氧化层。喷丸试样表面Cr的扩散遵循Fick定律,试样表面Cr的扩散系数用有效扩散系数Deff来表征。此时Deff为晶界扩散系数DGB和晶内扩散系数DL的加权平均值,如下式:
式中,a为晶界的体积分数,b为晶内的体积分数,因此a+b=1。
对于未喷丸试样,a+b,有效扩散系数Deff≈DL。而对于喷丸试样,Deff≈DL,原因是喷丸处理后试样表面晶粒细化,产生大量的晶界。
据此认为,在蒸汽氧化过程中,Cr主要通过晶内向未喷丸试样表面扩散;而喷丸后合金近表面区域Cr通过晶界和界内向试样表面扩散,且晶界扩散远快于晶内扩散。基于Cr在晶界和晶格内的扩散方程,Cr在晶界和晶格内扩散的质量流量的关系如下:
式中,jL和jGB分别为Cr通过晶内和晶界的扩散通量,dCdxdCdx为Cr的浓度梯度,Cb和Cs为Cr的基体浓度和表面浓度,t为氧化时间,δ为晶界宽度 (一般为0.5 nm),ds为试样表面的晶粒尺寸,mtLmLt和mtGBmGBt分别为单位时间内通过晶内与晶界的质量流量。Cr在晶内与在晶界的扩散系数见图9。Cr的质量流量比mtGB/mtLmGBt/mLt和mtGB/(mtL+mtGB)mGBt/mLt+mGBt与试样表面晶粒尺寸的关系见图10。经喷丸处理后,Super304H钢试样表面的晶粒尺寸由40 μm细化到3 μm,Cr通过晶界扩散的质量流量与Cr通过晶内扩散的质量流量之比mtGB/mtLmGBt/mLt从0.05增加到0.65,而Cr通过晶界扩散的质量流量占总的扩散质量流量分数mtGB/(mtL+mtGB)mGBt/mLt+mGBt从4.68%增加到39.56%。晶粒细化产生的大量晶界可显着提高Cr的扩散,极大地促进了喷丸试样表面富Cr氧化物的形成。
因此对Super304H钢试样表面进行喷丸处理,可显着促进Cr原子在高温氧化过程中向表面加速扩散,促进试样表面形成致密的富Cr氧化膜。这种富Cr氧化物与基体紧密结合,并且其热膨胀系数与母材接近 (见图11),因此富Cr氧化膜 (Cr2O3) 具有很好的抗剥落性能。此外,喷丸处理可以有效去除管子内表面的原始氧化膜,特别是最外层的纯铁氧化物,降低了水蒸汽分解触媒效应,减小基体金属的氧化。
4 结论
(1) 喷丸处理的Super304H钢蒸汽氧化后表面形成的氧化膜的厚度显着减小,仅为未喷丸试样的1/30。喷丸试样表面形成单层致密的富Cr氧化物,而未喷丸试样表面形成了外层富Fe而内层富Cr的双层结构氧化膜。
(2) 喷丸处理使得Super304H钢试样表面晶粒得到细化,大量晶界的产生促进Cr向试样表面扩散,使表面形成致密的富Cr的氧化膜,明显阻止了Fe向外的扩散,抑制了Fe氧化物的生成,使Super304H钢在蒸汽中的抗氧化性能显着提高,同时也提高了氧化膜的抗剥落性能。
参考文献
[1] Yang Y, Cheng S C, Yang G. Present situation of exploiting and research of Super304H steel for boiler [J]. Special Steel, 2002, 23(1): 27
[1] (杨岩, 程世长, 杨钢. Super304H锅炉钢的开发和研究现状 [J]. 特殊钢, 2002, 23(1): 27)
[2] Ma Y H. The study of high temperature steam oxidation of steel used in (Ultra) supercritical boilers [D]. Shanghai: Shanghai Power Equipment Research Institute, 2013
[2] (马云海. 超(超)临界锅炉用钢高温蒸汽氧化研究 [D]. 上海: 上海发电设备成套设计研究院, 2013)
[3] Haga S, Harada Y, Tsubakino H. Fatigue life prolongation of carburized steel by means of shot-peening [J]. Mater. Sci. Forum, 2006, 505-507: 775
[4] Zoeller H W, Cohen B. Shot peening for resistance to stress-corrosion cracking [R]. AMS Technical Report No. D5-20.1, 1965
[5] Li X G, He J W. Effect of shot blasting on oxidation behavior of TP304H steel at 610~770 ℃ in water vapor [J]. Mater. Lett., 2006, 60: 339
[6] Sato T, Fukuda Y, Mitsuhata K, et al. The practical application and long-term experience of new heat resistant steels to large scale USC boilers [A]. Proceedings from the Fourth International Conference on Advances in Materials Technology for Fossil Power Plants [C]. Hilton Head Island, South Carolina, 2004: 177
[7] Minami Y, Tooyama A, Seki M, et al. Steam-oxidation resistance of shot blasted stainless steel tubing after 10-year service [J]. NKK Tech. Rev., 1996, 75: 1
[8] Liang Z, Zhao Q, Singh P M, et al. Field studies of steam oxidation behavior of austenitic heat-resistant steel 10Cr18Ni9Cu3NbN [J]. Eng. Fail. Anal., 2015, 53: 132
[9] Warzee M, Hennaut J, Maurice M, et al. Effect of surface treatment on the corrosion of stainless steels in high-temperature water and steam [J]. J. Electrochem. Soc., 1965, 112: 670
[10] Shen J N, Zhou L J, Li T F. High-temperature oxidation of Fe-Cr alloys in wet oxygen [J]. Oxid. Met., 1997, 48: 347
[11] Wright I G, Tortorelli P F, Schütze M. Program on technology innovation: oxide growth and exfoliation on alloys exposed to steam [R]. Palo Alto, CA: Electric Power Institute, 2007
[12] Yuan J T, Wu X M, Wang W, et al. The effect of surface finish on the scaling behavior of stainless steel in steam and supercritical water [J]. Oxid. Met., 2013, 79: 541
[13] Holcomb G R. High pressure steam oxidation of alloys for advanced ultra-supercritical conditions [J]. Oxid. Met., 2014, 82: 271
[14] Ostwald C, Grabke H J. Initial oxidation and chromium diffusion. I. Effects of surface working on 9~20% Cr steels [J]. Corros. Sci., 2004, 46: 1113
[15] Naraparaju R, Christ H J, Renner F U, et al. Effect of shot-peening on the oxidation behaviour of boiler steels [J]. Oxid. Met., 2011, 76: 233
[16] Proy M, Utrilla M V, Otero E, et al. Effects of grit blasting and annealing on the high-temperature oxidation behavior of austenitic and ferritic Fe-Cr alloys [J]. J. Mater. Eng. Perform., 2014, 23(8):2847
[17] Alyousif O M, Engelberg D L, Marrow T J. Surface grain boundary engineering of shot-peened type 304 stainless steel [J]. J. Mater. Sci., 2008, 43: 1270
[18] Crank J. The Mathematics of Diffusion [M]. Oxford: Oxford University Press, 1956
[19] Fisher J C. Calculation of diffusion penetration curves for surface and grain boundary diffusion [J]. J. Appl. Phys., 1951, 22: 74
[20] Otsuka N, Shida Y, Fujikawa H. Internal-external transition for the oxidation of Fe-Cr-Ni austenitic stainless steels in steam [J]. Oxid. Met., 1989, 32: 13
[21] Clark S P Jr. Handbook of Physical Constants [M]. New York: Geological Society of America, 1966
[22] Sarver J M, Tanzosh J M, Plants P. Effect of temperature, alloy composition and surface treatment on the steamside oxidation/oxide exfoliation behavior of candidate A-USC boiler materials [A]. 7th International Conference on Advances in Materials Technology for Fossil Power Plants [C]. Waikoloa, HI, 2013: 22
[21] SteyerP, PilloudD, PiersonJ F, et al. Oxidation resistance improvement of arc-evaporated TiN hard coatings by silicon addition [J]. Surf. Coat. Technol., 2006, 201: 4158
免责声明:本网站所转载的文字、图片与视频资料版权归原创作者所有,如果涉及侵权,请第一时间联系本网删除。
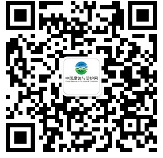
官方微信
《中国腐蚀与防护网电子期刊》征订启事
- 投稿联系:编辑部
- 电话:010-62316606-806
- 邮箱:fsfhzy666@163.com
- 中国腐蚀与防护网官方QQ群:140808414