随着国民经济的快速发展,换热器是生产过程中重要的特种设备,起着能量转换和传递的作用,被广泛应用在炼油、炼化、石油、石化等化工领域,特别是在炼油、炼化的成套生产装置中。据统计成套生产装置日常的大量故障及事故抢修,主要原因是换热器管束腐蚀泄漏导致的,约占成套装置中故障及事故抢修的60%左右。因此,为了保障成套生产装置的安全、平稳运行,最主要的手段是加强换热器管束腐蚀的监测和检测。据了解在换热器管束腐蚀检测应用中常用的检测技术有涡流检测、磁致伸缩低频导波检测和内旋转超声检测等技术。
涡流检测技术是换热器管束腐蚀检测最常用的检测技术。涡流检测技术一般采用内穿过式差分探头或/和绝对式探头进行检测,涡流检测是利用比较法,需要制作一根与被检管子相同(同规格、同材料、同批号等)的样管,将检测信号与样管的人工缺陷进行比较才能得出实际缺陷的大致情况,而且很难判断缺陷的种类和形状。该技术由于受管子的电导率、磁导率及管子状况等因素的影响,很难准确的获得整个管束腐蚀缺陷的信号,故涡流检测技术在指导换热器管束是否应当堵管上并不理想。
磁致伸缩低频导波技术应用在换热器管束腐蚀检测中是最近几年发展起来的,主要用于检测管束金属腐蚀损失的一种无损检测方法。其原理是以铁磁性材料的磁致伸缩效应及其逆效应为基础的检测技术,利用低频超声导波沿着换热器管束的截面内进行传播遇到的结构特征信号或腐蚀信号反射回探头进行经过处理后显示出来,简单分析后即可快速地评估管束的腐蚀情况。与内旋转超声检测技术相比,虽然具有检测过程简单,方便快捷,不需要耦合剂等优点;但是其只能检测铁磁性材料,只能给出金属腐蚀损失占管束截面的损失率,不能准确地判断腐蚀的形状和大小,因而在换热器管束腐蚀检测应用上受到限制。
内旋转超声检测技术是目前换热器管束腐蚀检测中应用最广、最为有效的一种检测技术。在重点介绍内旋转超声检测技术的原理及检测过程的基础上,分析了影响该检测技术在换热器管束腐蚀检测应用中的主要原因,并提出了相应的改进建议。
1 旋转超声检测原理
1.1 旋转超声的组成及工作原理
仪器主机、涡轮旋转头、对中装置、定位装置、耦合装置、水流管适配器、水浸聚焦探头、声反射镜和目标针等部件是旋转超声检测系统的主要组成部分,其原理是基于脉冲回波检测法,探头激发一个高频脉冲在水中产生超声波,一个反射镜将超声波反射90度变成垂直管壁方向波束,在管子内外表面都会反射回来的一个回波,内表面回波与外表面回波的时间和波幅经系统数字化处理后,通过计算就可以得到管子的内径、外径和壁厚。适用于碳钢,304不锈钢,316不锈钢,铜等所有能传递超声波信号的金属和非金属材料。图1为IRIS检测示意图。
图1 IRIS检测示意图
1.2 旋转超声的检测过程
旋转超声的检测过程是先由专业清洗工将换热器管束清洗干净,再将管束的一端用塑料堵头封堵,另一端往管束里充满水,然后将探头的对中装置推入管子内部,通过耦合水泵推动涡轮传动装置带动声反射镜自动旋转,在水中形成垂直于管壁的入射波束,对管束进行周向扫查;通过手动一边均速拉出对中装置,检测系统一边同时采集数据,采集到的数据能提供管束腐蚀的准确位置,能实时显示其横截面图(B扫描)、管壁展开图(C扫描)、以及管子纵向截面图(D扫描),如下图2所示。
图2数据图
2.应用案例
某化工厂的一台脱光气塔顶空冷器,其换热管规格Φ25×3×6000mm,材质10#。应用IRSI检测系统对该台换热器管进行抽查检测,发现下管板部分换热管没有减薄现象,剩余壁厚均匀分布,见图3-1所示;而上管板部分换热管存在明显减薄,且管中间部位严重减薄,主要表现在内壁减薄,减薄量超过50%换热管壁厚,剩余壁厚1.47mm左右,典型图谱如下图3-2所示。且对其中指定的一根换热管进行抽管验证,证明实际腐蚀与检测结果基本吻合,图4为该验证换热管解刨后的内壁实际腐蚀状态照片。
图3-1 未发现减薄的下管板换热管
图3-2 明显减薄的上管板换热管
图4 内壁实际腐蚀状态
某化工厂的一台立式机组中冷器,其换热管规格Φ57×3.5×3500mm,材质10#。应用IRSI检测系统对该台换热器管进行检测,本次抽检换热管20根,发现所有换热管都有明显减薄现象,减薄位置在管子与折流板交接处和全管体随机分布的腐蚀坑,在设备竣工图纸上查得换热管的壁厚为3.5mm,而抽查的换热管检测中壁厚减薄量高达32%的管壁厚,该最大减薄处剩余壁厚为2.39mm,如图5所示。
图5典型减薄图谱
3.IRSI检测的主要影响因素
3.1 管束的影响
换热管束内部状况对于检测信号影响很大,诸如管束内清洗不干净或者有油污会造成耦合剂水与管束内壁不能良好耦合,使声束无法穿透管束管壁,会造成漏检或者无法检测;管束内有脱落的锈斑会挡住声波的传输,使声束直接传输在锈斑块上形成虚假信号;管束局部变形会形成一个一定角度的截面,会改变声束的传播方向,从而使探头无法接收到信号,导致漏检或无法检测。因此,检测前须对管束进行彻底清洗,清洗掉里面油污和脱落的锈斑;检测过程中也要随时观察采集的检测信息。如果事先能对管束进行了彻底清洗处理,不仅对旋转超声检测大有裨益,而且有利于通过观察检测信号发现管束是否存在局部变形的情况。
3.2 涡轮转速的影响
涡轮转速对于检测信号亦有很大影响,涡轮转速不均匀会使图谱不连续,可能导致管束缺陷特征信号的遗失,从而造成漏检,因此,每次检测前必须在样管上调整好涡轮转速。图6中长条状黑色带即为涡轮转速不均匀造成的。
图6 典型涡轮转速不均图谱
4.结语
对在用换热器管束的腐蚀检测,内旋转超声检测是目前最为有效、准确、快速的检测方法,不仅能对整根管束进行快速扫查,还可以通过内表面回波与外表面回波的时间差和波幅经系统数字化处理后,通过计算就可以得到管子内径、外径和壁厚。内旋转超声检测技术的最大优点是不受材料电导率或磁导率的影响,也是其他检测技术不可比拟的优点。但其往往存在对管束清洗要求高,对涡轮转速操作均匀等问题,这些因素都限制了旋转超声检测技术在换热管束腐蚀检测中的应用。通过实验研究若能开发出拥有固定涡轮转速的新型装置,就能很好地克服由于涡轮转速不均而导致管束缺陷漏检的情况。同时通过加工定制与旋转超声探头尺寸大小相匹配的管束清洗装置,就能很好地解决由于清洗不到位而导致管束漏检或无法检测的情况,也能很好地防止由于有脱落的锈斑会挡住声波的传输,使声束直接传输在锈斑块上形成虚假信号的情况发生。今后只要能克服这两大影响因素,内旋转超声检测技术在换热管束腐蚀检测的应用中,一定能得到更大的推广应用。
免责声明:本网站所转载的文字、图片与视频资料版权归原创作者所有,如果涉及侵权,请第一时间联系本网删除。
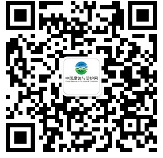
官方微信
《中国腐蚀与防护网电子期刊》征订启事
- 投稿联系:编辑部
- 电话:010-62316606-806
- 邮箱:fsfhzy666@163.com
- 中国腐蚀与防护网官方QQ群:140808414