摘要
结合自修复微胶囊防腐涂层与合金镀层的优点,在Q235碳钢基体制备Ni-Co/Cap(T+Y)复合涂层以提高碳钢材料的耐侯性和服役周期。首先采用恒电流合金电镀法在Q235碳钢基体生成Ni-Co合金镀层,然后将以桐油和金属缓蚀剂做囊芯的双组份自修复胶囊均匀分散在醇酸树脂防腐涂层中制备有机防腐涂层,得到Ni-Co/Cap(T+Y)复合涂层。SEM观测和热重分析结果表明,合成的双组份自修复微胶囊的平均粒径约为3 μm,囊芯包覆率达到49%。中性盐雾试验和微区电化学测试结果表明,经历380 h中性盐雾试验后复合防腐涂层只在划痕交点处出现轻微腐蚀,其他部位仍旧完整,没有出现鼓泡和腐蚀。以Ni-Co合金镀层与自修复涂层相结合的复合涂层,能长期保护Q235碳钢。
关键词: 材料失效与保护 ; 自修复涂层 ; 微胶囊 ; Ni-Co合金电镀
在海水或高温、高湿、高盐的海洋大气中,对浸泡的各种钢铁构件,必须采取有效的防腐措施[1, 2]。使用有机涂层是主要的防腐蚀方法之一,得到了广泛的应用[3~6]。但是,涂层的成型过程伴随着有机分子的交联、缩聚和溶剂的挥发,使涂层内部密度不均、形成微孔、裂纹缝隙等微观缺陷,从而引起金属与涂层间界面的腐蚀致使涂层失效,甚至导致海洋工程装备腐蚀而引发严重的事故[7,8]。自修复涂层概念的提出,为解决有机涂层材料外部创伤和内部缺陷提供了理想的途径。通过对损伤作出感应和响应,在不影响体系整体性能的条件下修复损伤,使材料更可靠、安全、耐用,从而大大降低维护和维修费用[9~14]。
加入含修复剂的微胶囊或者含缓蚀剂的纳米容器,可实现防腐涂层的自修复。前者对涂层的破坏处进行物理修复以保持防腐涂层的完整性,阻隔腐蚀环境中腐蚀性离子的入侵,从而实现自修复防护;后者在纳米容器中担载缓蚀剂,当涂层受到外界破坏时纳米容器中的缓蚀剂流出,与基体结合形成防护膜实现自修复[15~17]。
主要的微胶囊修复剂,有环氧树脂、桐油、亚麻油、异氰酸酯等[18~20]。Hia等以环氧树脂为修复剂、以有机钪为催化剂,制备了粒径为300~400 μm的自修复微胶囊。胶囊的加载量超过20%涂层,具有自修复功能[21]。Lang[22]等用原位聚合法使亚麻油包覆在据脲醛壳体制备出具有自修复功能的微胶囊,在涂层中均匀分布的微胶囊具有优异的愈合性能。Huang[23]制备出以亚甲基二苯基二异氰酸酯和1,4-丁二醇为自修复剂的聚氨酯微胶囊。改变微胶囊的囊芯材料,使其遇到氧气等外界条件时能自然成膜。这种膜层比使用催化剂或引发剂制备的膜更均匀,修复性能更好。Qiao等用原位聚合法合成粒径为51~323 μm的酚醛树脂微胶囊,其产率高达82.33%。这种微胶囊的含量为20%时,即可实现有机涂层最佳自修复功能[24]。但是,目前制备的微胶囊粒径较大(平均粒径超过100 ?m),有机涂层每层的厚度约为100 ?m,使其使用受到限制。
主要的无机纳米容器材料,包括SiO2、CaCO3、TiO2、ZrO2等介孔纳米颗粒,以及工业矿物如埃洛石等[10, 25~27]。Snihirova[28]制备了缓蚀剂型碳酸钙微胶囊,掺杂硝酸铈的复合微米球涂层具有明显的自修复效果。Ma[29]等使用介孔纳米二氧化硅负载铜的缓蚀剂,实现了涂层的自修复功能。使用含4%复合纳米粒子的防腐涂层,具有最佳的自修复功能。使用介孔材料负载金属缓蚀剂,是自修复涂层的一个重要研究方向。但是制备介孔材料比较困难,制备自修复涂层的步骤复杂。同时,介孔材料的孔径限制环境友好型生物大分子缓蚀剂的负载[27]。本文针对自修复微胶囊粒径较大和缓蚀剂在胶囊中的负载受限等问题,结合自修复微胶囊、缓蚀剂纳米容器和合金镀层的优点,研究具有双重功能的自修复复合涂层的制备和耐蚀性。
1 实验方法
1.1 材料的制备
(1) 自修复微胶囊的制备 用乳液聚合法制备双组分微胶囊(Cap(T+Y)),囊芯为桐油(T)和金属缓蚀剂(Y),囊壁为脲醛树脂(UF)。在260 mL超纯水中加入2 g乳化剂Op-10,使用搅拌分散机搅拌使其完全溶解,然后依次加入5 g脲、0.5 g氯化铵和0.5 g间苯二酚,待溶解后用浓度为1%的 HCl调节pH值至3.0。酸化进行一段时间后加入T和Y(T和Y质量比5:1),维持较高转速,继续乳化直至油状物完全乳化。将溶液加热到60℃后逐滴滴加13.67 g甲醛溶液,在此温度下维持转速800 r/min,使其充分反应2 h。反应完毕后骤冷,然后过滤,在80℃干燥6 h。对制备出的微胶囊用丙酮除油充分清洗三次,最终得到自修复微胶囊。
微胶囊的聚合反应为
(2) Ni-Co合金镀层的制备 基体的预处理:对Q235碳钢基体依次用400目、800目、1000目、1500目和2000目砂纸打磨,然后用丙酮和酒精超声清洗以除油,最后用吹风机冷风吹干备用。
Ni-Co合金的电镀:用高纯镍板做正极,用预处理后的Q235做负极,使用PARSTAT 2273电化学工作站进行两电极体系恒流电镀,电镀工艺参数:电流密度50 mA/cm2,pH=4.0,温度40℃,电镀时间60 min,磁力搅拌速度300 r/min。
(3) Ni-Co基自修复涂层(N-C-SR)的制备 将质量比为1:9的双组份微胶囊与醇酸树脂防腐涂层混合,然后用细胞破坏仪分散45 min,最后超声分散30 min以使微胶囊充分分散。使用匀胶机在Ni-Co合金镀层表面旋涂,然后在自然条件下干燥3 d。覆层磁性测厚仪进行测量,厚度控制为100±5 μm。
1.2 材料的表征
用ULTRA 55型场发射扫描电镜(FESEM)观察样品的表面形貌,电压调至2 kV。采用NETZSCH STA 409PC型热重分析仪对自修复微胶囊进行热重测试分析以评价微胶囊的稳定性和包覆量,测试时采用氮气气氛保护,将微胶囊(约10~15 mg)放入氧化铝坩埚中,设置温度范围:25℃~800℃,升温速率为10℃/min,降温速率为20℃/min,连续记录微胶囊的质量变化。
1.3 中性盐雾实验
使用JK-FH90盐雾试验机进行带有划痕的N-C-SR和完整的N-C-SR的中性盐雾实验,环境中的实验溶液为5% NaCl溶液,其pH值为6.5~7.2,环境温度为35℃,盐雾沉降量为1~2 mL/cm2·h,实验中样品倾斜45°。使用交叉划线制备划痕,长度为1.5 cm,宽为0.1 mm。
1.4 微区电化学测试
使用VersaSCAN型微区电化学测试系统测试N-C-SR自修复过程中划痕处的电位分布。测试时,调整试样使其与仪器操作平台平行,测试探针为钨探针,直径为500 μm,探针移动形式为步进式移动,扫描类型为面扫描,扫描区域为2000 μm×2000 μm,探针移动速率是100 μm/s,气氛为空气,环境相对湿度55%。在N-C-SR表面制备出一条长1.5 cm、宽0.1 mm的划痕,将其浸泡在天然海水中,测试不同浸泡时间的自修复行为,直至完成自修复。
2 实验结果
2.1 自修复微胶囊表征分析
图1给出了以桐油(T)和金属缓蚀剂(Y)为芯材的双组份自修复微胶囊Cap(T+Y)的微观形貌。可以看出,Cap(T+Y)呈现圆球状,粒径分布均匀,其粒径约为3 μm,微胶囊较少团聚。
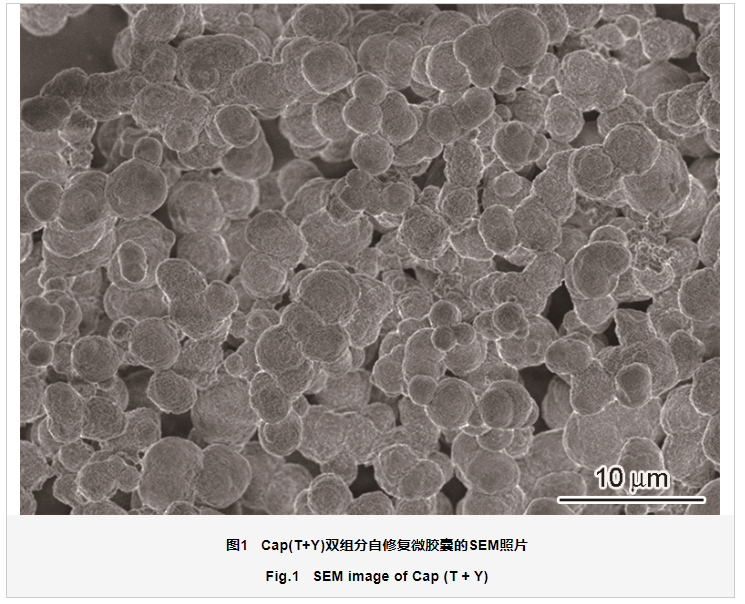
进行热重(TGA)实验分析微胶囊的热稳定性和包覆量。UF、T、Y和Cap(T+Y)的失重曲线和DTG曲线,如图2所示。从图2b可以看出:UF的分解温度为210℃左右,完全分解温度为350℃;T的分解温度在350℃左右,完全分解的温度为480℃;Y的分解温度在300℃左右,完全分解的温度为450℃。Cap(T+Y)在210℃出现UF的分解,当其未完全分解时出现了Y的分解,当Y未完全分解时又出现了T的分解,当Y在450℃完全分解时T仍未分解完全,直至温度到达480℃时T完全分解。这充分证明,Cap(T+Y)已经成功地包覆了T和Y两种囊芯。根据图2a可估算微胶囊囊芯材料的包覆率
式中W(T+Y)为囊芯材料T和Y的包覆率,Mcap0和Mcapt为微胶囊Cap(T+Y)热重测试前后的质量,mUF0和mUFt为囊壁脲醛树脂热重测试前后的质量。计算结果表明,Cap(T+Y)的囊芯包覆率约为49%。
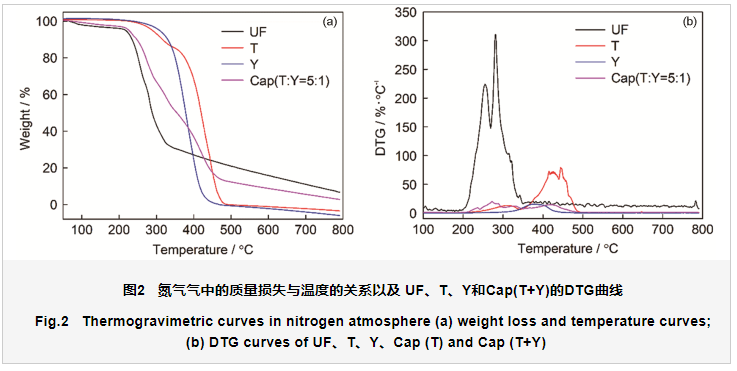
2.2 中性盐雾实验结果
图3给出了Ni-Co合金镀层、带划痕的N-C-SR和完整的N-C-SR在中性盐雾不同时间下的实验结果。从图3a可以看出,盐雾实验进行200 h时Ni-Co合金镀层出现大量点蚀, 300 h时点蚀部位不断向周围延伸。其原因是,Ni-Co合金镀层也有微裂纹或晶界,在腐蚀环境中腐蚀性粒子最先侵蚀在镀层中形成腐蚀通道,直至穿过镀层到达基体表面。基体在腐蚀环境下容易腐蚀生成腐蚀产物,随着时间的延长基体的腐蚀区域不断扩大,大量腐蚀产物从腐蚀通道中流出。但是,如果Ni-Co合金镀层与自修复涂层相结合,在盐雾实验200 h时只在划痕的交点处出现一个锈点。盐雾380 h时划痕交点的锈点扩大,但是其他非划痕交点处仍保持较好的完整性,如图3b、c所示。这表明:掺杂自修复微胶囊的涂层与Ni-Co合金镀层复合,当自修复涂层存在时,破损后自修复微胶囊芯材对涂层进行修复。同时,金属缓蚀剂在一定程度上阻碍了基体的腐蚀。如图3c所示,完整N-C-SR进行中性盐雾实验380 h后依然没有任何锈点。着表明,掺杂适当微胶囊的N-C-SR整体具有良好的耐蚀性,能有效保护基体。增加Ni-Co合金镀层后盐雾实验试样出现腐蚀现象的时间延后,证实了双层结构延长了对基体的保护作用。
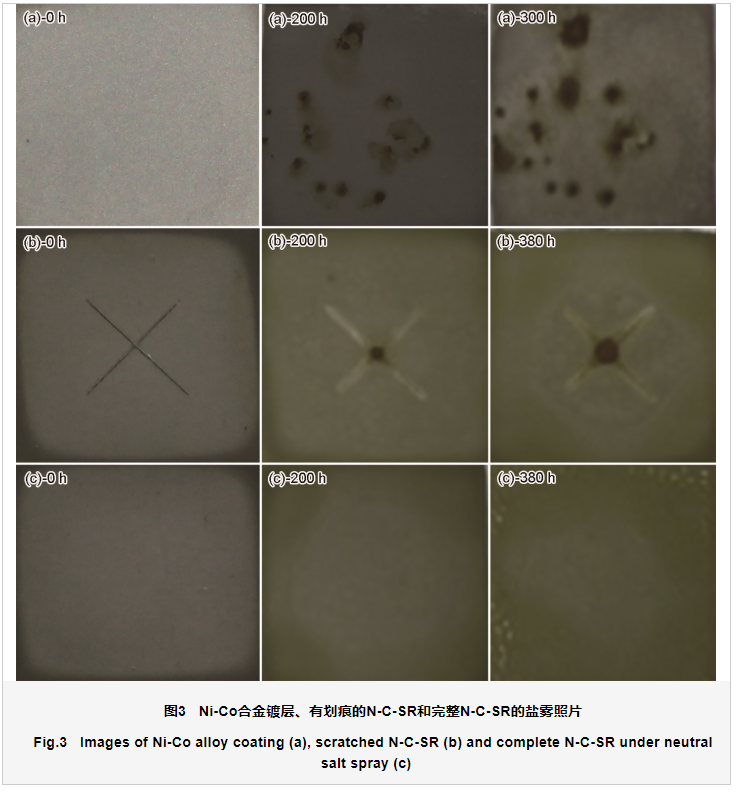
2.3 N-C-SR的SKP测试结果
扫描Kelvin探针技术(SKP)是一种有效的检测样品表面局部差异性的技术,在测试过程中探针不接触试样表面,不损害材料表面,也不破坏材料的性能 [30, 31]。在扫描过程中探针获取材料表面的功函数,探针与样品的伏打电位差(Δψ)与材料的自腐蚀电位(Ecorr)具有相关关系[32]
其中Const为常数项,其数值由实验确定,因此,可使用Kelvin探针测得试样表面的伏打电位的差值以研究有机涂层对金属基体的保护效果。
本文通过SKP来测试涂层缺陷处电化学状态,评估镍钴基自修复涂层的自修复行为。先在N-C-SR制备出长为1 cm、宽为0.1 mm的人工缺陷,将试样放置在室温环境下维持一段时间,然后放入天然海水中浸泡。图4给出了不同浸泡时间SKP测试缺陷处的电位变化。从图4a可以看出,浸泡前划痕的最高伏打电位为506 mV,最低伏打电位在202 mV。因为在室温环境下划痕处自修复微胶囊的囊壁受到破坏,囊芯材料流出在镍钴表面形成一层较薄的膜层,因此伏打电位与周围完整涂层之间有一定的差别。当浸泡时间的延长,当浸泡4 h时涂层缺陷处最高伏打电位为554 mV,最低伏打电位为216 mV,电位差值为338 mV,如图4b所示。其原因是,浸泡在海水中的自修复涂层有一定的吸水性。在浸泡24 h时最高伏打电位为274 mV,最低伏打电位60 mV,伏打电位的差值在214 mV,如图4c所示;浸泡50 h时最高伏打电位为298 mV,最低伏打电位140 mV,伏打电位的差值在158 mV,如图4d所示,此时涂层基本上还保持完整。伏打电位在较大的范围变化,表明表面易于腐蚀或腐蚀产物在表面分布不均匀;当伏打电位在较小的范围变化且伏打电位明显负移,表明在其表面成膜,具有保护效果。其原因是,在浸泡过程中有机涂层微裂后微胶囊破损,囊芯部分逐渐流出;在水中氧气的作用下桐油修复剂充满裂纹处发生聚合固化反应,完成有机涂层的自修复。自修复微胶囊破裂成膜,抑制了缺陷的发展并阻隔了海水环境接触Ni-Co合金镀层,从而能较好地保护基体。

3 讨论
从盐雾实验和SKP测试结果可以看出,N-C-SR自修复效果较好。其中的微胶囊含有双组分:涂层修复剂和金属缓蚀剂。对N-C-SR的腐蚀机理进行讨论,建立了N-C-SR的腐蚀机理演化模型,如图5所示。
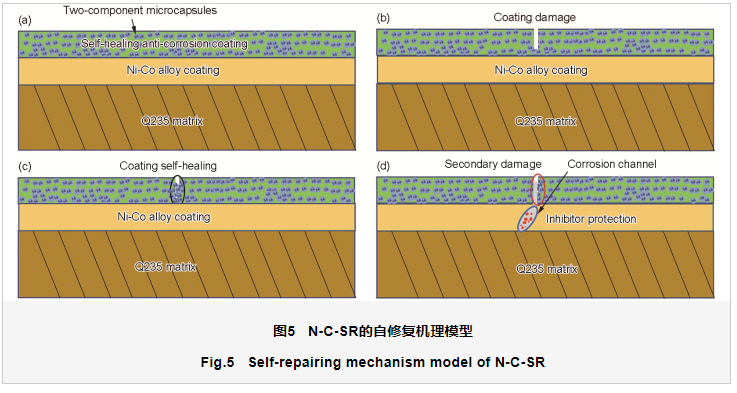
图5a为构建的Q235/Ni-Co镀层/微胶囊自修复复合涂层体系,其中微胶囊中含有桐油修复剂和金属缓蚀剂。涂层产生微裂纹后,埋植于基体内部的微胶囊因外力作用而破裂释放出芯材。微胶囊中的囊芯具有一定的流动性,在虹吸作用下桐油修复剂充满裂纹处发生聚合固化反应完成有机涂层的修复过程,如图5b和c所示。桐油修复剂的聚合固化过程为:桐油的主要成分桐油酸甘油三酯在酸性或碱性条件下分解为桐油酸(主要为α-桐油酸和β-桐油酸)和甘油,其中α-桐油酸在日光、空气等中不稳定,受日光、氧气等的作用而转变为β-桐油酸。桐油酸分子结构中的共轭双键临近碳原子上的氢,在日照、O2等作用下发生夺氢反应,生成的氢过氧化物分解产生自由基而引发共轭双键的聚合反应,形成桐油酸高聚物,最终完成固化反应。可能的反应路径为
随着试验的进行,当修复剂成膜部位再次受到破坏或者膜层失效时Ni-Co合金镀层暴露在腐蚀环境中。随着腐蚀性粒子的不断入侵Ni-Co合金镀层逐渐被腐蚀而形成缺陷,此时在缺陷处发生腐蚀。随后,随着腐蚀区域的不断扩展腐蚀通道逐渐形成,此时微胶囊中的金属缓蚀剂释放溶解到腐蚀溶液介质中。随腐蚀溶液介质流动到基体表面,覆盖到暴露的Q235基体处形成缓蚀剂膜,减缓了腐蚀环境的入侵,从而更好的保护基体、延长基体的寿命。
4 结论
结合自修复微胶囊、缓蚀剂纳米容器和合金镀层的优点,制备了基于Q235碳钢/Ni-Co镀层的双组份自修复微胶囊复合涂层。涂层出现微裂纹后埋植在基体内部的微胶囊因外力作用破裂释放出芯材,即修复剂和金属缓蚀剂,在虹吸作用下芯材充满裂纹处,修复剂发生聚合反应完成自修复。同时,金属缓蚀剂吸附在Ni-Co镀层表面,通过物理或化学作用抑制腐蚀电化学反应的进行。自修复胶囊失去作用后,Ni-Co合金镀层对Q235基体进行防护。当有机涂层中自修复微胶囊含量为10%时,在合金镀层和自修复涂层的双层结构的共同作用下经历380 h的中性盐雾试验基体仍然得到较好的保护。
参考文献
[1] Han E, Chen J, Su Y, et al. Corrosion protection techniques of marine engineering structure and ship equipment—current status and future trend[J]. Mater. Chin., 2014, (33): 65
[1] 韩恩厚, 陈建敏, 宿彦京等. 海洋工程结构与船舶的腐蚀防护—现状与趋势 [J]. 中国材料进展, 2014, (33): 65
[2] Sander G, Tan J, Balan P, et al. Corrosion of additively manufactured alloys: a review. Corros., 2018, 74(12): 1318
[3] Lin J, Li W, Che K, et al. Research progress in marine engineering of anticorrosive coatings [J]. Mod Paint Finishing, 2018, 21(9): 7
[3] 林静, 李文婷, 车凯圆等. 防腐涂层在海洋工程中的研究进展 [J]. 现代涂料与涂装, 2018, 21(9): 7
[4] Shi H, Liu F, Wang Z, et al. Research progress of corrosion-resisting paints for marine application [J]. Corros. Sci. Pro. Technol., 2010, 22(1): 43
[4] 史洪微, 刘福春, 王震宇等. 海洋防腐涂料的研究进展 [J]. 腐蚀科学与防护技术, 2010, 22(1): 43
[5] Pourhashem S, Ghasemy E, Rashidi A, et al. A review on application of carbon nanostructures as nanofiller in corrosion-resistant organic coatings [J]. J. Coat. Technol. Res., 2020, 17(1): 19
[6] Gao S, Liu M, Pang X, et al. Fabrication and properties of super-hydrophobic composite coatings [J]. Chin. J. Mater. Res., 2018, 32(7): 502
[6] 高硕洪, 刘敏, 庞晓军等. 超疏水复合涂层的制备和性能研究 [J]. 材料研究学报, 2018, 32(7): 502
[7] Guo Q, Chen H. The protective mechanism and evaluating methods of anticorrosion coatings [J]. Synthetic. Mater. Aging. Appl., 2003, 32(04): 36
[7] 郭清泉, 陈焕钦. 金属腐蚀与涂层防护 [J]. 合成材料老化与应用, 2003, 32(04): 36
[8] Lv P, Li H, Huang W. New progress of the research on organic protective coatings [J]. Mater. Rev., 2011, 25(13): 83
[8] 吕平, 李华灵, 黄微波. 有机防护涂层老化研究进展 [J]. 材料导报, 2011, 25(13): 83
[9] Li H, Cui Y, Wang Q, et al. Advances in self-healing coating materials [J]. Polymer Mater. Sci. Eng., 2016, 32(10): 177
[9] 李海燕, 崔业翔, 王晴等. 自修复涂层材料研究进展 [J]. 高分子材料科学与工程, 2016, 32(10): 177
[10] Pan M, Wang L, Ding X, et al. The research progress of self-healing anti-corrosion coatings [J]. Mater. Chin., 2018, 37(1): 19
[10] 潘梦秋, 王伦滔, 丁璇等. 自修复防腐涂层研究进展 [J]. 中国材料进展, 2018, 37(1): 19
[11] Zhang Y, Fan W, Zhang T, et al. Review of intelligent self-healing coatings [J]. Chin. J. Corros. Pro., 2019, 39(4): 299
[11] 张勇, 樊伟杰, 张泰峰等. 涂层自修复技术研究进展 [J]. 中国腐蚀与防护学报, 2019, 39(4): 299
[12] An S, Lee W M, Yarin A, et al. A review on corrosion-protective extrinsic self-healing: Comparison of microcapsule-based systems and those based on core-shell vascular networks [J]. Chem. Eng. J., 2018, 344: 206
[13] Leal D A, Riegel-Vidotti I C, Ferreira M G S, et al. Smart coating based on double stimuli-responsive microcapsules containing linseed oil and benzotriazole for active corrosion protection [J]. Corros. Sci., 2018, 130: 56
[14] Wang X, Jin T, Wang H, et al. Preparation and properties of poly (urea-formaldehyde) microcapsules containing polysulfide sealant [J]. Chin. J. Mater. Res., 2018, 32(10): 730
[14] 王璇, 金涛, 王浩伟等. 脲醛树脂包覆聚硫密封剂微胶囊的制备和性能 [J]. 材料研究学报, 2018, 32(10): 730
[15] Hughes A E, Cole I S, Muster T H, et al. Designing green, self-healing coatings for metal protection [J]. NPG Asia Mater., 2010, 2(4): 143
[16] Yabuki A, Sakai M. Self-healing coatings of inorganic particles using a pH-sensitive organic agent [J]. Corros. Sci., 2011, 53(2): 829
[17] Wang X, Zhang X, Li F, et al. Research progress on self-healing anticorrosion coating [J]. J. Funct. Mater., 2012, 43(19): 2584
[17] 王晓岗, 张星, 李原芃等. 自修复功能防腐涂膜研究进展 [J]. 功能材料, 2012, 43(19): 2584
[18] Shi X, Song Y, Cai Z, et al. The influence of microcapsules with a partially filled structure on the damping properties of an epoxy resin [J]. New J. Chem., 2018, 42(14): 12119
[19] Zhou X, Li W, Zhu L, et al. Polymer–silica hybrid self-healing nano/microcapsules with enhanced thermal and mechanical stability [J]. RSC Adv., 2019, 9(4): 1782
[20] Wazarkar K, Patil D, Rane A V, et al. Microencapsulation: an emerging technique in modern coating industry [J]. RSC Adv., 2016, 6(108): 106964
[21] Hia I L, Chan E-S, Chai S-P, et al. A novel repeated self-healing epoxy composite with alginate multicore microcapsules [J]. J. Mater. Chem. A, 2018, 6(18): 8470
[22] Lang S, Zhou Q. Synthesis and characterization of poly(urea-formaldehyde) microcapsules containing linseed oil for self-healing coating development [J]. Prog. Org. Coat., 2017, 105: 99
[23] Huang M, Yang J. Facile microencapsulation of HDI for self-healing anticorrosion coatings [J]. J. Mater. Chem., 2011, 21(30): 11123
[24] Qiao L, Xue Y, Zhang Q. Synthesis and characterization of phenol-formaldehyde microcapsules for self-healing coatings [J]. J. Mater Sci, 2018, 53(2): 1035
[25] Li K, Li H, Cui Y, et al. Dual-functional coatings with self-lubricating and self-healing properties by combining poly(urea-formaldehyde)/SiO2 hybrid microcapsules containing linseed oil [J]. Ind. Eng. Chem. Res., 2019, 58(48): 22032
doi: 10.1021/acs.iecr.9b04736
[26] Díez-García I, Eceiza A, Tercjak A. Self-healable nanocomposites with enhanced thermal stability by incorporation of TiO2 nanoparticles to waterborne poly(urethane-urea) matrices based on amphiphilic triblock copolymers [J]. J. Phys. Chem. C, 2019, 123(34): 21290
doi: 10.1021/acs.jpcc.9b06184
[27] Shchukina E, Wang H, Shchukin D G. Nanocontainer-based self-healing coatings: current progress and future perspectives [J]. Chem. Comm., 2019, 55(27): 3859
doi: 10.1039/c8cc09982k pmid: 30895976
[28] Snihrova D, Lamaka S V, Montemor M F. "SMART" protective ability of water based epoxy coatings loaded with CaCO3 microbeads impregnated with corrosion inhibitors applied on AA2024 substrates [J]. Electrochim. Acta, 2012, 83: 439
[29] Ma X, Xu L, Wang W, et al. Synthesis and characterisation of composite nanoparticles of mesoporous silica loaded with inhibitor for corrosion protection of Cu-Zn alloy [J]. Corros. Sci., 2017, 120: 139
[30] Lamaka S V, Zheludkevich M L, Yasakau K A, et al. High effective organic corrosion inhibitors for 2024 aluminum alloy [J]. Electrochim. Acta, 2007, 52(25): 7231
[31] Yu S, Jia R, Zhang H, et al. Effect of (Gd, Y) containing-phases on local corrosion of aged GW103K alloy [J]. Chin. J. Mater. Res., 2019, 33(3): 199
[31] 于爽, 贾瑞灵, 张函等. (Gd, Y)相对GW103K时效合金局部腐蚀的影响 [J]. 材料研究学报, 2019, 33(3): 199
[32] Lee S J, Hong A, Kim I H, et al. Surface potential measurements of a polymer film following primary ion gun irradiation for ToF-SIMS analysis of insulator using a Kelvin probe and the observation of effects from the vacuum gauge [J]. Appl. Surf. Sci., 2020, 525: 146561
免责声明:本网站所转载的文字、图片与视频资料版权归原创作者所有,如果涉及侵权,请第一时间联系本网删除。
相关文章
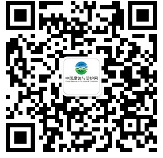
官方微信
《中国腐蚀与防护网电子期刊》征订启事
- 投稿联系:编辑部
- 电话:010-62316606-806
- 邮箱:fsfhzy666@163.com
- 中国腐蚀与防护网官方QQ群:140808414
点击排行
PPT新闻
“海洋金属”——钛合金在舰船的
点击数:7204
腐蚀与“海上丝绸之路”
点击数:5800