引 言
在海洋石油平台中,出于工艺的需要,开采出来的石油只有在合适的温度和压力下,其流动性才能达到最合适的输送状态。因此大量的管道或设备均需要覆盖保温层。保温层的作用不仅能够减少工艺输送的热量损失、保持整个系统的操作温度,同时也可以作为阻隔外界有害物质的屏障。
然而,管道或设备的保温层往往在安装、使用过程中,由于各种因素造成破损,在保温材料和基体金属间局部区域形成半密闭的腐蚀环境,这种环境比海洋大气环境还恶劣,将造成保温层下管道或设备发生严重的腐蚀。这类发生在保温层下的腐蚀现象,学术界统称为保温层下腐蚀(corrosion under insulation,CUI)。研究表明,设备或管道的保温层结构,在运行5~10 a后,60%均含有腐蚀性的冷凝水,将难以避免CUI发生。
由于外层铝箔等包覆材料和保温材料的存在,使CUI具有极强的隐蔽性。当发现CUI时,腐蚀已经相当严重了,甚至可引起突发性的泄漏事故。在石油化工领域,CUI导致了超过60%的泄露故障。全球因CUI引起的设备损坏,停产损失、人员伤亡等损失高达每年数十亿美元。
不仅在石油石化领域被发现和研究,同样在发电厂、核电站、无机化工、有机化工、炼化工厂等各种存在保温的领域均有发现。目前学术界就CUI开展了针对性的研究,从传统的石油天然气工业领域,扩展到建筑科学工程,化学工程,核科学工程,燃料,电力,无机,金属工艺等各个方面。CUI受到越来越多学者们的重视,这对我们认识CUI、保护被保温设备设施的安全有着积极的作用。
CUI常用的检测技术
由于保温层的阻隔,需要将保温层剥离才能准确检测。维修完涂层或者设备基体后,必须重新制作保温层。常用的检测方法有目视检测,超声检测,射线检测和涡流检测等,这些方法均无法在腐蚀发生的第一时间确认CUI。
1 目视检测
目视检查是确定碳钢和低合金钢上是否存在CUI的最基础的方法,但是需要拆除保温层系统。目视检查可用于确定奥氏体不锈钢上CUI是否存在。通常情况下,钢材表面的腐蚀垢体积会不断增加,通常比原始损失金属的体积大10倍。然而,并非所有保温层下腐蚀都能用目视判定,有些需通过金属损失量的测量确定,甚至需要使用更精细的无损检测技术。
2 超声检测
通常采用手动操作方法,可以安装固定的监测点监测碳钢和低合金钢设备的内部腐蚀动态,定期进行多点厚度测量,相关数据也可用于确定CUI的发生。若在保温层外使用超声检测,则需在保温层外制作探测孔,用盖子遮蔽该孔防水,这样的测试仅限于在不易受CUI影响的适合区域使用,要获得可靠的结果则需要测量多处。由于保温层上切下的检查孔将损害保温层的完整性,如果修补不良,反而会增加CUI发生的概率。超声检测在任何情况下都不能确定奥氏体不锈钢中的CI-ESCC。
3 射线检测
对小部分管道进行射线曝光,通过和原始数据比较从而计算管道的剩余壁厚。曝光源通常为铱192(可检测材料厚度12~63 mm)和钴60(可检测材料厚度50~150 mm)。钴60一般无法用于海上。射线检测是一种有效的评估方法,但当管道的公称直径﹥250 mm(10 in)时,采用射线检测有一定局限,通常只能提供相对较小区域的验证性检测。有研究报道,在某些射线检测条件下,可以检测到裂纹,如应力腐蚀开裂等。
4 涡流检测
脉冲涡流技术可以“在线”使用,它可以隔着保温层测量铁磁性材料的平均剩余壁厚。脉冲涡流技术的测量主要基于一种在导电材料中,受到可变磁场的作用,会产生涡流的现象进行测量。主要原理为:感应磁性的强度通常大于给定材料的本征磁性,通过感应线圈系统产生磁场,线圈放置在待测位置的保温板表面上,在规定的时间内,直流电通过线圈,在管道或容器壁上形成稳定磁场,切断电流后,磁场迅速降至零,这会在受检材料内产生涡流。封闭磁场中涡流的持续时间与材料厚度直接相关,涡流的强度和可测量的持续时间取决于磁场的强度以及材料的导电性和磁导率。如果测量强度和持续时间确定,则可以计算出平均壁厚。脉冲涡流可用于几何规整的管道或设备的表面,对于管嘴、焊缝等,由于几何限制,无法使用涡流监测技术。
其他检测技术还有红外射线、数字成像、中子扫描等,不逐一展开介绍。
预防CUI措施
1 选择合适的外防护层
保温层的外防护层是防护CUI的首要屏障,一般认为外防护层可以保护设备或管道免受机械损伤,同时能够阻挡恶劣环境中水等腐蚀介质。通常外防护层的选取只考虑经济性、实用性、易于安装和被保温设备或管道的工况温度等条件。
外防护层一般分为金属和非金属材料。金属防护层具有一定的厚度,可以抵抗冲击,抗腐蚀性能优异。常用的材料有镀铝钢、铝箔和不锈钢板等。
非金属防护层通常包括固化玻璃纤维增强塑料、热塑性塑料和相关材料的聚合物等,相比金属防护层,非金属防护的可塑性使得其具有更好的密封性能,然而在面对更恶劣的工况时,非金属的低熔点和较差的耐冲击性使其应用受到不少限制。
外防护层很容易受到气候变化、机械损伤、环境腐蚀等影响,因此,经常性地维护防护层是必不可少的。根据管道和设备实际情况,选择可靠的外防护层,是保温系统抵抗CUI能力不可或缺的条件之一。
2 选择优异的保温材料
保温材料是包裹在管道或设备外的第二道屏障,是保温系统必不可少的部分。设计合理的保温材料,在正确安装并提供充分的维护的情况下,能有效提高对CUI的防护效率。
根据对水分的保持程度,分为疏水保温材料和亲水保温材料。疏水性保温材料的原理通常分为自身疏水和加入化学添加剂疏水。通常使用的岩棉、硅酸钙等均属于亲水性保温材料。
研究发现,能有效抵抗CUI的保温材料贮存水分最少并且干燥速率最快。在CUI容易发生的温度范围内 (-4~175℃),保温材料越吸水,越会加速CUI;相反,当保温材料不易吸水即疏水性材料时,能够抑制CUI。针对疏水保温材料的研究较少,同时疏水性材料价格较高,使得高效的疏水性保温材料难以推广,导致疏水性材料的应用并不广泛。
目前已知的保温材料均无法规避CUI的出现。究其原因,保温材料的安装均会与基体间形成环形空隙,加上设备和管道本身存在缺陷,导致腐蚀性介质容易存留,为水分的聚集提供场所,是引起CUI的关键。大量的工程案例表明,经过长期运行后,保温材料内部和外界的污染物 (例如氯化物、硅酸盐等)会不断随着水分的渗透而溶解,加上保温材料本身逐渐老化,加剧了腐蚀的发生。基于此情况,应要求保温材料中Cl-含量<10 mg/kg(可浸出值),或者在保温材料的制造过程中采取添加抑制剂、疏水剂等措施。通常添加的疏水材料对水分的贮存越低,干燥时间越短,发生CUI的风险也更低。
将保温材料包裹在裸露碳钢管外进行实验室条件下的环境模拟,Williams等利用该模拟方法研究不同保温材料的性能。结果表明,常用的玻璃棉保温材料导致碳钢发生CUI最严重,大量由管壁、玻璃棉保温层形成的楔形空间留存有积水。玻璃棉材料本身具备的疏水性,反而使水分气相和液相难以自然迁移,从而留存在易于存水的空间中。矿物棉保温材料则在管线顶部发现了部分腐蚀,且其腐蚀表面风化严重,触感潮湿,矿物棉纤维自身的吸水性能良好,顶部易于保存积水。与之相同的硅酸钙保温材料,大量的CUI腐蚀集中在管道底部,最终整体的吸水量为保温材料的157%,这是由于过高的吸水性,水分由于重力自发聚集在管线底部引起的。
由上述分析可知,慎重选用能有效阻止水分渗入的保温材料抵抗CUI能力最佳。
3 选择高性能的防护涂层
高性能的有机涂层和热喷铝涂层已广泛用于CUI的防护中。与通常的腐蚀环境不同,CUI的腐蚀环境更加恶劣,在抵抗CUI中使用的防护涂层应具备的特性有:优异的耐高温降解性能、优秀的抵抗热膨胀和收缩应力性能;良好的耐热性能、充足的防腐蚀性能、优良的抗氧化性和抗热循环性能;对于低表面处理的容忍性高,施工快捷、高效且与基体结合性能良好;能够提供可靠的屏障用以抵抗腐蚀性污染物或者水汽的腐蚀。以上性能同时具备的防腐涂料很少,若使用不合适的涂层,则会在保温层下这类恶劣腐蚀环境中长时间后发生涂层降解,导致抵抗水分渗透能力降低,进而引发CUI。因此,选择高性能的防护涂层是预防CUI的重要环节。
>有机涂层防护
有机涂层的防护机理是将涂层作为阻挡侵蚀性离子扩散的阻挡层,涂层防腐性能的关键是涂层与金属基体间的粘结强度和涂层对侵蚀性离子溶液的抗渗透能力。然而,在涂层施工安装过程中,不可避免地产生破损和划伤,有机涂层自身的渗透性也是难以隔绝CUI的因素。
环氧涂层是有机涂层中一种重要的类型,环氧树脂是其中主要的成膜物,具有良好的延展性,固化速度快且粘附性能高。环氧树脂不仅耐化学腐蚀性优良,耐磨性能良好也是其应用广泛的重要原因。其缺点也很明显,在温度波动严重时,环氧树脂容易出现脆性转变,在应力作用下形成细小裂纹。其有机的化学成分使环氧涂层只适用<120 ℃的环境中,过高的温度将使涂料内部的聚合物碳化,化学键断裂,进而导致涂层失效。即使严格把控涂层施工质量,加强常规检查及维护,环氧涂层在保温层下也只能使用9~13a。
与之相似的另外一种有机涂层是酚醛环氧,其维修性能良好,防腐蚀性能优异,耐酸性、耐水性和抗渗透性均表现优良,常用于<230 ℃的工况。相比其他环氧涂层,酚醛型环氧涂料对喷涂厚度、喷涂工艺等要求更为严苛,对热循环和热冲击下的抵抗力较差。
>热喷铝涂层
热喷铝是制备金属涂层的一种优良的工艺方法,是金属表面防护的新技术之一,其可靠性已经被大量工程项目证实,在恶劣环境下均可对基体表面形成良好保护。大量实验结果表明,经过热喷铝涂层处理后的材料,其防护寿命可达20~30a。然而,单位造价昂贵是制约热喷铝广泛使用的因素。
在海洋石油中,相对于传统有机涂层,热喷铝涂层的主要优点有:
① 寿命更长,维护和检查要求最低;
② 抗机械损伤;
③ 比有机涂层具有更大的耐温范围(-100~500℃);
④ 为浸泡环境中的钢材提供阴极保护。
热喷铝涂层相比传统有机涂层的主要缺点有:
① 应用成本更高;
② 现场施工的难度大;
③ 运营和维护修复的费用较高。
总结以上,如果综合考虑到海洋平台的全寿命周期成本,热喷铝涂层作为一种防腐保护涂层,在CUI的防护应用中比使用有机涂层更加有效,其可靠性使海洋平台的保温层维护和检修费用极大降低,具有很高的应用前景。
结 语
CUI具有隐蔽性,常规的检测手段难以在第一时间发现CUI,往往引发严重的腐蚀失效后才被察觉,从而造成巨大的财产损失。在海洋平台工程中,CUI受到越来越多重视,如何减轻甚至避免CUI,是未来海洋油气发展的重要方向。
未来主要研究方向有:
(1)研究更加优良的防腐涂料,能长效抵抗严苛的CUI环境。无溶剂、高固含量的防腐涂料是未来研究方向之一;
(2)研究憎水性、耐老化性保温材料,集保温和防腐于一体性的复合保温材料是未来研究方向之一;
(3)研究更有效可靠的便捷检测,监测技术,第一时间发现腐蚀线索,提前消除腐蚀因子是CUI预防的研究方向之一;
(4)研究更加高效的金属镀层,如热喷铝等,降低整体综合成本,是能够长效解决CUI的防护方法之一。
随着后续海洋油气田逐步往深海方向开发,平台整体的免维护性要求不断提高,CUI的防护,基于以上或更多研究方向,都有待更多学者和工程师不断的深入研究。
免责声明:本网站所转载的文字、图片与视频资料版权归原创作者所有,如果涉及侵权,请第一时间联系本网删除。
相关文章
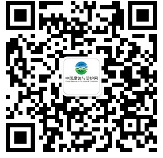
官方微信
《中国腐蚀与防护网电子期刊》征订启事
- 投稿联系:编辑部
- 电话:010-62316606-806
- 邮箱:fsfhzy666@163.com
- 中国腐蚀与防护网官方QQ群:140808414
点击排行
PPT新闻
“海洋金属”——钛合金在舰船的
点击数:7130
腐蚀与“海上丝绸之路”
点击数:5741