Al-Zn-Mg系合金具有强度高、密度小、可焊接、易加工等优点,被广泛应用于轨道交通等领域的结构材料。但实际服役时,这些合金常会发生局部腐蚀如剥落腐蚀等,导致材料表面金属翘起分层,甚至脱落,从而引起材料强度、韧性、抗疲劳等性能下降,威胁构件安全,缩短构件寿命,因此进一步提高Al-Zn-Mg系铝合金的抗剥落腐蚀性能具有重要的意义。
添加微量元素是改善Al-Zn-Mg系合金抗腐蚀性能的一种重要途径。如在Al-Zn-Mg系合金中添加微量Mn元素,可以细化晶粒,而且形成的含Mn弥散相可以降低基体中Zn原子的浓度,同时提高强度和耐蚀性能。但是,Al-Zn-Mg-Mn合金热处理后往往完全再结晶,耐腐蚀性能改善效果有限,具有明显的剥落腐蚀敏感性。因此,还需在Al-Zn-Mg-Mn合金中添加其他微量元素。徐跃等发现将少量混合稀土元素加入到Al-Zn-Mg-Mn合金板材中,可以显着提高其抗腐蚀性能。Li等和Deng等发现,向Al-Zn-Mg-Mn合金板材中复合添加Sc、Zr可以提高其抗腐蚀能力。但是Sc等稀土元素资源稀少,非常昂贵;Zr元素价格较低,向铝合金中添加微量Zr可以显着提高合金的抗再结晶能力,窄化晶界无沉淀析出带,提升强度与耐蚀性能,但是关于单独添加Zr对Al-Zn-Mg-Mn合金抗剥落腐蚀性能的影响,到目前为止还缺乏认识。
因此本文主要研究微量Zr的添加对Al-Zn-Mg-Mn合金板材抗剥落腐蚀性能的影响,并结合OM、EBSD、STEM等显微组织表征结果探讨其影响机理。
1 实验方法
实验材料为3 mm厚Al-Zn-Mg合金热轧板材,使用电感耦合等离子体原子发射光谱仪(ICP-AES)测试化学成分,如表1所示。板材试样在空气炉中加热至470℃固溶处理1 h后,室温水淬,然后在120℃下进行峰时效。
晶粒组织的背散射电子衍射测试在配备EBSD系统的ZEISS EVO MA10型扫描电镜上完成,结果用HKL Channel 5软件进行分析。样品检测前进行电解抛光,所用溶液为10% HClO4+90% C2H5OH(体积分数),电解电压为20 V,电解时间为10 s。透射电镜样品先经机械研磨减薄至厚度约为80 μm,冲成直径为3 mm的小圆片后,在MTP-1A型双喷电解减薄仪上进行减薄。双喷电解液为30% HNO3+70% CH3OH(体积分数),使用液氮将温度控制在-20℃以下,电流为50~70 mA,电压为10~20 V。采用FEI Titan G2 60-300型透射电镜在高角环形暗场像(HAADF)模式下观察试样中的微观组织,加速电压为300 kV,并用能谱仪(EDS)分析第二相化学成分,束斑直径为1 nm。
剥落腐蚀浸泡实验按照GB/T 22639-2008 标准进行,溶液体系为4 mol/L NaCl+0.5 mol/L KNO3+0.1 mol/L HNO3(EXCO溶液),溶液体积与试样被浸面面积之比为25 mL/cm2,每种状态采用平行试样3块。实验时,通过水浴将温度控制在25±2℃,浸泡过程中观察表面腐蚀情况,48 h后取出并根据标准评定剥蚀等级;而后在不同位置切取样品制备金相试样,进一步观察腐蚀情况,测量最大腐蚀深度。金相试样经粗磨、细磨、抛光后用Graff Sargent试剂浸蚀,其成分为(1 mL HF+16 mL HNO3+3 g CrO3+83 mL 蒸馏水),然后在BX51M型光学显微镜下观察显微组织。
采用AUTOLAB M204电化学工作站进行电化学阻抗谱(EIS)测试,采用三电极系统,参比电极为饱和甘汞电极,辅助电极为铂电极,板材试样作为工作电极,测试前将试样抛光,实验面的面积为1 cm2,溶液体系为EXCO溶液,扰动信号为幅度为10 mV、频率0.01 Hz~100 kHz的正弦波,采用ZView软件拟合和分析实验结果。
2 实验结果
2.1 晶粒组织
图1为两种板材轧向-法向(RD-ND)截面的晶粒取向分布图。图中,黑色线条代表大于15°的大角度晶界(GBs),白色线条代表2~15°的小角度晶界,即亚晶界(SGBs)。利用HKL Channel 5软件统计晶粒尺寸(自动截线法)、再结晶分数及大小角度晶界的比例,结果列于表2。Al-Zn-Mg-Mn板材发生了完全再结晶,晶粒尺寸不太均匀,如图1a,沿轧向最大的尺寸可达90 μm,最小尺寸约为3.6 μm,平均尺寸约21.6 μm,沿法向平均尺寸约10.7 μm。Al-Zn-Mg-Mn-Zr板材为再结晶与未再结晶的混合组织,如图1b,再结晶分数为69.4%,亚晶界比例为37.9%,再结晶晶粒的尺寸较均匀,沿轧向平均尺寸约17.6 μm,沿法向平均尺寸约9.3 μm。
图2给出了Al-4.3%Zn-1.2%Mg-0.28%Mn-x%Zr的变温截面相图。虚线所示为Al-Zn-Mg-Mn-Zr板材的成分。由图可知,在Al-Zn-Mg-Mn合金中添加微量Zr元素后,会出现Al3Zr相。合金在凝固时冷却速率高,Zr往往固溶在Al基体中,然后在均匀化过程中以细小弥散的Al3Zr粒子形式析出。Al3Zr粒子较稳定,在后续的塑性变形及热处理时变化不大。图3给出了Al-Zn-Mg-Mn-Zr板材固溶处理后的HAADF-STEM照片。可以看到大量细小弥散的Al3Zr粒子,尺寸约20~30 nm,对晶界有很强的钉扎作用,从而可强烈抑制再结晶。因此,在Al-Zn-Mg-Mn合金中添加微量Zr元素后,再结晶分数从100%下降至69.4%,并保留了较多的亚晶界(图1)。
2.2 晶界第二相及无沉淀析出带
抗剥落腐蚀性能与晶界处的析出相及其成分密切相关,因此对两种板材的晶界处组织和化学特性进行分析,典型HAADF-STEM照片如图4所示。两种板材的大角度晶界处均能观察到η相(MgZn2),晶界附近有明显的无沉淀析出带(PFZ)。在不同晶界上,η相尺寸、间距及PFZ宽度有差别,参考文献的方法统计大角度晶界η相尺寸、间距以及PFZ宽度的尺寸分布,如图5,并将平均尺寸列于表3。由图5a可以看出,Al-Zn-Mg-Mn板材中晶界η相尺寸主要分布在40~80 nm,没有大于100 nm的η相;Al-Zn-Mg-Mn-Zr板材晶界η相尺寸主要分布在40~100 nm,存在大于100 nm的η相。两种板材晶界η相间距分布都不均匀,如图5b,Al-Zn-Mg-Mn板材晶界η相间距集中分布在0~60 nm,而Al-Zn-Mg-Mn-Zr板材晶界η相间距处于80~180 nm之内的比例高于Al-Zn-Mg-Mn板材的。由图5c可知,Al-Zn-Mg-Mn板材晶界PFZ的宽度集中分布在50~70 nm,Al-Zn-Mg-Mn-Zr板材晶界PFZ宽度大都处于30~60 nm之间。由表3可知,在Al-Zn-Mg-Mn板材中添加Zr元素后,大角度晶界上η相的平均尺寸由53.6 nm增至84.2 nm,平均间距由31.5 nm增至72.2 nm,PFZ平均宽度由56.1 nm减小至52.9 nm。
晶界η相的化学成分统计结果见表3。可以看出,Al-Zn-Mg-Mn板材和Al-Zn-Mg-Mn-Zr板材的晶界η相成分差别不大。但是,在Al-Zn-Mg-Mn-Zr板材中,大角度晶界和亚晶界上的η相特征有很大的差别,图6给出了典型的HAADF-STEM照片。在大角度晶界处,η相明显更大,PFZ更明显;在亚晶界上,η相更小,PFZ很窄。另外,在TEM试样制备时发现,大角度晶界上的η相容易被腐蚀,呈现出很多黑色孔洞,如图6,而亚晶界上的η相很少被腐蚀。
2.3 剥落腐蚀浸泡试验
两种板材在浸泡过程中呈现出不同的腐蚀行为。作为代表,图7为浸泡2 h和48 h后板面(RD-TD面)的宏观照片。Al-Zn-Mg-Mn板材在浸泡2 h后表面部分区域出现了明显的黑色腐蚀沟壑;浸泡48 h之后,材料表面一些区域翘起分层剥落,可评为EB级。Al-Zn-Mg-Mn-Zr板材在浸泡2 h后表面部分区域颜色暗淡,无明显腐蚀沟壑;浸泡48 h后板材部分区域出现爆皮,可评为EA级。
浸泡48 h之后,沿RD方向切取若干个样品,观察RD-ND截面的腐蚀情况,如图8所示;并测量其最大腐蚀深度,结果列于表4。采用了Graff Sargent试剂对样品进行浸蚀,可区分部分再结晶组织中的再结晶区域和未再结晶区域,如图8b,白色区域为再结晶组织,灰色区域为未再结晶组织。Al-Zn-Mg-Mn板材有大量晶粒脱落,沿晶腐蚀特征明显,如图8a,腐蚀已经扩展至金属内部,最大腐蚀深度约为593 μm。Al-Zn-Mg-Mn-Zr板材可观察到明显的分层形貌,腐蚀主要沿大角度晶界扩展,如图8b,最大腐蚀深度约为421 μm。
2.4 电化学阻抗谱
图9a、b分别为两种板材在EXCO溶液体系中电化学阻抗谱测试的Nyquist图和Bode图。各样品的Nyquist图均由中高频容抗弧和低频感抗弧组成。由图9a可以看出,Al-Zn-Mg-Mn-Zr板材的容抗弧半径明显大于Al-Zn-Mg-Mn板材的。从图9b可以看出,Al-Zn-Mg-Mn-Zr板材的Z模量值、最大相位角的高度和宽度均大于Al-Zn-Mg-Mn板材的。一般而言,容抗弧半径越大,Z模量的值越大,最大相位角高度和宽度越大,意味着材料的耐蚀性能越好。
根据体系特点选取如图9c所示的等效电路对阻抗谱进行拟合,其中Rs表示溶液电阻,Rp表示极化电阻,Rt表示电荷转移电阻,L为等效电感。Bode图中的最大相位角小于90°,意味着电极双电层偏离理想电容。由于在实际电化学行为中几乎不存在纯电容,因此使用常相位角元件(CPE)来表示原始表面双电层电容,以获得更精确的拟合实验结果。通过ZView软件对实验结果进行拟合,得到各电化学参数如表4所示。电荷转移电阻Rt的值与腐蚀过程中腐蚀电流密度,即腐蚀速率成反比。电荷转移电阻越大,材料的耐蚀性能往往越好。Al-Zn-Mg-Mn-Zr板材的Rt值为383.9 Ω·cm?,显着大于Al-Zn-Mg-Mn板材的227.8 Ω·cm?。因此,交流阻抗谱的测试结果与2.3小节的浸泡实验的结果都表明,微量Zr的添加可以提高Al-Zn-Mg-Mn板材的抗剥落腐蚀性能。
3 讨论
剥落腐蚀是晶间腐蚀与内应力协同作用下发生的一种腐蚀形态,因此晶界析出状态的变化严重影响Al-Zn-Mg合金的抗剥落腐蚀性能。在3.5%NaCl溶液中,晶界平衡η相的自腐蚀电位为-1044.7 mV,PFZ是-685.8 mV,基体是-848.3 mV,因此晶界η相相对于基体及PFZ为阳极,三者构成一组多电极系统,晶界η相一般优先发生阳极溶解,是剥落腐蚀萌生的主要原因。晶界η相的电化学活性与其成分有很大关系,一般而言,Zn、Mg含量升高或者Cu含量降低会增强其电化学活性,使其更容易被腐蚀。根据表3可知,Zr元素的添加对晶界η相的成分不产生明显的影响,因此对剥落腐蚀的萌生影响不大。
晶界上连续分布的η相会使其成为快速溶解的阳极通道,而大尺寸及离散分布的晶界η相可以降低阳极溶解速率。而且晶界上大尺寸的η相能成为“氢陷阱”,使氢原子变成氢气泡而逸出,从而减少晶界处氢原子的含量,抑制了氢脆的出现,从而改善合金的抗剥落腐蚀性能。另外,晶界PFZ的宽化会促使晶界迅速溶解,降低合金的抗剥落腐蚀性能。根据图5和表3,在Al-Zn-Mg-Mn板材中添加Zr元素后,晶界η相尺寸和间距明显变大,PFZ变窄,这有利于抑制大角度晶界的连续溶解,延缓剥落腐蚀的扩展。
另外,晶粒组织对抗剥落腐蚀性能也有重要的影响。由图8b可知,腐蚀主要沿着大角度晶界扩展,这是因为大角度晶界界面能大,时效相富集并且形成了明显的PFZ区,更容易成为腐蚀扩展的通道。亚晶界的存在可以一定程度上抑制腐蚀的扩展,提高合金的抗剥落腐蚀性能。腐蚀裂纹沿亚晶界扩展所需的能量大于沿大角度晶界扩展所需的能量,晶界的应力集中会因亚晶界的存在而发生松弛,因而腐蚀裂纹往往被阻碍于亚晶界处。从图6可以看出,Al-Zn-Mg-Mn-Zr板材中大角度晶界上的η相大部分被腐蚀,留下黑色的孔洞,而亚晶界上的相则基本没有被腐蚀,这也表明大角度晶界的抗腐蚀能力不如亚晶界的。根据图1和表2,Zr元素的添加抑制了再结晶,保留了许多亚晶界,这也有利于板材抗剥落腐蚀性能的提高。
4 结论
(1) 在Al-Zn-Mg-Mn板材中添加微量Zr可以提高其抗剥落腐蚀性能,剥落腐蚀等级由EB级变为EA级,最大腐蚀深度由593 μm降至421 μm。
(2) 微量Zr加入Al-Zn-Mg-Mn板材,抑制了再结晶,细化了晶粒,保留了许多亚晶界,提高了抗剥落腐蚀性能。
(3) Al-Zn-Mg-Mn板材中添加微量Zr后,晶界η相的化学成分基本不变,但尺寸和间距明显变大,PFZ变窄,有利于抑制晶界的连续溶解,提高抗剥落腐蚀性能。
免责声明:本网站所转载的文字、图片与视频资料版权归原创作者所有,如果涉及侵权,请第一时间联系本网删除。
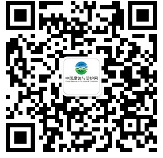
官方微信
《中国腐蚀与防护网电子期刊》征订启事
- 投稿联系:编辑部
- 电话:010-62316606-806
- 邮箱:fsfhzy666@163.com
- 中国腐蚀与防护网官方QQ群:140808414