摘要
研究了纳米铝改性有机硅高温涂层的固化、抗650℃高温氧化性能和耐3.5% NaCl水溶液电化学腐蚀性能。当聚氨酯:有机硅的质量分数达到1:3或更高时,有机硅涂料可以在24 h内完成常温固化。制备出的纳米铝改性有机硅高温涂层表面致密,没有微观裂纹等缺陷。纳米铝改性的有机硅涂层显著提高了304不锈钢抗氧化性能,经1028 h氧化实验,基体几乎没有发生氧化,涂层没有出现开裂和剥落。纳米铝改性的有机硅涂层还显著提高了氧化后的304不锈钢耐氯化钠水溶液腐蚀性能,无涂层的304不锈钢氧化后形成的氧化膜低频阻抗仅3.2 Ω·cm2,而涂装涂层的不锈钢的低频阻抗约为1.1×105 Ω·cm2。
关键词: 材料失效与保护 ; 耐高温氧化 ; 纳米改性 ; 有机硅 ; 常温固化 ; 304不锈钢
不锈钢是常用的结构材料,具有优异的耐腐蚀性能。不锈钢的高耐腐蚀性能与其表面形成的富铬CrOOH钝化膜或Cr2O3氧化膜有关[1,2,3]。不锈钢表面钝化膜的结构和厚度与温度有密切的关系。在50~450℃随着温度的提高这种钝化膜的厚度增加,但是其性质不变[4]。在350℃氧化膜的晶粒尺寸很小且表面粗糙度较低,随着温度的升高晶粒的尺寸减小;氧化膜的致密性随着温度的升高而降低,在50℃形成部分钝化膜[5]。304不锈钢在中高温(500~800℃) 发生氧化,超过800℃氧化更严重[6]。在高温下氧化膜的结构发生变化,除了含有铬和铁的氧化物外还生成具有铁铬尖晶石结构的氧化膜。氧化膜中有较大的裂纹且不均匀、疏松易剥落[7,8]。因此,在温度超过500℃时有必要采取措施以提高其抗氧化性能。
使用耐高温涂料,是防止材料高温氧化的重要措施。涂料和涂层的成分可控、适应性强且工艺简便。耐高温涂料在200℃以上不变色、不脱落且保持良好的机械性能。有机硅树脂是以高键能(443.7kJ·mol-1)的硅氧键Si-O[9]为分子主链的半无机高分子材料。有机硅涂料具有优异的热稳定性和耐热性能,可用于烟囱、锅炉、消音器、燃烧室、热转换器和排热管等高温设备[10]。高极性Si-O键中的Si、O原子的电负性差异很大,可屏蔽所连接的烃基基团,使有机硅材料具有较高的抗氧化性能。纯有机硅树脂的使用温度不超过300℃,因此要研制耐热性能更优异的树脂。Jia等[11]研制了一种含有亚苯基新型有机硅树脂,其开始降解温度为500.3℃,在900℃的失重仅为14.4%。孙举涛等[12]研制的含有端羟基的聚甲基苯基硅树脂在空气中的初始分解温度为250℃,在500℃的失重为18%。在有机硅树脂中掺入苯基可提高其热稳定性和疏水性[13]。在有机硅树脂涂料中掺入耐热氧化物填料,如Fe2O3[14]、Al2O3和ZnO [15]、纳米金属粉[16]等,可提高其耐热性能。
在高温下使用时有机硅涂料树脂中的甲基、乙基等有机基团分解挥发,产生的微观孔洞使其致密性降低。纳米金属粉如Al粉在高温下快速氧化[16]。这些纳米Al粉氧化物均匀弥散分布,体积膨胀弥合了有机成分挥发产生的微观孔洞,使涂层的致密性提高,进而提高了涂层的防护作用。纳米TiO2具有较高的耐高温性能和良好的触变性能,添加少量的这种粉体即可改善涂料的储存和沉降性能。有机硅涂料需要在150℃以上的温度长时间固化[17],这限制了在大型零部件和长管线的应用。因此,实现有机硅树脂涂料的常温固化对于其应用极为重要。鉴于此,本文制备一种纳米改性常温固化耐高温有机硅涂料,研究其常温固化行为和抗高温氧化性能。
1 实验方法
1.1 涂料和涂层的制备
试验基体为304不锈钢,其名义化学成分(%,质量分数)为C 0.04, Si 1.48, P 0.03, S 0.03, Mn 1.38, Cr 16.86, Ni 8.45, Fe余量。样品尺寸为20 mm×10 mm×2 mm,表面经喷砂处理(80目玻璃珠,喷砂压力0.5 MPa)。
实验用原料包括工业级纯度聚酯改性有机硅树脂和聚氨酯树脂、亚铬酸铜(CuCr2O4)、纳米铝粉(Al)和纳米二氧化钛粉(TiO2)、防沉剂,以及分析纯二甲苯。
按比例称取聚酯改性有机硅树脂(RS)、亚铬酸铜(CuCr2O4)、纳米铝粉(Al)、纳米二氧化钛粉(TiO2)、防沉剂和二甲苯并将其放入容器内进行预混合,然后连同粒径为1 mm的硅酸锆研磨珠一起放入MiniZeta 03 型循环砂磨机中,以2500 r/min的转速研磨20 min,制得组分I。按比例称取组分I和聚氨酯固化剂,将二者混合均匀后用200目不锈钢网过滤,制得涂料。
用空气喷涂法将涂料喷涂到304不锈钢表面。将第一道喷涂后的试样在室温中放置15~20 min,然后喷涂第二道。待喷涂第二道的涂层表干后在室温干燥环境中固化24 h。
采用红外光谱法(FTIR,Spectrum Two, PerkinElmer, USA)研究涂料的固化行为,确定聚氨酯树脂的最佳比例,进而确定固化剂的最佳含量,并在此基础上制备纳米改性有机硅涂料。测试波数的范围为4000~400 cm-1,精度为4 cm-1。
1.2 性能测试
在马弗炉中测试304不锈钢和涂装纳米改性有机硅涂层的304不锈钢在650℃空气中的氧化行为。用扫描电子显微镜(SEM,FEI INSPECT F50)观察原始涂层和氧化后不锈钢和涂层的微观形貌,并测量EDS能谱 (INCA, X-Max)分析涂层和304不锈钢表面氧化物的成分。使用X-射线衍射仪(XRD,X′Pert Pro Panalytica Co.)测试涂层氧化前后的相结构。采用电化学方法测试氧化前后不锈钢表面氧化膜在室温、1000 Hz条件下的Mott-Schottky特征以及电化学交流阻抗行为。测试介质为3.5% NaCl水溶液,所用仪器为PARSTAT 2273电化学工作站,采用三电极体系:辅助电极为铂片,参比电极为饱和甘汞电极(文中所有电位均相对于饱和甘汞电极电位),工作电极为氧化前后不锈钢试样。测试电化学交流阻抗的激励信号为10 mV正弦波,测试频率为105~10-2 Hz。
2 结果和讨论
2.1 有机硅涂料的常温固化行为
表1列出了不同含量聚氨酯树脂对有机硅树脂固化性能。从表1可见,聚氨酯树脂添加量小于20%的涂料放置24 h也不能完全固化,聚氨酯树脂的添加量大于25%的涂料放置24 h后完全固化。因为聚氨酯树脂的含量过高影响涂料的耐高温性能,故取聚氨酯固化剂与有机硅树脂的比例为3:7。
表1 有机硅树脂的固化性能
有机硅树脂、聚氨酯树脂和固化后涂料的红外光谱如图1所示。与有机硅树脂固化性能相关的基团是峰位为3500~3000cm-1[18,19]的硅羟基≡SiOH(图1a),有机硅树脂固化的基本形式是在高温(100~250℃)下有机硅树脂中的硅羟基之间的脱水缩合,进而形成高交联度的网状结构[20]。从图1可以看出,当有机硅与30%聚氨酯树脂混合并在常温环境中固化24 h后,FTIR谱中的硅羟基-OH峰消失,表明有机硅树脂中的-OH基团与聚氨酯树脂中的氨酯键NCO(2260~2280 cm-1)发生化学反应而实现了有机硅树脂的固化(图1b)。固化后的有机硅涂料保持了有机硅和聚氨酯的大部分结构(图1c)。
图1 有机硅树脂、聚氨酯树脂和固化后涂料的红外光谱图
2.2 在650℃的氧化行为
304不锈钢(304SS)和涂装涂层的不锈钢(Coatings)在650℃干燥空气中的氧化动力学曲线如图2所示。涂装涂层的304不锈钢料在650℃加热5 min后快速失重,因为有机硅涂层中的有机成分如甲基Si-CH3等在高温下裂解形成H2O、CO和CO2等小分子挥发[23,24]。在随后的氧化过程中涂层重量几乎不发生变化,保持了稳定的状态(图2a),表明纳米改性有机硅涂层具有良好的高温稳定性。
图2 304不锈钢和涂层在650℃的氧化动力学曲线
为了更清晰地分析涂层对不锈钢试样氧化速率的影响,以氧化5min时试样的质量作为零点,绘制了氧化5 min~1028 h这一过程中带涂层试样的质量变化和不锈钢原始试样的质量变化,如图2b所示。从图2.b可见,不锈钢在650℃氧化初期出现了失重,氧化15 h后出现连续而缓慢的增重,直到氧化约400 h出现较为显著的增重,氧化890 h的增重量约为0.076 mg/cm2。在高温空气中304不锈钢表面主要形成保护性的Cr2O3,随着氧化时间的延长还出现Fe2O3等氧化产物[21]。不锈钢氧化初期失重的原因可能是初期氧化膜主要为Cr2O3,它进一步氧化可形成挥发性CrO3[22];随着氧化膜中Fe含量的增加,导致氧化速率提高和挥发性CrO3形成速率降低。涂装涂层的不锈钢在5 min至200 h期间出现小幅度失重,之后质量变化很小,表明涂层在200 h之前仍有少量的热解,在整个实验过程中基体在涂层的保护作用下氧化速率很低。
Mott-Schottky方法是评价金属材料表面钝化膜性质的一种有效方法[25,26]。图3给出了304不锈钢的Mott-Schottky曲线。可以看出,未氧化的304不锈钢的Mott-Schottky曲线在电位较负的线性区斜率为正,表明在此电位范围内不锈钢表面自然形成的钝化膜是以氧空位为主的n型半导体。而当电位高于0.52 V时线性区斜率的负值,表明钝化膜是以金属空位为主的p型半导体[27,28]。相比之下,氧化的304不锈钢试样(304SS oxided)在650℃氧化890 h后的Mott-Schottky曲线,只有斜率为负的线性区,表明不锈钢表面氧化膜是以空位为主的p型半导体,与Cr2O3的半导体性质相符。
图3 304不锈钢的Mott-Schottky曲线
采用电化学交流阻抗技术测试了650℃氧化后不锈钢和涂装涂层的不锈钢的腐蚀行为,如图4所示。从图4a, c可以看出,氧化的304不锈钢和涂装涂层的不锈钢均具有高频和低频两个时间常数。低频时间常数反映了涂层下基体不锈钢的电化学反应信息,而高频时间常数反映了涂层或不锈钢氧化层的信息。可以看出,涂装涂层的不锈钢的阻抗显著大于无涂层不锈钢的阻抗。常用低频(0.01 Hz)下的阻抗模值|Z|0.01评价涂层的防护性能[29,30]。从图4b可以看出,氧化后304不锈钢的|Z|0.01约为3.2 Ω·cm2,而涂装涂层的不锈钢的|Z|0.01约为1.1×105 Ω·cm2,表明在650℃氧化后不锈钢表面氧化膜已呈导通状态,完全失去了保护作用,而涂层显著提高了不锈钢在氯化钠溶液中的耐腐蚀性能。
图4 304不锈钢氧化后的交流阻抗谱
2.3 涂层的氧化形貌和结构
图5给出了不锈钢和涂层的微观SEM形貌。从图5可见,原始涂层的表面致密,没有微观裂纹等缺陷,有利于涂层抗氧化和耐腐蚀性能,涂层中还弥散分布有细小的铜铬黑颗粒(图5a)。涂层在650℃氧化1028 h后表面粗糙度有所提高,是涂层中有机成分的分解挥发造成的,但的没有出现裂纹等微观缺陷,保持了连续性和完整性(图5b)。涂层氧化后的截面微观结构(图5c)表明,涂层完整而致密,与基体不锈钢结合良好,基体不锈钢与涂层之间未出现剥落破坏也没有发生互扩散。EDS能谱分析表明,涂层中未检测到Fe元素,元素及其原子分数列于如表2。结果表明,在高温作用下涂层对氧起到了屏蔽作用,没有氧通过涂层到达基体金属表面而避免了不锈钢基体的氧化。相比之下,304不锈钢在650℃经890 h氧化后表面由细小颗粒状氧化物构成(图5d),氧化层的厚度约为1 μm (图5e),EDS能谱分析表明,不锈钢表面氧化物主要由Fe、Cr、Mn、O和Ni构成(图5f)。
图5 原始和氧化后的涂层以及304不锈钢氧化后的SEM形貌和成分
表2 氧化后涂层试样的原子重量百分比
图6给出了原始涂层和氧化1028 h后的涂层的XRD谱。从图6可以看出,原始涂层中主要包括亚铬酸铜、铝和二氧化钛。在650℃氧化后涂层中的亚铬酸铜和二氧化钛没有变化也没有检测到金属铝。在XRD谱中出现了明显的Al2O3峰,表明在氧化过程中纳米铝粉与扩散到涂层中的氧气发生化学反应生成了Al2O3。
图6 原始涂层和氧化后涂层的XRD谱
纳米铝粉比表面积大、表面原子数多、表面活性大,其化学反应活性高于微米铝粉的特点[31]。纳米铝粉在温度高于500℃时即发生强烈的氧化增重反应[32,33],而微米铝粉只有温度达到1000℃以上时才出现明显的氧化[34]。在氧化过程中,氧通过吸附和扩散向涂层内部渗透,涂层表面的铝在650℃即与氧气发生反应形成氧化铝。当氧进一步向涂层内部扩散时,由于纳米铝粉均匀分布在涂层内部,进入涂层的氧遇到纳米铝粉即生成氧化铝,降低了氧气向涂层内部扩散的速度。同时,由于铝粉在氧化形成氧化铝的过程中体积膨胀,其PBR(氧化物的体积与消耗的金属体积之比)值为1.28[35]。于是,在纳米铝粉消耗扩散进入的氧的同时,由于铝氧化反应的体积膨胀填充了有机硅树脂热裂解而形成的孔隙,提高了涂层的致密性,使涂层在较高温度下具有较高的防护性能。
3 结论
(1) 当聚氨酯:有机硅的质量分数达到1:3或更高时,有机硅涂料可以在24 h内完成常温固化。
(2) 纳米铝改性的有机硅涂层显著提高了304不锈钢抗650℃空气氧化性能,经1028 h氧化实验,基体几乎没有发生氧化,涂层也没有出现开裂和剥落。
(3) 纳米铝改性的有机硅涂层显著提高了氧化后的304不锈钢耐氯化钠水溶液腐蚀性能,无涂层的304不锈钢长时间氧化后形成的氧化膜低频阻抗仅3.2 Ω·cm2,而涂装涂层的不锈钢的低频阻抗约为1.1×105 Ω·cm2。
免责声明:本网站所转载的文字、图片与视频资料版权归原创作者所有,如果涉及侵权,请第一时间联系本网删除。
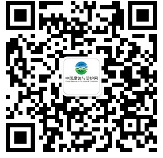
官方微信
《中国腐蚀与防护网电子期刊》征订启事
- 投稿联系:编辑部
- 电话:010-62316606-806
- 邮箱:fsfhzy666@163.com
- 中国腐蚀与防护网官方QQ群:140808414