摘要
研究了充氢时间、充氢电流密度、晶体结构对不锈钢氢脆敏感性的影响。结果表明:对于铁素体不锈钢,随着充氢时间的延长、电流密度的增大,塑性显著降低,氢脆敏感性大幅度增加;通过SEM观察实验钢断口形貌,断裂类型由韧性断裂转变为脆性断裂。而相同条件下,奥氏体不锈钢氢脆敏感性较低,抗氢脆性能较好。充氢后实验钢表面存在大量H,且氢含量随试样深度逐渐降低,晶界可能作为氢陷阱影响实验钢的氢脆敏感性。
关键词: 电化学充氢; 铁素体不锈钢; 奥氏体不锈钢; 氢脆敏感性
氢能以及核能作为高效、清洁的能源受到了世界范围内的广泛关注。奥氏体不锈钢具有较高的耐腐蚀性和良好的力学性能,广泛应用于石油化工和核电站的管道系统中,被认为是氢存储的候选材料[1]。与奥氏体不锈钢相比,铁素体不锈钢具有更高的屈服强度和更强的抗应力腐蚀开裂能力。此外,作为奥氏体主要合金元素Ni的价格不稳定且偏高[2]。因此,有用铁素体不锈钢取代奥氏体不锈钢的发展趋势。实践证明,两种不锈钢在加工或使用过程中从环境中吸收H会导致材料开裂失效,尤其是在高应力集中区域[3]。
目前,关于不锈钢氢脆的研究大部分集中在加工工艺对氢脆的影响,系统地研究充氢参数对氢脆敏感性的影响较少,而且具体的作用机制尚未明确。另外,H是在钢铁中扩散速度最快的元素,其原子半径最小,在低温区仍有很强的扩散能力,用传统能谱法很难检测出H的存在。Tarzimoghadam等[4]将充氢样品浸入4.3 mmol/L Ag[K(CN)2]溶液中1 h,并利用金属表面原子氢的特殊活性将Ag+还原为Ag,然而Ag[K(CN)2]溶液有剧毒性。Li等[5]分析了材料内裂纹扩展模式以及H的分布。Fan等[6]利用三维原子探针显微分析法检测了H在残余奥氏体中的分布。Chen等[7]利用低温原子探针观察到了具有特定微观结构特征的钢中的H。但这些高端设备使用成本高,实验条件要求高,纳米针状样品制作条件苛刻。本文以Cr15铁素体不锈钢和304奥氏体不锈钢为研究对象,通过一系列实验研究不同充氢时间、不同充氢电流密度以及晶体结构对不锈钢抗氢脆性能的影响,通过飞行时间二次离子质谱仪 (TOF-SIMS) 成功检测到H的分布,为氢脆机理的深入研究提供有力的证据,同时为设计抗氢脆不锈钢提供理论支持。
1 实验方法
1.1 实验材料
本实验主要是以0.8 mm厚退火态Cr15铁素体不锈钢和0.8 mm厚固溶态304奥氏体不锈钢为研究对象,两种实验钢均由太钢提供,化学成分如表1所示。
表1 实验用钢的化学成分
1.2 不同充氢参数实验
针对Cr15铁素体不锈钢:将钢板通过电火花线切割制成标准拉伸试样,尺寸如图1所示。研磨抛光后在1 mol/L NaOH+1 g/L硫脲溶液中电化学充氢,充氢装置如图2所示。然后对未充氢和充氢后的拉伸试样进行3.3×10-4/s速率慢应变拉伸[8]。
图1 室温拉伸试样尺寸
图2 电化学充氢示意图
设计4组充氢参数:未充氢,记为A;充氢电流密度为10 mA/cm2,充氢时间为24 h,记为B;充氢电流密度为10 mA/cm2,充氢时间为48 h,记为C;充氢电流密度为20 mA/cm2,充氢时间为24 h,记为D。其中A,B和C可以对比不同充氢时间对氢脆敏感性的影响;A,B和D可以对比不同充氢密度对氢脆敏感性的影响。
1.3 两种不同晶体结构钢的对比实验
铁素体不锈钢具有bcc晶体结构,而奥氏体不锈钢的晶体结构为fcc。为了比较两种晶体结构对氢脆敏感性的影响,设计304奥氏体不锈钢与Cr15铁素体不锈钢进行氢脆敏感性的比较实验。
充氢装置和电解液同上,参考上述Cr15铁素体不锈钢的充氢电流密度10 mA/cm2,充氢时间24 h对304奥氏体不锈钢进行电化学充氢,比较两种晶体结构材料的氢脆敏感性。随后对304奥氏体不锈钢继续增大充氢参数,研究其氢脆敏感性的变化规律。设计3组参数:(1) 充氢电流密度为20 mA/cm2,时间24 h;(2) 充氢电流密度为50 mA/cm2,时间48 h;(3) 充氢电流密度为100 mA/cm2,时间96 h。
所有样品均采用标准金相技术进行研磨和抛光,并用配备在场发射扫描电子显微镜 (FE-SEM,Tescan Mira 3) 上的电子背散射衍射仪 (EBSD,Oxford) 进行检测。在25 V电压和-30 ℃条件下,采用5% (体积分数) 高氯酸溶液和95% (体积分数) 无水乙醇的混合溶液对每个试样的法向-轧制方向横截面进行60 s的电解抛光。EBSD数据用HKL-Channel软件分析。此外,还利用Smartlab X射线衍射仪 (XRD) 对材料的物相进行检测。采用电子万能试验机 (DNS 200) 测定充氢前后试样的室温拉伸强度和延伸率,采用3个重复样本计算平均值。用FE-SEM对断口形貌进行表征。用安装在Gallium FIB-SEM系统 (S8000G) 上的TOF-SIMS,在1nA电子束和30 kV电压下,对充氢后样品中的H分布进行检测。
2 结果与讨论
2.1 实验钢微观组织
图3为Cr15退火态铁素体实验钢和304固溶态奥氏体实验钢的IPF图。可以看到,Cr15不锈钢组织为等轴状的晶粒,304不锈钢组织由等轴奥氏体和退火孪晶组成。图4为两种实验钢的XRD谱,可以看到两种实验钢都为单相组织,Cr15不锈钢中为单相铁素体组织,304钢中为单相奥氏体组织。
图3 Cr15不锈钢和304奥氏体不锈钢的IPF图
图4 Cr15不锈钢和304不锈钢的XRD谱
2.2 不同充氢参数对Cr15实验钢氢脆敏感性的影响
因为H在钢中扩散速度很快,试样充氢结束0.5 h内要及时进行实验,防止H逸出,确保实验的准确性。对4组Cr15实验钢电化学充氢前后试样进行室温拉伸实验,拉伸方向平行于试样的轧制方向,拉伸后数据如表2所示。用IHE(δ)=(1-δH/δ0)×100%表示氢脆敏感性[9,10],式中,δ0为未充氢时的伸长率,δH为充氢后的伸长率。IHE(δ) 即为材料的氢致伸长率降低率,IHE(δ) 越大,材料的抗氢脆性能越差,氢脆敏感性越高。
表2 充氢前后Cr15不锈钢钢拉伸实验结果
将表2数据整理分别得到对应不同充氢时间和不同电流密度下Cr15不锈钢的力学性能,如图5所示。其中,图5a为相同电流密度 (10 mA/cm2),不同时间(0,24,48 h) 充氢对Cr15不锈钢力学性能的影响;图5b为相同时间 (24 h),不同电流密度 (10和20 mA/cm2)充氢对Cr15不锈钢力学性能的影响。其中,Rm表示抗拉强度,Rel表示屈服强度,A表示断后伸长率。
图5 不同充氢条件下Cr15不锈钢力学性能的变化
从表2及图5中可以看出,与未充氢的原始试样相比,充氢后实验钢的Rel和Rm变化不大,而A却显著降低,即塑性大幅度降低,所设计充氢参数下实验钢的氢脆敏感性都达到50%以上。一方面,当电流密度为10 mA/cm2时,随着充氢时间的延长,塑性继续降低,氢脆敏感性升高,由充氢24 h的50.0%上升到48 h的62.5%;另一方面,当充氢24 h时,随着充氢电流密度的增大,强度依然变化不大,塑性降低,氢脆敏感性升高,由10 mA/cm2时的50.0%上升到20 mA/cm2时的56.2%。
根据美国NASA8-30744判定合金氢损伤程度标准[11]:当IHE(δ)>50%时,为极度氢损伤;当IHE(δ)> 25%时,为严重氢损伤;当IHE(δ)>10%时,为发生氢损伤;当IHE(δ)<10%时,为低氢损伤。本文中实验钢在电化学充氢后的IHE(δ) 均大于50%,所以均发生了极度氢损伤。
钢充氢后发生氢损伤,其塑性的降低有多方面的原因。一是扩散进入金属内部的H降低了金属原子之间的结合力;二是聚集的H会结合成H2或与金属形成氢化物,体积变化导致产生附加应力;三是H的吸附使金属的表面能降低,从而使裂纹易于形核和扩展。根据不锈钢中普遍认同的氢脆机制-氢增强局部塑性机制 (HELP):在拉应力状态下,材料内部产生大量位错,积聚的H降低了位错运动的阻力,导致位错迁移率增加,同时可能促进局部滑移,产生局部塑性变形,从而导致材料过早失效。此外,位错作为氢陷阱捕捉H,在位错运动的同时携带着H进行扩散,又在一定程度上促进了氢扩散[9]。
图6为4组Cr15不锈钢试样拉伸后断口的SEM像。可以看出,未充氢试样的拉伸断口由大量的韧窝组成 (图6a),尺寸比较均匀,且较深,为典型的韧性断口;充氢24 h的试样断口大部分表现为解理断裂;充氢48 h的试样断口完全呈大片的撕裂状,表现为明显的脆性断裂特征[12],并出现裂纹 (图6c)。由此可见,随着充氢时间的延长,实验钢的氢损伤程度增加,由韧性断裂逐渐变为脆性断裂。电流密度为20 mA/cm2的充氢试样断口也主要为解理状,几乎看不到韧窝,有明显的裂纹[13] (图6d),且能看出虽然仍以穿晶准解理断裂为主,但出现部分沿晶断裂。随着充氢电流密度的增加,Cr15实验钢的氢损伤程度增加,由韧性断裂逐渐变为脆性断裂,断裂模式由穿晶断裂逐渐变为沿晶断裂,这是因为H在晶界处富集,故晶界上氢浓度较高,达到一定浓度后,会导致沿晶断裂[14]。
图6 不同充氢参数下Cr15不锈钢试样拉伸断口形貌
利用TOF-SIMS[15]对在20 mA/cm2电流密度下充氢24 h的Cr15钢试样进行检测,表面氢分布如图7所示。可见,H在试样表面上的分布并不均匀,亮点处代表氢含量分布最多的位置,可以粗略看出亮点大部分分布在晶界位置,晶界可能作为氢陷阱对扩散氢进行捕捉。
图7 充氢后Cr15不锈钢表面氢分布
2.3 不同晶体结构对氢脆敏感性的影响
对4组电化学充氢前后的304奥氏体不锈钢进行拉伸实验,结果如表3。可见,随着充氢电流密度的增大和充氢时间的延长,实验钢的A逐渐降低,氢脆敏感性逐渐升高,但幅度很低,在50 mA/cm2、48 h充氢后继续增加参数幅度,氢脆敏感性不再发生变化。根据NASA8-30744判定合金氢损伤程度标准,当IHE (δ)>10%时,发生氢损伤。本实验钢只有在电流密度50 mA/cm2下充氢48 h 后才发生轻微损伤。
表3 充氢前后304不锈钢拉伸实验结果
比较表2和3可见,厚度相同时,bcc结构的铁素体不锈钢的抗氢脆性能明显低于fcc结构的奥氏体不锈钢。H在奥氏体不锈钢中的扩散系数 (1.8×10-16~8×10-16 m2·s-1) 远远低于铁素体钢中的 (10-12 m2·s-1),故H向奥氏体不锈钢内的渗透、扩散、富集是比较困难的[11]。而且,实验钢中H的溶解度影响抗氢脆性能,奥氏体钢具有更高的氢溶解度,是铁素体钢的103倍。故在对抗氢脆性能要求比较高的情况下,铁素体不锈钢并不能取代奥氏体不锈钢。
H的扩散深度d可以粗略地用下式表示[11,16]:
其中,D为氢扩散系数,t为充氢时间。按H在奥氏体不锈钢中的扩散系数为10-16 m2·s-1,在铁素体钢中的为10-12 m2·s-1,经过粗略计算,铁素体不锈钢充氢24 h的氢扩散深度为0.42 mm,奥氏体不锈钢充氢24 h的氢扩散深度为4.16×10-3 mm。图8和9分别为充氢后两种实验钢在电流密度为20 mA/cm2条件下,充氢24 h后周边区域与中心区域的断口形貌。试样厚度只有0.8 mm,可看出铁素体不锈钢充氢后H可以渗透整个试样。图8为Cr15铁素体不锈钢的断口形貌,图8a为断口全貌,图8b~c分别对应图8a中框选的位置,可以看到3个位置处均为脆性断裂。图9为304奥氏体不锈钢的断口形貌,可以看到奥氏体不锈钢仅仅表面发生脆性断裂,中心区域仍为韧性断裂,能明显看到脆性断裂和韧性断裂的过渡形貌 (图10c)。
图8 充氢后Cr15铁素体不锈钢断口形貌
图9 充氢后304奥氏体不锈钢断口形貌
图10 电化学充氢后304不锈钢中H的分布
为了更直观地观察到H的分布,通过TOF-SIMS对在电流密度20 mA/cm2下充氢24 h的304奥氏体不锈钢试样进行了检测,检测结果如图10所示。
图10a中显示,充氢后304实验钢中成功检测到了H的存在;从图10b中可以看出,在试样表面分布着大量的H,即电化学充氢后大量的H集中在试样表面;从图10c中可见,H分布随着深度方向逐渐减少,这也解释了为什么奥氏体不锈钢拉伸断口周边区域是脆性断裂,而中心区域仍为韧性断裂。
3 结论
(1) 随着充氢时间的延长,充氢电流密度增大,铁素体不锈钢塑性显著降低,氢脆敏感性升高,断裂类型由韧性断裂变为脆性断裂。
(2) 在相同条件下,奥氏体不锈钢充氢后塑性稍有降低,即使充氢参数增大,塑性降低幅度也很小,且脆断仅发生在试样表面。即奥氏体不锈钢比铁素体不锈钢氢脆敏感性低,抗氢脆性能较好。
(3) 电化学充氢后,H大部分分布在试样表面,随深度增加而逐渐减少,钢中晶界可能作为氢陷阱起捕捉H作用。
参考文献
[1]
Michler T, San Marchi C, Naumann J, et al.
Hydrogen environment embrittlement of stable austenitic steels
[J]. Int. J. Hydrogen Energy, 2012, 37: 16231
[本文引用: 1]
[2]
San Marchi C, Michler T, Nibur K A, et al.
On the physical differences between tensile testing of type 304 and 316 austenitic stainless steels with internal hydrogen and in external hydrogen
[J]. Int. J. Hydrog. Energy, 2010, 35: 9736
[本文引用: 1]
[3]
Kim S M, Chun Y S, Won S Y, et al.
Hydrogen embrittlement behavior of 430 and 445NF ferritic stainless steels
[J]. Metall. Mater. Trans., 2013, 44A: 1331
[本文引用: 1]
[4]
Tarzimoghadam Z, Rohwerder M, Merzlikin S V, et al.
Multi-scale and spatially resolved hydrogen mapping in a Ni-Nb model alloy reveals the role of the δ phase in hydrogen embrittlement of alloy 718
[J]. Acta Mater., 2016, 109: 69
[本文引用: 1]
[5]
Li X G, Gong B M, Deng C Y, et al.
Failure mechanism transition of hydrogen embrittlement in AISI 304 K-TIG weld metal under tensile loading
[J]. Corros. Sci., 2018, 130: 241
[本文引用: 1]
[6]
Fan Y H, Zhang B, Yi H L, et al.
The role of reversed austenite in hydrogen embrittlement fracture of S41500 martensitic stainless steel
[J]. Acta Mater., 2017, 139: 188
[本文引用: 1]
[7]
Chen Y S, Lu H Z, Liang J T.
Observation of hydrogen trapping at dislocations, grain boundaries, and precipitates
[J]. Science, 2020, 367: 171
[本文引用: 1]
[8]
Zhu X.
An investigation into the hydrogen embrittlement mechanism in the 3rd Generation advanced high strength automotive steels employing TRIP effect
[D]. Shanghai: Shanghai JiaoTong University, 2016
[本文引用: 1]
朱旭.
基于TRIP效应的第3代先进高强汽车用钢氢脆机制的研究
[D]. 上海: 上海交通大学, 2016
[本文引用: 1]
[9]
Zhu X, Zhang K, Li W, et al.
Effect of retained austenite stability and morphology on the hydrogen embrittlement susceptibility in quenching and partitioning treated steels
[J]. Mater. Sci. Eng., 2016, A658: 400
[本文引用: 2]
[10]
Jiang W, Gong J M, Wang Y F, et al.
Plasticity comparison of 304L austenitic stainless steel before and after electrochemical hydrogen charging
[J]. Mater. Mechan. Eng., 2012, 36(2): 28
[本文引用: 1]
蒋旺, 巩建鸣, 王艳飞等.
电化学充氢前后304L奥氏体不锈钢的塑性对比
[J]. 机械工程材料, 2012, 36(2): 28
[本文引用: 1]
[11]
Lai C L, Tsay L W, Chen C.
Effect of microstructure on hydrogen embrittlement of various stainless steels
[J]. Mater. Sci. Eng., 2013, A584: 14
[本文引用: 3]
[12]
Lu H H, Guo H K, Du L Y, et al.
Formation of intermetallics and its effect on microstructure and mechanical properties of 27Cr-4Mo-2Ni super ferritic steels
[J]. Mater. Charact., 2019, 151: 470
[本文引用: 1]
[13]
Bak S H, Ali Abro M, Lee D B.
Effect of hydrogen and strain-induced martensite on mechanical properties of AISI 304 stainless steel
[J]. Metals, 2016, 6: 169
[本文引用: 1]
[14]
Michler T, Naumann J.
Microstructural aspects upon hydrogen environment embrittlement of various bcc steels
[J]. Int. J. Hydrogen Energy, 2010, 35: 821
[本文引用: 1]
[15]
Tarzimoghadam Z, Ponge D, Klöwer J, et al.
Hydrogen-assisted failure in Ni-based superalloy 718 studied under in situ hydrogen charging: The role of localized deformation in crack propagation
[J]. Acta Mater., 2017, 128: 365
[本文引用: 1]
[16]
Fan Y H.
Effect of microstructures on the hydrogen embrittlement of stainless steels
[D]. Shenyang: University of Science and Technology of China, 2019
[本文引用: 1]
范宇恒.
不锈钢微观组织结构对其氢脆性能的影响
[D]. 沈阳: 中国科学技术大学, 2019
[本文引用: 1]
免责声明:本网站所转载的文字、图片与视频资料版权归原创作者所有,如果涉及侵权,请第一时间联系本网删除。
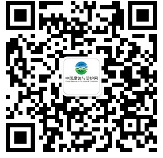
官方微信
《中国腐蚀与防护网电子期刊》征订启事
- 投稿联系:编辑部
- 电话:010-62316606-806
- 邮箱:fsfhzy666@163.com
- 中国腐蚀与防护网官方QQ群:140808414