摘要
研究了化学组分和显微组织结构对AZ31,AZ91,AM60和ZK61等4种镁合金在含有不同浓度NH4NO3的0.1 mol/L NaCl溶液中腐蚀行为的影响。通过浸泡实验、电化学测试、SEM和CLSM表面分析等探讨了4种镁合金的腐蚀机理。结果表明,NH4NO3的存在会加快镁合金的腐蚀;并且由于在特定浓度范围内,Cl-,NH4+和NO3-的协同作用,会发生自催化点蚀。不同镁合金的耐蚀性与合金的化学成分和显微组织密切相关。
关键词: 镁合金; 硝酸铵; 自催化点蚀; 化学组分; 显微结构
镁合金是最轻的一种金属结构材料,由于其低密度和良好的力学性能而受到越来越多的关注 [1],被广泛应用于航空、航天和汽车工业[2-4]。然而,由于较差的耐腐蚀性能[5],其应用范围比铝合金更受限制。雾霾的存在对金属的腐蚀行为有一定的影响。Cui等[6]研究了AZ31镁合金在Cl--NH4+-NO3-溶液体系内的腐蚀机制,研究结果表明特定的溶液体系会影响暴露在雾霾环境中镁合金的腐蚀过程。
对于镁合金而言,Al可以通过形成第二相 (β-Mg17Al12) 显著提高合金的抗拉强度[7]。添加一定量的Al会提高镁合金中β相的含量,当β相形成连续网状结构时,会显著改善材料的耐腐蚀性[8]。Zn对于镁合金的强度也有着至关重要的影响,它的存在可以抑制Fe及Ni对镁合金腐蚀的不利影响。当Zn含量较少时 (Zn<1%),可以提高Al在镁合金中的固溶度,提高Al的固溶强化作用[9]。Song等[10]认为,为保证镁合金的耐蚀性能,AZ系镁合金中的Zn添加量应该控制在1%~3% (质量分数)。Mn在镁合金中会与Fe形成熔渣,可以在一定程度上消除Fe对于镁合金耐腐蚀性的不利影响。因此,一般耐腐蚀的镁铝合金中都含有一定量的Mn。除以上合金元素外,Zr也是一种较常见的元素,通常被添加到非铝系镁合金中。添加到镁合金中的Zr不仅能很好地细化晶粒,而且可以有效地去除杂质[11]。在熔融的镁基体中,Zr与Fe反应形成Fe-Zr金属间化合物,由于该金属间化合物具有较高密度,会快速沉积,因而可以提高镁合金的纯度,这在一定程度上改善了镁合金的耐蚀性。然而,Zr在非铝合金晶粒中通常分布不均匀,Zr会富集在晶粒的中心。此外,不能固溶的Zr颗粒可能会作为腐蚀电偶的阴极从而加速镁合金的腐蚀速率,因此应该注意避免Zr的过量添加。
基于此,本文研究了不同化学组分和显微结构的镁合金 (AZ31,AZ91,AM60和ZK61) 在模拟滨海雾霾环境下的腐蚀行为。研究采用在NaCl溶液中添加NH4NO3模拟滨海雾霾环境,探讨了NH4+和NO3-对4种镁合金在NaCl溶液中腐蚀行为的影响,以及它们发生点蚀和均匀腐蚀的演变过程。
1 实验方法
本实验采用的实验材料为轧制的AZ31 (Mg2.6Al1.0) 和AZ91 (Al8.2Zn0.4) 板材以及AM60 (Al5.9Mn0.3Zn0.001) 和ZK61 (Zn5.5Zr0.5Mn0.008) 铸锭。溶液环境为0.1 mol/L NaCl溶液和添加不同浓度NH4NO3的0.1 mol/L NaCl溶液,溶液的初始pH是直接通过pH计测量得到。实验中所有使用的化学药品都为分析级试剂。在整个实验过程中,溶液温度控制在 (25±1) ℃。
试样加工成20 mm×20 mm×3 mm的方形试样,用砂纸打磨到1500#,之后用酒精脱脂并用去离子水清洗后冷风干燥。为保证实验结果具有重复性,每个条件均使用5个平行试样。用分析天平对样品原始重量 (w0) 进行称量并记录,试样在300 mL的溶液中浸泡12 h。之后,将试样放置在除锈液 (200 g/L CrO3,10 g/L AgNO3和20 g/L BaNO3) 中浸泡去除腐蚀产物,用去离子水冲洗并冷风干燥。对干燥好的试样进行称重并记录最终质量 (w1)。试样的失重 (C,mg/cm2) 由下式得到:
其中,A是试样的暴露面积。
电化学测试所用仪器为CS350电化学工作站,试样加工成10 mm×10 mm×3 mm方形试样,测试采用传统的三电极体系,以试样为工作电极,Pt片为对电极,饱和甘汞电极 (SCE) 为参比电极。测试前用砂纸将工作面逐级打磨到1500#,之后用酒精和去离子水对工作面进行仔细清洗并用冷风干燥。以开路电位 (OCP) 为测试起始点,分别对试样动电位极化曲线的阳极分支和阴极分支进行测试,动电位扫描速率为0.333 mV/s。
采用扫描电镜 (SEM,Quanta 250) 对浸泡试样表面的腐蚀形貌进行表征,之后采用激光共聚焦显微镜 (CLSM, KEYENCE VK-X250) 对试样表面点蚀坑进行表征和分析。CLSM的每个视场面积为0.015 cm2,每个试样选取5个视场进行统计分析。
2 结果与讨论
2.1 原始微观组织结构
AZ31,AZ91,AM60和ZK61合金的原始组织如图1所示。从图1a和b中可以看出,AZ91合金的SEM像包含更多的β相 (Mg17Al12),而在AZ31合金中几乎看不到β相。从图1c中可以看出,除基体相外,AM60合金的显微组织还包含β相和Al8Mn5相。图1d中显示,ZK61合金的微观组织还包含基体Mg相和Zn2Zr。除基体α相外,共晶α相在腐蚀系统中充当阴极,这会促进基体α相的腐蚀,从而导致ZK61合金的耐腐蚀性较差。
图1 AZ31,AZ91,AM60和ZK61合金的微观结构
2.2 失重及腐蚀速率比较
图2是4种镁合金的失重和腐蚀速率。可以看出,加入NH4NO3后,4种镁合金的重量损失都有所增加,但增幅各不相同,这归因于镁合金的化学组成和微观结构的差异。
图2 AZ31,AZ91,AM60和ZK61 4种镁合金在0.1 mol/L NaCl和0.1 mol/L NaCl+0.01 mol/L NH4NO3两种溶液中浸泡12 h的失重和腐蚀速率
镁合金腐蚀速率的计算公式如下[12]:
其中,V是腐蚀速率 (mg·cm-2·d-1);t是浸泡时间 (h)。通过等式PW?=?2.1 V将V值转换为腐蚀速率 (PW,mm/a),如图2b所示。在0.1 mol/L NaCl溶液中,AZ91合金的腐蚀速率最低,ZK61合金的腐蚀速率最高。加入0.01 mol/L NH4NO3溶液之后,4种镁合金的腐蚀速率均有所提高,而AM60合金的腐蚀速率最低,表明AM60合金在该溶液体系中具有更好的耐蚀性。ZK61合金的腐蚀速率仍然是最高的,说明ZK61合金的耐蚀性较差,这些结果也可从表1中得出。
表1 NH4NO3对4种镁合金的腐蚀加速倍率
图3分别显示了AZ31,AZ91,AM60和ZK61合金在未含有和含有0.01 mol/L NH4NO3的0.1 mol/L NaCl溶液中的极化曲线。在图3a中,ZK61合金的阴极Tafel斜率明显高于其他3种镁合金,另外3种镁合金的阴极极化曲线在0.1 mol/L NaCl溶液中具有相同的变化趋势,均为典型的氢析出反应,具有极为接近的Tafel斜率。从表2中可以看出,图3a中的阴极曲线依次向右移动 (从左至右依次为AZ91,AM60,AZ31和ZK61合金) ,腐蚀电流密度依次增加,表明腐蚀速率依次增加。ZK61合金的腐蚀电流密度比AZ91和AM60合金的高出一个数量级,约是AZ31合金的6~7倍,这表明ZK61合金的腐蚀速率远高于其他3种合金的。表2为4种镁合金在0.1 mol/L NaCl溶液中极化曲线的拟合数据,参照之前的研究表明,腐蚀电流可以作为腐蚀速率的标准度量之一,即腐蚀电流越小,耐腐蚀性越好[13]。综上所述,4种镁合金耐蚀性的顺序依次为:AZ91>AM60>AZ31>ZK61,极化曲线测试结果与失重实验一致。
图3 AZ31,AZ91,AM60和ZK61镁合金在0.1 mol/L NaCl和0.1 mol/L NaCl+0.01 mol/L NH4NO3溶液中的极化曲线
表2 4种镁合金在0.1 mol/L NaCl溶液中的自腐蚀电流密度 (Icorr) 和腐蚀速率 (Pi)
与图3a中的曲线相比,添加NH4NO3后,极化曲线发生了很大变化。图3b中扫描曲线的阴极部分表明,AZ91合金的氢析出电流密度值低于其他合金的,AM60,AZ31和ZK61合金的依次降低。这表明从动力学上来讲,ZK61合金的阴极反应比其他3种合金更容易发生,这可能是由于ZK61合金中存在更多的阴极第二相,这可能会导致电偶腐蚀。图3b中AZ91和AM60合金扫描曲线的阳极部分有明显的拐点,在此之前电流密度缓慢增加,然后随着电位的增加而迅速增加。但是,随着电流密度的增加,ZK61合金的阳极曲线上没有明显的拐点。Song等[14]认为,极化曲线扫描过程中腐蚀电位的差异是由于未腐蚀表面的阴极氢逸出速率不同所致。如果阳极过程没有明显改变,较低的阴极极化曲线通常会导致更大的负腐蚀电位[13]。
2.3 腐蚀形貌观察
2.3.1 SEM形貌观察
前期研究[6]表明,AZ31镁合金在含有NH4NO3的NaCl溶液中发生了明显的点蚀行为,且与传统镁合金点蚀横向生长不同,这种情况下的点蚀沿深度方向生长。为了探讨合金元素对自催化点蚀的影响,本文通过添加不同NH4NO3含量,研究4种镁合金的“自催化”点蚀的离子浓度区间。图4显示了去除腐蚀产物的AZ31,AZ91和ZK61合金的SEM形貌 (AM60合金没有出现“自催化”点蚀行为)。可以看出,AZ31,AZ91和ZK61 3种合金在去除腐蚀产物后显示出各不相同的腐蚀形态。此外,3种镁合金发生自催化点蚀的NH4NO3浓度范围也不同。
图4 AZ31,AZ91和ZK61合金在NaCl溶液中浸泡12 h后的腐蚀形貌
由图4a可以看出,随着NH4NO3浓度的逐渐增大,AZ31试样表面由浅坑到强点蚀再到均匀腐蚀,自催化点蚀浓度在0.001~0.1 mol/L之间。在图4b和c中可以看到相似的腐蚀趋势,AZ91合金的自催化点蚀浓度在0.007~0.04 mol/L之间,ZK61合金的自催化点蚀浓度在0.0002~0.09 mol/L之间。浓度区间的大小可以反映出镁合金的耐蚀性差异,AZ91合金的耐蚀性优于AZ31和ZK61镁合金的。对于AM60合金来说,没有特定的自催化点蚀的NH4NO3浓度范围,仅在某些浓度 (0.001和0.01 mol/L NH4NO3) 时出现少量的腐蚀坑。这些腐蚀特征可以在图5中看出。
图5 4种镁合金在0.1 mol/L NaCl和0.1 mol/L NaCl+0.01 mol/L NH4NO3两种溶液环境中的点蚀参数
2.3.2 点蚀参数统计
点蚀参数具有6种指标,如图5所示。除了AZ91合金外 (图5a),其他合金的点蚀密度在添加0.01 mol/L NH4NO3的NaCl溶液中发生下降,这表明点蚀坑合并或某些点蚀坑的优先生长取决于NH4NO3的浓度。在两种溶液中,最大点蚀深度 (图5b) 和平均点蚀深度 (图5c) 有所不同。加入NH4NO3后,ZK61合金的最大点蚀深度 (图5b) 和平均点蚀深度 (图5c) 增加了约100倍。说明在含0.01 mol/L NH4NO3的NaCl溶液中,ZK61合金的耐腐蚀性最差。添加NH4NO3后,点蚀坑直径 (图5d) 与点蚀坑深度的变化趋势相同。AZ31和AZ91合金的单个点蚀坑体积 (图5e) 变化不大,加入0.01 mol/L NH4NO3后,AM60合金的点蚀坑体积减小。ZK61合金的点蚀坑体积在添加NH4NO3后会成倍增加,腐蚀坑由浅变深。图5f所示的点蚀坑的几何形状是用于阐明点蚀坑特性的有效参数[15]。根据点蚀坑直径 (d) 与点蚀坑深度 (D) 的比值,点蚀坑形状可以简单地分为半圆形 (d/2D=1),深孔形 (d/2D<1) 和浅碟形 (d/2D>1)。与其他3种镁合金相比,ZK61合金的d/2D值下降最多,这间接表明ZK61合金的耐腐蚀性最差。
2.4 讨论
合金元素在一定程度上决定着镁合金的微观结构。然而,镁合金的不均匀组织容易造成微电偶腐蚀[16,17]。因此,镁合金的微观结构在其腐蚀机理中起着重要作用。
Pardo等[16]指出,β相在腐蚀过程中具有双重作用。根据β相的数量和分布,可以起到腐蚀阻挡层或加速阴极电偶的作用。本文中AZ91合金的β相呈网状结构连续地分布在基体相中,可以有效地阻止AZ91合金进一步发生腐蚀。相反,AZ31合金中很少且不连续分布的β相会起到加速腐蚀的作用。在Cl--NH4+-NO3-溶液体系中,连续的β相也可以起阻碍腐蚀的作用,可以明显看到AZ91合金的耐蚀性要优于AZ31合金的。
Zn有助于克服Fe和Ni的有害腐蚀作用,但高含量的Zn会导致第二相沉淀物的形成,从而导致不可避免的电偶腐蚀。Huan等[18]证明了ZK30合金的耐腐蚀性优于ZK60合金的,认为ZK30合金中Zn含量较低,形成较少的第二相颗粒和微电偶腐蚀。当Zn含量超过3% (质量分数) 时,根据Mg-Zn二元相图可知[19],大量形成的Mg7Zn3相将导致微电流与基质偶联,从而加速材料的腐蚀。从图1d可以看出,ZK61合金中存在一些Mg2Zn相和枝晶,这可能会导致微电偶腐蚀,是ZK61合金耐腐蚀性差的原因之一。Zn含量的差异会影响4种镁合金在含有0.01 mol/L NH4NO3的NaCl溶液中的腐蚀行为。Zn可与溶液环境中的NH4+络合,导致镁基体脱落并腐蚀。4种镁合金中自催化点蚀的NH4NO3浓度范围最大的是ZK61合金,这可能与其Zn含量较高有关。
Zr可以细化晶粒,在一定条件下,Mg-Zn-Zr合金具有良好的耐蚀性。但是,如果Zr含量过高会导致镁合金的耐蚀性降低。Song等[8]研究表明,当Zr含量超过0.48%时,镁合金的腐蚀速率会增加,这与Zr在镁合金中的固溶度有关。当Zr含量超过其在镁合金中的固溶度时会析出沉淀,含Zr沉淀充当镁合金中的有效阴极相,从而加速了镁合金基体相的腐蚀。在该实验中,ZK61合金含有0.512%的Zr,超过文献中的0.48%,这可能是ZK61合金耐腐蚀性差的另一个原因。
Mn可通过去除Fe和其他重金属元素来避免形成有害的金属间化合物,从而提高合金的耐腐蚀性。AM60合金中的Mn可以形成AlMnFe相,降低合金中Fe的含量,净化合金,从而提高合金的耐腐蚀性。Mn被添加到大多数Mg-Al合金中以去除杂质Fe和Ni,对于AZ91和AM60合金,通常添加足够的Mn以确保Fe:Mn比小于0.032,从而显著提高耐腐蚀性[10,20]。另外,AM60镁合金中不含Zn,其也未观察到“自催化”点蚀区间,这进一步说明,Zn的存在可能是引起镁合金“自催化”点蚀的重要因素。这一部分内容将通过炼制不同含量的Mg-xZn合金来进一步研究。
实验结果表明,引入NH4NO3会加快4种镁合金的腐蚀速率,原因主要在于NH4NO3的引入会降低溶液的pH,酸性环境下镁合金会更容易腐蚀;再者由于NH4+的缓冲作用,添加NH4NO3会使Mg(OH)2保护膜遭到破坏并促进阴极NO3-的还原反应,从而加速了镁合金的腐蚀。
3 结论
(1) 在0.1 mol/L NaCl溶液中添加0.01 mol/L NH4NO3可加快AZ31,AZ91,AM60和ZK61 4种镁合金的腐蚀速率。
(2) 在0.1 mol/L NaCl溶液中,4种镁合金的腐蚀速率排序为ZK61>AZ31>AM60>AZ91;而在0.1 mol/L NaCl溶液中添加0.01 mol/L NH4NO3时,4种镁合金的腐蚀速率排序变为:ZK61>AZ31>AZ91>AM60。
(3) 当在溶液中添加0.001~0.1 mol/L NH4NO3时,AZ31镁合金就会出现“自催化”点蚀;当溶液中添加0.007~0.04 mol/L NH4NO3时,AZ91镁合金会出现自催化点蚀。ZK61镁合金自催化点蚀发生在溶液中NH4NO3的浓度范围为0.0002~0.09 mol/L时,AM60镁合金未发现自催化点蚀。
(4) Zn可能是导致镁合金在一定NH4NO3浓度区间发生自催化点蚀的关键因素。
参考文献
[1]Wang X J, Xu D K, Wu R Z, et al.
What is going on in magnesium alloys?
[J]. J. Mater. Sci. Technol., 2018, 34: 245
DOI:10.1016/j.jmst.2017.07.019 URL [本文引用: 1]
[2]Song G L, Bowles A L, StJohn D H.
Corrosion resistance of aged die cast magnesium alloy AZ91D
[J]. Mater. Sci. Eng., 2004, A366: 74
[本文引用: 1]
[3]Li J X, Zhang Y, Li J Y, et al.
Effect of trace HA on microstructure, mechanical properties and corrosion behavior of Mg-2Zn-0.5Sr alloy
[J]. J. Mater. Sci. Technol., 2018, 34: 299
[4]Atrens A, Johnston S, Shi Z M, et al.
Understanding Mg corrosion in the body for biodegradable medical implants
[J]. Scr. Mater., 2018, 154: 92
DOI:10.1016/j.scriptamat.2018.05.021 URL [本文引用: 1]
[5]Wu Z N, Li P J, Liu S X, et al.
Present state of research on corrosion of magnesium alloys
[J]. Foundry, 2001, 50: 583
[本文引用: 1]
(吴振宁, 李培杰, 刘树勋等.
镁合金腐蚀问题研究现状
[J]. 铸造, 2001, 50: 583)
[本文引用: 1]
[6]Cui Z Y, Ge F, Lin Y, et al.
Corrosion behavior of AZ31 magnesium alloy in the chloride solution containing ammonium nitrate
[J]. Electrochim. Acta, 2018, 278: 421
DOI:10.1016/j.electacta.2018.05.059 URL [本文引用: 2]
[7]Cheng Y L, Qin T W, Wang H M, et al.
Comparison of corrosion behaviors of AZ31, AZ91, AM60 and ZK60 magnesium alloys
[J]. Trans. Nonferrous Met. Soc. China, 2009, 19: 517
DOI:10.1016/S1003-6326(08)60305-2 URL [本文引用: 1]
[8]Zhao J M, Li T, Zhao X H.
Corrosion behavior of four cast magnesium alloys in simulated body fluid
[J]. Corros. Sci. Prot. Technol., 2015, 27: 444
[本文引用: 2]
(赵景茂, 李彤, 赵旭辉.
4种铸造镁合金在SBF溶液中的腐蚀行为研究
[J]. 腐蚀科学与防护技术, 2015, 27: 444)
DOI:10.11903/1002.6495.2014.348 URL [本文引用: 2]
[9]Li L J, Yu S H, Lei J L, et al.
Corrosion electrochemical behavior of AZ31 and AZ61 magnesium alloys in simulated sea water
[J]. Electrochemistry, 2008, 14: 95
[本文引用: 1]
(李凌杰, 于生海, 雷惊雷等.
AZ31和AZ61镁合金在模拟海水中的腐蚀电化学行为
[J]. 电化学, 2008, 14: 95)
[本文引用: 1]
[10]Song G L, Atrens A.
Corrosion mechanisms of magnesium alloys
[J]. Adv. Eng. Mater., 1999, 1: 11
DOI:10.1002/(ISSN)1527-2648 URL [本文引用: 2]
[11]Xia L T, Gao S, Luo X P, et al.
Corrosion factor analysis of magnesium alloy at different circumstance
[J]. Foundry, 2005, 54: 794
[本文引用: 1]
(夏兰廷, 高珊, 罗小萍等.
影响镁合金腐蚀性能的因素分析
[J]. 铸造, 2005, 54: 794)
[本文引用: 1]
[12]Cui Z Y, Li X G, Xiao K, et al.
Corrosion behavior of field-exposed zinc in a tropical marine atmosphere
[J]. Corrosion, 2014, 70: 731
DOI:10.5006/1177 URL [本文引用: 1]
[13]Li T, Zhang H, He Y, et al.
Comparison of corrosion behavior of Mg‐1.5Zn‐0.6Zr and AZ91D alloys in a NaCl solution
[J]. Mater. Corros., 2015, 66: 7
[本文引用: 2]
[14]Song G L, StJohn D.
The effect of zirconium grain refinement on the corrosion behaviour of magnesium-rare earth alloy MEZ
[J]. J. Light Met., 2002, 2: 1
DOI:10.1016/S1471-5317(02)00008-1 URL [本文引用: 1]
[15]Aouina N, Balbaud-Célérier F, Huet F, et al.
Single pit initiation on 316L austenitic stainless steel using scanning electrochemical microscopy
[J]. Electrochim. Acta, 2011, 56: 8589
DOI:10.1016/j.electacta.2011.07.044 URL [本文引用: 1]
[16]Pardo A, Merino M C, Coy A E, et al.
Influence of microstructure and composition on the corrosion behaviour of Mg/Al alloys in chloride media
[J]. Electrochim. Acta, 2008, 53: 7890
DOI:10.1016/j.electacta.2008.06.001 URL [本文引用: 2]
[17]Yu G, Liu Y L, Li Y, et al.
Corrosion and protection of magnesium alloys
[J]. Chin. J. Nonferrous Met., 2002, 12: 1087
[本文引用: 1]
(余刚, 刘跃龙, 李瑛等.
Mg合金的腐蚀与防护
[J]. 中国有色金属学报, 2002, 12: 1087)
[本文引用: 1]
[18]Huan Z G, Leeflang M A, Zhou J, et al.
In vitro degradation behavior and cytocompatibility of Mg-Zn-Zr alloys
[J]. J. Mater. Sci: Mater. Med., 2010, 21: 2623
DOI:10.1007/s10856-010-4111-8 URL [本文引用: 1]
[19]Liu M, Uggowitzer P J, Nagasekhar A V, et al.
Calculated phase diagrams and the corrosion of die-cast Mg-Al alloys
[J]. Corros. Sci., 2009, 51: 602
DOI:10.1016/j.corsci.2008.12.015 URL [本文引用: 1]
[20]Zeng G, Xian J W, Gourlay C M.
Nucleation and growth crystallography of Al8Mn5 on B2-Al(Mn,Fe) in AZ91 magnesium alloys
[J]. Acta Mater., 2018, 153: 364
DOI:10.1016/j.actamat.2018.04.032 URL [本文引用: 1]
免责声明:本网站所转载的文字、图片与视频资料版权归原创作者所有,如果涉及侵权,请第一时间联系本网删除。
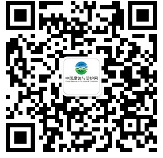
官方微信
《中国腐蚀与防护网电子期刊》征订启事
- 投稿联系:编辑部
- 电话:010-62316606-806
- 邮箱:fsfhzy666@163.com
- 中国腐蚀与防护网官方QQ群:140808414