MgCl2-NaCl-KCl熔盐体系中金属Mg对316H不锈钢的缓蚀性能研究
摘要
通过电化学方法结合浸泡腐蚀测试考察了金属Mg对MgCl2-NaCl-KCl (MNKC) 熔盐的净化和腐蚀抑制作用。结果表明,金属Mg的加入量在500 μg·g-1以上时,316H不锈钢在600 ℃ MNKC熔盐中的腐蚀电位Ecorr<-0.80 V vs NiCl2/Ni,腐蚀电流密度Icorr<25 μA/cm2,线性极化电阻Rp>800 Ω·cm2,熔盐对316H不锈钢的腐蚀得到显著抑制。并对金属Mg对MNKC熔盐的净化和腐蚀抑制机理进行了探讨。
关键词: 氯化物熔盐; 腐蚀控制; 316H不锈钢; 聚光太阳能发电站 (CSP)
Abstract
The effect of Mg on purification of molten salts MgCl2-NaCl-KCl (MNKC) and corrosion behavior of 316H stainless steel in MNKC molten salts were investigated by means of immersion test and electrochemical means. Results indicated that the corrosion of 316H stainless steel in MNKC molten salts at 600 ℃ was well inhibited when the addition amount of Mg exceeds 500 μg·g-1, correspondingly, 316H stainless steel presents the free corrosion potential of Ecorr<-0.80 V vs NiCl2/Ni, corrosion current density of Icorr<25 μA/cm2, and linear polarization resistance of Rp>800 Ω·cm2. The purification and corrosion inhibition mechanism of Mg for the MNKC molten salts were discussed simultaneously.
Keywords: chloride molten salt; corrosion mitigation; 316H stainless steel; concentrated solar power (CSP)
左勇, 曹明鹏, 申淼, 杨新梅。 MgCl2-NaCl-KCl熔盐体系中金属Mg对316H不锈钢的缓蚀性能研究[J]. 中国腐蚀与防护学报, 2021, 41(1): 80-86 doi:10.11902/1005.4537.2020.012
ZUO Yong, CAO Mingpeng, SHEN Miao, YANG Xinmei. Effect of Mg on Corrosion of 316H Stainless Steel in Molten Salts MgCl2-NaCl-KCl[J]. Journal of Chinese Society for Corrosion and Protection, 2021, 41(1): 80-86 doi:10.11902/1005.4537.2020.012
由碱金属或碱土金属氯盐混合组成的氯化物熔盐具有稳定性好、热容及热导率高、工作温度范围宽等特点,是极具竞争力的太阳能集热候选介质[1]。研究者们已从熔盐物性[2-4]、热循环稳定性[5]、材料相容性[6]、综合经济性[7]等角度对不同组成的氯化物熔盐开展了大量的研究工作,筛选出综合性能优异的氯化物熔盐体系。其中,MgCl2-NaCl-KCl熔盐 (摩尔分数为45.4%-33.0%-21.6%,MNKC代表该熔盐体系) 以其较低的熔点 (385 ℃)[7,8]、较高的热容 (1.180 J·g-1·K-1)[7]、较低的成本 (325/t,4.95/kWh)[7]吸引了众多研究者的注意[7-9]。其中,低熔点在工程上具有重要意义,一方面可提高熔盐介质的工作温度范围,另一方面可以降低熔盐管道发生冻堵的可能性,提高集热系统整体的可靠性。
熔盐材料相容性问题是研究者们关注最多的问题之一[10],也是基于熔盐介质的太阳能集热系统能否成功的核心问题之一[11]。尽管氯盐对各类高温合金的本征腐蚀很低,甚至低于氟盐对金属的本征腐蚀[12],然而由于水、氧等杂质不可避免的存在氯化物熔盐中[13],在高温下带来的腐蚀实际是非常严重的,特别是在环境中氧分压控制不好的条件下[14]。即使在惰性气氛下,由氯盐中杂质驱动引起的腐蚀仍不容忽视[15]。熔盐杂质的存在甚至被认为是引起氯盐或氟盐腐蚀加剧的最重要原因[16]。因此,熔盐净化是熔盐腐蚀控制的重要手段。
熔盐电位是决定熔盐腐蚀性的一个重要参数[17]。熔盐电位由熔盐自身的组成、杂质及所处的环境共同决定。通过净化熔盐、添加氧化还原缓冲离子对、或控制熔盐覆盖气的组成可以降低熔盐电位,从而达到腐蚀控制的目的[17]。另外,通过熔盐电位结合熔盐氧酸碱度 (E-pO2?图) 可以预测金属的稳定区、钝化区及腐蚀区,为熔盐腐蚀控制提供理论依据[18]。
金属Mg在氯化物熔盐中具有一定的溶解度[19],可与熔盐中的镁离子形成具有电位控制作用的电极电对。有研究[20,21]表明,金属Mg在含镁盐的熔盐中可能以Mg+、Mg2+或Mg22+等形式溶解。这一现象为采用金属Mg作为MNKC熔盐体系的缓蚀剂提供了理论基础。首先,金属Mg的引入可以除去熔盐中的各类氧化性杂质 (如过渡金属离子、溶解O2或Cl2、水及水解产物HCl、Mg(OH)Cl等),对熔盐起到净化效果。另外,溶解的金属Mg可以与Mg2+形成具有电位调节能力的氧化还原离子对,大幅降低熔盐电位,从而达到抑制金属材料的腐蚀的目的。已有文献采用金属Mg控制含镁氯盐的腐蚀并取得不错的效果。文献[22,23]发现向MgCl2-KCl(32-68,mol%) 熔盐中加入1.15% (摩尔分数) 金属Mg,可以大幅降低该氯盐对Haynes 230合金的腐蚀速率,使其腐蚀速率低于15 μm/a,满足DOE SunShot项目30 a设计使用寿命的目标要求。
尽管金属Mg对含镁氯盐有很好的腐蚀抑制效果,但由于金属Mg在高温下具有较高的蒸汽压 (330 Pa/650 ℃)[24],长时间运行会有较高的损耗。另外,环境中微量的水、氧杂质也会不断消耗溶解Mg致使其含量下降,Mg的腐蚀抑制效果也会降低。因此,如何对含镁氯盐体系金属Mg的缓蚀效果进行在线监测显得尤为必要。本文通过电化学方法结合浸泡腐蚀测试考察了金属Mg对MNKC熔盐的净化及腐蚀抑制作用,对比了不同镁金属添加量下316H不锈钢在MNKC熔盐中的腐蚀,并对实验结果及相关机理进行了讨论。
1 实验方法
MNKC熔盐的制备:考虑到MgCl2具有较强的挥发性,实验中将称取的196 g (45.4%) MgCl2置于刚玉坩埚底部,将混合好的87.4 g (33.0%) NaCl与73.0 g (21.6%) KCl覆盖在MgCl2上面,350 ℃烘干脱水过夜,随后升温至680 ℃并保温10 h,随后程序控制12 h降至室温,得到白色晶体形态的MNKC盐。所采用的氯盐原料均为分析纯无水氯盐。熔盐的称量、装料、烘干、熔融及后续的电化学测试及浸泡腐蚀测试均在带自净化功能的氩气手套箱及与之相连的井式炉中进行。手套箱内氩气气氛中的水、氧指标低于2×10-6。经过称量发现,在此条件下两次制备MNKC熔盐收率分别为98.5%和98.9%。
分别称取10 g NiCl2,22 g MgCl2,9.8 g NaCl,8.2 g KCl,均匀混合,配制成20% (质量分数) NiCl2-MNKC混合盐。将上述混合盐填充至定制的高纯热压氮化硼管 (?8 mm×50 mm,壁厚δ1 mm,底部有0.5 mm刻槽便于离子导通) 中制成Ni/NiCl2参比电极。每支参比电极管填充0.7 g左右的上述混合盐。封装完毕后置于坩埚中预熔融活化。实际测试发现其稳定性和灵敏性良好,置于熔盐中5 min内即可达到稳定工作状态,使用寿命经测试可达50 h以上。使用过程中定期通过循环伏安法对参比电极的稳定性进行标定,即通过观察MNKC熔盐电化学窗口的漂移观测参比电极电位是否发生改变,整个使用寿命期间参比电极电位漂移不超过5 mV。文中电位值如无特殊说明均为相对该Ni/NiCl2参比电极的电位值。
实验测试中使用?1 mm的钨金属工作电极材料纯度高于99%。腐蚀测试采用的316H不锈钢材料 (?1 mm金属丝或20 mm×7 mm×2 mm金属片) 的主要组成为Fe (基),C 0.09%,Si≤1%,Mn≤2%,Cr 17%,Ni 12%,Mo 2.5%。所使用的金属镁粉、镁棒 (φ8 mm) 纯度高于99%,镁粉粒径为75~150 μm。实验中使用的其它试剂如无水氯化亚铬均为分析纯试剂。
电化学测试在AutoLab 302N型电化学工作站上完成。三电极体系,研究电极为待测金属材料,辅助电极为石墨棒,参比电极为Ni/NiCl2。稳态极化曲线测试时扫描电位范围从低于开路电位0.15 V到高于开路电位0.15 V,扫描速率为5 mV/s,电极浸入熔盐平衡5 min后开始测量。电化学测试前,金属电极均依次经过38,18和11 μm碳化硅砂纸打磨后进行测试,以保证不同测试中金属电极的表面状态处于相近状态。测试重复3次以上,直至获得重现性较好的极化曲线,然后根据曲线读取腐蚀电位并计算腐蚀电流密度和线性极化电阻。循环伏安测试中工作电极为钨丝,其它测试条件与上述极化曲线相同。浸泡腐蚀实验在电化学测试同一装置中进行,316H不锈钢片 (20 mm×7 mm×2 mm) 经分级打磨、除油、清洗后于MNKC熔盐中浸泡100 h。完成浸泡后取出清洗、制样打磨后通过扫描电镜 (SEM LEO,1530VP) 观察截面微观形貌。实验中金属镁粉经称量后通过特制的不锈钢长颈漏斗直接加入熔盐,搅拌后保温30 min,再进行相关测试。
2 结果与讨论
2.1 镁粉对MNKC熔盐的净化效果
由于无水氯化镁具有较强的吸潮特性,MNKC熔盐在配制、熔融过程中所吸收的水会与氯盐发生水解反应,生成腐蚀性较强的MgOHCl和HCl,其中前者能稳定的存在于熔盐体系[6],并对金属造成较大的腐蚀危害。金属Mg作为强还原剂对熔盐中的水解产物、溶解氧、过渡金属离子、硫酸根离子等均有良好的去除效果 (见式 (1)~(5))。特别是水解产物和溶解氧,常规分析方法 (如ICP-OES、离子色谱等) 不便测量,但是对熔盐的腐蚀性往往是决定性的。
图1为添加金属Mg前后MNKC熔盐循环伏安曲线对比。从图中可以看到,未添加金属Mg的熔盐体系循环伏安曲线上有5处比较明显的氧化峰 (A1至A5) 和3处对应的还原峰 (C1至C3),其中A1/C1峰归为Mg的氧化和还原峰 (-1.75 V vs NiCl2/Ni),A5归为氯气的析出 (1.05 V vs NiCl2/Ni),A2/C2、A3/C3及A4峰由熔盐杂质造成。添加400 μg·g-1金属Mg的熔盐体系循环伏安曲线中A2/C2及A3/C3峰均消失,其中消失的A3/C3峰对应于水解产物MgOHCl的还原和氧化 (式 (6) 和 (7))[25],而A2/C2对应杂质金属离子。因此,通过循环伏安图可以非常直观地看到金属Mg对这两类杂质的净化效果。值得注意的是添加金属Mg以后,A4氧化峰有增强的趋势,根据文献中O在惰性电极上的析出电位[26]分析A4对应熔盐中O2-的氧化峰。因此,金属Mg对熔盐中O2-的脱除没有效果。添加金属Mg后O2-氧化峰增强的原因可能是Mg与水解产物MgOHCl反应后释放出部分自由O2-导致的。
图1 钨电极在600 ℃ MNKC熔盐体系中的循环伏安曲线
除了上述循环伏安曲线外,熔盐电位也可作为衡量熔盐氧化性杂质去除效果的一个重要参考指标。熔盐电位并不是一个严格的物理化学概念,可以理解为熔盐氧化还原的水平。在以氧化物为主的熔盐体系可采用“氧势”的概念表示熔盐电位,而在氟盐体系可以采用“氟势”的概念表示,Olander等[17]对此有专门论述。当熔盐中氧化性杂质含量较高时,熔盐具有较高的熔盐电位,而当氧化性杂质降低时,熔盐电位随之降低。熔盐电位通常不便直接测定,但可以通过添加氧化还原电极电对对熔盐电位进行调控[17]。例如,根据Nernst方程可以很方便地计算MNKC熔盐中溶解Mg对熔盐电位的调控作用:
式中,E0*为表观标准电极电位,由图1循环伏安曲线Mg析出电位可以认为E0*为-1.75 V vs NiCl2/Ni,XMg2+为MNKC体系MgCl2摩尔分数,XMg为溶解金属Mg的摩尔分数,R为理想气体状态常数,F为法拉第常数,n为转移电子数2。根据上式计算MNKC熔盐中分别溶解1、10、100、1000 μg·g-1金属Mg时的熔盐电位分别为-1.305、-1.391、-1.478、-1.565 V vs NiCl2/Ni。因此,在溶解有金属Mg的MNKC熔盐体系可以通过分析熔盐中Mg的浓度来计算熔盐电位。实际的熔盐回路中,直接对熔盐取样分析是比较困难的。通过电化学探针在线进行电位测量,可反映熔盐电位的变化情况。
根据混合电位理论,金属 (含合金) 的腐蚀电位是熔盐与金属材料反应耦合形成的混合电位,主要由熔盐电位、金属材料组成及表面状态共同决定。因此,通过测量确定组成和表面状态的金属腐蚀电位可以反映熔盐电位的高低。图2给出了316H不锈钢在MNKC熔盐体系随金属Mg添加量增加时的腐蚀电位变化曲线,从图中可以看到,随着Mg添加量的增加,腐蚀电位由-0.64 V逐渐降低至-1.14 V,根据混合电位理论可以推断熔盐电位从由氧化性杂质控制逐渐转向由溶解Mg与MgCl2形成的Mg2+/Mg电对控制,这种转变对熔盐腐蚀的抑制极为重要。综上所述,金属Mg的添加不仅能去除MNKC熔盐体系中的氧化性杂质,而且溶解的金属Mg可以与MgCl2形成电位很低的氧化还原电极电对并实现对熔盐电位的控制。

图2 316H不锈钢在600 ℃ MNKC熔盐体系的腐蚀电位随Mg添加量的变化曲线
2.2 金属Mg对MNKC熔盐腐蚀特性的影响
为了进一步量化Mg的添加量对MNKC熔盐腐蚀特性的影响,本文测定316H不锈钢在不同Mg添加量MNKC熔盐中的稳态极化曲线 (图3),并通过Tafel外延法计算了316H不锈钢的腐蚀电流密度 (图4),同时也给出了相应的线性极化电阻 (图5)。从图4可以看到,在未添加镁粉的MNKC熔盐中,316H不锈钢的腐蚀电流密度为1670 μA/cm2,向MNKC熔盐中添加200 μg·g-1金属镁粉以后,316H在MNKC熔盐中的腐蚀电流密度大幅下降约2个数量级至50.2 μA/cm2,随着Mg添加量的增加,腐蚀电流密度继续小幅下降直至添加量为800 μg·g-1时达到最低点11.5 μA/cm2,随后小幅增加。而图5的线性极化电阻曲线则呈现相应的先升高随后小幅下降的趋势。从整体趋势看,当Mg添加量高于500 μg·g-1时,316H不锈钢在MNKC熔盐中测得的腐蚀电位低于-0.80 V (图2),腐蚀电流密度低于25 μA/cm2,而线性极化电阻高于800 Ω·cm2,腐蚀特征指标远优于未添加Mg的数据,表明其处于很好的腐蚀抑制状态。
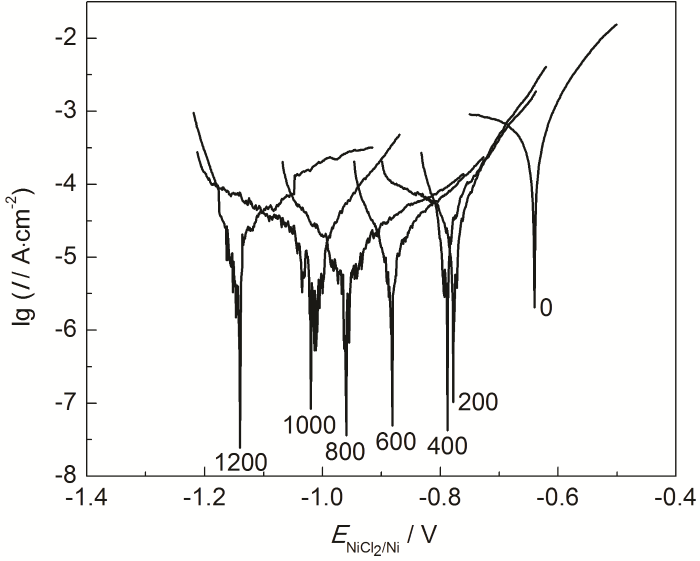
图3 600 ℃下316H不锈钢在MNKC-Mg (0~1200 μg·g-1) 熔盐体系的极化曲线
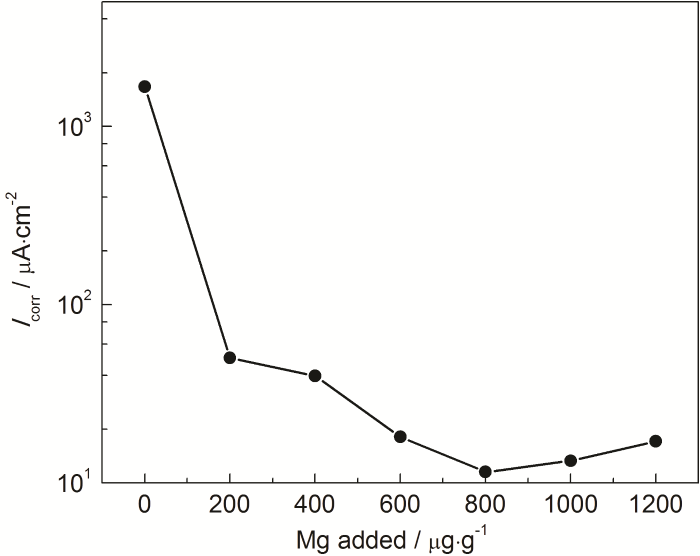
图4 600 ℃下316H不锈钢在MNKC熔盐体系中的腐蚀电流密度随Mg添加量的变化曲线
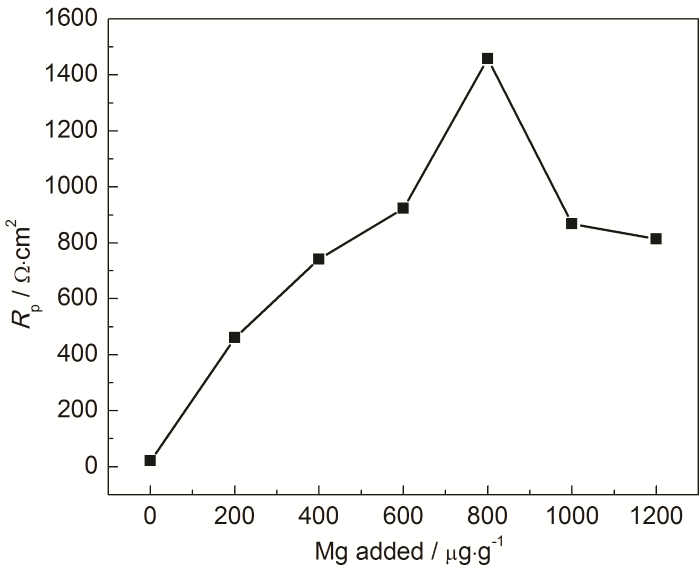
图5 600 ℃下316H不锈钢在MNKC熔盐体系中的线性极化电阻随Mg添加量的变化曲线
值得关注的特殊现象是,当金属Mg添加量高于800 μg·g-1时测得的腐蚀电流密度有小幅上扬,或极化电阻有一定程度的降低,分析认为这并不意味着316H不锈钢腐蚀的增加,而可能是熔盐中溶解金属Mg浓度的增加导致其参与到腐蚀反应中来。即在较低的腐蚀电位下 (如-0.96 V以下),溶解金属Mg在腐蚀电极上的氧化逐渐替代316H不锈钢中Cr的氧化腐蚀。此时,通过316H不锈钢电极测得的腐蚀电流密度应远高于316H不锈钢的真实腐蚀速率。鉴于此种情形下通过极化曲线测得腐蚀参数指标仍处在较低水平 (Icorr<25 μA/cm2,Rp>800 Ω·cm2),因此我们仍可以通过该方法来监测316H不锈钢在该体系中的腐蚀速率。例如,当测得316H不锈钢在MNKC-Mg体系中的腐蚀电位高于-0.80 V且腐蚀电流密度高于25 μA/cm2或极化电阻低于800 Ω·cm2,我们可以向体系中添加适量金属Mg,直到各项监测指标满足我们的预期值。这组特征指标 (即Ecorr<-0.80 V,Icorr<25 μA/cm2,Rp>800 Ω·cm2) 可以作为316H不锈钢在MNKC熔盐体系腐蚀监测和调控的临界点。
2.3 MNKC-Cr(II) 熔盐体系循环伏安研究
由于316不锈钢钝化膜在氯盐中不能长期稳定存在,316不锈钢在熔盐体系的腐蚀机理主要是Cr的流失[27]。为了进一步阐明金属Mg和熔盐电位对熔盐腐蚀抑制的机理,对MNKC-Cr(II) 体系的循环伏安行为进行了研究。实验前先采用金属镁棒与MNKC熔盐接触平衡以去除杂质,然后加入质量分数0.2%的CrCl2,考察了Cr的各种物种在MNKC熔盐体系的氧化还原行为。由Martinez等[28]对氯盐体系Cr电化学行为研究可知Cr(II) 在含氧氯盐中存在自由Cr2+、Cr2O2+以及CrO 3种形式,并与熔盐中的O2-保持平衡。上文已经提到,金属Mg并不能去除MNKC熔盐中的O2-,因此所研究的MNKC-Cr(II) 体系必然也含有Cr2+、Cr2O2+以及CrO 3种形式的Cr(II) 物种。通过文献[28]所给出的各种氧化还原反应的标准电极电势,结合本文MNKC-Cr(II) 体系的实际特点 (如以Cr(II) 为主且存在多种形式),将图6中各氧化还原峰的归属列于表1。其中A3峰对应3种Cr(II) 物种氧化为Cr2O3的叠加峰。由于A3反应的产物Cr2O3为不溶物,因此反应的可逆性较差,与C3还原峰相对弱小的表现相符。
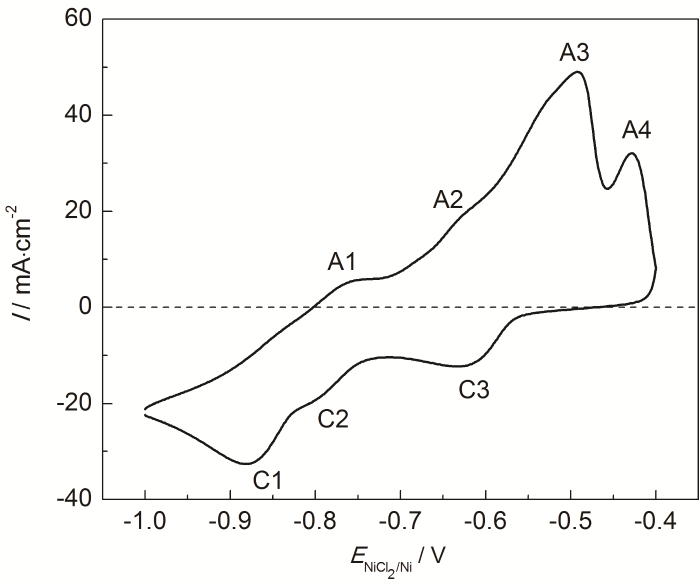
图6 钨电极在600 ℃的MNKC-0.2%CrCl2熔盐体系中的循环伏安曲线
表1 循环伏安曲线氧化还原峰归属汇总
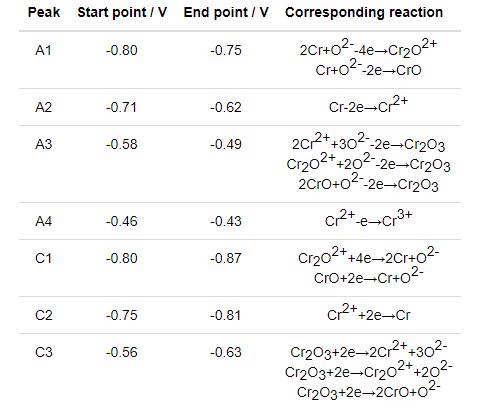
与金属腐蚀行为相关的两个氧化峰是A1和A2,分别对应金属Cr氧化为Cr2O2+(或CrO) 和Cr2+。从图6和表1的结果可以看到,A1峰的起始电位在-0.80 V,A2峰的起始电位在-0.71 V。即由于O2-的存在,金属Cr的氧化起始电位由-0.71 V降低至-0.80 V。这一结论对316H不锈钢的腐蚀控制非常关键。因此,欲抑制316H不锈钢的氧化腐蚀,其在熔盐中的腐蚀电位应控制在-0.80 V以下,这与上文极化曲线测试的结果相吻合。即腐蚀电位高于-0.80 V,316H不锈钢中的金属Cr在含有O2-的MNKC熔盐体系有氧化为Cr2O2+(或CrO) 的趋势,而低于这一电位则呈现Cr2O2+(或CrO) 还原为金属Cr的趋势。这也解释了极化曲线测试在腐蚀电位降低至-0.96 V及以下时,随着Mg添加量的增加,腐蚀电流密度有所增加的原因 (图3和4)。此时从腐蚀电位向阳极极化时 (即-0.96→-0.81 V),电极上的主要反应是溶解Mg的氧化而非316H不锈钢电极中金属Cr的氧化。因此,在熔盐腐蚀监测中,我们不能只看腐蚀电流密度或极化电阻的大小,而应结合腐蚀电位以及电极上发生的反应进行综合分析,从而判断体系的真实腐蚀情况。
2.4 MNKC熔盐体系浸泡腐蚀
通过以上腐蚀电化学的相关测试表明,向MNKC熔盐中加入500 μg·g-1以上的金属Mg可以有效控制316H不锈钢的腐蚀,相应的腐蚀控制判据为Ecorr<-0.80 V,Icorr<25 μA/cm2,Rp>800 Ω·cm2。为进一步证实这一判断,在MNKC熔盐体系开展了316H不锈钢浸泡腐蚀测试。在添加500 μg·g-1金属Mg的MNKC熔盐中浸泡100 h,316H不锈钢样片未见可观测的失重或增重现象,微观截面照片未见Cr流失导致的晶间腐蚀现象 (图7)。而相同条件下,316H不锈钢在未添加金属Mg的MNKC溶液中浸泡100 h后失重0.18%,样品截面照片显示发生了Cr流失造成的晶间腐蚀,腐蚀深度达30 μm (图8)。这一对比测试表明添加的500 μg·g-1金属Mg对MNKC体系316H不锈钢的腐蚀抑制作用非常显著。
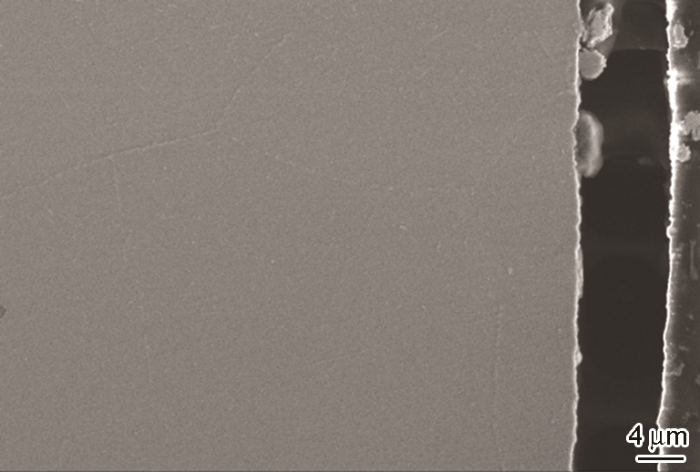
图7 600 ℃下MNKC-500 μg·g-1 Mg体系浸泡100 h后316H不锈钢截面SEM像

图8 600 ℃下MNKC体系浸泡100 h后316H不锈钢截面SEM像
此外,500 μg·g-1金属Mg添加量对应的腐蚀电流密度 (25 μA/cm2) 转换为316H不锈钢100 h腐蚀深度约为12 μm,而在该体系实际浸泡100 h后并未发现Cr流失 (图7)。这也从侧面证实了Ecorr<-0.80 V时所测得的Icorr远高于316H不锈钢真实腐蚀速率的判断。
3 结论
金属镁对MgCl2-NaCl-KCl(MNKC) 熔盐具有良好的净化和电位控制效果。316H不锈钢在不同镁添加量的MNKC熔盐体系的稳态极化曲线测试表明,当镁添加量高于500 μg·g-1时,MNKC熔盐对316H不锈钢的腐蚀作用基本可以忽略,相应的腐蚀特征参数Ecorr<-0.80 V vs NiCl2/Ni,Icorr<25 μA/cm2,Rp>800 Ω·cm2可以作为腐蚀监测与控制的判据。当镁的添加量高于800 μg·g-1且316H不锈钢Ecorr<-0.96 V vs NiCl2/Ni时,采用极化曲线测量得到的腐蚀电流密度或极化电阻主要由溶解镁在电极上的反应所产生的,316H不锈钢自身腐蚀反应的贡献基本可以忽略,且由于此时测得的总的腐蚀速率仍在较低水平 (Icorr<25 μA/cm2,Rp>800 Ω·cm2),因此即使在较高镁含量下,稳态极化曲线法仍可作为MNKC-Mg熔盐体系腐蚀监测手段,并仍可将Ecorr<-0.80 V vs NiCl2/Ni,Icorr<25 μA/cm2,Rp>800 Ω·cm2作为腐蚀控制或干预的目标。
参考文献
1 Myers P D, Goswami D Y. Thermal energy storage using chloride salts and their eutectics [J]. Appl. Therm. Eng., 2016, 109: 889
2 Xu X K, Wang X X, Li P W, et al. Experimental test of properties of KCl-MgCl2 eutectic molten salt for heat transfer and thermal storage fluid in concentrated solar power systems [J]. J. Sol. Energy Eng., 2018, 140: 051011
3 Xu X K, Dehghani G, Ning J X, et al. Basic properties of eutectic chloride salts NaCl-KCl-ZnCl2 and NaCl-KCl-MgCl2 as HTFs and thermal storage media measured using simultaneous DSC-TGA [J]. Sol. Energy, 2018, 162: 431
4 Li Y Y, Xu X K, Wang X X, et al. Survey and evaluation of equations for thermophysical properties of binary/ternary eutectic salts from NaCl, KCl, MgCl2, CaCl2, ZnCl2 for heat transfer and thermal storage fluids in CSP [J]. Sol. Energy, 2017, 152: 57
5 Hu B H, Ding J, Wei X L, et al. Test of thermal physics and analysis on thermal stability of high temperature molten salt [J]. Inorgan. Chem. Ind., 2010, 42(1): 22
5 胡宝华, 丁静, 魏小兰等. 高温熔盐的热物性测试及热稳定性分析 [J]. 无机盐工业, 2010, 42(1): 22
6 Ding W J, Bonk A, Bauer T. Corrosion behavior of metallic alloys in molten chloride salts for thermal energy storage in concentrated solar power plants: A review [J]. Front. Chem. Sci. Eng., 2018, 12: 564
7 Mohan G, Venkataraman M, Gomez-Vidal J, et al. Thermo-economic analysis of high-temperature sensible thermal storage with different ternary eutectic alkali and alkaline earth metal chlorides [J]. Sol. Energy, 2018, 176: 350
8 Pelton A D, Chartrand P. Thermodynamic evaluation and optimization of the LiCl-NaCl-KCl-RbCl-CsCl-MgCl2-CaCl2 system using the modified quasi-chemical model [J]. Metall. Mater. Trans., 2001, 32A: 1361
9 Sun L P, Wu Y T, Ma C F. Experimental study on optimization of molten salt for solar high temperature heat storage [J]. Acta Energ. Sol. Sin., 2008, 29: 1092
9 孙李平, 吴玉庭, 马重芳. 太阳能高温蓄热熔融盐优选的实验研究 [J]. 太阳能学报, 2008, 29: 1092
10 Patel N S, Pavlík V, Bo?a M. High-temperature corrosion behavior of superalloys in molten salts: A review [J]. Crit. Rev. Solid State Mater. Sci., 2017, 42: 83
11 Sun H, Su X Z, Zhang P, et al. Research status and progress of molten salts corrosion for concentrated solar thermal power [J]. Corros. Sci. Prot. Technol., 2017, 29: 282
11 孙华, 苏兴治, 张鹏等. 聚焦太阳能热发电用熔盐腐蚀研究现状与展望 [J]. 腐蚀科学与防护技术, 2017, 29: 282
12 Vignarooban K, Pugazhendhi P, Tucker C, et al. Corrosion resistance of Hastelloys in molten metal-chloride heat-transfer fluids for concentrating solar power applications [J]. Sol. Energy, 2014, 103: 62
13 Vindstad J E, Mediaas H, ?stvold T. Hydrolysis of MgCl2-containing melts [J]. Acta Chem. Scand., 1997, 51: 1192
14 Tzvetkoff T, Kolchakov J. Mechanism of growth, composition and structure of oxide films formed on ferrous alloys in molten salt electrolytes-a review [J]. Mater. Chem. Phys., 2004, 87: 201
15 Ding W J, Shi H, Xiu Y L, et al. Hot corrosion behavior of commercial alloys in thermal energy storage material of molten MgCl2/KCl/NaCl under inert atmosphere [J]. Sol. Energy Mater. Sol. Cells, 2018, 184: 22
16 Raiman S S, Lee S. Aggregation and data analysis of corrosion studies in molten chloride and fluoride salts [J]. J. Nucl. Mater., 2018, 511: 523
17 Olander D. Redox condition in molten fluoride salts-Definition and control [J]. J. Nucl. Mater., 2002, 300: 270
18 Zeng C L, Zhang J Q, Wu W T. Electrochemistry of corrosion in molten salts [J]. Corros. Sci. Prot. Technol., 1992, 4: 16
18 曾潮流, 张鉴清, 吴维. 熔盐腐蚀电化学 [J]. 腐蚀科学与防护技术, 1992, 4: 16
19 Tian H Q, Du L C, Huang C L, et al. Enhanced specific heat capacity of binary chloride salt by dissolving magnesium for high-temperature thermal energy storage and transfer [J]. J. Mater. Chem., 2017, 5A: 14811
20 Jasien P G, Dykstra C E. An ab initio study of the stability and electronic structure of univalent magnesium salts [J]. Chem. Phys. Lett., 1984, 106: 276
21 Krumpelt M, Fischer J, Johnson I. Reaction of magnesium metal with magnesium chloride [J]. J. Phys. Chem., 1968, 72: 506
22 Garcia-Diaz B L, Olson L, Martinez-Rodriguez M, et al. High temperature electrochemical engineering and clean energy systems [J]. J. S. C. Acad. Sci., 2016, 14: 11
23 Mehrabadi B A T, Weidner J W, Garcia-Diaz B, et al. Modeling the effect of cathodic protection on superalloys inside high temperature molten salt systems [J]. J. Electrochem. Soc., 2017, 164: C171
24 Zhang M J, Li J D, Guo Q F. Recovery of magnesium from rejected magnesium alloy by vacuum sublimation process-magnesium alloy treating technology [J]. Light Met., 2006, (2): 48
24 张明杰, 李继东, 郭清富. 真空升华法从废镁合金中回收镁—镁合金无害化处理技术 [J]. 轻金属, 2006, (2): 48
25 Ding W J, Bonk A, Gussone J, et al. Electrochemical measurement of corrosive impurities in molten chlorides for thermal energy storage [J]. J. Energy Storage, 2018, 15: 408
26 Wang D H, Xiao W. Inert anode development for high-temperature molten salts [A].
26 Lantelme F, Groult H. Molten Salts Chemistry [M]. Oxford: Elsevier, 2013: 171
27 Sun H, Wang J Q, Li Z J, et al. Corrosion behavior of 316SS and Ni-based alloys in a ternary NaCl-KCl-MgCl2 molten salt [J]. Sol. Energy, 2018, 171: 320
28 Martínez A M, Castrillejo Y, B?rresen B, et al. Chemical and electrochemical behaviour of chromium in molten chlorides [J]. J. Electroanal. Chem., 2000, 493: 1
免责声明:本网站所转载的文字、图片与视频资料版权归原创作者所有,如果涉及侵权,请第一时间联系本网删除。
相关文章
无相关信息
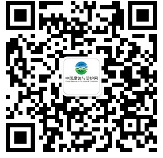
官方微信
《中国腐蚀与防护网电子期刊》征订启事
- 投稿联系:编辑部
- 电话:010-62316606-806
- 邮箱:fsfhzy666@163.com
- 中国腐蚀与防护网官方QQ群:140808414
点击排行
PPT新闻
“海洋金属”——钛合金在舰船的
点击数:7214
腐蚀与“海上丝绸之路”
点击数:5804