引言
我国在2020年底,全国油气管网规模预计将达到16.9万公里,其中原油、成品油、天然气管道里程分别为3.2、3.3、10.4万公里。随着国内油气管道建设速度不断加快,受制于管道沿线地质灾害、建设质量、运行压力等现实因素,输气管道近些年来事故多发。多数事故为管道本体应力超限,导致管道薄弱处破裂、泄漏、起火或爆炸[1]。油气田内部站场常见地质灾害形式为地质沉降、滑坡等,管道容易在沉陷区域土体位移的作用下发生拉压和扭曲变形,产生裂缝、拉断等形式的破坏,给输油管道的安全造成了极大的威胁。
因此基于以上,对存在可能或已发生地质沉降区域的管道进行表面残余应力检测,监测管道应力,提高管道安全管理及风险预警能力具有重要意义。
残余应力测量技术概述
残余应力测量技术开始于上世纪初。根据是否破坏被测试样,其检测方法分为有损检测与无损检测。有损检测主要原理是把试件上被测点的应力给予释放,并采用电阻应变计测量测出释放应变而计算出原有残余应力。残余应力的释放方法是通过机械切割分离,在试件表面钻一小孔,对试件进行取条、拨层等方法,因此它是一种破坏性或半破坏性的测量方法。其中尤以钻孔法研究较为成熟,基本原理为在试件表面上钻一小孔,使得孔的周围部分应力释放从而产生相应的位移和应变,并用粘贴应变片进行测量,最后得到钻孔处深度方向上的平均残余应力。有损检测法特点为可靠、经济、准确性较高,但检测过程因需要钻孔、取条等会对试件表面存在破坏及半破坏,特别是受限于油田管道等承压设备,对设备有极高的承压要求,不能以牺牲承压能力而进行检测,因此其应用范围受到了一定的限制。无损测量法主要有磁性法、超声波法、中子衍射法、X射线衍射法等。磁性法的基本原理是基于铁磁性材料(如低碳钢等)的磁致伸缩效应,即铁磁性材料在磁化时会发生,尺寸变化;反过来铁磁体在应力作用下其磁化状态(导磁率和磁感应强度等)也会发生变化,因此通过测量磁性变化可以测定铁磁材料中的应力。磁性测定法对工件表面质量要求低但测量结果受多种因素影响,可靠性和精度差测量值标定困难,对材质较为敏感,仅能用于铁磁材料的测量[2]。超声波法测量残余应力技术是基于声弹性理论,即在弹性介质中传播的超声波波速会因材料内部应力的影响产生微小变化[3]。但是因为超声波波长较长,而试件内部的残余应力引起的波速变化又很微小,且材料的形状和结构也会对测量结果产生影响,导致其测量精度较低,且只能测到试件内部的平均残余应力[4]。中子衍射法是测量材料内部应力的一种新兴方法,中子的穿透能力比x射线强,可以得到材料沿厚度方向的残余应力,但由于中子源较难获得,并且在中子衍射法中需要先测出自由状态下晶体晶格原子面间距或布拉格角,因此用中子衍射法测量实际残余应力时仍存在一定的困难[5]。X射线衍射法其理论相对成熟,相应的检测标准也已完善,如《无损检测 X射线应力测定方法》GB∕T 7704-2017,但该方法大多基于实验室测量,相应仪器复杂,对于工业现场检测使用较少。
X射线衍射法测量表面残余应力原理
X射线衍射法测量表面残余应力利用布拉格定律,X射线波长λ、衍射晶面间距d、衍射角2θ之间关系满足布拉格方程:
(1)
在已知X射线波长λ的条件下,布拉格定律把宏观上可以测量的衍射角2θ与微观的晶面间距d建立起确定的关系。当材料中有应力存在时,其晶面间距d必然随晶面与应力相对取向的不同而有所变化,导致衍射峰发生偏移,通过测量衍射峰的偏移程度,即残余应变,通过胡克定律由残余应变计算残余应力值。
1961年德国的E.Mchearauch提出了X射线应力测定的sin2ψ法,即应变(应力)与衍射晶面方位角ψ的正弦平方成函数关系,见图1,应力方程为:
(2)
εψ的量值可以用衍射晶面间距的相对变化来表示,且与衍射峰位移联系起来,即:
(3)
式中θ0为无应力试样衍射峰的布拉格角,θψ为有应力试样衍射峰位的布拉格角。经过换算,可得到:
其中K是只与材料本质、选定衍射面HKL有关的常数,当测量的样品是同一种材料,而且选定的衍射面指数相同时,K为定值,称为应力系数。M是(2θ)-sin2ψ直线的斜率,对同一衍射面HKL,选择一组ψ值(0°、15°、30°、45°),测量相应的(2θ)ψ以(2θ)-sin2ψ作图,并以最小二乘法求得斜率M,就可计算出应力(φ是试样平面内选定主应力方向后,测得的应力与主应力方向的夹角)。由以上可看出当K、M均小于0或均大于0时,为拉应力,反之则为压应力,而M=0时无应力存在。
图1 sin2ψ法原理示意图
1997年日本科学家SASAKI等提出用单次入射的方法在试样和面阵探测器相对位置固定的情况下,通过单次曝光获得的德拜环信息计算应力,方程变量为cosα,该方法也被称为单次入射cosα法,简称为cosα法。2012年起日本制造商开始向市场上提供商业化的cosα法应力仪。该残余应力分析仪利用圆形全二维探测器获取X射线在给定角度入射后的全部衍射德拜环,从而摆脱了传统X射线残余应力分析仪的测试局限,使得真正的现场测量和不规则形状样品测量成为了可能。这款全新残余应力分析仪在实际使用中操作十分简单,单角度一次入射即可获取完整德拜,在整个德拜环上可以采集多达500个的数据点,并最多可用125个数据点进行高精度数据拟合计算残余应力[6]。
cosα法应力仪采用的是中间开孔的面阵探测器,X射线穿过中心孔照射到样品上,探测器在相对于样品的固定角度和距离上捕获衍射峰的环状信息即德拜环,见图2~4。根据有无应力存在时德拜环的偏离角α,通过胡克定律推导出以下应力方程:
假定试样表面平面应力状态下,表面法线上的剪切应力τ13、τ23为零,即残余应力的计算表述为:
因此从以上公式可看出,应变与cosα成线性关系。
表面残余应力在X射线衍射法中的表现形式
习惯将第一类内应力称为残余应力。一般英、美文献中把第一类内应力称为“宏观应力”(Macrostress),把第二类和第三类内应力合称为“微观应力”(Microstress)。残余应力可以认为是第一类内应力的工程名称。
内应力是指没有外力或外力矩作用而在物体内部存在并自身保持平衡的应力。依据对晶体的X射线衍射现象的不同,可将内应力分为三类:
(1)第I类内应力:宏观尺寸范围内存在并保持平衡的应力,与之对应的应变导致原子间晶面间距变化,引起X射线谱线峰位移;
(2)第II类内应力:几个晶粒范围内存在并保持平衡的应力,应力的作用与平衡范围较小,引起衍射谱线宽化;
(3)第III类内应力:一个晶粒晶胞尺寸数量级范围内存在并保持平衡的应力,引起衍射谱线强度下降。
图5 内应力结构关系图
基于cosα法的X射线衍射检测技术的应用
5.1试样及技术参数
检测材料各选取某2座净化厂(简称为A、B厂)4条在役放空管道进行轴向应力检测,其中A厂放空管道存在地基沉降,管道规格为φ168×7.5mm,管道材质为20#钢;B厂管道未发生沉降。A厂的2条管道分别与B厂的2条管道走向、规格、介质、功能、运行条件等一致。现场检测设备主要有2台,一台是电解抛光机,另一台是型号为u-X360的便携式X射线应力检测仪,测量方法是基于cosα法的X射线衍射检测技术。测量参数见表1。
表1 X射线应力检测仪测量参数
表2 电解抛光仪抛光参数
5.1检测方法
(1)除漆剂除去表面防腐油漆,露出管材本体。
(2)采用1000目砂纸手工打磨除去管体表面氧化层,打磨区域面积2cm×2cm,采用W2.5/4000目金刚石研磨膏进行表面抛光。
(3)透明胶带贴出正方形的待电解抛光区,面积为1cm×1cm,调节电解抛光仪电压,对该区域进行电解抛光。
(4)调试u-X360的便携式X射线应力检测仪,对电解区域进行残余应力检测。
5.3检测结果与分析
5.3.1两座净化厂管道检测数据对比
对A、B厂的放空管线进行检测,选取A、B厂相同位置的4条管线,A厂的a、b管线存在沉降,B厂的a、b管线不存在沉降。每条管线检测6处轴向应力。检测位置示意图见图6。检测数据见图7、图8。
图6 测点位置示意图
由图7,图8可看出,A、B两厂4条管道表面残余应力均为拉应力,且图中趋势可以看出,A厂管道所受拉应力对应位置大于B厂管道。
从X射线衍射的原理可以看出,一切影响管道表面晶体间距的因素均可影响管道表面残余应力大小,同时X射线衍射检测的表面应力为第一、二、三类内应力的综合状态。这包括管道加工制造过程对表面的影响,如冷轧和热轧过程中产生的表面应力等,管道焊接过程中产生的应力,如焊接过程产生的热应力、相变应力等,内压对管道表面应力的影响,检测时温度的影响等各种因素。四条管道材质,处理状态,焊接工艺,检测环境,检测时的介质状态等因素均相同,由此造成的应力差基本可判定为地质沉降引起的,基本符合现场情况,即A厂管道存在不均匀沉降,引起管道表面应力变化。
同时,图7、图8中可以看出,随着检测位置的延伸,其中由测点1到测点2,测点5到测点6两厂管道变化趋势相同,其余测点3、4、5变化规律不明显,因测点3、4、5均位于直管段,沉降对该区域影响造成。
5.3.2不同深度下应力的检测
选取与a、b管道相同材质(20#钢)的加工试样进行不同时间的电解抛光,其中试样尺寸为:50×25×2.55mm。试样待电解抛光区域原始壁厚为2.55mm,经过10秒、60秒、240秒三次不同时间下的抛光,测得剩余厚度分别为2.55mm、2.43mm、2.38mm,经计算平均电解腐蚀速率为0.7μm/s。在上述时间范围内,电解抛光剥层厚度在几微米到几百微米的范围内。
选取A厂的a、b管道,在其上选取两点,位置见图6中测点7点,进行机械抛光后,对不同电解时间下的表面应力进行检测,由图8、图9可以看出,在不同的电解抛光时间下,所测应力成梯度降低趋势。即随着电解抛光时间的延长,对管体表面形成了逐层剥离,所测应力实际反映了管体表面不同深度的应力大小。
从图8、图9中数据可以看出,管体表面在加工过程中经受的外力和变形,遭遇的温度变化,以及自身发生的组织结构变化或相变,沉降产生的应变等综合因素下,表层应力明显区别于内部应力,综合因素下引起的效应都比其内部强烈。因此,最大的或变化最剧烈的应力往往存在于管体表面或近表层,管道制造过程产生的较大残余应力,或者所引起的显著应力梯度,都集中于表层或次表层,管体壁厚深层应力强度效应递减,递减过程较为剧烈。
从以上数据也可看出,在役状态管体总是表面承受最大的应力,在不考虑管道焊接缺陷,管壁原本存在的裂纹等缺陷,管壁存在夹层等情况下,受管道沉降应力产生的裂纹源相应产生于接近表面的区域。所以,虽然X射线法测试的深度比较浅,但表层的应力往往引起不容忽视。
图8 A净化厂的a管道测点7深度方向的应力值
图9 A净化厂的b管道测点7深度方向的应力值
6 结论
(1)在役油气管道表面应力检测中,相对于有损检测技术,基于cosα法的X射线衍射检测技术提供了一个较好的检测方向。
(2)采用基于cosα法的X射线衍射检测技术,通过对沉降区域及未沉降区域的同类管道表面应力检测,沉降区域管道表面应力明显大于未发生沉降区域,较好的反映管道受力情况。
(3)在管体表面微米级深度方向,表面应力随深度的增加而递减,最大的或变化最剧烈的残余应力往往存在于管体表面或近表层。
(4)虽然采用基于cosα法的X射线衍射检测技术为表面应力检测提供了方向,反应的是微观区域的应力,如何采用表层或近表层微观区域应力评价管道所受宏观应力,建立相应的评价模型,还需继续研究。
免责声明:本网站所转载的文字、图片与视频资料版权归原创作者所有,如果涉及侵权,请第一时间联系本网删除。
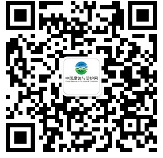
官方微信
《中国腐蚀与防护网电子期刊》征订启事
- 投稿联系:编辑部
- 电话:010-62316606-806
- 邮箱:fsfhzy666@163.com
- 中国腐蚀与防护网官方QQ群:140808414