1 合理选择与使用材料
纯金属的耐蚀性决定于电极电位,电极电位越高(越正), 耐蚀性越好,因此有贵金属与贱金属之分。合金耐蚀性与化学成分及组织结构有关,也与介质种类及条件等因素有关系。提高金属材料耐腐蚀程度,应从热力学和动力学考虑,腐蚀的控制因素可用腐蚀电流(I ) 大小予以判断。
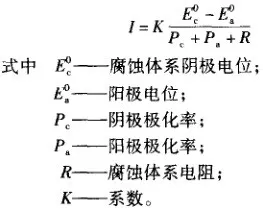
从上式可以看出,材料的耐蚀性可采用以下控制措施。
1. 在其他条件一定时,图片值越小,I 也越小,材料耐蚀性越好。因此用合金化方法提高材料的图片降低图片值。例如Cu 中加入Au、Ni中加入Cu 可使合金耐蚀性显著提高。这种方法消耗贵金属,一般情况下不易实现。
2. 增大Pc值减少腐蚀电流。
控制阴极过程可用减小阴极面积及提高阴极析氢电位等方法。合金中第二相或夹杂物大多数是阴极相,通过提高材料纯净度,进行固溶处理等可以提高材料耐蚀性。例如单相硬铝合金比退火态耐蚀性提高。但是体系中阳极相可钝化时,减少阴极面积反而不利于提高材料耐蚀性。
在非氧化性或氧化性不强的酸中,析氢电位可控制材料的腐蚀,析氢电位越低(越负)腐蚀速度增大,合金中加入析氢电位高的元素可以降低腐蚀程度。例如Mg 中加入质量分数为0.5%~1.0%的Mn时,使Mg-Mn合金在含有氧化物的水溶液中的腐蚀速度大大降低。
3. 增大Pa值减少腐蚀电流。
采用降低材料阳极活性,阻碍阳极过程,提高耐蚀性。如果合金中的第二相是阳极相,基体是阴极相,采用提高材料纯净度或固溶处理,减少阳极面积,提高材料耐蚀性。如果合金中阳极第二相数量多时,在腐蚀过程中将逐渐降低腐蚀速度。例如Al-Mg 系合金中强化相(Al2Mg3 ) 是阳极性,在腐蚀过程中将逐渐被腐蚀掉,合金表面微阳极相总面积逐渐减小,材料腐蚀速度降低,所以Al-Mg合金耐蚀性比 Al-Cu 合金好。
基体中加入易钝化元素,促使合金钝化,提高材料耐蚀性。例如钢中加入质量分数为12% ~13%的Cr, Ni或Ti 中加入Mo可大大提高材料耐蚀性。
4. 增大R值减少腐蚀电流。
加入某些元素使合金表面产生保护膜,增大R值,提高材料耐蚀性。例如钢中加入 Cu、P时能促使表面形成FeOx (OH)3-2保护膜,可提高材料耐大气腐蚀能力。
2 表面防护
在金属材料表面加上覆盖层(或镀层), 使基体与腐蚀介质隔开,防止零件腐蚀。用做覆盖层的材料有金属和非金属两大类。
2.1 金属覆盖层
2.1.1 镀层用材料
所选用的覆盖层材料为阳极性与阴极性两种。如果镀层材料的电极电位比基体金属低时(负), 它成为阳极,基体是阴极,受覆盖层的保护。镀层中存在空隙时也不影响防蚀效果,例如钢铁表面镀Zn属此类情况。
如果镀层材料的电极电位比基体高(正),则基体为阳极,镀层是阴极,镀层中如存在空隙时将加速基体金属腐蚀。例如钢铁表面镀 Sn属此类镀层材料。
2.1.2 覆盖方法
1. 热浸镀。
将基体金属浸人熔融状态的液体金属中,使表面沾上一层镀层金属,防止基体受腐蚀。热浸镀Zn的历史最长,至今仍是钢铁防腐蚀的重要措施。镀Zn层具有良好的耐蚀性,在水及大气介质中Zn的平均腐蚀速度是钢铁的1/25。镀Zn层在城市大气中的腐蚀速度约为2~7μm/a(注:a—年的缩写,下同。), 有优良的耐蚀性,可使镀Zn板寿命达到50年。海洋大气中的腐蚀速度与城市大气相同,约为1~7μm/a, 飞溅区的腐蚀速度约为15μm/a.热带地区镀Zn层的腐蚀速度也不大,干大气中小于 2μm/a, 潮湿大气中小于3μm/a, 海岸区小于6um/a。
镀Zn层在硬水中腐蚀速度约为2.5mg/ (㎡·a) , 在软水中约为硬水中10倍。水中溶解氧越多,腐蚀越快。水温对镀Zn层的腐蚀有影响,工业用水40℃左右、软水90℃左右腐蚀最快。浸泡在海水中的镀Zn 钢板的腐蚀速度约为12~24μm/a。
热浸镀AI防腐蚀方法发展迅速,其工艺与热浸Zn相似。Al的电极电位为-1.66V, 比Fe(-0.44V) 和Zn (-0.1763V) 都低。镀AI层能形成致密又稳定的Al2O3, 保护膜,起到良好的防蚀作用。如镀 AI层发生机械损伤时,镀Al层对钢铁基体仍可起保护作用。镀Al钢板耐大气腐蚀,也耐海水腐蚀、土壤腐蚀及应力腐蚀。镀Al 钢板耐大气腐蚀能力是镀 Zn 钢板的3~6倍。图1 是热浸镀Zn 钢板与热浸镀 Al 钢板耐工业大气腐蚀的比较。
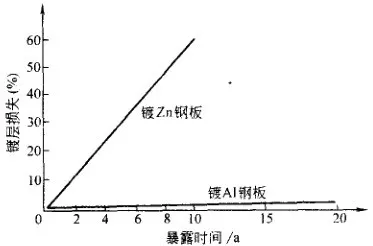
▲图1 板耐工业大气腐蚀比较
热浸镀Zn钢板与热浸镀AI钢
镀Al钢板还具有耐含S介质的腐蚀能力。表1 及表2 是热浸镀Al钢板在高温氧化、硫化气氛及H2O介质中的腐蚀效果。
▼表1 中的暴露试验在高温氧化、硫化气氛
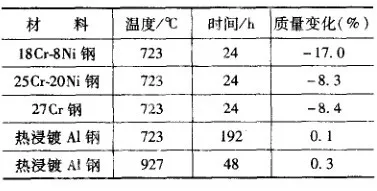
▼表2 在高温H, S介质中的腐蚀试验(50h)
热浸镀Al 钢板有一定耐热性,在500℃以下长期加热时外观无变化。此外还有热浸镀Sn、Sn-Pb合金等方法。
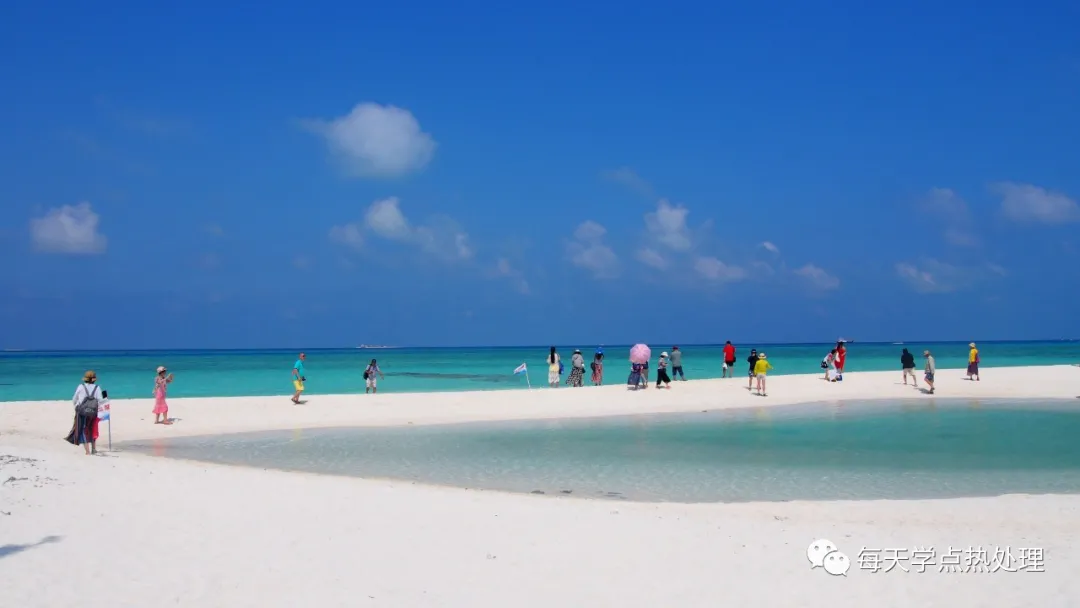
2. 表面渗金属。
为提高材料耐腐蚀性,对零件表面渗金属的方法已有相当长历史,应用十分广泛。渗金属不仅能提高材料耐蚀性,也能提高硬度及强度。所渗的金属主要有Zn、Al、Cr 及 Si 等。
渗Zn 与热浸镀Zn 比较,前者的耐蚀效果更好,如果镀Zn后在500℃左右退火,产生Zn扩散层,可明显提高耐蚀性,如表3 所示。
▼表3 渗Zn和镀Zn制品的耐蚀性比较
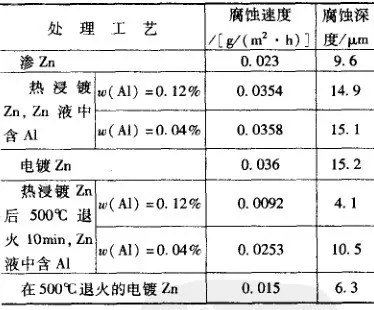
渗AI钢具有良好的高温抗氧化性,其抗氧化能力与渗AI层厚度及AI含量有关。在断续氧化条件下碳钢临界渗Al质量分数为5%, 连续氧化条件下为2%。高温长期使用时渗AI层厚度应达到0.3mm。
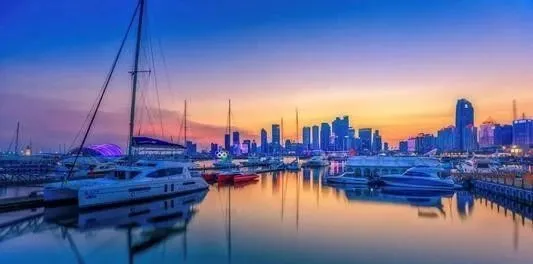
3. 电镀。
用直流电源将电解液中的金属离子沉积于基体金属表面(阴极)。电镀可显著
提高材料耐蚀性,应用广泛,是十分重要的防腐蚀方法。用于电镀的金属有:Cu、Cu-Zn、Ni、Cr、Sn、Zn等。
(4) 其他表面镀层技术,例如热喷镀、离子镀、离子注入及气相沉积等方法。
2.2 无机非金属覆盖层
1. 用化学或电化学方法在基体金属表面覆盖一层无机物防蚀层,也称为化学转化层(Chemical Conversion Coating) , 电化学法形成的无机防护层也称为阳极氧化。工业上常用的金属材料可采用此法,其中最常见的是钢铁材料的磷化处理、发黑处理;铝及铝合金的阳极氧化处理,Zn、Cd、 Mg 等金属均可进行这种防蚀处理。
2. 其他方法,例如玻璃覆盖层法、陶瓷涂层法、耐酸水泥涂层法等。
2.3 有机涂层
有机涂层是金属防腐蚀最常采用的措施之一,广泛应用于工业及生活领域中。有机涂层材料的组成为:主要成分(漆料及颜料)、辅助成分(溶剂、稀释料)和助剂(各种添加剂)。覆盖层起阴极保护及缓蚀作用。漆膜是颜料在漆料(聚合物)中形成的涂料在基底表面固化的结果,漆膜对基体的保护作用常常取决于颜料的物理化学性质。颜料有金属粉(例如Zn、Al、不锈钢粉等)、天然无机物(例如云母、氧化铁)、合成无机物(铅酸钙、铬酸锌等)和合成有机物。它们不溶于漆料中,有良好的化学稳定性和光稳定性。用于涂料的漆料有植物油(其中亚麻子油用量最多) 和油性树脂,其中使用最多的是酚醛树脂。
有机涂层的失效主要是在阳光、大气、雨水等作用下的老化,特别是紫外线、氧、水汽、高温和腐蚀性气体(例如SO2 ) , 会加速老化,使表面失去光泽、起泡、粉化、剥落、生锈等,从而失去防蚀作用。因此,应根据产品特点选用合适涂料。
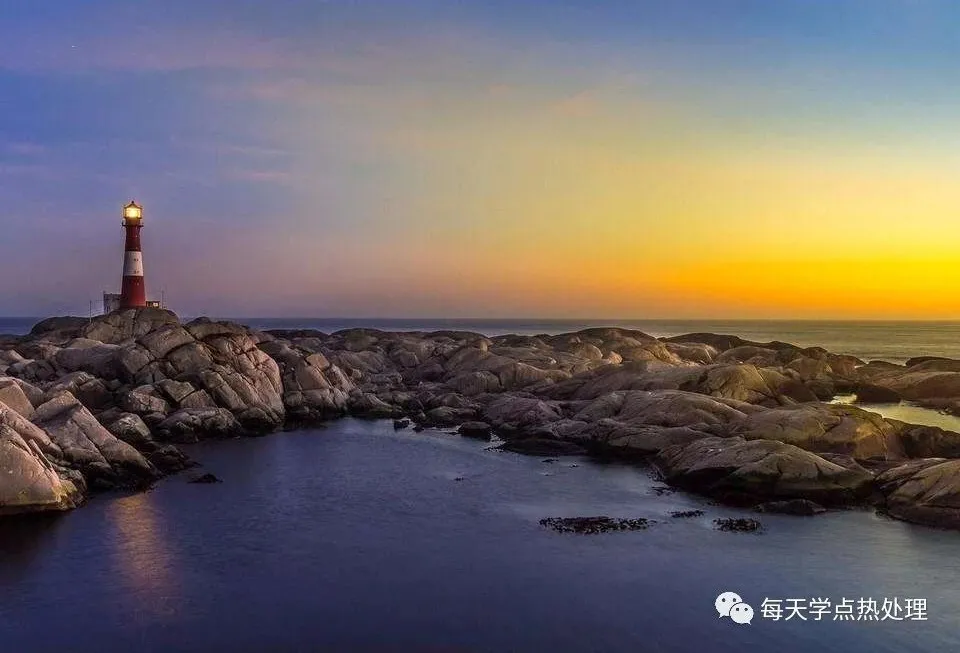
3 缓蚀剂
3.1 分类
金属腐蚀大多数是电化学反应,因此在介质中加人缓蚀剂,防止或减缓腐蚀是经济、简便的方法。缓蚀剂可按下列方法分类:
1. 按化学成分,分为有机型缓蚀剂和无机型缓蚀剂。
2. 按照使用状态,分为水溶液、油溶性和汽化型缓蚀剂。
3. 按pH值,为中性溶液和酸性溶液缓蚀剂。
4. 按缓蚀剂作用机理,分为阳极型、阴极型、吸附型和保护膜型。
3.2 缓蚀剂的选用原则
1. 不同腐蚀介质应选用不同缓蚀剂。
中性水介质主要采用钝化型(阳极型)和沉淀型缓蚀剂,这些缓蚀剂多数为无机物。酸性介质采用多为有机物的吸附型缓蚀剂。油类介质采用油溶性吸附型缓蚀剂,以排除水的吸附,起到防护作用。
缓蚀剂在液体腐蚀介质中的溶解度、在气体介质中的挥发度均对缓蚀效果有影响。溶解度太低会影响缓蚀物质在介质中的传递,不能有效地达到金属表面,即使缓蚀剂的吸附性好,也不能充分发挥缓蚀作用。出现这种情况可加入一些表面活性剂,增加缓蚀物质的分散性。腐蚀介质的温度、压力、流速等对缓蚀效果有影响。
2. 不同金属采用不同缓蚀剂。
3. 单品种缓蚀剂比复合缓蚀剂的缓蚀效果小、因此现代使用的缓蚀剂很少采用单品种缓蚀剂,而是复合缓蚀剂。
4. 许多高效缓蚀剂常常有毒性,例如铬酸盐是中性水介质中的高效氧化性缓蚀剂,其pH值为6~11。除钢铁材料外,对大多数非铁金属也能产生有效保护作用。铬酸盐有毒,危害环境,使用受到限制。
3.3 中性介质中的缓蚀剂
中性介质溶液有各类水(例如冷却水、锅炉水、洗涤水、供暖水、回收处理污水等)、中性盐水溶液(例如含 NaCI、MgCl2、NH4CI、Na2SO4, Na2CO3 水溶液)以及中性有机溶液(例如油类、醇类、多卤代烃等)。应用缓蚀剂最多的是循环冷却水。
3.3.1 工业循环冷却水用缓蚀剂
1. 无机盐缓蚀剂
1) 铬酸盐有良好的缓蚀作用,常用的有Na2Cr2O7或K2Cr2O7于钝化型(阳极型)缓蚀剂。在钢铁表面形成几纳米(nm) 厚的Fe2O3, 和Cr2O3氧化膜。铬酸盐在水中形成钝化膜的临界含量为10E-4~1.3x10E-4 (质量分数)。当液体中CI-浓度增加或温度升高时,其临界含量也升高,否则将产生局部腐蚀。铬酸盐单独使用时防止局部腐蚀较困难,常常与聚磷酸盐或锌盐复合使用。在自来水中复合缓蚀剂的缓蚀效果如图2所示。
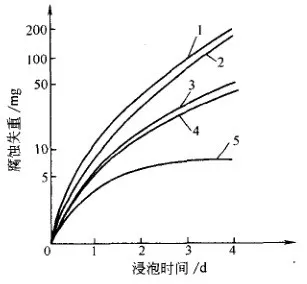
▲图2 在自来水中复合缓蚀剂
的缓蚀效果(30℃)
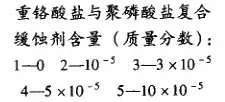
铬酸盐与聚磷酸盐复合缓蚀剂在循环冷却水及海水中,水温在100℃以下时,对碳钢、Cu、Cu-Zn合金、Al及不锈钢等都有良好的缓蚀效果。铬酸盐有毒,需要进行排污处理,使Cr2+含量不超过0.05~0.1mg/L.因此,现在用铬酸盐做缓蚀剂已很少,甚至不使用这种缓蚀剂。
2) 聚磷酸盐缓蚀剂常与锌盐等缓蚀剂复合使用,提高缓蚀效果。常用的聚磷酸盐是三聚磷酸钠和六偏磷酸钠。六偏磷酸钠缓蚀效果较好,而三聚磷酸钠价格低,所以使用较多。六偏磷酸钠在有溶解氧的水中有显著缓蚀作用,促进钢铁表面生成γ-Fe2O3 钝化膜,是阳极型缓蚀剂。
水中含有Ca2+、Zn2+等离子时对聚磷酸盐的缓蚀效果有影响,只有[Ca2+ / (NaPO3 ) n]大于0.2以上时,才有良好的缓蚀效果。
聚磷酸盐易水解,水解后降低了缓蚀效果,是其主要缺点。
3) 硅酸盐缓蚀剂的组成为Na2O·nSiO2。
在pH>6的水中时n=3.3, 在pH<6的水中n=2 较为合适。硅酸盐属沉淀型缓蚀剂。Ca2+可使硅酸盐缓蚀效果提高,硅酸盐与Ca2+、Mg2+离子形成不溶性保护膜。应当指出,使用硅酸钠缓蚀剂时水中的Ca2+、Mg2+离子浓度不能过高,否则有形成硅酸钙、硅酸镁水垢的危险。水中Mg2+含量大于250mg/L时,不宜采用硅酸钠缓蚀剂。
硅酸钠与锌盐等复合使用时可提高缓蚀效果。硅酸钠缓蚀剂的优点是无毒,价格便宜。
4) 钼酸盐缓蚀剂属阳极型,有溶解氧存在时可使碳钢表面形成钝化膜。常用的钼酸盐是Na2MoO4单独使用钼酸盐时的加入量应达到4x10E-4(质量分数)时才有较好的缓蚀作用。所以与有机磷酸盐、锌酸盐等复合使用,可减少钼酸盐用量,提高缓蚀效果。
钼酸盐对抑制点蚀和缝隙腐蚀有显著效果。溶解的钼酸盐离子能有效地使蚀孔内的铁再钝化,减少氧化物聚积。钼酸盐的毒性极低,适应性较强,是有应用前景的缓蚀剂。
5) 其他无机盐缓蚀剂,例如亚硝酸盐(NaNO2, 、KNO2 ) 是阳极型缓蚀剂,其添加量达到(25~50) x10E-6 (质量分数)时,有较好的缓蚀效果。亚硝酸盐在pH<6的酸性介质中易分解,无缓蚀作用,pH=9-10时缓蚀效果最好。
亚硝酸钠易转变为致癌物质,危害人的健康,不宜采用。
锌盐缓蚀剂是复合型缓蚀剂的组分,属沉淀型和阴极型缓蚀剂。锌盐有毒性,其用量应限制在排污规定范围内,因此经常使用的加入量仅为(3~5) x10E-6 (质量分数)。
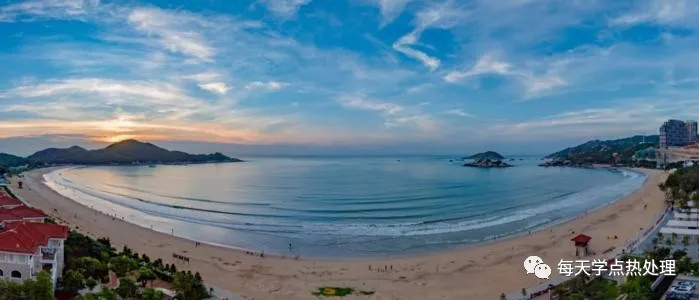
2. 有机盐缓蚀剂
1)有机磷酸与磷酸盐及磷酸酯类。
这类缓蚀剂有络合金属离子的能力,在金属表面形成络合物沉淀膜,对金属产生缓蚀效果。有机磷酸缓蚀剂含量较高时的缓蚀效果比无机磷酸盐大,例如HEDP (羟基乙叉二磷酸)及EDTMP (乙二胺四甲叉磷酸)含量为100×10E-6 (质量分数)时的缓蚀效果比聚磷酸盐大4~7倍。表4 是碳钢在50℃、pH值为8.0~8.5介质中96h的试验结果。
▼表4 有机磷酸与无机磷酸盐缓蚀效果比较
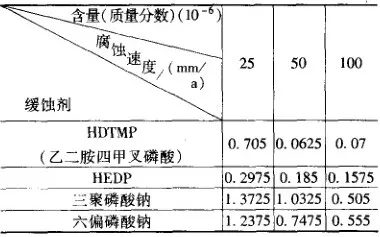
如将有机磷酸与无机磷酸盐复合使用,其缓蚀效果更好。有机磷酸的化学稳定性高、不易水解,可耐较高温度,有较好的阻垢能力,是有发展前景的缓蚀剂。
2) 有机羟酸类。
应用于中性水介质的缓蚀剂有芳香族羧酸及脂肪族取代羧酸(例如羟基酸、氨基酸及酰胺羧酸等)及其钠盐。例如酰基肌氨酸的原料容易获得,无毒性,不产生环境。污染,适用于pH=6~11的软水或硬水介质,除冷却循环水外,锅炉水、盐水系统、高炉及转炉冷却水均可应用,是有发展前景的缓蚀剂。
3.3.2. 含中性盐水溶液中的缓蚀剂
水中溶解中性盐,例如 NaCI、KCI、MgCl2、 CaCl2、Na2CO3、Na2SO4等,能促进金属腐蚀。用于冷却水系统的缓蚀剂多数也可作为中性盐水溶液的缓蚀剂。但是这些盐含量高时,应选用缓蚀效果更好的缓蚀剂。
1. 烷氨基醇类。
烷氨基醇对NaCl、CaCl2水溶液中的碳钢有很好的缓蚀作用,缓蚀率可达到90%以上。表5 是2-乙氨基乙醇对在w (NaCI) 为3%水溶液中碳钢的缓蚀效果。随其含量增加缓蚀效果增大,pH值也增加。当含量为3. 1x10E-4时 pH=10.3, 此后再增加缓蚀剂含量时、pH值不变。如果加入NaOH调pH值,也能产生一定缓蚀效果。
▼表5 2-乙氨基乙醇对在w (NaCI)
为3%水溶液中碳钢的缓蚀效果
2. 葡萄糖酸锌。
试验发现,葡萄糖酸锌(C4H11O17)2Zn 对海水中的碳钢有很好的缓蚀作
用,对海水中的Cu 也有缓蚀作用。葡萄糖酸锌浓度对缓蚀效果有影响,当含量达到4x10E-3 mol/L时,缓蚀率可达到60%, 继续增加含量时缓蚀效果降低。
4 电化学防腐蚀
4.1 阴极防护
在水及土壤中的金属结构或设备可采用阴极保护法防止或减缓腐蚀。阴极防护方法有两种,一是将被保护体与直流电源连接,通过辅助阳极和介质使电流到达被保护结构;二是采用比被保护金属的电极电位低(负)的金属作为牺牲阳极,牺牲阳极首先溶解,释放出的电流使结构阴极极化至所需要的电位,产生防蚀作用。图3 所示为阴极保护示意图。
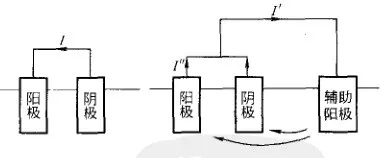
▲图3 阴极保护示意图
4.1.1 牺牲阳极法
最主要的是选择牺牲阳极 材料。作为牺牲阳极应有足够低的开路电位和稳定的闭路电位,单页不能过负,否则会出现阴极析氢。要有稳定的电流效率,即消耗单位牺牲阳极所产生的电量(A·h/kg) 。原料充足,价格常用的牺牲阳极材料有纯Mg、Mg-Mn、Mg-Al-Zn-Mn、纯Zn、Zn-Al、Zn-Sn、Zn-Al-Mn、Zn-Al-Ca、AI-Zn-Mg、Al-Zn-Sn 及Al-Zn-Ir等。
4.1.2 外加电流阴极保护法
用恒电位仪、整流器、太阳能电池及直流发电机等作为电源,通过辅助阳极及阳极屏、参比电极等保护系统,实现阴极保护。通电流时辅助阳极不断溶解。阳极
屏的作用是防止电流短路,扩大电流分布范围,确保阴极保护效果,因此在阳极周围涂上屏蔽层,即阳极屏。参比电极用于测量被保护结构的电位,向恒电位仪提供信号,以调节保护电流大小,使被保护金属处于保护电位范围内。
Zn-Al-Ca、AI-Zn-Mg、Al-Zn-Sn 及Al-Zn-Ir等。
常用的辅助阳极材料有三类,一是可溶性阳极材料,例如废钢铁、铝等;二是微溶性阳极材料,例如硅铸铁、石墨、铅合金等;三是不溶性阳极材料,例如铂及铂合金等。
4.2 阳极保护
在不含CI-介质中能促使金属钝化,进行阳极保护。被保护金属通阳极电流,使之产生钝化区。由于阳极保护使用条件受限制,因此不如阴极保护应用广泛。
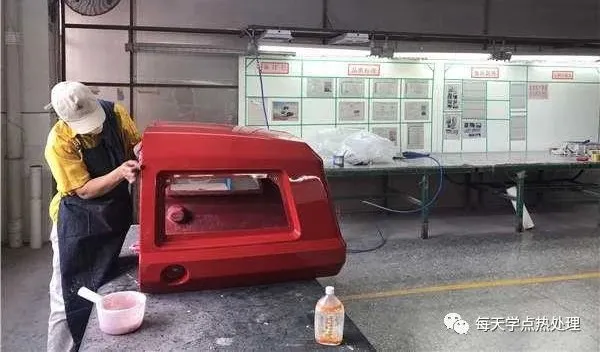
免责声明:本网站所转载的文字、图片与视频资料版权归原创作者所有,如果涉及侵权,请第一时间联系本网删除。
相关文章
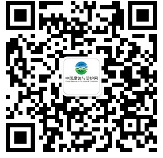
官方微信
《中国腐蚀与防护网电子期刊》征订启事
- 投稿联系:编辑部
- 电话:010-62316606-806
- 邮箱:fsfhzy666@163.com
- 中国腐蚀与防护网官方QQ群:140808414
点击排行
PPT新闻
“海洋金属”——钛合金在舰船的
点击数:7130
腐蚀与“海上丝绸之路”
点击数:5741