情况说明
某地铁生产用铝合金车体底架边梁型材在机加工过程中,出现批量性型材板翼板端部位置出现贯穿性裂纹(见图1),该型材翼板系地铁车下设备安装的承载部位,裂纹的存在对列车运行具有相当的安全隐患。针对上述问题,对型材的原材料理化性能、断口进行了分析,并结合机加工工艺,查明型材开裂的原因,为防止今后发生类似问题提供了科学依据。
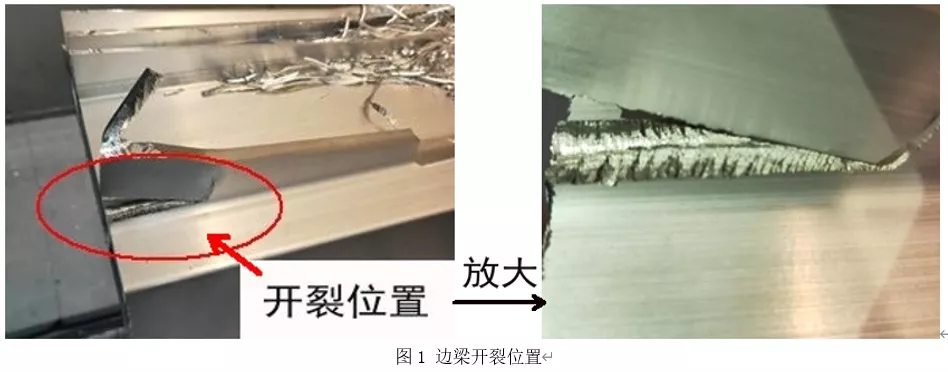
断口宏观观察
开裂边梁型材断口宏观形貌见图2,断口呈现双面多源开裂特征(疲劳源见图中型材表面小箭头处),可见交变应力条带,裂纹扩展方向由翼板根部表面向板厚中心扩展(见图中断面上小箭头处),板厚中心为最终断裂区,断口右侧为取样时人工扳断区。
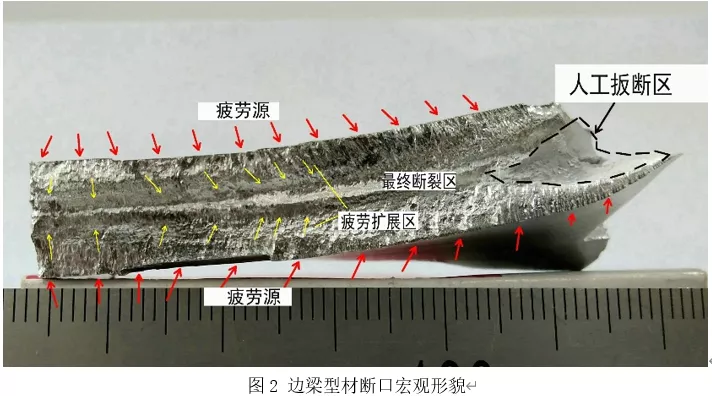
断口SEM分析
对边梁型材断口进行扫描电镜断口分析,断口经酒精超声波清洗后,采用EV0-18扫描电子显微镜(SEM)观察边梁断口形貌,断口低倍形貌见图3a,可见断口经过反复挤压的擦伤痕迹;疲劳源区SEM形貌见图3b,可见轮胎花样疲劳特征;疲劳扩展区SEM形貌见图3c,可见疲劳条带及平行于疲劳条带的二次裂纹形貌;最终断裂区SEM形貌见图3d,可见严重的挤压擦伤及次生裂纹形貌。
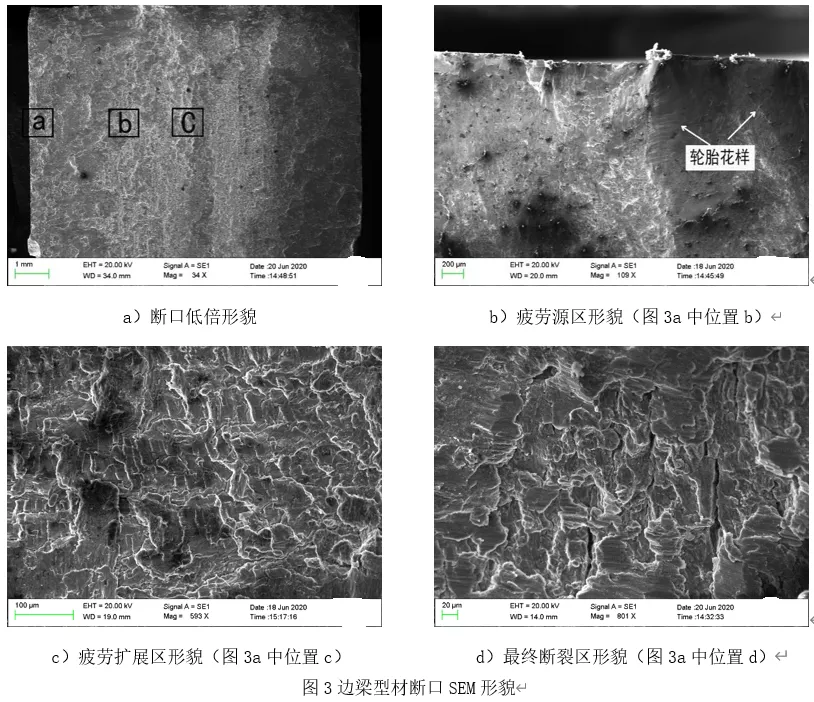
挤压焊缝检验
对边梁型材依据TB/T3260.4-2011《动车组用铝及铝合金 第4部分:型材》进行扩口试验,边梁型材设计焊缝位置及实际焊缝位置见图3,边梁型材扩口试验试样见图4。结果表明型材的挤压焊缝不存在焊合不良现象。
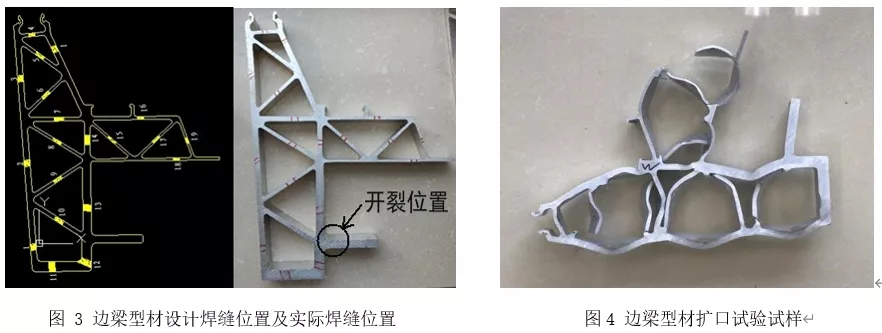
化学成分分析
使用ARL4460直读光谱仪,依据GB/T7999-2015《铝及铝合金光电直读发射光谱分析方法》对边梁型材进行化学成分分析,测试结果见表1。
结果表明边梁型材的化学成分均符合EN573-3-2013《铝和铝合金 锻制产品的化学成份和形式 第3部分:化学成份》标准中6005牌号铝合金化学成分技术要求。

力学性能测试
使用CMT5205-微机控制材料试验机,依据GB/T228.1-2010《金属材料拉伸试验 第一部分室温试验方法》对边梁型材进行拉伸性能检测;使用WE-100液压万能试验机,依据GB/T232-2010《金属材料 弯曲试验方法》对边梁型材进行弯曲性能检测,检测结果见表2,边梁型材力学性能测试试样见图5。
结果表明边梁型材的拉伸性能与弯曲性能符合EN755-2-2016《铝和铝合金挤压杆材/棒材、管材及型材第二部分:机械性能》 标准中6005牌号铝合金技术要求。
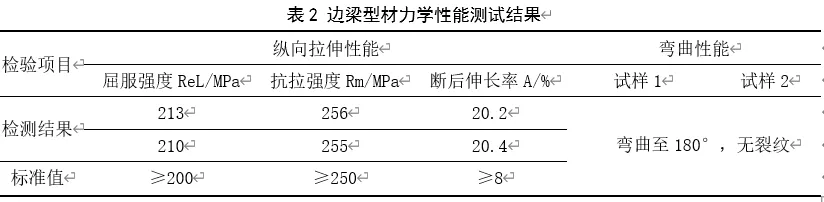
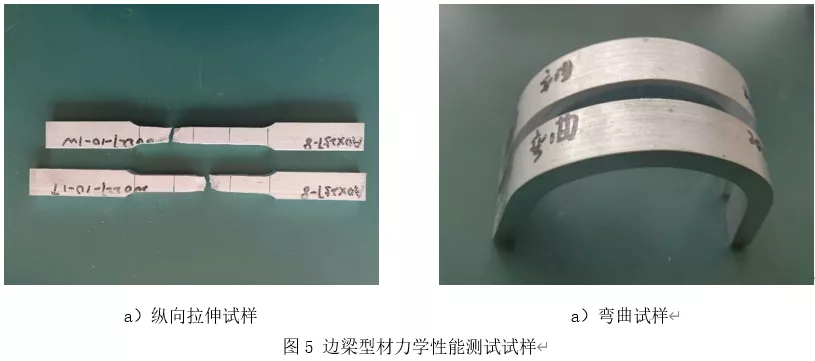
微观金相分析
对边梁型材开裂位置附近取样,使用D1m金相显微镜与放大镜,依据GB/T3246.1-2012《变形铝及铝合金制品组织检验方法 第1部分 显微组织检验方法》和GB/T3246.2-2012《变形铝及铝合金制品组织检验方法 第2部分 低倍组织检验方法》进行金相检验,检验结果见表3。边梁型材金相组织形貌见图6。

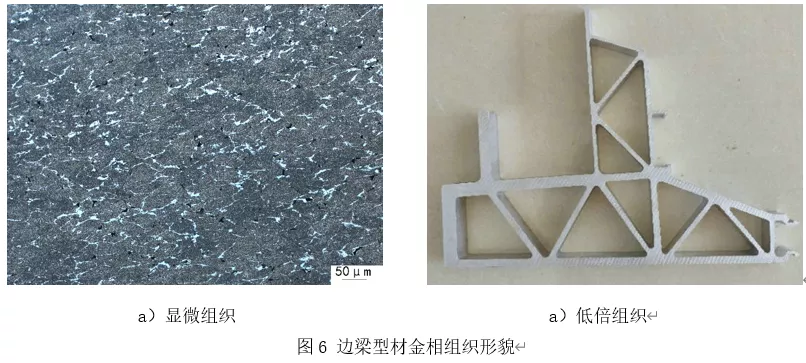
机加工工艺分析
边梁型材翼板开裂时机加工程序见图7,刀具前进方向及刀具转向见图中箭头处。可见边梁翼板开裂位置在机加工的最后工序,在加工该部位时,翼板整体已不连续,加工部位已呈独立承载壮态,且受工装长度所限,该部位无工装加固,悬空近320mm左右,在加工过程中翼板根部承受交变弯曲应力。
分析与讨论
(1)边梁型材成份、拉伸和弯曲性能、宏微观组织均符合标准要求,开裂位置与型材焊缝不重合。
(2)边梁型材裂纹断口呈多源性疲劳特征,在加工过程中受交变弯曲应力与振动叠加作用,在边梁翼板根部萌生疲劳源,并由表面向根部心部扩展。
(3)开裂批次边梁型材的机加工与前期生产的批次由于加工工位的变更,机加工工艺作了调整,主要体现在以下三个方面:一是原来加工方向为由边梁端部开始加工,改为边梁端部最后工序加工;二是加工进给量增加;三是采用垂向铣刀。
结论及建议
(1)型材开裂的主要是由于机加工工艺不当,造成型材端部翼板受到较在交变弯曲应力与振动作用所致。
(2)建议对机加工工艺进行如下调整:1、改变加工方向;2、减少进给量;3、改立铣为横铣机加工方式。
免责声明:本网站所转载的文字、图片与视频资料版权归原创作者所有,如果涉及侵权,请第一时间联系本网删除。
相关文章
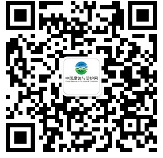
官方微信
《中国腐蚀与防护网电子期刊》征订启事
- 投稿联系:编辑部
- 电话:010-62316606-806
- 邮箱:fsfhzy666@163.com
- 中国腐蚀与防护网官方QQ群:140808414
点击排行
PPT新闻
“海洋金属”——钛合金在舰船的
点击数:7130
腐蚀与“海上丝绸之路”
点击数:5741