一、组织与性能的关系
金属零件通过热处理获得一定的组织,以期达到要求的使用性能。热处理是手段,使用性能是目的,而组织则是机械性能的基础和保证。
钢铁材料成分、组织与性能的关系可以用图1 来示意。
▲图1 钢铁材料成分、组织、性能关系示意图
(Fe3C)Ⅰ-一次渗碳体(Fe3C)Ⅱ-二次渗碳体
各种热处理工艺处理过的工件,其使用状态下的组织及性能要求如表1所示 。
▼表1 常用钢种热处理工艺、组织及性能
一般零件根据工作服役情况,确定主要性能要求,从而选择合适的热处理工艺和使用状态下的组织。热处理质量除了通过对热处理零件或随炉试样的性能进行测试外,还有一些性能或热处理缺陷如,耐蚀性、耐磨性、红硬性以及脱碳、过热、过烧等等,必须通过金相组织的检验来检查。为此,为了加强对热处理质量的控制与检验,国家或行业制定了不少有关金相的检验标准。
热处理产生的组织不合格是指通过宏观观察和显微分析发现的组织不符合技术条件要求或者明显热处理组织缺陷。
二、氧化与脱碳
2.1 氧化
氧化是钢在空气等氧化性气氛中加热时,表面产生的氧化层。氧化层由Fe2O3、Fe3O4、FeO 三种氧化物组成,外表面有过剩的氧存在,因而形成含氧较高的氧化物Fe2O3,在靠近基体的内部,由于氧少金属多,因而形成含氧较低的氧化物FeO,氧化层中间部分为 Fe3O4 ,即由外层到内层氧化过程逐渐减轻,如图2 所示 。
图2 铁的氧化层组成示意图
随气氛中氧含量增加以及加热温度升高,氧化程度增加,氧化层厚度增加如图3 所示 。
图3 温度和气氛对氧化速度的影响
氧化层达到一定厚度就形成氧化皮了,由于氧化皮与钢的膨胀系数不同,是氧化皮产生机械分析,不仅影响表面质量,而且加速了钢材的氧化。
氧化是金属表面失去金属光泽,表面粗糙度增加,精度下降,这对精密零件是不允许的。
2.2 脱碳
脱碳是指钢在加热时表面碳含量降低的现象。脱碳的实质是钢中碳在高温下与氧和氢等发生作用生成一氧化碳或甲烷的化学反应。其化学反应如下:
这些反应是可逆的,氧、氢、二氧化碳、水使钢脱碳,一氧化碳和甲烷可以使钢增碳。一般情况下,钢的氧化脱碳同时进行,当钢表面氧化速度小于碳从内层向外层扩散速度时,发生脱碳。反之,当氧化速度大于碳从内层向外层扩散的速度时,则发生氧化。因此,氧化作用相对较弱的氧化气氛中容易产生较深的脱碳层。
脱碳层由于被氧化,含碳量降低,金相组织中碳化物较少。脱碳层包括全脱碳和半脱碳两部分,全脱碳层显微组织为全部铁素体,半脱碳层是指全脱碳层的内边界至钢的正常含碳量的组织处。典型的脱碳组织如图4 所示 。
图4 钢的脱碳层典型组织 100X
材料:30CrMoA
脱碳在钢表面形成铁素体晶粒的形状有柱状和粒状两种,如图5 所示。
图5 脱碳组织的两种形态
a)粒状晶脱碳 b)柱状晶脱碳
钢在A1~Acm区域内加热时,强脱碳形成柱状晶脱碳,在A3以上加热或A1以上加热弱脱碳产生粒状晶脱碳。
随加热温度升高、加热介质氧化性增强,钢的氧化托他不能增加,如表3 和图6 所示。脱碳会明显降低钢的淬火硬度、耐磨性及疲劳性能,高速钢会降低红硬性。
▲图6 40钢在氮基气氛中加热时的脱碳情况
(加热温度850℃,H2=8%~12%+其余N2)
1-H2O/H2=0.065 2-H2O/H2=0.045
3-H1O/H2=0.033 4-H2O/H2=0.025
▼表3 50钢在空气电路中加热3h的氧化情况
2.3 防止和减轻氧化脱碳的措施
防止氧化脱碳的措施图表4 所示。防止氧化脱碳的有效措施是采用盐浴炉、保护气氛炉或真空加热炉,如采用空气炉或燃料炉加热时,必须采取适当保护措施,如涂料、包套、装箱、控制炉气还原性等。
▼表4 防止氧化脱碳的措施
三、过热与过烧
金属或合金在热处理加热时,由于温度过高,晶粒长得很大,以致性能显著降低的现象,称之为过热;加热温度接近其固相线时,晶界氧化和开始部分熔化的现象,称之为过烧。
3.1 过热
过热组织包括结构钢的晶粒粗大,马氏体粗大、残余奥氏体过多、魏氏组织,高速钢的网状碳化物、共晶组织(莱氏体组织)、萘状断口、马氏体不锈钢的铁素体过多、黄铜合金脱锌使表面出现白灰,酸洗后呈麻面等。
典型的过热组织如图7 所示 。过热组织按正常热处理工艺消除的难易程度,可分为稳定过热和不稳定过热两类,一般过热组织可通过正常热处理消除,称之为不稳定过热组织。稳定过热组织是指经一般正火、退火和淬火不能完全消除的过热组织。
▲图7 典型过热组织形貌
过热的重要特征是晶粒粗大,它将降低钢的屈服强度、塑性、冲击韧度和疲劳强度,提高钢的脆性转变温度。参见图8、图9 ,表5、表6 。
▲图8 晶粒大小对钢的屈服强度的影响
▲图9 晶粒大小对钢的脆性转变温度的影响
1-C0.02% Ni0.03% 2-C0.02% Ni3.64%
▼表5 晶粒度对工业纯铁力学性能的影响
▼表5 晶粒度对2135合金疲劳性能的影响
过热的另一个重要特征是淬火马氏体粗大,它将降低冲击韧度和耐磨性,增加淬火变形倾向和淬火开裂倾向,如图10、图11、和表7、表8 所示 。中碳钢马上按其形态和尺寸分为8级,7、8级即为过热组织。
▲图10 马氏体等级对冲击韧度的影响
▲图11 马氏体等级对耐磨性的影响
▼表7 45钢及40Cr钢淬火变形的尺寸变化(0.01mm)
▼表8 45钢淬裂实验结果
钢的过热缺陷还有魏氏组织、萘状断口、石状断口等,不仅能大大降低钢的力学性能而且很容易产生淬火开裂。
各种过热组织的特征和预防措施建表9 。为了防止产生过热,应正确的制定并实施合理的热处理工艺,严格控制炉温和保温时间一般过热组织可以通过多次退火或正火消除,对于较严重的过热组织,如石状断口,不能用热处理消除,必须采用高温形变和退火联合作用才能消除。
▼表8 国组织特征及预防挽救措施
3.2 过烧
过烧组织包括晶界局部熔化、纤维空洞,铝合金表面发黑、起泡、断口灰色无光泽,镁合金表面氧化瘤等。
典型的过烧组织见图12 。
图12 典型的过烧组织(50A钢) 150X
过烧组织使性能严重恶化,极易产生热处理裂纹,所以过烧是不允许产生的热处理缺陷,一旦出现过烧,珍贵零件只能报废,因此热处理生产中要严格防止出现过烧。
四、球化级别不合格
汽车、拖拉机及其他各种机器都大量使用标准件和紧固件,轴、销、杆等标准件大多数使用自动车床车削加工,而螺栓、螺母、铆钉等紧固件大多数采用冷镦加工,为了提高生产率,适应自动切削和冷镦加工,其钢料的预备热处理是退火或球化退火,应该对球化程度予以控制。
自动车削加工要求钢材具有良好的车削性能,塑性不能太高, 否则容易“粘刀” 车屑不断,希望钢材组织为片状珠光体;而冷镦加工要求钢材具有良好的冷镦性能,塑性要好,以保证冷镦时不开裂,希望钢材金相组织为球状珠光体。为此有行业标准JB/T5074-91《低、中碳钢球化率级别 》来评定球化级别。 以碳化物球化程度评级,1级球化率为0,即珠光体完全是片状,6级球化率为100%,即碳化物为完全球化状态。冷镦用中碳钢一般要求4~6级,自动机床加工用低、中碳钢一般要求1~3级。
低、中碳钢预备热处理的球化不合格将严重影响其冷镦和自动切削性能,球化级别对冷镦性能影响如表10 所示 ,由此可以看出,球化1~3级冷镦量大时,将会产生开裂,而在4~6级则冷镦时无开裂,所以冷镦用钢球化率控制在4~6级为合格。大量生产实践表明,自动化车削加工用钢球化率控制在1~3级时,零件表面粗糙度合适,带锯磨损正常,生产率高;如果球化率超过3级,很难进行自动化机床加工。
表10 不同级别金相组织对预顶锻结果的影响
五、渗碳与碳氮共渗组织
渗碳与碳氮共渗组织缺陷主要有以下几种:
1)表层碳化物过多,呈大块状或网状分布;
2)残余奥氏体量过多;
3)马氏体粗大;
4)内氧化;
5)黑色组织。
5.1 表层碳化物过多,呈大块状或网状分布
渗碳件出现大块状和粗大网状碳化物,主要是表层含碳量过高引起的,如采用滴注法渗碳时,滴量过大;可控气氛渗碳时,富化剂的量过多,或者延时控制系统失灵,采用渗碳后直接淬火时,预冷时间过长,淬火温度过低,在预冷时间里使碳化物沿奥氏体晶界析出。采用一次淬火时,淬火温度太低,渗碳预冷后形成的网状、块状氧化物,在重新加热时没有消除。此外,渗碳后冷却太慢也会形成网状碳化物。
由于表层碳的质量分数过高引起上述缺陷时,可重新在碳势较低的气氛中扩散一段时间来消除。由于直接加热淬火和一次淬火温度过低而造成上述缺陷时,可重新加热到较高的温度正火,使网状碳化物溶解,而后在稍高的温度下淬火来消除。
为了防止网状碳化物呈出现,可按下式适当地选择强渗期和扩散期的比例:
为了预防网状或块状碳化物,其关键是合理地控制炉内碳势,并有足够的扩散时间和适当淬火温度。
5.2 残余奥氏体量过多
适量的的残余奥氏体,能够提高渗层的韧度,接触疲劳强度,以及改善啮合条件,扩大接触面积。但残余奥氏体量过多,常会伴随着马氏体针粗大,导致表面硬度下降,降低耐磨性,对不同承载能力的渗碳件,残余奥氏体应有一个最佳范围,通常认为残余奥氏体量在20%(体积分数)以下是允许的 。
引起残余奥氏体过量的原因有以下几个方面:
1)钢种合金元素多。如Cr、Mn、Ti、Mo、W、Ni、等元素融入奥氏体中,增加了奥氏体的稳定性,促使淬火后残余奥氏体量增多。
2)深层中碳的质量分数过高。渗碳气氛碳势过高和渗碳温度偏高,使溶入奥氏体中的碳含量增加,造成淬火后残余奥氏体量增多。
3)淬火温度偏高。加热温度越高,溶入奥氏体中的碳和合金元素量越越多,奥氏体稳定性提高,残余奥氏体量增多。
4)淬火温度偏高,淬火剂温度愈高马氏体转变愈不充分,残余奥氏体量愈多。
为了使残余奥氏体量适当,而又不使马氏体粗大,应合理选择渗碳钢,恰当调整炉内碳势,降低渗碳、淬火和冷却介质的温度。对渗层中过量的残余奥氏体可采用重新加热二次淬火和淬火后深冷处理等方法来消除。
5.3 马氏体粗大
在正常情况下,渗碳层应为回火马氏体、均匀分布的颗粒状碳化物和少量的残余奥氏体。马氏体的的主要作用是提高表面硬度和强度,它的针叶粗细和均匀度对使用性能影响很大。其针愈小,力学性能,特别是韧度好。相反,马氏体针愈粗大,性能愈差,工程上将马氏体针状组织分为8个级别。1级马氏体最小,8级最大,不同零件服役条件不同,对马氏体级别要求也不同,齿轮类零件6级以下为合格,7、8级为粗大组织,不合格。
马氏体粗大同渗碳用钢、渗碳温度和淬火温度过高有关。钢中不含细化晶粒的合金元素如Ti、V、Al、Nb、Zr、N等元素,或不属于本质细晶粒钢时,经渗碳淬火,则容易出现粗大马氏体。对于粗大马氏体,一般可采用降低一次淬火温度方法来解决。
5.4 内氧化在渗碳气氛中,总有一定含量的O2、H2O、CO2气体,当炉子气氛中上述分子含量较高,或炉子密封不好,有空气侵入,或者零件表面有严重氧化皮时,在渗碳过程中将发生内氧化。内氧化的实质是:在高温下,吸附在零件表面的氧可沿奥氏体晶粒边界扩散,并与氧有较大亲和力的元素(如Ti、Si、Al、Cr)发生氧化反应,形成金属氧化物,造成氧化物附近基体的合金元素贫化,淬透性变差,淬火组织中出现非马氏体组织。
典型的非马氏体组织图片
零件表面显微硬度明显下降。当内氧化深度小于13μm时,对疲劳强度没有明显的影响;当大于13μm深度时,疲劳强度随内氧化层的深度增加而明显下降。对20CrMnTi钢,在2675MPa接触应力条件下,表面30μm左右的非马氏体层使疲劳寿命下降20% 左右,100μm的非马氏体层使疲劳寿命下降63%。内氧化的存在也影响表面残余应力分布,内氧化层愈深,表面张力愈大。
为了减少内氧化,应选择不易发生内氧化的钢。内氧化与有些合金元素的存在以及在奥氏体中的含量有关。图13 是常用渗碳钢合金元素氧化趋势,从图中可以看出:Ti、Si、Mn 和 Cr 易被氧化,而W、Mo、Ni、Cu则不被氧化。在含镍的钢中,可有效防止钢的内氧化。在Cr-Mo类钢中,Mo的质量分数偏低时,总是发现内氧化。采用0.5%或更高的钼,对防止内氧化和提高淬透性非常有益。 当Mo/Cr的比值在0.4以下时,可观察到内氧化层是深度达14~20μm;Mo/Cr的比值为1时,钢中则观察不到内氧化现象。对Cr-Ni-Mo类钢,其中Mo/Cr 比值为0.4,而镍的质量分数1%时,也不易出现内氧化现象。国外已相继出现能够抑制内氧化的新型渗碳钢。
为防止内氧化,除了考虑选材外,还可以从工艺上采用以下措施:
1)在渗碳时,要控制炉气中O2、CO2、H2O等气体的含量;减少渗剂中的杂质,如硫的含量。
2)渗碳前要将零件表面氧化皮,锈斑清除干净。
3)在渗碳操作时,要保证炉子良好的密封性,要保护炉内正压并稳定,防止空气进入炉内。
4)排气期,加大富化气量或采取其它措施,尽在恢复炉气碳势。
5)为了减少或者消除内氧化不良后果,可在渗碳结束前向炉内通入质量分数为5%~10%的氨气,只要共渗10分钟,深入少量的氮,即可恢复内氧化损失的淬透性。
6)可通过珩磨、磨削加工、点解抛光、喷砂和抛丸处理去除表面氧化物和减小氧化物厚度,这些措施均可减轻或者克服内氧化的有害影响。
5.5 黑色组织
工件C、N共渗后,在几十微米的表层内出现许多小黑点或小黑块,呈不连续分布,或相连成网状直通表面,形成黑色网状组织;或者出现托氏体黑色网带,这三类组织统称“黑色组织”。
黑色组织一般出现在0.1mm的表层内,在抛光后未经浸蚀的试样中即可观察到,呈斑点状分布,有时呈网状。经浸蚀后可见其分布在白色化合物基底上,经观察证明,黑色色斑点主要由大小不等的孔洞组成。
黑色网状组织是由合金元素氧化物、托氏体、贝氏体等组成的混合组织,一般为黑色网状分布在表层的一定深度以内。式样经过抛光不腐蚀就可以看到黑色网状组织,经腐蚀后更加明显切在最外层出现黑色带。这主要是由于内氧化引起的。
黑色网带组织与内氧化引起的黑色网状组织不同,它在抛光未经浸蚀表面看不见,只有在腐蚀后才能在金相显微镜下看到,其特征是在整个渗层内沿奥氏体晶界析出托氏体网;当表面有粒状碳化物时,在其周围有时也可以看到托氏体、贝氏体组织。
渗层中出现黑色组织将大大降低零件的表面硬度、耐腐蚀性、抗弯疲劳强度,从而显著降低零件的使用寿命。黑色组织对零件性能的影响程度与黑色组织的严重程度有关。20CrMnMo、20Cr2Ni4A钢碳氮共渗的内氧化深度大于0.013mm时,会使钢的疲劳极限下降20%~25%。40Cr钢经碳氮共渗后,在0.3-0.4mm的共渗层中存在0.05~0.06mm的浅黑网时,多次冲击寿命下降30%~60%,存在黑色带状托氏体时,多次冲击寿命下降60%~80%。
综上所述,黑色组织是三种不同组织的统称,由于种类不同其形成机理和产生原因也不同。
5.5.1 黑色点状组织
通过扫描电镜观察表明,黑色点状组织显示为孔洞,孔洞表面光滑,总的形态犹如溶洞。这显然是气体作用的结果。孔洞内比较干净,只有晒书孔洞存在少量孤立的夹杂物,小块状的粒子为硅酸盐夹杂。孔洞中无任何残留的氧化物夹杂或碎片。所以孔洞不可能是晶界上形成的氧化物脱落后的残孔。在孔洞中找不到黑色石墨片或石墨块残存痕迹。孔洞表面露出来的颗粒,是同基体组织结合在一起的晶界上的碳氮化合物,他们也没有分解。
对深冷脆性断口的观察表明,黑色组织孔洞与气体析出有关,不是晶界氧化物或析出的石墨脱落后留下的孔隙。所以造成孔洞的原因,应从氮和氢的作用来考虑。
在800~900℃的共渗温度下,只会有碳氮化物的生成,不会碳氮化合物的分解。在共渗后温度降低时,由于这类化合物稳定性增强,更不能析出气体氮。所以孔洞的形成不一定与碳氮化合物的生成和分解有必然联系。
在共渗温度下,渗层的基体处于稳定的含氮奥氏体状态。一般情况下,氮的气体分子是不易析出的。在某些情况下,如果有气体析出,不是化合物分解的结果,而可能是在约600℃~700℃以下过饱和固溶体的分解。 计算表明,在600℃时,平衡气体氮的压力为25000MPa,这说明在600℃以下的温度时,溶解于共渗层中的氮充分析出时,是有可能造成孔洞的。
在气体碳氮共渗处理中, 碳原子主要来源于碳氢化合物,氮原子主要来于氨,二者热分解后均含有大量的氢。因此钢不可避免地产生强烈的渗氢过程。氢的渗入有两种作用 ,一种作用的直接造成孔洞另一种是间接促成孔洞。后者有两种可能,第一,渗入钢中过量的氢在钢的内部与渗碳体生产甲烷,甲烷在钢中溶解度极小,不易排除,也往往聚集在晶界上或缺陷处,在这些地方造成孔洞或裂纹。第二,共渗层中溶解的氮的摩尔分数很高,在冷却过程中存在析出的趋势。气体氮的析出,必然有氮原子向晶界、缺陷内表面扩散并和氢结合呈氧分子的过程。在低于700℃的温度下,固溶氮的质量分数低,可以主要依靠氢的作用以形成NH3的形式来实现。这样,依靠氨的聚集和压力增长,也能在钢的内部形成孔洞。生产实践表明,黑色点状组织在下述条件下容易出现:共渗介质中氨气量过多,共渗层表面氮的质量分数大于0.5%;共渗温度低,共渗时间长等。降低氨的通入量和提高共渗温度,可以减轻黑色点状组织的产生。
5.5.2 黑色网状组织
黑色网状组织的产生,是由于合金钢在碳氮共渗气氛中加热时,零件的表面与气氛中的二氧化碳、氧气、水蒸气相互作用而被氧化,形成合金氧化物,使奥氏体中的合金元素贫化,降低了奥氏体的稳定性,同时氧化物又促使扩散性转变的非自发成核,随后淬火冷却时,这部分合金元素贫化了奥氏体转变为托氏体、贝氏体等飞马氏体组织。
在碳氮共渗温度下,钢中的合金元素与氧的亲和力从大到小一次为Al、Ti、V、Mn、Fe、Mo、W、Co、Ni。愈靠前的元素愈易被氧化……
碳氮共渗层内氧化倾向较大与共渗介质的氧势较大有关。这是因为液氨中经常含有一定的水分,当氨气干燥不充分时,水分被带入炉内。碳氮共渗温度较低,渗剂裂解不完全,产气量少,排气速度较慢炉内氧化性气体停留时间较长,特别是炉内中的CO2、CO、O2与氨气发生化学反应生成水蒸气,进一步提高了炉内氧势。随着氨气含量增加,内氧化增加。
在实际碳氮共渗条件下,内氧化主要发生在排气阶段。为了防止内氧化,可以采取以下措施:
充分干燥氨气。定期更换或再生干燥装置。如果使用滴注式碳氮共渗,应严格控制渗剂中的水分含量。
在排气阶段,要采取加速排气措施。可用氮气、吸热式气氛进行大气量排气,或者用大滴量甲醇加速排气。在排气初期,要适当减少氨气的供给量。
5.5.3 托氏体黑色网带组织
托氏体黑色网带组织产生的原因,也可能是碳氮共渗时,Cr、Mn等合金元素大量溶入表层的碳氮化合物中,使得奥氏体的合金元素以及碳氮含量降低,使奥氏体稳定性降低,同时这些碳氮化合物起非自发形核作用,进一步加速奥氏体的分解,导致网状托氏体形成。也有可能是共渗温度偏低,炉气活性差,表面含氮量不足,奥氏体不够稳定,或者脱碳而引起的。这类托氏体黑网带经重新加热,快速冷却淬火,可得到消除。
六、渗氮组织缺陷
6.1 渗氮前原始组织中铁素体过多、回火索氏体组织粗大
渗氮前预备热处理目的是消除残余应力,减小渗氮件变形;改善组织,使零件心部获得合适的组织性能,为渗氮做好组织准备。
渗氮前原始组织对渗氮后零件质量有很大影响,渗氮前原始组织中托氏体量增加,使氮化层脆性增加,用声发射弯曲试验方法测定38CrMoAl钢渗氮层表面脆性结果如表11 所示 。
▼表11 原始组织对渗氮层脆性的影响
此外,原始组织中铁素体过多,使预备热处理硬度降低,影响渗氮件心部和表面硬度,如表12 所示 。
▼表12 40CrNiMoA钢预备热处理硬度对渗氮层硬度的影响
渗氮前组织应为细小索氏体和少量游离铁素体,特别要控制铁素体的量,在《钢铁零件渗氮层原始组织测定和金相组织检验》GB/t11354-2005标准中,根据原始组织中游离铁素体量和索氏体形态分为5级,一般1~3级为合格,原始组织中铁素体含量不得超过15%,不允许有粗大索氏体和脱碳层。
防止原始组织中铁素体量过多和粗大索氏体组织的措施是严格控制渗氮前的预备热处理,一般应进行调质处理,采用合适的淬火冷却,并防止温度过高,回火温度一般比渗氮温度高10℃~50℃。对于形状复杂、尺寸稳定性和变形要求严的零件,还应进行稳定化处理,其温度一般等于或高于渗氮温度。
6.2 化合物层疏松
在氮化特别是氮碳共渗后,渗层的化合物层出现细小分布的微孔或者孔洞,可在金相显微镜下可直接从未经腐蚀的氮化层金相抛光面上观察到。由于微孔尺寸的大小、数量和分布不同,对性能的影响也不同。在GB/T11354-2005标准中,主要根据表面化合物层内微孔的形状、数量和密集程度将疏松分为5个等级。一般1~3级合格,4、5级不合格,因其易起皮、剥落。
化合物层疏松多发生在氮碳共渗或高氮势长时间气体渗氮的情况下。
气体氮碳共渗的化合物层疏松,是由于亚稳定的高氮相在氮化过程中发生分解,析出氮分子而留下气孔。生产实践发现,疏松层的形成与不同炉气成分的混合比和处理温度有关。当炉气中NH3含量的继续增加,疏松程度越严重。随着处理温度提高,NH3分解率变化,氮势提高,表面疏松程度增加。
气体渗氮时,化合物层出现疏松与氨气纯度、渗层平均氮浓度有关。如氨气中含有水分,渗层中氮浓度过高,均易产生疏松。
6.3 针状组织
化合物层与过渡层之间出现氮化物这是高氮的 ε 相和 γ? 相。这些针状氮化物沿着原铁素体晶界成一定角度平行生长。这种缺陷组织与渗氮前的原始组织有关。如果原始组织中有大块铁素体存在,或者表面严重脱碳,则容易出现针状组织。
针状组织使化合物层变得很脆,容易剥落。因此,对渗氮零件应严格进行氮化前的调质处理,正确进行工艺过程的控制,防止调质处理过程中产生严重的脱碳和游离铁素体过多的缺陷。在氮化过程中,要经常检查炉子的密封性,防止漏气跑气,保护炉内压力平稳,分解率稳定,严格控制氨气含水量。
6.4 网状和脉状氮化物
合金钢在氮化过程中,因淡化温度过高,氨气含水量过多,调质淬火温度过高造成的晶粒粗大,零件尖角等都可能形成网状或脉状氮化物。根据扩散层中多少形状、数量和分布情况,标准GBt11354-2005中将其分为5级,太长1~3级为合格。
扩散层中形成的脉状级网状组织,严重影响氮化质量,使氮化层脆性增加,耐磨性和疲劳强度下降,极易剥落。为了防止这类组织的出现,可以采用下列预防措施:
1)正确进行调质处理。氮化前,一定要进行调质处理,调质时的淬火温度必须严格控制,过高的淬火温度将引起晶粒长大。调质后的组织应该是均匀度晶粒细小的回火索氏体组织。
2)严格控制氨气中的水分。采用一级液氨或采用高效的吸湿剂,降低其水分含量。
3)选择适当的氮化温度。氮化温度不能太高,长时间的高温氮化会加速网状或波纹状氮化物的形成。
4)零件在设计时,应避免尖角呈锐角,氮化前工件表面不能太粗糙。
当氮化件的扩散层中已经产生网状或波纹状氮化物时,可在500℃~560℃温度下进行10~20h的扩散处理,以改善组织,减轻不良影响。
免责声明:本网站所转载的文字、图片与视频资料版权归原创作者所有,如果涉及侵权,请第一时间联系本网删除。
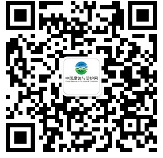
官方微信
《中国腐蚀与防护网电子期刊》征订启事
- 投稿联系:编辑部
- 电话:010-62316606-806
- 邮箱:fsfhzy666@163.com
- 中国腐蚀与防护网官方QQ群:140808414